Key Takeaways:
- Perpetual inventory and automated replenishment improve accuracy through real-time data and technology.
- Some methods predict future needs based on trends.
- Operational priorities and external conditions dictate the choice of inventory tracking methods.
Managing construction inventory on a single site or multiple projects is no easy task.
It’s not just about keeping your stock levels in check—there’s always a risk of mismatches between the actual inventory and records.
The stakes are high because missing key materials at the wrong moment can significantly impact project timelines and overall costs.
Luckily, inventory tracking helps prevent that.
In this article, we’ll explore 6 inventory tracking methods you can use.
Ready to get rid of the inventory headaches and find the perfect tracking system for your business?
Then join us for a deep dive!
In this article...
Perpetual Inventory Tracking
Perpetual inventory tracking ensures accurate inventory by recording each item whenever it’s received or used.
It is a continuous process, giving you real-time visibility into stock levels and material usage.
Unlike periodic inventory checks, perpetual tracking records every inventory change in real time.
Businesses that use perpetual systems run fewer inventory counts while still getting better accuracy and efficiency than the alternative.
For construction businesses, the biggest advantage of real-time visibility is reduced risk of stockouts and overstocking, plus easier planning for future demand.
If this seems too good to be true, consider that perpetual tracking systems can integrate multiple calculation methods, from FIFO and LIFO to WAC, depending on your business model.
Now, how do you go about setting up this system?
Perpetual tracking could involve spreadsheets or similar makeshift systems, but this would require frequent manual updates and regular physical counts.
While theoretically feasible, it would be very time-consuming, and still prone to errors.
And that defies the purpose.
A real perpetual inventory system centralizes your inventory data to deliver precise inventory counts instantaneously.
To do that, you need at least two things:
- An integrated software system
- Scanners and trackers
Our GoCodes Asset Tracking solution leverages QR codes and a cloud-based system to track construction tools, equipment, and materials in real time.
A seamless check-in/check-out system ensures that every item is logged as it is used or returned while all relevant staff get easy access to a single source of truth.
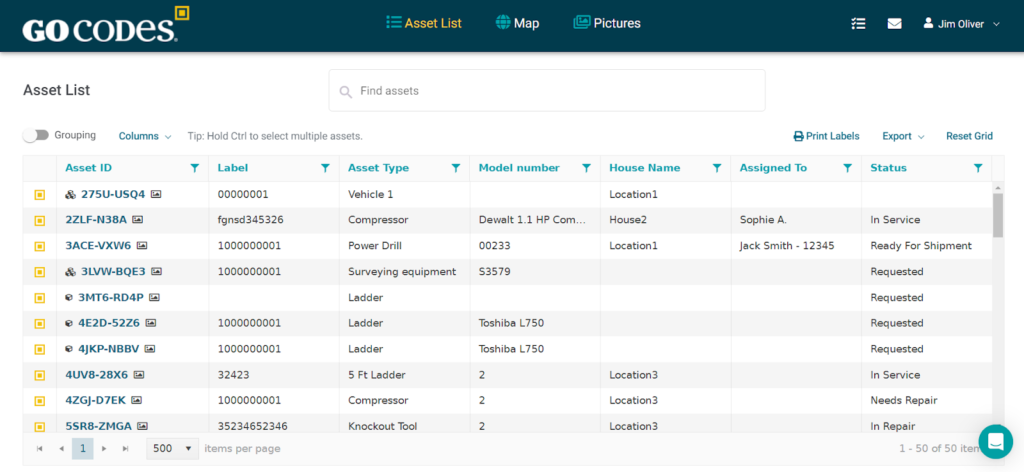
GoCodes Asset Tracking automates inventory management and other processes through various features, such as real-time alerts.
You can use the mobile app to track inventory quantity and easily set up low-quantity notifications and other optional features.
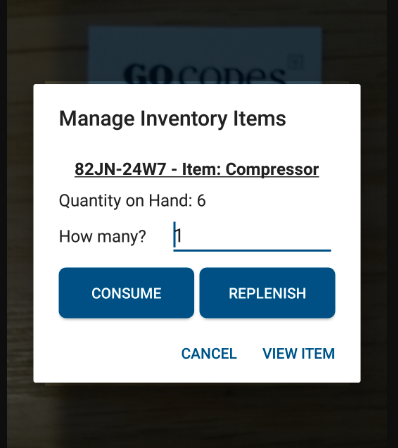
One quick setup and you’ll be reminded to restock on time and avoid shortages and project delays.
To sum up, perpetual tracking supports proactive decision-making, making it virtually impossible for your inventory levels to drop dangerously low.
Just-In-Time Inventory
Just-In-Time (JIT) inventory keeps the inventory levels as low as possible by ordering materials and supplies in line with project phases.
JIT is both a lean construction principle and a core inventory management system that follows project timelines to a tee.
To put it simply, this method enables you to acquire inventory items as needed, often just a few days ahead of time.
This makes it easier for a materials manager to adjust orders based on real-time project needs.
Moreover, you don’t have to grapple with the costs of large storage areas or extra material waste.
Specialized items like HVAC systems or custom steel beams can easily create storage challenges. The same thing applies to perishable or weather-sensitive materials which risk spoilage.
But, you can avoid this, as they arrive just before they are installed.
Finally, thanks to JIT’s low inventory levels, inventory tracking is simpler and less time-consuming, which saves on labor and administrative costs.
Nevertheless, not having stock on hand can turn into a big problem really fast.
If suppliers run into issues and can’t deliver the order on time, you will be in a lot of trouble.
One way of ensuring this doesn’t happen is by working with reliable suppliers.
Lisa Sallstrom, one of the ASCM’s Executive VPs, explains that supplier relationships were at the forefront during the pandemic.
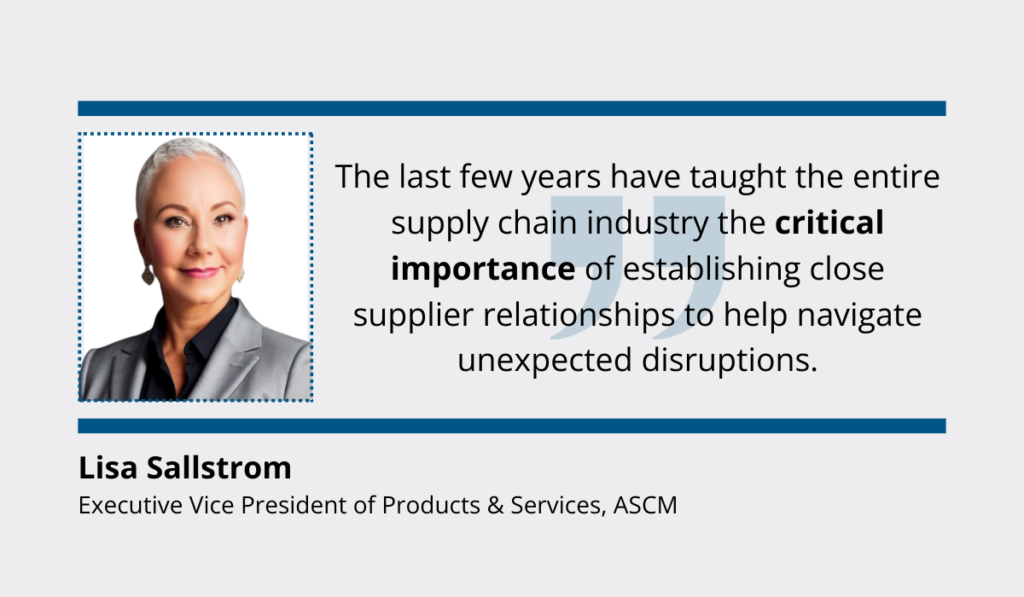
And it rings even more true in this case.
Building long-term supplier relationships is the cornerstone of successful JIT implementation.
That’s the only way you can ensure everything arrives precisely when you need it, and you won’t be hung to dry.
Demand Forecasting
The demand forecasting method predicts future material needs for upcoming projects.
Accurately forecasting inventory is one of the top inventory management challenges because there are many variables you need to consider.
When it comes to making accurate forecasts, you need to rely on several sources, including:
- historical project data,
- project timelines, and
- external market factors.
Anticipating just external factors, such as price increases and weather conditions, can be tricky.
In fact, they constitute a specific subtype of forecasting altogether.
Active demand forecasting | Analyzes dynamic internal (i.e. software adoption) and external shifts (i.e. economic trends, regulatory changes). |
Passive demand forecasting | Relies on historical project data to forecast material needs. |
Short-term demand forecasting | Focuses on immediate needs, seasonal changes, and peak construction periods. |
In all cases, the goal is for inventory managers to align material availability with project timelines by analyzing different sets of data.
Doing so successfully drives efficiency and helps you mitigate risks by improving your decision-making.
But how do you go about it?
If you’re picturing a mountain of records that you need to sift through and manually input everything from past project data to weather forecasts and likely regulatory changes, don’t worry—that’s not the way to go.
The digital age has brought new advances, making intelligent demand forecasting systems available to construction companies of all sizes.
Simply put, tracking and analyzing large amounts of data has never been easier.
Jenny Freshwater, Former VP of Forecasting & Capacity Planning at Amazon, explains how machine learning and AI deliver superior results compared to human forecasts.
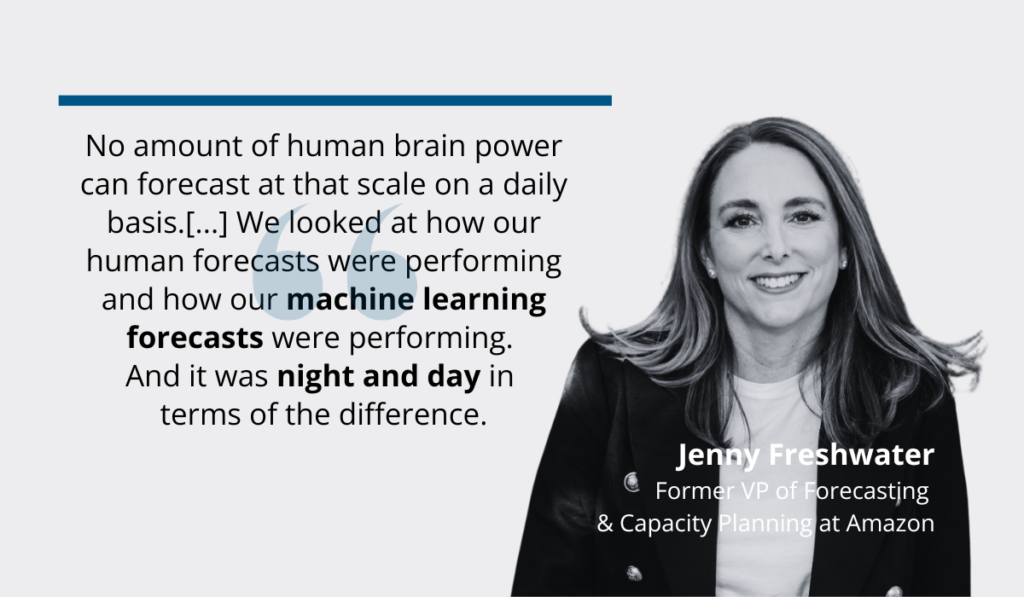
The advantage of these models is that they can identify patterns and trends in huge datasets and actively learn, delivering increasingly better forecasting.
You’re probably thinking: “But we’re no Amazon, do we have to make this switch?”
The answer is yes and no.
Intelligent systems are a must in this day and age, but this doesn’t mean you must jump to machine learning immediately.
Instead, it’s more important to implement these key forecasting practices.
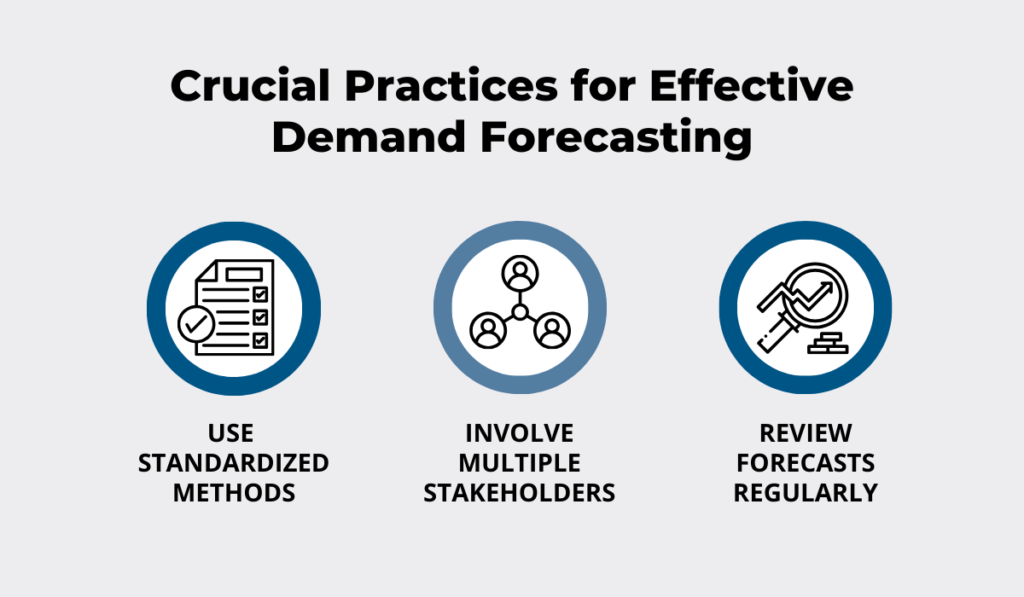
When collecting data, ensure the methods, formats, and units follow the same standard across all project sources.
That way, you’ll have it ready for analysis in a jiffy.
Next, don’t forget to collaborate with project managers and other stakeholders!
Extracting data is important, but if you want the full picture, you need to involve key figures who have the best understanding of the on-site situation.
Finally, any changes in project scope, timelines, and budget need to be reflected in the forecasts, and for that, you need regular reviews.
Making the most of this inventory tracking method requires continuous analysis of data, strong collaboration, and swift adjustments.
Automated Replenishment
Automated replenishment systems use software to help you monitor inventory levels, but take it a step further by automatically reordering necessary materials.
It does exactly what it says on the tin—once the predefined reorder level is reached, the software automatically replenishes inventory to ensure optimal stock levels.
This is similar to perpetual inventory tracking.
Both methods leverage real-time data and technology, giving you a constant and accurate view of stock levels and delivering key inventory management benefits which are listed below.
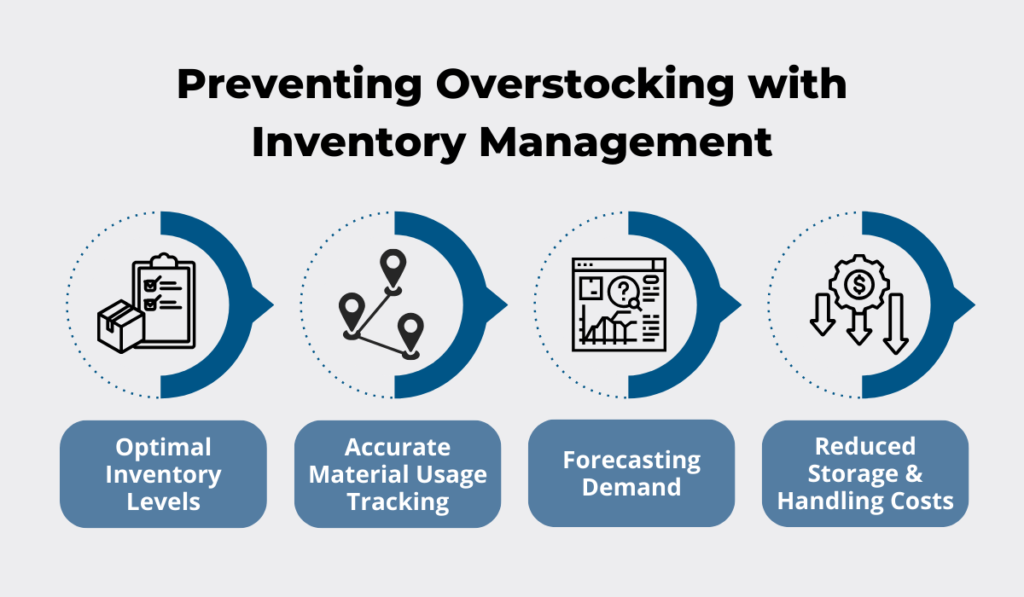
The difference is that automated replenishment systems take it a step further by automating the reordering process.
You decide the conditions for triggering new orders, eliminating stockouts, and ensuring operational continuity.
Such automation boosts your efficiency while reducing any chances of manual errors.
Not to mention that it cuts down on labor costs.
Of course, there are various methods to determine when the orders will be triggered, and it all depends on your projects.
For example, if you have a steady demand for a specific material, it’s best to define minimum and maximum replenishment thresholds to stay within the desired range.
Meanwhile, companies who’ve adopted a leaner JIT system should go for JIT replenishment, making sure that the orders are aligned with timelines or immediate project requirements.
Automated replenishment also overlaps with demand forecasting, enabling you to use historical data and forecasting models to predict future needs.
Replenishment software tools like Leafio can generate over 1,000 orders a day purely based on forecasts.
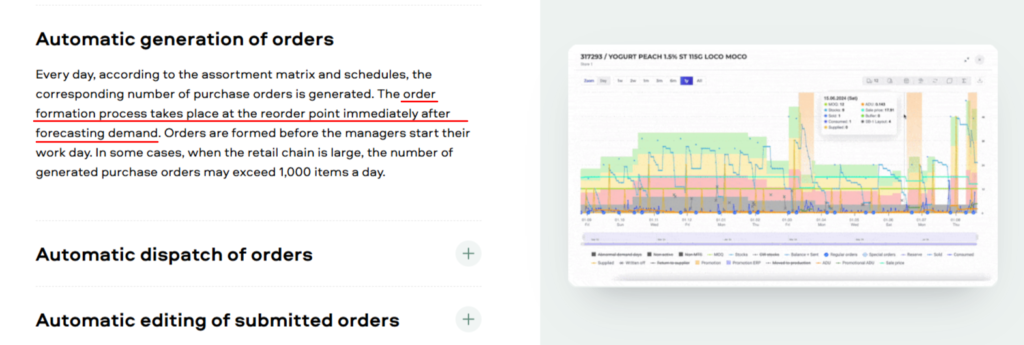
Naturally, different functionalities serve different needs.
A construction business won’t place the same volume of orders as retail but would benefit from supplier monitoring and seamless integration with existing software.
The bottom line is this: If you want to gain real-time insights and speed up processes, the automated replenishment tracking method is the way to go.
ABC Analysis
ABC analysis helps you track inventory by dividing it into three groups based on value and frequency of use.
In this way, businesses can easily prioritize their highest-value items while still keeping track of less important ones.
Each letter is assigned to one priority category, starting with A for critical inventory.
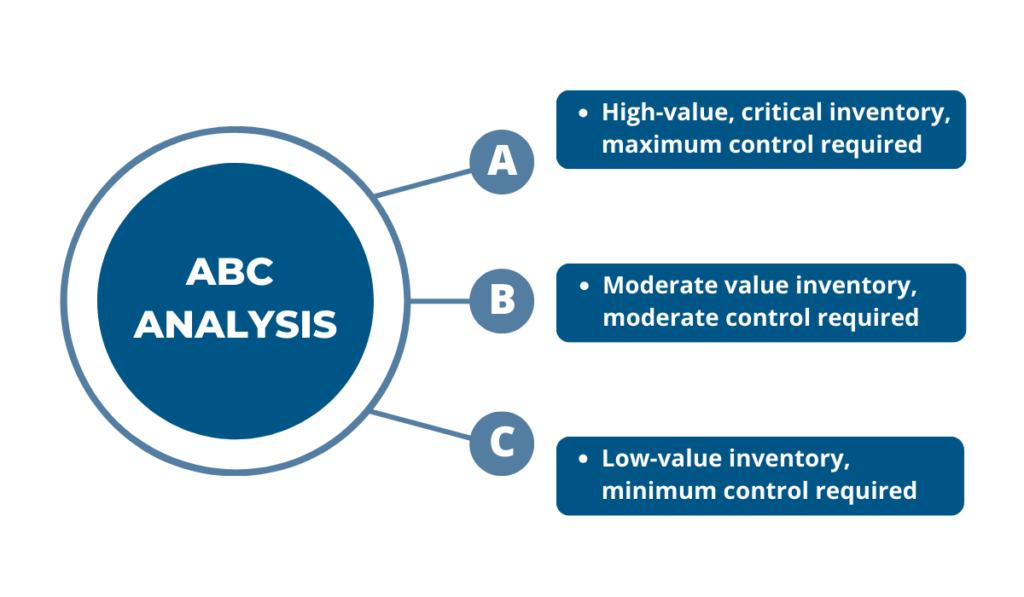
So, how do you know which item falls under which inventory category?
The key is to determine each item’s annual consumption value, which includes:
- units sold,
- inventory value, and
- holding costs.
The analysis relies on Pareto’s 80/20 rule, helping you pinpoint the 20% of goods that yield around 80% of the value, and divert your key resources there.
Here’s how this breakdown would look according to Netsuite.
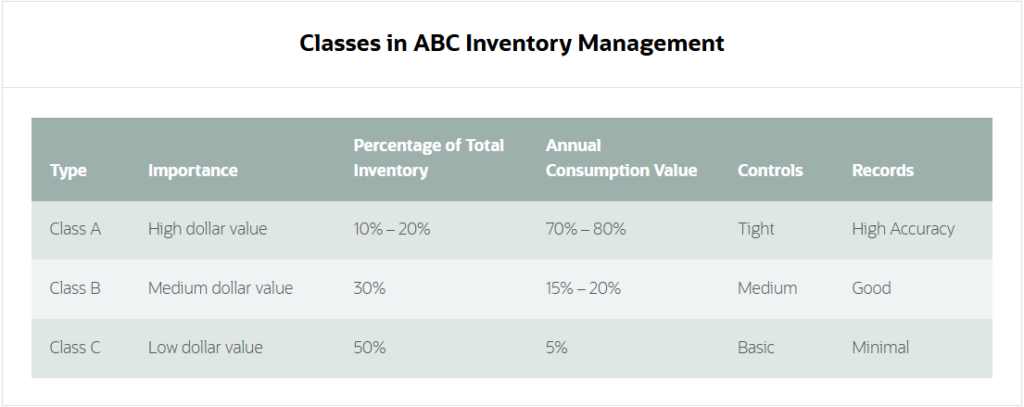
Following this framework ensures that critical tools and materials are always accessible across multiple job sites.
ABC analysis supports an in-depth understanding of all stock.
However, all three priority categories should be checked and revised regularly.
Of course, some materials or assets are more likely to hold critical value, but every project requires some fine-tuning.
After all, if you’re categorizing your inventory based on item value, you need to be ready to account for any changes in their demand, value, or importance.
As sourcing and supply chain expert Mukesh Negi puts it, you need to go beyond ABC’s inherently static classification and cultivate adaptability.
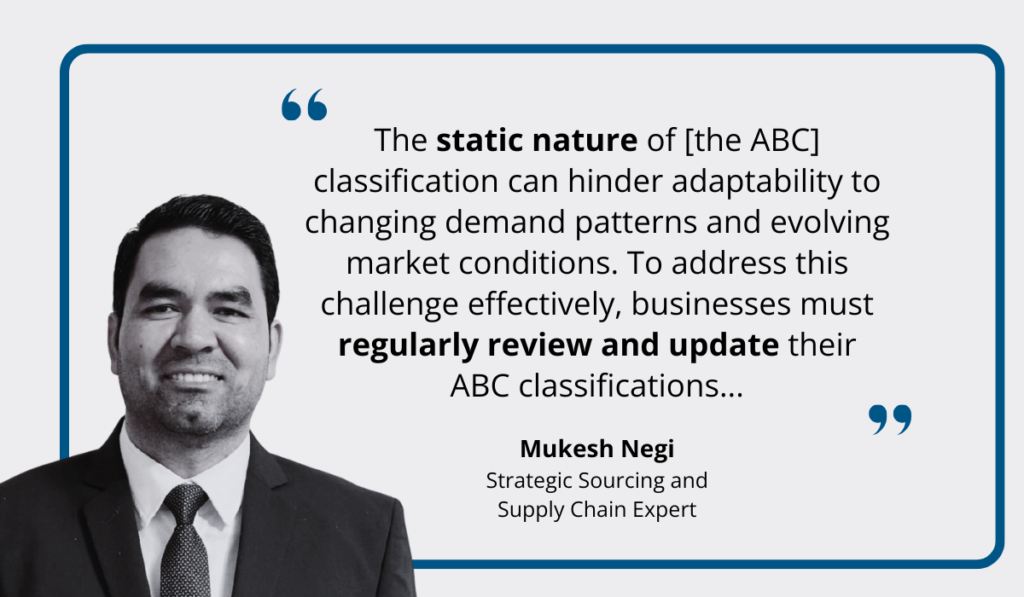
Regular updates of ABC classifications ensure you’re always focusing on the most impactful items and can meet evolving project demands.
To recap, here’s what you need to do to implement this inventory tracking method:
- Gather relevant and accurate inventory data
- Review sales & demand records to establish value
- Run the ABC calculation and categorize your stock
- Develop policies and SOP’s for managing each category
ABC analysis is an excellent inventory tracking method that will help you concentrate your efforts on items that are crucial for your continued success.
Economic Order Quantity
Finally, we have the economic order quantity (EOQ) formula, which helps you determine the optimal order quantity while maximizing cost-efficiency.
As the name implies, the EOQ formula puts a lot of emphasis on the financial side of things, helping you reduce frequent ordering costs.
Your starting point is to understand how the costs of a specific item add up, says Masood Saeed Khan, Management Consultant at a Dubai-based accounting firm, GFinSer.
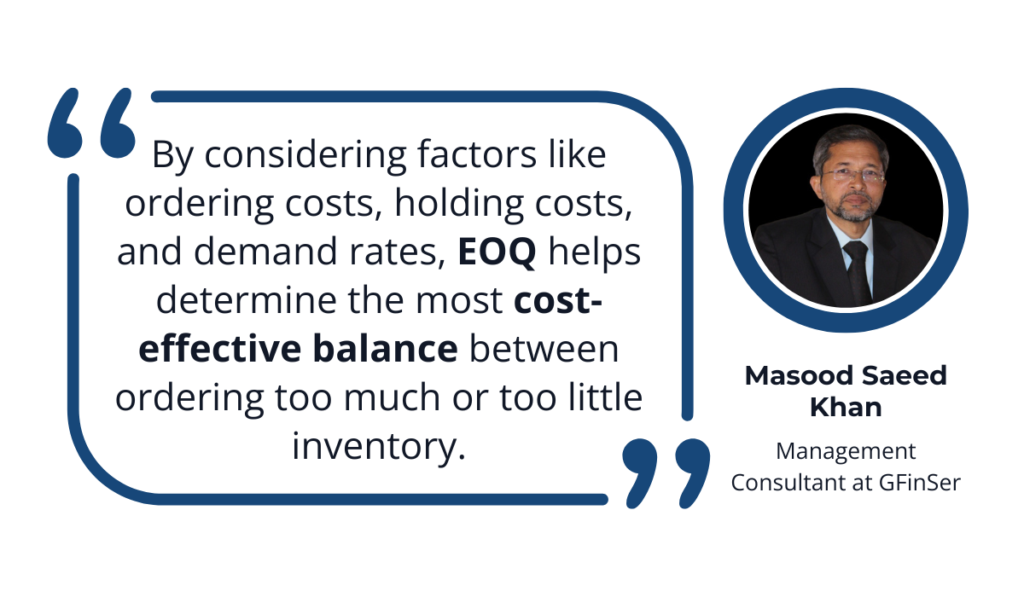
Finding the most cost-effective balance between holding and ordering costs begins with a simple formula.
EOQ = √(2DK / H)
Here are the three key values to take into account in stock-level optimization:
- D represents setup costs such as shipping, handling, and administrative expenses.
- K is the demand rate i.e. the quantity of goods required or sold annually.
- H stands for holding costs, calculated per unit and per year.
Since the formula helps companies prevent excess stock and reduce inefficiencies, this can lead us to draw parallels between EOQ and the JIT method.
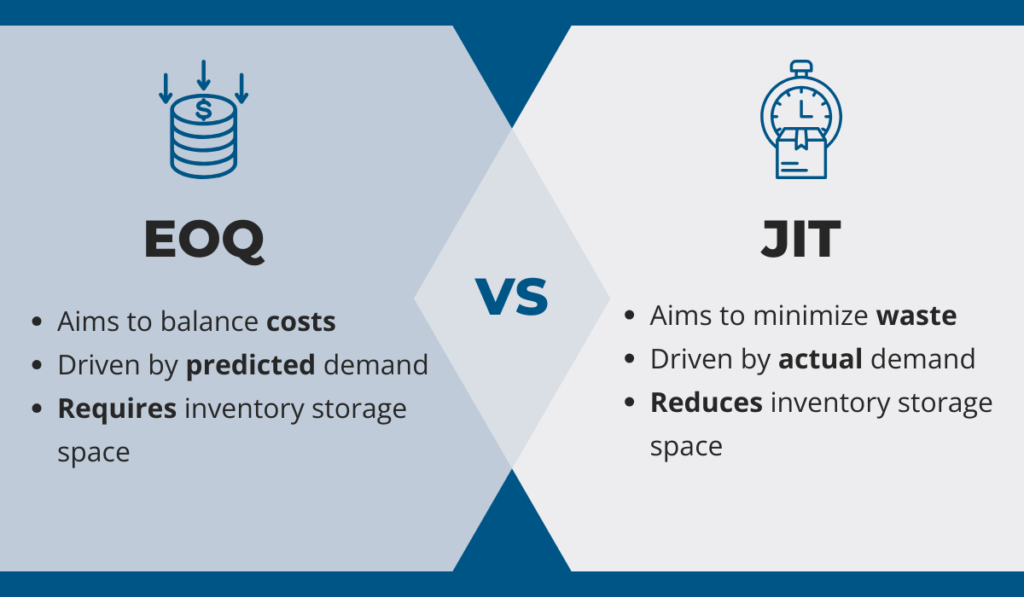
As you can see, both methods look to eliminate waste and save costs, but they’re different in how they address inventory levels and timing.
For instance, the EOQ method is a perfect fit when you’re ordering bulk materials that have fairly predictable demand, such as cement or bricks.
In these cases, ordering in optimal quantities saves costs and ensures availability without overstocking.
As such, it’s recommended you integrate EOQ with the company’s project scheduling for seamless procurement.
JIT, on the other hand, observes immediate demands and discourages large stockpiles entirely.
This difference also impacts your risk management strategy.
Thanks to its buffer inventory, EOQ is more resilient to supply chain disruptions, allowing companies to maintain steady operations even if there are procurement delays or other issues.
This is much different from JIT’s reliance on precise timelines and flawless supplier coordination.
In the end, EOQ is the preferred method for balancing procurement and storage costs while keeping the risks at bay, which makes it a valuable tracking method for any construction business.
Conclusion
And there you have it!
Construction inventory tracking isn’t a one-size-fits-all solution, but a dynamic process that requires continuous monitoring and plenty of forethought.
With this article, we gave you a glimpse of the methods that would benefit every construction business toolbox.
Finding success means unlocking the right combination of tools and techniques for your business model.
Do this, and you’ll gain data-driven insights that will enable you to meet project demands confidently all while staying within budget.
Remember: your inventory challenges don’t stand a chance against careful planning and execution.