This article is designed for construction company owners and managers looking for best practices to maximize efficiency, minimize loss or theft, and gain better control over their inventory.
In the context of construction, the term “inventory” often encompasses both consumable materials (such as lumber, cement, and spare parts) and durable physical items (such as tools and equipment), commonly referred to as “construction assets.”
Simply put, to gain control over your company’s entire construction inventory and efficiently track and manage all these inventory items over time, you need to follow these best practices.
In this article...
Creating an Inventory Control Plan
Before deciding what software and tracking technology you’ll use for inventory control, you and your team should create a comprehensive inventory control plan.
That’s because technology, despite playing a crucial role in automating manual inventory processes, cannot compensate for poor inventory planning.
In essence, an inventory control plan will define the workflows, policies, and procedures necessary to ensure your company has the right materials, tools, equipment, and other supplies—when and where they’re needed.
That way, project delays and cost overruns will be minimized.
Naturally, all these guidelines will depend on numerous factors specific to your company or your construction projects, such as project size and complexity, types of materials and equipment used, and specific regulatory requirements (e.g., hazardous substances).
Another factor is the available storage space.
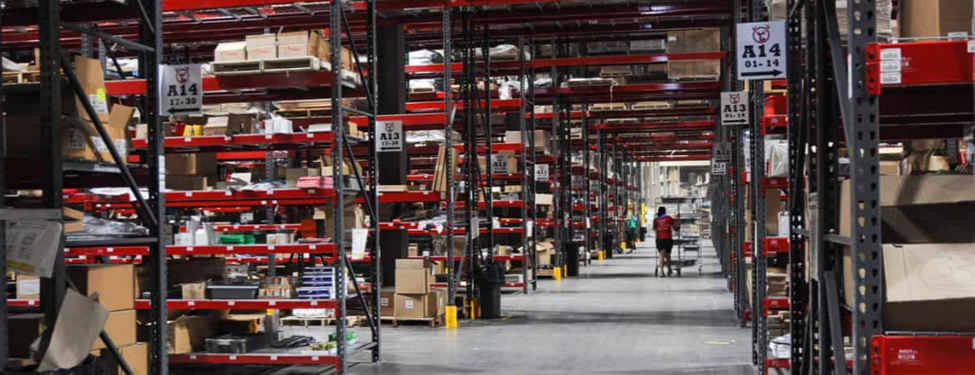
Aside from accounting for such factors, your plan should have clearly defined inventory goals and objectives, such as avoiding stockouts and overstocking, minimizing inventory loss and theft, and reducing inventory holding costs.
Additionally, it should outline specific strategies for managing different types of construction inventory items.
For example, durable items like tools and equipment should have set procedures for tracking their location and usage and defined regular maintenance and replacement cycles, including the frequency of performing routine inspections.
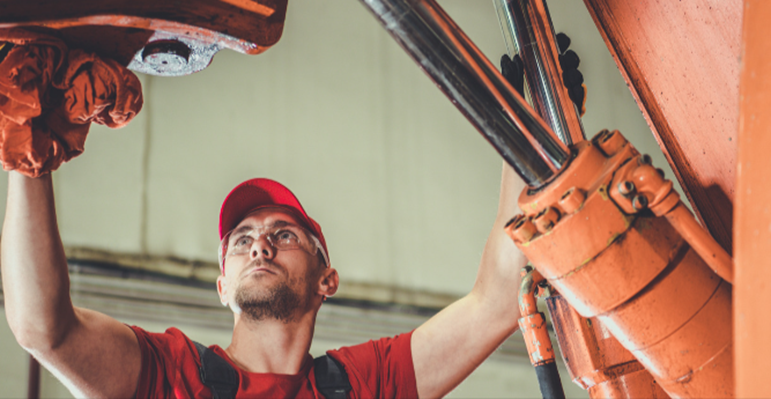
For consumable inventory, such as building materials and various supplies (like spare parts and accessories for construction equipment), the plan may define:
- procedures for tracking the usage, location, and quantity of inventory items
- reordering processes based on factors like specific project requirements, safety stock levels, historical data, demand planning, etc.
- guidelines for implementing proper storage and organization methods to prevent damage, loss, or expiration of perishable items
By developing a comprehensive inventory control plan tailored to your company’s needs, you can proactively manage all inventory types, minimize costs, and improve operational efficiency.
This will serve as a roadmap for future decision-making, guiding the selection of suitable software and tracking technology that aligns with the company’s specific inventory control objectives and requirements.
Tagging and Tracking Your Inventory
Accurate records and efficient inventory control are best achieved by tagging your inventory using barcode labels (or their more advanced cousins, QR code labels).
The main reason for barcoding inventory—as opposed to other inventory tracking methods—is the utmost simplicity and unparalleled affordability that the combination of barcodes, software, and scanners can provide.
Inventory items are tagged with barcode or QR code labels, so they can be scanned and thus tracked from the moment they arrive at the company’s warehouse until they’re consumed (e.g., lumber), used (e.g., spare parts), or replaced due to wear-and-tear (e.g., drill).
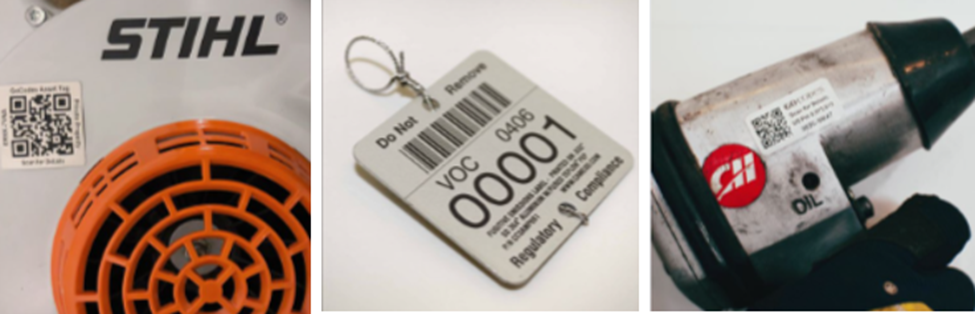
Considering all the different inventory types and items a construction company typically needs to track, using barcodes for inventory control is the most widely applied tracking method due to its ease of implementation and cost-effectiveness.
Put simply, barcode/QR code labels are inexpensive to print (or order customized labels made from durable material for specific purposes), easy to apply, and fast to scan.
For instance, when a shipment of lumber arrives, the warehouse staff can tag each bundle/pallet of lumber with barcode tags that their inventory control system (covered later) generated, and they themselves printed out.
This enables managers and workers to track the location, movement, and usage of that lumber from that moment on simply by scanning the barcode (using special barcode readers or, in the case of QR codes, in-app scanners on their smartphone or tablet).
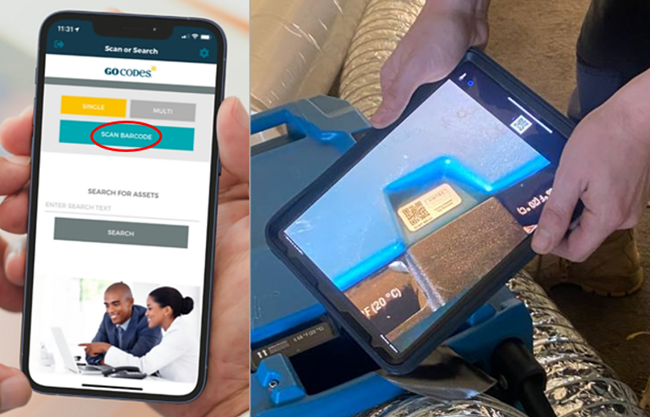
Once tagged, lumber bundles and pallets are stored in the warehouse, and their location is recorded in the inventory control system.
When a specific quantity of lumber is needed on-site, the warehouse staff will scan “out” this quantity, i.e., indicate that it has been taken, by whom, and to what location.
Naturally, the system will deduct the quantity from the warehouse stock, allowing for timely restocking when inventory levels are low.
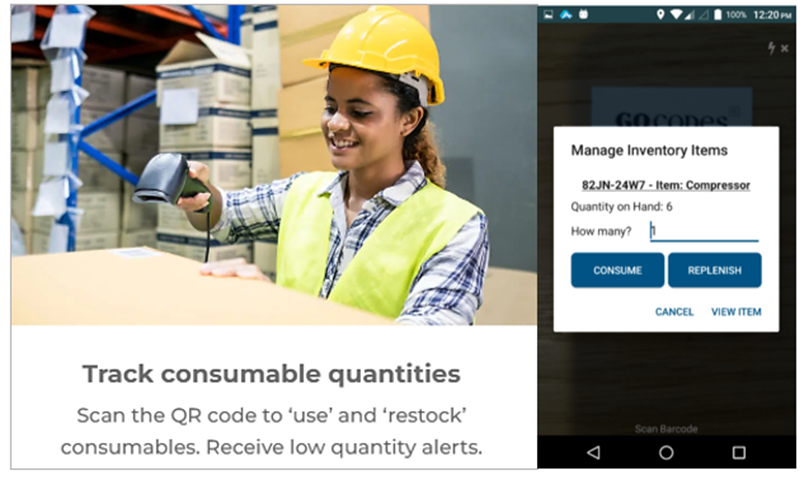
When lumber is delivered to the jobsite, workers can scan tags to confirm they received the material, use the system to record its on-site location, and can also scan the tag one last time to indicate the material has been used.
Again, the biggest advantage of tagging and tracking your inventory using barcodes/QR codes is that they can be used on any inventory items you want, from containers with spare parts to individual hand and power tools and even heavy equipment and construction vehicles.
At the same time, tags are inexpensive (to order or print) and can be easily applied and scanned, making barcoding the most efficient and affordable best practice for inventory control.
Performing Regular Inventory Audits
By performing regular inventory audits, your construction company can maintain control over its inventory, making sure that inventory records are accurate and match the inventory you actually have on hand.
Of course, to establish an efficient inventory control system, the initial inventory audit should be performed. Inventory items should be counted, categorized, and tagged, and the system’s database populated.
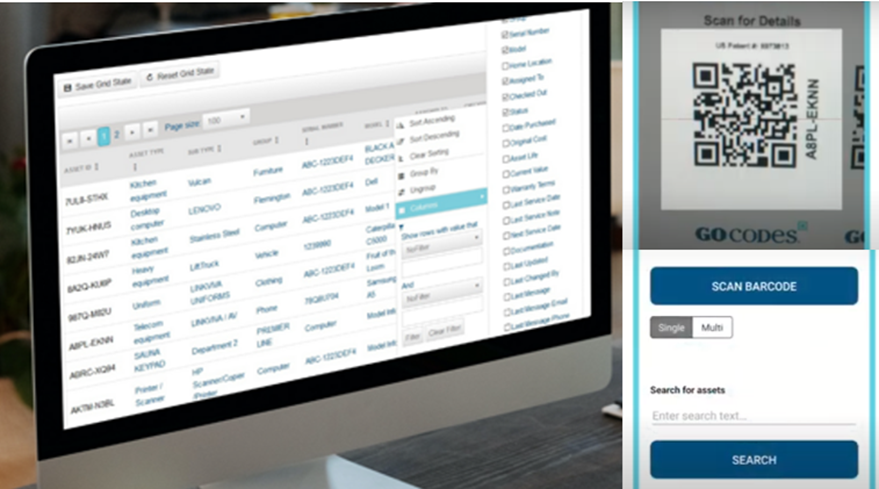
Depending on the number of inventory items you want tracked, this initial step can be time-consuming, but the rewards of doing the first audit before digitizing and automating inventory control in an accurate and organized manner will be far-reaching.
One of the advantages is that once the initial inventory audit is done, your company will be able to eliminate ghost assets (or inventory).
As their name suggests, these inventory items might be in your company’s records (typically in spreadsheets or paper-based), but upon inspection during the first audit, it’s established they’re missing or no longer usable (e.g., expired varnish or paint).
This enables you to remove such items from your records and get an accurate count and condition of all materials, supplies, tools, and equipment your company has.
Naturally, this also allows you to automate and thus make future regular inventory audits much easier, as shown in this short video.
However, the audit mode and multiple item scanning can only be used once the inventory control system is up and running.
The system needs to be populated with relevant data about your inventory, such as:
- item name, description, and unique identification number
- purchase price and date, supplier information
- current location, quantity on hand, and the minimum quantity when an item should be reordered to avoid stockouts (reorder point)
- expiration date, if applicable
Therefore, to establish an efficient inventory control system, you first need to know exactly what inventory your company has, namely the quantity and the condition of specific items and their current location.
From there, you’ll be able to utilize the system and enable your staff to quickly and easily perform regular inventory audits.
Using an Inventory Control System
It’s already clear from previous sections that the ultimate best practice is finding, establishing, and using a digital, largely automated, cloud-based inventory control system.
In other words, establishing and maintaining a spreadsheet or paper-based inventory control would be an overly time-consuming, error-prone, and resource-intensive process.
Instead, construction companies should opt for inventory control software coupled with barcodes/QR codes and in-app barcode scanners that turn workers’ smartphones and tablets into scanning devices.
Such software solutions will not only eliminate human error during data entry but also track inventory quantities in real time, indicate when it’s time to reorder and make inventory audits much simpler.
This brings us to what features you should look for to pick the right inventory control system.
Here are seven of them.
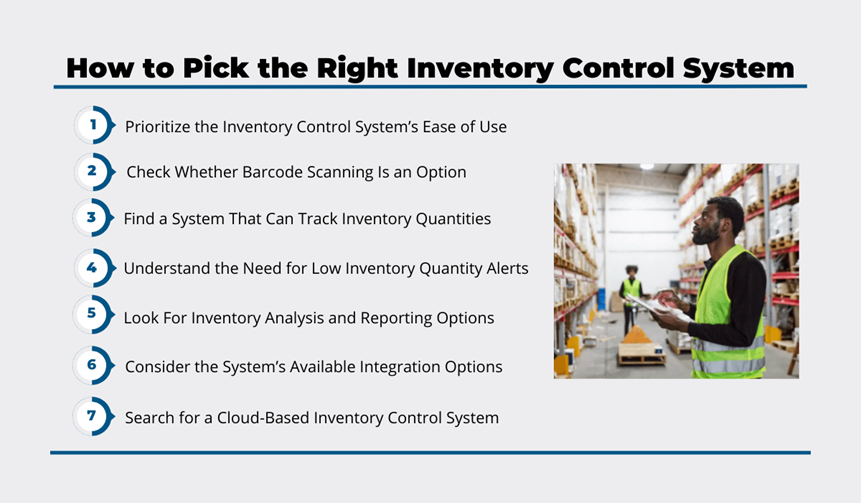
As you can see, ease of deployment and use of the system—along with minimum training requirements—should be your top priorities.
Similarly, the affordability criterion dictates that barcode scanning should be the main, if not only, inventory tracking method.
Naturally, you need a system that can track inventory quantities and send automated low inventory quantity alerts to avoid stockouts and overstocking.
Finally, your inventory control system should provide inventory analysis and reporting options, integration with other systems (e.g., accounting software), and be cloud-based, and therefore accessible from any internet-connected device at any time.
For instance, one solution incorporating all these features is our inventory/asset tracking and management solution, GoCodes.
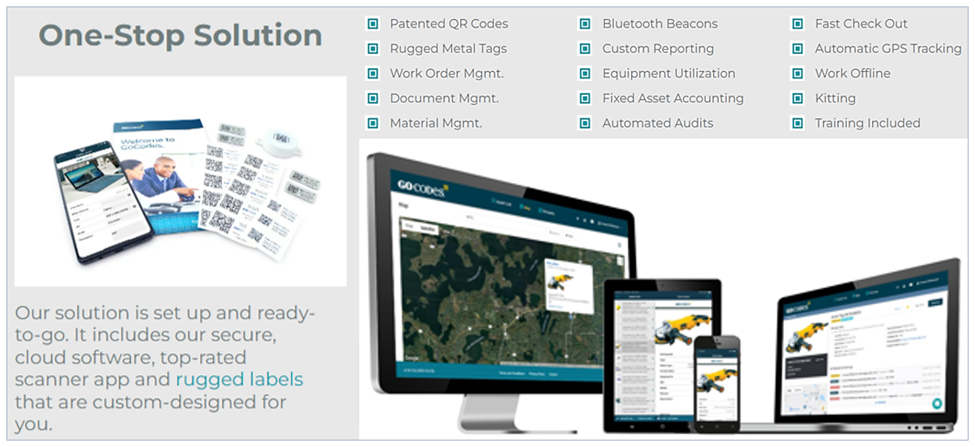
In addition to its ease of use and affordability, supported by a range of valuable features, maybe the best thing about the GoCodes tracking system is its versatility.
Simply put, it can be used to track and manage consumable construction inventory, more durable construction assets like tools and equipment, and everything that falls in between, such as different equipment accessories or personal protective equipment (PPE).
For example, you can track how many materials, spare parts, and other supplies you have in storage and when they should be replenished, or you can track the usage, location, and status of your equipment and schedule their maintenance using the same system.
Long story short, anything that can be tagged (e.g., QR codes of any size can be scanned even when damaged) can be tracked and managed with the help of GoCodes.
And that’s why the ultimate best practice is to select, deploy, and utilize an affordable, user-friendly, and easy-to-setup inventory control system with all the critical features for efficient inventory control.
Conclusion
If we were to roll all these best inventory control practices into one, your path to maximizing operational efficiency, minimizing inventory or asset loss and theft, and gaining better control over your company’s inventory would look something like this.
You and your team would identify, categorize, and prioritize different types of inventory, establish workflows and procedures, and develop an inventory control plan (which should be subject to regular reviews and updates).
Next, you would select the right inventory control software solution for your company’s needs, perform the initial inventory audit, tag your inventory, and set up the system.
Naturally, an inventory control system would provide real-time inventory tracking (plus benefits) and allow you to easily perform regular inventory audits from that moment forward.
All in all, you’ll have an effective, easy-to-use, and affordable system, which can then be used to make inventory management improvements and savings across your construction company.