Have you ever faced critical delays on an important project simply because a crucial tool broke down when you needed it the most?
Tracking down the broken part, followed by the agonizing wait for its replacement from a limited pool of suppliers, can lead to major setbacks, increased labor demands, and unexpected expenses.
You’re probably familiar with the saying, “Prevention is better than cure,” and this principle also holds for your equipment.
What if there was a way to proactively avoid these issues and keep your machinery in top-notch condition?
We are talking about equipment maintenance software—the ultimate solution for such setbacks.
In this comprehensive guide, we will explore equipment maintenance software’s purpose, intended users, and some compelling reasons why you should adopt it.
Additionally, we will uncover the key features that make this software an indispensable asset for your business.
First and foremost, let’s explain what equipment maintenance software is.
In this article...
What Is Equipment Maintenance Software
In the past, retrieving old equipment records and manuals for inspections was a tedious task.
Moreover, manual scheduling of maintenance and inspections demanded significant time and effort from your team members.
But this has changed entirely with equipment maintenance software.
This robust technological solution can schedule, track, and optimize maintenance tasks, making sure that your equipment remains in peak condition at all times and operates efficiently.

Since this software works on the principle of automation and centralization—that means all equipment data is in one place, in the cloud—you can keep track of maintenance tasks and schedule them seamlessly from one platform.
In addition to planning and tracking the maintenance of each tool, this software can:
- Keep a comprehensive record of all your assets, including equipment details, maintenance history, and warranty information.
- Track spare parts and inventory levels, receiving alerts for low stock.
- Store and organize equipment manuals, repair guides, and safety documents for easy access.
- Ensure regulatory compliance and safety standards by tracking maintenance activities and documentation.
- Utilize data analytics and machine learning to predict equipment failures and schedule maintenance proactively.
- Monitor maintenance expenses and analyze costs to optimize budget allocation.
In summary, equipment maintenance software is a game-changing tool that empowers organizations like yours to take control of managing your tool maintenance.
This leads to increased team productivity, reduced costs, extended equipment lifespan, and a safer environment for your employees.
Why Use Equipment Maintenance Software
Equipment is the lifeblood of your business, and safeguarding its well-being is paramount for your organization’s smooth operations and profitability.
Designed precisely for this purpose, equipment maintenance software takes care of your equipment’s health.
In the following sections, we will explain how it does this and how it can benefit your business further.
Centralizes All of Your Maintenance Data
As we mentioned a few moments ago, equipment maintenance software securely stores all your data on the cloud, making it accessible to authorized team members from wherever they are.
This centralized data management becomes invaluable for construction companies that work in more locations simultaneously, with a diverse array of tools and machinery on-site.
For instance, technical specifications, inspection forms, operation manuals, and warranty papers for each tool can be all at your fingertips within one centralized platform, eliminating the need for static and isolated spreadsheets.
This streamlined documentation saves you significant time, ensuring smoother project workflows and quicker access to critical information.

Furthermore, this digital record-keeping replaces the traditional pen-and-paper approach, making data retrieval and analysis much more efficient.
Not only does this enhance productivity, but it also saves your company a considerable amount of money that would otherwise be spent on physical documents.
Finally, having a centralized platform is essential for easy communication and collaboration within the system itself—it minimizes the need for back-and-forth emails or phone calls to track maintenance tasks.
The software’s real-time updates and notifications keep everyone informed, promoting efficient teamwork and timely responses, further enhancing construction site safety and efficiency.
Reduces Your Maintenance Costs
Efficiently cutting maintenance costs for your business is possible with close equipment monitoring and preventive maintenance, all made easy by equipment maintenance software.
The software’s automated scheduling ensures precise execution of maintenance tasks when needed, preventing unnecessary downtime and premature maintenance.
Additionally, regular inspections allow for early detection of potential issues, averting costly repairs.
Roberto Bogdanoff, director for customer solutions at Volvo Construction Equipment, emphasizes this by giving an example:
If you repair a pin and bushing when the wear starts, this repair may cost around $1,000 and take four hours for the repair. But if you don’t repair it on time and the bushing wears out completely, damaging the bore, then the repair cost would be around $5,000 and would take, in some cases, 16 hours. You do the math.
Notably, Caterpillar Inc., the world’s largest construction equipment manufacturer, also recognizes the impact of good maintenance practices on profitability.
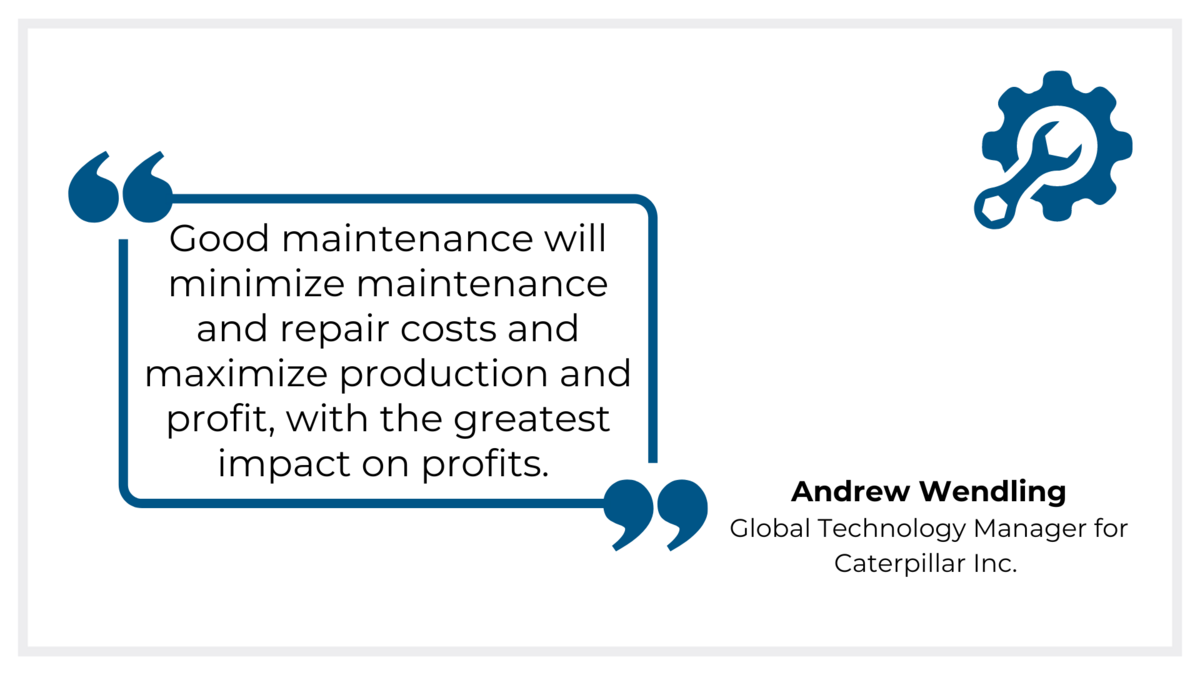
Their global technology manager, Andrew Wendling, highlights that proper maintenance helps control costs and service intervals, lengthens equipment life, reduces downtime, and adds resale value to tools.
In summary, using equipment maintenance software can lead to significant cost savings, increased operational efficiency, and improved profitability for your business.
All this is possible because of regular checks and preventive equipment maintenance.
Improves the Safety of Your Employees
Equipment maintenance software plays a pivotal role in enhancing the safety of your employees by promoting proactive maintenance practices.
With this software in place, you can schedule regular equipment checks and timely repairs and not only save money, as mentioned before, but also ensure that critical safety components are always in top-notch condition.
For instance, on construction sites, you can easily schedule routine inspections for heavy machinery like cranes and excavators and monitor crucial safety features, such as brakes and safety guards.
Moreover, if any issues arise, you can communicate these faults through a centralized portal so that everyone is aware of the problem and refrains from using the affected tool.
This automation reduces the risk of accidents, safeguarding the well-being of workers.
The Occupational Safety and Health Administration (OSHA) highlights the importance of this safety-focused approach, as inadequate machine guarding and unsafe machinery are among the top ten most frequent safety violations on construction sites that lead to non-fatal and fatal workplace injuries.
In a nutshell, using this software mitigates safety risks and fosters a secure working environment for employees.
Who Uses Equipment Maintenance Software
Equipment maintenance software is widely used in various industries that heavily rely on using equipment and tools.
These include construction, energy, oil and gas industries, and agriculture.
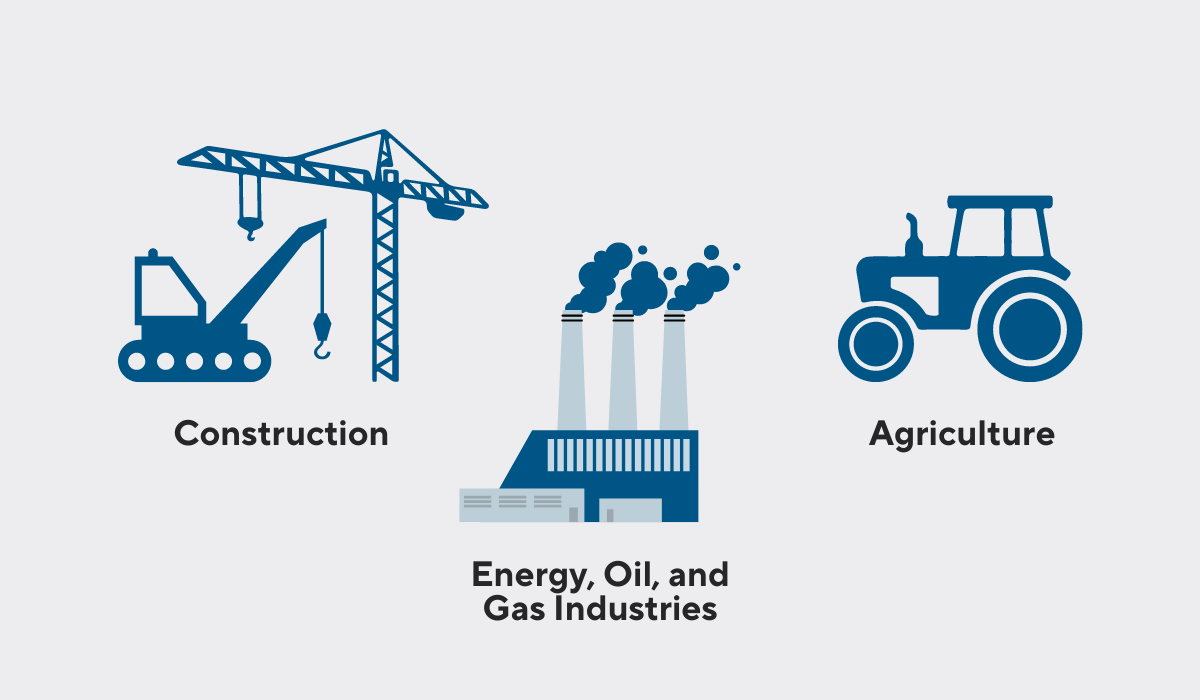
Let’s take a closer look at each of these fields.
Construction
Construction companies operate a wide range of heavy machinery and equipment critical to their projects.
With equipment maintenance software, they can efficiently schedule maintenance tasks, track equipment health, and ensure that all machinery works properly.
This proactive approach helps prevent unexpected breakdowns on construction sites, reducing equipment downtime and ensuring a safe work environment.
Energy, Oil, and Gas Industries
The energy, oil, and gas sectors involve complex and specialized equipment for drilling, refining, and power generation.
With equipment maintenance software, companies can closely monitor the performance of critical equipment, conduct routine inspections, and address maintenance needs promptly.
All this is crucial to ensuring the safety and reliability of operations in these hazardous and high-stakes industries.
Agriculture
Farms and agricultural businesses rely on machinery such as tractors, harvesters, and irrigation systems to optimize agricultural processes.
Equipment maintenance software allows farmers to keep their machinery in optimal condition, reducing downtime during critical farming seasons and maximizing productivity.
These are just a few examples of industries that benefit from using equipment maintenance software.
However, the software can be utilized in other sectors, too. For example, transportation, logistics, healthcare, and education can benefit from equipment maintenance software.
In general, any industry that relies on equipment and machinery can use equipment maintenance software to enhance efficiency and ensure the longevity of its assets.
Key Features of Equipment Maintenance Software
Throughout our exploration of equipment maintenance software, we’ve covered its definition, the advantages of using it, and the industries it benefits.
Now, let’s focus on its key features that ensure effective tool maintenance.
The three crucial features every robust equipment maintenance software should have are:
- giving maintenance work orders
- scheduling maintenance tasks
- sending maintenance notifications
We will illustrate these features in the example of GoCodes Asset Tracking, our all-in-one asset-tracking solution that excels in equipment maintenance management.
Maintenance Work Orders
Assigning work orders is the crucial first step in equipment maintenance.
However, tracking multiple tasks and communicating instructions through emails or phone calls can be time-consuming and error-prone.
Thankfully, with equipment maintenance software like GoCodes Asset Tracking, this process becomes streamlined and efficient.
GoCodes Asset Tracking allows you to give work orders to your employees from a single platform in just a few clicks—no need to juggle between different tools or systems.
Once a task is assigned, the designated employee can easily view it in their “My Tasks” window. This ensures clear communication and eliminates the risk of tasks being overlooked.
To create a work order, start by finding the ID of the asset you wish to work with.
Access the asset’s information window and scroll down to the “Task” section. Click the “+Add” button to open a new task window.
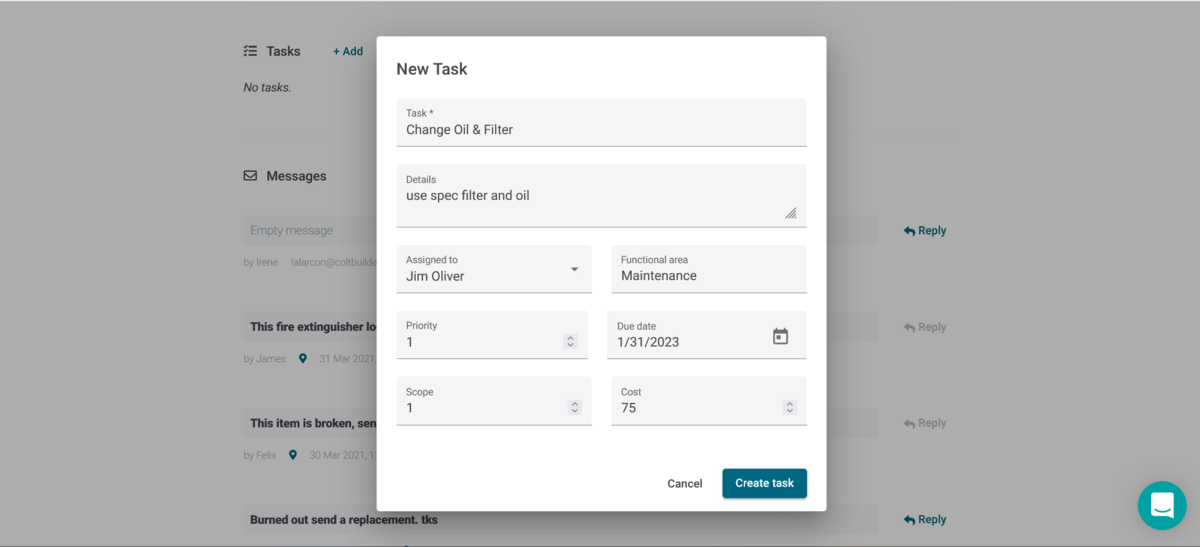
In the task window, fill out essential information such as the task name, details, due date, and the assigned person.
And remember—adding more context enhances task clarity and efficiency.
Once the task details are complete, click on “Create task,” and the work order is set.
The assigned employee will promptly see the task listed under their “My Tasks” section.
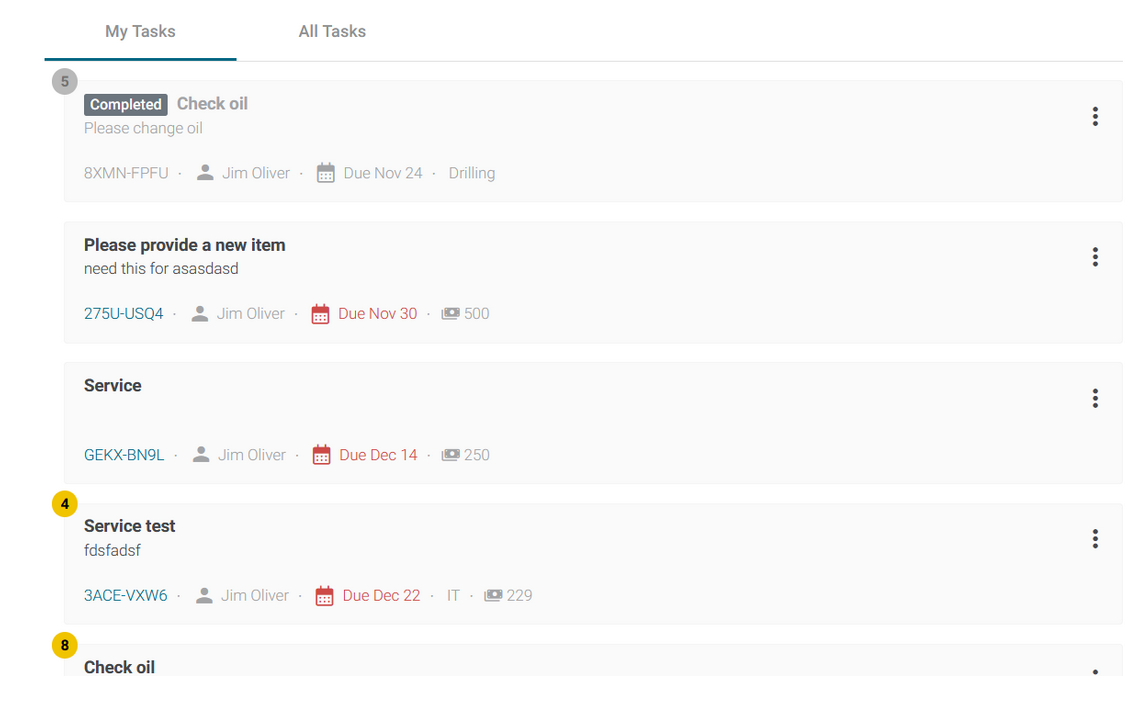
With everything consolidated in one place and easy task creation and assignment, equipment maintenance software simplifies giving work orders.
Its user-friendly interface ensures that everyone is well-informed and can promptly carry out their maintenance tasks.
Maintenance Scheduling
An essential aspect of equipment maintenance software is the ability to schedule maintenance tasks periodically, ensuring the proper functioning of your equipment.
As we’ve emphasized throughout this guide, proactive maintenance is crucial for optimal equipment performance.
With GoCodes Asset Tracking, scheduling maintenance tasks becomes a seamless and straightforward process.
Let’s see how you can easily schedule maintenance tasks in GoCodes Asset Tracking.
Start by locating the asset for which you want to schedule maintenance. Access the asset’s information and select the “Edit info” option.
In the “Edit info” section, locate the “Next service” field. Here, you can easily set the date for the next scheduled maintenance.
You can see the video with the instructions below:
And to stay on top of scheduled maintenance, you can turn on email notifications to remind you of maintenance and ensure you never miss a maintenance task.
In summary, GoCodes Asset Tracking’ equipment maintenance software streamlines the scheduling process, ensuring no equipment remains unmaintained or broken.
With easy-to-use features and reliable notifications, your tools will be in peak condition, minimizing downtime and maximizing productivity.
Maintenance Notifications
The last but not least crucial feature of equipment maintenance software is the ability to send service notifications.
Reliable software not only helps with work orders and maintenance scheduling but also serves as a reminder for upcoming maintenance tasks.
In GoCodes Asset Tracking, this feature can be enabled through the Customization settings.
Let’s see how.
To turn on maintenance notifications, navigate to the top right corner of the screen, where your name is displayed.
Click on the dropdown menu, and select “Customization,” as seen in the photo below.

Once in the Customization section, you will see five features on the right side of the screen.
Look for the “Scheduled Service Notifications” feature, which allows GoCodes Asset Tracking to send notification emails to Admin users when scheduled services are due, and enable it.

The software will send an email notification to the designated Admin user, providing timely reminders for planned maintenance services.
The screenshot below shows an example of such an email.

This handy feature ensures no scheduled maintenance tasks are missed, keeping your equipment in top-notch condition and preventing potential issues.
With all three crucial features, GoCodes Asset Tracking simplifies tracking and scheduling equipment maintenance, making it the perfect choice for organizations like yours.
Conclusion
In conclusion, equipment maintenance software is a game-changer that empowers businesses to prevent critical delays and unexpected breakdowns.
By proactively managing maintenance tasks, you can ensure your machinery operates efficiently, avoid costly setbacks and provide a safe environment for your employees.
Hopefully, these reasons and benefits we mentioned in this guide will encourage you to utilize this indispensable tool in your organization.