The assets belonging to construction companies are usually different from those in other service-oriented industries.
Many items necessary in construction, such as large machines, are hugely expensive and yet must stay outside in the elements.
The items move from place to place as they are needed.
At the same time, the company might also own replacement parts, office supplies, and technological items, such as desktop computers, that do not leave the central hub.
Construction companies must manage all of these items in addition to organizing employees, working with third-party contractors, and seeing to marketing. This can quickly become taxing.
Although the specific items may differ, most can benefit from the five asset management tips for construction companies we’re going to cover in this article.
Let’s dive in.
In this article...
Keep a Detailed Register
Construction companies should keep a detailed and accurate register of each asset. This kind of database stores data that proves invaluable in the event of loss or theft.
It is also useful for determining when the item has reached the end of its life cycle.
The asset register should show at least some of the following information for each item:
- Date of purchase
- Cost of purchase
- Contact information for the seller
- Warranty information
- Maintenance records
- How the item is performing
- Repair history
- Location (either current or when the item is stored in a warehouse)
Properly conducted registers contain a great many items, and it’s extremely difficult to maintain control of them manually.
Because of this, using a robust asset tracking solution such as GoCodes Asset Tracking can greatly reduce the uncertainty and massive workload usually associated with these records.
With an asset tracking software solution in place, register items update automatically.
They offer accurate and shareable information with a simple scan using familiar technology, and since the data is stored in the cloud, it is immediately accessible to any employee authorized to access it.
It might seem daunting to collect all this information on assets already in hand, but consider the many benefits of keeping such a register:
- Ensuring business viability
- Staying on top of statutory requirements
- Keeping track of the asset and ensuring it’s secure
- Tracking gross book and net value
- Calculating the repairs and maintenance cost
- Estimating future capital investment
- Conducting business valuations
What is more, manual registers are susceptible to theft or damage. The data is by no means secure and requires money and employee attention to store and organize.
However, asset tracking helps you monitor thousands of items in real time, and all information is securely maintained online.
Calculate Asset Depreciation
Depreciation represents the decline of an asset’s value over time, or put differently:
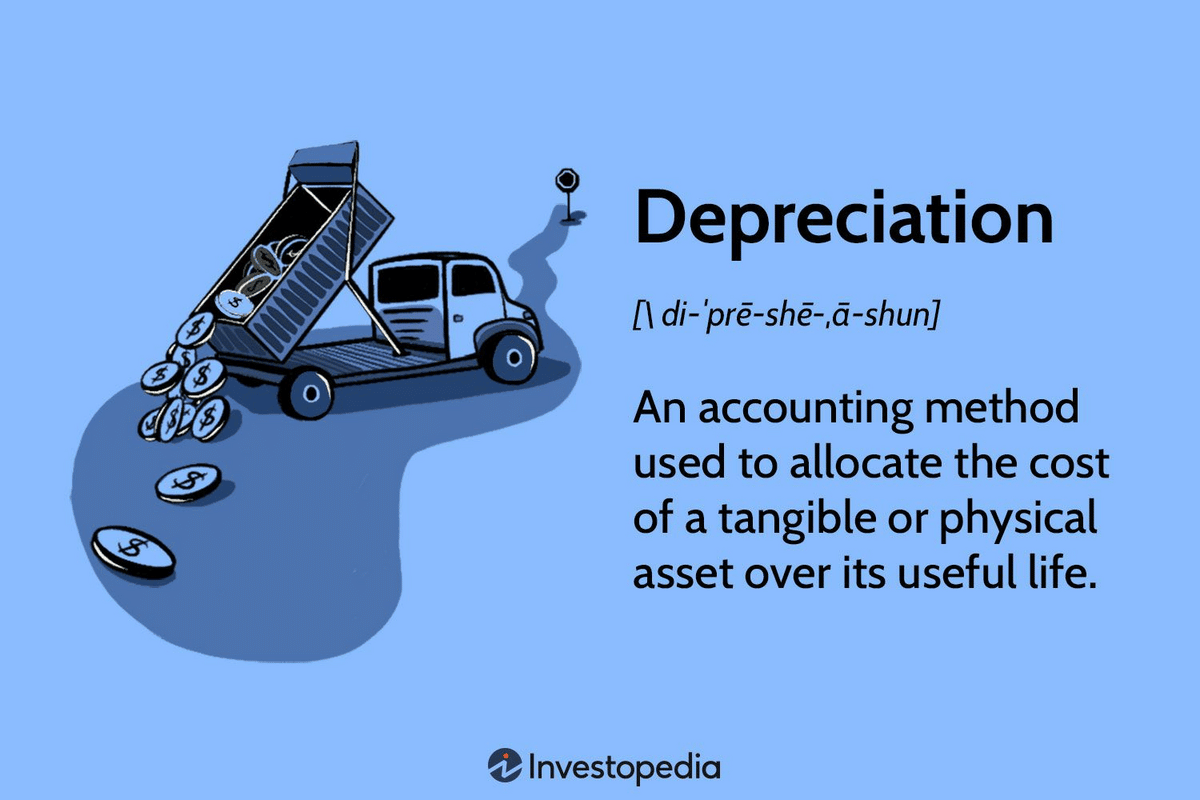
Both of these definitions emphasize approaching the asset holistically.
It’s important to consider not only what the asset can bring to your construction company at the time of purchase, but also how long it can serve you well over the entirety of its life cycle.
For the purpose of asset management, calculating asset depreciation is required to understand when an asset will be reaching the end of its useful life, which means it will need to be replaced.
If your construction company does not already take asset depreciation into consideration, now is a good time to start.
Tracking depreciation ensures that your past investment is unfolding as expected. This involves drafting a plan to preserve and analyze various data points regarding each major asset.
It’s important to review this information at least quarterly to track its accuracy against market prices and the performance of the asset.
If you find that the asset is not operating as expected, a quarterly review will alert you to the situation much faster than an annual audit would.
The sooner you can make adjustments to your asset or the way you are using it, the better.
In order to keep up to date on how well the asset is functioning, it is a good idea to solicit the opinion of team members or equipment managers, and draw up a checklist that will ensure consistent points of comparison.
Invest in Preventive Maintenance
A major aspect of asset management involves keeping each item in working condition.
Construction companies should invest in preventive maintenance because doing so can help to extend the useful life of their assets.
Proper preventive maintenance involves much more than checking the oil on the assets in your fleet every now and then.
In order for preventive maintenance to serve you as well as it possibly can, it is best to make a plan and institute a workflow.
Here’s an example:
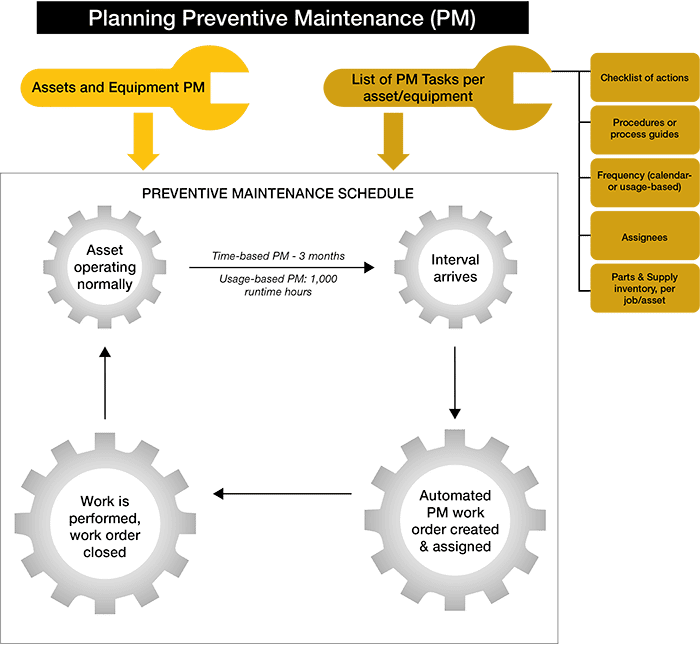
This structure involves different actions to take depending on whether or not the asset is operating normally.
However, if preventive maintenance is a priority from the start, it can help prevent unexpected breakdowns and avoidable problems.
It is usually best practice to construct a checklist to ensure that each action is performed, and to verify the date as well as the employees who completed it.
The checklist can include action items such as sharpening blades, repairing minor surface damage, or ensuring proper calibration.
Preventive maintenance also involves such tasks as cleaning instruments, replacing tires, measuring fluids, checking seals, maintaining correct amounts of grease, and ensuring bolts are in place.
This can take place either on a calendar schedule—for example, the first day of every month—or by operating hours.
As an example, a work team might determine to perform a preventive maintenance check on a concrete mixer truck for every 500 hours it is in operation.
Track Your Assets
The benefits of asset tracking extend beyond the mere knowledge of GPS coordinates of expensive machinery.
Asset tracking can assist in storing important information such as instruction manuals, warranty details, and the custody chain of certain items.
Assets that never move from their initial position—known as fixed assets—are also trackable.
For example, tracking a water heater might involve not just information about preventive maintenance, but also the temperature of the water, the rate of warming, the ambient conditions of its location, and other essential data.
These types of data can alert your maintenance team to factors that could cause damage to your asset, such as temperatures, water amounts, and air quality sweeps.
Asset tracking systems such as GoCodes Asset Tracking use such methods using QR, Bluetooth, or barcode technology to quickly store important information about your assets as they move through the workday.
Your employees will use devices with which they are already familiar—smartphones, tablets, or both—which means that training can proceed more quickly and team members feel more comfortable with a comprehensive change from manual tracking.
GoCodes Asset Tracking even offers free trials to ensure that the system is a good fit for your company and mode of operation.
Your company can use such products for so much more than asset register management,
An asset tracking system can function as a GPS reporter, keep track of employee use, and conveniently place at hand important documents such as service records and warranties.
Your own app and QR codes, and unique sequencing IDs will further fit the system to your company.
Perform Regular Audits
An audit is a full examination of each inventory item or asset in your company. It seeks to match the numbers in the asset register with what is physically present.
Some companies perform audits on a quarterly basis, others do so yearly.
Many business owners dread audits when using a manual tracking system because the process is often slow, cumbersome, and disruptive.
However, regular audits are much easier with an asset tracking system—scans take no more than a brief moment for each item, and accuracy is far better than when audits are conducted manually.
Employees use smartphones or tablets to scan QR codes or barcodes on each asset. In GoCodes Asset Tracking’ case, the QR codes rest on a custom label for the asset.

The type of tag depends on the type of asset under consideration as well as its usual location.
For example, flexible foil tags are effective for textbooks, but heavy metal tags welded to a side panel are a better choice for a digger that experiences constant exposure to harsh weather, extreme temperatures, or sea salt.
When construction companies perform regular audits, they risk generating incorrect numbers or copying errors. Employees might also miscount.
Since many companies then have the onerous task of applying the asset count to a spreadsheet such as Excel, more opportunities for yet more errors are present.
Manual audits, while they might provide an approximation of the actual number of assets in the company, are almost never perfectly correct.
However, performing a regular audit with an in-place asset tracking system proceeds much faster and with a far higher assurance of accuracy.
In short, performing regular audits is well worth the investment of time.
Audits can help to prove the veracity of financial statements and can stop irregularities before they cause financial strain or organizational nightmares.
In addition, regular audits regularize tax documents and save time for employees preparing for taxes or end-of-year statements.
Conclusion
Construction companies can manage their assets much more easily when an asset tracking system is in place.
It’s best to keep a detailed register so that all pertinent information about an asset is up to date and easy to extract.
Calculating depreciation for each major asset investment can help to ensure a good return for your purchase, while taking the time to invest in regular preventive maintenance can help to extend the usefulness of vehicular assets.
An automatic tracking system such as GoCodes Asset Tracking can help track your assets so that you are aware of the location and properties of each item.
Finally, performing regular audits help to ensure that your company’s asset register is correct and up to date.