If you’re reading this article, you’re probably aware that asset mismanagement can have dire consequences for your company.
Misplaced equipment, maintenance issues, unreliable asset data, and other problems can have long-lasting effects. Namely, your company’s profits can be severely harmed.
Therefore, if you’re ready to take control of your asset management and track valuable equipment, tools, and materials, then let’s look at the most important asset tracking problems and how you can solve them.
In this article...
Losing Assets Due to Misplacement
Construction sites are among the most dynamic workplaces in the world. With the constant movement of people and machinery that takes place every day, it’s not uncommon for key assets to get misplaced.
A worker takes out a tool from the storage facility, moves it somewhere to do their task for the day, leaves it there, and the next thing you know—you can’t find the tool anymore.
This means you’ll have to search all over the construction site for that missing tool or buy a replacement.
This type of inefficiency is a widespread problem in the construction industry.
Misplaced or missing equipment makes field workers spend almost a full day of every workweek on unproductive work (i.e., looking for missing assets).
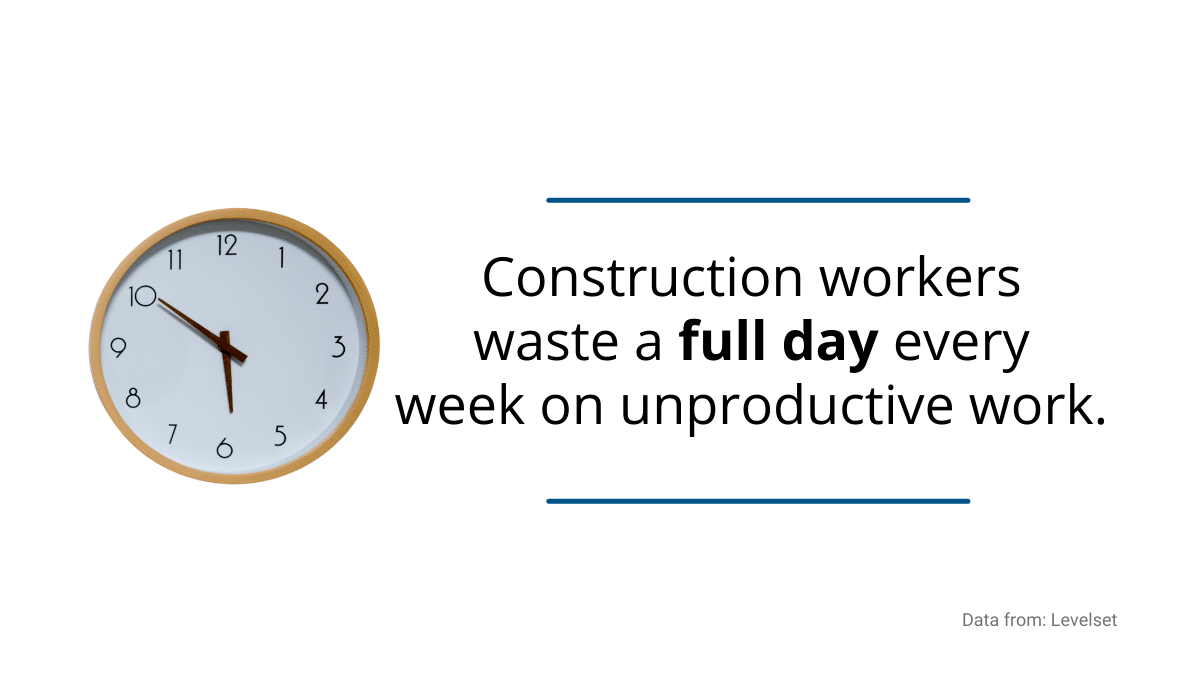
It goes without saying that the wasted time has a snowball effect on your company.
Each minute your workers spend looking for tools could be used to do their job, thus following the project’s schedule better.
Additionally, your project costs are also growing unexpectedly for every misplaced asset.
Part is due to added costs for asset replacement, and part is due to worker overtime because, without that asset, they couldn’t do their tasks on time, so they’ll have to work more.
Therefore, better visibility into the company’s assets (owned and rented) is essential to avoid these problems and keep a reputation as an efficient and organized construction company.
In order to do that, you need help tracking asset location, status, and movement. This is where asset management software can help you.
From the very beginning of asset purchase, you can tag your assets and keep an eye on them until the end of their lifespan.
The best thing about asset tags is that you can use them on all types of valuable assets you want to track—from office supplies to heavy equipment.
Tags come with scannable barcodes or QR codes that can help you monitor asset usage and location at all times.
Even better, each tag comes with an asset ID that creates an efficient check-in/check-out system.
Every time someone checks out an item, you’ll be able to see the user, the time, and the asset’s current location in your database.
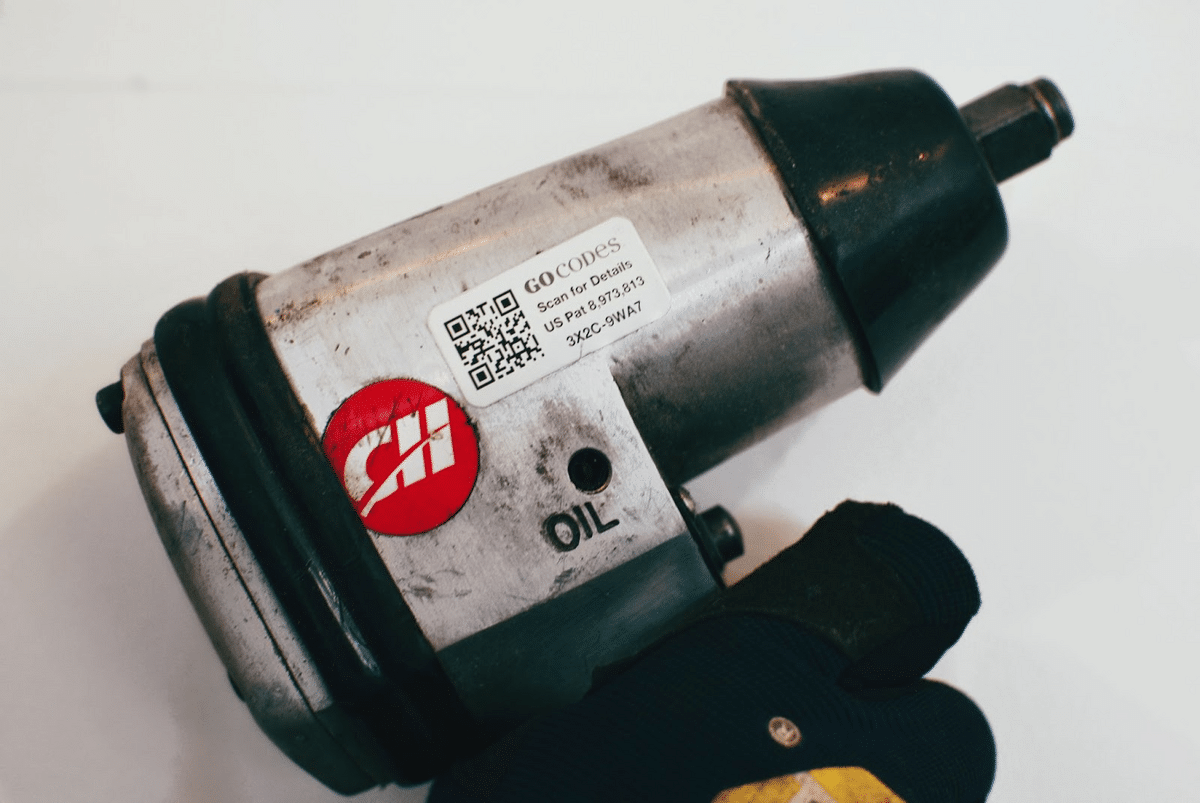
Furthermore, it can instill a sense of responsibility in your workers because they know that each time they check out a tool, someone will monitor them, and they’ll be more likely to put the tool back in storage.
Keep in mind that misplacing and losing assets is inevitable, but with a cloud-based asset management tool, your chances of recovering them are better than if you’re relying on traditional methods.
Inaccurate Data Problems
A study conducted by AutoDesk revealed that 25% of all project data construction companies collect is unusable. Their common complaints are as follows:
- It is difficult to combine the data from one source with data from another.
- Data is incomplete and missing certain aspects.
- Data is not easily accessible.
- There is too much data to use effectively.
- Errors raise suspicion about the data’s usefulness.
If you use manual methods like entering asset information into a spreadsheet, you’re most likely familiar with these problems.
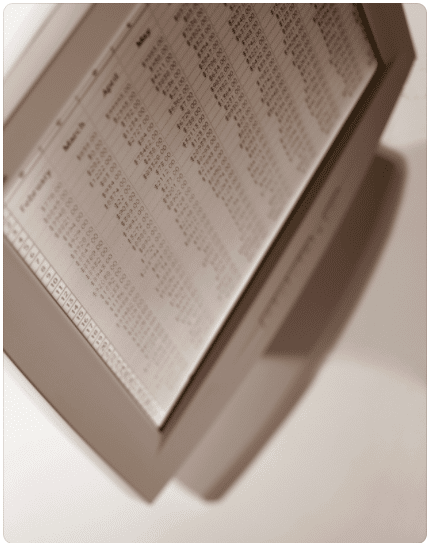
Human errors are more common with manual processes because workers tend to forget to update information regularly.
Additionally, fatigue and overwork often lead to employees entering wrong info, so you’re never certain you’re operating with accurate data.
The good news is that you can combat this problem with the right digital solution.
Working with vendors who will give you automated and customizable options for asset tracking will enable you to always collect and analyze relevant data for your company.
This will create more accurate reporting and better decision-making regarding asset management.
For example, GoCodes Asset Tracking enables you to hide unused fields to enter the information you need easily.
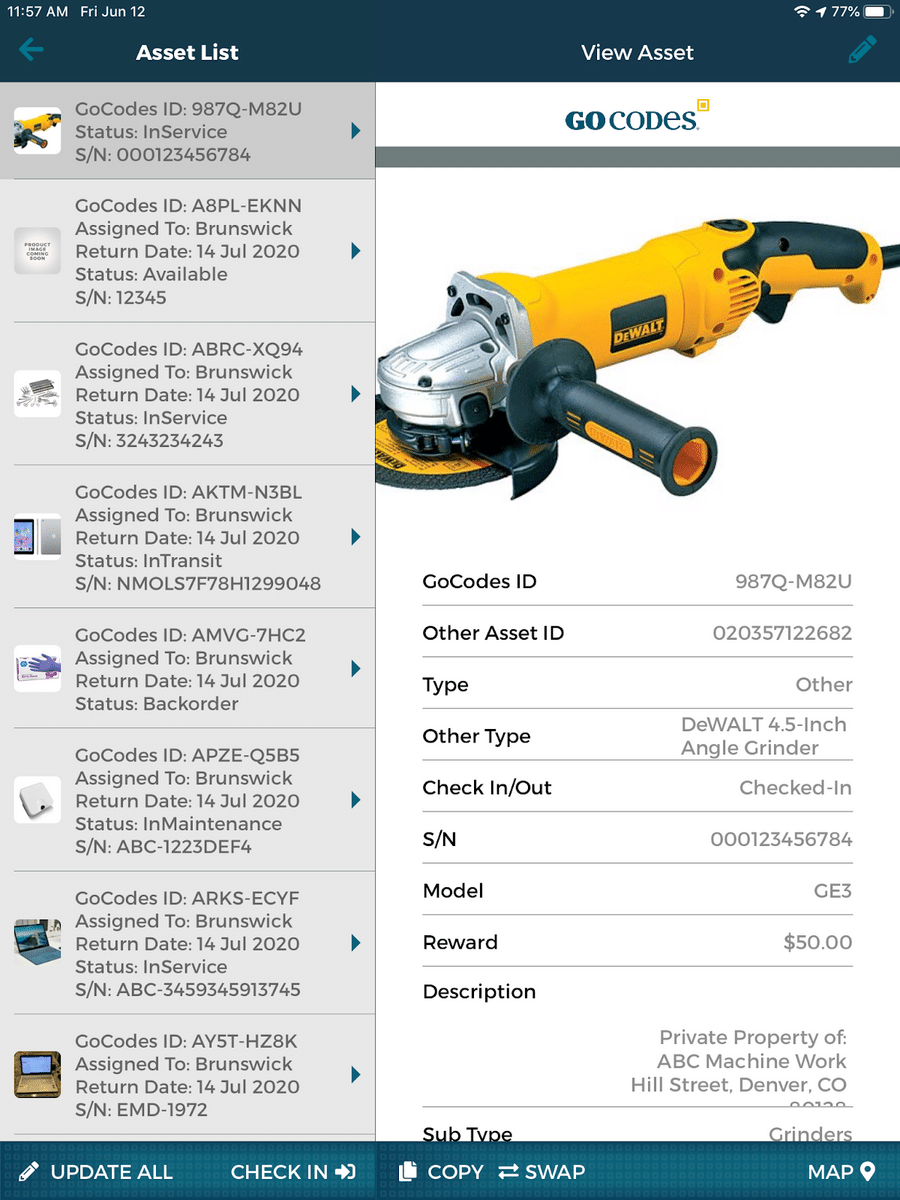
Integrating different data into one centralized and easily accessible system is a surefire way to simplify important asset management processes.
What’s more, it creates more consistent asset data, so you know which assets are available and when.
In the end, if you want to be competitive and join the 53% of your peers who use digital software for better asset management, then your best option is to look into a good asset management software for accurate data collection.
Maintenance Issues
When your assets are in good condition, they perform well and increase overall productivity on a job site. This also means you can finish projects on time and within budget.
Everybody wins, right?
In order to sustain that momentum, it’s also necessary to keep up with equipment maintenance.
Once your equipment breaks down unexpectedly, it will have a rippling effect on the entire company.
According to Frank Byers, president and CEO of AgriSphere, any breakdown can have catastrophic consequences for a company, such as costly repairs, injuries, compliance, and liability issues.
But there are hidden costs as well.
He also mentions that equipment failure can negatively affect employee morale and the company’s reputation.
A broken excavator means employees will have to abandon their work and either wait until the machine gets fixed or have another one delivered.
This can lead to frustration and reduced motivation because they’ll eventually have to work overtime to catch up with work tasks.
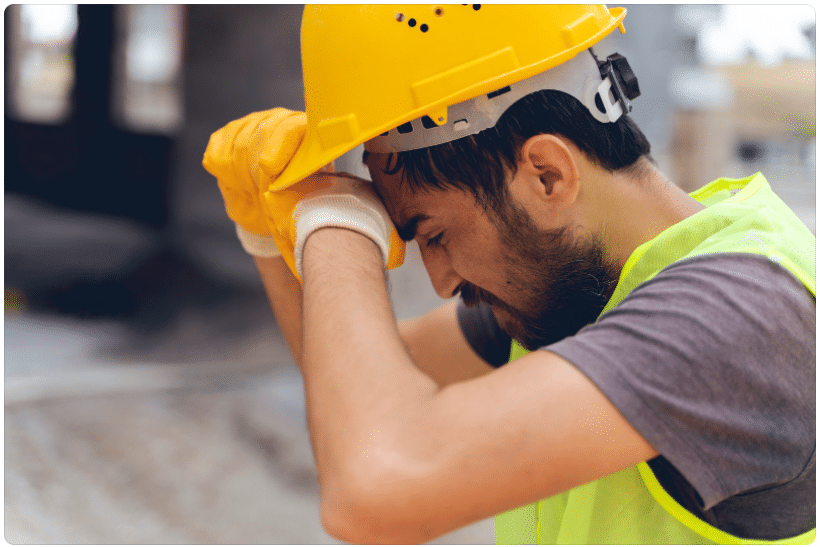
Clients also don’t look favorably on equipment failure because it often results in project delays.
Their negative experience could potentially cost you new clients and new jobs.
Not to mention, the company’s ability to respond to market opportunities is also put into question.
You can’t be effective at bidding for jobs if you have three operating wheel loaders, when you need six to complete the project the way the client wants.
So, the answer is regular maintenance, of the preventive kind.
Each piece of equipment has a standard cycle when parts need to be replaced, fuel and oil levels need to be checked, or electric components need a thorough inspection.
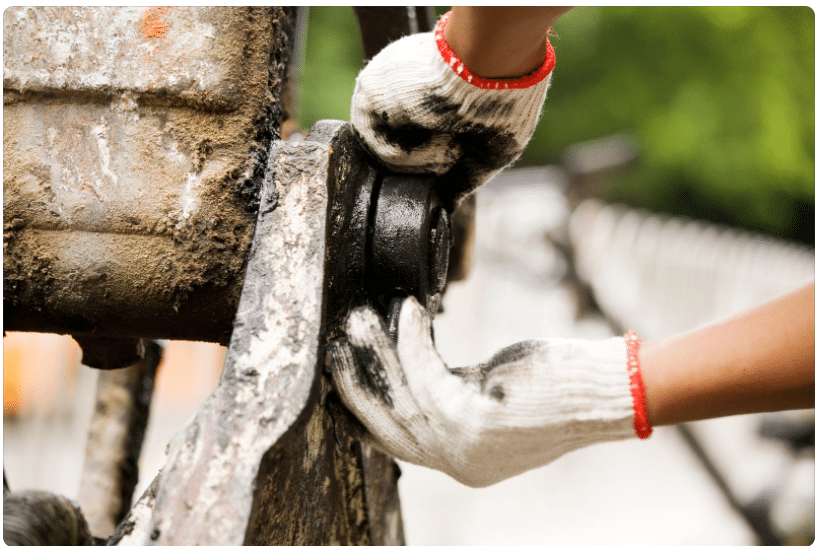
To ensure all your assets are looked after regularly, use asset tracking software to schedule servicing.
You can customize it according to each piece of equipment’s needs, but it’s important to find an optimal plan, so you’re not over-maintaining your assets.
Excessive maintenance can eat up the company’s budget, just like insufficient maintenance can.
In the end, as Alan Berndtson, director of sales at WEM Automation, says—a good preventive maintenance program is about avoiding costly breakdowns and saving you money long-term. E
ssentially, think about it as another investment in your company.
Event Failure Caused by Tool Unavailability
Losing assets and equipment breakdowns are challenges that impact the construction company’s speed, operational costs, and efficiency.
But there’s another thing to keep in mind that has similar consequences as the previously mentioned problems.
That is asset unavailability.
Obviously, any company event or job can be jeopardized if you don’t have the assets you need.
But asset availability extends to your office equipment as well as heavy machinery and tools.
Consider the following: to keep projects on track, you’ll have to hold many meetings with different stakeholders.
How can you discuss important design adjustments and change orders if your IT equipment is scheduled for servicing or BIM software is being updated?
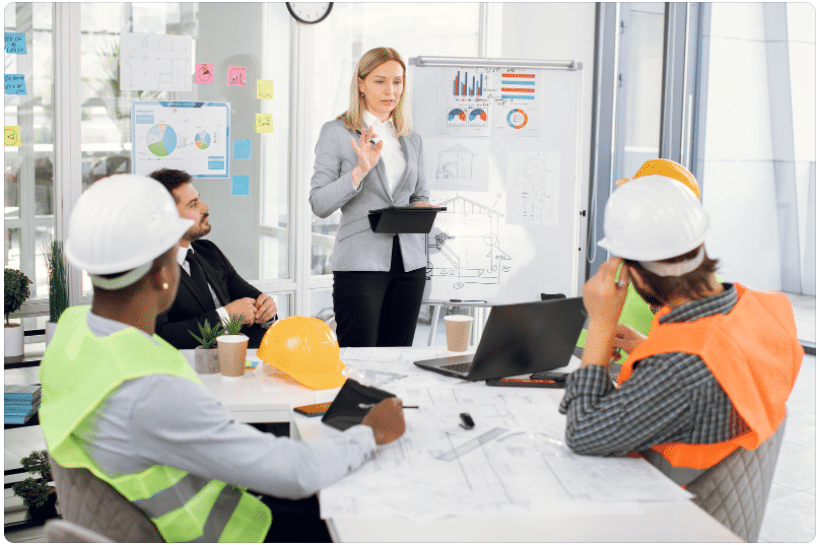
Therefore, office events and meetings should be scheduled around the availability of certain assets.
Booking equipment in advance will ensure you have the assets you need for a successful company meeting or event.
This is also an area where asset management software can help you.
Just like you can create a good check-in/out system to allocate equipment and machinery, the same can be applied to reserve assets to hold company meetings and events.
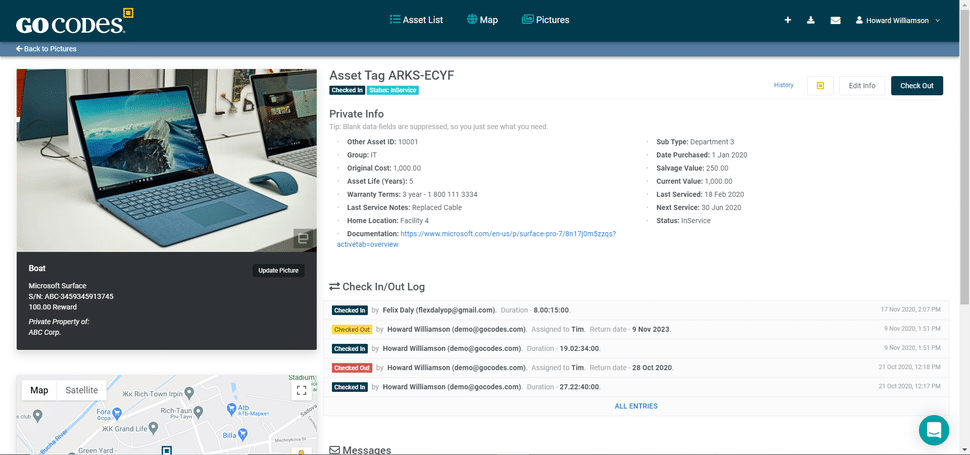
A centralized system that will list every asset and enable employees to see what the company owns can optimize workflows and eliminate booking conflicts.
Planning and organizing meetings is easier when you know you can rely on important assets being available on the day of the meeting.
Inaccurate Cost Predictions
Construction is an industry with small profit margins, so it’s essential to squeeze out every invested dollar to create a sustainable business.
Just look at these profit margins for different sectors in the construction industry in 2019, provided by CONEXPO-CON/AGG.
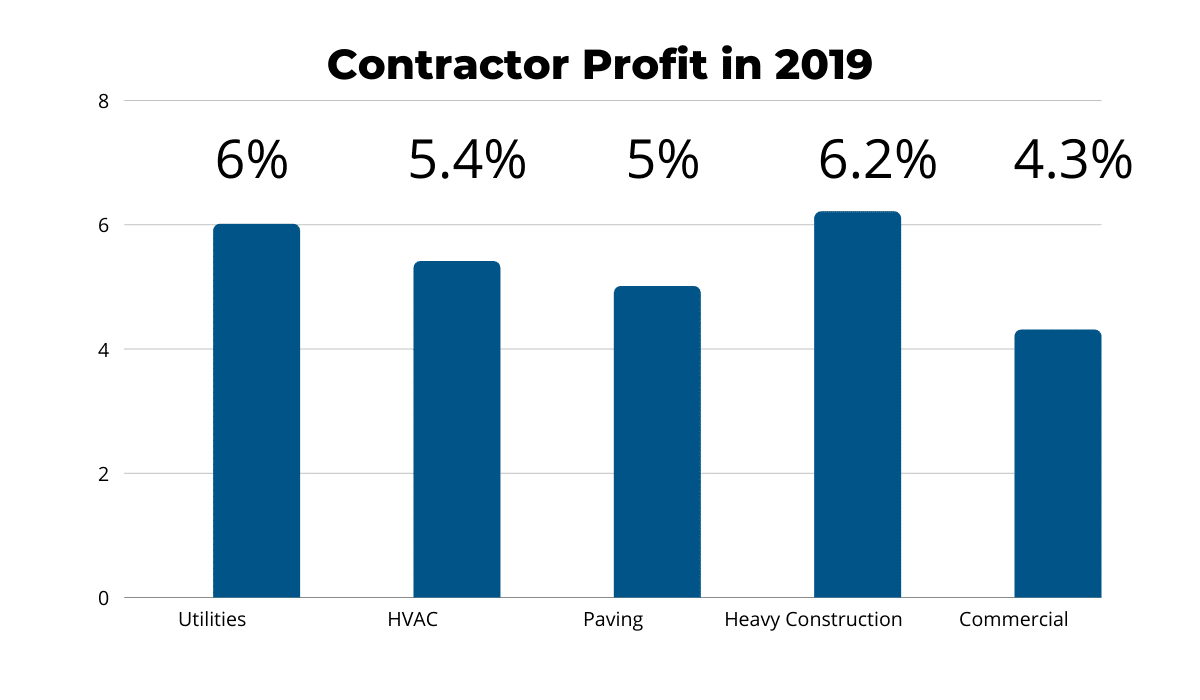
The average range for construction profit margins seems to be between 4% and 6%, and the situation hasn’t improved since.
In fact, almost 58% of contractors believe their revenues will remain the same in the upcoming year due to challenges posed by the pandemic, which exacerbated existing problems in the industry.
Factors such as labor shortages, supply chain issues, change orders, and underutilization of equipment contribute to diminishing construction revenues.
Therefore, having accurate cost predictions regarding asset purchasing, utilization, and disposal becomes essential to manage or even increase the low profit margins.
Companies of any size can use asset tracking software to predict future equipment costs and needs accurately.
Basically, having full visibility of your assets and their status can help you match project requirements to the available resources.
This means that you can assign the necessary equipment and budget for the costs of utilizing them for the current project.
For example, if you know you need ten excavators for a job, you can accurately calculate maintenance and operator costs for the project.
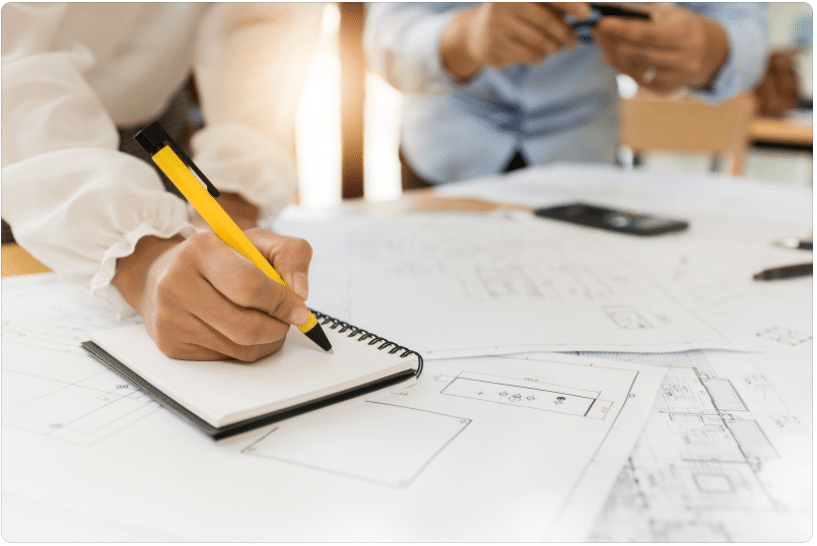
In addition, you can even forecast stock shortages and address inventory levels on time.
Determining the right amount of materials can be tricky, but if you know what you already own and what you’re missing, the entire process becomes more straightforward.
It all boils down to having the necessary data and asset visibility to allow you more accurate cost estimations and improve budgeting.
Conclusion
As you probably noticed, all of the issues discussed in the article can be solved by utilizing asset management software.
It will help you create more efficient operational processes and methods to eliminate errors and save time and money with the right solution.
Asset tracking becomes difficult once you have a long list of items to manage, so identify key challenges in your company and invest in an asset tracking software solution that will give you peace of mind.