Key Takeaways:
- Asset optimization focuses on improving the existing assets’ performance, availability, and value.
- Optimization strategies increase equipment uptime by up to 25% and extend asset lifespan by 20–40%.
- Using asset management software for optimization reduces downtime and inventory costs.
- 55% of companies using asset tracking technologies see a positive ROI in under a year.
From heavy machinery and vehicles to equipment and tools, construction companies rely on a wide range of assets to keep projects moving forward.
But are those assets being utilized as effectively as they could be?
That’s where asset optimization comes in.
In this guide, we’ll break down what it is, why it matters, and how to do it right, so you can get the most value from every piece of equipment you own.
In this article...
What Is Asset Optimization?
Asset optimization is a subset of asset management focused on maximizing the efficiency, performance, and value of assets you already own.
Think of asset management as the big picture.
It covers the entire asset lifecycle, from purchasing and deploying equipment to maintaining and eventually retiring it.
Asset optimization fits within that bigger framework.
It zooms in specifically on how to use your construction assets in smarter, more productive ways.
In other words, while asset management oversees the entire journey, asset optimization focuses on getting the most out of assets currently in use.
The illustration below shows how these two concepts and their main activities complement each other.
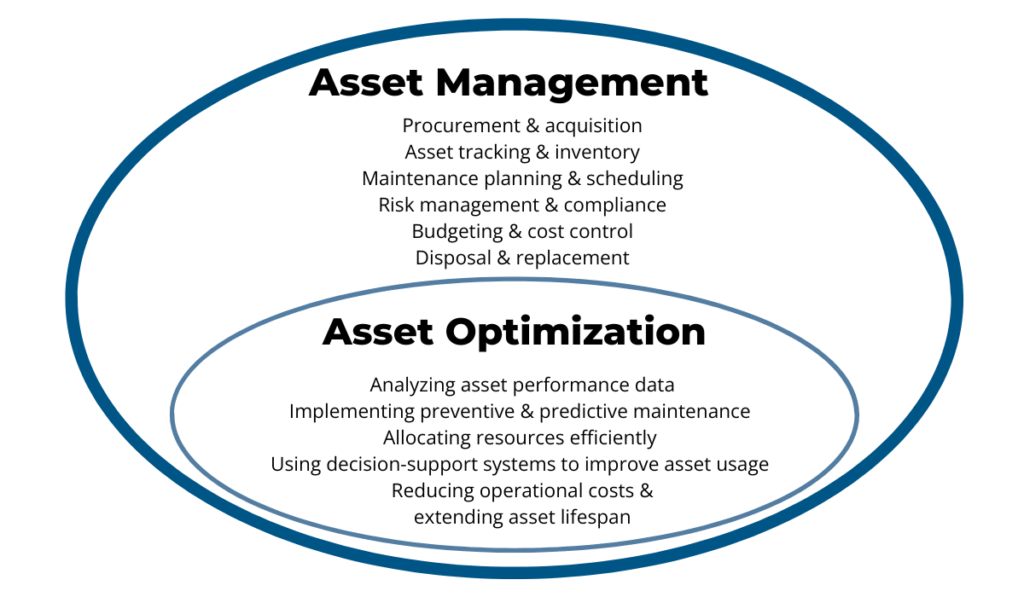
Source: GoCodes
While some theorists and non-practitioners like to stress the distinction between asset management and optimization, the two are inseparable in real-world construction operations.
Why?
Because opportunities to optimize assets depend entirely on strong management practices—specifically, effective tracking, maintenance planning, and compliance management.
Without a clear understanding of where assets are, how they are performing, and what risks they face, optimization efforts become either impossible or misdirected.
As Tom Richter, Enterprise Campus Edge Head at Nokia, puts it:
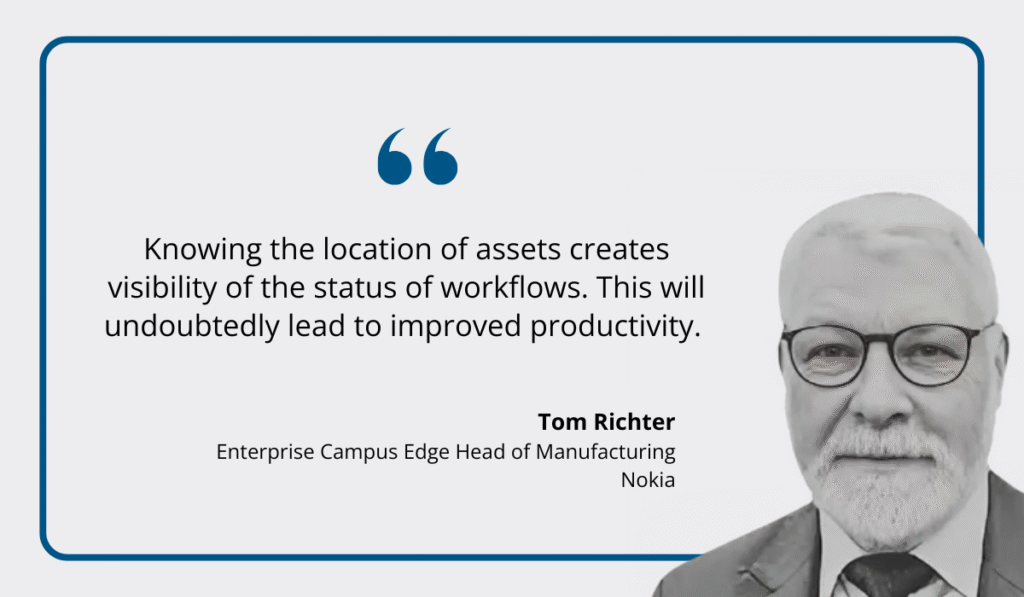
Illustration: GoCodes / Quote: Manufacturing Digital
Of course, effective optimization goes beyond just tracking asset locations.
It also depends on:
- Using data analytics to monitor asset performance and identify patterns
- Implementing proactive maintenance to reduce downtime and extend asset life
- Allocating resources efficiently to ensure the right equipment and inventory are available
- Applying continuous improvement strategies to refine asset management practices
By consistently applying these practices, construction companies can reduce waste, lower operational costs, and ultimately maximize the value of every asset.
Now, let’s explore the key benefits that asset optimization strategies deliver.
Key Benefits of Asset Optimization
When asset optimization strategies are built on accurate data and applied consistently, they unlock a range of operational and financial benefits.
Here are the four primary benefits.
Maximized Asset Availability
Keeping equipment available when it’s needed is the core of any asset optimization strategy.
When machines break down without a backup ready, it can throw off an entire project, leading to delays, missed deadlines, and extra costs that go beyond just repairs.
Daniel Corbett, Equipment Manager at Lancaster Development, agrees:
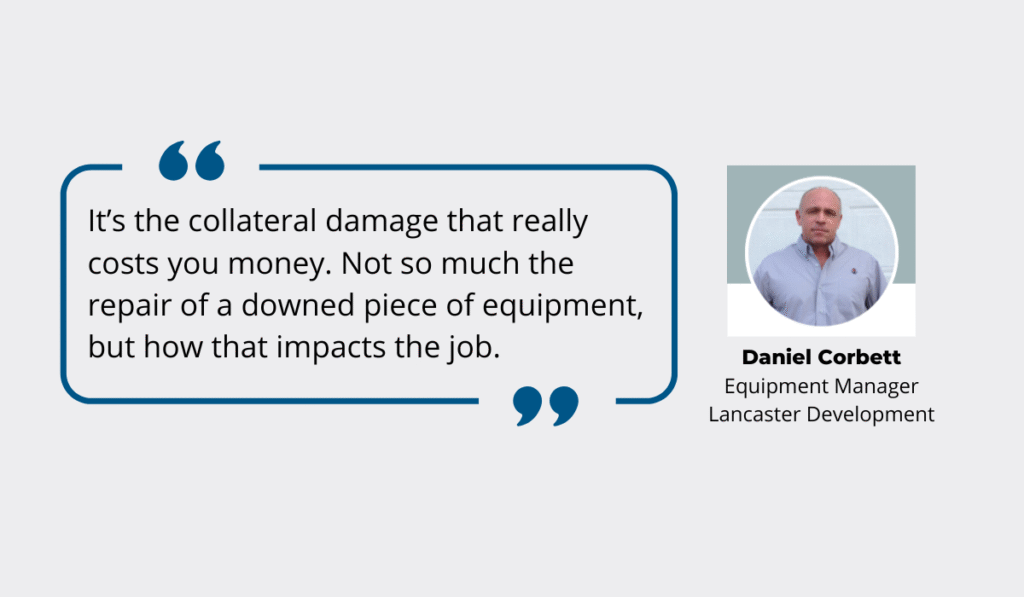
Illustration: GoCodes / Quote: For Construction Pros
The longer a machine is out of service, the more it puts your project at risk.
By maximizing asset availability, construction companies can reduce these risks and keep projects on track.
So, how do you actually improve availability?
It starts with monitoring asset performance, scheduling regular maintenance, and using predictive analytics to detect potential issues before they lead to downtime.
For example, Verizon Connect reports that using telematics systems to monitor asset health and receive alerts can boost vehicle uptime by up to 25%.
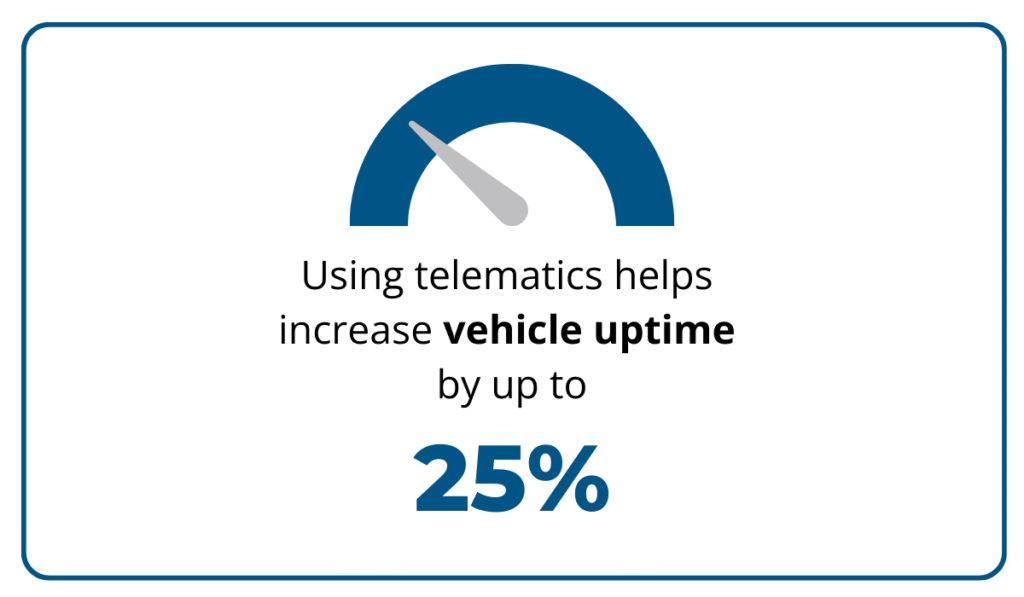
Illustration: GoCodes / Data: Verizon Connect
This same approach works for construction equipment, too.
Telematics and asset tracking help you stay ahead of problems, reduce downtime, and keep your machines working when you need them most.
By being proactive, construction companies can get more from their equipment, avoid delays, and run projects more efficienty.
Extended Asset Lifespan
Maximizing asset availability doesn’t just reduce downtime.
It also helps your equipment last longer.
By avoiding breakdowns and using machines more efficiently, construction companies can get more years of service from their equipment and delay expensive replacements.
This boosts long-term capital efficiency by helping you get the most value from each asset.
On that note, OxMaint research shows that equipment lifespan can be extended by 20-40% through continuous asset health monitoring and targeted interventions.
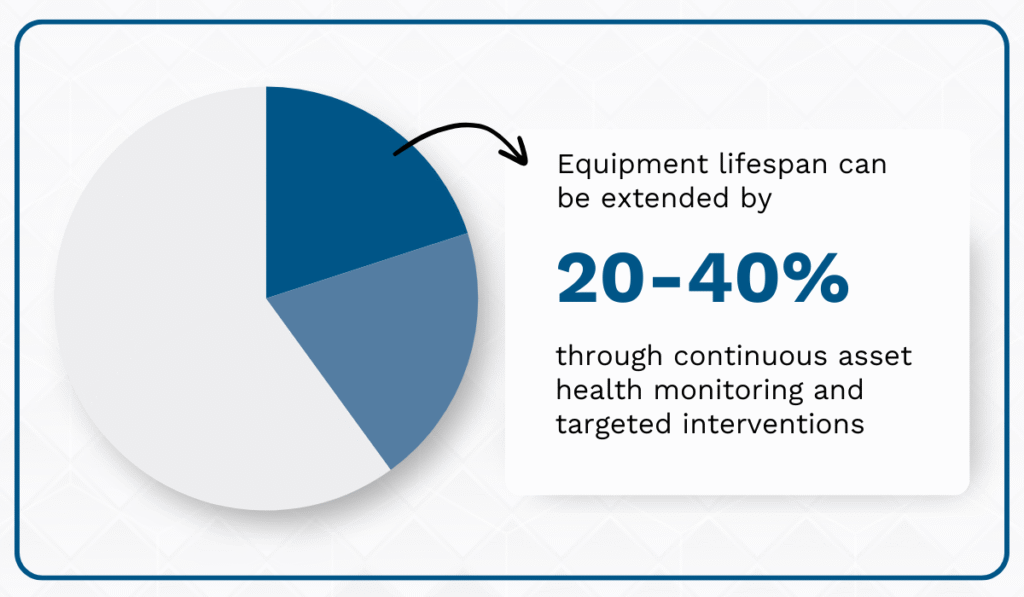
Illustration: GoCodes / Data: OxMaint
To achieve these gains, you need a combination of the right tools and smart strategies.
For example, built-in or added-on equipment sensors can be integrated with software to track asset health and report issues in real time.
If temperature, pressure, vibration, or other readings fall outside the safe range, you’ll get an alert before serious damage happens.
That means you can fix small issues early and avoid major repairs, keeping your machines in better shape for longer.
Another way to extend lifespan is by automating preventive maintenance scheduling based on your equipment’s usage hours, mileage, or other relevant parameters.
Software can ensure that everyone, particularly the assigned technician(s), is notified when it’s time for preventive maintenance.
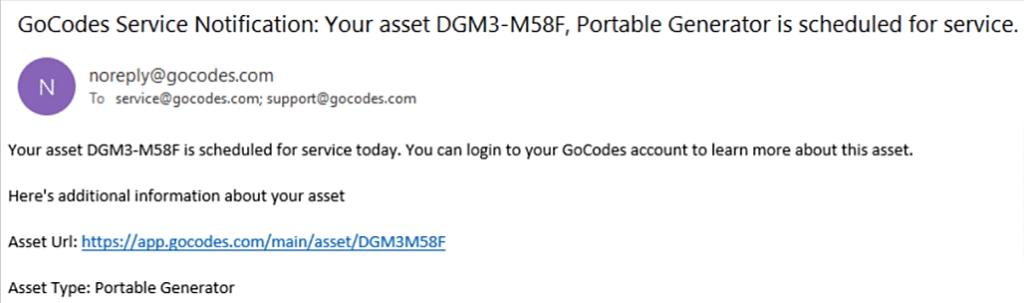
Source: GoCodes
Overall, using your assets wisely and maintaining them proactively leads to longer lifespans and lower replacement costs.
It also sets the stage for more cost-effective maintenance, which we’ll cover next.
Lower Maintenance Costs
One of the biggest payoffs of asset optimization is cutting down on maintenance costs.
For starters, increased availability and extended lifespan reduce the need for costly reactive maintenance and premature replacements.
Ultimately, this results in less money spent on new equipment, spare parts, materials, and internal or outsourced maintenance crews.
Technology is key to making this happen.
BusinessWire found that companies using asset, inventory, and maintenance management software achieve an average 20% reduction in both material costs and equipment downtime.

Illustration: GoCodes / Data: BusinessWire
These savings come from more accurate asset conditions tracking, smarter preventive maintenance scheduling, and better inventory management for parts and materials.
For example, tracking asset locations and maintenance status helps managers optimize staff workloads and reduce travel time for technicians or equipment as needed.
Inventory tracking is another big contributor to cost reduction.
By maintaining an accurate record of available parts and materials, companies can avoid over-ordering, last-minute purchases, and stockouts.
This matters because, as Jeff Shiver, CEO of People and Processes Inc., points out, not having the right spare parts on hand is one of the top causes of equipment downtime.
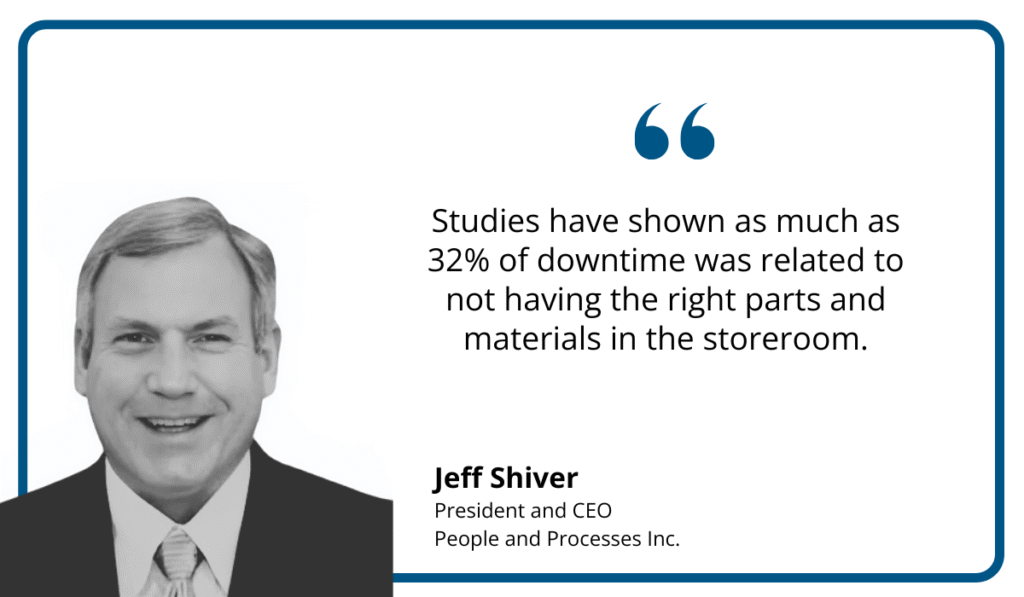
Illustration: GoCodes / Quote: Plant Services
Beyond these direct savings, software also supports data analysis and reporting, helping teams spot inefficiencies and make smarter, data-driven decisions that reduce costs even further.
All of these benefits lead to one major outcome: improved return on investment.
Increased ROI
When assets run longer, cost less to maintain, and support smoother operations, you get more value out of every dollar invested.
That’s the core of ROI—and it extends beyond the equipment itself.
A Geotab survey highlights how investing in asset tracking technologies (like GPS trackers and sensors) can significantly boost returns by enabling smarter usage and better decision-making.
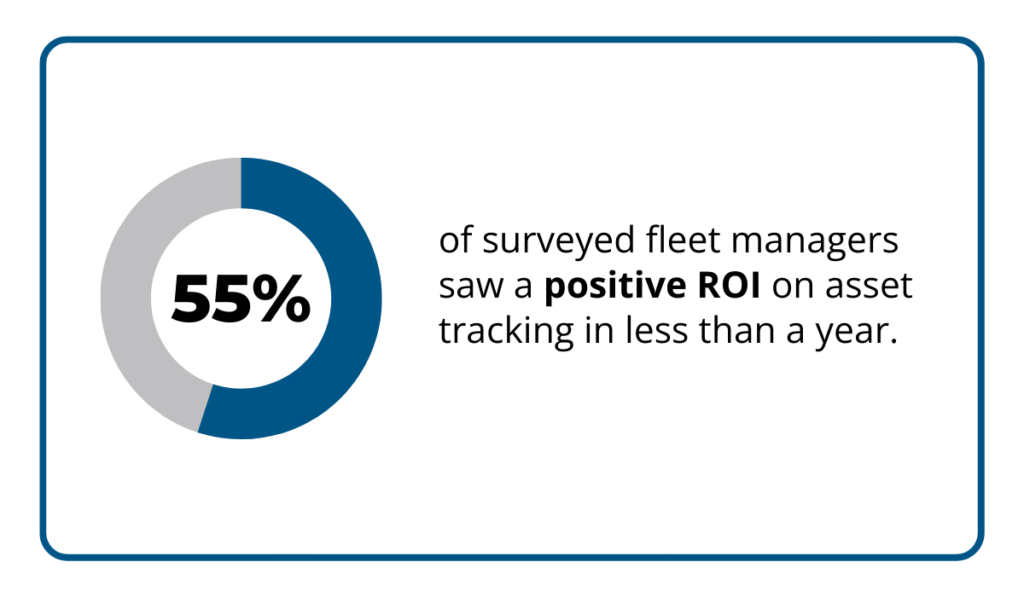
Illustration: GoCodes / Data: Geotab
In other words, pairing physical equipment with optimization tools increases its productivity—and your return on investment.
The bottom line?
The better a company monitors, maintains, and uses its assets, the faster it recovers its investment and boosts profitability.
Now that we’ve explored the key benefits, let’s dive into some best practices for optimizing asset performance.
Best Practices for Optimizing Assets
Optimizing asset performance requires the right tools, practices, and mindset.
Here are four best practices to help you maximize the value of your construction equipment.
Implementing Asset Tracking Software
Effective asset optimization relies on accurate data to inform the right strategies.
To achieve this, data must be collected, organized, and made accessible in a user-friendly format.
That’s where asset tracking software comes in.
It enables construction teams to monitor asset location, usage, and condition in real time.
One simple, versatile, and cost-effective asset tracking solution is our GoCodes.
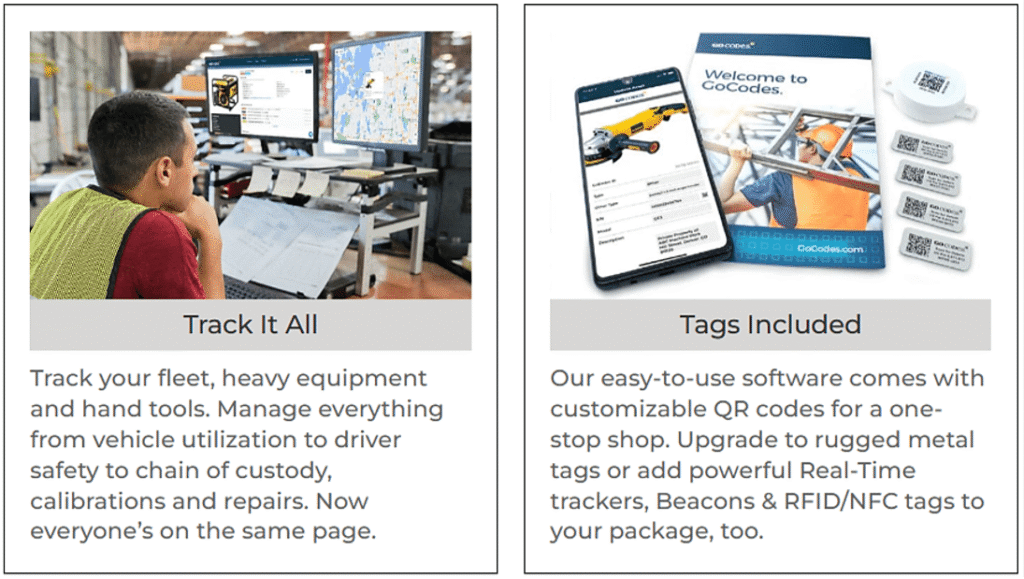
Source: GoCodes
With GoCodes, you can track all types of physical assets, from small tools to large cranes.
Each asset is tagged with durable QR codes that can be scanned with smartphones and tablets.
When scanned, the asset’s location is automatically captured, and users can view and update details like availability, maintenance history, and next service date.
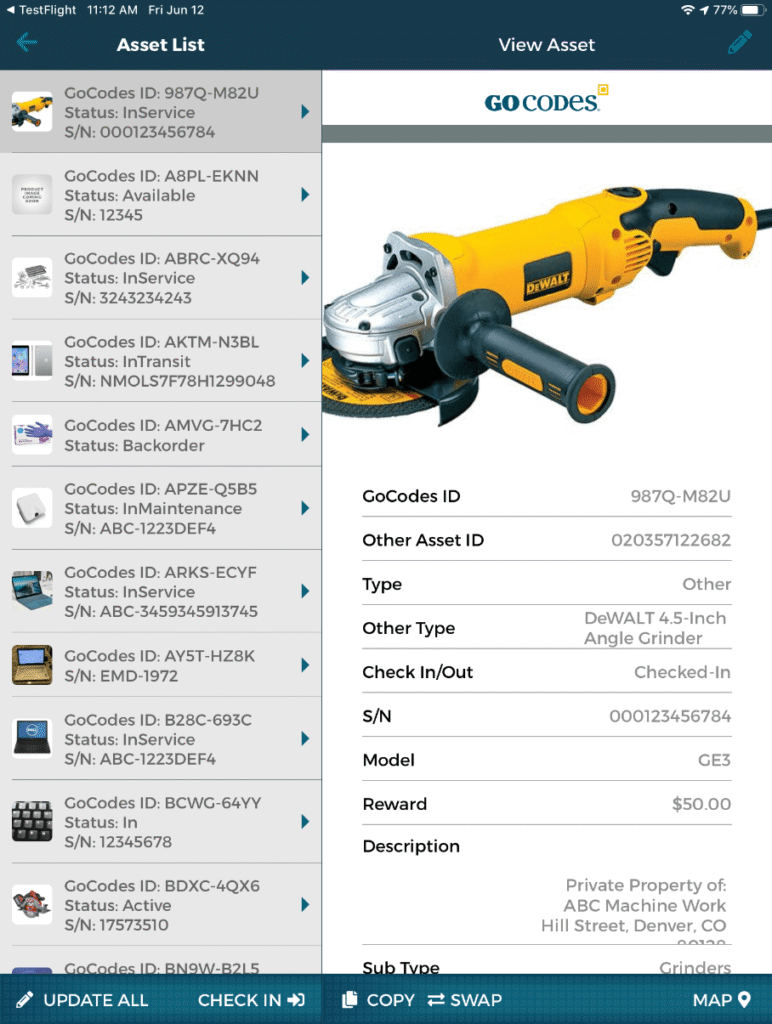
Source: GoCodes
For heavy equipment and vehicles, you can add real-time GPS trackers.
Implementing an asset tracking system like GoCodes brings direct benefits like reduced theft and loss, streamlined asset allocation, and improved accountability across your team.
Most importantly, it generates the data you need for smarter, more strategic asset optimization—including proactive maintenance.
Establishing Proactive Maintenance
Proactive maintenance is essential for optimizing construction assets.
Instead of reacting to breakdowns, it focuses on preventing them before they happen, reducing downtime, extending equipment lifespan, and lowering repair costs.
This strategy combines two key tools:
- Preventive maintenance schedules to reduce the risk of surprise failures
- Predictive monitoring (using sensors or software) to detect early warning signs
As this 2024 survey shows, proactive maintenance is becoming the industry standard:
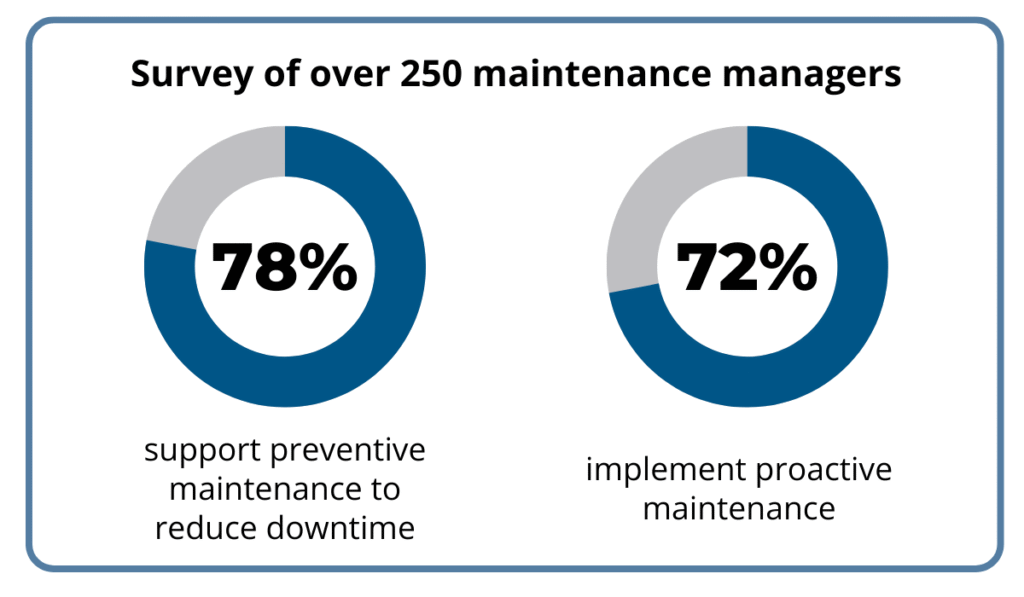
Illustration: GoCodes / Data: Facilities Dive
So, how do you make proactive maintenance part of your workflow?
It starts by building preventive schedules around usage data, like hours run or mileage, and sticking to them.
Then, layer on predictive tools that monitor equipment conditions in real time, such as temperature, vibration, or oil levels.
With this system in place, your team can spot issues early, plan repairs in advance, and avoid costly disruptions.
The payoff will be a more reliable fleet, fewer delays, and smoother project execution.
Conducting Regular Asset Audits
With an asset tracking system in place and a proactive maintenance plan underway, conducting regular asset audits becomes easier—and far more valuable.
Routine audits improve asset visibility, ensuring that every item is accounted for and tracked accurately.
By consistently reviewing asset records, companies can identify discrepancies, such as misplaced equipment, incorrect data entries, or assets that are overused or near the end of their life.
Audits also help uncover underutilized assets, which can then be redeployed to improve overall asset usage and project efficiency.
Another key benefit?
Regular audits keep your depreciation records accurate.
As shown in this dashboard, asset management software like GoCodes can automatically calculate depreciation:
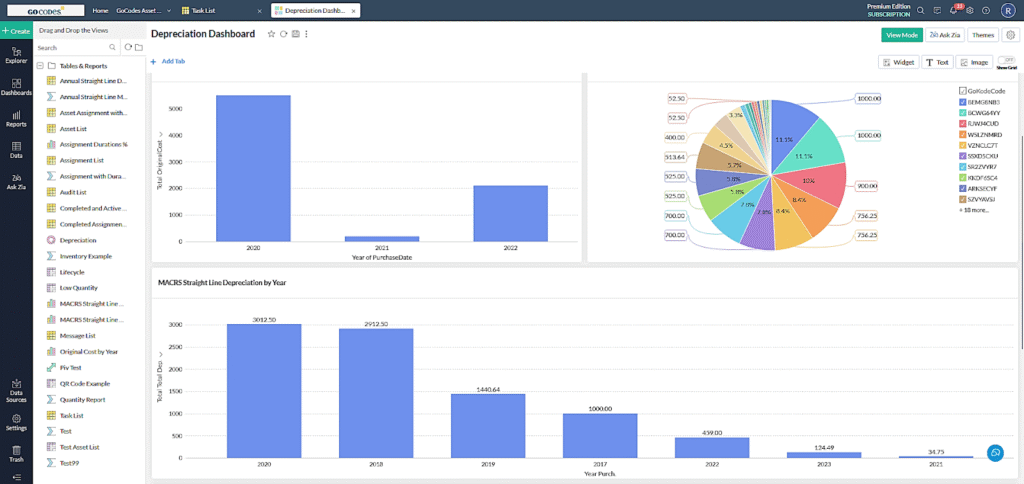
Source: GoCodes
Tracking depreciation helps you decide when to repair, upgrade, or retire equipment, so you’re not spending more than necessary on aging assets.
Ultimately, consistent audits are key to optimizing asset management.
They reduce waste, tighten control, and give your team a clear picture of asset performance.
Making Use of Data Analytics
Data analytics transform raw information into actionable insights.
To start, asset data analytics enable your team to identify which equipment needs attention based on performance, usage, and condition, allowing them to prioritize maintenance more effectively.
They can also analyze asset usage trends and track depreciation, using these insights to optimize replacement cycles and ensure equipment is replaced when it’s no longer cost-effective to maintain.
Of course, all this data must be presented in a user-friendly format.
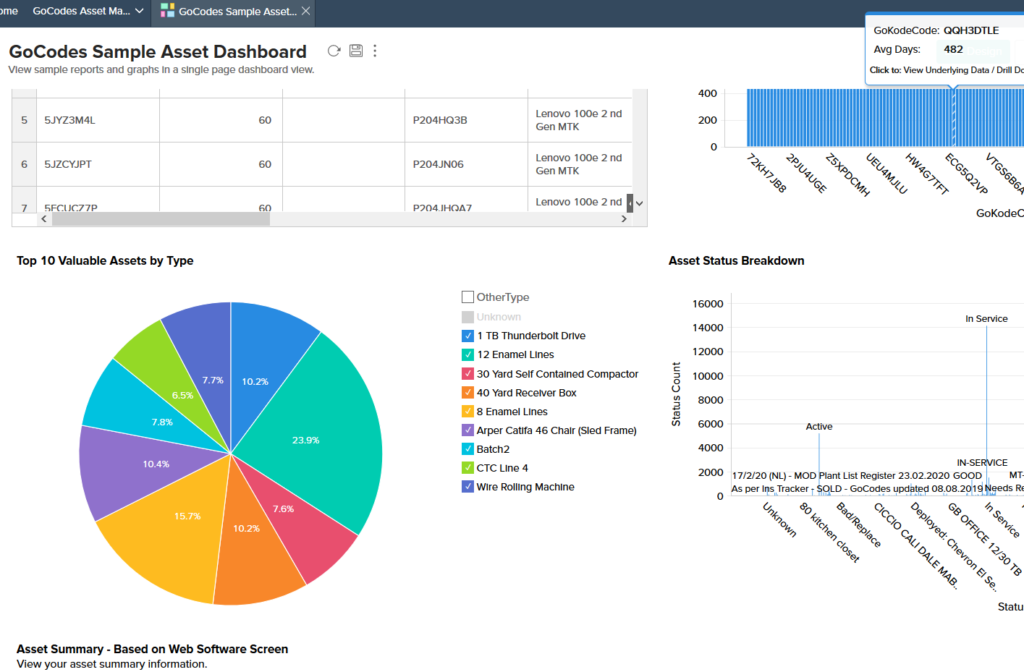
Source: GoCodes
When asset data is easily accessible, the real advantage comes from turning insights into data-driven decisions that enhance asset management.
With technologies like IoT sensors and AI-powered analytics becoming more common, leveraging data for asset optimization is rapidly becoming standard practice in the construction industry.
Conclusion
Optimizing construction assets isn’t just about managing them well.
It’s about maximizing their value at every stage.
With the right tracking system, proactive maintenance, regular audits, and smart data analytics, you can turn asset data into stronger performance, lower costs, and better project outcomes.
When done consistently, asset optimization becomes a lasting operational and financial advantage.