Key Takeaways:
- Start your audit with a complete, up-to-date inventory that includes all tools.
- Use asset tracking software to automate audits, reduce errors, and improve accountability.
- Schedule regular audits, assign clear roles, and check tool conditions to prevent loss and downtime.
Think your job site’s tools are all accounted for? Think again.
Missing drills, duplicate records, unmarked equipment—these aren’t just minor headaches.
They’re costly liabilities that pile up fast. That’s where a well-run tool audit can save your budget and your timeline.
In this guide, we’ll walk you through five proven tips to run successful tool audits that boost accountability, reduce loss, and keep your projects running smoothly.
In this article...
Start with a Comprehensive Tool Inventory
Every strong tool audit starts with creating a comprehensive, up-to-date inventory.
Why?
Because if your tool list is incomplete or outdated, your audit results will be, too.
That’s why your first step is to gather a complete, detailed inventory of every tool and asset in your system—no exceptions.
And don’t make the mistake of listing just the big-ticket items like generators and jackhammers.
Instead, make sure to include smaller, easily misplaced gear, too: think torque wrenches, extension cords, and hand tools.
For each tool, be sure to log all the essential details, such as serial numbers, model types, last known locations, and to whom the item is assigned, just like in the example below.
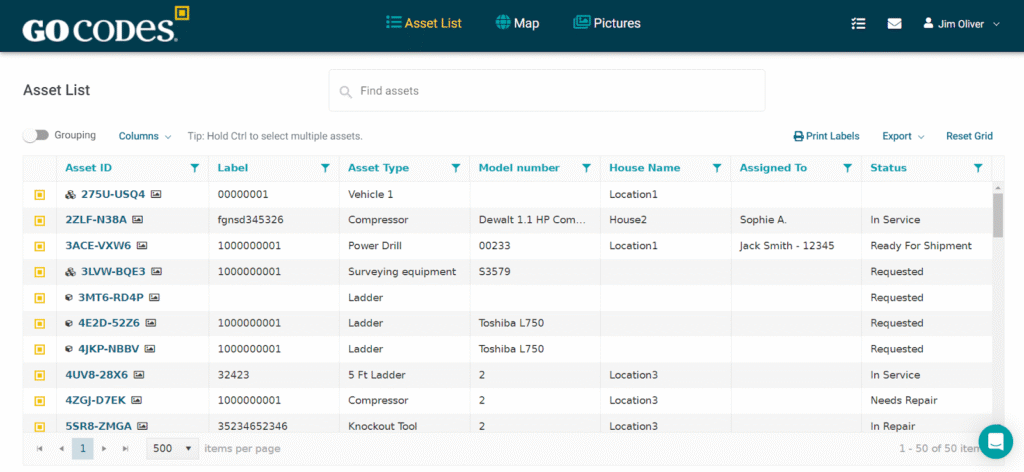
Source: GoCodes Asset Tracking
Your list should also consider how tools are grouped.
Kitting assets that are often used together—for example, a power drill, charger, and spare batteries—can simplify inventory workflows and prevent confusion when individual components go missing.
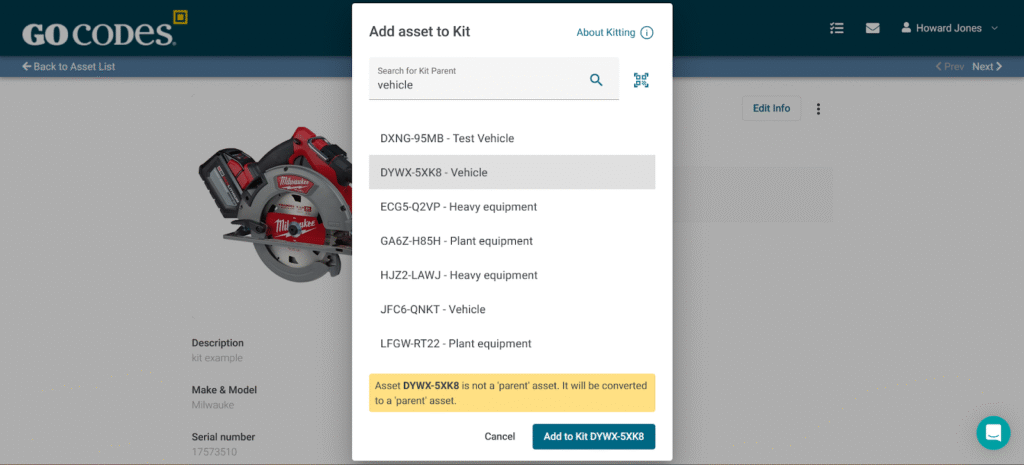
Source: GoCodes Asset Tracking
But the consequences of incomplete records go beyond inconvenience.
Not keeping track of your tool inventory can lead to severe financial losses, too.
Take the experience of the restoration contractor J&M Keystone, Inc., for example.
Their former operations manager, Lee Sherman, explains that the company experienced huge financial drain from accidental tool and equipment loss:
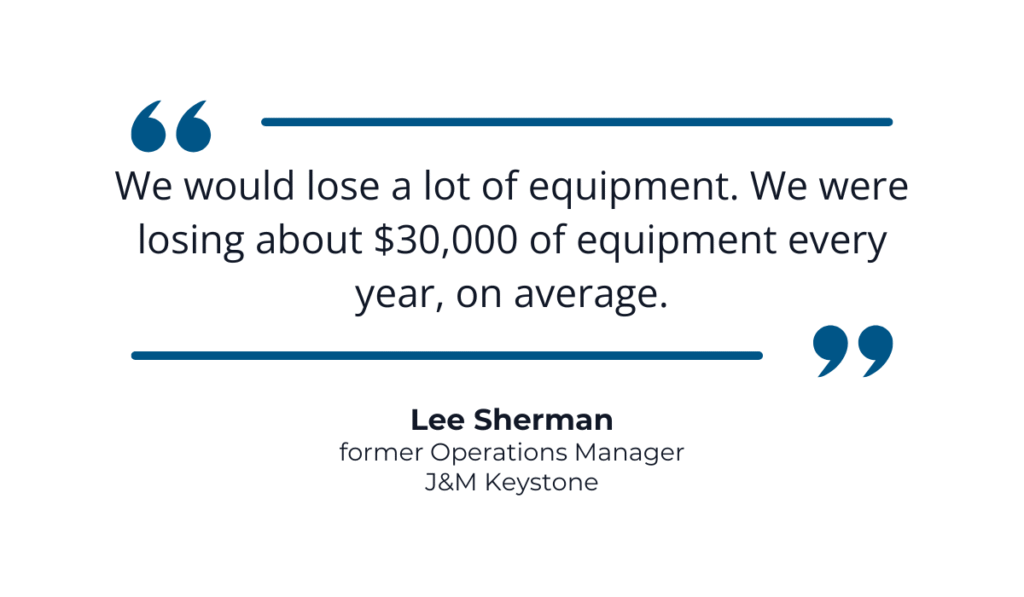
Source: GoCodes Asset Tracking
Having spotted that loss, they realized that they needed to change something, so they invested in GoCodes Asset Tracking, an asset tracking solution.
As a result, the loss dropped from $30,000 to about $1,500 a year—a significant reduction.
The visibility they got from making this one change translated into tangible savings and smoother operations across the board.
So, let’s explore what asset tracking software can do in more depth.
Invest in Asset Tracking Software
Manual spreadsheets just don’t cut it anymore, no doubt about it.
If you’re still keeping track of your tools on paper or using Excel, you’re not only wasting time—you’re also increasing the risk of errors, duplication, and lost assets.
Asset tracking software solves that challenge by centralizing your tool data, automating check-ins and check-outs, and creating a real-time audit trail in the process.
A solution like our GoCodes Asset Tracking takes it even further with built-in QR code tracking.
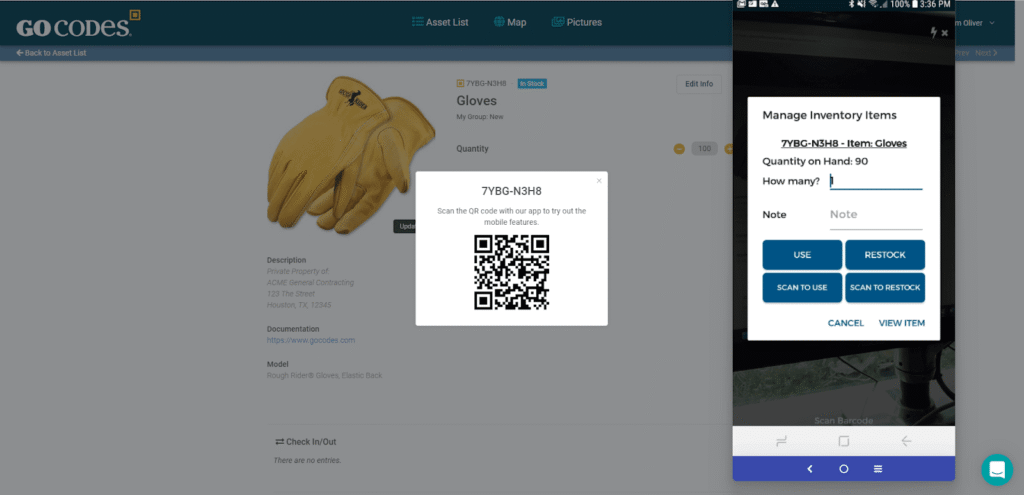
Source: GoCodes Asset Tracking
All you need to do is scan the QR-coded label attached to the asset to instantly see where it is, who has it, and when it was last used.
And the best part is, you and your staff can do all that on the go, using your mobile devices—no need for handheld scanners.
This also means no more hunting through job trailers or making phone calls to track down missing gear, because the GoCodes Asset Tracking check-in/check-out system lets teams manage tools directly from their phones.
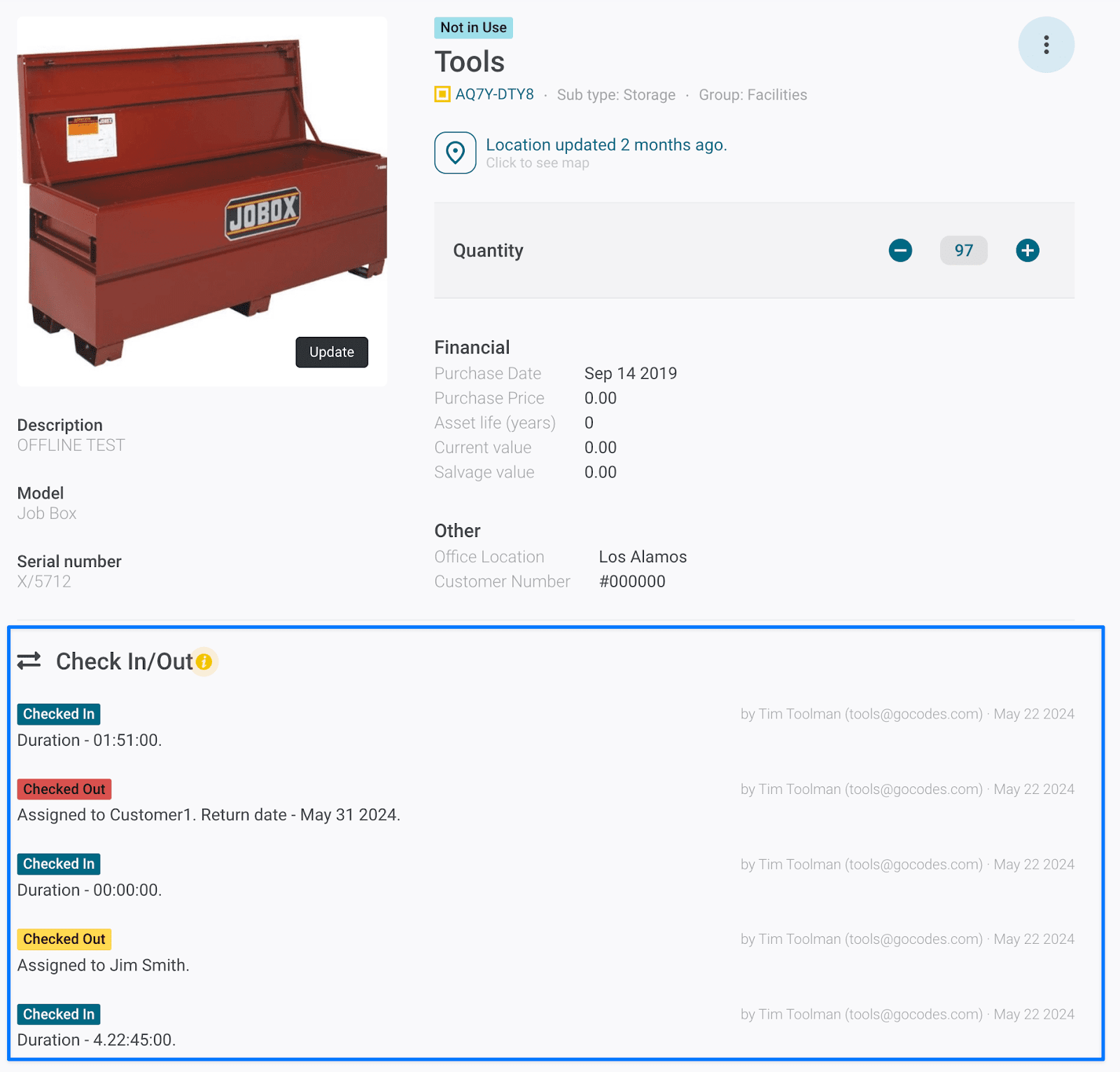
Source: GoCodes Asset Tracking
On top of that, supervisors can view live tool locations, monitor usage trends, and flag overdue returns.
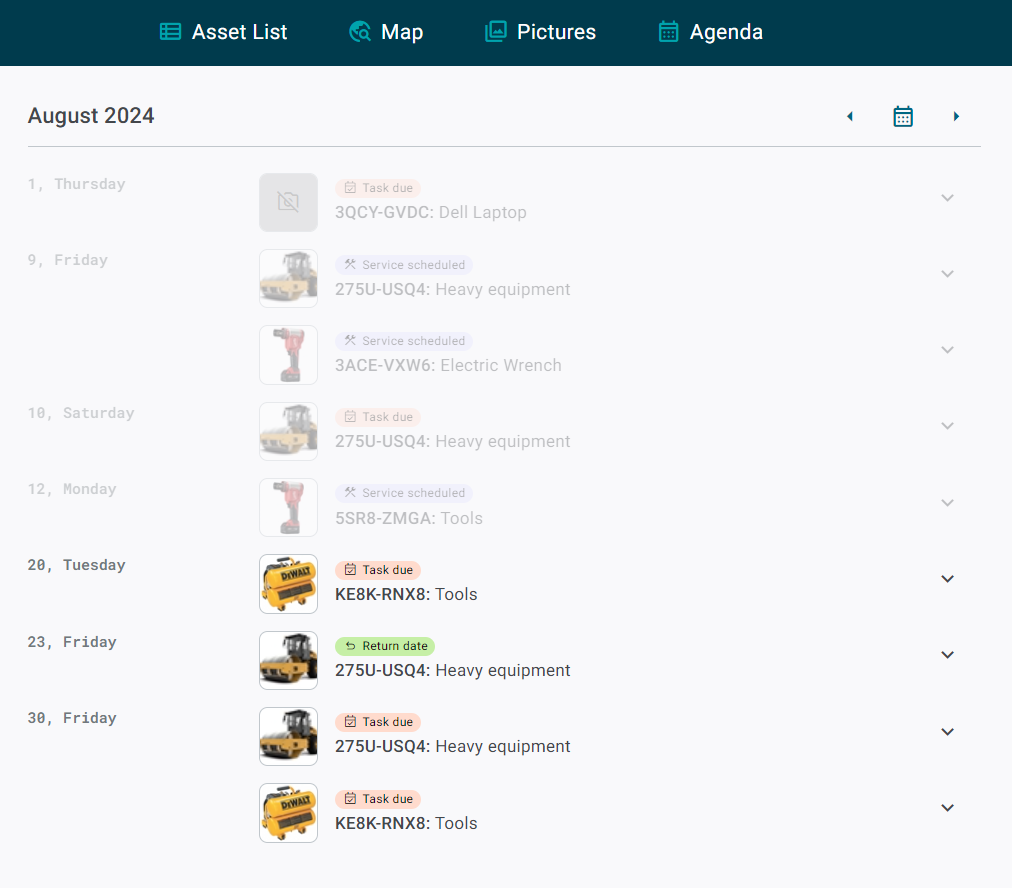
Source: GoCodes Asset Tracking
Each of these transactions is automatically recorded, creating a built-in audit trail.
This level of transparency encourages accountability across the entire team, which translates to fewer disputes or finger-pointing when something goes missing.
And with the GoCodes Asset Tracking audit feature, users can run fast, reliable audits right in the field, without needing to pull up dusty spreadsheets or flip through paper records.
You can see just how easy this is in the video below:
Source: GoCodes Asset Tracking on YouTube
Overall, investing in an asset tracking solution is a huge shift from traditional inventory methods.
Yes, spreadsheets might work on day one, but they become a mess as your inventory scales.
They’re static, prone to human error, and lack any real traceability.
Paper logs? Even worse: easy to lose, hard to read, and impossible to update in real time.
When you replace these outdated systems with mobile-ready software, you speed up every step of the audit process.
You also increase accuracy, because you’re eliminating manual data entry.
And since the data is centralized and constantly updated, your audit reports reflect reality—not outdated guesses.
The bottom line is, asset tracking isn’t a “nice to have” anymore. It’s the backbone of audit speed, tool accountability, and operational efficiency.
Schedule Regular Audit Intervals
Tool audits aren’t one-and-done. For audits to actually work, they need to become a part of your routine.
That means setting consistent, repeatable audit schedules—whether that’s monthly, quarterly, or aligned with project cycles.
The key is to strike a balance between thoroughness and feasibility.
If your company manages a large fleet of tools across multiple job sites, quarterly audits may be more realistic than monthly ones.
On the other hand, high-turnover or high-loss environments might benefit from more frequent checks.
Regular audits reduce the risk of cascading loss, where one missing item triggers a domino effect of project delays, reorders, or blame games.
But here’s the thing: consistency matters more than frequency.
A perfectly timed audit once a quarter beats a rushed one every month.
Your audit schedule should match your team’s capacity and your project load. Here’s a quick cheat sheet:
Operation size | Audit frequency |
---|---|
Small companies (under 100 tools) | Quarterly audits |
Medium operations (100–500 tools) | Monthly or bi-monthly audits |
Large-scale firms (500+ tools across job sites) | Monthly audits, with rotating team-level spot checks |
The goal is to build a habit of accountability that’s achievable, repeatable, and valuable.
And let’s not forget that regular audits also help with regulatory compliance.
In some states, routine equipment checks are a requirement for OSHA reporting or site inspections.
Neglecting these inspections doesn’t just invite safety risks—it can hit your wallet hard.
OSHA fines can climb past $15,000 for a single violation, and if the issue drags on past their deadline?
You’ll rack up that amount every single day until it’s fixed.
And if they decide it’s a willful or repeat offense, brace yourself: those fines can be ten times higher.
So skipping audits doesn’t just cost you tools. It could cost you your safety rating or license.
Using automated audit features in your software can help you stay on track with regular audits and make sure this doesn’t happen.
GoCodes Asset Tracking, for instance, lets users enter Audit Scanning Mode to quickly confirm asset presence and log findings in real time.
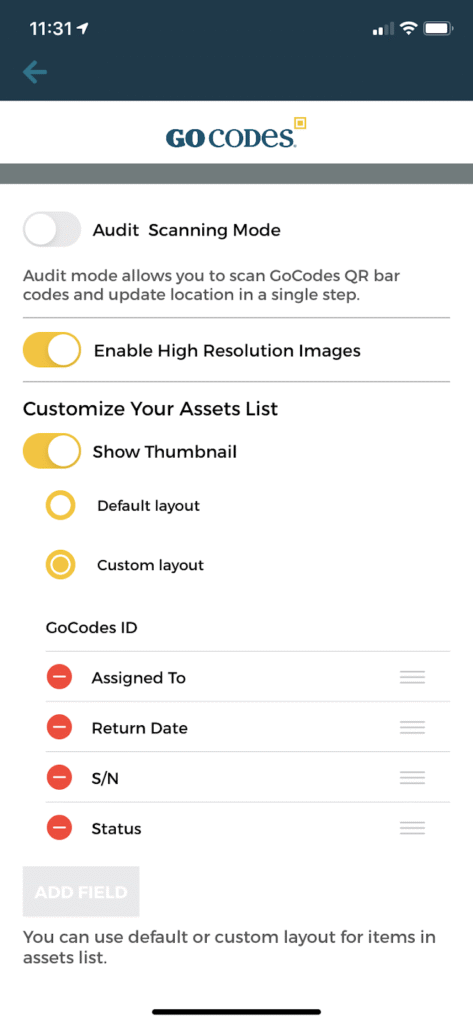
Source: GoCodes Asset Tracking
Remember: frequency doesn’t matter if you can’t sustain it.
So, pick a cadence your team can realistically maintain, and stick to it. Consistency builds trust in your data and confidence in your crews.
Assign Clear Responsibility for Tool Audits
Who’s in charge?
That’s a question too many construction teams struggle to answer when the time comes to perform a tool audit.
And when nobody owns the process, tools go missing, mistakes go unnoticed, and accountability disappears.
That’s why it’s crucial to assign clear roles in your audit process.
Start with a designated audit lead—typically a site manager, inventory supervisor, or tool crib manager.
This person is responsible for organizing the audit, assigning tasks, and reviewing the final results.
However, this doesn’t mean that all the responsibilities associated with auditing tools should fall solely on their shoulders or be handled in isolation.
Cris Lauer Aranda, an Enterprise Account Executive at OSA Commerce, explains:
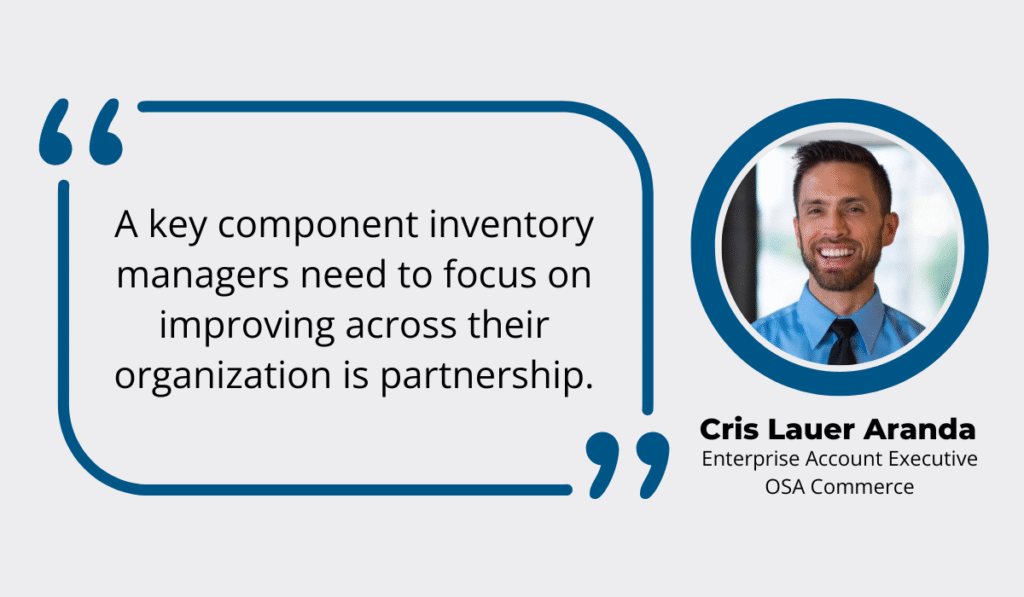
Illustration: GoCodes Asset Tracking / Quote: One-Key Resources
Auditing requires cross-functional collaboration, not just individual effort.
When everyone involved understands their role in maintaining tool inventory integrity, audits become more efficient and less error-prone.
But how do you determine who will take ownership of what?
This is where using the RACI method can help.
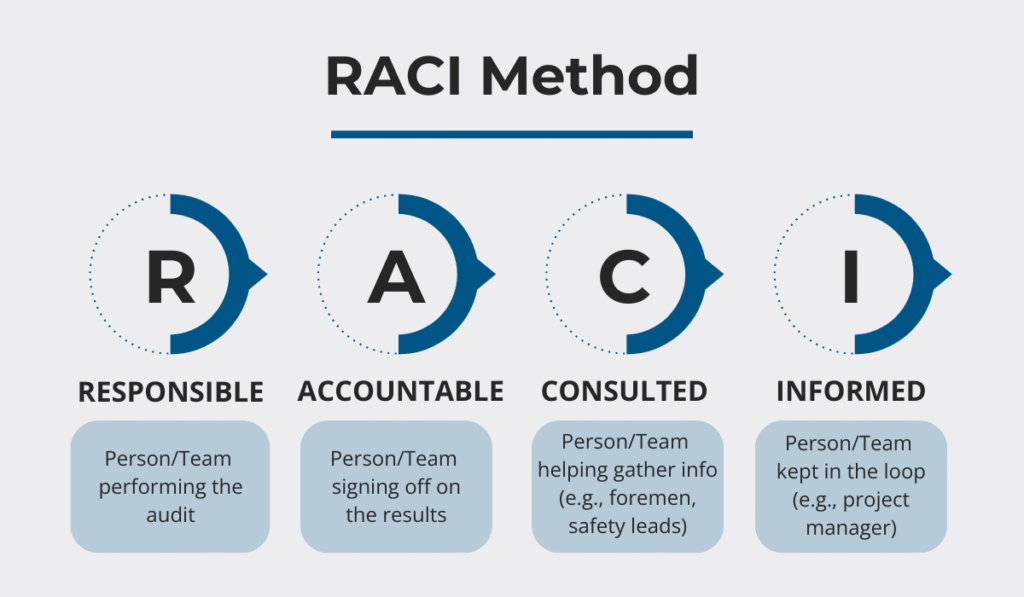
Source: GoCodes Asset Tracking
When roles are clear, audits run faster, and the results are more reliable.
Also, don’t overlook training.
Even if your team is tech-savvy, they still need a standardized process for handling scans, flagging condition issues, and documenting results.
A short training session or onboarding guide can prevent inconsistent entries that derail your records.
So, give your crew the structure and support to succeed, and your audits will speak for themselves.
Assess the Condition of Your Tools
Audits aren’t just about what’s there: they’re also about what shape it’s in.
Every time you run a tool audit, you’re also getting an opportunity to assess the condition of your assets.
Is the battery corroded? Are safety tags up to date? Is the tool working at full capacity, or barely limping along?
After all, construction tools take a beating.
Between weather, transport, and daily use, it’s easy for damage to go unnoticed until something breaks—and suddenly you’re facing downtime, delays, or worse, safety issues.
During audits, include a physical inspection checklist:
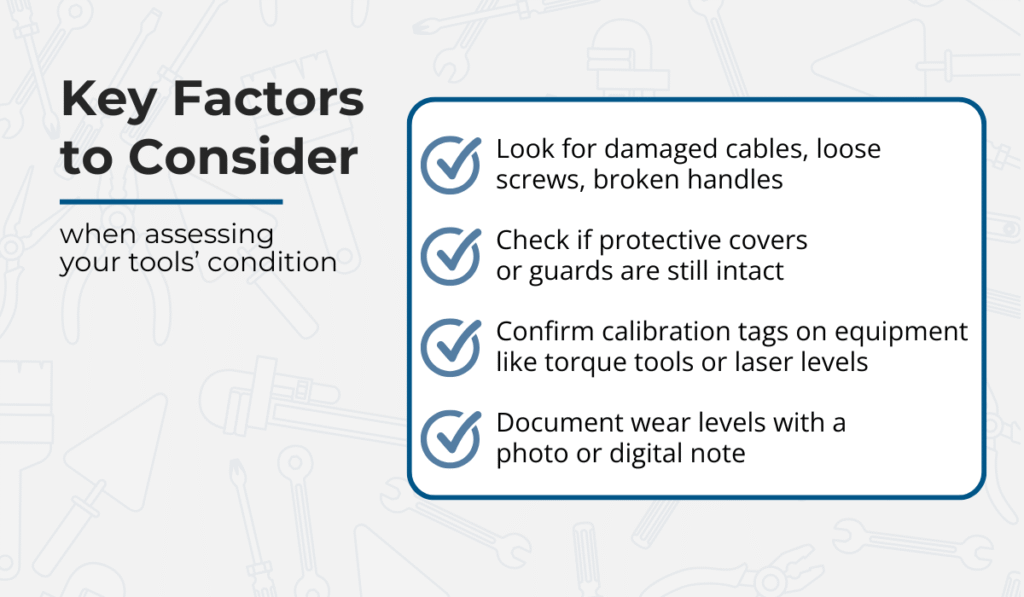
Source: GoCodes Asset Tracking
If a tool is nearing the end of its life, log it for retirement or replacement.
After all, it’s better to budget proactively than deal with an urgent breakdown that will derail your operations and incur additional costs.
And let’s not forget safety. A single malfunctioning grinder or faulty extension cord could put your entire team at risk.
So, don’t just assume that your tools are operable, advises Ralph Natale, Safety Director at McKamish Inc., a leader in HVAC, plumbing, piping, and metal fabrication.

Illustration: GoCodes Asset Tracking / Quote: ACHR News
Use audits as an opportunity to trigger maintenance or upgrades.
It’s not just about keeping the job moving—it’s also about keeping your people safe.
Conclusion
A successful tool audit doesn’t just track what you own—it transforms how you manage it.
By building a thorough inventory, adopting smart software, scheduling consistent reviews, assigning clear roles, and checking tool conditions, you create a system that works for you, not against you.
In the construction industry, where every delay matters and every dollar counts, staying on top of your tools gives you a real competitive edge.
Start your next audit with confidence, and let GoCodes Asset Tracking help make it your easiest one yet.