Tool calibration is an important part of any construction company’s maintenance and construction process.
In order to correctly conduct tool calibration, it is vital to first understand what it is, and be aware of the many reasons why it is important to maintain calibration at the proper intervals.
There are many factors that determine how frequently tool calibration is scheduled, including industry standards and input from company operators.
Various considerations also direct which tools should be calibrated and when.
Following a definitive process has the best chance of resulting in consistent tool calibration, and software solutions like GoCodes Asset Tracking are invaluable for managing it.
In this article...
What Does It Mean to Calibrate a Tool?
Understanding what tool calibration is and what it involves is vital for successfully integrating it into your construction company.
Tool calibration is the process of ensuring the accuracy of measuring instruments by contrasting a tool’s measurements against known and standard data.
It is important to note that not all tools require calibration. Only those producing measurements require this process.
Here’s a list of some tools and equipment that do require it:
- Barometers
- Residual current devices
- Balances
- Weight and mass instruments
- Pressure calibrators
- Thermal cameras
- Scales
Even if a tool is working correctly in other aspects, it could require calibration, or it might provide inaccurate measurements and data.
Although it is impossible to perfectly match a measuring standard each time, allowing for adjustments within an acceptable deviation can provide a reliable guideline.
The chart below indicates the factors to keep in mind in tool calibration:
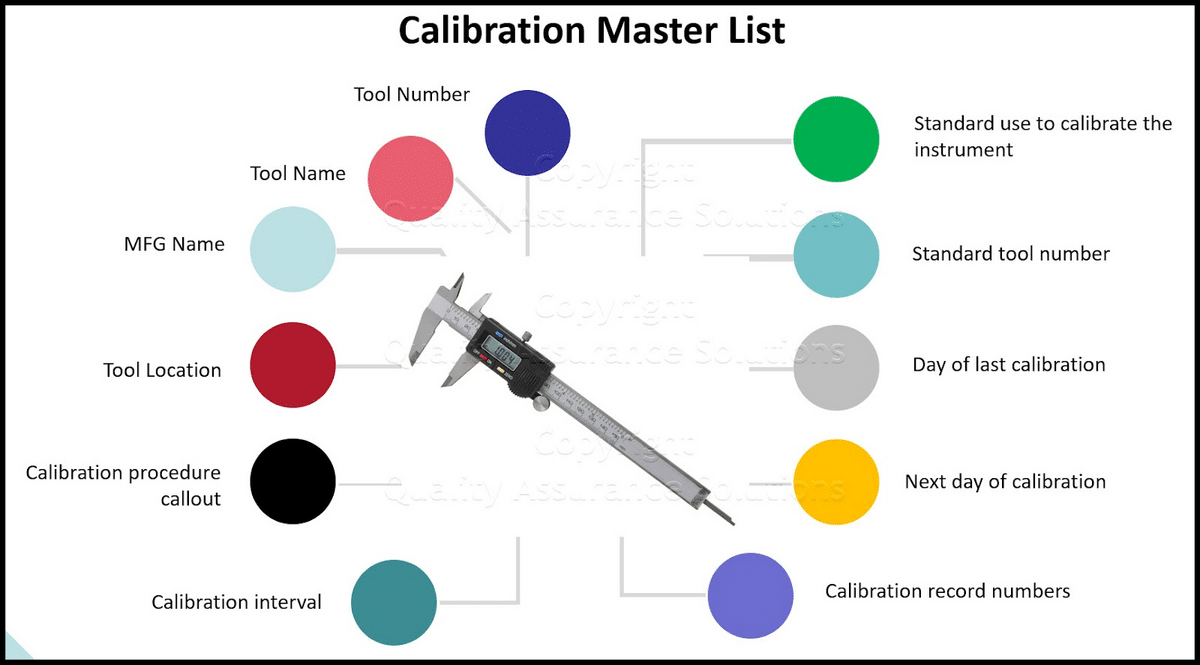
This is especially important for tools that establish quality assurance. By checking for accuracy in this way, regularity in production is more easily achieved.
It is important to note that both digital and analog machines might require calibration.
When tool calibration is part of regularly scheduled preventive maintenance, it is much easier to depend on properly aligned tools.
Why Should You Calibrate Construction Tools?
Calibrating construction tools is indispensable in ensuring accuracy.
Because a tool’s accuracy can decline due to overuse, environmental issues like rust, or simply improper use, it is important to calibrate tools regularly to avoid errors.
The errors that accumulate as part of this degradation are usually referred to as drift.
Take a look at the infographic below, provided by Chicago Pneumatic, to see why calibration is so important.
The infographic shows how the torque value of a kind of nutrunner for tightening the bolts on the wheels of a truck changes with use.
As you can see in the video, although the tool shows the same value over time, independent analyses reveal deviations from the indicated value that go beyond what’s acceptable.
However, regular calibration will lead to adjustments that will improve the tool’s functionality and prolong its useful life.
In short, while uncalibrated tools can negatively affect output, regular calibration will improve performance, and ultimately lead to cost savings and better organization.
Not only does regular construction tool calibration encourage more acceptable tolerance intervals and contribute to a reduction in expenses, but it also carries the following benefits:
- Improved product quality
- Enhanced tool accuracy
- Increased customer satisfaction
- Minimized damage from error-prone tools
- Earlier detection of deviations to company processes and improved optimization
- Better integrity of manufacturing processes
- Greater regulatory compliance
- Diminished scrap costs
While it’s important to avoid over-reliance on construction tool calibration alone for performance, customer service and quality, there are many ways in which it can contribute to smoother execution in all aspects of your construction company.
In addition, calibration is important because it can help create a more predictable and safer work environment.
How Often Should You Calibrate Construction Tools?
For best results, construction tool calibration should take place on a regularly scheduled basis. It is usually more efficient to regard tool calibration as a part of preventive maintenance.
Here are some things to consider when attempting to understand tool calibration.
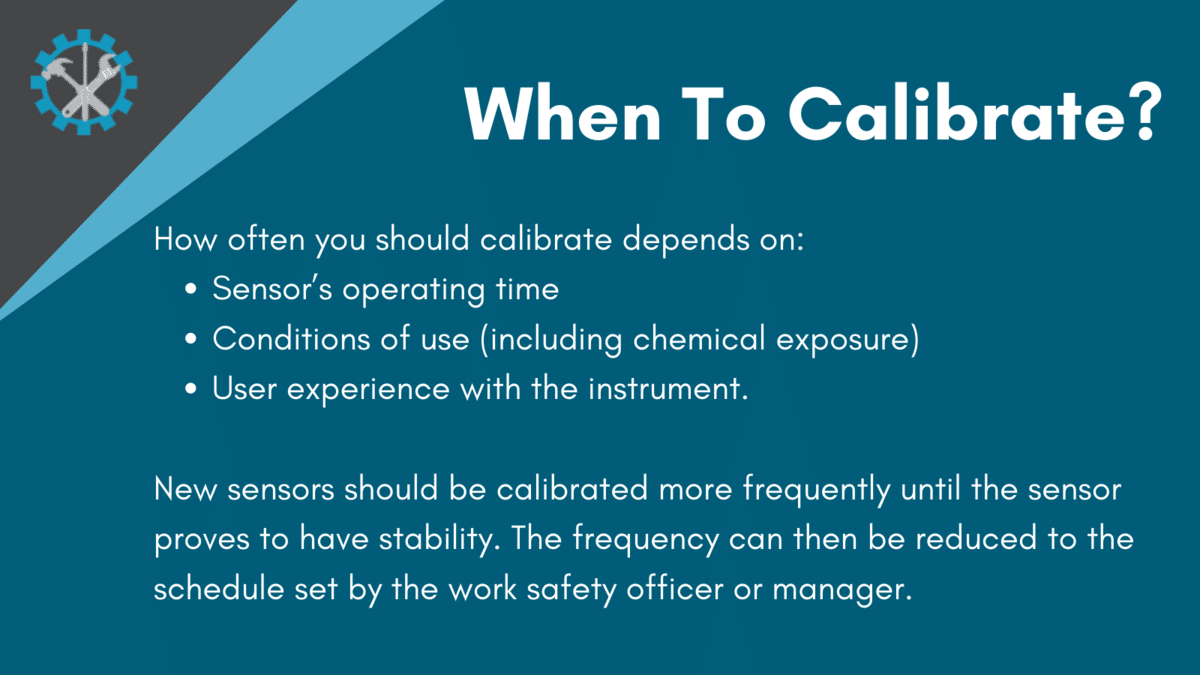
To decide how often to calibrate your construction tools, make certain to consult the tool manufacturer’s calibration frequency recommendations.
These will communicate the best parameters for calibration.
For example, some manufacturers recommend that tools be calibrated after a certain number of use cycles, time used, or mileage, and doing so more frequently than recommended can lead to wasted time, resources, and money.
In addition to this, it is also a good idea to consider how long a tool tends to remain calibrated.
If it usually drifts more often than other items your company has previously owned or used, strongly consider talking to your maintenance staff, operators, and team members about a reasonable calibration schedule.
Finally, consider whether or not the equipment presents a potential safety risk.
With this in mind, some industries, labor contracts, OSHA (Occupational Safety and Health Administrations) rules, and municipal laws regulate how often certain pieces of equipment should undergo calibration.
Which Construction Tools Should You Calibrate?
Carefully attending to tool calibration in every aspect of your business can help to increase profits and efficiency.
This can also help you accurately predict your assets’ positions in their life cycles.
Construction companies work with more than tools used for building.
Production, office, and organizational activities might also require calibration. For example, construction tools that should undergo calibration include scales.
Some might not classify scales as a construction tool or even a tool at all, but they require maintenance and monitoring.
On the other hand, here are some traditional construction tools that usually require regular calibration:
- Laser distance meter
- Level meters
- Gas detectors
- Electrical testers
- Hardness detectors
- Feeler gages
- Socket testers
- Insulation testers
It is vital to ensure that such tools are calibrated to render accurate measurements.
Maintaining correct measurements constitutes a major part of correctly completing a construction job, keeping your work area safe, and helping to ensure customer satisfaction.
What Is the Process of Calibrating Construction Tools?
The process of calibrating tools can differ widely from one tool to the next, so there are several considerations that go into making sure you’re doing it effectively.
First, it is important to determine who should calibrate the tools in your construction company.
Some items are easily maintained by your own team members, but some tool calibration may only take place within an ISO/IEC 17025-certified laboratory.
Once you have determined who should calibrate your construction tools, the process can really take place.
Traditionally, the industrial tool calibration process undergoes six phases, so let’s take a look at what they are.
First, you must verify that the equipment requires calibration, as well as the schedule on which this should take place.
Then, it is imperative to decide which process to use for calibration, as well as whether the calibration should constitute a separate action or take place as a regular part of preventive maintenance.
This step also includes deciding on which parameters should be recorded, such as test results, extra reviews, and test protocols.
Next, assign specific responsibilities to specific employees. When choosing which of your team members should take on calibration duties, consider the following:
- Knowledge of and experience with calibration
- Familiarity with the equipment
- Amount of training and formal education with the tool
- Commitment to safety
- Ability to properly follow instructions
Without selecting staff members or a trustworthy lab to undertake calibration tasks, this important aspect of safety and accuracy might become lost in other duties.
The next phase–deciding on custody of calibration tools and equipment–is as important as assigning calibration tasks.
For example, is it best to maintain the equipment in a locked tool cage, or is that area already full of assets? Is it safe to keep them in a work area?
What about the appropriateness of keeping this equipment in an office area? Exploring all of these options can help you and your team make the best decision.
Finally, the calibration process requires the identification of relevant standards. What is the standard deviation or acceptable margin of error for the instrument?
This is another good time to check with the manufacturer’s instructions or an ISO/IEC 17025 lab for reasonable ranges.
To manage the calibration process, it is a good idea to rely on software, so that’s what we’ll be covering next.
Why Should You Use Calibration Management Software?
Since tool calibration is so important in many aspects of the construction industry, calibration management software is a smart investment.
For instance, a system such as our own solution, GoCodes Asset Tracking, is invaluable where organization, information storage, and ease of use are concerned.

GoCodes Asset Tracking is designed for use with technology with which most employees are already familiar—namely, smartphones and similar devices.
Data is safely and securely stored, and team members may receive different levels of authorization as appropriate.
Most importantly, the tasks feature is ideal for calibration applications, and automating these actions boosts reliability as well as efficiency.
The ease with which GoCodes Asset Tracking is applicable to future task scheduling means that construction companies can assign calibration and service tasks to employees in seconds.
Conclusion
Tool calibration is the process of verifying the accuracy of a tool. Conducting it regularly contributes to efficiency, safety, and cost savings.
Determining which construction tools should undergo calibration, as well as how often, helps to maintain a streamlined process.
Managing a calibration process is greatly facilitated by the use of the right calibration management software, and a solution such as GoCodes Asset Tracking is useful in every phase of the process.