Managing inventory in the construction industry poses several challenges that significantly impact project timelines, costs, and overall efficiency.
Are you grappling with missing inventory, facing challenges coordinating inventory across multiple construction sites, or encountering discrepancies between your records and actual stock levels?
These are the everyday battles construction companies face with inventory management.
And today, we will address them all.
But not without offering insights and strategies to help you tackle these challenges head-on.
Buckle up, and let’s dive right into the challenges—and the solutions.
In this article...
Accurately Forecasting Inventory Needs
Forecasting inventory needs is crucial for construction projects, but it’s easier said than done.
You might find yourself in a bind if you underestimate your needs—delays and extra costs are almost guaranteed.
On the flip side, overestimating leads to a different set of problems, like excess inventory gathering dust—what we call dead stock.
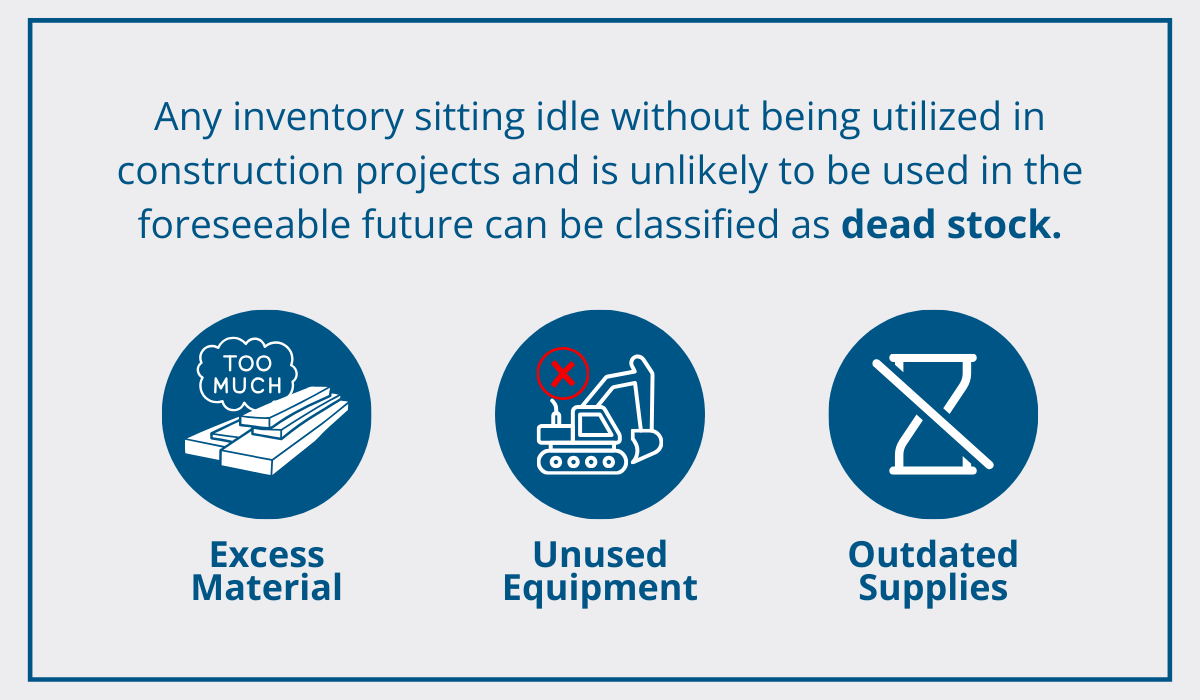
However, dead stock is more than just a nuisance. It’s also a drain on the construction company’s resources.
Dead stock ties up capital that could be better spent elsewhere in your business, and storing it eats into your budget with space, maintenance, and security costs.
Moreover, dead stock is an environmental hazard, too.
Unused materials contribute to construction waste, piling up in landfills and straining natural resources.
Disposing of them adds to emissions and worsens the construction industry’s carbon footprint, which is a growing concern in today’s environmentally conscious world.
So, what’s the solution to avoid both understocking and overstocking? Getting better at predicting and forecasting your inventory needs.
Start with your historical data—it’s a goldmine of information on past usage and trends.
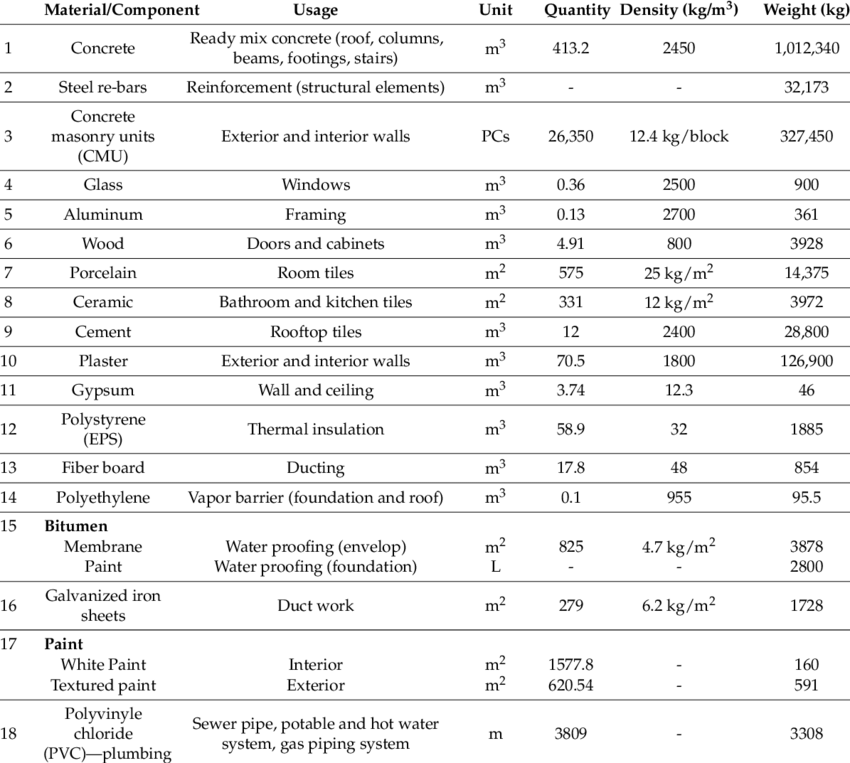
Combine your past projects’ inventory data with your project schedules and apply demand forecasting techniques tailored to your industry.
One such technique is time-series analysis, where you analyze your past data to identify patterns and trends over time.
For example, you can look at previous project timelines, seasonal variations, or market trends to forecast future demand more accurately.
Let’s say you’re planning a construction project in a region that experiences harsh winters.
By analyzing past data, you notice that construction activity slows down during the winter months due to weather conditions.
You can adjust your inventory forecasts accordingly, ensuring you have enough materials on hand to meet demand during peak construction seasons while avoiding excess inventory during slower periods.
It goes without saying that you should regularly review and adjust your forecasts as your projects progress and requirements change.
Flexibility is key here, and staying nimble allows you to adapt to unforeseen circumstances and avoid shortages or excess inventory.
Mismatch Between Physical Inventory and Records
If you want your inventory management to be as effective as possible, you have to maintain accurate inventory records.
If that’s not the case, inaccuracies in inventory can lead to overstocking, stockouts, and increased costs.
But why do mismatches between physical inventory and records occur in the first place?
According to James Prior, Pre-sales and Sales Ops Manager at Tryon Solutions, a company providing supply chain execution solutions, the reasons are the following:
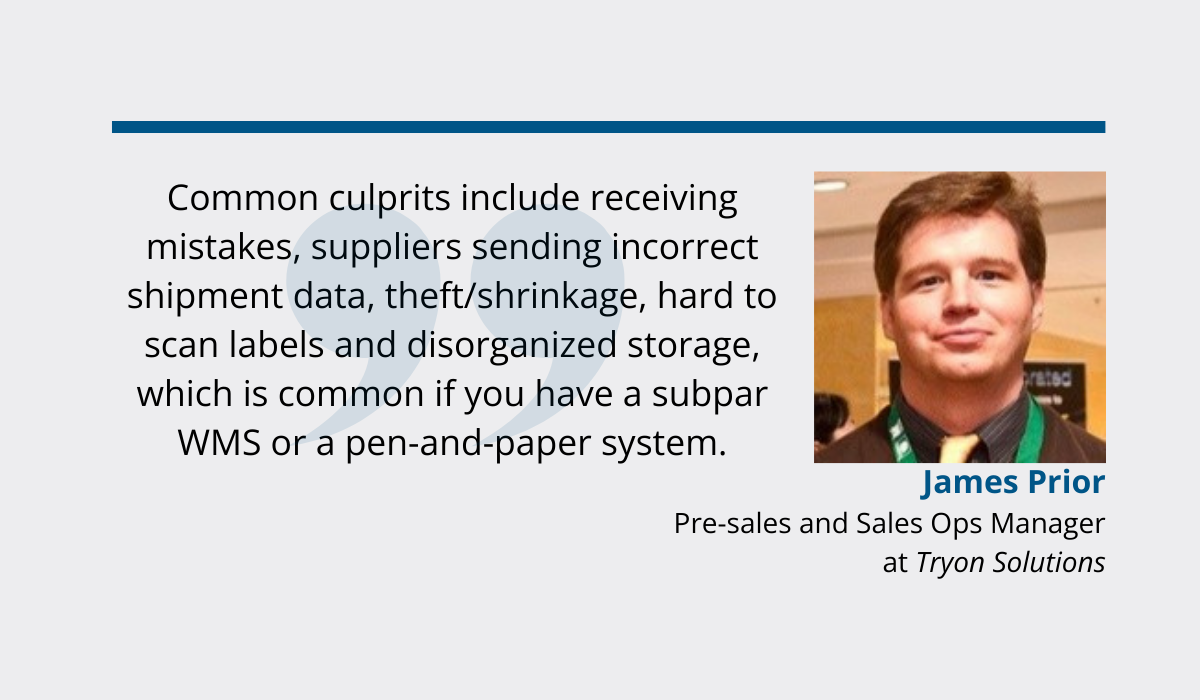
One solution to address the challenge of mismatched inventory is to conduct regular physical inventory counts and reconcile them with inventory records.
However, construction companies make one more common inventory management mistake here—conducting these counts only once a year.
This practice can be detrimental, as it may result in discrepancies going unnoticed for longer periods.
This then leads to inaccurate inventory management decisions and increased risk of stockouts or overstocking.
Another factor contributing to mismatches between physical inventory and records is the complexity of construction projects.
With multiple sites, diverse materials, and dynamic project timelines, it’s easy for inventory records to become outdated or inaccurate.
Changes in project scope, unexpected delays, and variations in material requirements further complicate inventory management, increasing the likelihood of discrepancies between physical inventory and records.
To address both of these challenges, you can implement cycle counting procedures to continuously monitor inventory levels and address any mismatch in time.
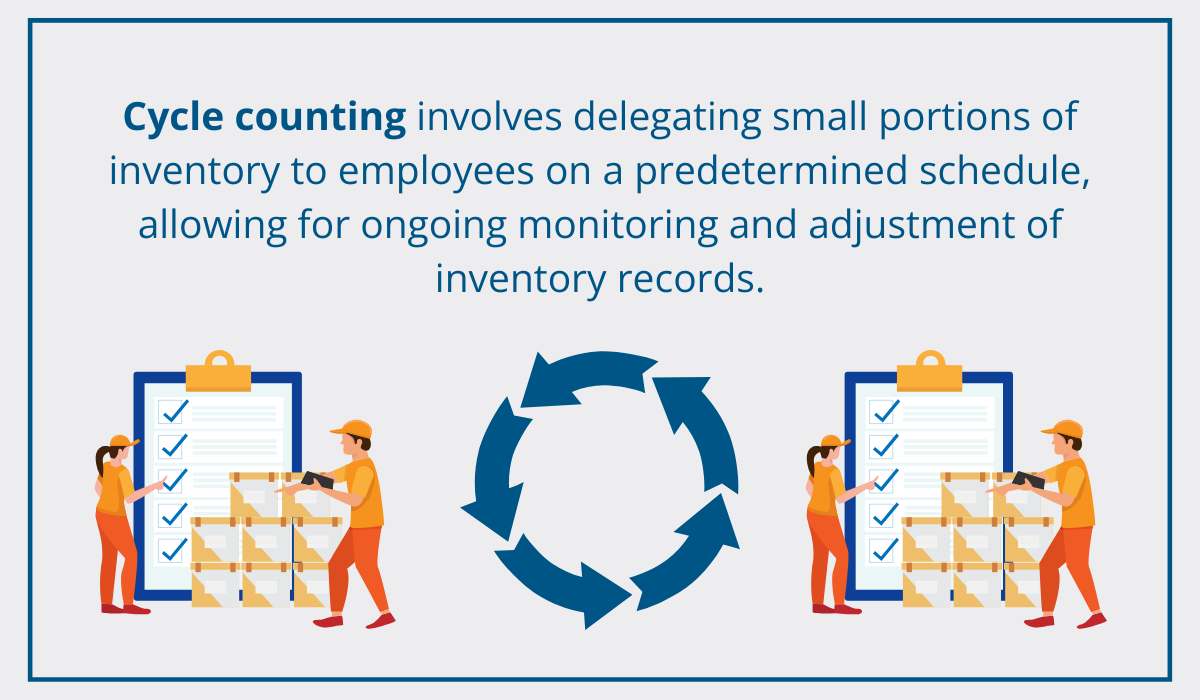
This minimizes disruption to warehouse operations and reduces the risk of errors associated with conducting full physical counts at once.
All in all, when you adopt cycle counting procedures, you can more easily match your physical inventory and records, thus reducing the risk of stockouts or overstocking and enhancing overall operational efficiency in your construction projects.
Tracking Inventory Across Multiple Job Sites
Tracking inventory across multiple job sites can be a herculean task, and the consequences of being unable to overcome this challenge are also severe.
When you lack visibility into the materials and tools at each construction site, you face issues such as delays and wasted time searching for materials or tools that, in the end, are not there.
This, then, results in workers idling at the construction site.
When you multiply all these problems, delays, and extra costs with the number of construction sites you operate on, it’s clear that you need to improve your inventory tracking game.
Another key challenge we must address at this point is the manual nature of inventory tracking, which often relies on error-prone spreadsheets or paper-based systems.
When you manually track your inventory across multiple sites, you can’t have real-time visibility.
Namely, without real-time visibility into inventory levels, companies struggle to allocate materials efficiently.
This leads to order duplication or material misplacement, and risks of delays or critical shortages are also way too common.
Fortunately, there is a solution for all the above—a centralized inventory management software to both track and manage your inventory.
Such systems usually leverage technologies such as barcode scanning or RFID, which help you record inventory movement and usage in real time, ensuring that your inventory levels are continuously updated.
For example, our asset tracking software, GoCodes Asset Tracking, is one such user-friendly and cost-effective solution for tracking inventory across multiple job sites.
GoCodes Asset Tracking comes with QR code labels that you attach to your inventory items, which you can then scan with a scanner or, even simpler, through a GoCodes Asset Tracking mobile app.
This way, you always know where your inventory is and can maintain a comprehensive inventory register.
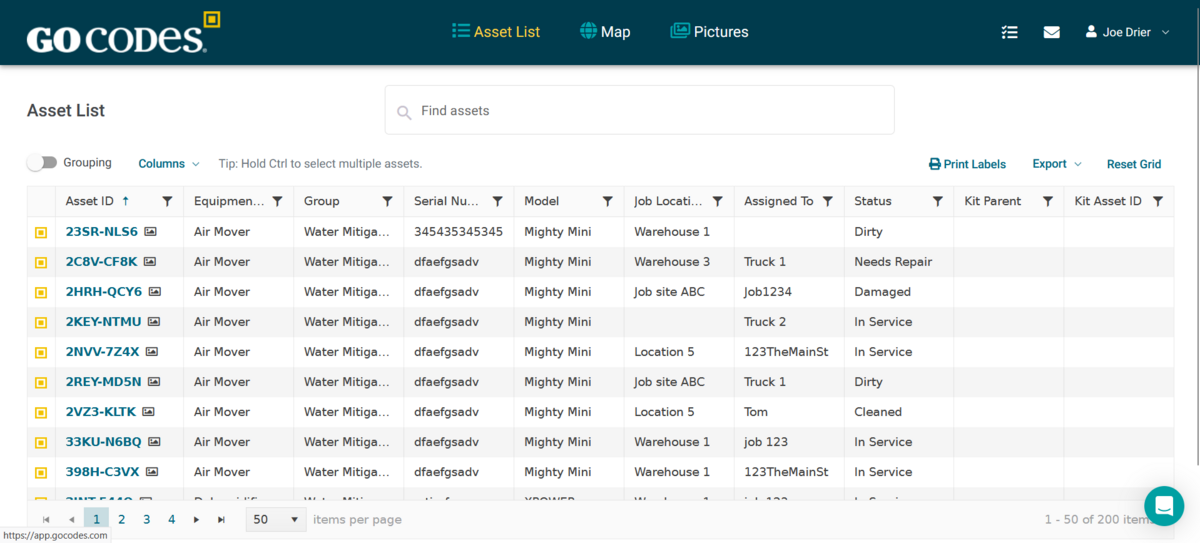
The latter is essential to ensure tools, materials, and equipment are on the sites where and when they need to be, as well as to reduce idle time and minimize delays or inventory shortages.
The key takeaway is this: a centralized inventory management system with advanced tracking technologies is essential for effectively managing inventory across multiple job sites.
Only then will you improve visibility, accuracy, and efficiency in inventory tracking and, ultimately, enhance everyone’s productivity.
Handling Supply Chain Disruptions
Dealing with supply chain disruptions is another significant challenge for construction companies.
Since your projects rely heavily on a steady stream of materials, any disruptions—due to weather, transportation issues, or manufacturing delays—can severely impact your project timelines and budgets.
For instance, construction projects in Nashville faced significant delays attributed to supply chain issues, particularly the availability of transformers, explained David McGowan, president of Regent Homes.
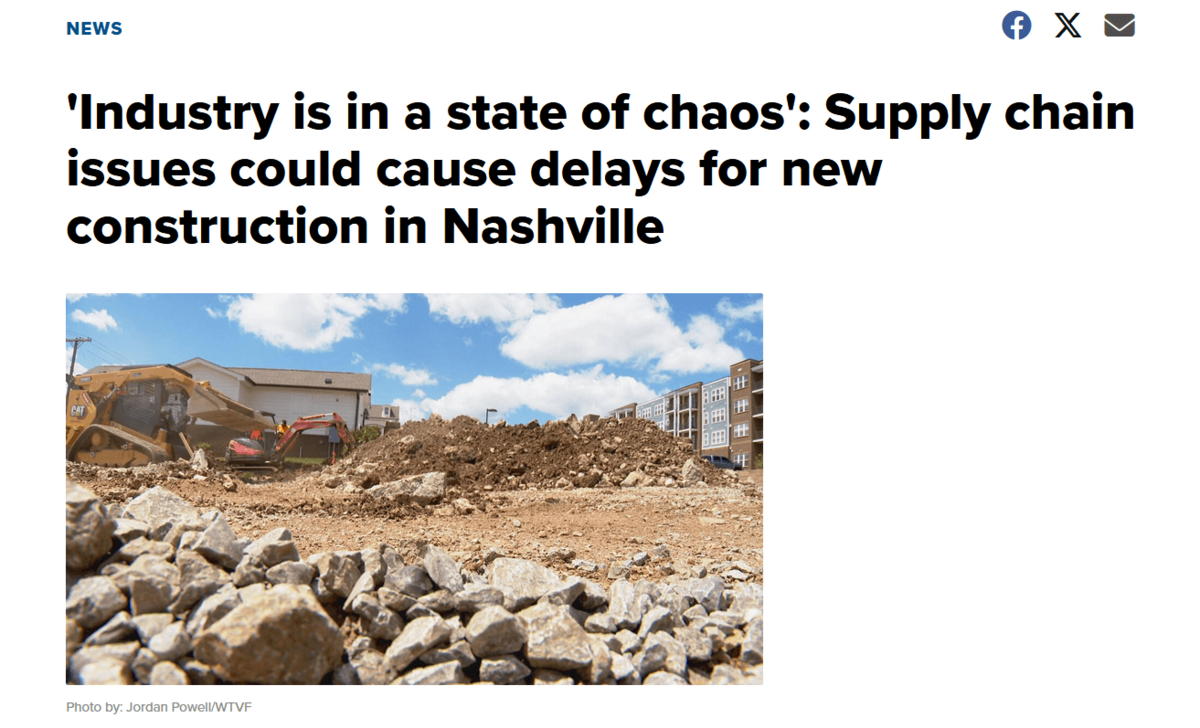
NES, the local electric service provider, faced challenges due to labor shortages and raw material supply issues worsened by the pandemic and recent natural disasters.
These shortages directly affected companies like Regent Homes, leading to delays in projects because of the inability to power buildings and complete construction.
One effective solution to better handle such disruptions is to diversify your supplier base.
By sourcing materials from multiple suppliers, you can mitigate the risk of disruptions from a single source.
This strategy helps ensure that you have alternative options available if one supplier faces challenges or delays.
Additionally, it’s crucial to maintain a list of reliable suppliers that is regularly updated.
You can see an example of such a list in the image below:
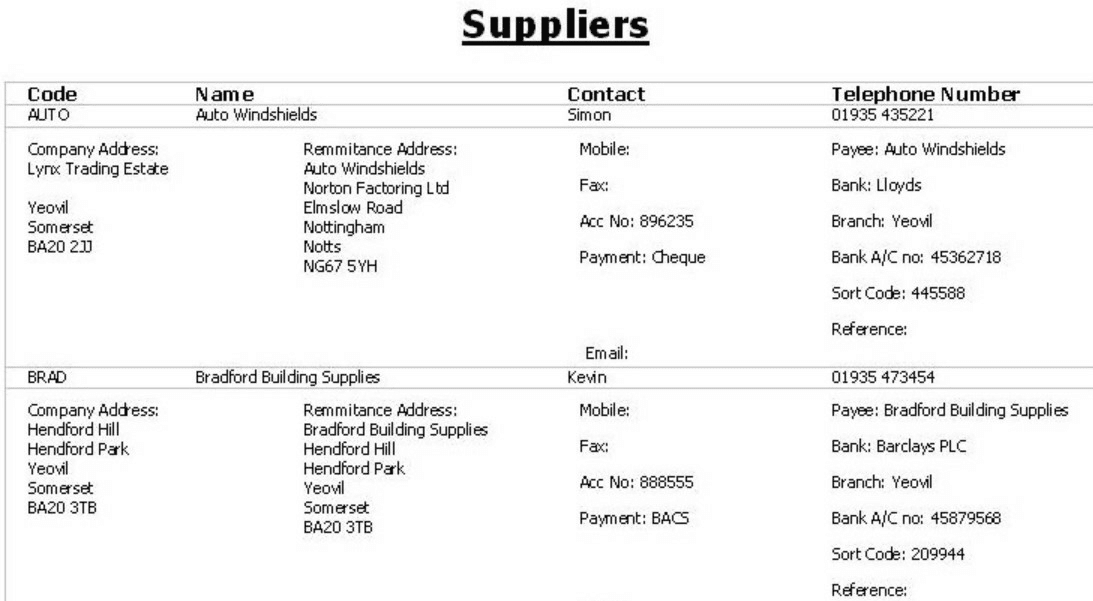
Having a roster of trusted suppliers allows you to quickly pivot and procure materials from alternative sources when needed.
Finally, maintaining open communication with suppliers is essential to handle supply chain disruptions.
By fostering transparent and collaborative relationships with your suppliers, you can stay informed about potential challenges or delays in the supply chain.
This can also help anticipate disruptions and implement contingency plans to address them effectively.
While supply chain disruptions are inevitable in the construction industry, diversifying your supplier base, maintaining a list of reliable suppliers, and fostering open communication with them are key strategies to mitigate the impact of disruptions on your projects and overcome this challenge.
Preventing Inventory Loss and Theft
Construction sites are, unfortunately, vulnerable to theft and loss of materials, equipment, and tools, which can severely disrupt efforts to effectively manage construction inventory.
For example, $40,000 worth of tools were stolen from a construction site on the north side of the UC Berkeley campus.
And this is not an isolated incident.
But it’s not just about tools and materials.
It’s also about costly equipment, as Billy Porter, director of risk management at Cable East Inc., a telecommunications construction company based in northeast Georgia, explains:
“We often have a half-million dollars of equipment spending the night on job sites. That’s the nature of what we do.”
This company uses various types of heavy equipment, such as excavators and specialized drills, that weigh tons and cost up to $750,000.
Unfortunately, this is a tempting target for thieves.
However, as technology advances, there are more and more solutions available to prevent inventory loss and theft.
Security measures such as fencing, surveillance cameras, and access control systems can deter theft on construction sites.
Sometimes, all you need is good asset tracking software like our GoCodes Asset Tracking, which works through real-time GPS tracking.
With GoCodes Asset Tracking, you can mark inventory items like costly equipment and set geofences around designated areas.
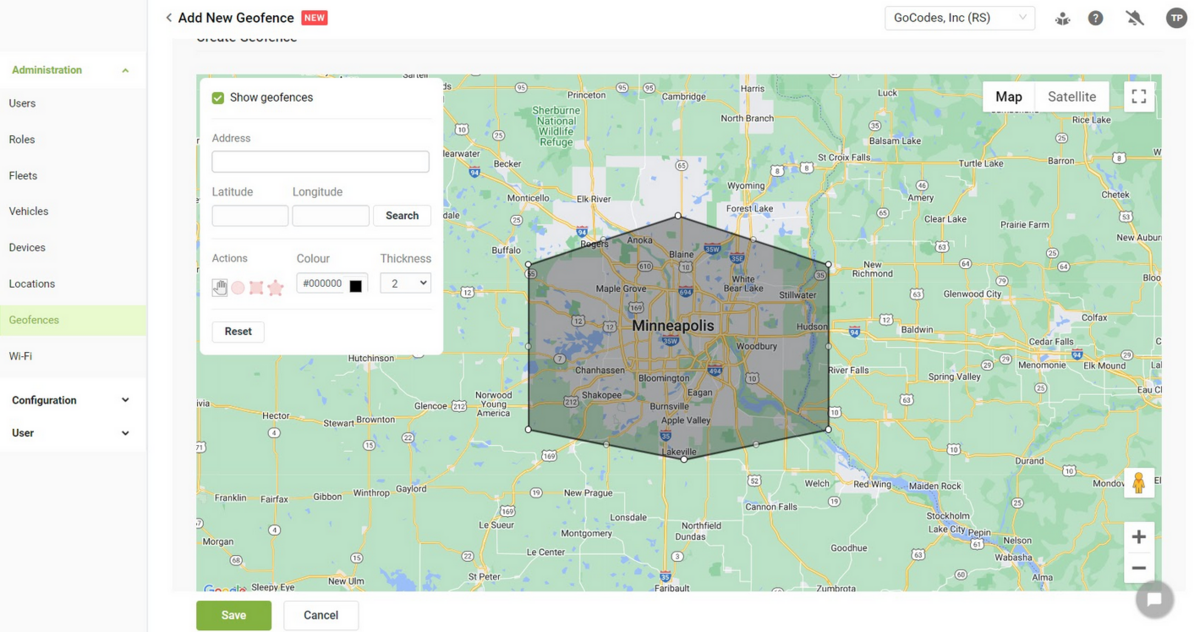
If the asset moves outside of the defined zone, you receive real-time notifications, and you can take immediate action.
Cable East estimates that using a similar system with GPS tracking for inventory has saved them $2.5 million through successful equipment recovery.
Porter explains how it works:
“We’ve been able to track the assets on GPS and notify law enforcement. They secure the scene and we’re able, in real time, to provide our folks with everything they need, from bill of sale to title, to substantiate our ownership.”
In addition to technological solutions, conducting regular inventory audits will also help you identify missing items.
As you can see, inventory theft and loss don’t have to be your construction site’s reality. That is—if you use some of the solutions we mentioned.
Conclusion
Indeed, managing construction inventory presents a myriad of challenges—from tracking inventory across multiple locations to handling supply chain disruptions and forecasting inaccuracies.
However, all these can be overcome.
Most often, the right solution is adopting a centralized system for real-time inventory tracking, monitoring, and management.
Equipped with such a tool, you ensure that your inventory is always in the right place, at the right time, and in the correct quantities.
And you understand better than anyone that this is the only recipe for completing construction projects on time, within budget, and to the satisfaction of all stakeholders.
As we conclude, we hope that the insights shared today will empower you to address these challenges in your construction company—and start overcoming them.
Best of luck!