Key Takeaways:
- Using real-time monitoring reduces emergency repair costs and downtime.
- Properly storing equipment prevents premature wear, system failures, and costly breakdowns.
- Well-trained operators are less likely to misuse equipment and more likely to detect early warning signs.
Have you ever looked at your monthly equipment maintenance bill and thought, “We are bleeding money”?
Yes, equipment maintenance is essential in construction, but so is keeping costs under control.
Rising fuel prices, unplanned breakdowns, and rushed fixes can quickly eat away at your margins. Luckily, this is avoidable.
In this article, we’ll share six practical ways to reduce maintenance costs without cutting corners on safety or performance.
Let’s dive right in!
In this article...
Track Maintenance History
Tracking your equipment’s maintenance history allows you to remain proactive and alert about your equipment’s performance.
Without centralized records, you risk overspending, repeated failures, and loss of control over your assets.
But how do you get started with this?
By keeping a detailed and accessible log of all maintenance activities, including routine services, part replacements, inspections, and breakdowns.
When you log specifics like fluid top-ups, hydraulic oil changes, and emergency repairs, you gain a clear view of each machine’s wear-and-tear lifecycle.
This history helps you spot early warning signs, identify repeat issues, and understand when a machine is starting to cost more to maintain than it’s worth.
Jay Voraliya, a Quality Assurance Engineer, explains the importance of having a maintenance history card.
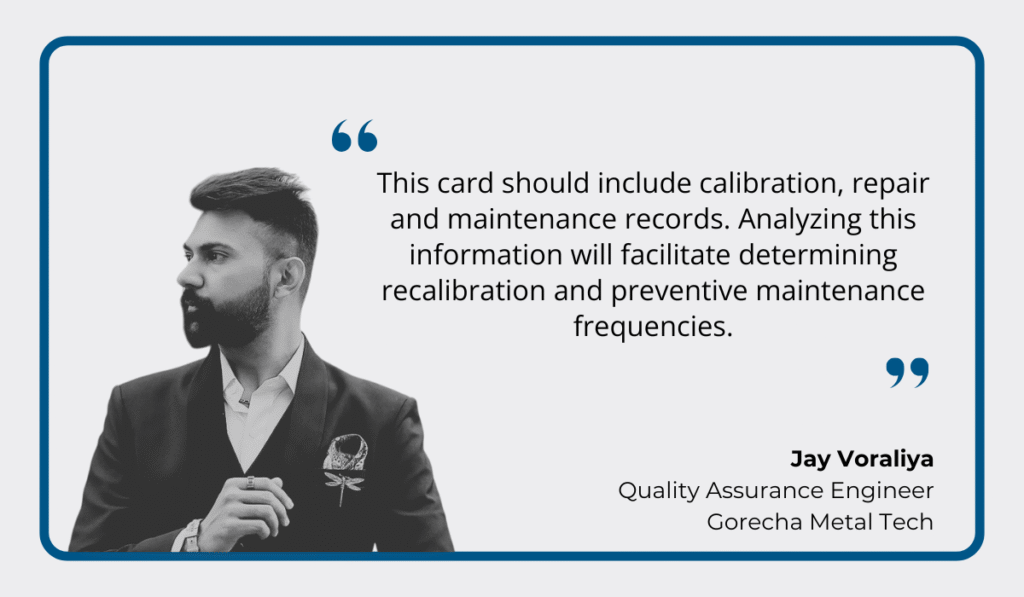
Illustration: GoCodes / Quote: LinkedIn
Let’s say that your records reveal that, after every 700 operating hours, your excavators begin showing hydraulic system issues.
With a proper maintenance log, this pattern becomes obvious.
This enables you to then plan a repair or part replacement ahead of time, making your maintenance preventive, rather than reactive.
By doing this, you can avoid costly emergency repairs, minimize downtime, and ultimately reduce your overall maintenance costs.
In construction, your maintenance history acts like a GPS: guiding decisions and preventing expensive detours. It’s your blueprint for fewer surprises and smarter decisions.
Implement Proactive Maintenance
When it comes to equipment care, waiting for something to break is the costliest approach.
That’s where proactive maintenance comes in.
Unlike reactive maintenance, which kicks in only after equipment fails, proactive maintenance is built around regular inspections, timely lubrication, and early parts replacement.
The goal is simple: catch the small hiccups before they snowball into downtime or major, expensive repairs.
According to a survey by Limble CMMS, 75% of manufacturing maintenance professionals implement proactive maintenance to optimize their aging infrastructure.
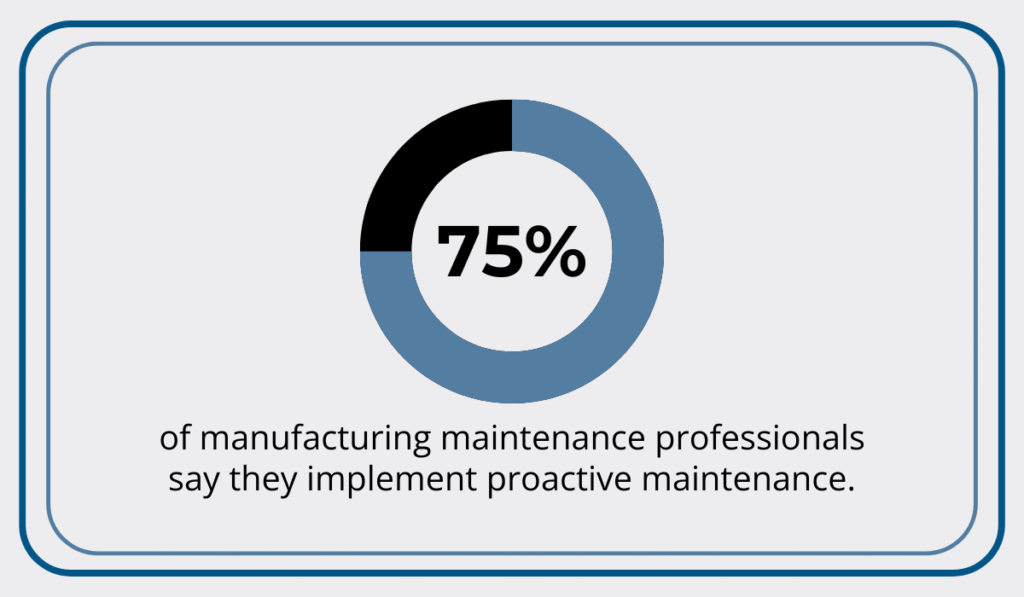
Illustration: GoCodes / Data: Limble
The same principles can be applied in construction, too.
Scheduling your maintenance tasks based on Original Equipment Manufacturer (OEM) guidelines is a smart strategy in this regard.
Sticking to them helps you avoid both over-maintenance, which drives up unnecessary costs, and under-maintenance, which leads to breakdowns that drive up unplanned expenses.
And the more consistently these routines are followed, the easier it is to tailor your program over time.
So, keep it all documented and refer back regularly, using your OEM as a benchmark and your records as proof of progress.
You can think of it this way: it’s cheaper to replace a worn belt today than to buy a new machine tomorrow.
Need an example?
Say your loaders consistently show signs of overheating.
A proactive strategy might include scheduling cooling system flushes and radiator inspections ahead of peak season.
This small shift would likely prevent mid-project shutdowns and keep crews moving during your busiest times of the year.
And if you want to take it a step further, choose predictive maintenance.
It uses sensor data, analytics, and equipment diagnostics to forecast exactly when a component is likely to fail.
Below is a concise breakdown of the differences between preventive and predictive maintenance.
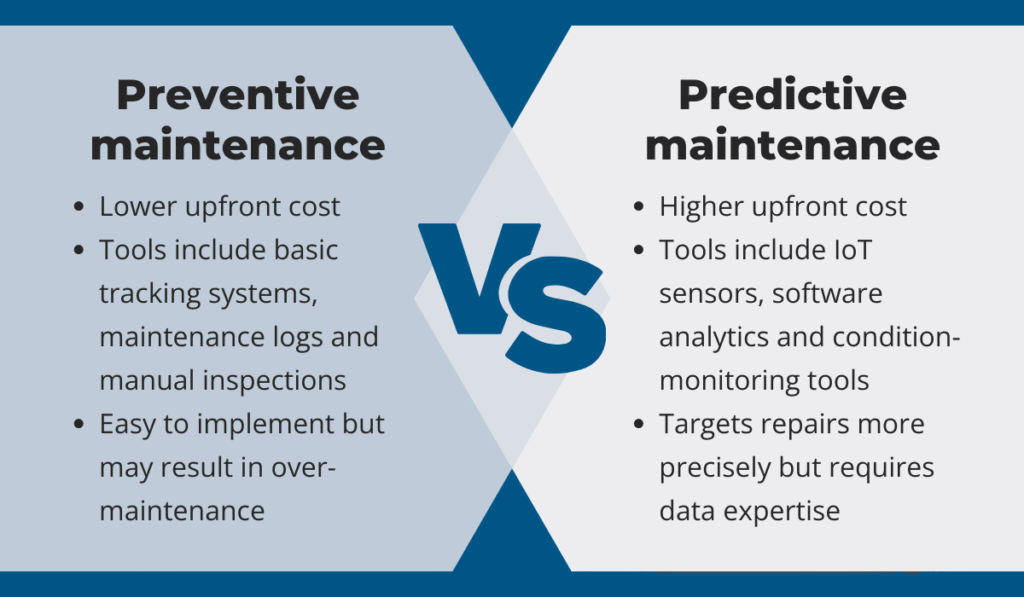
Source: GoCodes
Even though it comes with a learning curve and requires an investment upfront, predictive maintenance can be worth consideration.
This is especially the case if your goal is to decrease costs and enhance uptime, research shows.
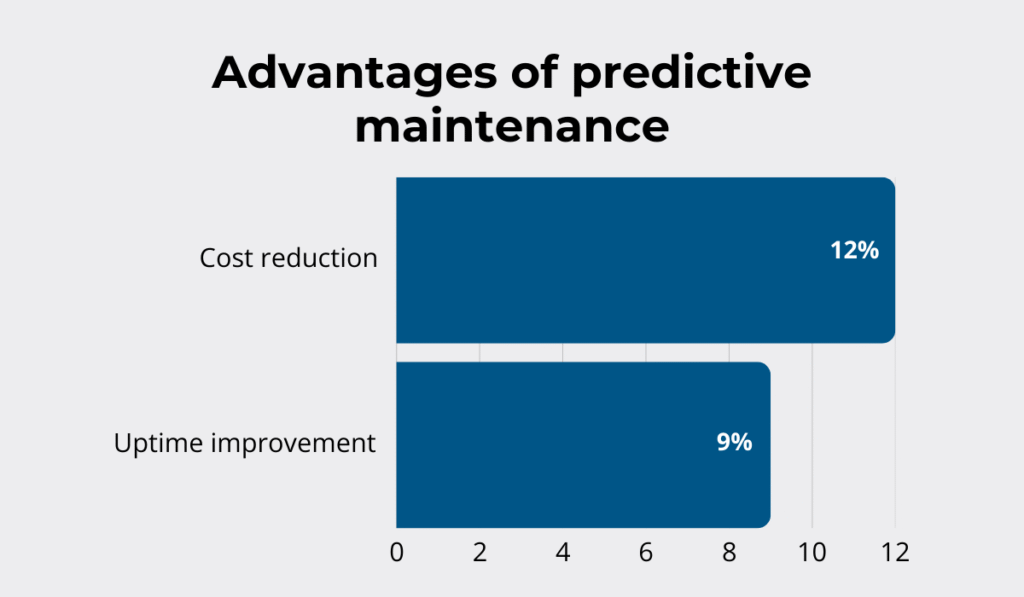
Illustration: GoCodes / Data: PwC and Mainnovation
In a nutshell, proactive maintenance helps you stop firefighting and start forecasting.
No matter which approach to proactive maintenance you opt for, one thing is for certain:
By addressing issues before they escalate, you can significantly reduce emergency repair costs and extend equipment life.
They also help optimize labor and parts usage, so you’re only spending where it truly matters.
Over time, all of this translates into more predictable budgets, fewer surprises, and healthier profit margins.
Leverage Real-Time Equipment Monitoring
The next effective method of reducing equipment maintenance costs is implementing real-time monitoring.
Teams can now track machine performance live, minute by minute, thanks to telematics and asset tracking solutions.
This allows equipment managers to gain instant visibility into equipment runtime, idle time, location, and even how machines are being operated.
That’s exactly the type of control you want—and you’re not alone.
The growing popularity of equipment monitoring is confirmed by a report by Global Market Insights.
It shows that the construction equipment tracking market was valued at $1.7 billion in 2023 and is expected to continue growing at a CAGR of 9.8% between 2024 and 2032.
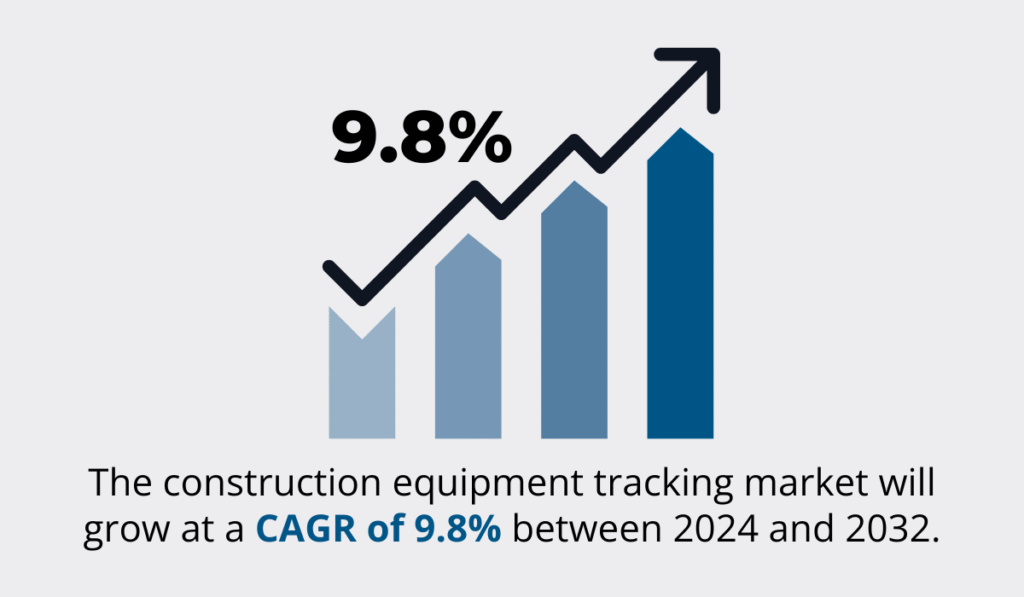
Illustration: GoCodes / Data: Global Market Insights
Imagine if one of your bulldozers sits idle for 2 hours every shift with the engine running. Without tracking, this might go unnoticed.
But with real-time monitoring, you can spot the pattern, retrain the operator, and cut the idle time by a large margin.
Or think of a skid steer showing early signs of engine strain in the form of vibrations and abnormal temperature.
With a real-time monitoring system, you don’t find out after it breaks down. You get ahead of it.
This enables you to schedule service proactively, avoid unplanned downtime, keep your replacement asset value (RAV) high, and save costs.
And the best part is, you don’t have to do any of this manually.
GoCodes’ real-time tracking capabilities can be a great help in this regard.
You can track equipment across job sites, monitor how long it’s been running, and see where it’s being used, all in one place.
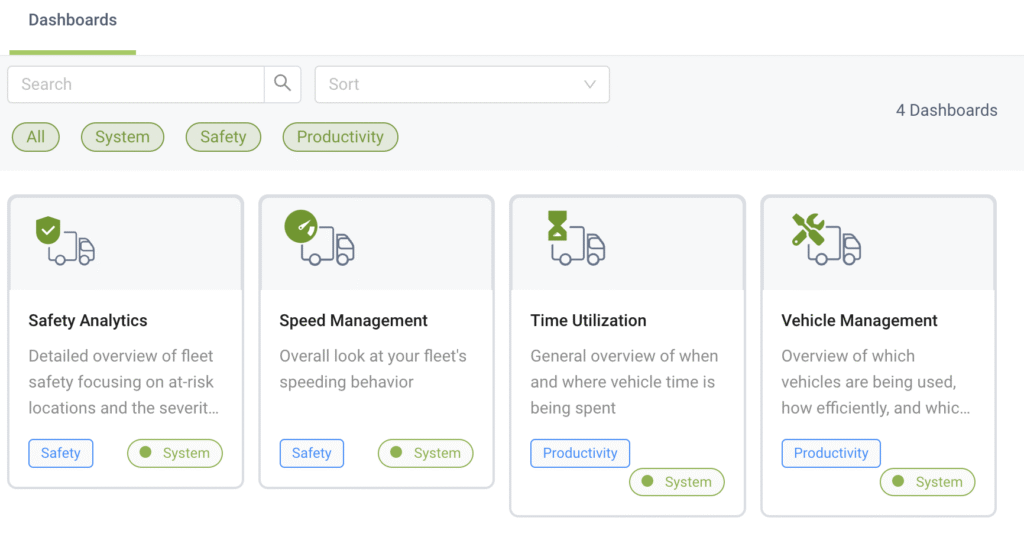
Source: GoCodes
And if the equipment gets moved off-site or isn’t where it should be, you’ll know thanks to the geofencing features GoCodes provides.
Any time an asset enters or exits the predefined area, you’ll receive an instant alert, helping you monitor movement, prevent unauthorized use, and reduce the risk of loss.
GoCodes also lets you track key performance data like geofence overtime, undertime, and speed, giving you deeper visibility into how equipment is actually being used on-site.
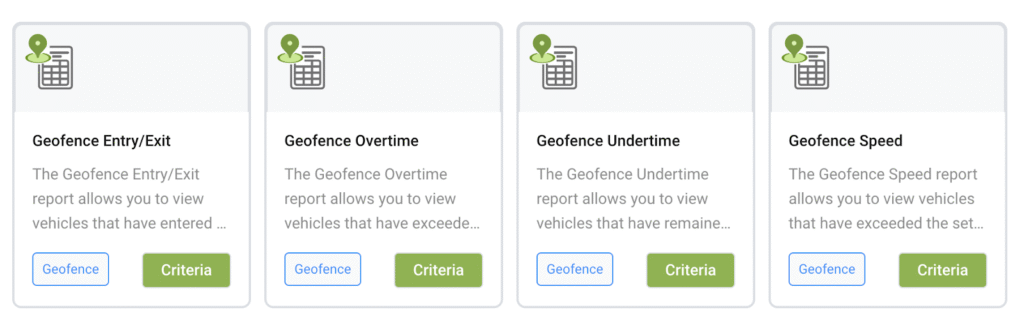
Source: GoCodes
By identifying equipment misuse, overuse, or idle time through data provided by real-time monitoring solutions, you can prevent unnecessary wear and tear.
Ultimately, all of this reduces maintenance costs and extends equipment life.
Use High-Quality Replacement Parts
Cutting corners on parts might save you money now, but cheap replacement components often fail down the road.
So, choosing OEM or certified high-quality replacements is a smarter way to drive down maintenance costs in the long run.
When you install a generic part, you’re likely putting the entire asset in jeopardy.
Poor-quality parts often lead to compatibility issues, premature wear, and in some cases, secondary damage to more expensive systems.
Worse yet, they can compromise safety on the construction site.
The construction industry has a high fatal work injury rate of 9.6 deaths per 100,000 workers.
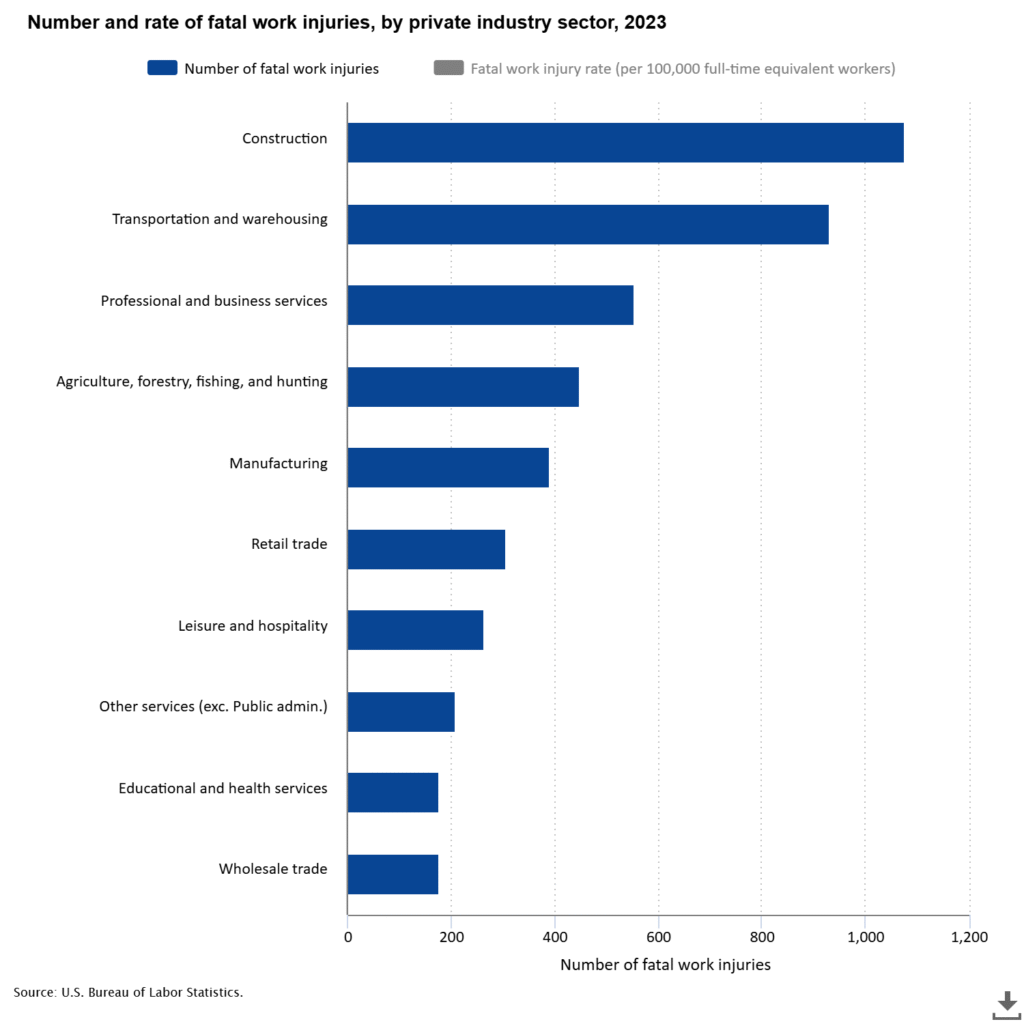
Source: U.S. Bureau of Labor Statistics
This highlights the use of high-quality parts to maintain equipment safety and thus reduce accidents caused by machine failure.
Yes, high-quality parts might cost more upfront. But they’re engineered for performance, built to last, and backed by the manufacturer’s testing.
That kind of assurance pays off, especially when uptime is everything. Would you rather replace a $100 OEM belt once a year or a $40 generic one three times?
As the construction industry becomes more aware of the importance of high-quality parts for reliability and cost control, demand for these parts is rising.
This shift is reflected in the projected growth of the Aftermarket Parts market: from $80 billion in 2024 to $114 billion by 2032.
Illustration: GoCodes / Data: Credence Research
Suppose you replace the fuel filter on a high-value excavator with a non-OEM version to save money. The low-quality filter doesn’t fit properly.
Over time, it allows debris into the fuel system. That debris clogs the injectors, leading to a loss in fuel efficiency and eventually, engine damage.
Suddenly, a small saving turned into a 4-figure repair and several days of downtime.
The bottom line?
High-quality parts protect your equipment, your workers, and your investment.
In construction, where extended timelines bleed a lot of money, it’s smarter to plan long term.
Store Your Equipment Properly
Proper storage is an important line of defense against rising asset repair costs.
Yet, poor off-season storage is one of the most common equipment maintenance challenges.
If your machines are left exposed, they are likely to experience weather-related damage, rust, fluid degradation, battery drain, and even pest infestations.
Certified equipment manager Mason Ford explains:
“They can attack equipment, and the one thing you don’t want is to come back and find a fleet of equipment that contains beehives or bird nests. They can do real damage to wiring and lights. It’s not uncommon to come back from a break and find a machine has electrical problems because mice have eaten all the insulation off the wiring.”
Other than that, moisture builds up. Lubricants break down.
And then, when you fire them up weeks later, you’re often staring at problems that didn’t need to happen in the first place.
What you should do is shield your equipment to minimize avoidable damage.
Always start by parking machines on level ground, ideally under a cover or inside a storage shed. If that’s not possible, use heavy-duty covers to protect key components from sun, rain, and frost.
Thad Pirtle, VP and equipment manager at Traylor Bros, provides additional tips on how to properly store and protect your assets:
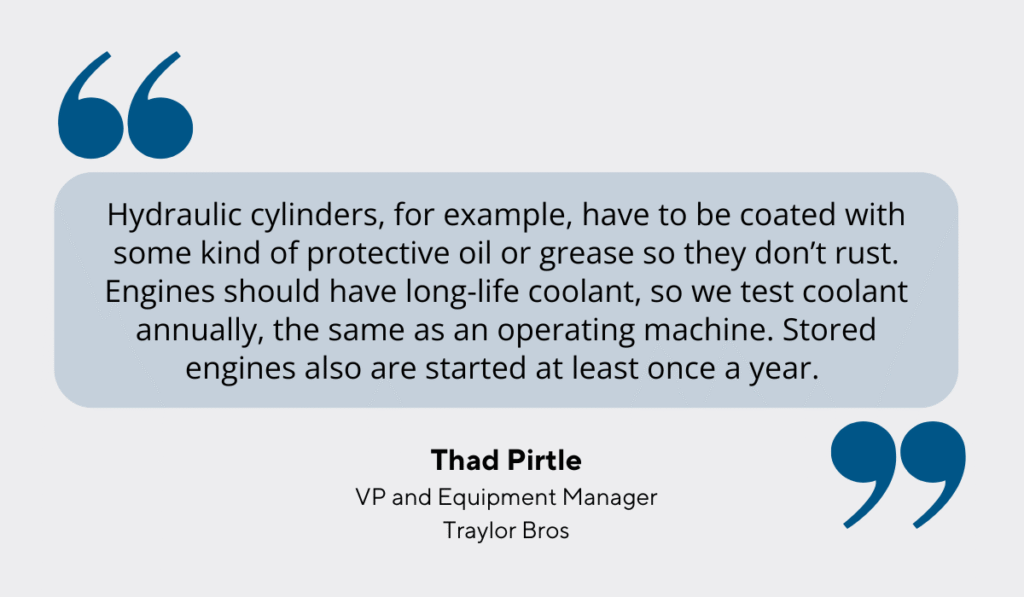
Illustration: GoCodes / Quote: For Construction Pros
If you’re not doing this, you’ll have to face issues like corroded components, degraded seals, and clogged cooling systems.
Ultimately, this leads to costly repairs or complete part failure when the equipment is finally put back into service.
So, the verdict is clear:
It’s always better to perform preventive storage care rather than repair storage-related damage.
At the end of the day, storing your equipment well saves you money and preserves its value.
Invest In Operator Training
Even the newest, most advanced equipment won’t last long in the wrong hands. That’s why investing in operator training is crucial.
A report by Nova Technology shows that only 10% of industrial equipment fails due to natural wear.
This means that the majority of failures—and associated costs—are preventable, and investing in operator training can help with that.
Untrained operators can unintentionally cost you money.
Rough handling, ignoring warning signs, skipping daily inspection routines, or a lack of safety guideline awareness: all of these can shorten your equipment’s lifespan.
Even worse, small issues often go unreported until they escalate into costly breakdowns.
But investing in structured maintenance training helps your team operate smarter, spot early signs of wear, and prevent misuse.
According to a report by OSHA, companies with safety-focused training programs, which also include equipment safety, see 21% more profits.
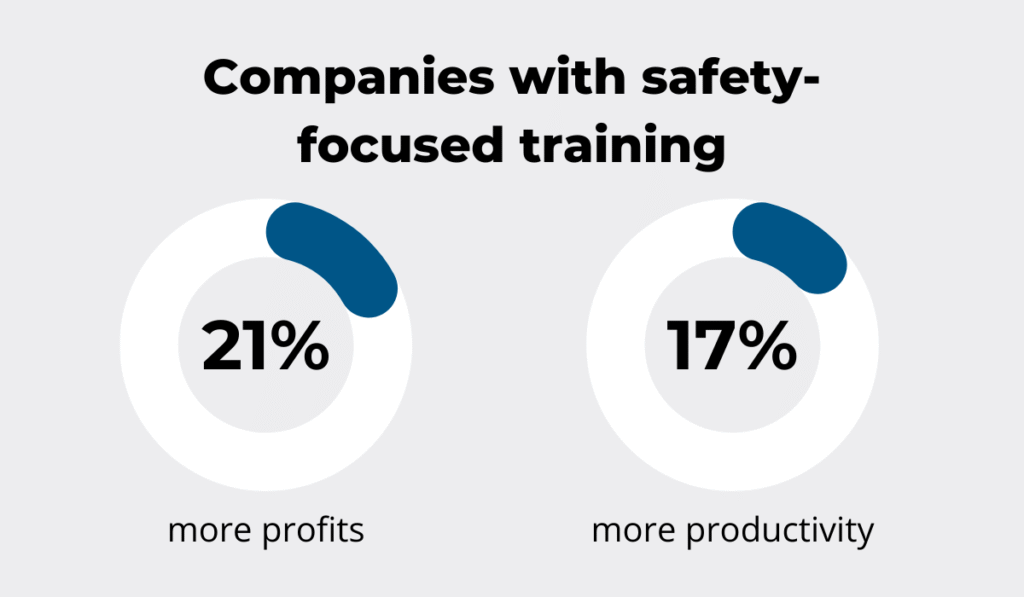
Illustration: GoCodes / Data: OSHA
But training shouldn’t stop at educating on how to operate the machine.
It’s also about knowing what “normal” looks like.
Daily checks like monitoring fluid levels, checking tire pressure, identifying loose bolts, or listening for odd noises may seem minor, but when performed consistently, they keep bigger issues at bay.
After all, operators who are trained to notice and report these issues early can help maintenance teams do timely repairs.
Take Simmons Feed Ingredients, a company that produces high-quality animal nutrition, as an example.
They had their 30 technicians sent for a high-level lubrication certification.
As a result of this investment in worker education, they were able to reduce the downtime by 50-60%.

Source: Machinery Lubrication
Though not in the construction industry, they set a great example of how investing in operator training can lead to significant improvements in equipment reliability and ultimately, cost savings.
So ask yourself: are you training your operators well enough?
When your crew knows how to handle machines properly, you minimize wear, reduce downtime, and protect your investment from the inside out.
Conclusion
Hopefully, you now understand that reducing equipment maintenance costs isn’t just about one magic fix.
It’s about doing the small things right and consistently.
From training your operators to tracking maintenance history and using quality replacement parts, every step adds up to longer machine life and fewer surprise repairs.
Treat your equipment like the investment it is, and it’ll return the favor, project after project.
So start small, stay consistent, and let your maintenance strategy work just as hard as your crew does.