Key Takeaways
- Buying less expensive, lower-quality construction materials can cost more in the long run.
- Material management is a process that spans the entire project lifecycle.
- Material theft can be prevented with the right set of security measures and tools.
Construction material management is a complex process with many moving parts, so it’s no surprise that there are quite a few misconceptions about how to do it right.
But be careful: falling for these myths can lead to wasted resources, increased costs, and various operational disruptions.
That’s why the main objective of this article is to set the record straight.
In it, we’ll cover the five most common myths about material management and explain why they are unfounded—all backed by research and expert opinions.
Ready to rethink what you know about this important process?
Let’s get started.
In this article...
Construction Material Management Is About Procurement Only
While procurement certainly is a vital aspect of construction material management, it represents only the initial phase of the entire process.
That’s right: material management is a process, not a one-time task of buying materials.
In order to make the most out of it, you need to keep your eye on materials throughout the whole project lifecycle, handling tasks like:
- storage,
- transport,
- on-site distribution,
- stock level tracking, and
- waste management.
Neglecting even just one of these activities can have serious consequences, both for your operational efficiency and budget.
For example, inadequate storage can result in material damage or increase the risk of theft.
On the other hand, failing to track stock levels as the project progresses can lead to unexpected shortages in the middle of a job.
This further leads to unnecessary expenses and impedes the progress of your operations.
In fact, a 2022 survey by Cornerstone Projects has already shown that the second most common cause of project delays in construction is resource issues.
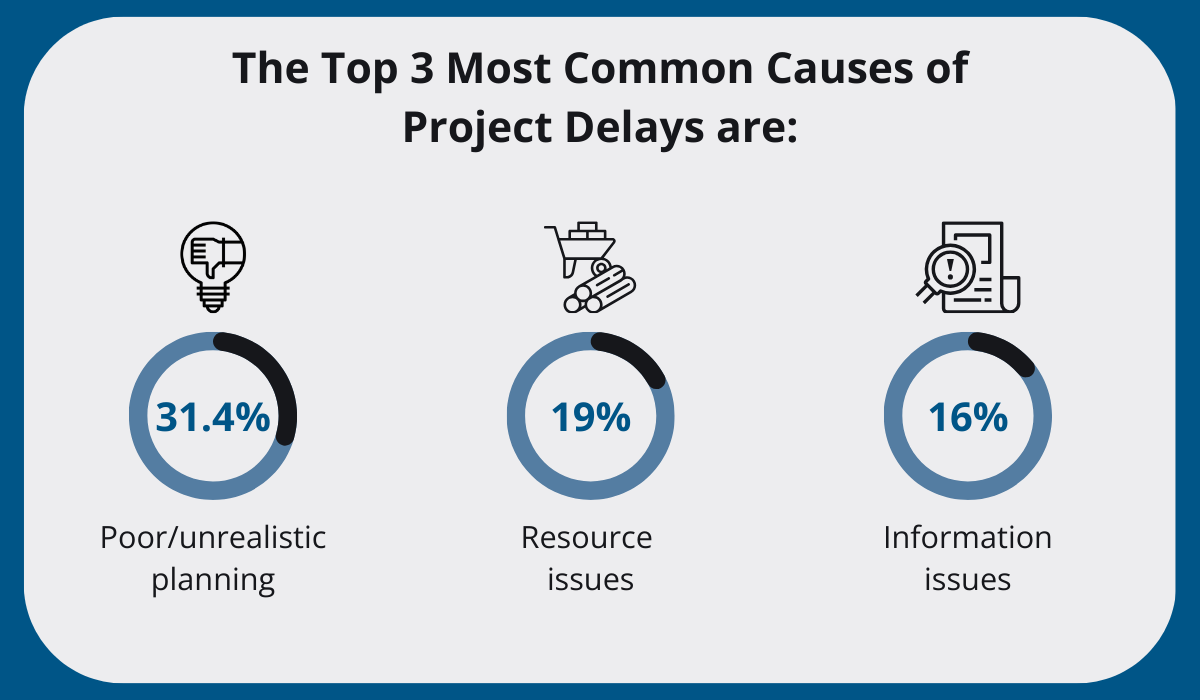
It makes sense: without labor, tools, or materials, you can’t really expect to get anything done on time.
And that’s exactly why you should always ensure your inventory is properly handled, stored, tracked, used, and discarded.
This is, simply put, the foundation of successful project completion.
Without proper material management, you’ll always be running into some kind of trouble.
The bottom line is this: thinking of purchasing as the entirety of material management when it’s just half the battle, is a very risky mistake.
Every experienced contractor and project manager understands that material control is a dynamic process that requires constant attention from a project’s start to finish.
Ordering Extra Materials Is Always Better
Given that material shortages are a common cause of project delays, it’s easy to see how ordering extra materials as a buffer might seem like an obvious solution to this problem.
However, that wouldn’t necessarily be the wisest choice.
These additional materials cost money, take up valuable space—which also costs money—and, worst of all, often end up being discarded.
Did you know that 13% of construction materials in the UK go straight to waste without ever being used?
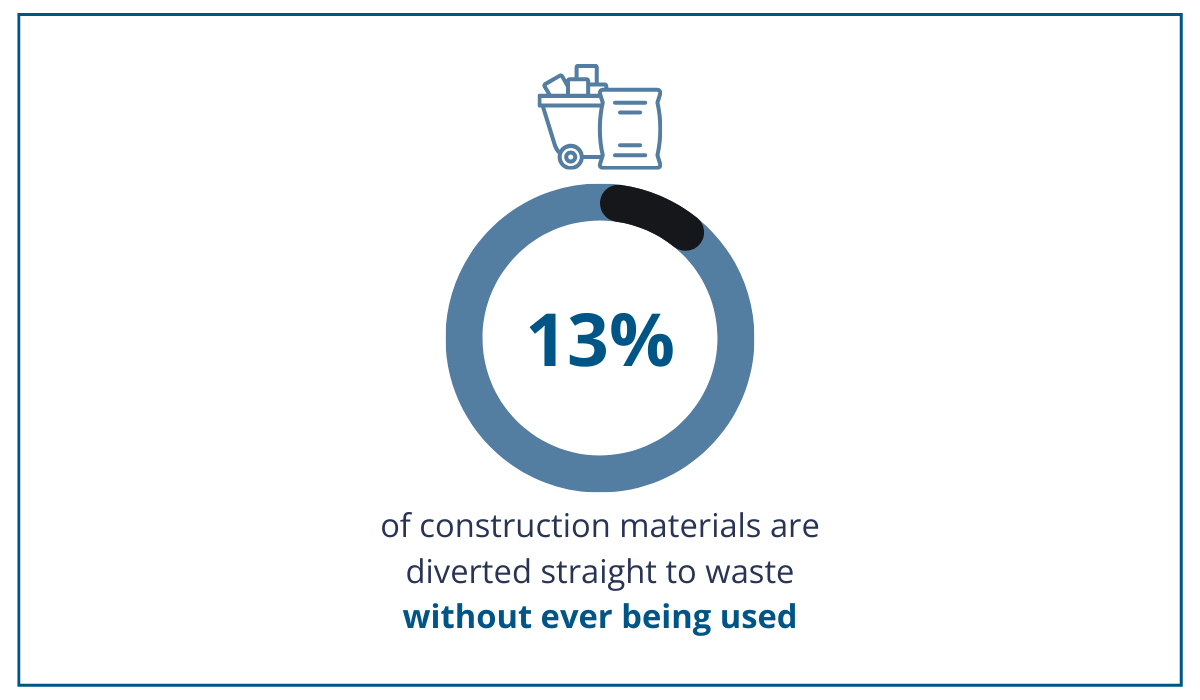
Imagine paying for all those items, finding space to store them, and then just throwing them away.
Not the best way to boost your profitability, right?
Especially when about a third of residential projects already struggle with staying on budget, demonstrating that the industry desperately needs smarter, more cost-effective ways to manage resources.
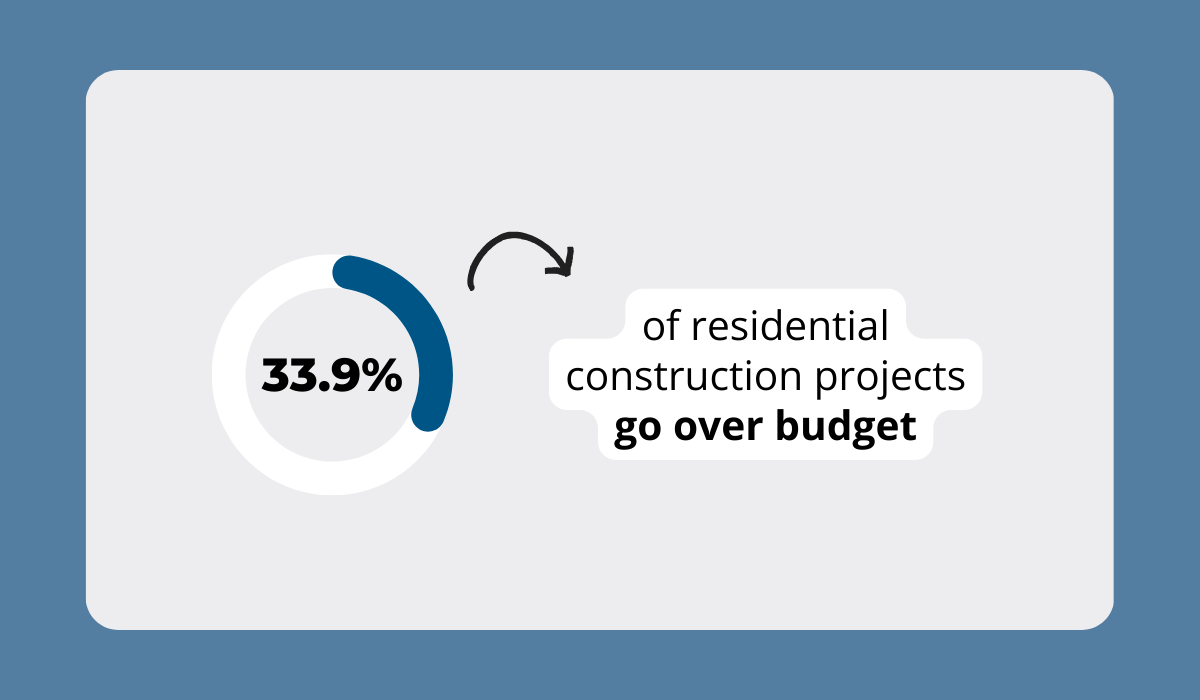
Because of this, we see many construction professionals shift from a “just in case” mentality to a “just in time” (JIT) system.
JIT inventory management involves accurately forecasting project requirements and timing deliveries so that products arrive right when they’re needed, rather than storing them for extended periods.
Furqan Ali, Civil Engineer Specialist at the project management platform Disperse, explains the perks of this approach:
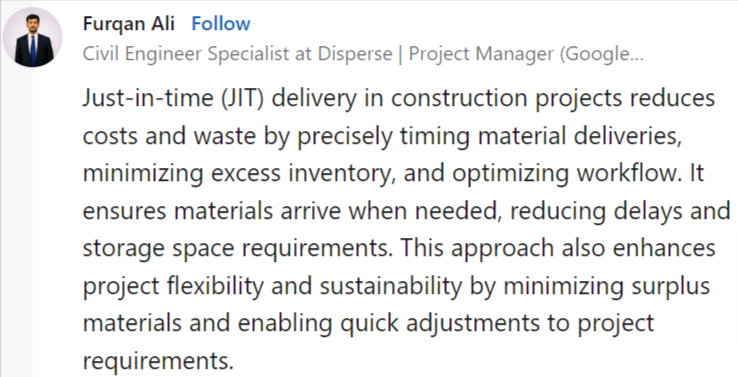
Of course, keeping a small amount of extra material as a contingency isn’t always a bad idea, but it’s important not to go overboard.
It’s all about that perfect balance between making the most profitable decisions and ensuring your workers have all they need to deliver high-quality work on time.
Material Theft Can’t Be Avoided
A seemingly never-ending stream of news articles and statistics about construction site theft could easily make anyone believe that this type of crime is simply inevitable.
For instance, a recent BauWatch survey shows that a startling 70% of construction workers have witnessed theft on-site at least once a year.
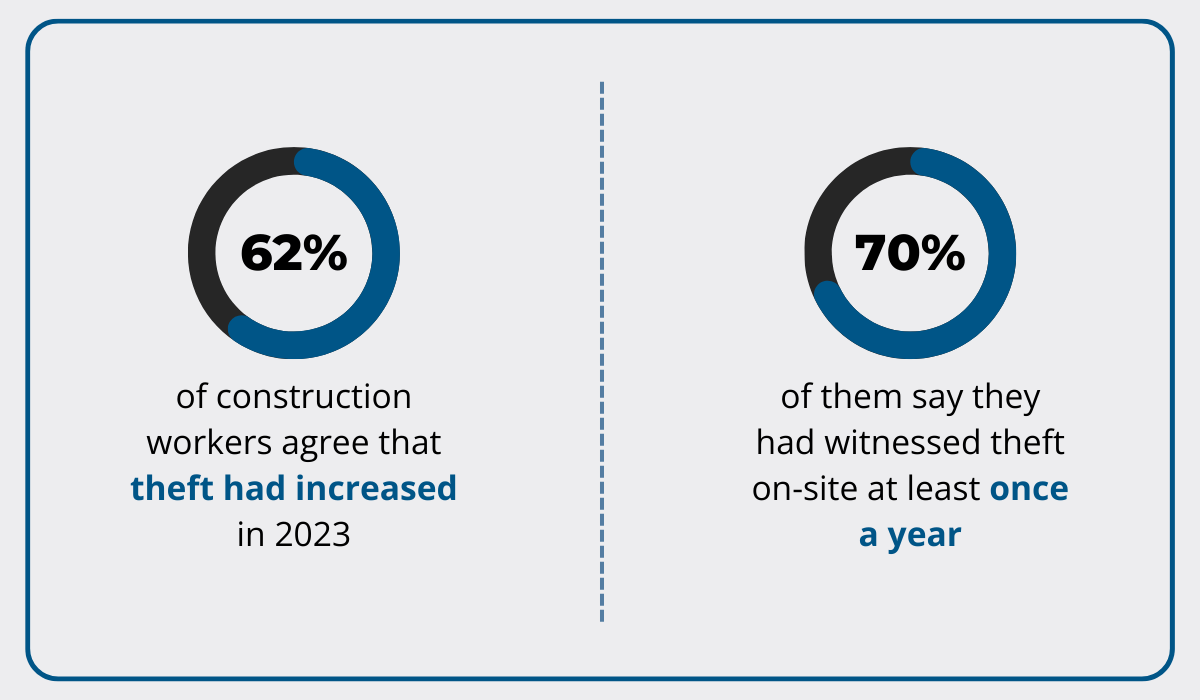
No wonder people are so pessimistic about the effectiveness of job site security.
However, the survey reveals another interesting fact: over a third of respondents say that job site security is a low priority where they work.
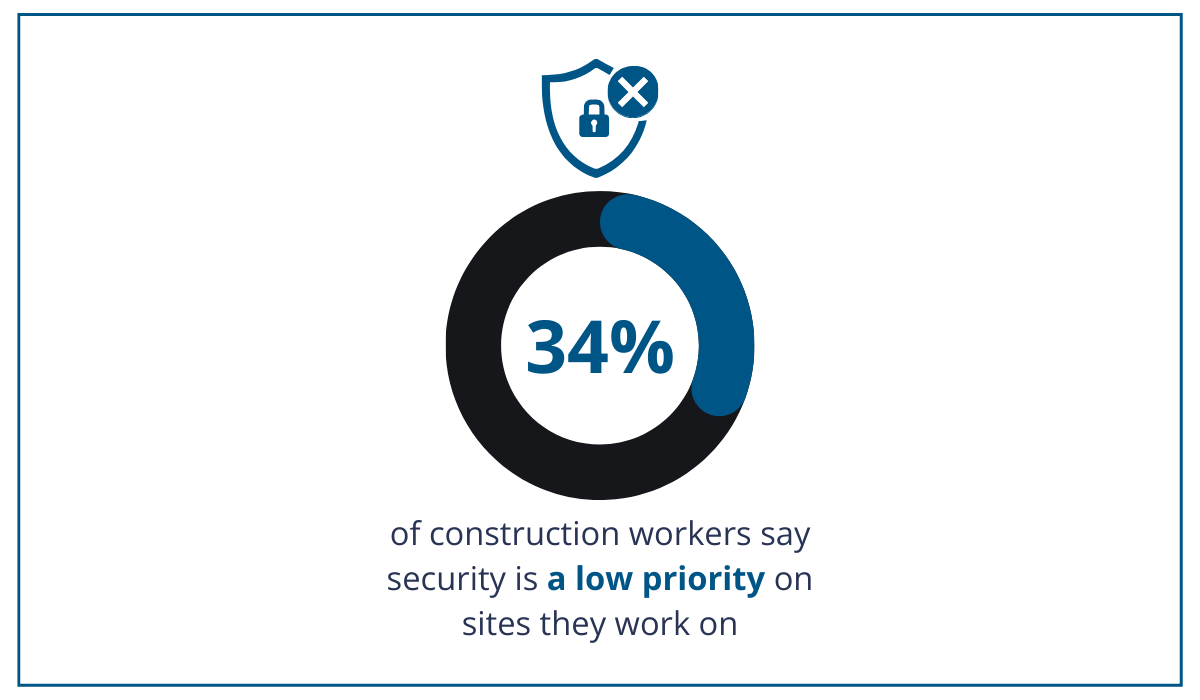
This raises the question:
Is construction theft actually unavoidable, or is the industry not taking the issue as seriously as it should?
In reality, theft can definitely be prevented—you just need the right set of tools.
And there are so many different tools available nowadays:
- Sturdy fencing around the perimeter
- Strict access control
- Motion detectors
- CCTV cameras
- Alarms
Besides, thanks to asset tracking software like GoCodes Asset Tracking, keeping a close eye on your materials has never been easier.
GoCodes Asset Tracking system consists of only three components—software, scanner app, and QR code asset labels—which makes it a user-friendly yet powerful anti-theft solution.
How so?
For starters, our tags act as a deterrent against thieves.
They clearly indicate that the item is being tracked and are quite difficult to remove, which might be more trouble than it’s worth for some robbers.
Second, in the event of theft, these labels help with stolen asset identification.
You can print anything you want on your GoCodes Asset Tracking tags, including your company name and other relevant details, which can then serve as proof of ownership.
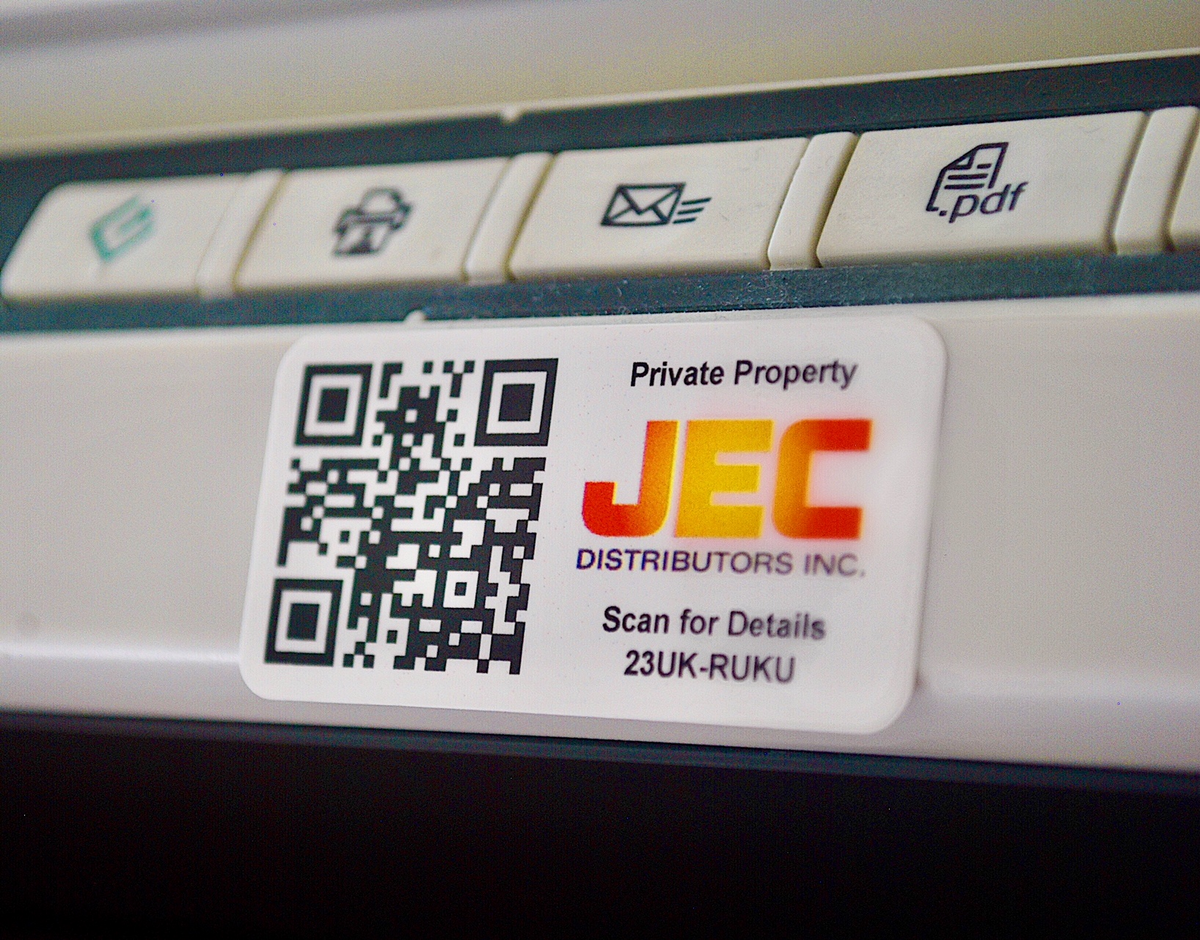
This means getting your missing items back much faster.
Lastly, the GoCodes Asset Tracking system simplifies the retrieval of stolen goods by showing the asset’s last known location.
How does that work exactly?
Whenever a worker uses a material, they scan the label attached to it using our mobile app. This allows them to view asset data, update its quantities, set up low-quantity alerts, and more.
At the same time, as soon as this simple action is performed, the item’s GPS location is automatically recorded.
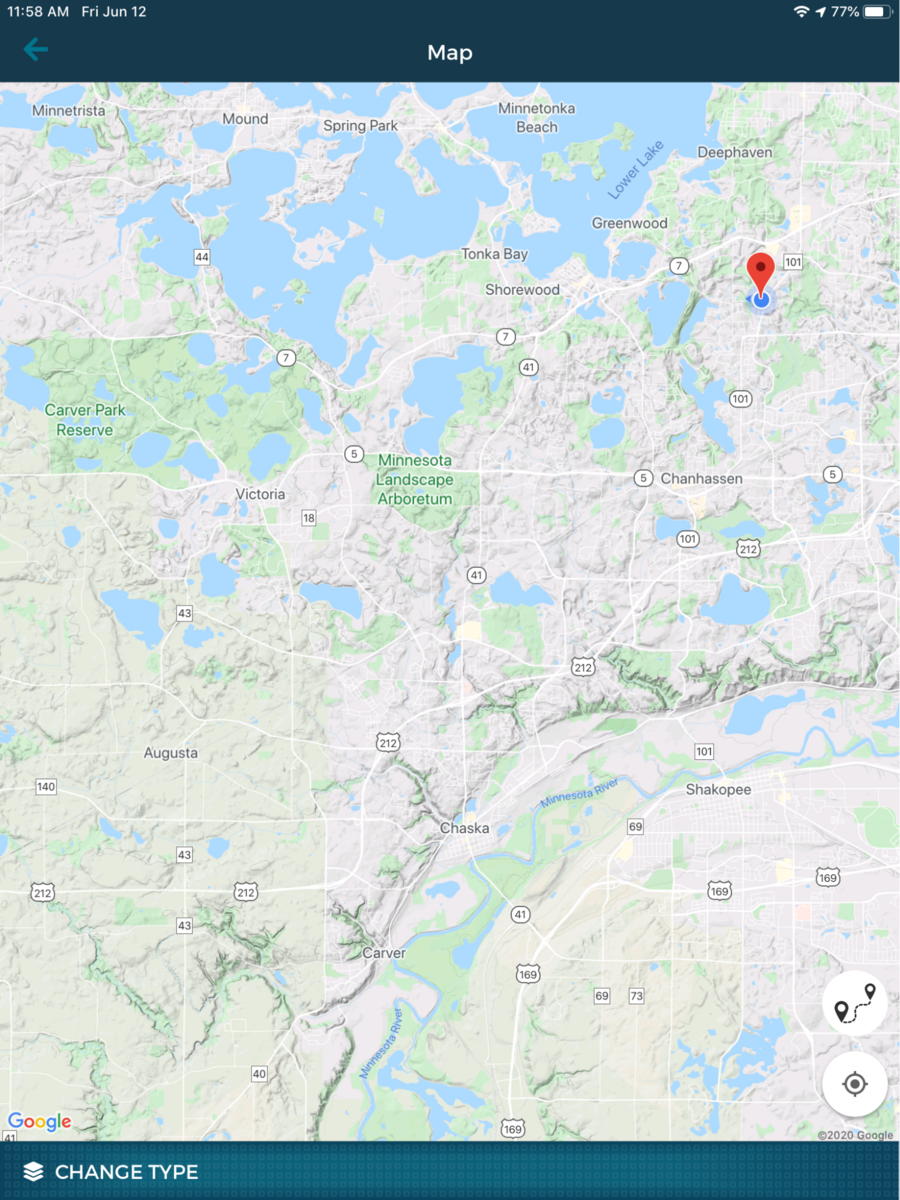
This kind of information can drastically increase the chances of your assets being found.
Another way how GoCodes Asset Tracking can help you prevent material theft is with geofencing.
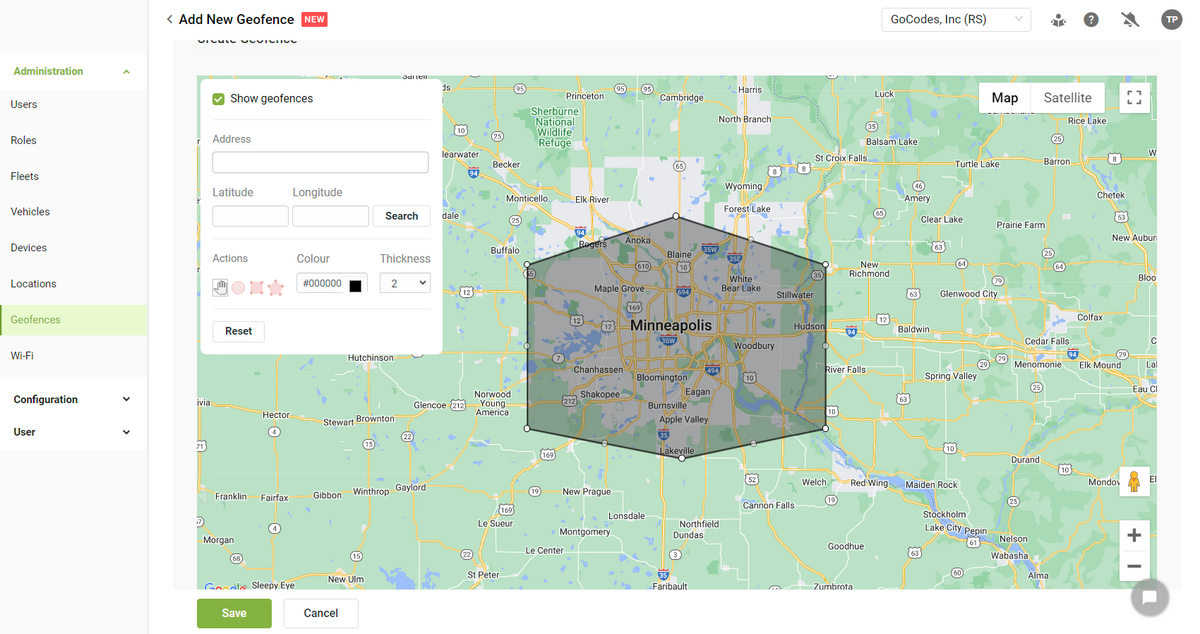
In short, you can set up a geofence around your construction site or a storage yard.
Then, whenever your material units that have GPS trackers on them are moved outside of it, GoCodes Asset Tracking alerts you so you can quickly take action.
The key takeaway?
While the threat of theft is real, there are still things you can do to mitigate such risks.
With the right technology and a proactive mentality, you can absolutely protect your valuable materials from thieves and keep your operations running smoothly.
Opting for Cheaper Materials Saves You Money
Delivering cost savings is one of the top priorities of material management and can be achieved in many different ways.
However, purchasing cheaper materials should never be your go-to solution in this context.
Remember, opting for less expensive, lower-quality products isn’t just an ineffective approach to saving money, but it also typically backfires because these items:
- Are less durable
- Are less sustainable
- Don’t come with a warranty
At the end of the day, the quality of your materials directly impacts the integrity of the entire building structure.
In other words, poor construction material equals poor building quality.
Just take a multistory building in Kolkata, India, which collapsed in 2024 after low-quality materials were used in an attempt to cut expenses.
An official from the Kolkata Municipal Corporation elaborates on the issue:
“Low-quality materials were being used to save costs. Casting is done with 10 mm rods instead of 16mm. They had kept 5,000 bricks loaded on top of the building which was unable to bear the weight and it collapsed.”
Similarly, buildings in rural Morocco aren’t able to withstand earthquakes due to, again, the use of cheaper materials in their construction.
And what about a house in Buckland, a residential community in Portsmouth, England, which collapsed due to poor-quality bricks, also triggering a partial collapse in the neighboring property?
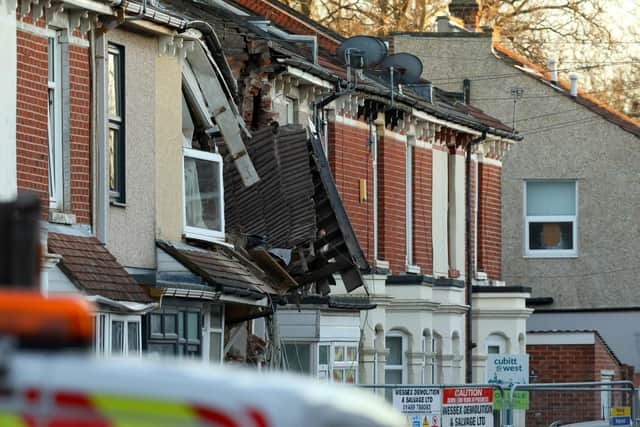
These stories are just the tip of the iceberg.
There are countless other examples of substandard materials leading to poorly built structures.
And the consequences are serious: safety risks, higher maintenance costs, and increased need for that dreaded rework.
Research from PlanRadar shows that rework can cost more than 11% of project costs.
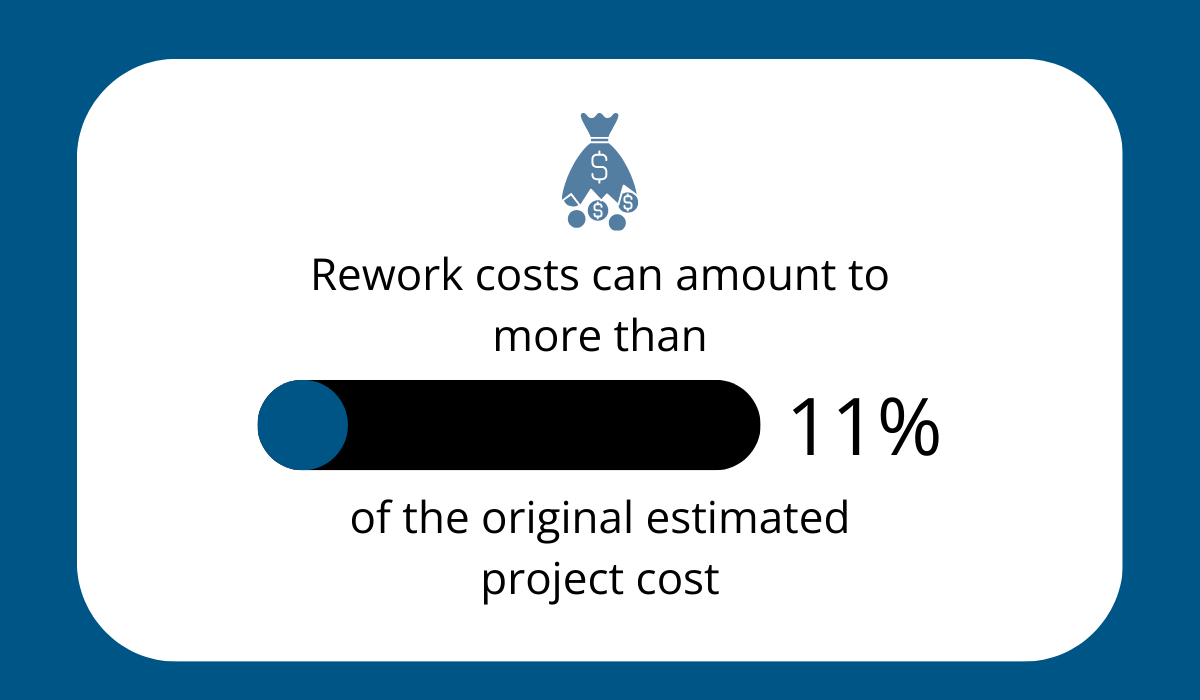
That’s a huge price to pay for a mistake that could have been avoided by choosing better materials from the start.
On top of this, there’s the reputational damage and the loss of future business opportunities that usually follow in these situations.
So, is saving a few bucks on materials really worth risking the safety, quality, and future of your projects?
Probably not.
Small Projects Don’t Need Material Management
Claiming that small projects don’t need material management is like saying they don’t need to reduce waste, cut costs, or ensure high-quality construction.
The truth is that any project, regardless of its size or complexity, can benefit from strategic material inventory allocation and control.
And here’s the thing: smaller projects don’t automatically mean less complexity.
Ryan McCracken, Project Executive at a construction engineering company DPR Construction, points this out:
“Smaller projects are not necessarily less complex, less difficult or less risky. But they do have a specialized set of priorities, requirements and challenges that go along with them. They’re different from large ground-up projects, but often we’re still doing almost the same scope of work in office buildings, hospitals, pharmaceutical or lab facilities, higher education campuses, hotels or data centers. We just do the work in a different way, on a different scale.”
They can be just as risky and challenging as larger ones, which means they can’t exactly afford to neglect this essential part of project management.
According to various sources, construction materials account for about 65-80% of project budgets.
Sure, small-scale projects may have fewer funds available, but we’re still talking about more than half of the overall project costs here.
In fact, an argument could be made that there’s even less room for error with smaller jobs.
With tighter budgets and schedules, contractors working on these projects need to be laser-focused on ensuring smooth, cost-effective operations.
And this is where material management plays a very large role.
At its core, material management is about securing those vital “5 Rs”:
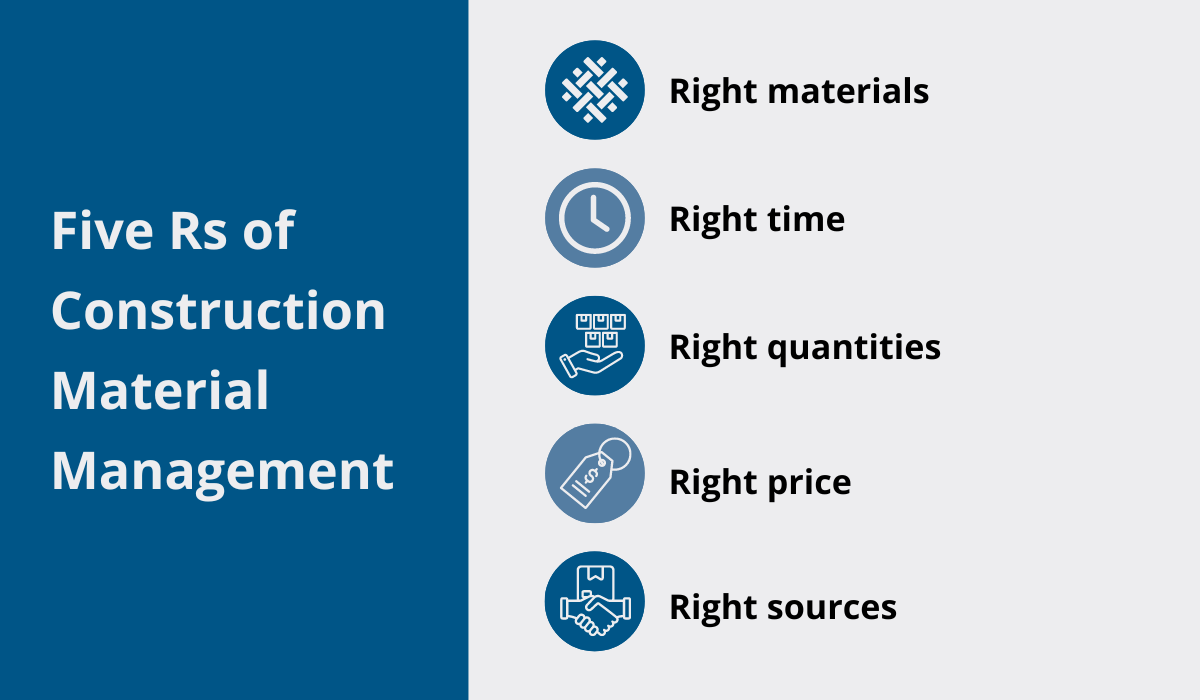
And those principles are important for any job, no matter how large or small.
They are the foundation for timely project completion, effective cost control, high quality, and, ultimately, client satisfaction.
Conclusion
If there’s one thing you should take away from this article, it’s that there is no one-size-fits-all solution for efficient material management.
Be wary of anyone who insists that you must always do things a certain way or that some challenges, like theft, are just part of the game in this industry.
In truth, every project is different, and the key to success lies in understanding those unique needs, planning strategically, and keeping a close watch on your materials throughout the project’s lifecycle.
That’s how you truly minimize risk and ensure timely project completion.