Key Takeaways
- Tracking drivers’ work and rest hours is crucial for compliance with Hours of Service regulations
- Route optimization can speed up operations as well as reduce fuel consumption and CO2 emissions
- Fuel costs are a number one business challenge for 47% of fleet operators
Looking to optimize your fleet or equipment management with telematics but unsure what to expect?
Curious about what these systems actually bring to the table?
Don’t worry, we’ve got all the answers.
In this article, we’ll walk you through all the different types of data telematics can deliver and show you exactly how to use it to transform your operations.
And by the time you’re finished reading, you’ll be more than well-equipped to boost the overall safety, efficiency, and profitability of your assets.
Let’s get started.
In this article...
Location Data
With real-time GPS tracking, route histories, and trip logs provided by telematics, you can get a complete picture of where your equipment has been and where it is at any given moment.
Below, you can see what that might look like.
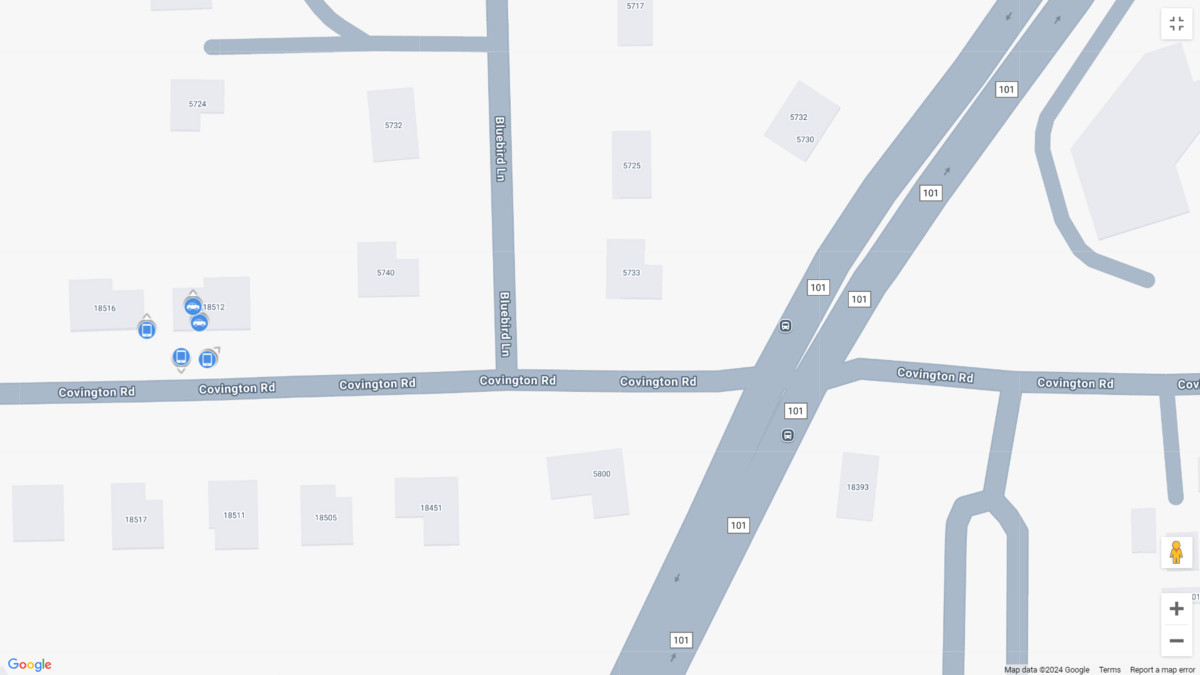
This valuable information can then be used to improve operations in so many different ways.
For instance, you can use it to optimize routes, especially if you pair your telematics system with route planning software.
In this case, telematics supplies all past routes and travel times, while the software calculates the shortest, most efficient path based on the final destination and this historical data.
Some systems even offer dynamic routing, meaning real-time adjustments based on changing traffic conditions.
As Simon Spriggs, Senior Sales & Partnerships Manager at FLS, a company offering solutions for field force and logistics scheduling, notes, manually optimizing routes is nearly impossible to do efficiently.
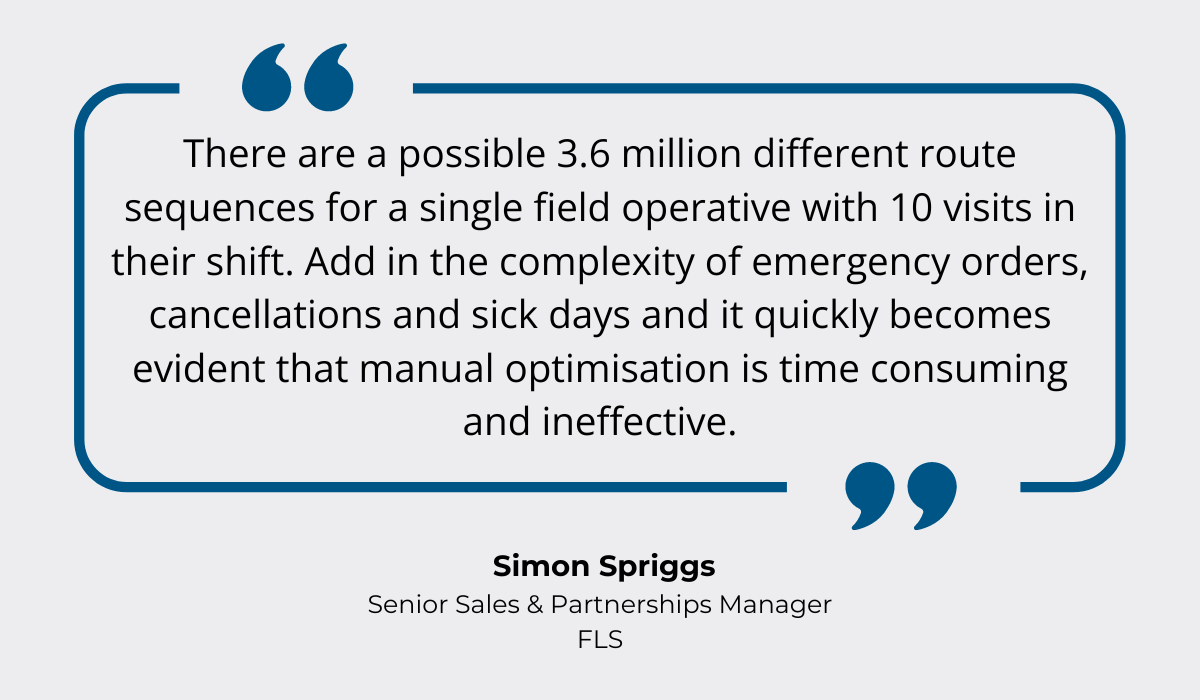
But, with the right technology, the whole process is completed in moments.
And the benefits are substantial.
Your fleet becomes so much faster, more efficient, and more reliable.
Plus, shorter travel times translate into reduced fuel consumption and CO2 emissions, making your operation more cost-effective and sustainable.
It’s a win on all possible fronts.
Another key application of location data is geofencing.
Geofencing allows you to set virtual boundaries around specific areas where your assets aren’t allowed to leave, just like in the example below.
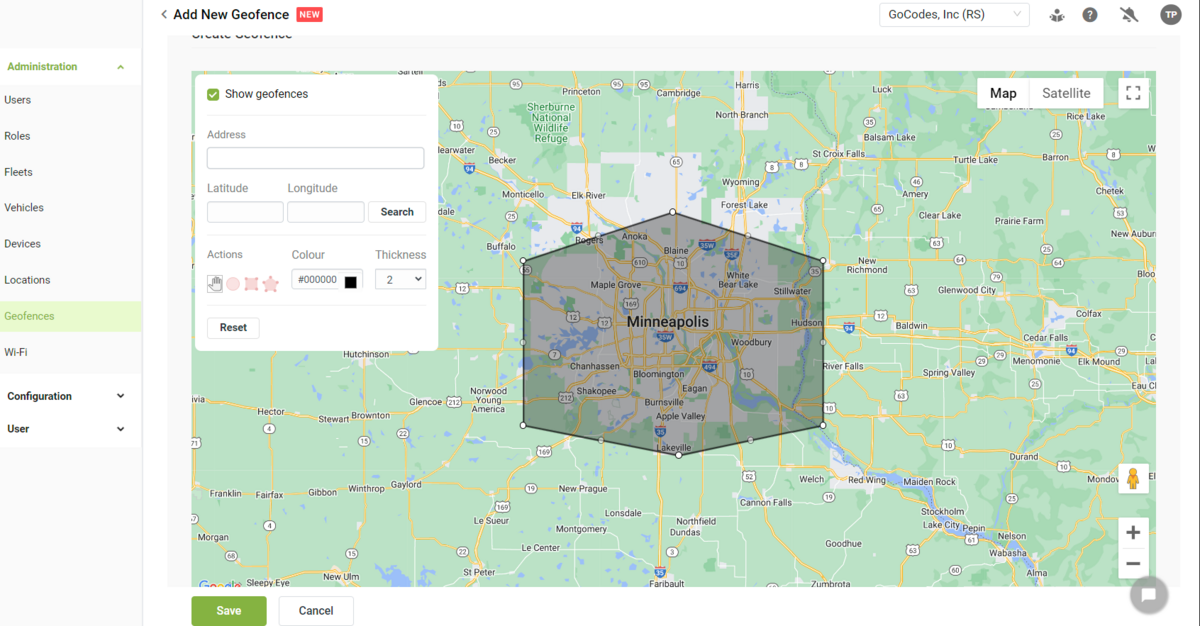
So, if a vehicle equipped with a GPS tracker does cross these boundaries, you’ll immediately receive an alert about the unauthorized movement.
This can be a potent theft prevention tool, allowing you to take action the moment something’s amiss.
However, geofencing does so much more than just prevent theft. It can also promote overall job site safety.
Ted Polzer, Director Of Product & Customer Support at CNH, an equipment, technology, and services company, gives an example.
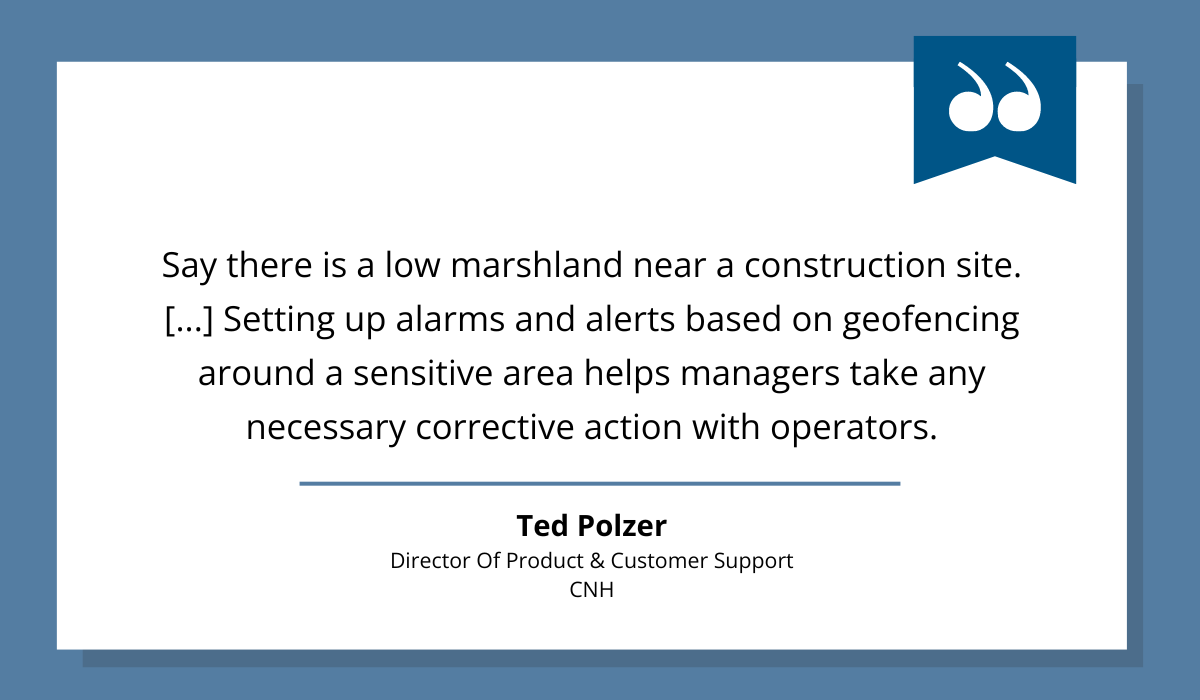
What a smart way to protect both your assets and workers!
All in all, location data has always been the foundation of successful asset management, helping contractors allocate their resources more efficiently and cost-effectively.
Just imagine what else it can achieve when integrated with the other data types we’re going to cover.
Vehicle Diagnostics Data
Today, it isn’t enough to only know where your equipment is. You also need information about its health, preferably in real-time and with as much detail as possible.
That’s exactly what diagnostic data is.
It encompasses various metrics that indicate how well a vehicle is doing, such as oil pressure, temperature, RPM, torque, and more.
Recognizing the importance of tracking asset conditions, our own asset management software, GoCodes Asset Tracking, offers several valuable diagnostic reports.
For example, the Engine Coolant Over Temperature report helps you identify machines or vehicles that have exceeded a particular coolant temperature.
As shown below, you can select which assets to include, define the time period for the analysis, and set the temperature threshold.
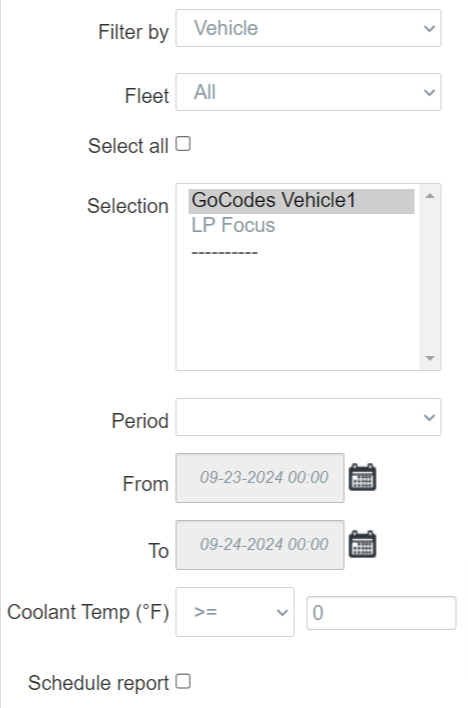
These reports can then be accessed immediately or scheduled to be sent at a specific frequency, to specific recipients, and in the desired format.
The same goes for our Engine Oil Over Temperature and Engine Low Oil Pressure reports.
They show you which machines have a too high oil temperature or abnormal oil pressure levels respectively.
GoCodes Asset Tracking also provides insights into diagnostic trouble codes (DTCs).

Generated by a vehicle’s onboard diagnostic (OBD) system, these codes tell you when something is wrong with a machine, making them essential for timely issue diagnosis and resolution.
Ultimately, all this data serves the same purpose: to keep you well-informed about your assets’ health at all times, which is absolutely crucial for any efficient maintenance strategy.
Patrick Brown, Director of Strategy at the American truck manufacturing company Mack Trucks, elaborates.
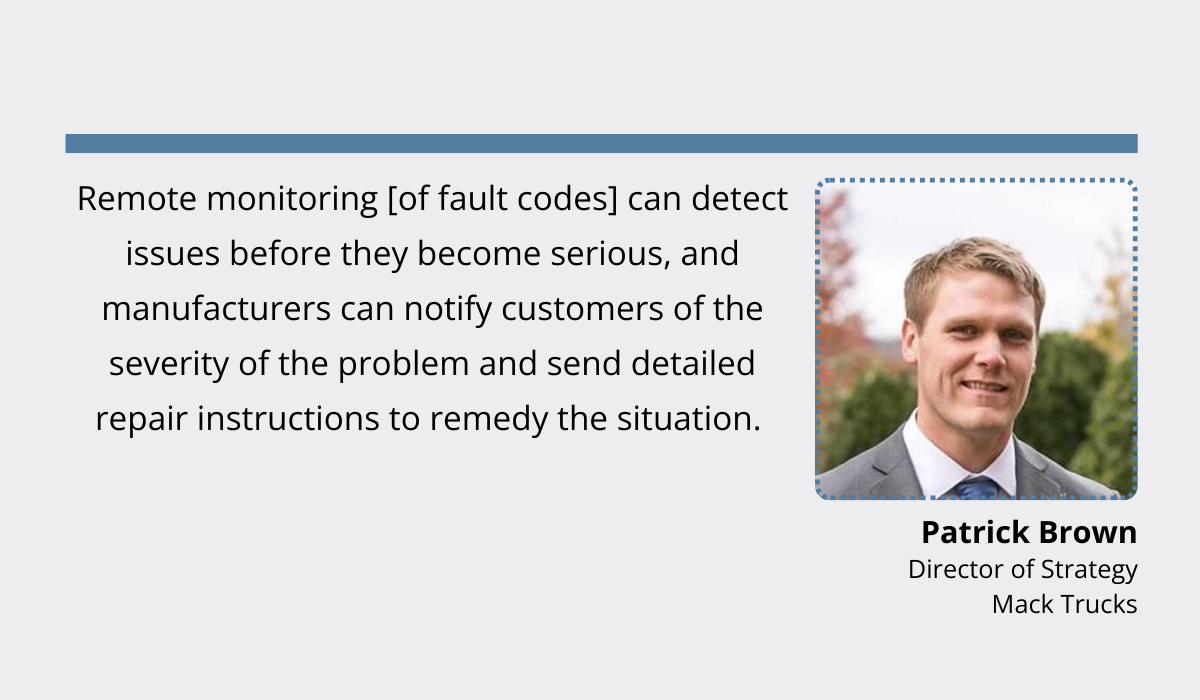
Put simply, thanks to diagnostic data, you can always schedule maintenance on time and easily determine the best course of action to fix issues before they snowball into more serious damage or failure.
This proactive approach to upkeep is vital for boosting both operational efficiency and the lifespan of your equipment.
Fuel Consumption Data
Fuel consumption data tells you how much fuel a machine or vehicle uses over a specific distance or time period.
Below, you’ll find an example fuel consumption report.
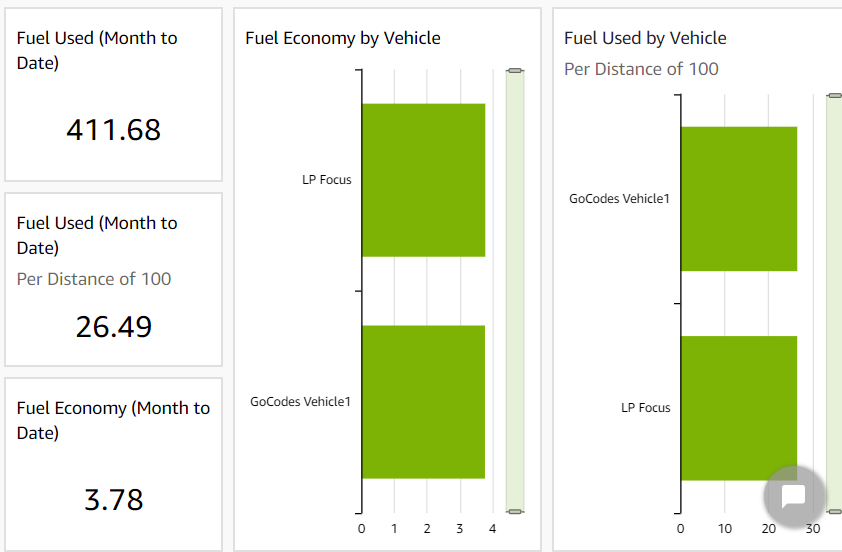
As you can see, these insights make it easy to identify trends or patterns, particularly those linked to excessive fuel use.
These findings are very valuable because they can be used to optimize the usage of this important resource and drive down operational expenses.
A recent Teletrac Navman survey already proved that fuel costs are a major concern for fleet operators, with 47% citing them as their top business challenge.
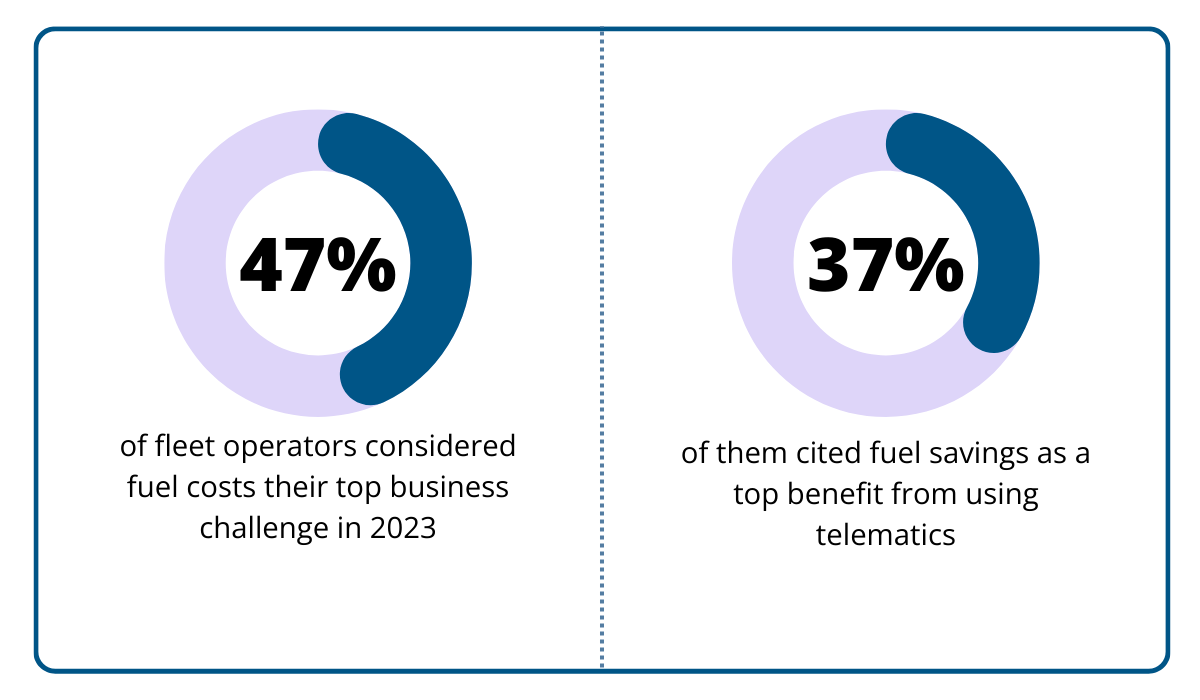
But there’s good news, too: 37% of survey respondents reported they were able to achieve fuel savings after implementing telematics.
This just goes to show that, with the right data, you can unlock some tangible benefits for your company.
Of course, your fuel optimization strategy will depend on the root cause of overconsumption.
For instance, if drivers tend to speed, training them to maintain more stable, lower speeds could be the solution.
If the routes they take are inefficient, then route optimization may be the answer.
Research from Cat Simulators shows that engine idling is another significant contributor to excessive fuel consumption.
As it turns out, idling can waste one gallon of fuel or more per hour.
So, over a year, a machine operating 2,000 hours, with 40% of that time spent idling (which they estimate is the norm), can waste over $2,300 in fuel.
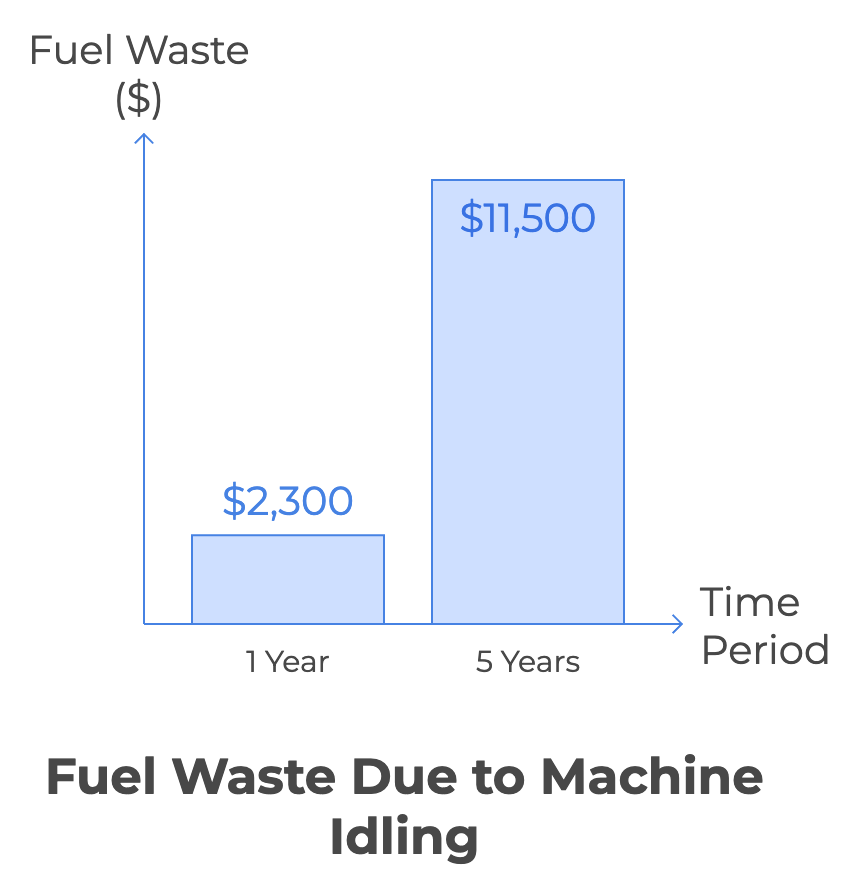
That’s more than $11,500 over the course of a five-year ownership.
Luckily, fuel data enables you to spot any fuel-related inefficiencies, making it an excellent starting point for your fuel use reduction journey.
This information becomes even more helpful when combined with other types of data, as these insights help in developing a truly effective fuel optimization strategy.
Driver behavior data is one of these types.
Driver Behavior Data
Driver behavior data is a surprisingly broad category.
It encompasses all sorts of insights, including:
- harsh braking or cornering
- seatbelt usage
- accelerations
- idling time
- speeding
Some more advanced systems, especially when paired with in-vehicle cameras, can even detect distracted driving or fatigue.
And the applications of this data are just as diverse as the data itself.
The most obvious use case is monitoring and correcting driver behavior to ensure safer operations.
In 2023, Lytx analyzed 40 billion miles of driving data, uncovering the top ten risky practices contributing to road accidents in the U.S.
Here’s what they found:
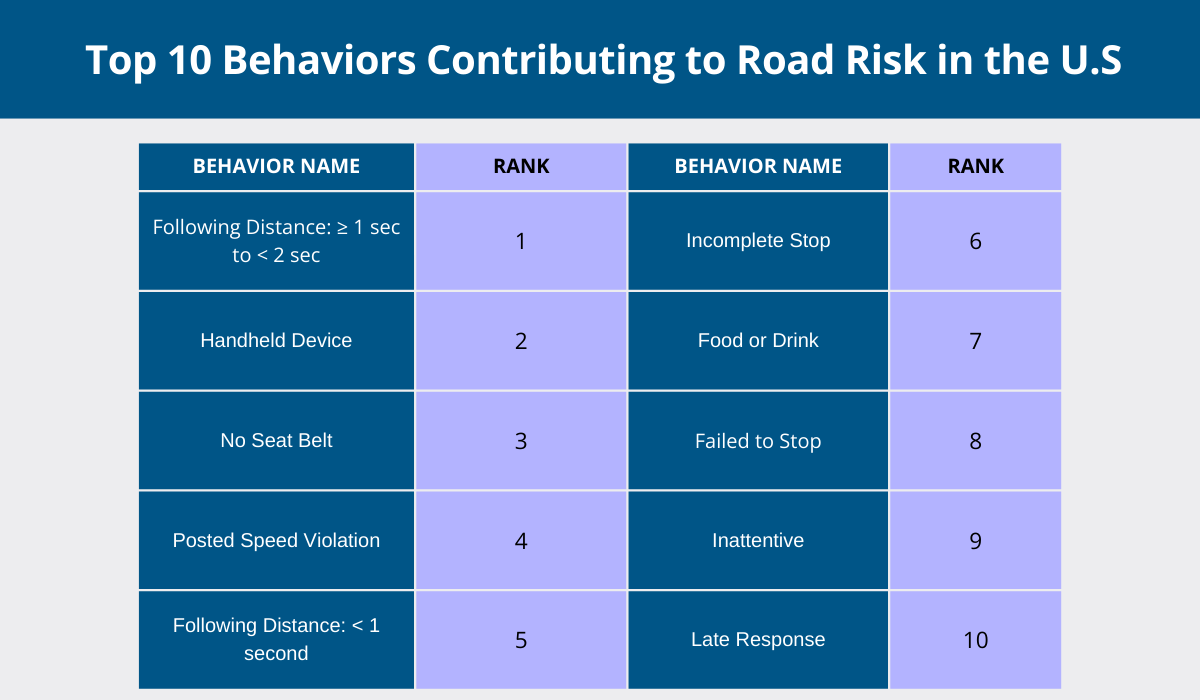
Telematics can easily capture all of these behaviors and help you address them.
This can be either in real-time, by sending alerts directly to drivers engaging in unsafe practices, or by acting as a framework for tailored coaching after reviewing a driver’s long-term performance.
Either way, you get safer, more responsible drivers and operators.
Plus, your vehicles benefit from safer driving, too, as they’re exposed to less wear and tear.
But it’s not all just about better driving.
This information can also serve as proof in insurance claims or legal disputes involving traffic accidents.
Considering the rising costs associated with such incidents, being able to prove your driver wasn’t at fault can really protect your profitability.
Greg Stefan, VP of Risk Control at Arch Insurance Group, agrees, explaining that accident-related expenses have drastically increased over the last 15 years.
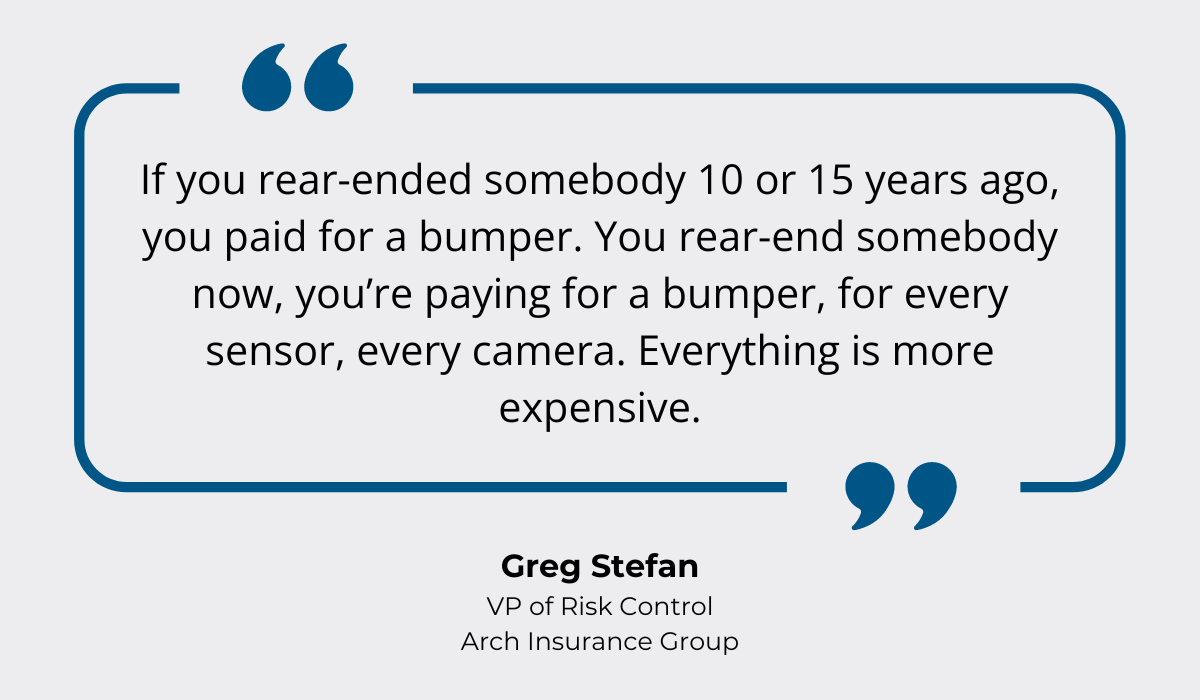
This makes having objective data on hand more important than ever.
Telematics provides just that, offering the ability to recreate the sequence of events in any incident, empowering you to back up your claims or challenge false accusations.
Bottom line?
Driver behavior data is an incredibly valuable asset, helping you correct unsafe driving and serving as reliable evidence in legal situations.
As such, it’s a very efficient tool for protecting your drivers, your assets, and your business as a whole.
Safety and Compliance Data
This is another broad data category that covers a wide range of insights, some of which overlap with previously mentioned types.
These insights play a major role in ensuring that your assets and drivers comply with all relevant rules and regulations, helping you avoid fines, reputational damage, and safety issues.
For instance, telematics systems integrated with ELDs can automatically monitor drivers’ work and rest hours and, therefore, help you stay compliant with Hours of Service (HOS) regulations.
As depicted in the example below, these systems show how much time each driver has driven and how many hours they have left, with some even sending alerts if a driver is nearing a violation.
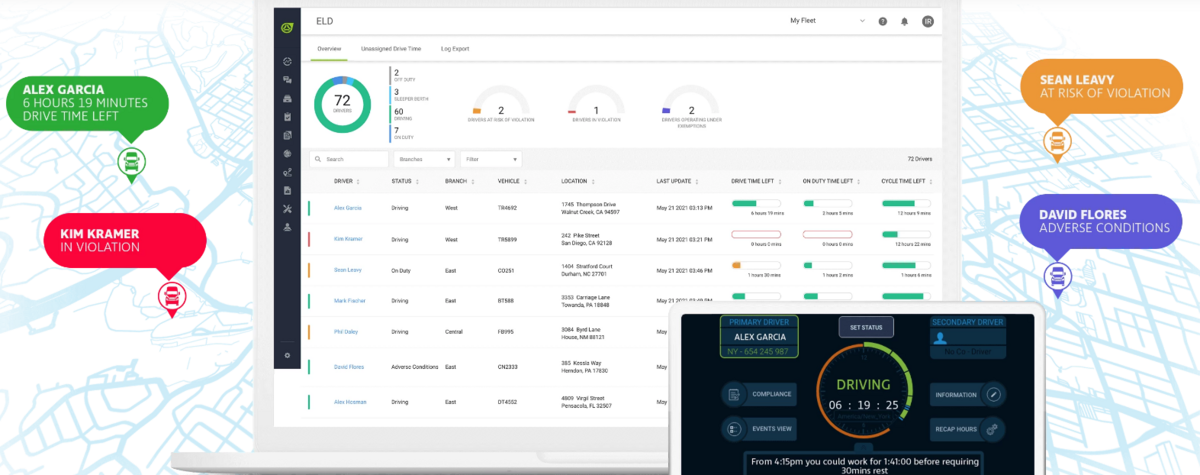
This makes it so much easier to plan jobs or breaks in advance.
Moreover, telematics can log all inspection reports, giving you a clear record of when each asset was last serviced and what issues were identified.
This helps you address equipment problems before a roadside inspector does.
After all, pre- and post-trip inspections—or the lack thereof—are common areas of noncompliance.
TJ Thomas, Director of Marketing & Customer Solutions at Bendix Commercial Vehicle Systems, a developer and supplier of active safe technologies, agrees.
Especially when it comes to the inspections of critical components like brakes:
“So many violations are preventable through proper maintenance practices and regular equipment examination. You simply can’t overstate the importance of keeping up with maintenance and examination of the wheel-ends and braking system, because so many aspects of safe vehicle operation are directly impacted by what goes on in those areas.”
But, with telematics and maintenance tracking, you can ensure your vehicle stays roadworthy and provide inspectors with accurate, up-to-date service reports.
Fuel consumption is another aspect of compliance that telematics helps tackle.
Under the International Fuel Tax Agreement (IFTA), which applies to 48 U.S. states (excluding Alaska and Hawaii) and 10 Canadian provinces, drivers must record:
- miles driven
- fuel purchased
- purchase locations
and submit this data quarterly to the IFTA office.
Based on the number of miles driven in each jurisdiction, IFTA then distributes fuel taxes accordingly.
With telematics, IFTA reporting is a breeze, enabling you to always send in accurate, complete, and fresh data.
No more manual tracking, no more human error.
Essentially, telematics puts you in control of every aspect of compliance, from driver behavior to vehicle health.
It enables you to spot potential issues early, fix them, and keep your entire operations safe, efficient, and fully compliant—all through a single system.
Maintenance Scheduling Data
Telematics provides all the data you could ever need for effective maintenance scheduling.
This includes real-time diagnostic and driver behavior data, as well as complete upkeep histories and statuses of active tasks.
You can see who’s responsible for each task, their progress, costs, and the spare parts involved, all at a glance.
Some systems even send reminders for scheduled service or automatically trigger maintenance events after a failed inspection.
As Ryan Driscoll, VP of Marketing at fleet maintenance software & consulting services company RTA, notes, telematics has made maintenance planning and scheduling so much more data-driven.
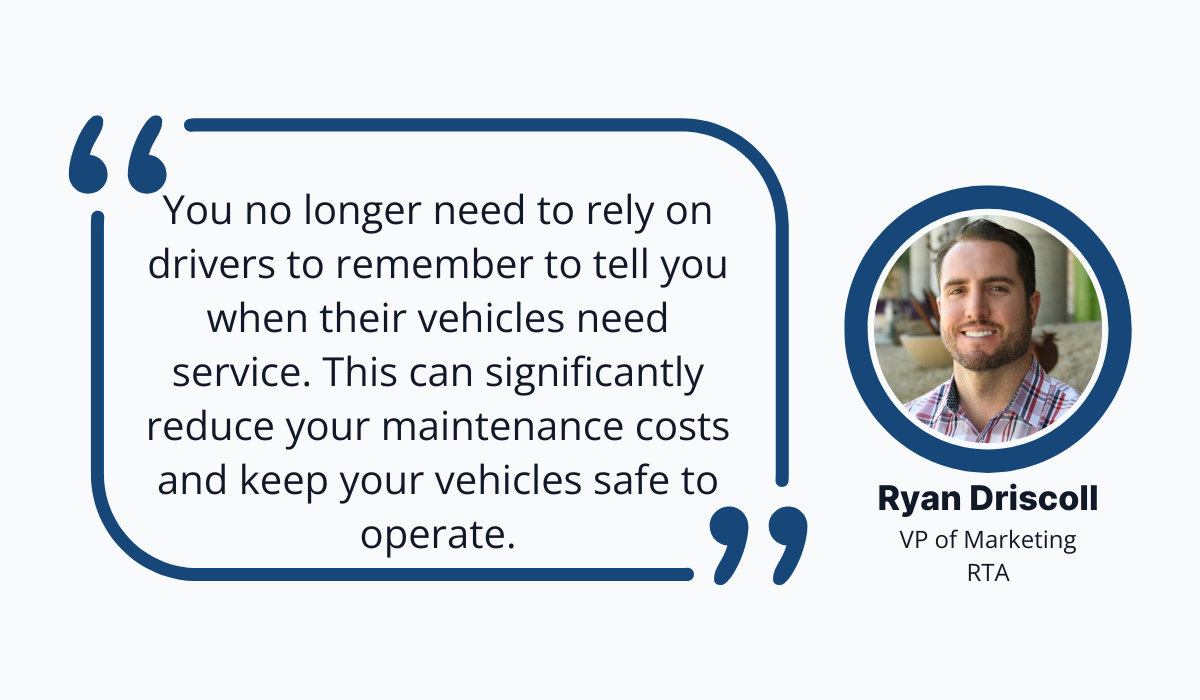
Thanks to this technology, you’re always in the loop about the condition of your assets, empowering you to take a proactive approach to their upkeep.
So, instead of waiting for problems to arise, you can strategically schedule repairs and inspections to catch issues early, preventing them from becoming threats to overall safety and efficiency.
Take E.K. Services, Inc., for example.
This full-service utility, excavating, and paving contractor manages more than 700 pieces of equipment across central Pennsylvania.
Now, that’s a lot of machines to keep track of.
Their CIO, Shawn Beinhower, recalls how, before adopting telematics and maintenance software, they struggled with inefficient upkeep and costly downtime:
“When a piece goes down, there’s downtime in just figuring out what is wrong, and then more downtime on the repair. If it’s an excavator on a pipe crew, then your whole crew’s just sitting there waiting to be fixed. And if it can’t be fixed, then, you incur the cost of getting a rental piece in, as well as the lost time waiting for it to be delivered.”
But now, their maintenance team is so much more efficient.
Telematics tracks asset and component conditions or usage and software displays that information to technicians so that they can plan repairs with more accuracy.
Even location data has a role to play in scheduling, says Beinhower:
“When our field mechanic is preparing to go out for a job, he can not only see what other pieces of equipment are on the jobsite, but also check out equipment on other sites within the area. This really helps him plan his day with the greatest efficiency.
He can load up all the parts he needs and take care of maybe five issues, instead of just one and having to be sent back out to the field.”
With telematics, maintenance planning is on an entirely different level, no doubt about it.
Each asset and component gets the care it needs to maximize performance and reliability, without the risk of over-maintenance or unnecessary repair costs.
Conclusion
Isn’t it amazing how many different insights telematics can provide?
From tracking fuel consumption for each machine to knowing whether drivers are eating while driving, you can learn so much thanks to this amazing technology.
However, none of this matters unless you turn the data into actionable insights.
A key piece of advice here would be to avoid tracking everything at once.
Yes, it can be tempting but it could easily overwhelm you as well.
Instead, zero in on what really matters to you.
If your goal is to cut fuel costs, for example, focus on metrics like fuel usage, idling time, and speeding, rather than getting sidetracked by less relevant data.
It’s only when you set clear and specific goals that telematics data becomes a powerful tool, guiding your decisions and driving real results.