Key Takeaways:
- Contractors lose up to 90 hours per month tracking tools.
- 31% of construction projects face delays due to theft.
- 60% of employees struggle with new software due to poor training.
- Web-based asset management software cuts search times and improves productivity.
Keeping track of tools, equipment, and materials in construction isn’t easy—especially if you’re still relying on spreadsheets or outdated systems.
Mistakes pile up, delays happen, and costs spiral out of control.
That’s where web-based asset management software comes in.
It gives you real-time visibility over your assets from any device, helping you reduce downtime, prevent losses, and streamline operations.
If missing equipment and outdated records are slowing you down, this could be the solution your business needs.
In this article...
Why Choose Web-Based Over Traditional Asset Management?
If your team is constantly searching for missing equipment, struggling with outdated records, or dealing with unexpected downtime, your asset management system isn’t working.
Spreadsheets and manual logs may seem simple at first, but they quickly lead to confusion.
One misentry, and suddenly a machine is marked as lost—when it’s actually sitting on another job site.
And even traditional on-premise software has its limitations.
While it eliminates paperwork, it often requires users to be in a specific office or location to access data.
In a fast-moving construction environment, that lack of flexibility can cause major delays.
Web-based asset management software solves these issues.

Source: GoCodes Asset Tracking
Since it runs through a web browser, there’s no need to install software on individual devices, and your team can access asset data from anywhere with an internet connection.
Many web-based systems are also cloud-based, so all data is stored on secure remote servers rather than local computers.
This eliminates the need for costly IT infrastructure and ensures automatic updates, backups, and seamless access across multiple locations.
Instead of wasting time chasing down equipment, web-based asset management lets you see exactly what’s available, where it’s located, and who’s using it—all in real time.
Given all this, it is not surprising that the digital asset management market is expected to double in size by 2029.
How Does Web-Based Asset Management Software Work?
At its core, web-based asset management software connects physical assets to a digital system.
Instead of relying on handwritten logs, every tool and piece of equipment is registered with detailed information on its location, condition, and usage history.
It also includes warranty information, purchase dates, and more.
In many cases, assets are labeled with QR codes, RFID tags, or GPS trackers.
This means that, when a worker needs a specific tool or machine, they can simply scan the code with a mobile device to pull up all relevant details instantly, as well as check the asset out.
At the same time, the system automatically records who used it, when, and at which location, thus eliminating guesswork and improving accountability.
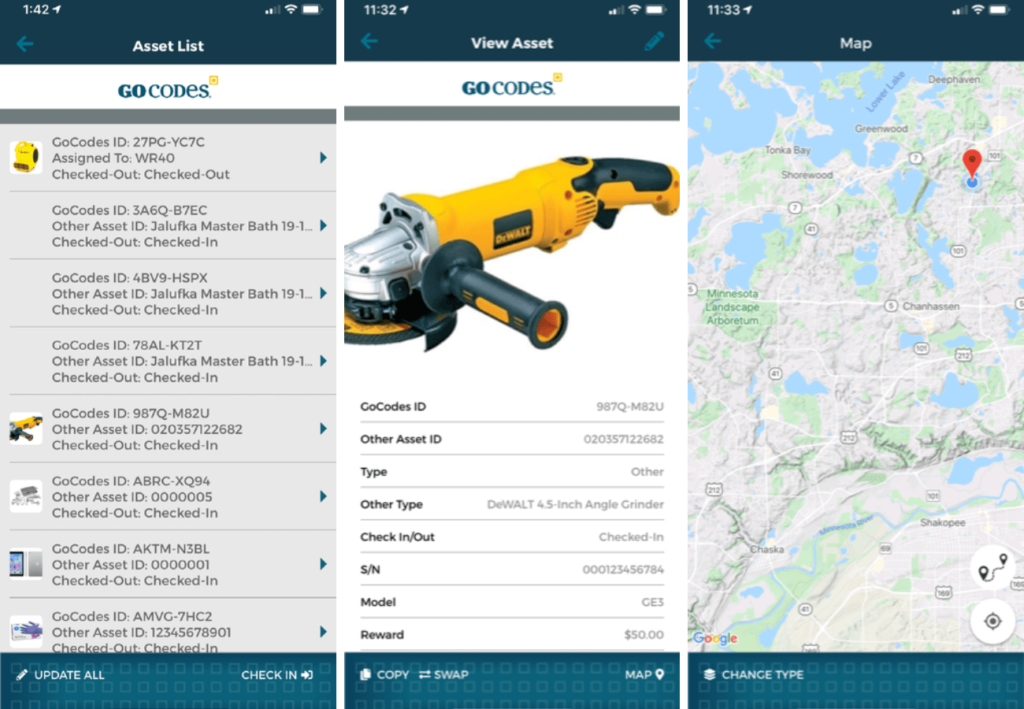
Source: GoCodes Asset Tracking
This is exactly what GoCodes Asset Tracking offers.
Our solution allows managers to store detailed information about each asset—such as names, descriptions, warranties, manuals, and maintenance schedules—all in one, web-accessible platform.
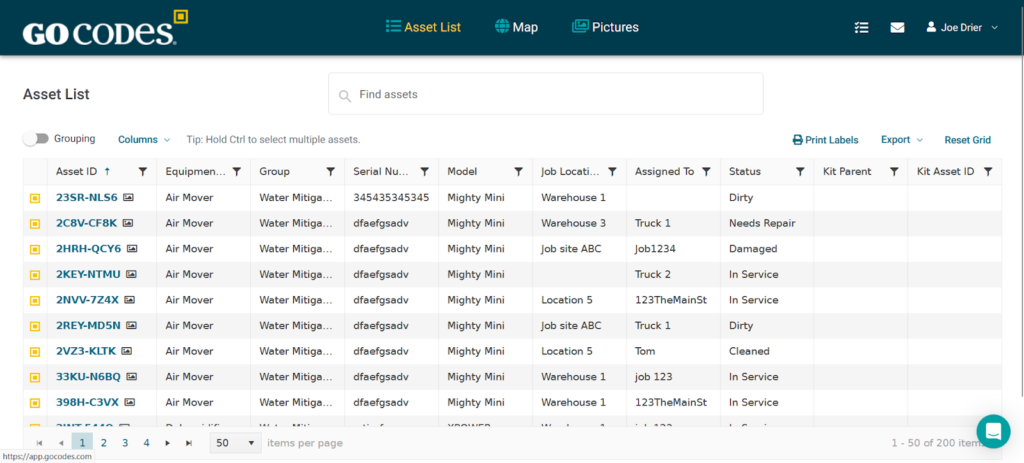
Source: GoCodes Asset Tracking
Moreover, each asset receives a durable QR-coded label.
When workers scan these labels using smartphones or scanners, they can instantly access important details like manuals or usage instructions, while managers receive real-time notifications about the asset’s location.
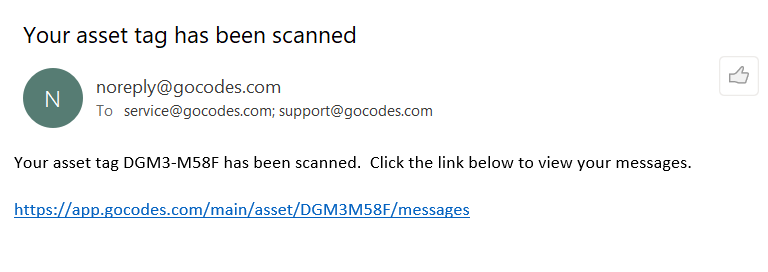
Source: GoCodes Asset Tracking
Additionally, GoCodes Asset Tracking offers:
- GPS trackers for real-time equipment tracking
- Geofencing capabilities with automated alerts when assets leave designated areas
- Simple tools for scheduling routine maintenance
This combination of features ensures construction teams can track, manage, and maintain their assets effortlessly—anytime, anywhere, and on any device with an internet connection.
Signs Your Business Needs Web-Based Asset Management Software
If you’re still wondering whether web-based asset management software is right for your company, take a moment to think about the everyday challenges of managing tools, equipment, and materials.
You might not even realize how much time and money is slipping through the cracks until you see the full picture.
Difficulties Locating Equipment
How much time does your team spend looking for tools and equipment?
If the answer is “too much,” you’re not alone.
Construction sites are fast-paced environments, and assets are constantly being moved from one location to another.
But when there’s no reliable system in place to manage them, valuable time is wasted searching for missing tools.
According to Michael McGowan, region head and CEO of Hilti North America, contractors lose up to 90 hours per month tracking tools.
Additionally, simply because workers can’t find what they need, an entire day of productivity is lost per job site every month.
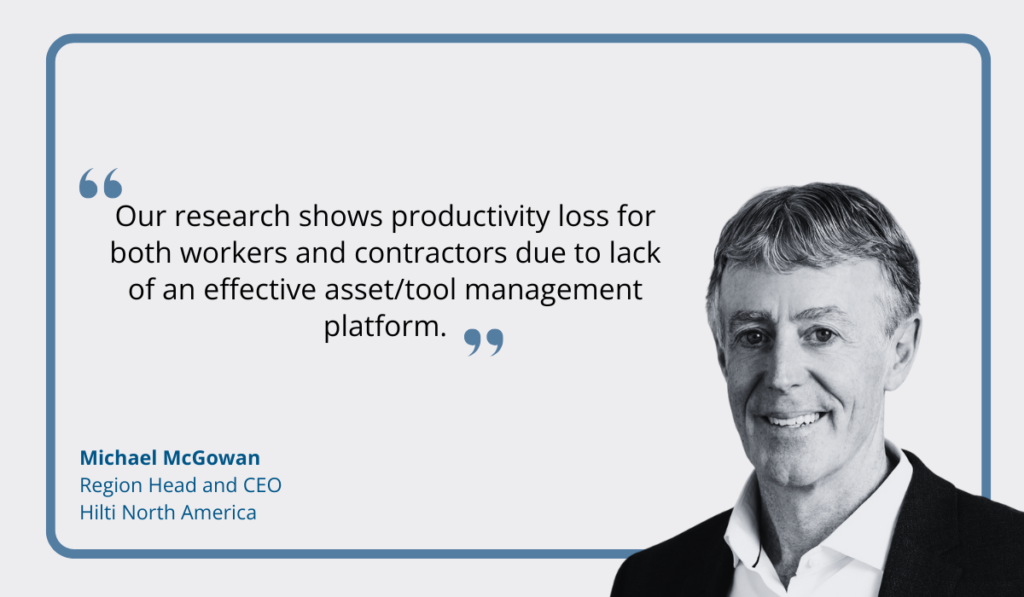
Illustration: GoCodes Asset Tracking / Quote: For Construction Pros
Those delays lead to increased costs, scheduling issues, and frustrated crews who can’t do their jobs efficiently.
This is where web-based asset management software makes a difference.
With a system that tracks equipment in real time, workers don’t have to guess or make phone calls to find what they need.
They can simply open their phones, and instantly, they know where a tool is, who last used it, and whether it’s available.
They can even see it on a map:
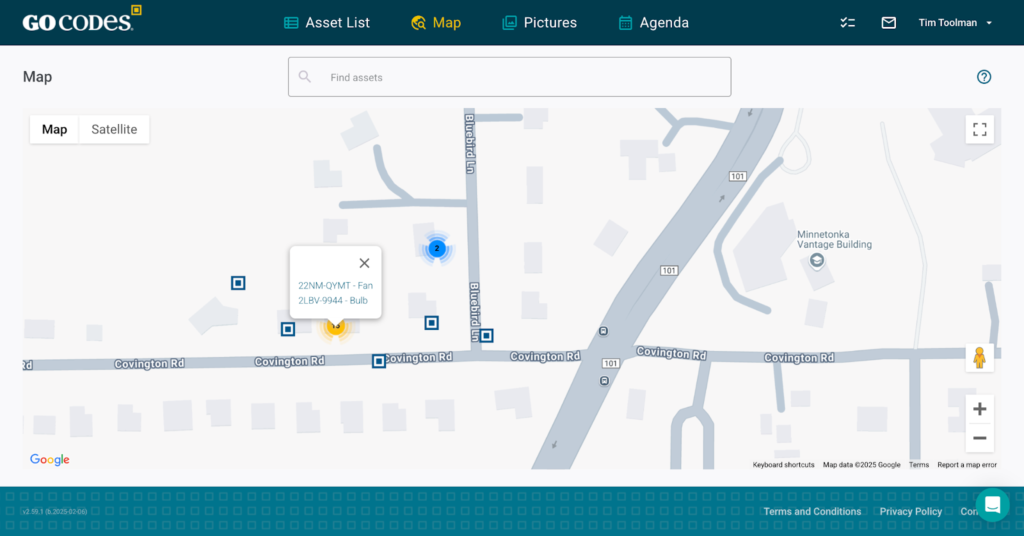
Source: GoCodes Asset Tracking
Not only does this improve productivity, but it also helps with better asset utilization.
When managers have real-time insights into where their equipment is and how often it’s being used, they can make smarter decisions about purchases, rentals, and job site logistics.
But lost equipment may not be your only problem.
Rising Incidence of Asset Theft
Construction sites are prime targets for theft.
Tools and machinery are expensive, and let’s be honest—not every job site has tight security.
In fact, tool theft has been a growing concern for years.
A 2017 study by the Federation of Master Builders found that 51% of builders in the UK had experienced tool theft.
The trade association’s Chief Executive, Brian Berry, explained at the time:
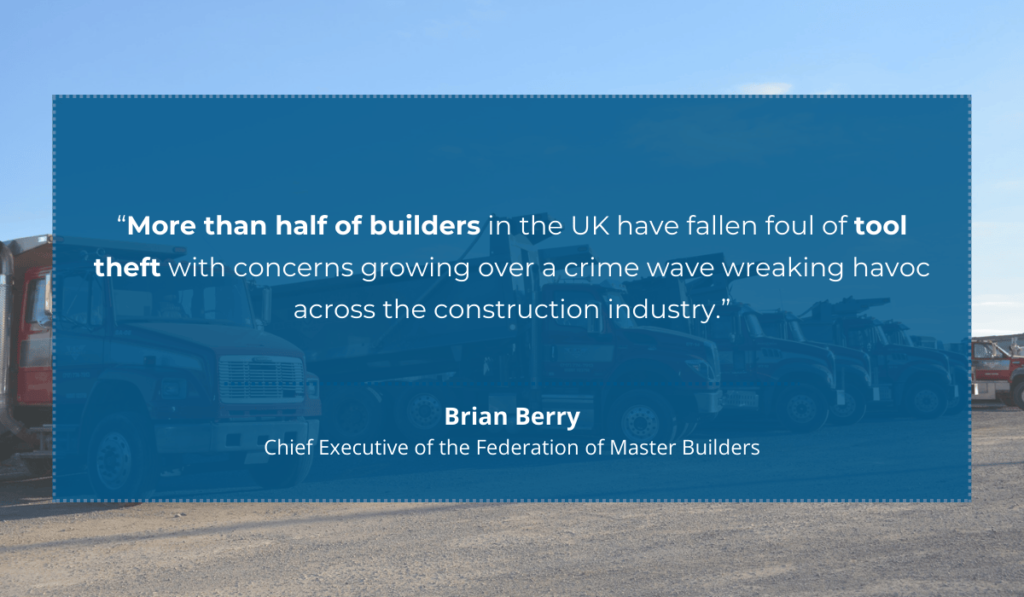
Illustration: GoCodes Asset Tracking / Quote: Allianz
And the problem isn’t going away, either: reports suggest that theft incidents have continued to rise.
Beyond the direct cost of replacing stolen equipment, theft has a wider impact on construction businesses.
According to BauWatch, 31% of projects have been delayed due to construction-related crime.
Even minor incidents can throw off timelines, making it harder for companies to meet project deadlines.
As Annabel Hiatt, Senior Category Manager at Travis Perkins, UK’s largest builders’ merchant, puts it:
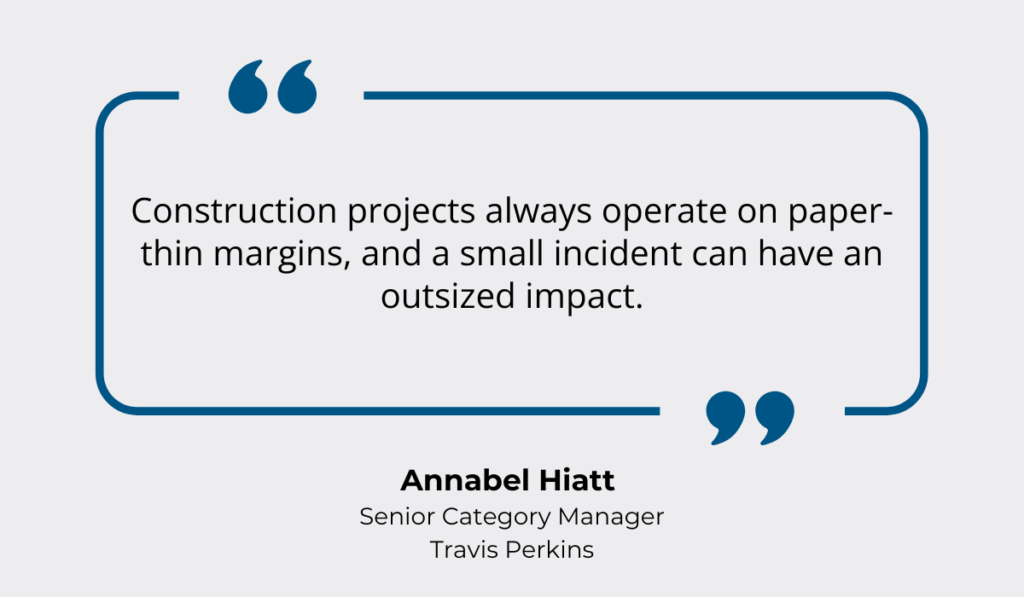
Illustration: GoCodes Asset Tracking / Quote: BauWatch
What’s even more concerning is that not all theft comes from the outside.
BauWatch study also showed that 27% of construction site thefts are carried out by insiders—employees who take advantage of poor tracking systems to take tools without permission.
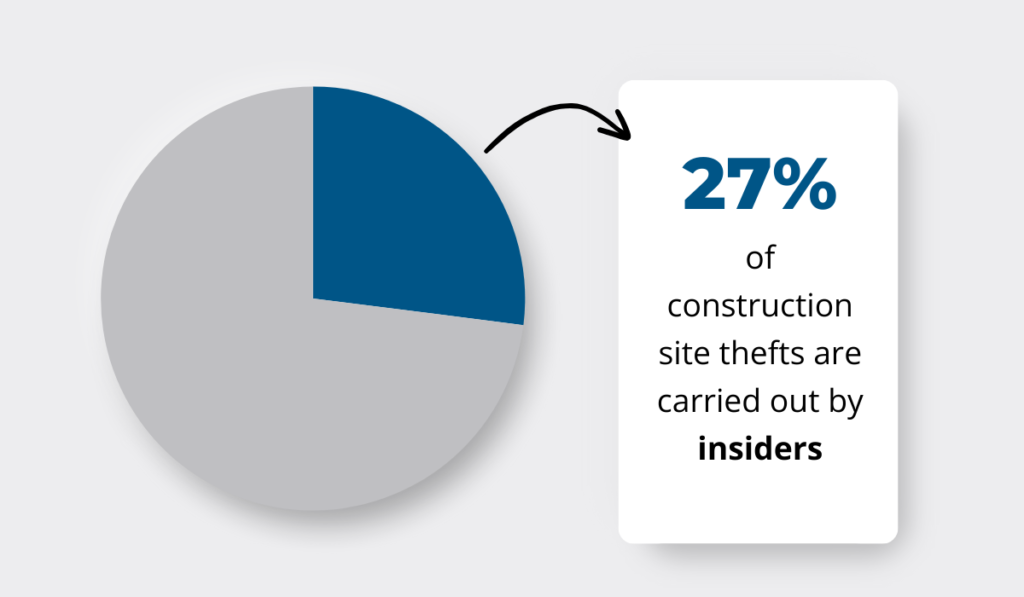
Illustration: GoCodes Asset Tracking / Data: BauWatch
Think about it: If no one knows exactly who checked out a tool, when it was used last, or where it’s supposed to be, it’s easy for things to disappear.
But with a web-based asset management system like GoCodes Asset Tracking, you get an extra layer of security.
Every asset is tagged with a unique QR-coded label, and scanning it instantly shows who accessed it, when, and where.
While someone attempting theft likely wouldn’t check out the tool, the last legitimate scan provides a clear starting point for tracking it down.
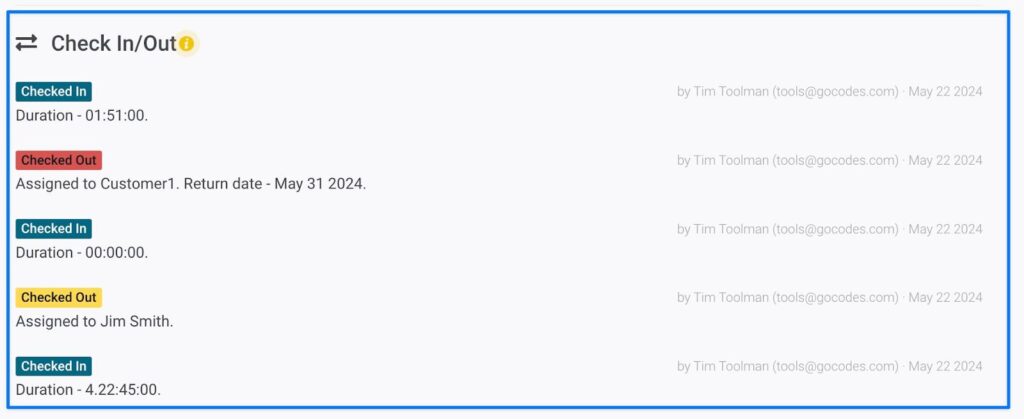
Source: GoCodes Asset Tracking
For high-value assets, GoCodes Asset Tracking offers GPS trackers that provide real-time location data.
If equipment leaves a designated job site unexpectedly, geofencing alerts notify managers immediately, allowing them to act before the item is gone for good.
This combination of real-time tracking, scan notifications, and geofencing is a strong deterrent in and of itself.
When employees know that every asset movement is monitored and logged, the chances of opportunistic theft drop significantly.
Compliance Issues
Beyond theft and lost equipment, another issue construction businesses face is compliance.
Keeping track of maintenance schedules, inspections, and certifications is tough when everything is scattered across spreadsheets, paper logs, or outdated systems.
But falling behind on compliance can have serious consequences—not just fines, but real safety risks.
Take, for example, a case investigated by OSHA in 2023.
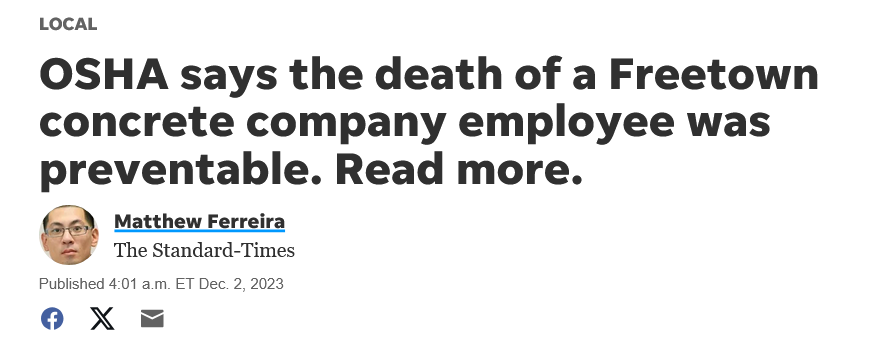
Source: South Coast Today
A construction worker was fatally injured while servicing a soil screener because the company failed to enforce lockout/tagout procedures.
Had there been an easy way for that worker to check safety instructions before performing maintenance, this tragedy might have been avoided.
This is another area where web-based asset management software helps.
When every piece of equipment is tagged and stored in a central system, workers can instantly scan a tool and pull up critical safety information:
- Whether it’s due for maintenance.
- If there are any usage restrictions.
- If it requires specific handling procedures.
Instead of relying on memory or scattered paperwork, safety becomes part of the process.
Statistics confirm this, too.
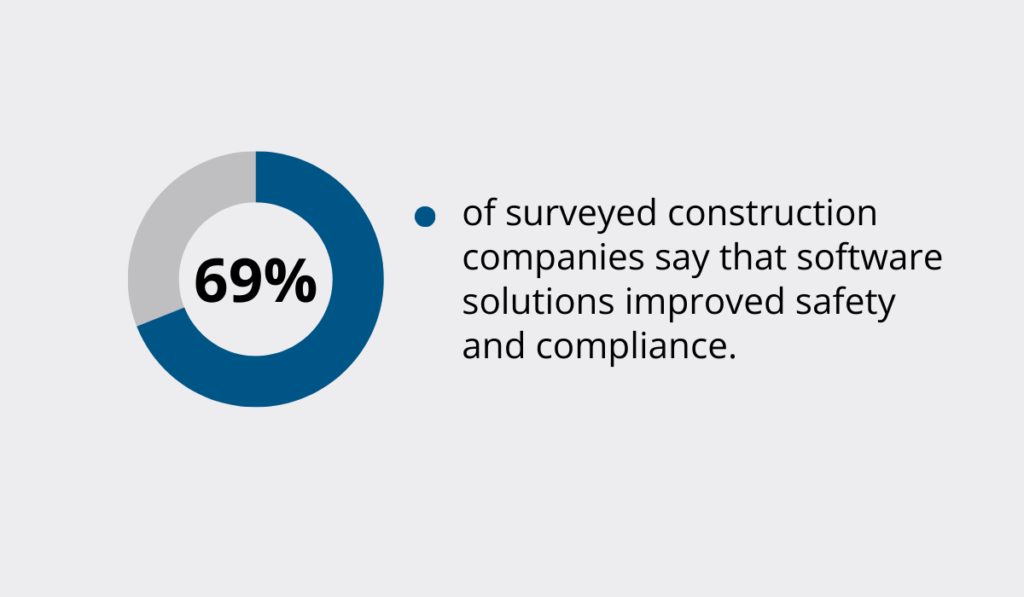
Illustration: GoCodes Asset Tracking / Data: Teletrac Navman
And for managers, automatic record-keeping makes audits a breeze.
They don’t have to scramble to find inspection reports or proof of maintenance—it’s all there, up to date, and ready when needed.
Maintenance Delays
Speaking of maintenance, how many times have you dealt with unexpected breakdowns that could have been avoided?
Equipment failures don’t just cause inconvenience—they create massive project delays and unexpected costs.
Shawn Beinhower, CIO of E.K. Services, who has more than 700 pieces of equipment to manage, knows this too well:
“If it’s an excavator on a pipe crew, then your whole crew’s just sitting there waiting to be fixed. And if it can’t be fixed, then you incur the cost of getting a rental piece in, as well as the lost time waiting for it to be delivered.”
Many of these breakdowns happen simply because routine maintenance is overlooked.
When teams rely on manual scheduling, it’s easy to miss a service check—until a machine suddenly stops working.
In some cases, this can even lead to serious accidents.
Just look at the crane collapse in New York in 2023, which injured 12 people.
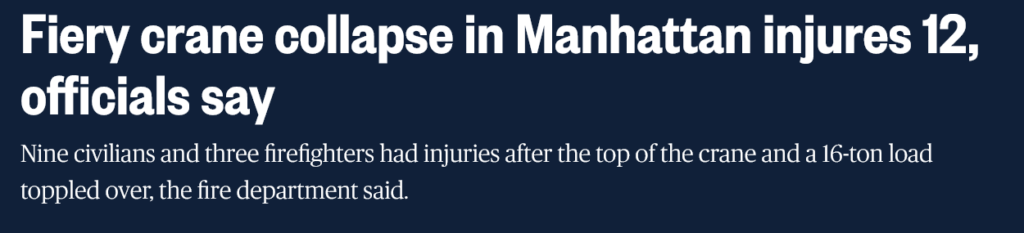
Source: NBC News
The cause?
A hydraulic fluid leak.
Regular maintenance could have caught that issue before it became a disaster.
With web-based asset management software, these risks are minimized.
Instead of relying on memory or spreadsheets to track maintenance, the system automates the process.
When a piece of equipment is due for servicing, the software sends alerts so it doesn’t get overlooked.
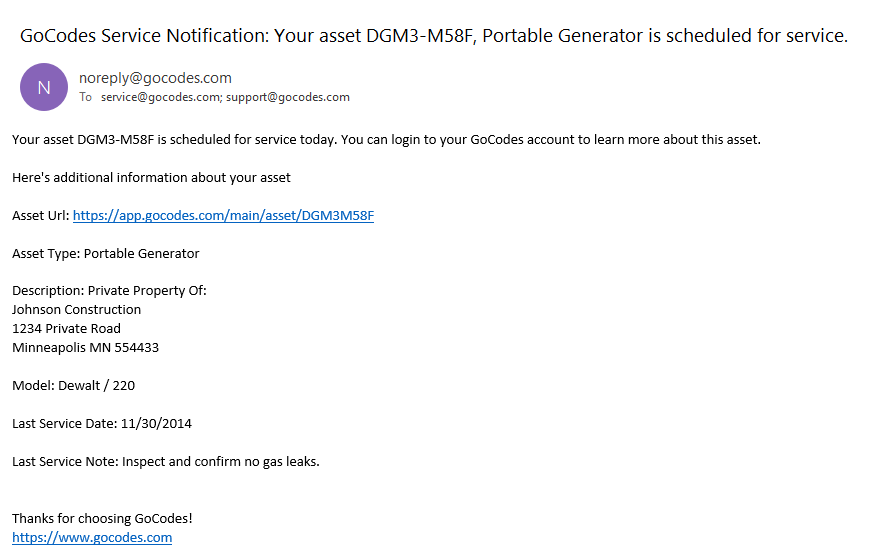
Source: GoCodes Asset Tracking
And if a worker notices an issue on-site, they don’t have to wait until they’re back at the office to report it.
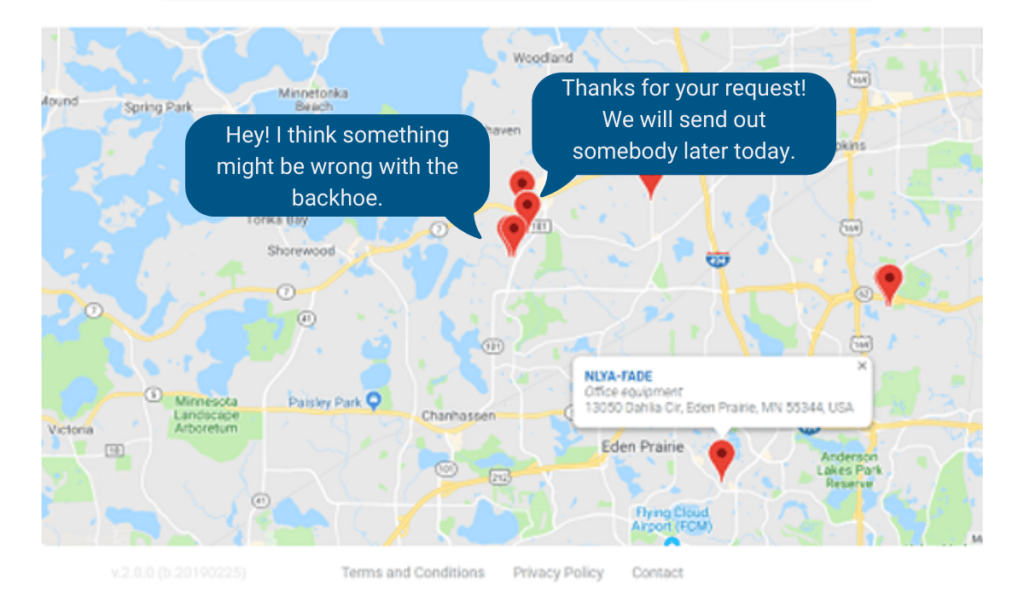
Source: GoCodes Asset Tracking
They can instantly log a problem right then and there on their phone or a tablet, ensuring the right people are notified immediately.
Best Practices for Implementing Web-Based Asset Management Software
By now, you’ve seen the value of web-based asset management software.
But like any new system, its effectiveness depends on how well it’s implemented.
So before we wrap up, here are three things to keep in mind when implementing web-based asset management software.
Choose a Scalable Solution
Your asset management needs today won’t be the same five years from now.
As your company grows, so will your equipment, job sites, and workforce.
That’s why it’s crucial to choose a web-based system that scales with you—one that can handle more assets, users, and locations without performance issues.
Look for a cloud-based platform with real-time tracking, mobile accessibility, and flexible reporting.
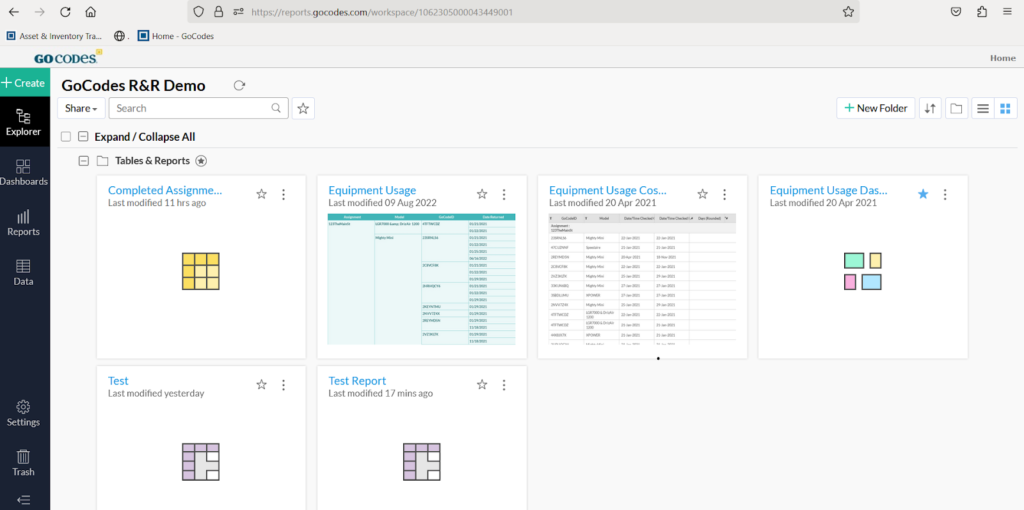
Source: GoCodes Asset Tracking
That way, workers in the field can check asset availability instantly, and managers can oversee everything remotely—without investing in costly IT infrastructure or software upgrades.
A system that integrates with other tools (such as ERP or project management software) will also make it easier to adapt as your business evolves.
Provide Hands-On Training
Even the best software won’t help if your team doesn’t use it.
In fact, a Gartner survey found that 60% of employees experience frustration with new software, often because they weren’t properly trained.

Illustration: GoCodes Asset Tracking / Data: Gartner
The good news?
Web-based asset management tools are typically more intuitive than traditional systems.
Unlike complex enterprise software that requires IT specialists, most web-based solutions are designed for simplicity.
And since web-based platforms work on smartphones and tablets—and any device with an internet connection—they’re easier for field workers to adopt.
Instead of tackling a complicated system, they can simply scan a QR code or RFID tag to check out equipment, log usage, or report a maintenance issue—all from their phone.
Still, to make adoption smoother:
- Train a small pilot group first, so they can help you train the rest of the team.
- Show workers exactly how the system fits into their daily tasks.
- Make sure they have an easy way to ask questions and get help when needed.
The goal is to show workers that this software makes their jobs easier, not harder—and once they see the benefits, adoption becomes second nature.
Measure Software’s Impact
Once your system is in place, how do you know if it’s actually working?
The answer is data.
Measuring key performance indicators (KPIs) helps you track the success of your implementation and its ROI, as well as identify areas for improvement.
Start by setting clear goals.
For example:
- Are you trying to reduce lost equipment?
- Minimize downtime from unexpected repairs?
- Or perhaps speed up audits?
Pick a few critical metrics and track them over time.
And when you can show real improvements—like cutting equipment search times in half or saving thousands on theft prevention—it becomes much easier to justify expanding the system further.
So, the more you measure, the more value you get from the software.
Conclusion
If your business is dealing with constant equipment searches, rising theft, compliance headaches, or unexpected maintenance failures, it might be time to rethink how you manage your assets.
As we illustrated today, web-based asset management software is a solution to the everyday problems that slow down construction projects and drive up costs.
How much longer can you afford to go without it?