Key Takeaways:
- Poor project planning is the main cause of delays in construction and hinders productivity on the construction site.
- Ineffective budget and material management can put projects on hold.
- A lack of communication among stakeholders makes it difficult for construction teams to be productive, stick to deadlines, and avoid budget overruns.
Who wouldn’t love to see their job sites and workers buzzing with productivity every single day?
After all, that’s the key to finishing projects on time, staying within budget, and, ultimately, achieving success in construction.
But let’s be real: there are countless obstacles that can throw a wrench in your operational efficiency.
That’s exactly what we’re diving into in this article.
We’ll uncover the challenges that often slow things down and share some useful tips to tackle them head-on.
So, keep reading and get ready to take your productivity to the next level.
In this article...
Ineffective Project Planning
In construction, productivity is often hampered long before the first shovel hits the ground.
If you don’t dedicate enough time to pre-construction planning or rush through it, you’re bound to run into issues with scheduling or resource conflicts, and ultimately face project delays.
Cornerstone Projects has the numbers to back this up.
According to their survey, poor or unrealistic planning and scheduling are the number one causes of delays in construction.
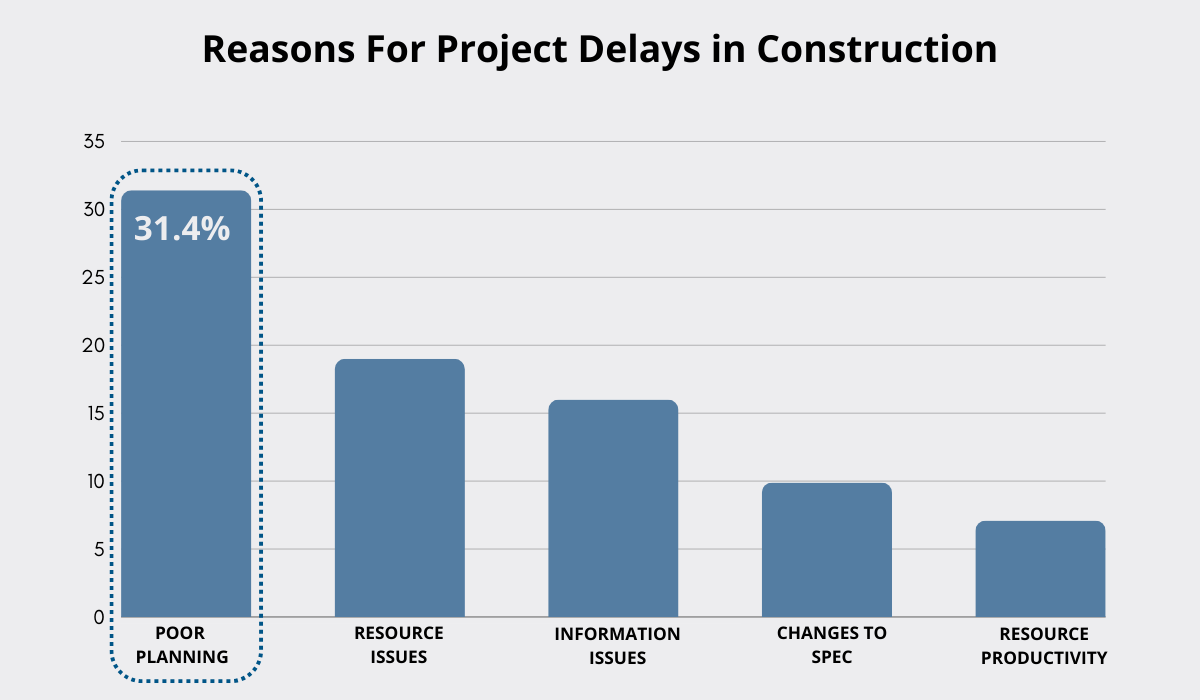
Think about it: if you don’t fully consider your project’s scope and needs, or set overly ambitious deadlines, you’re setting yourself up for trouble.
Falling behind schedule and watching productivity plummet is a natural consequence.
To avoid these problems, ensure enough time is dedicated to planning, and that it’s done right.
Use a Work Breakdown Structure (WBS) to organize all the tasks that need to be carried out from the project’s start to finish.
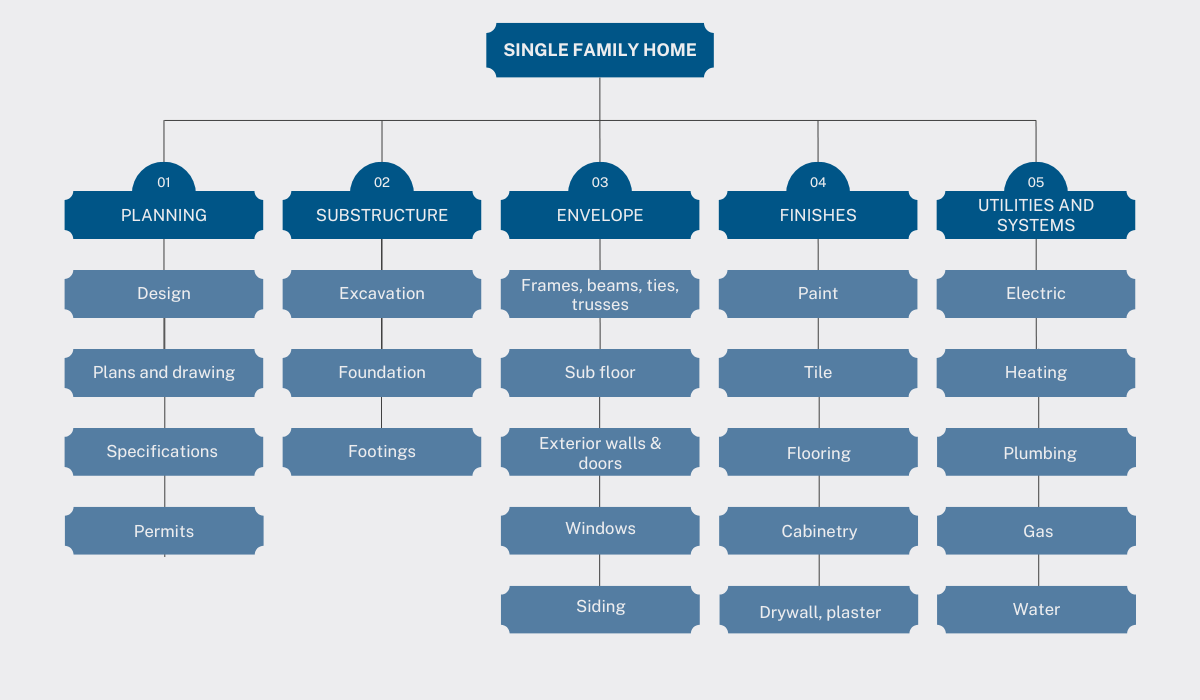
This way, the entire process will be divided into more manageable chunks, giving everyone a clear visual roadmap of objectives and timelines.
In addition to a WBS, you can use the SMART framework to set your goals.
This will provide clarity and direction during planning and make sure your objectives are well-defined and achievable within a specific timeframe.
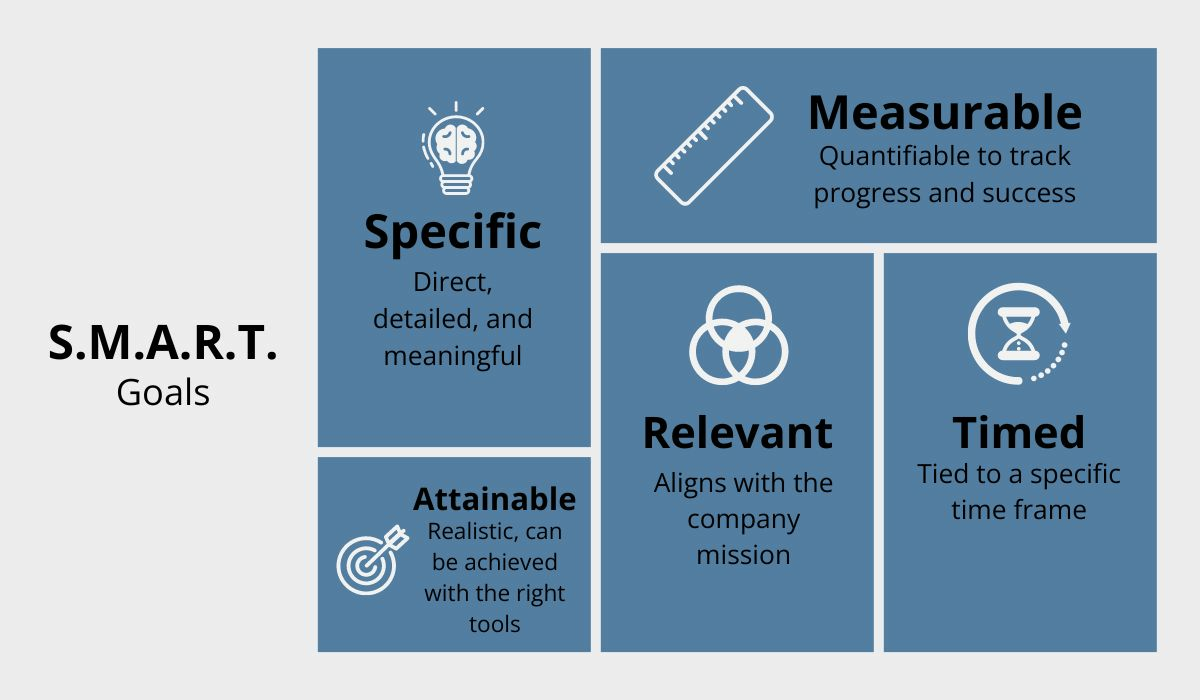
But, how can you check if your goal is SMART?
Let’s say you need to complete the foundation for a building.
To see if that objective is SMART, ask yourself the following:
Is it specific? | Yes, you need to complete the foundation of the new office building you’re working on. |
Is it measurable? | Yes, you need to lay down 200 cubic meters of concrete. |
Is it achievable? | Yes, if you ensure all necessary resources are available. |
Is it relevant? | Yes, because this step is crucial for the overall integrity of the building you’re working on. |
Is it time-bound? | Yes, the foundation needs to be completed within the next four weeks. |
Of course, even the best-laid plans need constant monitoring.
Construction projects are highly prone to sudden changes and unexpected challenges.
By tracking your progress and staying adaptable, you can navigate these hurdles more effectively.
So, invest time in detailed planning, leveraging tools like the WBS and SMART goal framework, while also keeping a flexible mindset.
That way, you’ll steer clear of delays and keep your productivity soaring, no matter what.
Slow Adoption of Construction Technologies
The construction industry has a notorious reputation for lagging behind in technology adoption.
For instance, when Yooz surveyed 600 workers across various industries to rank them by technological proficiency, construction ranked at the very bottom.
But this isn’t just about the industry’s reputation; it’s also a productivity issue.
Avoiding automation and relying on manual, labor-intensive processes ultimately leads to more human error, wasted time, and poor communication and coordination.
Those who embrace technology and digitize their operations, on the other hand, nip these challenges in the bud and boost their overall operational efficiency.
In fact, did you know that, according to the 2024 Deloitte survey, increased productivity is among the top five benefits of adopting new tech in construction?
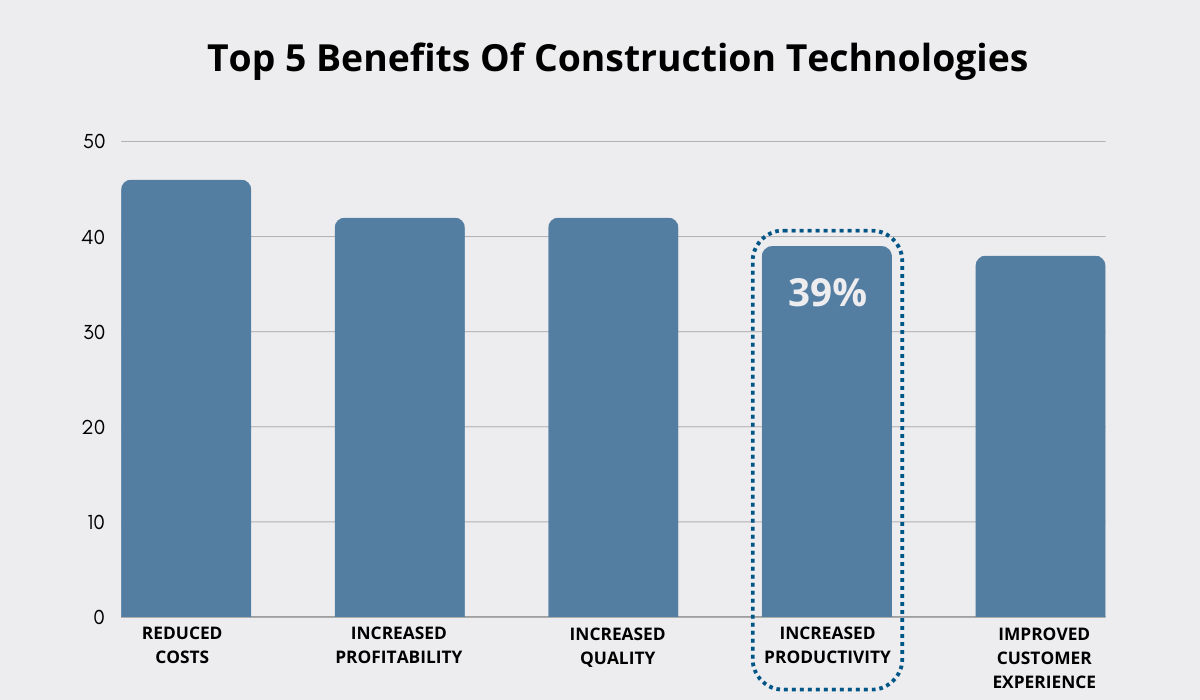
So why aren’t more construction professionals jumping on the technology bandwagon?
Or, more importantly, what can be done to change this?
Cameron Page, CEO of Clearstory, a change order communication platform, gives us a hint.
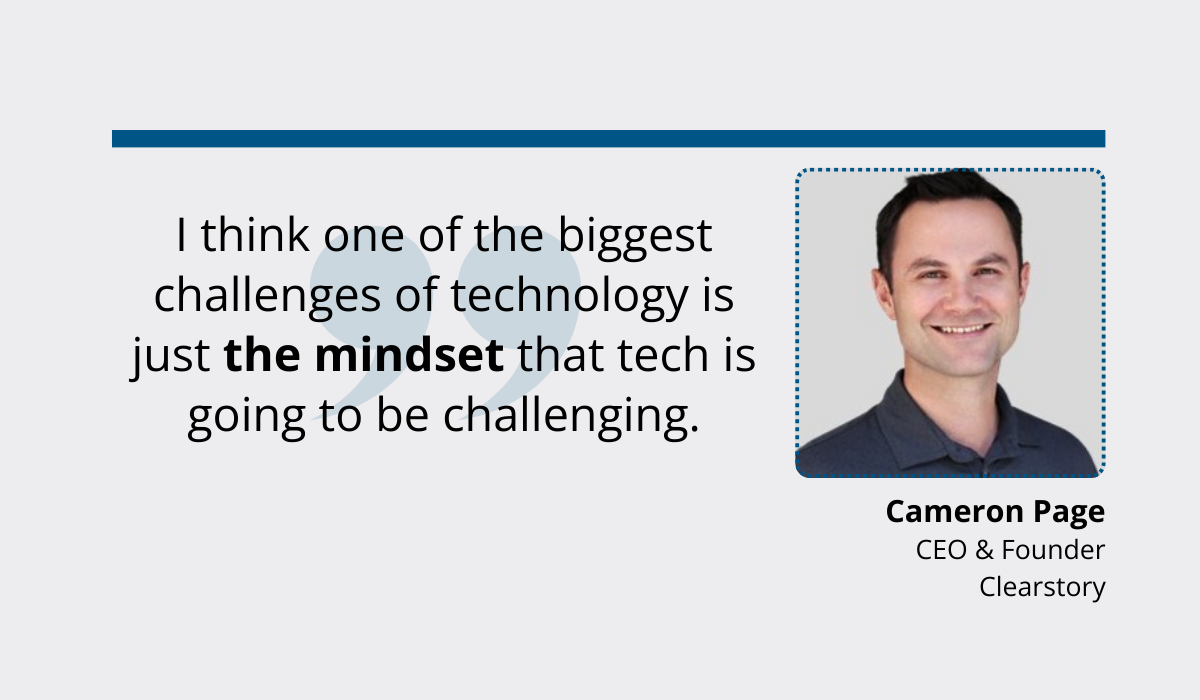
He suggests that the biggest problem is the industry’s perception of technology as too complicated and not worth the trouble.
So, to combat the resistance, it’s crucial to challenge this notion.
The easiest way to do so?
By implementing user-friendly software, of course.
Take GoCodes Asset Tracking, an asset management solution, for example.
It consists of only three elements—software, an app, and QR code asset labels—all of which are super easy to use, even for less tech-savvy employees.
Not only can the system be installed on devices workers already have, but the chances are your team is also familiar with QR codes, at least to some extent.
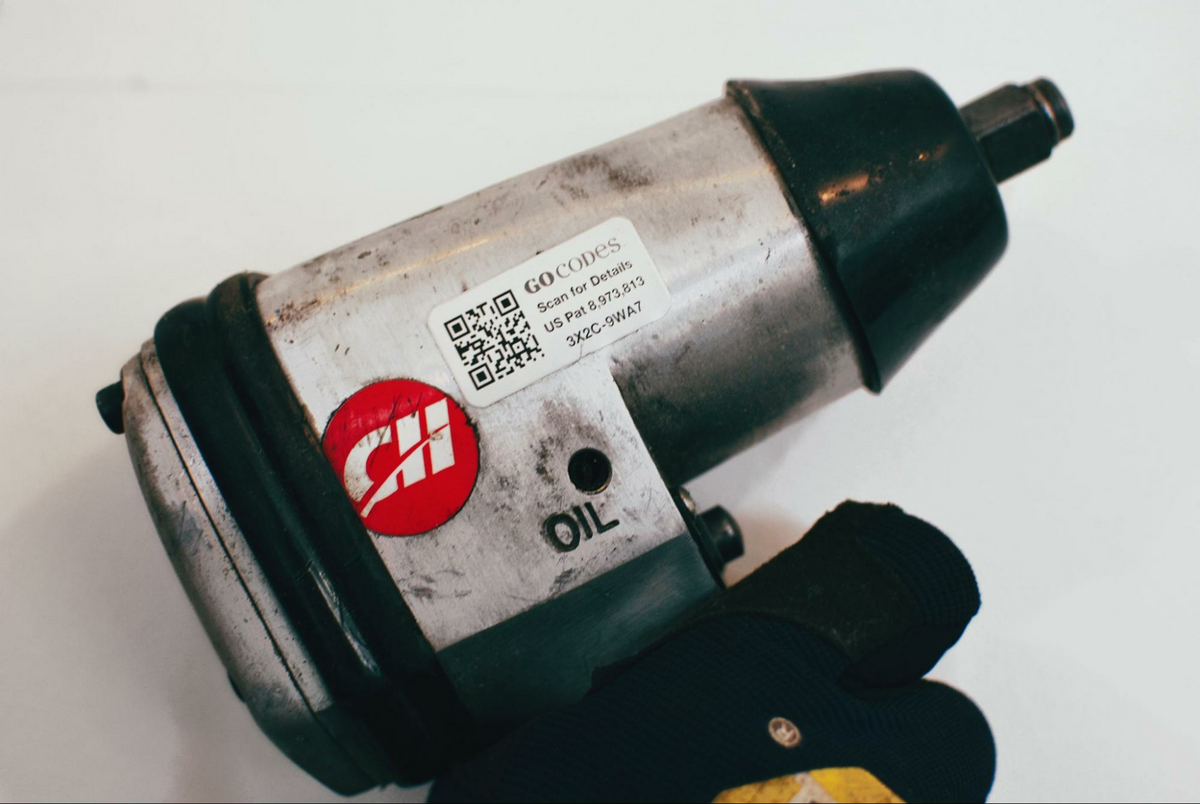
This can make a world of difference during the transition to this new solution.
The system itself is simple to use, too.
You just scan the label with the scanner app, and you can:
- Check an asset in or out
- Assign an asset to a worker
- Schedule maintenance
- Check the asset’s current location or user
- View asset data like usage or maintenance history, salvage value, warranty information, etc.
And if you encounter any issues along the way, we offer dedicated customer service and user tutorials you access at any time on our website.
But don’t just take our word for it by any means: take advantage of the free trial to test the solution yourself.
Explore the features, see what the system can do, and get feedback from your team.
This will help you make a more informed decision and secure employee buy-in, both essential for the successful implementation of new technology.
Poor Budget Management
You may not be aware of this, but poor budget management doesn’t impact just your bottom line or profitability.
It takes a toll on productivity, too.
Without proper budgeting and cost control, or if cost estimations are overly optimistic, budget overruns can easily occur.
This financial strain can then put the project on hold or lead to that dreaded rework.
For instance, if you don’t allocate enough funds upfront for construction materials, you might find yourself cutting corners later.
This could mean buying alternative materials that aren’t quite right for the project or settling for cheaper, lower-quality options.
Sure, that might save a few bucks initially, but poor-quality materials can cause more defects and repairs down the line, slowing everyone down and driving up costs.
Overall, budget management still seems to be a major hurdle in construction.
A survey by the Association of Professional Builders found that almost 40% of residential construction projects go over budget.
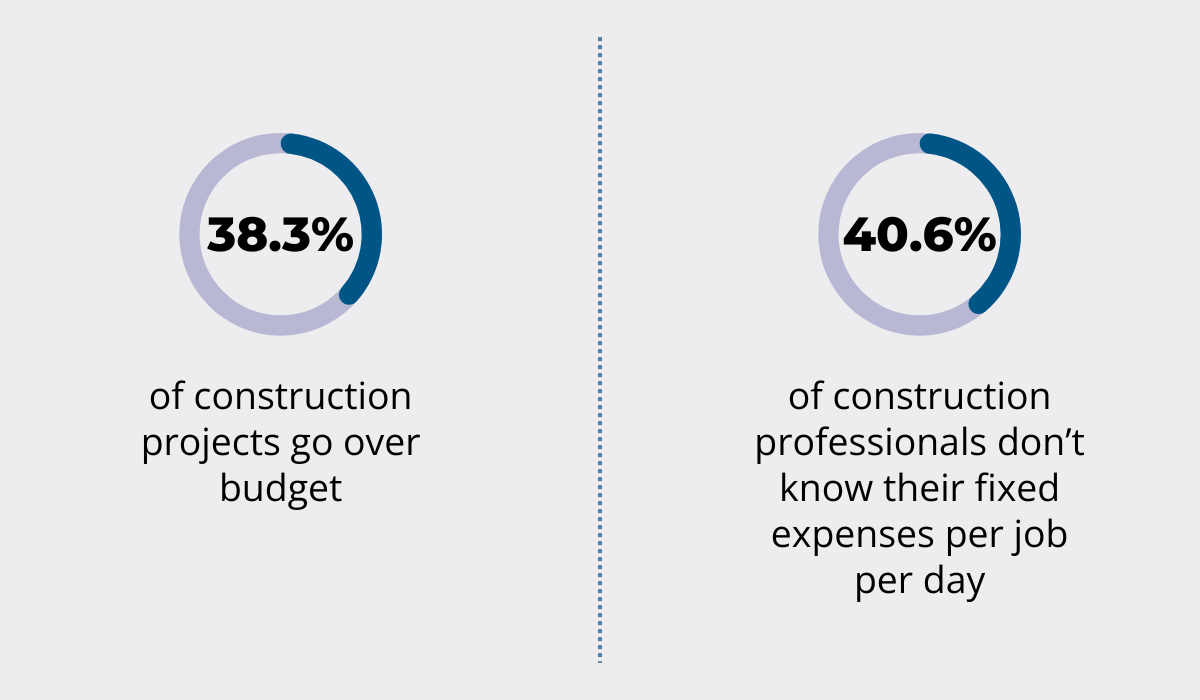
Even more worrying is the fact that 40.6% of those surveyed have no insight into their daily fixed expenses.
How can you manage your budget if you don’t know where your money is going?
This is precisely where vigilant cost control comes into play.
In addition to solid project and budget planning, keeping a close eye on costs throughout the project is a must for budget adherence and smooth operations.
One effective method in this context is checkpoint cost control.
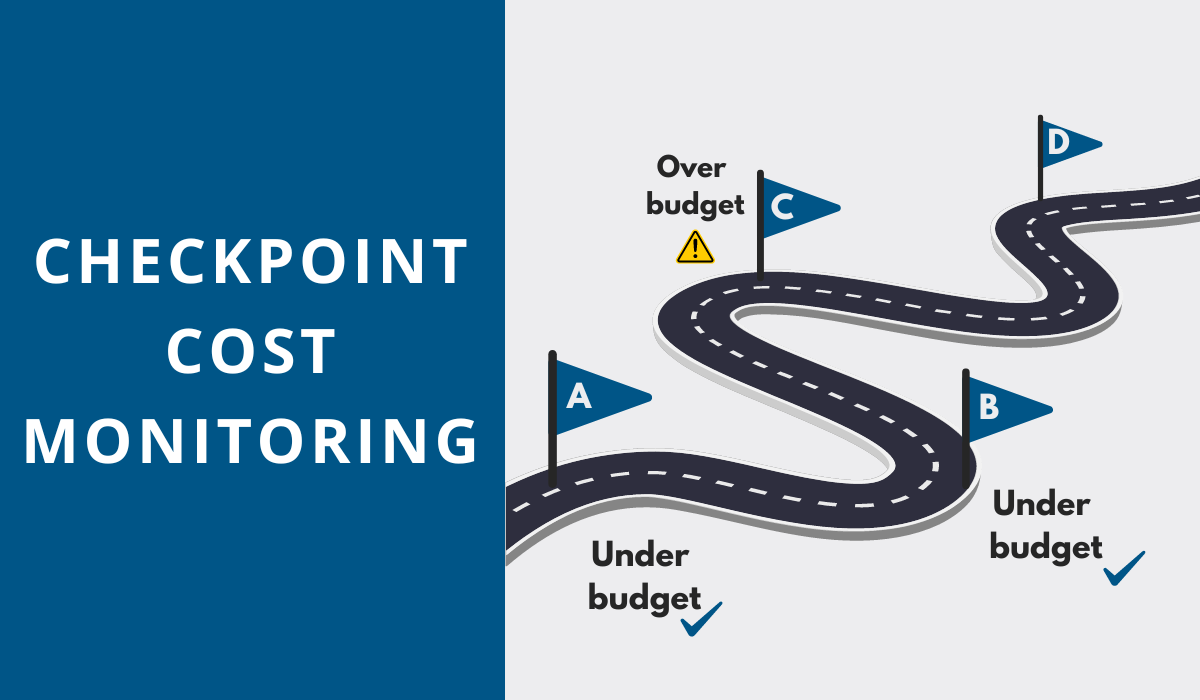
It involves setting up control checkpoints or milestones at various stages of the project, assigning specific budgets to each, and regularly comparing actual costs to these baselines.
This proactive approach helps you spot risks early and address them before they wreak havoc on your budget, and, of course, productivity.
Inefficient Communication
Construction projects are highly complex, consisting of numerous moving parts and involving different stakeholders.
Therefore, if communication falters, the consequences can be severe, with misunderstandings, errors, incomplete information, rework, and delays becoming common occurrences.
Grammarly’s survey provides a revealing look into this issue.
Its results show that business leaders across industries agree that poor communication ultimately leads to decreased productivity, missed deadlines, and increased costs.
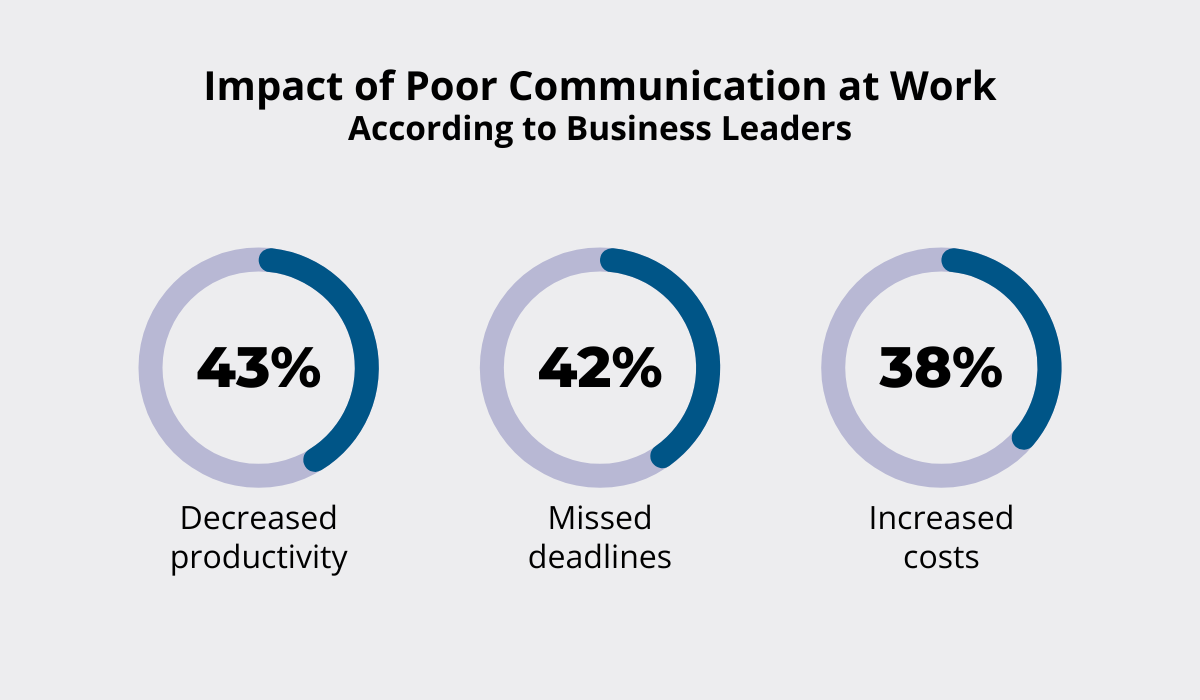
So, how can you sidestep these issues and improve communication?
Start with regular meetings.
But here’s the catch: you need to keep them clear and concise.
Long, drawn-out meetings drain productivity, which is, obviously, the opposite of what you’re trying to achieve.
The goal here is to make sure that everyone is aware of their responsibilities, tasks, expectations, goals, and timelines, but without sacrificing too much of their time.
Next, ensure your technology communicates just as effectively as your team.
More specifically, look for digital solutions that have robust integration capabilities, and can connect with systems used by various other teams working on a project.
This will make coordination and information-sharing much more seamless.
Construction professionals interviewed by JBKnowledge for their report on the use of technology tend to agree.
This is what one of them had to say:
“[I wish I could improve the company I work at with] communication between software systems. Integration would save so much time for our office staff!”
When systems integrate, you get a centralized database, real-time updates, and a detailed record of each of these updates, all accessible to every stakeholder.
Communication, then, immediately becomes more efficient.
The bottom line is this: communication can either be a huge productivity killer or a powerful tool for keeping your project on track and your workers in sync.
So be sure not to neglect it.
Poor Material Management
To create a truly productive work environment, you need to ensure that your workers have the right amount of all the right materials available at the right time and the right place.
Otherwise, you run the risk of encountering either wastage or shortages, eventually leading to unplanned downtime and delays.
For instance, insufficient material or delayed deliveries can halt work progress altogether, while using incorrect materials can result in defects or rework.
And it’s not just about what you order, but about where and how you store it, too.
If your materials are buried in some distant corner of the job site, your team will be burning precious time simply trying to track them down.
Michael McGowan, region head and CEO of Hilti North America, a global leader in construction technology, agrees that tracking resources can be a real productivity killer.
“Our research shows that each job site loses on average one day per month of productivity due to workers searching for tools. In addition, the contractors end up spending up to 90 hours per month tracking tools: in essence, productivity loss for both workers and contractors due to lack of an effective asset/tool management platform.”
While he specifically mentions tools, the same principle applies to materials as well.
Workers must know which resources are available, as well as where they are, and be able to get to them fast.
Part of the solution, once again, lies in thorough project planning.
You should always assess project requirements thoroughly, considering factors like inflation or potential shortages, and incorporating allowances into the project estimates.
The allowance refers to the amount of money that’s set aside for covering unexpected material wastage and its subsequent reorders.
Below, you’ll find recommended allowable wastage for various construction materials.
Cement | 3-4% | Cement can fly in the air when mixed with other materials |
Structural steel | 12-15% | Wastage happens during cutting and bending |
Coarse Aggregates | 6-8% | Some pieces may fall off during transportation |
Tile | 1-2% | Tiles can break during work, but this rarely happens |
Granite | 8-12% | Similar to tiles, it can break during work or transport |
Reinforcement steel | 4.5-6% | Happens during cutting and bending process |
Bricks | 3-4% | Mostly happens during transportation |
Paint | 3-4% | May fall off when applied to the wall, but proper work behavior can control it |
This list can guide you in determining allowances for upcoming projects.
Of course, you also need to keep a close eye on the use of materials throughout the entire project.
Here, just like McGowan said, asset or material management solutions like GoCodes Asset Tracking come in handy yet again.
With a simple scan of the asset label, you can instantly update the quantity of the item, ensuring inventory records are always accurate and up-to-date.
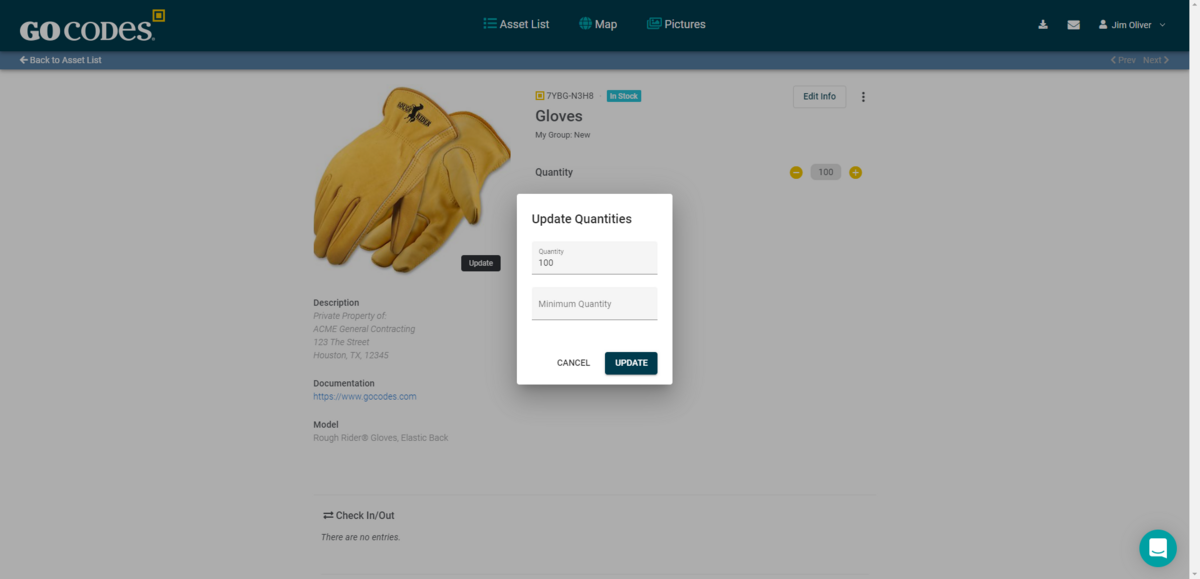
Plus, the system can issue low-quantity notifications, so that you can reorder your materials on time and avoid any unnecessary downtime.
At the end of the day, materials are at the core of construction projects, both figuratively and literally.
Mismanagement of these resources adversely impacts workflows, budgets, timelines, and overall operational efficiency.
Safety Violations
Safety violations not only pose a risk to your workers but also lead to various issues that ultimately cause a drop in productivity.
For example, they can easily result in injuries among employees, causing them to miss work.
As a matter of fact, according to research by Travelers, a leading workers’ compensation carrier, the construction industry has the highest average of missed workdays per injury.
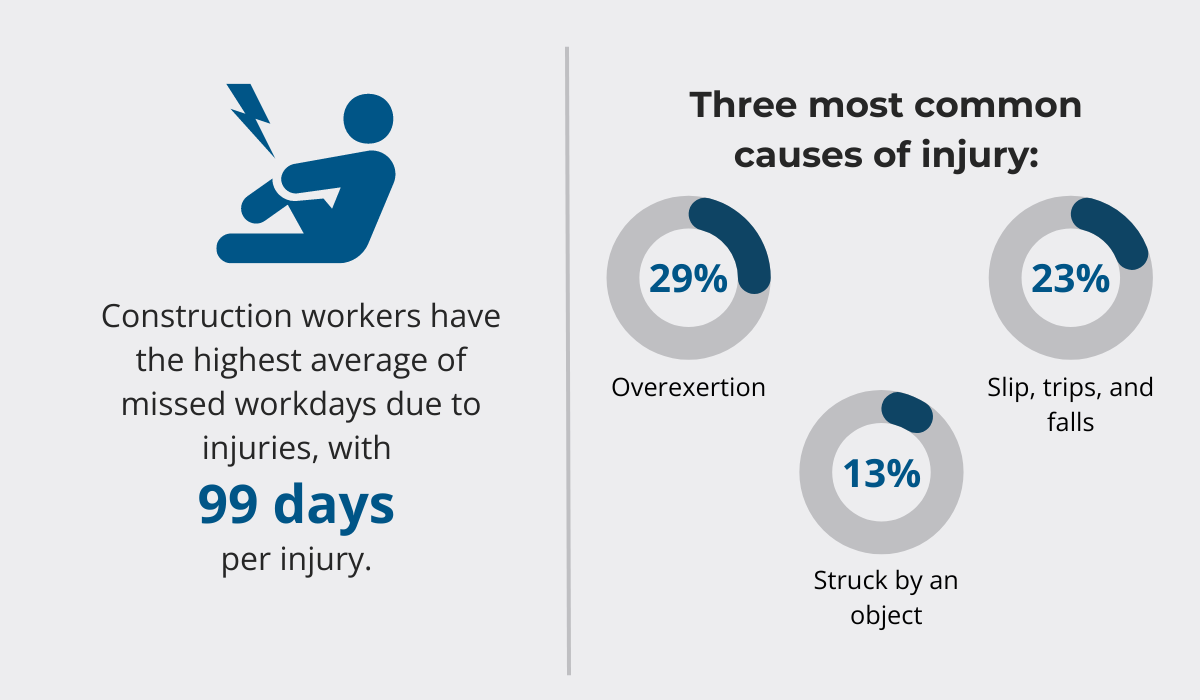
The causes of these injuries?
They include slips, falls, trips, or being struck by objects, all of which are often due to a lack of safety protocols or failure to adhere to them.
But that’s not all.
Safety violations can also lead to prolonged downtime due to repairs, inspections, and investigations, as well as damage to equipment.
Additionally, when accidents occur, retraining may be necessary, even further consuming time that could be spent on work.
Therefore, to keep safety violations to a minimum, follow these three steps:
Conduct frequent compliance audits | Regularly inspect your workers, equipment, etc., to ensure compliance with all regulations and laws, such as those of OSHA. |
Invest in the training of your employees | Educate your team about safety rules or protocols, as well as how to act in case of an accident. |
Stay informed about developments in safety | Stay on top of industry news and changes in laws to remain compliant and well-informed about the latest safety tools and methods. |
By sticking to these strategies, you’re not just ensuring safety compliance, but also fostering a culture of safety where each team member actually cares for everybody’s well-being.
The result?
Your workers stay safe and sound while on the job, and your operations keep running efficiently and with minimal disruption.
Talk about a win-win situation.
Conclusion
All in all, achieving peak performance and productivity in construction boils down to two key elements: thorough pre-construction planning and diligent monitoring during the project.
The former ensures that resources are optimized, schedules are spot-on, and goals are clearly defined and communicated, minimizing potential hiccups down the road.
Meanwhile, the latter keeps everything on track, allowing you to spot and tackle risks before they snowball into bigger issues.
Now, this might sound like a lot to handle, but remember—it’s a team effort.
Everyone has a part to play in keeping things running smoothly.
They just need to be provided with the right tools, knowledge, and training to contribute effectively.
And that is where you come in.