Asset monitoring has made significant strides in recent decades, to the point that construction companies that embrace new technologies have a significant competitive edge.
However, the task of selecting the ideal asset monitoring solution is not a straightforward one.
Before making your decision, it’s essential to closely examine the available options and assess how they meet your needs.
In this article, we will delve into how asset tracking software solutions are revolutionizing asset management practices, providing real-time insights, and assisting businesses in cost reduction.
We will also provide a comprehensive overview of commonly used asset monitoring technologies, explaining their functionality, primary benefits, and potential limitations.
Our aim is to equip you with the knowledge and insights needed to make an informed decision when selecting the perfect asset monitoring system tailored to your specific needs.
In this article...
What Is an Asset Monitoring Solution
Asset monitoring solutions are systems specifically designed to monitor and track the movements of assets, offering a wide range of benefits to organizations across various industries.
In the construction business, this technology enables executives to have a comprehensive view of the movement of their assets—such as tools, equipment, and vehicles—creating a quantitative record that includes real-time location data.
This feature alone offers tremendous advantages.
With a quick glance at their dashboard, managers can easily monitor the status and location of their assets, including the asset’s name, location, and current status.
This real-time information empowers organizations to run their operations smoothly and efficiently.
Reducing overall maintenance costs is another significant advantage of implementing asset monitoring solutions.
By continuously monitoring asset conditions and usage, managers can identify maintenance needs in advance, preventing costly breakdowns and downtime.
Moreover, the system notifies managers about asset malfunctions or failures, allowing them to make timely maintenance decisions and take preventive measures when necessary.
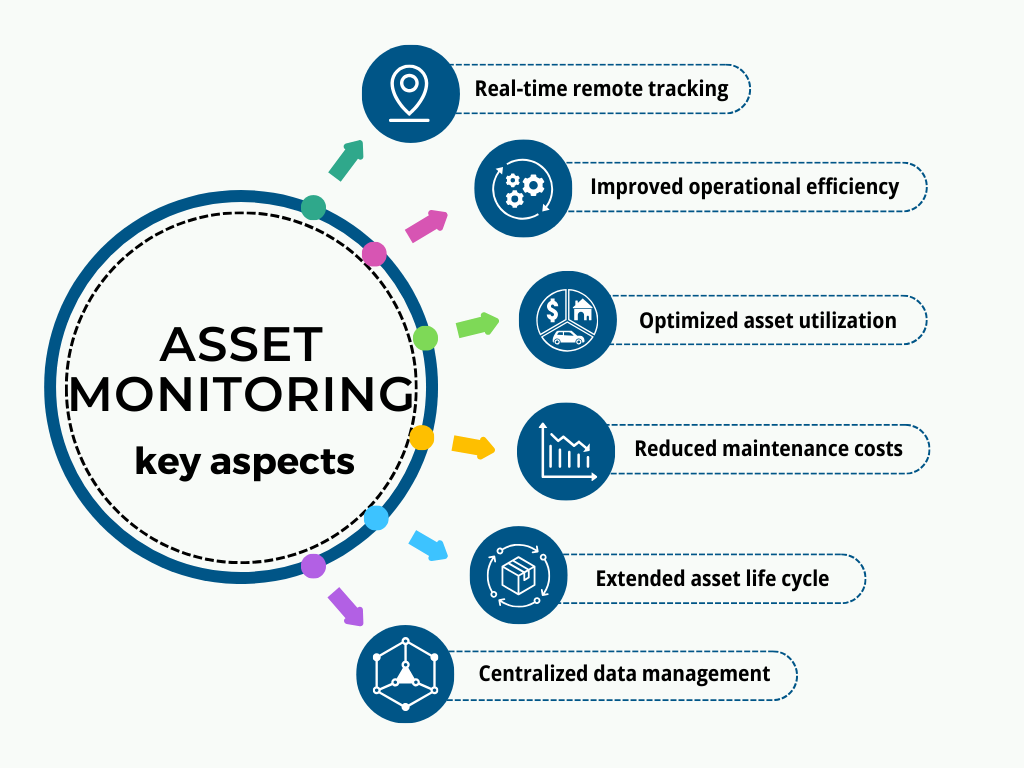
An additional benefit of this software solution is its ability to provide detailed information on an asset’s entire lifecycle, from procurement to disposal, including maintenance records and work orders.
These dynamic systems capture every relevant detail, enabling businesses to analyze data specific to each asset, allowing for more informed decision-making in asset management.
This level of detail can make a significant difference in optimizing asset utilization and reducing unnecessary costs.
This proactive approach not only saves money but also helps extend the lifespan of assets.
Remote access and centralized data management are also integral features of asset monitoring solutions.
This means managers can access critical asset information from anywhere at any time, making it easier to manage their assets effectively.
Centralized data storage ensures that all relevant data is stored securely and is easily accessible to authorized personnel.
Managing fleet vehicles, equipment, and heavy machinery is a daily construction management and operations task.
By identifying and implementing the appropriate asset monitoring solution, construction companies can make a significant step towards asset optimization, saving on costs, and enhancing productivity.
But how exactly does this solution work in practice?
Let’s explore further.
What Technologies Are Used for Monitoring Assets
Construction sites are usually busy places involving lots of tools and equipment, including large vehicles.
If a construction company works on several jobs at the same time, as is often the case, these assets are deployed on different projects.
The value of construction equipment makes it particularly attractive to criminals.
Theft in the construction sector has become a significant concern, causing the industry billions of dollars in annual losses in the United States alone.
Shockingly, approximately 85% of construction businesses have been a victim of some form of loss or theft.
This adds additional weight to the need to implement an asset monitoring solution that will help you track and protect your assets.
However, deciding which asset monitoring technology will best fit your business needs can pose a considerable challenge.
It’s essential to consider several critical factors that can guide you in making a well-informed choice.
These factors encompass your present needs, the quantity and worth of your assets, the simplicity of installation and usability, as well as the expenses associated with procurement and maintenance.
Let’s begin with QR codes.
Quick-Response Codes
QR codes are becoming increasingly popular in the construction industry due to their ability to simplify the process of tracking construction materials, tools, equipment, and inventory.
These square-shaped black-and-white digital marks—that can store data of up to 4,000 characters—allow fast access to information without any special scanning equipment.
All you need is your smartphone.
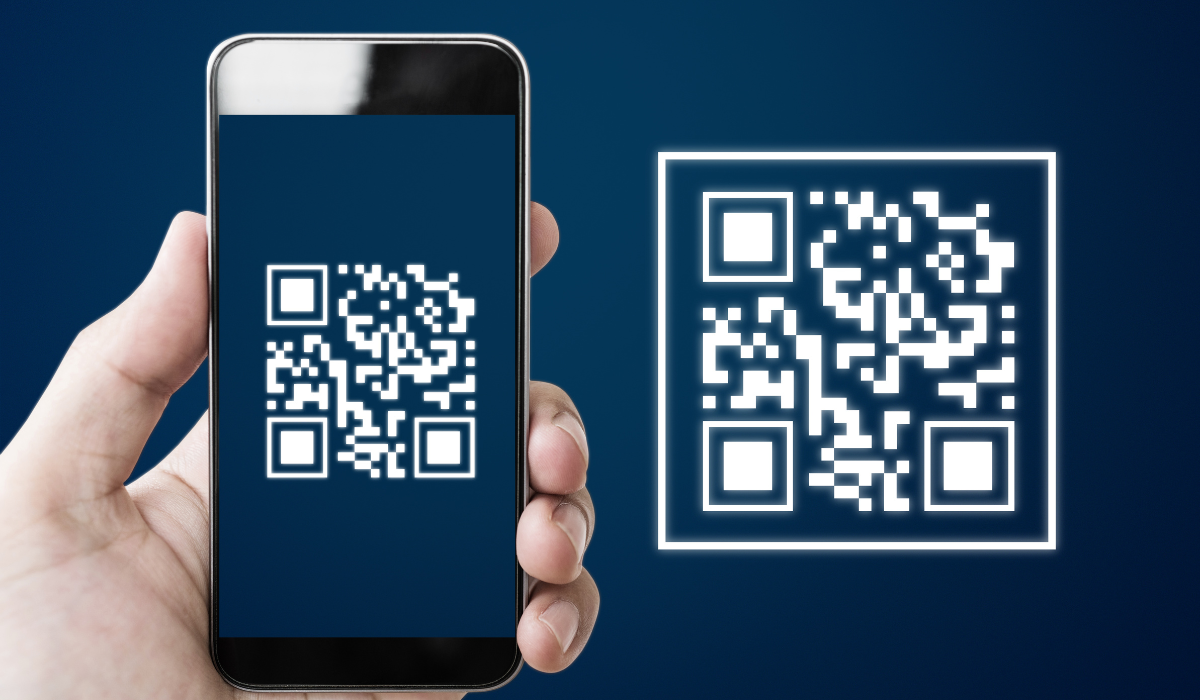
QR code labels and tags are easily applied to any piece of machinery or tool, allowing workers to scan them and retrieve information such as asset location, availability, manufacturer data, and maintenance history.
The GoCodes Asset Tracking software that supports them enables workers to quickly check the assets in and out whenever they have to use them and view and update asset information as needed.
When equipment is checked out by scanning the QR code, it creates a record showing the name of the employee who has taken a piece of equipment, along with the date and time. It also specifies the expected return date.
This process enables construction companies to track the location of their assets, significantly minimizing the chances of items being lost or misplaced.
By using only their smartphones and the GoCodes Asset Tracking app, workers and managers can effortlessly perform various tasks like scheduling maintenance, assigning work orders, or conducting audits.
These changes are instantly synced with a cloud database, accessible from any device, facilitating seamless information sharing among relevant team members.
In reality, construction companies can only rely on tags able to withstand harsh conditions and remain legible.
That’s why GoCodes Asset Tracking provides sturdy QR code tags that are water-resistant and attached with an extra-strong adhesive to ensure they stay secure.
In essence, QR codes offer an affordable and user-friendly solution for tracking construction tools and equipment, significantly decreasing the number of lost or stolen items.
However, they are less effective in tracking large movable machinery or vehicle fleets since they require manual scanning.
In addition, QR code technology can pinpoint the asset’s last known location but doesn’t allow for real-time tracking. Their shortcomings, though, don’t undermine their vast application and effectiveness when it comes to protecting your assets.
Global Positioning System
GPS is a system utilized to determine the precise location of an object anywhere on the globe, and it’s ideal for outdoor tracking of movable assets.
This technology—familiar from our car navigation systems—has emerged as a critical tool for monitoring and overseeing costly construction equipment, including heavy trucks, mobile cranes, service vehicles, generators, and compressors.
If you have ever wondered how GPS works, here’s the breakdown.
The three main components of a GPS system are satellites (the space segment), ground station (the control segment), and GPS tracker/receiver (the user segment).
The receiver, which can be a mobile phone, car navigation system, or a GPS tracker integrated into a vehicle, verifies the precise location by utilizing signals from a minimum of three satellites.
The ground stations use radar technology to confirm the location provided by the satellites.
This method is referred to as trilateration.
The location information is transmitted through a cell network to the software and regularly refreshed so that users can keep track of it in real time.
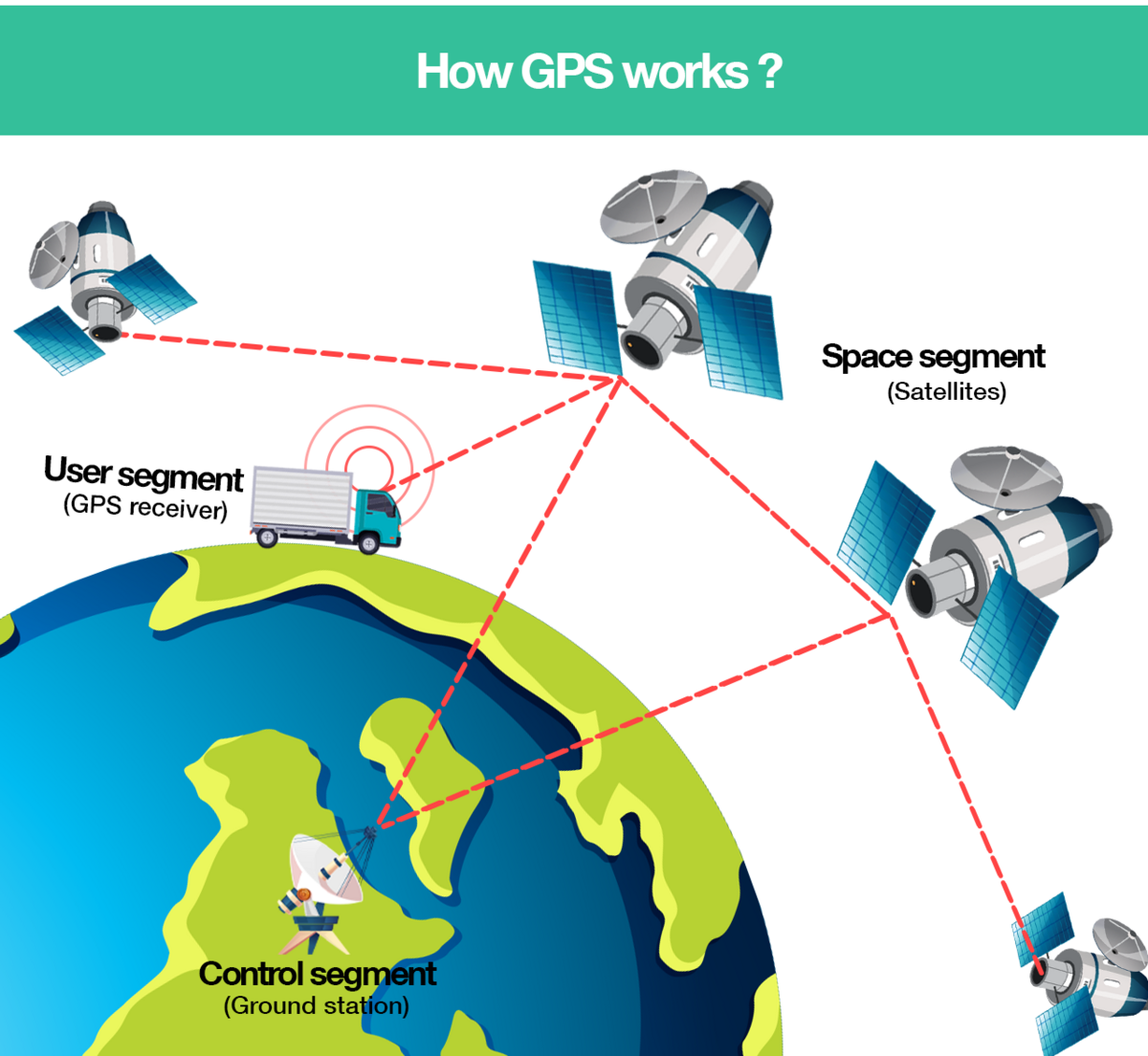
One of the standout features of a GPS tracking system is its ability to communicate over long distances.
This means it can offer accurate real-time location information, enabling sophisticated monitoring of valuable construction assets.
But there’s more to it—it also lets you keep an eye on other important vehicle-related data like the routes taken, speed, fuel usage, detours, and transport duration.
GPS technology is particularly beneficial for monitoring and tracking heavy vehicles, equipment, and machinery.
This is mainly because these trackers can draw power straight from the vehicle’s main battery, making them a reliable and convenient solution.
Conversely, since GPS trackers are rather large, they are unfitting for tracking smaller items, like hammers, cutters or hand drills.
Nevertheless, GPS has its limitations as well, and the main one is that it can be affected by various physical obstructions.
Factors such as tall buildings, mountainous terrain, atmospheric conditions, indoor or underground usage, and radio interference can weaken the GPS signal, potentially diminishing its accuracy.
Bluetooth Low Energy
BLE is a type of Bluetooth technology used to transmit short-range radio signals to mobile phone devices that can identify their presence and establish their proximity.
It has a lower data capacity than the classic Bluetooth, but operates with minimal power consumption from the device in which it is integrated. This translates into longer battery life.
BLE has found great application in many industries, including in tracking construction equipment through small portable devices called Bluetooth beacons.
In fact, the Bluetooth Low Energy Market is estimated to surpass the $16.7 billion mark by 2026.
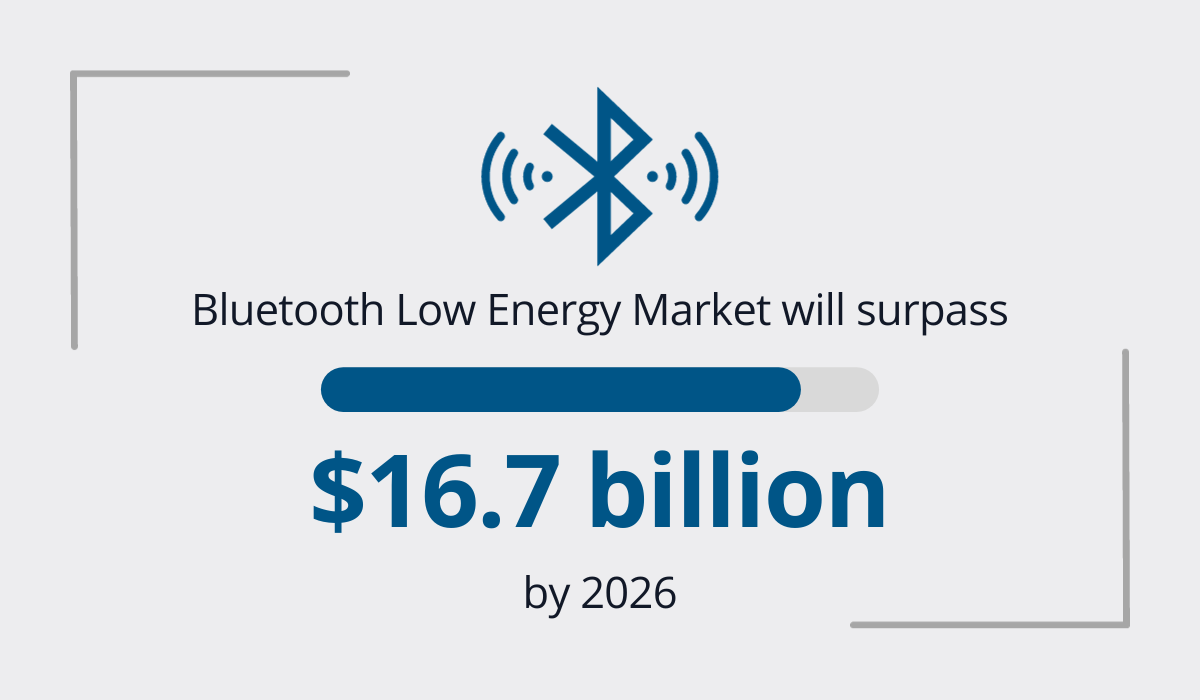
Furthermore, Bluetooth beacons are compact in size, which makes them simple to affix to assets without causing damage or disruption.
Another advantage is that they don’t require extra hardware for reading.
Any device equipped with BLE capabilities, like smartphones and laptops, can pick up their signals.
This ability allows BLE beacons to support location-based asset tracking on-site, even when those assets are hidden from sight, thus helping companies maintain an accurate inventory.
An additional benefit is that BLE beacons exhibit durability, allowing them to be transferred between different pieces of equipment or construction sites, essentially enabling companies to use them for extended periods.
However, they also come with a couple of shortfalls.
Namely, their short signal range of 100-300 feet makes them unfitting for tracking movable assets, like truck fleets or construction machinery.
Furthermore, when a beacon is obstructed by metal, water, or the human body, its signal will become lost unless it is situated at an elevated location.
Nonetheless, Bluetooth beacons bring numerous benefits to construction companies.
Managing inventory, optimizing workflows, preventing theft, and ensuring construction site security are only some of them.
Radio-Frequency Identification
RFID is a wireless technology used for real-time asset tracking based on radio waves. It’s used to locate and identify objects through asset tagging.
Every RFID tag consists of an antenna for transmitting the radio signal and a rewritable chip for storing data.
The best part is that all the information it stores can be read by a handheld device that doesn’t need a direct line of sight.
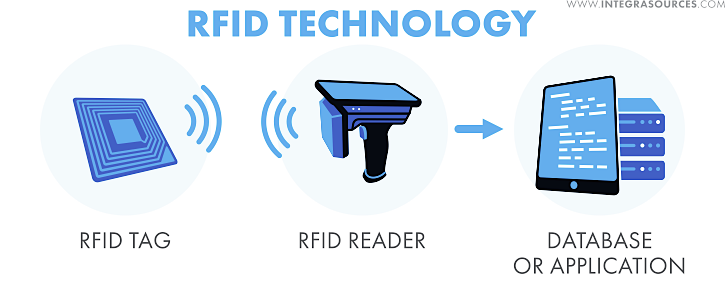
In the construction industry, RFID has become the go-to technology, and is primarily used for efficiently monitoring tools and equipment, as well as for inventory management.
Here’s how RFID is used in practice.
Imagine having a digital list of all your tools and where they’re kept, and this list is connected to special data-coded tags or labels attached to each tool.
Now, when someone needs to borrow a tool, they can easily scan its RFID tag.
This scan tells the database that the tool is currently in use at a specific construction site.
To make sure all the tools are present at the site, you can scan them all at once using a single scanner within a certain range. This quick scan confirms that everything is accounted for.
Once the tool is back in the warehouse, you just need to scan its tag once more, and the system will know it’s no longer in use.
It’s as simple as that.
One major benefit of RFID monitoring technology is its ability to verify the presence of tools on-site by reading hundreds of tags simultaneously within seconds.
Moreover, RFID tags offer the advantage of being reusable, and they have a greater data capacity compared to other types of tags or labels.
This includes the ability to store information such as manufacturer details, maintenance logs, inspection dates, location, and usage history.
A major setback worth mentioning is RFID’s price tag.
The fact that they require special infrastructure, such as RFID readers and antennas, can make their implementation costly.
How Does an Asset Monitoring Solution Work
Asset monitoring solution acts like a digital detective for your machinery and equipment’s lifecycle.
It gathers and organizes information about all your assets from the moment they enter the scene until they’re disposed of.
As your asset goes through its journey, the software keeps tabs on its location, who’s currently using it, and how much time it spends working versus resting.
Plus, it’s got a knack for generating reports automatically, giving management the inside scoop on each asset with all the numbers and analysis they need.
However, in the asset monitoring arena, there’s no one-size-fits-all solution.
Companies can opt for a single technology or blend multiple ones for a customized approach.
For instance, GPS transmitters are far from necessary for every tool in the warehouse, just as a QR code alone won’t suffice for tracking hefty assets like trucks and machinery.
Nevertheless, modern asset monitoring systems leverage the strengths of these technologies to simplify the process, enhancing efficiency and cost-effectiveness.
Regardless of whether they employ labels, tags, or specialized scanning devices, they all relay data to a cloud-based monitoring solution.
Ultimately, the goal is to maintain one central unified system, ensuring your company’s assets receive timely maintenance or replacement.
How to Choose an Asset Monitoring Solution
When venturing into the realm of asset monitoring systems, your first step should be a thorough self-assessment of your needs and priorities.
Begin by taking stock of the number and diversity of assets in your care. This insight will help you determine your ideal approach.
For example, if you manage a fleet of outdoor equipment or construction vehicles, GPS-based systems can provide an excellent visual representation of their locations.
However, when precision is paramount, especially indoors, Bluetooth beacons reign supreme with their greater accuracy.
Furthermore, consider your company’s size.
Asset monitoring solutions run the gamut from straightforward tools designed for small businesses to intricate enterprise-level systems.
Most importantly, factor in the limitations of various technologies.
Bluetooth beacons excel in challenging environments like wet or metal-rich settings, where RFID tags might falter.
Lastly, simplicity and ease of implementation are paramount.
Solutions like GoCodes Asset Tracking’ asset monitoring system offer a hassle-free experience.
There’s no need to invest in handheld scanners, install on-premises software, or rely on external sources for labels and tags.
It’s a streamlined solution that puts simplicity at the forefront.
Conclusion
In summary, asset-tracking software solutions have become indispensable tools for modern businesses.
They empower companies to optimize asset efficiency, minimize the risk of lost or underutilized assets, and reduce overall maintenance costs.
By providing real-time data and a holistic view of an asset’s life cycle, these solutions enable businesses to make smarter, data-driven decisions.
In an increasingly competitive business environment, the ability to efficiently manage and utilize assets can make all the difference in achieving success.
Lastly, keep in mind that implementing an effective asset monitoring solution can reduce losses by 90% or more.
After all, it’s worth giving it a try.