Construction project management mistakes plague every project, but pre-planning and careful attention to detail help curb them.
Since a construction project consists of so many moving parts, and managers have to deal with unpredictable factors as the weather, labor shortages, and client changes, it’s difficult to maintain daily flexibility, let alone tend to unexpected challenges.
The tips in this post, however, will keep your project as smooth as possible and give you the tools to avoid common errors that can make your job more difficult.
In this article...
Failing to Read the Contract Terms
It sounds like a basic requirement: know the terms of the contract you are fulfilling.
But sometimes, contracts for construction projects are stuffed with legalese or worded in a confusing way, and it’s easy to miss certain details.
Some project managers, accustomed to the language of boilerplate contracts, might fall prey to assumptions and skip over significant obligations or addendums.
It’s a common error, but one easily avoided.
Attorney Kevin Tharp suggests that project managers take the time to read the details of the contract with “What if?” questions in mind, conjuring various scenarios and how a shift in conditions might affect the project.
Studying contract terms is also important for understanding the rights of the project manager.
Remember that this document is in place to protect you as well as the client.
Knowing what your rights are and the definition of the terms that trigger them is useful in the event of an emergency or obstacle.
For example, if a weather-related disaster affects your worksite, your contract might enable you to extend the project timeline without penalty.
Knowing the type of contract into which you are entering allows you to understand the framing of the agreement before you read it. Working with unit prices, for example, differs from contracts for projects that are not clearly defined at the outset.
Here are the four common types of construction contracts:
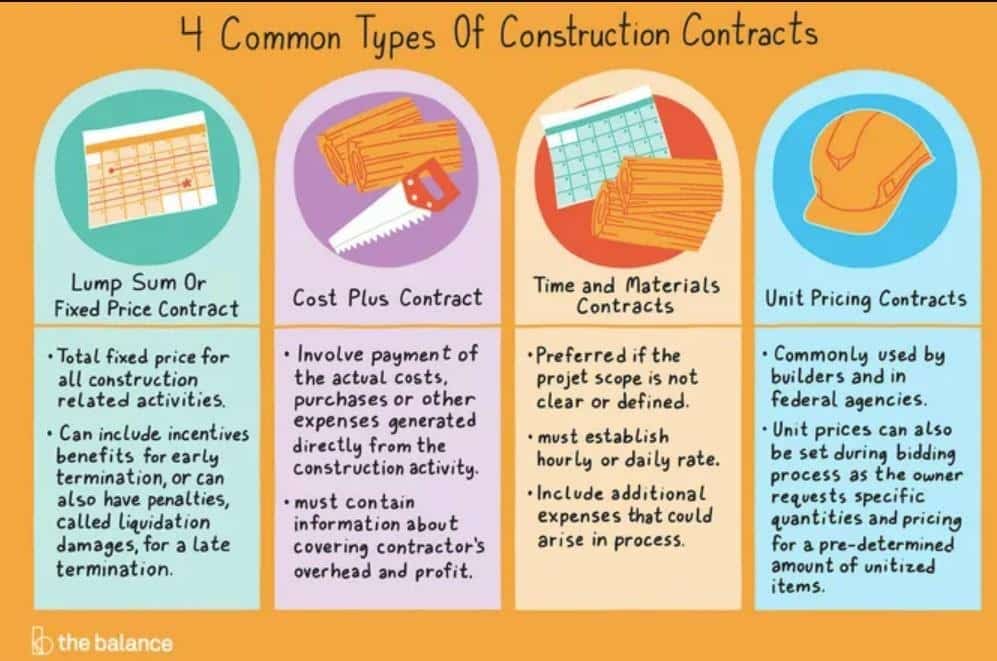
It can seem tempting to skip over footnotes, attachments, or an appendix or two.
However, when a project manager signs a contract, he or she is legally agreeing to the terms set forth by these “fine print” features just as much as what’s in the main section of the document.
Carefully examining each part of the agreement ensures that you understand the scope of the project.
Failure to read or fully understand each term of the contract could lead to costly errors. Lawsuits can become slow-moving resource drains that distract an entire organization from new projects or daily tasks.
Sometimes, neglecting to read a contract results in corrective work, which might disrupt timelines or resources allocated for other builds. Breach of contract lawsuits might also result in court fees, property loss, or fines.
Creating Inaccurate Estimates
It takes effort to accurately calculate the time, budget, and materials your organization requires to complete a job. Conducting research and generating honest projections helps to avoid costly overruns and last-minute panic.
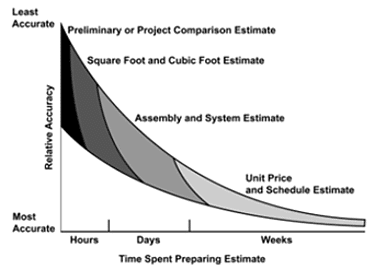
This stage of the project process can involve weeks of work, as this graph indicates. At the same time, committing resources to it enables project managers to provide clients with highly accurate estimates.
Software, particularly asset tracking programs, provides invaluable assistance in accurately projecting resource distribution.
In construction, four different methods can help project managers estimate how much a project will cost.
As the graph shows, the fastest method (preliminary or project comparison estimate) is typically the least accurate, and the most involved and detailed technique (Unit Price and Schedule Estimate) tends to yield more precise calculations.
ESTIMATING METHOD | DESCRIPTION |
Project Comparison/Parametric Cost | Used when the project manager has few details about the project and so relies on data from similar projects; usually, 15-25% accuracy |
Square Foot/Cubic Foot | Effective when floor area and volume are known. More accurate when unique conditions are adjusted for. |
Assembly and System | Prepared from design drawings. Uses trade and subcontractor costs/estimates. |
Unit Price and Schedule | The project is divided into sections, with a cost for each piece or stage. |
The process of cost estimation also involves collecting accurate information from subcontractors. These figures will play into setting realistic goals and allow you to maintain accountability throughout the course of the project.
Knowing your subcontractor’s capacity to complete the job is crucial for effective management. Collecting references and examples of work on similar projects is key.
While historical data can provide a useful guideline, it’s imperative to remember that each project is different—even when undertaken in similar conditions.
For example, constructing a house in a development where you’ve already worked means that you have useful experience to apply.
However, the needs and expectations of the client are likely different, the lot might offer its own challenges, and labor costs could have fluctuated.
“Knowing what you don’t know” is essential even when compiling estimates for comparable jobs.
Failing to Create a Risk Assessment Plan
Risk assessment is the act of seeking out possible hazards, then analyzing how to mitigate or avoid them. It is vital to promote a strong safety culture and provide control measures.
Risk assessment involves five steps:
- Identifying potential hazards
- Evaluating risks using a risk matrix (see below)
- Determining what measures will mitigate the risk
- Documenting, tracking, and analyzing data or findings
- Regular review and adjustment of controls
Building a risk matrix involves applying analysis and data to determine the dangers of a given situation, as well as the potential outcome. Speaking to employees involved in performing various tasks will help you assemble a realistic risk matrix.
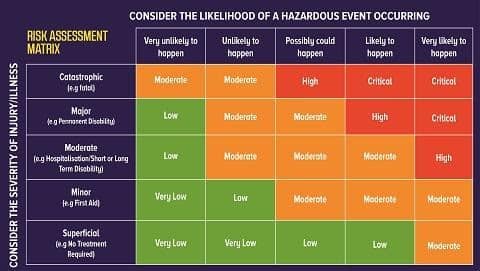
Above is an example of a risk assessment matrix. As you can see, it shows the likelihood of various hazardous events.
Some project managers might commit the error of thinking that the establishment of a risk assessment plan is all that’s necessary to meet safety standards, but it’s just as essential to maintain and enforce those standards for the duration of the project.
A major component of this is ensuring proper safety training and reminders. Visiting the site frequently and unannounced can help to keep workforce members mindful of safety standards.
It also allows you the opportunity to identify new risks, clarify protocol, and answer questions about changing conditions.
Not Setting up an Efficient Ordering Process
Some project managers study the contract, establish a realistic estimate, and form a sensible risk assessment plan only to hobble themselves by failing to set up an efficient ordering process.
With the aftermath of COVID 19 and labor shortages continuing to plague the worldwide supply chain, the ability to rely on an automatic but flexible ordering process is essential.
Well-trained employees and prudent timelines are of no good to a project manager who doesn’t have materials and equipment for them to use.
While some contractors have the foresight to supply the likes of concrete, lumber, and steel, others dismiss the necessity of ensuring the correct machinery is available at the proper time.
Anticipating all major needs, and the market forces that might affect acquiring them at the appropriate time, often present a planning nightmare.
Software solutions such as GoCodes Asset Tracking assist contractors with this crucial task.
GoCodes Asset Tracking uses tracking technology to seamlessly monitor critical material levels, and to alert necessary personnel when stock is running low.
The system can also send order alerts for materials at a pre-determined trigger point, eliminating the need to allocate precious resources and time to checking supply levels.
Real-time GPS tracking lets team members know which products are on the way, as well as where they are in the delivery process. These advancements keep the entire team up to date on time-sensitive deliveries and resource allocation.
This video describes how GoCodes Asset Tracking tracks usage patterns and projects when to re-order certain items.
Another aspect of efficient ordering is keeping track of your fleet, ensuring that vehicles are available when your company needs them.
The best way to sustain a healthy fleet is to provide regular preventative maintenance and attend to all issues as soon as they arise.
GoCodes Asset Tracking assists construction professionals by electronically storing operator’s manuals, providing equipment breakdown statuses, and updating easily searchable maintenance records.
In addition, GPS tracking and fencing offer real-time security updates to ensure that your equipment and vehicles stay where they belong.
Communicating Ineffectively
Since the construction industry tends to struggle to keep pace when it comes to digitalization, maintaining instant communication can be frustrating when working with multiple parties on a far-flung and complex project.
Even if workforce members frequently use digital technology, jobsites might not provide an adequate signal to provide cellular communication or large-file transfers.
But sometimes, communication blocks don’t stem from hardware or signal strength.
Poor communication practices can plague a project from its first moments, and yet maintaining respectful, regular means of raising issues helps to ensure a healthy work environment.
Here are a few suggestions for improving communication in the construction industry:
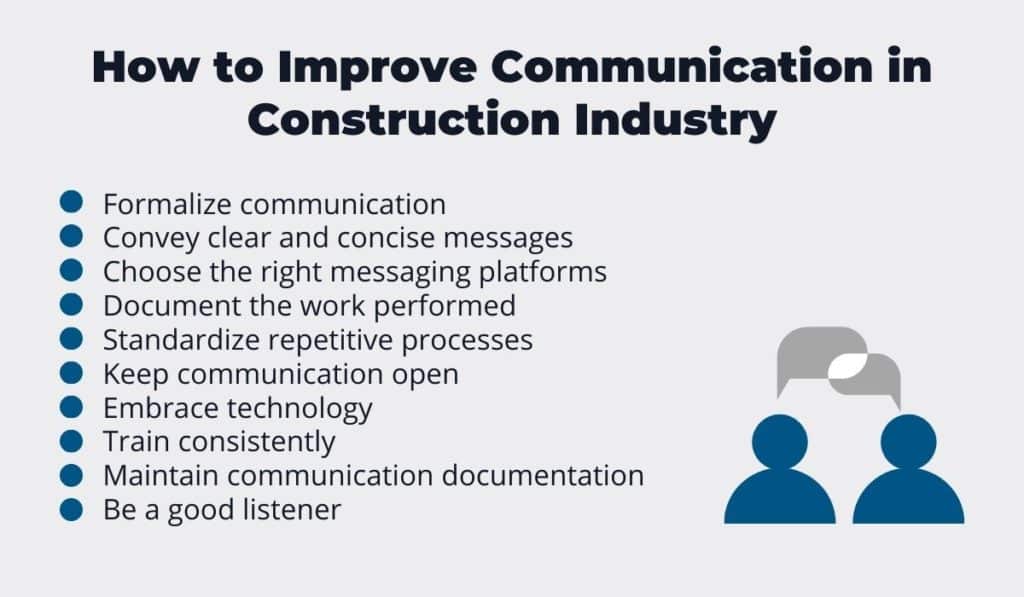
The techniques discussed here are useful, but it’s unlikely that team members will embrace them unless the contractor demonstrates strong communication skills first.
For example, skipping the kickoff meeting between you and the client is never a good idea.
This face-to-face event is a critical moment. It allows an opportunity to iron out last-moment sticking points or questions, and it offers an opportunity to set realistic expectations for everyone involved.
Project managers should also gather subcontractors to ensure that timelines are set and that everyone understands the scope of the work clearly.
At the same time, a kickoff meeting can’t help anyone when the project has already begun, and communication has become lax.
Therefore, ensuring that key members of the team stay in touch via calls or virtual meetings is an important component of ensuring that everyone has raised concerns, issued reminders, and relayed progress reports.
These meetings, when everyone attends them consistently, allow all participants to stay on top of every aspect of the project.
Relying on Insufficient Completion Data
There always seems to be another loose end to snip when it comes to construction projects.
Even more complex, it’s vital for a company, the client, and all subcontractors to have a common understanding of when the project is, in fact, finished.
For example, the client might assume that the contractor will arrange for landscaping when heavy exterior work is over.
But if there’s no specific mention of this in the contract, the project manager will not have made arrangements for grass seeding or major planting.
Therefore, agreeing to endpoints is an important part of a shared scope-of-work vision.
Project timeline templates, using up-to-date completion data, help provide a visual idea of how a job is unfolding.
Here’s a model:
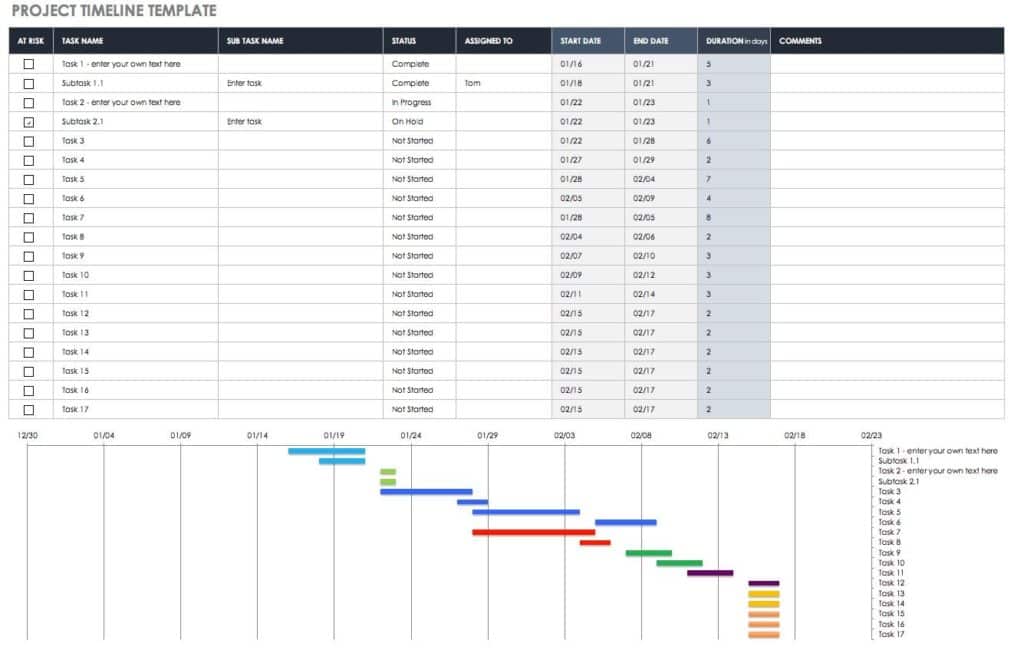
Sharing documents like this keeps everyone apprised of progress and future goals.
As the project unfolds, contractors and clients can agree on pre-set tracking deadlines. These provide definite milestones for the client to understand, while the project manager has useful hard dates for planning materials and labor allocation.
Without these landmark moments, the project can seem to drift endlessly along.
It’s easy for mismanagement to creep in when timelines suffer delay after delay, even if the project manager is not at fault.
Subcontractors still require payment on time, and failing to meet paycheck deadlines is a recipe for an unhappy crew and a ready worksite without workers.
Committing to a strong finish on closeout documents and final steps is impossible without accurate and updated data.
Conclusion
Setting your enterprise and work apart from other construction businesses might seem difficult at first.
However, paying attention to seemingly skippable steps or small details creates repeat clients and excellent word-of-mouth recommendations.
Understanding contracts and expectations while planning ahead for hazards, crew needs, and equipment distribution are valuable aspects to avoiding common construction management mistakes.
We hope this piece has given you insight into what issues to be on the lookout for when managing construction projects, as well as how to deal with them.