It’s tempting for project managers and decision-makers to rely on old construction equipment without investing in its long-term health.
Putting off major purchases or avoiding preventive maintenance often seems like the best way to cut corners on a project with a thin profit edge, especially while the industry is still feeling the impacts of the COVID-19 pandemic.
However, avoiding repairs or hanging on to antiquated equipment is rarely cost-effective in the long term.
Employee productivity suffers when site teams struggle to do their difficult and dangerous jobs with slow, outdated, or damaged items.
Using old construction equipment can result in unexpected equipment failure, reduced worker safety, and increased repair costs.
It can reduce the efficiency of your fleet, and cause downtime—which is often more expensive and frustrating than simply investing in updated gear.
In this article...
Unexpected Equipment Failure
In construction, the only thing that’s more frustrating than knowing that a struggling piece of machinery could break down at any moment is suffering an extended shutdown that takes place without warning.
It means a pause in work while the problem is diagnosed, waiting for a replacement, spending money to bring in a rental to complete the job, or wasting time waiting for expensive repairs.
That’s all without taking into account the schedule slip inherent in equipment failure. The loss of one piece of critical equipment might endanger the timeline of an entire project.
Moreover, sudden equipment failure can even result in damage to recently finished construction.
One way to avoid this nightmare is to conduct regular inspections and cleanings.
Preventive maintenance and employee training are highly recommended, as are regular reviews of maintenance safety.
The best way to stick to regular preventive maintenance is to rely upon a robust asset tracking system.
Not only does GoCodes Asset Tracking asset tracking provide pinpoint GPS information for expensive equipment, but it also stores vital data such as maintenance calendars, operator manuals, and warranty information.
Asset tracking systems can also provide reminders for preventive maintenance and inspections.
Sometimes, the best solution to unexpected equipment failure is to buy new assets, as this visual aid shows:
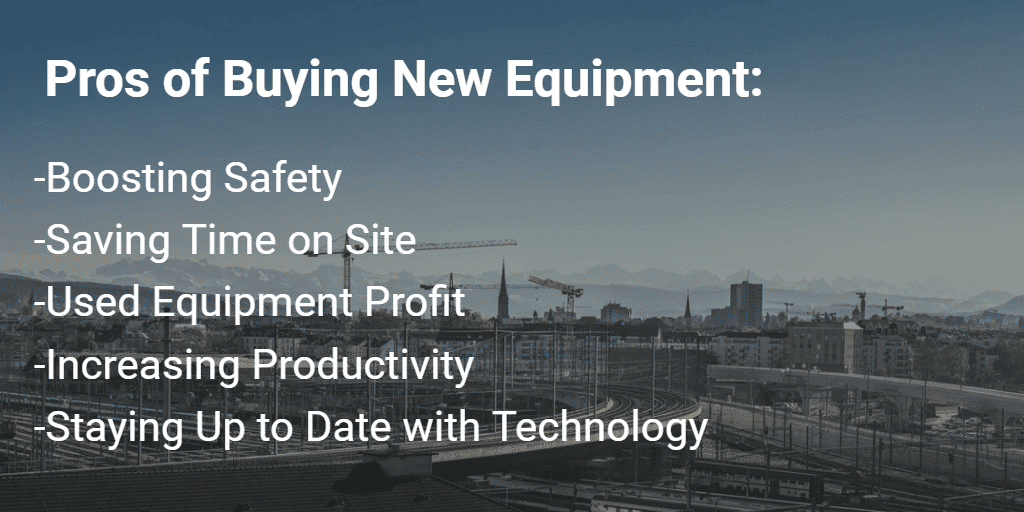
However, taking good care of quality, well-built items can help avoid this problem altogether.
Dedicated preventive maintenance is key to knowing where your equipment is in its life cycle.
Understanding when it’s time to repair and when there’s no other choice but to replace the item can give you confidence that you are making educated decisions about your assets.
Reduced Worker Safety
Jobsite safety is another compelling reason to avoid over-reliance on old equipment.
Project managers are responsible for providing a reasonable risk assessment on a site.
When employees handle glitchy, unreliable, or unserviced equipment, the likelihood of an accident rises.
Especially where safety is concerned, contractors should pay special attention to not just heavy machinery, but also handheld tools and PPE (personal protection equipment.)
Inoperable, frayed, or out-of-code items that are haphazardly repaired all contribute to a dangerous workplace.
Worker safety takes different forms depending on the site, job, and time of year, but each subset of construction tasks presents different dangers.
For example, imagine asking a crew of electricians to work with unsafe equipment in addition to these hazards:
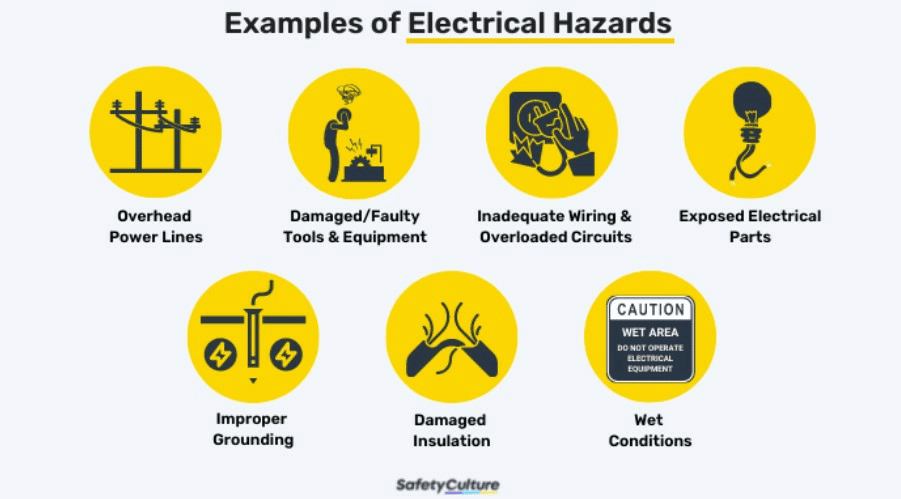
The Bureau of Labor Statistics reports that in 2019 alone, construction workers suffered nearly 80,000 injuries—and those were just the ones that were reported.
Many adjustments can contribute to lowering these numbers, such as committing to keeping worksite items in good repair.
New equipment nearly always contains more and better safety features than previous models, and your team deserves every possible advantage in such a dangerous profession.
Increased Repair Costs
No piece of equipment is infallible, so asset repair should appear in the yearly budget of every responsible construction company.
However, continuing to use old construction equipment adds to even baseline repair costs. This graphic shows how repair costs can rapidly rise over time:
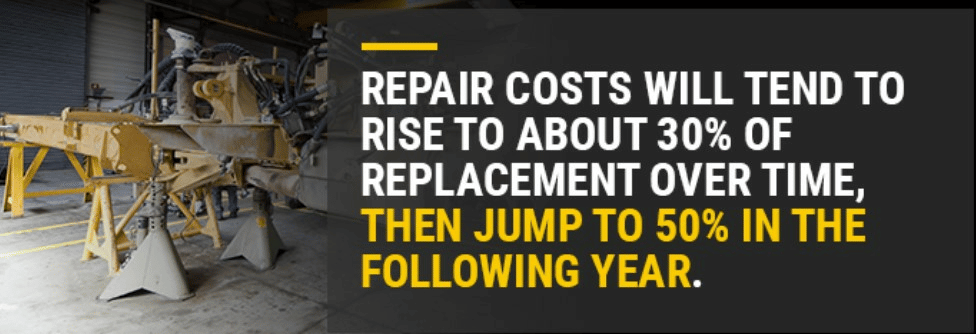
Heavy equipment maintenance mistakes include regularly pushing machinery past stated limits, as well as failing to check assets for minor damage or lack of cleanliness.
Setting a company culture of ignoring repairs, and constantly leaving them for the next shift, is a fast route to maxing out repair budgets.
Older equipment might also demand parts that are difficult to find, especially in a market suffering from a slow and unreliable supply chain.
As a result, such parts usually cost more than those readily available, and you might find a dearth of support from the manufacturer.
Expired warranties can also be another reason for increased repair costs, because they mean full economic responsibility for expensive repairs.
Worse, when a piece of equipment begins to break down, it is ever more difficult to find technicians with the knowledge and experience to diagnose problems or effect repairs.
And their expertise also comes at a price.
Regular equipment maintenance can offset some of the increased repair costs that come from overusing old equipment.
So make sure you take care of your tools and machinery and thus reduce the need for costly repairs.
Reduced Equipment Efficiency
Making the most of every piece of equipment is an important aspect of overall efficiency. A workplace outfitted with efficient machines stands a better chance of increasing productivity.
As the most successful contractors and project managers know, efficiency is essential for staying within budget.
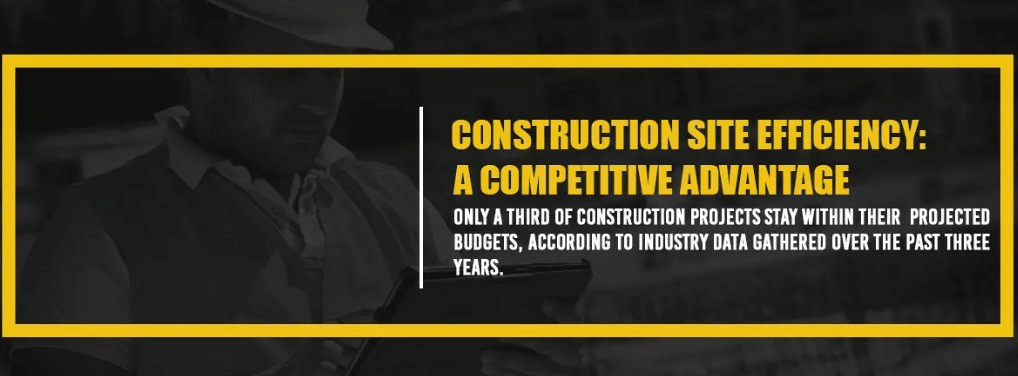
When equipment efficiency is reduced, tasks take longer and deadlines are more difficult to meet.
In addition, the usefulness of heavy construction equipment is often measured in hours of operation, miles driven, or cycles completed.
An older asset might not meet efficiency goals due to lagging behind its newer counterparts.
As this is a correctable variable in your company’s ability to hit its milestones, it doesn’t make sense to unnecessarily make it more difficult for your whole team to complete their tasks.
If you are looking to scale up your business, it’s important to focus on maintaining and increasing project capacity.
That’s impossible if antiquated equipment is taking up to an hour more than a new machine to move a project along. Those hours quickly add up.
So think about budgeting for new equipment, which will pay off its initial investment by completing the work quickly and within deadlines.
Longer Downtimes
The price tag on new construction equipment can often give you pause. However, this outlay can quickly result in larger and more reliable economic returns.
The irritating and expensive breakdowns of older equipment not only annoys your crew, it also makes for unhappy clients who are usually impatient with delays.
Long downtimes from extended breakdowns can take place even with the best preventive maintenance.
A recent study of 101 new businesses revealed that of those that failed, 29% simply ran out of operating capital or cash, which is dangerously close when downtime seems to stretch on forever.
Downtime can cost thousands of dollars per day, which can prove deadly to a company without a lot of reserves.
These factors aren’t the only components in the cost of completing jobs even for small or medium companies. This slide lists overall construction costs in addition to long downtimes:
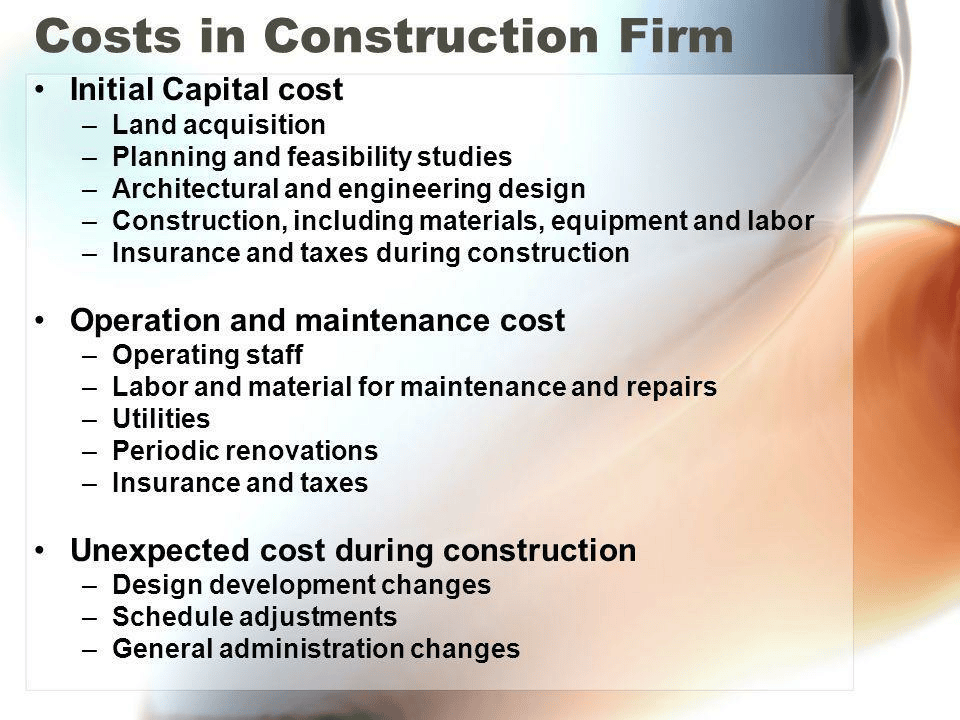
Adding unacceptably long standstills on a tight schedule increases the cost for each of these items.
Schedule adjustments lead to higher utility bills, increased security costs, and even penalty payments to clients.
Decreased Worker Productivity
Unsurprisingly, workers forced to grapple with unsafe equipment do not feel valued or taken seriously as professionals.
Instead, when companies expect them to produce excellent work with faulty tools, they may feel as if they are set up to fail.
Frustration among employees leads to churn, which is expensive in its own right.
Such a situation is demoralizing, and an unhappy, unmotivated team isn’t a good starting point for reliable work and happy clients.
Outfitting your skilled and hardworking team members with the best of what they need to complete their jobs not only encourages them to become more productive, it can help your company lure top talent to your employee pool in a time of staff shortage.
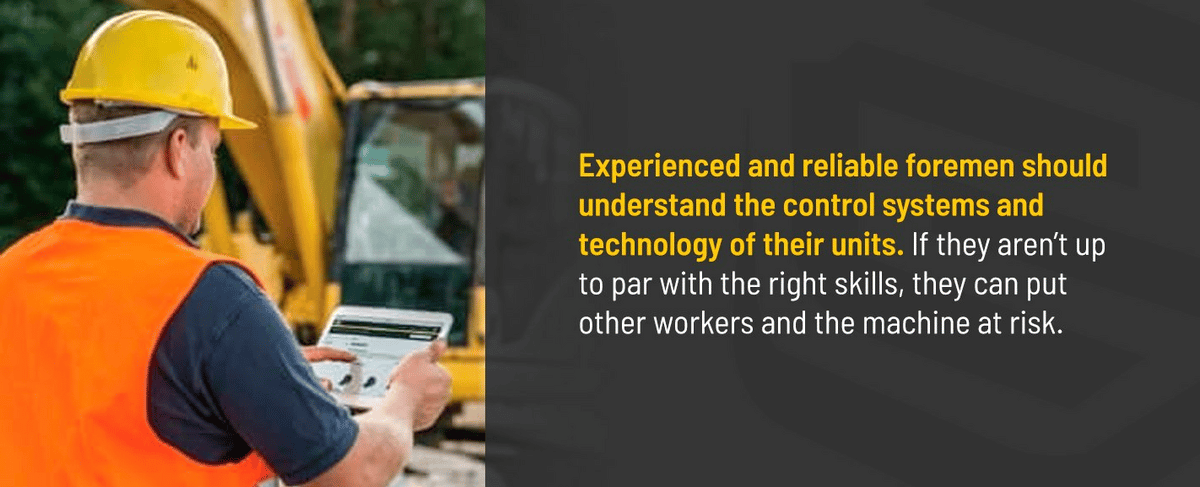
Consider the argument in this graphic. Newer equipment can also provide exciting and challenging new capabilities.
That means, foremen and workers alike can help increase productivity by staying up to date on control systems and best practices.
These opportunities to learn new skills can also help to contribute to a stronger site safety culture.
Conclusion
Construction businesses, foremen, decision-makers, and project managers have a great deal to worry them.
The pending headache of using old construction equipment unnecessarily adds to this stress.
Old construction equipment can contribute to unexpected equipment failure.
It unnecessarily endangers employees, and can contribute to company costs due to lawsuits, fines, and the expense of hiring temporary replacements.
Moreover, failure to keep equipment updated can mean longer and less predictable downtimes, not to mention decreased worker productivity.
In short, while it might seem economical to maintain old equipment, increased repair costs and reduced equipment efficiency often turn out to be a bigger drain on your resources than buying or renting new pieces.