Construction work is notorious for being one of the most dangerous occupations in the world. Not only is it physically hazardous, its outdoor nature, constant use of dangerous machinery, and flow of deliveries mean that the working environment is constantly in flux, which can be disorienting for the workers.
Mistakes can happen quickly and despite careful preparation. However, making a mistake on a construction site isn’t necessarily catastrophic.
If the mistake is acknowledged, documented, and corrected, the team can move on stronger than before, especially in terms of communication.
Here are six essential tips that will make construction mistakes more manageable, but also more preventable.
In this article...
Assign Responsibility for the Mistake
Project managers should be ready to accept responsibility for mistakes even if another member of the team actually made them.
Good leadership means forming a strong team and providing effective oversight.
So, for example, if a project manager hasn’t provided proper safety training, he or she is partially at fault if a new employee doesn’t know to wear a hi-res vest in inclement weather.
When dealing with the mistake, it’s important to speak openly about the event and to clearly communicate what has happened. Otherwise, it’s easy for the mistake to happen again.
Moreover, best practices for alerting a member of a work team to an error involve taking him or her aside to discuss the matter in private to gain perspective on what has taken place.
In addition to establishing facts about the mistake, this conversation is also an excellent opportunity for leaders to understand why the accident happened.
Take note of what contributed to the mistake:
- Did the employee understand best practices?
- Were expectations clearly communicated?
- Was the employee overwhelmed or distracted by other tasks?
- Does the employee have the proper tools to undertake these tasks?
- How did the actions of others contribute to the circumstances in which the mistake was made?
- Was the employee properly trained?
- Are employees receiving proper hydration, breaks, and direction?
Speaking to the employee with respect rather than placing blame is vital to fostering a healthy workplace.
Conversely, shouting in anger, resorting to threats and insults, and instituting cover-ups can help to contribute to a cycle of blame:
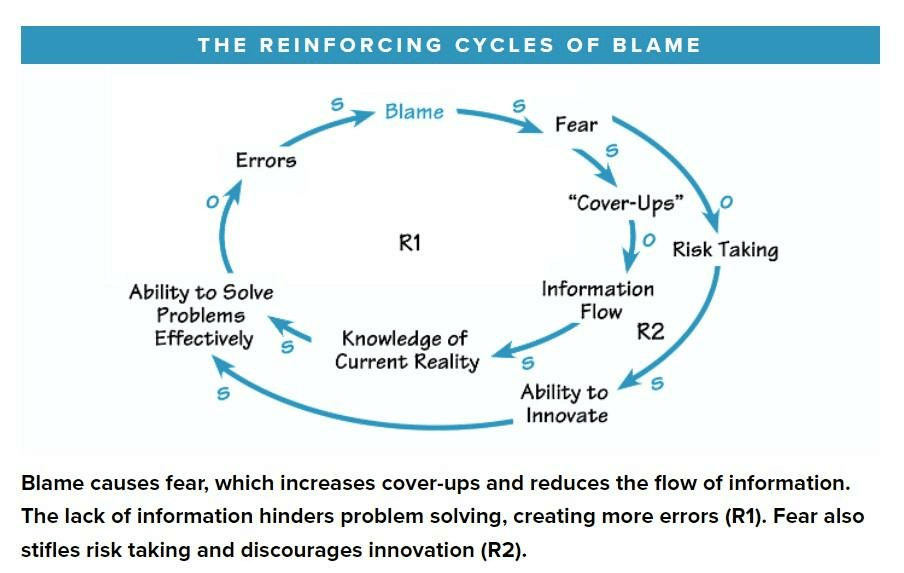
As you can see here, fear and restricted information do nothing but exacerbate the problem.
By encouraging effective problem-solving, which is only possible with full knowledge of the current reality, work teams are better able to find their way out of a toxic blame cycle.
Document All the Mistakes
Establishing a practice of daily reports helps create a safe work site.
Such reports can act as a checklist to ensure that safety procedures and other best practices are implemented. It provides a day-by-day diary of how the construction project is progressing.
Daily documentation can also help pinpoint trends that aren’t apparent until they are studied in aggregate.

As this quote indicates, documentation can seem frustrating or tedious, but it’s much easier and more accurate to document some problems when using an asset tracking solution with cloud storage.
These systems allow for instant communication and up-to-date information about equipment, such as maintenance issues, manufacturer warranties, and mechanical limitations.
All of this data is especially handy in the wake of a mistake on a construction site when confusion might temporarily stop workflow and acting fast makes a big difference.
If you use a strong template for a construction site’s daily report, it’s easier to add in a comprehensive account of a mistake.
Such templates can usually be found, ready-made, using online resources.
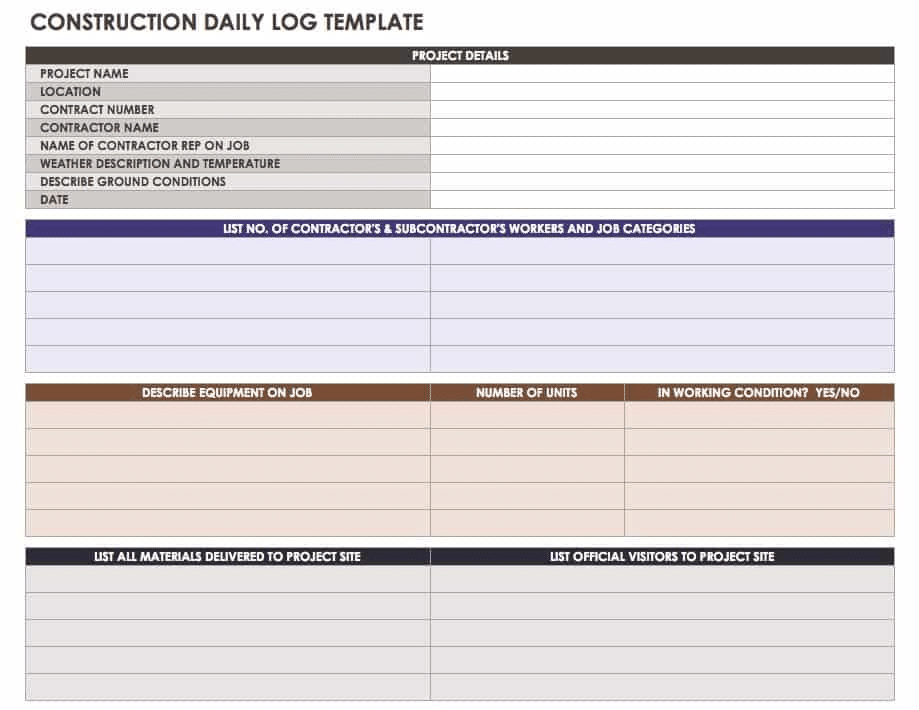
To adapt them to the needs of managing mistakes, consider including the following information in the error report:
- Date, time, and location of the incident
- Description of what happened according to as many witnesses as possible
- Names and contact information of the involved employees
- Equipment or material (if any) damaged or involved in the incident
- If the incident has taken place outside, describe the weather (temperature, precipitation, if heat warnings or wind advisories were in place, etc.)
- Risk incidents
- How the incident was reported
- Actions (if any) taken to remedy the situation
Errors that take place due to poor material or equipment handling can become opportunities to streamline workflows and minimize mistakes.
Since solutions such as GoCodes Asset Tracking allow the ability to create equipment reports quickly and easily, it’s easier to pinpoint weak links and faulty data processes.
Communicate the Mistake With the Staff
Good employees aren’t perfect, but they learn from mistakes and strive to apply feedback to result in better performance.
Sometimes that involves risk-taking, but that can also result in mistakes. To avoid falling into a blame cycle, as discussed earlier, communication is key.
This starts with good leadership.
This graphic summarizes important steps to take when you or someone in your organization has made a mistake.
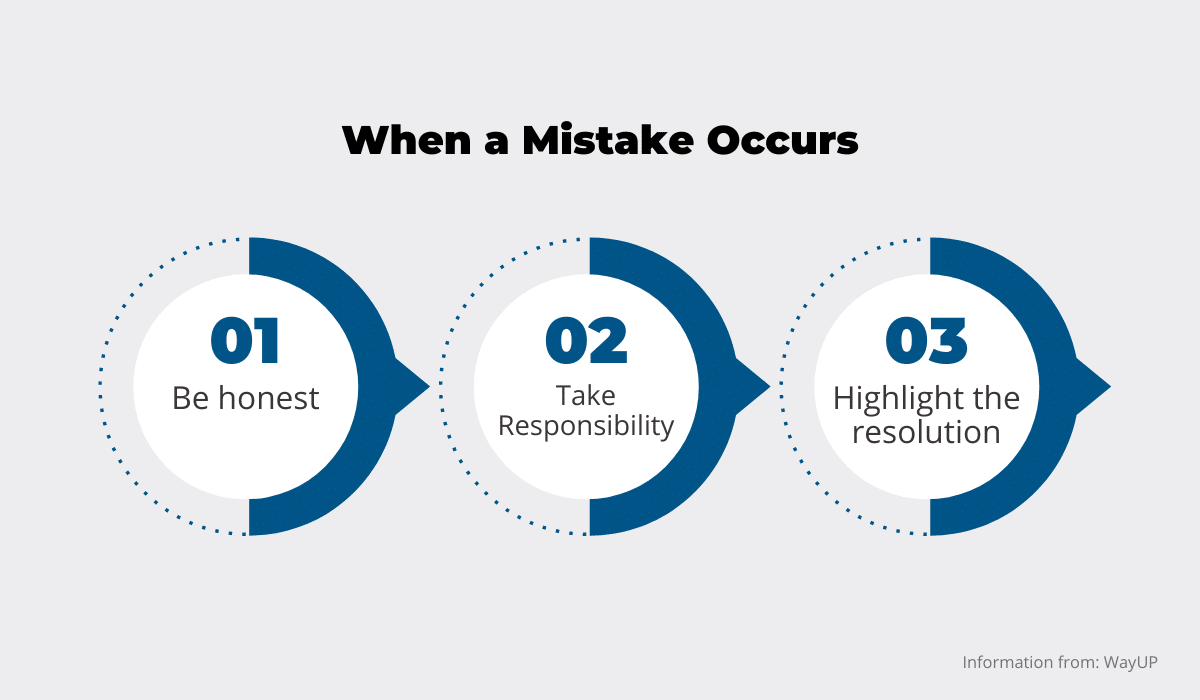
Note that the first item is honesty.
By fostering a healthy communication culture, employees will feel more comfortable with honestly reporting what has happened, and why.
This naturally leads to the proper parties taking responsibility for the mistake.
When this example is set at the highest level of decision-making, employees tend to feel more respected and more compelled to participate in a collaborative and open work environment.
Highlighting the resolution is a critical aspect of recovering from a mistake.
This ensures a forward-looking team ethos; allowing extended finger-pointing or recriminations does not allow the company to move forward.
A healthy attitude towards the mistake—confronting it head-on without wallowing is the balance to seek.
Finding ways to frame the event positively will help everyone to come to terms with the mistake.
However, while those affected should understand the circumstances of the error, sliding into excuse-making doesn’t help anyone. Aiming for authenticity can help to bring closure to a difficult moment.
Organize the Necessary Repairs
Arranging for repairs is perhaps the most difficult part of remedying a mistake on a construction site. It creates extra work and wreaks havoc with project deadlines and budgets.
However, the process of organizing repairs can serve as a reminder of the importance of maintaining a safe and efficient work site.
When organizing repairs, focus as closely as possible on the nature of the problem.
It is tempting to rush forward to avoid losing time on a project, but doing so might result in unnecessary expenses, not to mention creating an environment of chaos and stress on the site.
That, unfortunately, can lead to even more errors.
Rather than seeking to solve all problems at once, then, focus on the one at hand.
For example, if an employee has made a mistake with heavy equipment and this has resulted in damage to the roof of a project, your priority should be exactly what’s needed to repair the damage.
Assuming that your company doesn’t specialize in roof repair, you might need assistance from colleagues or subcontractors.
This graphic suggests the factors to keep in mind when budgeting for roof repair:
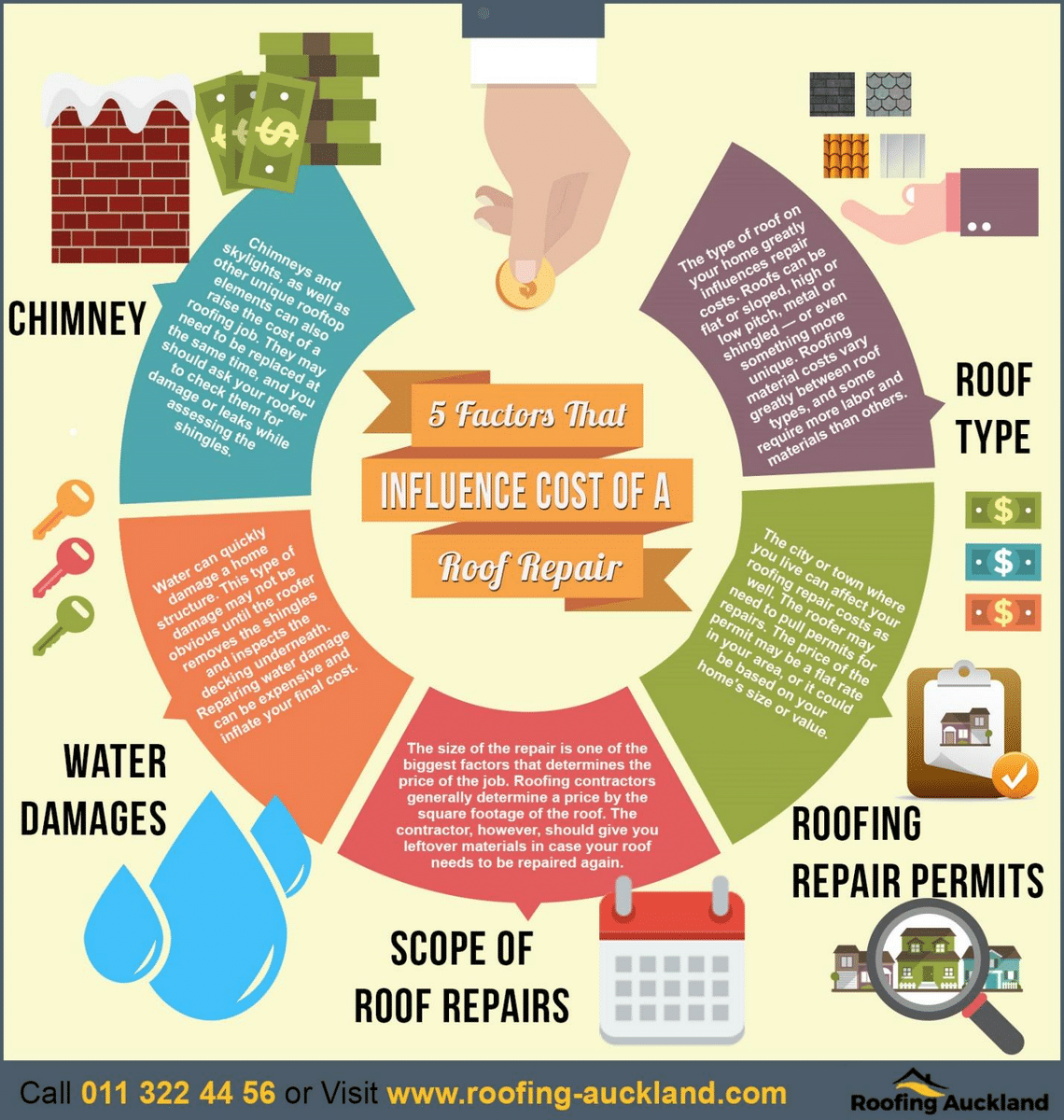
This process is easily repeatable for other types of damage.
Slowing down to take a full assessment of the situation after the damage has taken place is a key part of an effective recovery.
Perform Project Risk Assessment
Thinking about mistakes before a project begins its physical phase can help to avoid them. One way to do so is to form a risk matrix, as shown in this example:
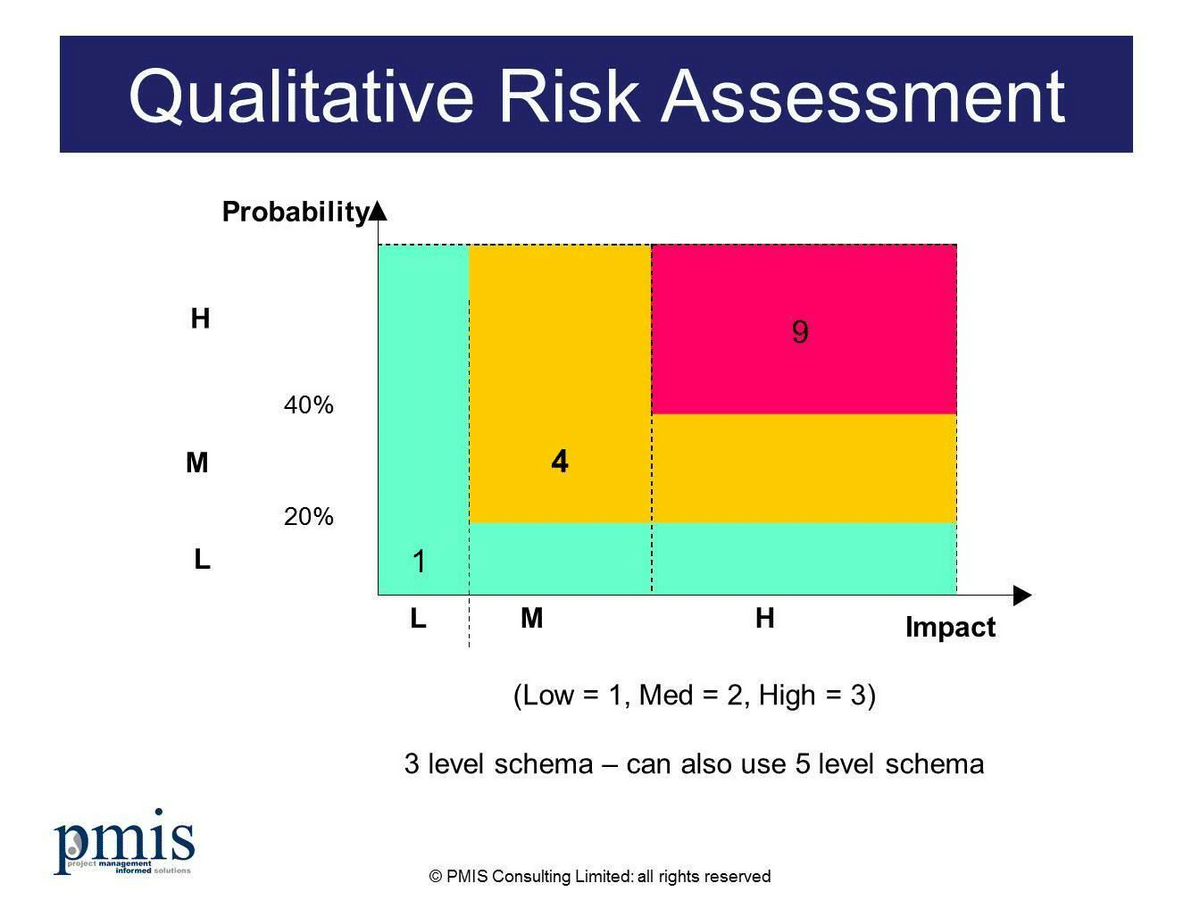
Once the risks on your site are identified, taking these steps will help mitigate them. This involves:
- Assessing risks
- Controlling risks
- Monitoring risks
Much of this comes from experience in how construction sites work and finding accurate, actionable ways to help your team negotiate these risks.
Some of the risks are beyond the control of your team (whether hazards, unknown quality of work sites, etc.), but others are knowable, and understanding their impact is the best way to face them.
The latter include:
- Common safety hazards
- Probable material availability
- Unclear contracts
- Conditions of change orders
- Estimates for labor or materials
Understanding these risks ahead helps avoid mistakes.
For example, if the project contract includes significant penalties to the client for submitting a change order, the possibility of receiving one drops, and your timeline is likely safer.
In the same way, it’s impossible to know what exactly the labor availability is for the duration of the project, but paying your team well and establishing a healthy work environment can go a long way to ensuring a consistent workforce.
In addition, effective safety training and ensuring that credentials are up to date lessens the possibility that negligence will result in a mistake.
Similarly, keeping track of your equipment’s preventive maintenance schedule with asset tracking helps to ensure that your fleet and tools remain in good repair.
In this, you can enlist the help of quality asset tracking software, such as GoCodes Asset Tracking.
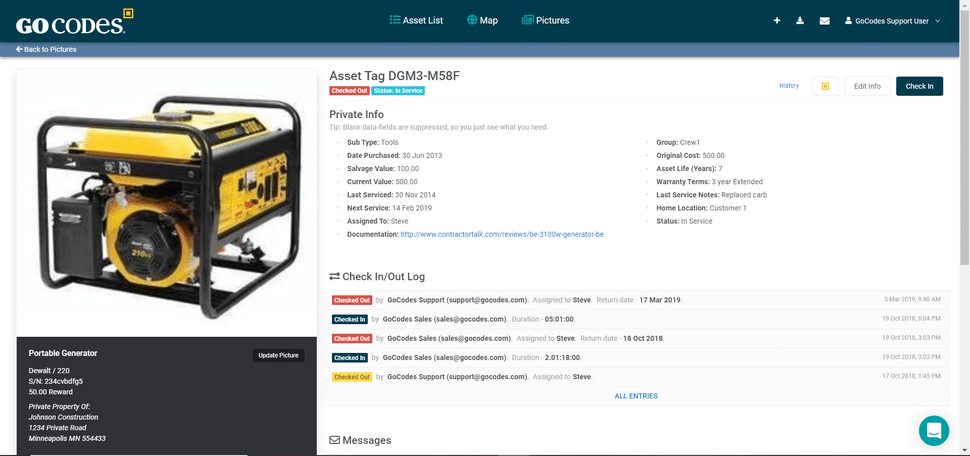
This kind of software will arm you with important information, such as service dates, reducing the possibility of mistakes caused by faulty equipment.
It will also show you a piece of equipment’s chain of custody so it’s much easier to assign responsibility in the event of human error.
Finally, since GoCodes Asset Tracking has inventory tracking capabilities, you’re less likely to encounter problems with material shortages on site.
By taking these steps to mitigate risk, your project is more likely to avoid major errors.
Conclusion
When a mistake happens on a construction site, it’s important to face it directly and as a professional.
By taking responsibility, documenting mistakes, and recognizing work or error patterns, it is possible to cut down on mistakes in the first place.
Communicating the mistake with the staff and organizing necessary repairs is an important part of the process, as is performing project risk assessments.