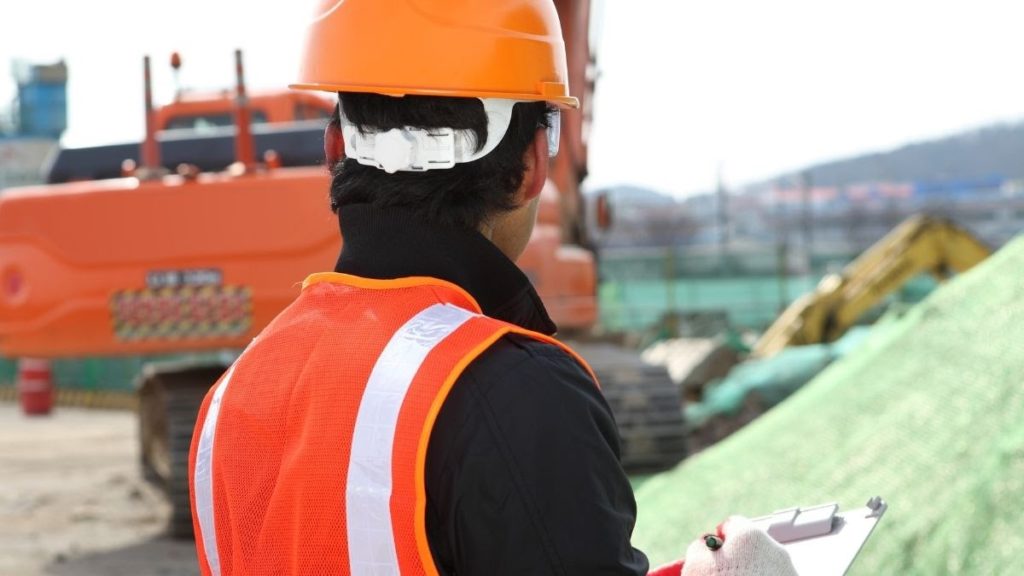
Each piece of heavy equipment is a major investment for your company.
Not only are these items costly to obtain, but maintaining them, training employees to operate them properly, and safeguarding them also requires significant resources.
It makes sense, then, that your care for your heavy equipment should extend to tracking its use, location, and technical upgrades.
But if you’re not already tracking your machinery, the task can seem overwhelming. Here’s a guide to getting started and making the most of your heavy equipment tracking adventure.
In this article...
Make an Inventory of the Equipment You Own
The first step is to make a list of all the heavy equipment your company owns.
An overview of your heavy equipment assets will help you make the right decisions about how to categorize, tag, and track them later.
Building a thoughtful and accurate inventory list helps to save you time and effort in the future. You can choose between creating an inventory list specifically tailored to the needs and goals of your company, or adapting one from a template.
Here’s an interactive template that can provide some granular detail about a company’s current equipment.
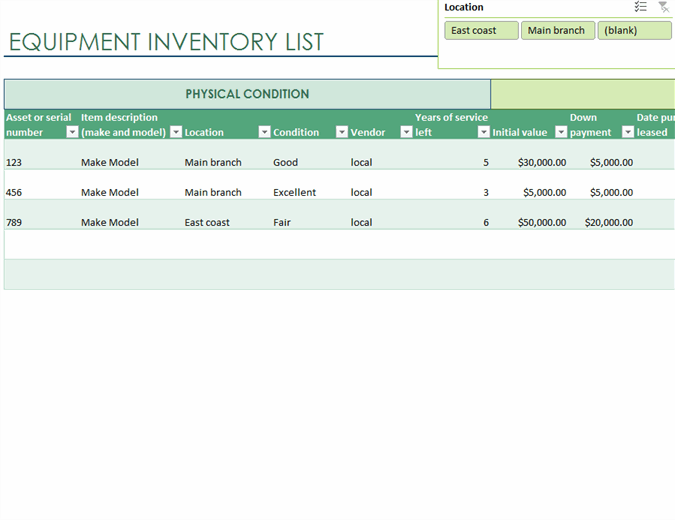
There’s a lot of information present in just this small document, from the type of machine and its condition, to where it is kept. You can see how valuable this data can be to decision makers.
Engineers often design heavy equipment to be versatile and fill a variety of different needs. Understanding how your operation uses these items, then, is an essential first step.
Speaking with operators and studying usage logs can help you understand not just how to categorize your heavy equipment, but how to use it as well.
What else should a heavy equipment inventory contain?
Useful information includes:
- Date of purchase
- Serial numbers
- Make
- Initial cost
- Condition
- Model
- Hours used
- Chain of ownership
- Repairs needed
- Dimensions
- Number of employees qualified to operate
- Current value
- Locations
- Vendor
- ROI (return on investment)
Having this information readily available can provide a useful snapshot of how the heavy equipment is operating within your business.
It can help you control spending, issue accurate projections for timelines and project completion, plan for maintenance, and predict usage trends.
Categorize the Equipment
The way you categorize your heavy equipment will likely depend on the type of work your company does.
Sometimes, cultural or language differences can result in multiple names for the same machine, so providing standard terminology helps avoid confusion or inefficiencies once you begin tracking.
Here’s an example of how one company sorts its heavy equipment:
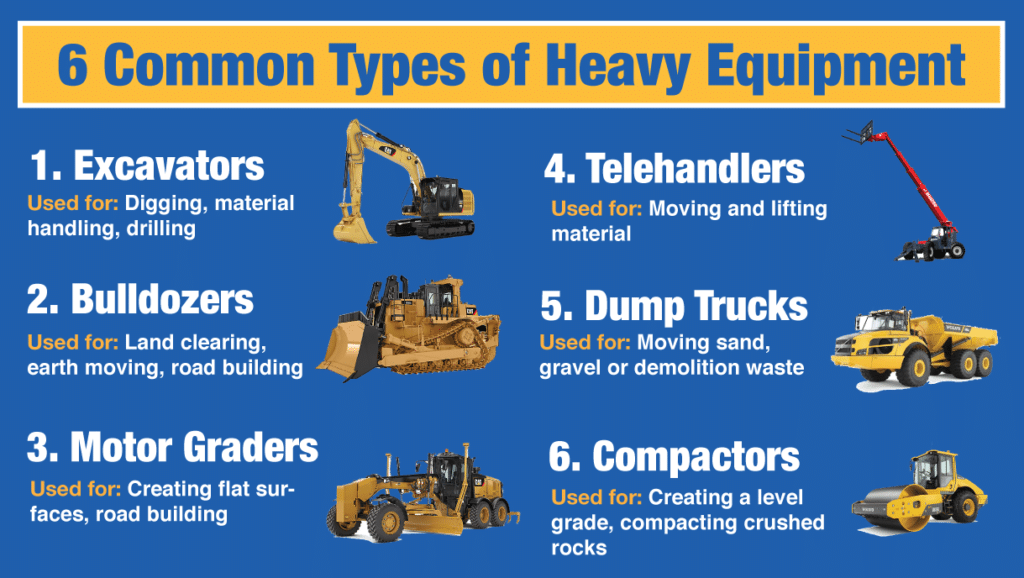
Not only does this graphic provide a consistent name for the equipment, but it also includes a brief description of its function.
Correctly identifying the heavy equipment in this way contributes to a safe working environment.
It also allows managers and employees to select the right equipment for the job and plan ahead for project needs. Doing so makes the distribution of resources more efficient and prevents schedule slippage.
Another way to categorize heavy equipment is by use or task. This strategy is especially useful when several employees have access to the same items, and resource efficiency is of premium importance.
Sorting heavy equipment by usage can unveil new patterns for you to study and leverage.
Algorithms and data systems enable your company to make quick, status-based decisions about where and when to place valuable equipment.
Some asset tracking software can even issue alerts if specific equipment categories aren’t meeting efficiency goals.
Your company might also benefit from ABC Inventory Analysis. This form of management leverages pieces of inventory based on how useful they are to your operation. The technique ranks each piece of heavy equipment according to the following factors:
- Amount of demand
- Initial cost
- Risk data
- Profitability
You can then group items into classes in such a way as to highlight the importance of each item. Class A items are the most important, followed by Class B and Class C.
Some organizations might choose to add even more groups or classifications to provide further flexibility and planning options.
Tag the Individual Machines
Properly labeling equipment is just as important as the initial inventory.
It’s also important to think about what kind of tags to place on your heavy items. In order to maximize the effort and time dedicated to the machine tagging process, consider the advantages of dedicating more than one task to your tags.
For example, GPS technology offers many possibilities.
Here’s a visualization of how a GPS label can help your company reach its goals, even beyond its use for heavy equipment:
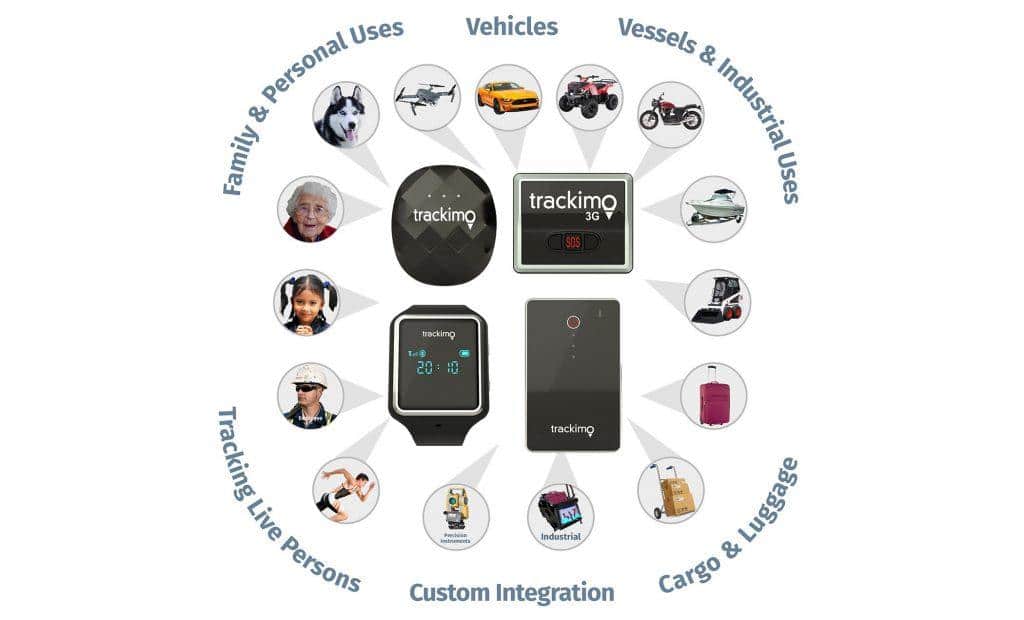
In addition to tracking vehicles, cargo, and employees, GPS tags are useful in boosting security.
Geofencing can provide an invisible but highly effective border around a predetermined area. It uses GPS and radio frequency identification (RFID) technology to enforce a perimeter.
You might be most familiar with geofencing as an “invisible fence” for pets or as a measure to keep shopping carts within a certain distance from a grocery store.
Your heavy equipment, however, can also benefit from GPS tags.
By outfitting specific items with a GPS label, your security team can receive an alert if the equipment moves at an unexpected time.
In this way, tracking protects your investments with a “movable fence” no matter where they are left for the night.
It’s just as crucial to ensure that your heavy equipment is outfitted with tags manufactured from appropriate materials.
Just as a fabric-based tracking label wouldn’t last long on a backhoe, light, flexible labels that work well for library books aren’t a good idea for cement mixers.
It is equally important that the labels are properly affixed.
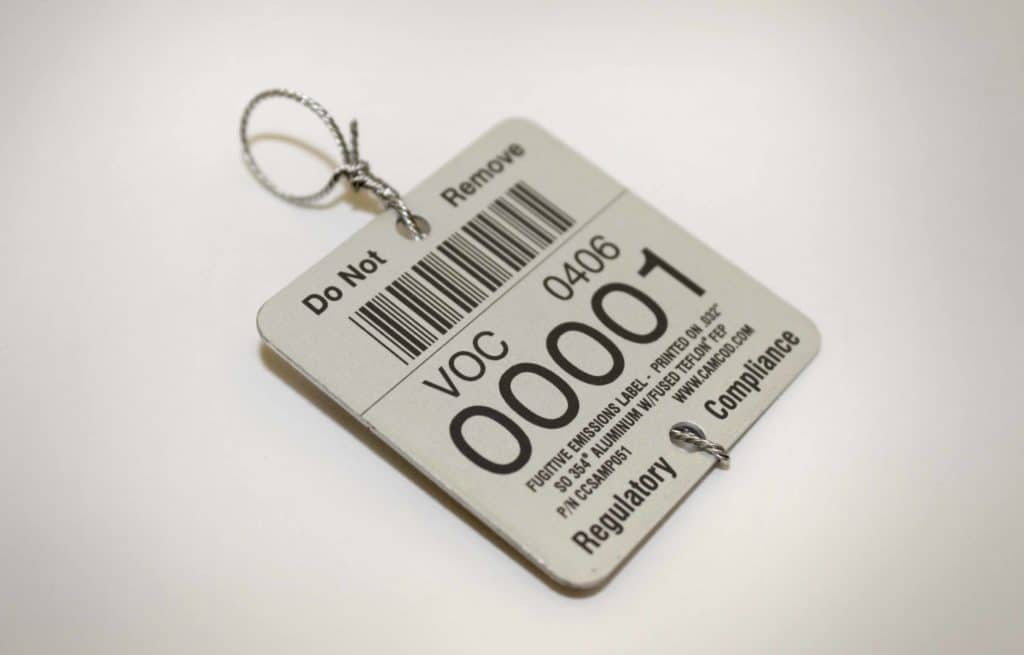
Metal tags can withstand extreme temperatures and last for decades. They provide reliable tracking even after long exposure to severe weather conditions— even the vacuum of space.
To sum up, choose the appropriate tags according to your needs to improve the security and efficiency of your heavy equipment.
Track Heavy Equipment Usage
Once you list, sort, and tag your company’s heavy equipment, tracking can begin. Just as sorting can take a number of forms, so can the ways in which you apply heavy equipment tracking.
The best way to initially keep tabs on these vehicles is to implement a check-in/check-out system.
This system not only provides a chain of possession for every item, it allows project managers to see where the equipment is in real time. Enforcing check-in/check-out procedures increases not only productivity, but also transparency and accountability.
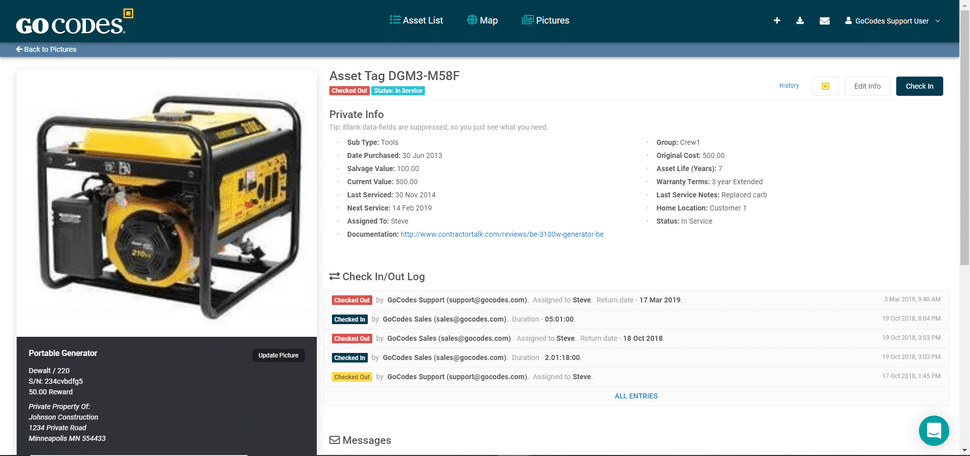
Heavy equipment tracking helps to prevent theft and eliminates time wasted in chasing down lost, misplaced, or misappropriated equipment.
An additional layer of security lies within the cloud storage of tracking data; hard copy or device-reliant records are easily destroyed, damaged, or altered.
Heavy equipment tracking can offer more assurance for clients and decision-makers regarding the delivery of equipment or material, especially in periods of supply chain uncertainty.
Even if delays occur, simply keeping customers aware of shifting timetables with constantly updated information can result in higher client satisfaction.
Equipment telematics helps detect unexpected movements, locate equipment on large sites, and study machine fuel management or idling time.
While the sheer amount of detail seems almost overwhelming, all of the data in the graphic below, when wisely leveraged, can quickly result in greater profits and increased institutional control.
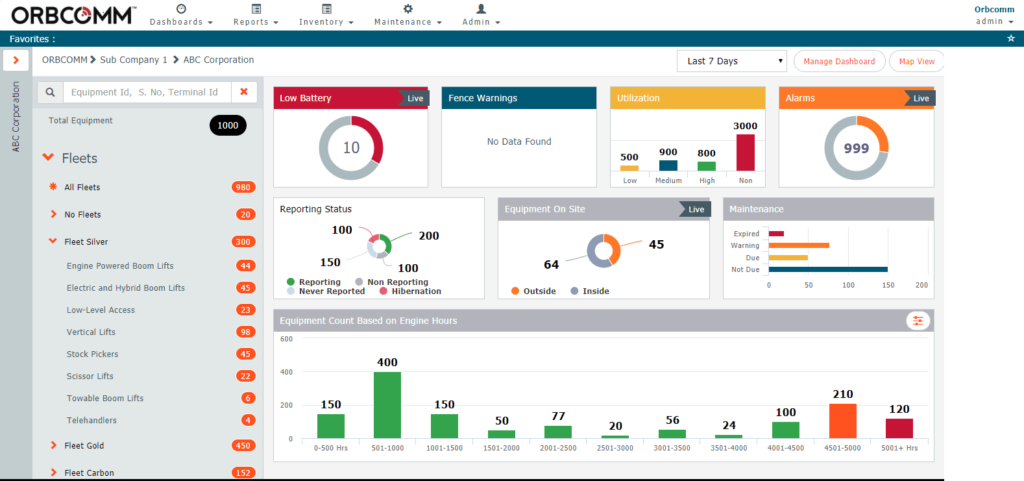
Improved maintenance is a major benefit of heavy equipment tracking. It proves compliance with regulation, assists in warranty claims, and allows automatic scheduling for more efficient working conditions.
Tracking also allows companies to quickly adapt to shifting conditions, as seen in the COVID-19 pandemic. Suddenly, and for an extended period, large swaths of the workforce were forced to work remotely.
In addition, companies were burdened by local governments with new and complex health regulations, some of which changed without warning.
Check-in/check-out software, along with other forms of tracking, was vital in contributing to an accurate picture of not only how the company was performing in the present moment, but in providing the means to make rapid changes.
Log Repairs and Warranties to Keep Your Machines Healthy
With GoCodes and similar tools, stakeholders and project managers can easily track equipment documentation, warranty periods, and regulation requirements.
They can also track maintenance actions and quickly share details about changes in condition or the need for parts.
The initial outlay a piece of heavy equipment requires is reason enough to track repairs and warranties.
Providing a consistent baseline and database for maintenance data also provides important data that leaves an analytical trail, which quickly yields actionable information.
This GoCodes video provides a glimpse at the many layers of information that equipment tracking can yield.
At a glance, it’s easy to see where a vehicle is, which employee has checked it out, and what assignment it is used for. The data is also instantly and accurately sortable, which means that audits and presentations are easily prepared.
Not only does information sharing become easier, tracking can extend equipment life.
By providing alerts that preventive maintenance is due, noting best practices, and providing operator instructions at a click, decision makers can stay ahead of major breakdowns and protect the health of their fleet.
Conclusion
Tracking your heavy equipment is the best way to care for it in both the long and short term.
Making an inventory of your company’s heavy equipment, categorizing it, and providing for appropriate labels are important initial steps.
Next, tracking usage provides security and vital information that generates valuable analysis. Software solutions like GoCodes make all this effortless.
And, in the event you require major maintenance or need to invoke a warranty, the data collected in tracking will be of great help.
Therefore, improve your operations by implementing the best equipment tracking practices we’ve recommended.