Back in the day, pickaxes used to be the quintessential mining equipment, but nowadays, mining operations are delicate and require sophisticated machinery.
When working underground, you need the very best equipment to handle challenging environments and complete the job efficiently.
In this article, you’re going to learn about the most common types of industrial mining machinery and find out how to manage it for maximum efficiency.
In this article...
Types of Industrial Mining Equipment
Mining includes many different tasks, from digging holes to transporting ore to the surface and even cleaning the mining site after a job is done.
Naturally, there are many types of equipment needed to handle all of these tasks, and they all have to be able to endure harsh conditions within the mine itself, and on the surface.
Let’s start with the first piece of machinery on our list—mining drills.
Mining Drills
As their name suggests, mining drills are the backbone of mining operations.
The first step of the mining process includes digging holes inside the rock you need to break, in order to place the explosives there. Inside each hole, a primer will set off an explosion that will release a high-pressure shock wave, causing the rock to crack and break.
However, it’s impossible to drill the holes accurately without using mining drills. They are specially designed to puncture holes in specific areas quickly and efficiently.
After they’re done drilling the holes, explosives technicians can go ahead with their part of the job.
To get a better understanding of the process, have a look at a mining drill in action, from the 1:50 mark:
Let’s talk about earthmovers next.
Earthmovers
Since various mining processes create an excess of waste materials and rocks, clearing the digging site after completing a task is very important. That’s what the earthmovers are used for.
Earthmovers are powerful machines that move large amounts of earth, debris, and dirt from the ground level of the mining site. Without them, excess materials would pile on top of the site, making maneuvering considerably more difficult.
A fleet of earthmovers can include two different trucks:
- Regular dump trucks with movable open beds that unload materials to specified sites.
- Heavy-duty haul trucks, used almost exclusively for mining operations because of the volume of materials they can carry.
Here’s a picture of a typical heavy-duty haul truck used in mining operations:
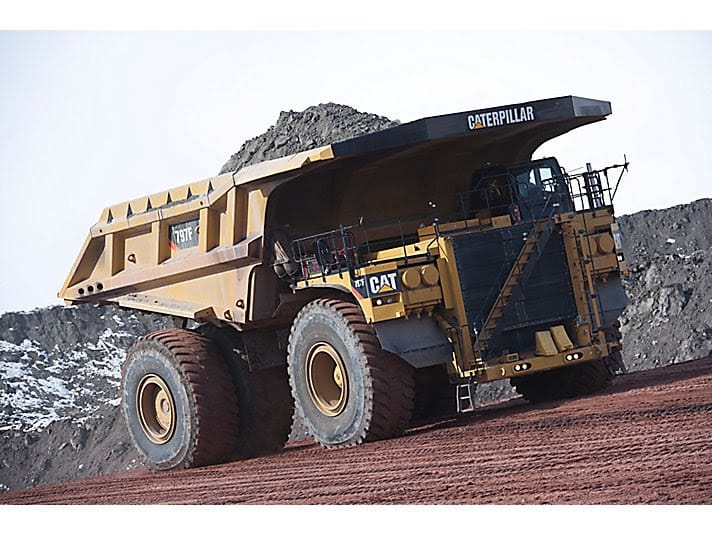
It’s worth noting that earthmovers are supported by excavators that pick up the materials and load them in.
Crushing Equipment
Moving excess material and waste would be considerably more difficult if the miners didn’t crush them to dust first.
Explosions and digging leave volumes of rubble behind that have to be made transportable. After all, boulders and rubble are hard to load if they’re not grained. For that reason, miners rely on crushing equipment.
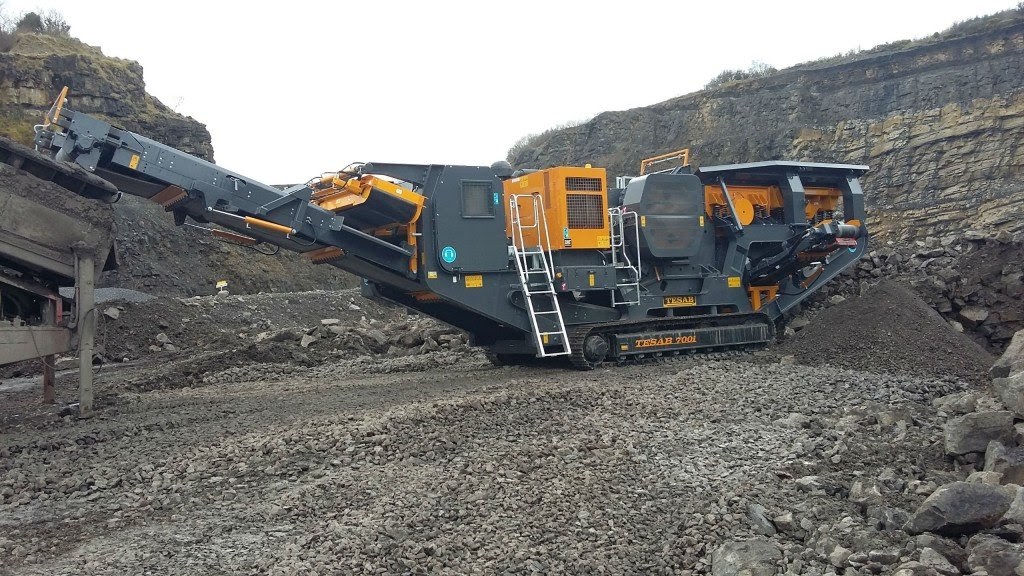
A typical piece of crushing machinery works in tandem with excavators to load the waste into the machine, which falls into the crushing chamber.
After the material has been crushed, the leftovers are transported out on an excavator track from the crusher onto a pile.
From there, earthmovers transport the crushed material off-site, leaving behind a clear mining site.
Underground Loader
After a strategic explosion has opened a tunnel shaft, there’s a lot of rubble all around the mining tunnel. To clear the way, miners use underground loaders to remove the materials and carry them to the designated unloading point.
You can see an underground loader carrying a large load of rocks below:
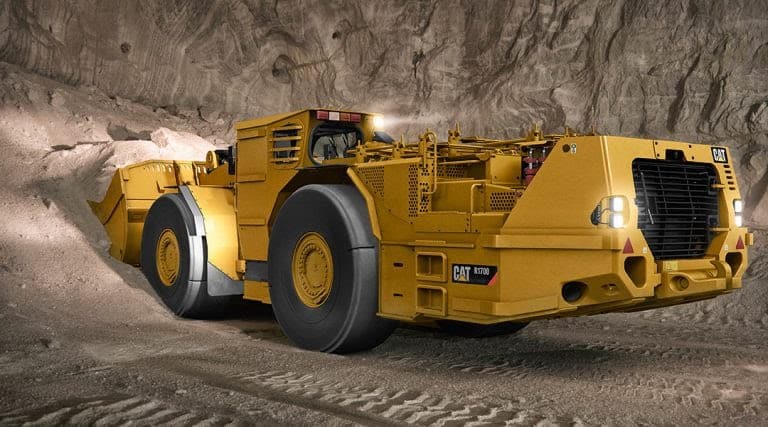
Underground loaders are designed to be lower than traditional loading trucks so they can fit into narrow spaces. Despite their size, they are powerful enough to carry tons of waste material back to the surface.
Longwall Mining
Longwall mining usually takes place deep underground, when excavating coal.
The process relies on incredibly sophisticated interconnected pieces of equipment that work together in an efficient and safe mining operation.
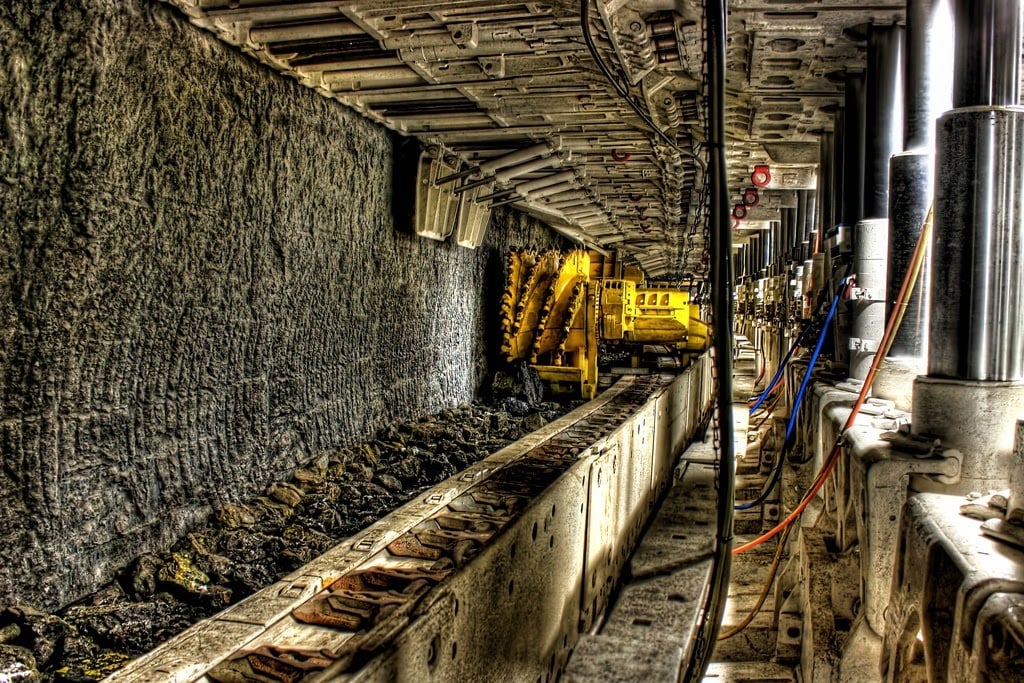
A longwall mining site is usually 3 to 4 kilometers long and 250 to 400 meters wide.
The machinery used there usually consists of 3 parts:
The plow travels across the longwall, cutting the wall of coal (also known as the face), which falls on the conveyor belt. The belt then carries the coal to the crusher.
Finally, various roof support systems hold the longwall mining structure together, keeping the miners safe from a collapse in the mining tunnel.
Continuous Miners
Continuous miners are large industrial mining machines designed to cut through coal and soft minerals. According to the Kentucky Coal and Energy Education Project, they are used in roughly 45% of all underground coal production sites.
Nowadays, continuous miners are remote-controlled and powered by electricity. They are distinguishable for their large rotating steel drum with teeth made of tungsten carbide that cut and grind the coal from the mining site.
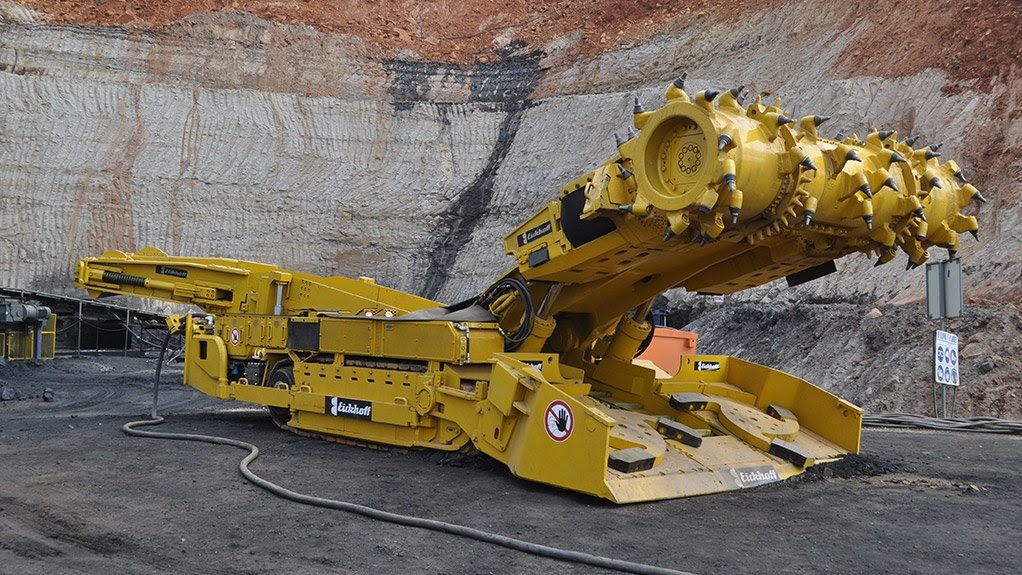
Continuous miners have effectively eliminated manual drilling and picking from the mining process.
Roof Bolters
When it comes to keeping the mining site secure, roof bolters are essential pieces of industrial mining machinery.
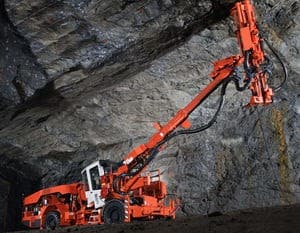
Roof bolters are used to secure the roof of the mining tunnel to prevent any possible cave-ins that could bury or injure miners working on site.
Therefore, the top of the mine is bolted, and a strong safety net is installed. In case the ceiling collapses, the net is designed to catch the debris.
Blasting Tools
Blasting tools are various pieces of industrial mining equipment designed for detonating explosive material.
As you can imagine, blowing rocks up is an essential part of mining operations. In the past, miners would light a fuse and time the detonation sequence for explosive charges. It’s easy to see how dangerous and ineffective that was.
Nowadays, miners use an array of blasting tools to detonate the charges remotely. Electric blasting tools provide precise control over the detonation process and deliver consistent blasting results.
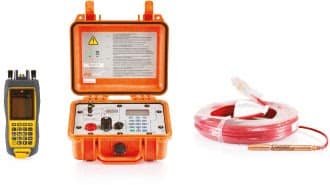
Besides mining, they are often used in the construction industry as well.
Electric Rope Shovel
Mining companies all around the world use electric rope shovels for material loading operations.
Although they vary in size, electric rope shovels can carry a payload of around 120 tons. They’re designed to maneuver in rough terrain and move around from one sector to the next once their tasks are completed.
Electric rope shovels are unique because they have 4 different loading methods:
Single back-up loading, which is effective in restricted mining sites with not much maneuvering space.
Double back-up loading, where trucks position themselves during their waiting time, so that shovel loading times are minimalized to achieve a higher output.
Drive-by loading, which is ideal for earthmovers that use belly-dump methods of unloading their cargo in coal mining sites.
Modified drive-by loading where trucks first park alongside the shovel and then back up. This method works best for end-dump style trucks during coal mining operations.
This is an electric rope shovel during modified drive-by loading operations:
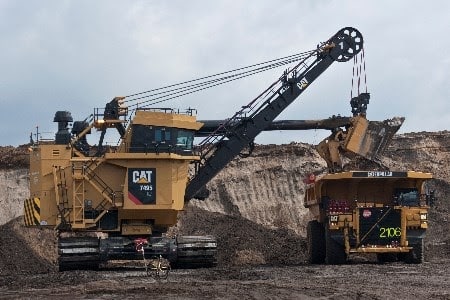
Electric rope shovels are renowned for their exceptional loading times and the lowest cost-per-ton in the industry.
Mining Graders
Mining graders play a variety of important roles at mining sites.
They keep the roads on the site open and clear. Since there’s a lot of heavy machinery moving cargo back and forth, it’s common for waste materials to fall off trucks and get in the way.
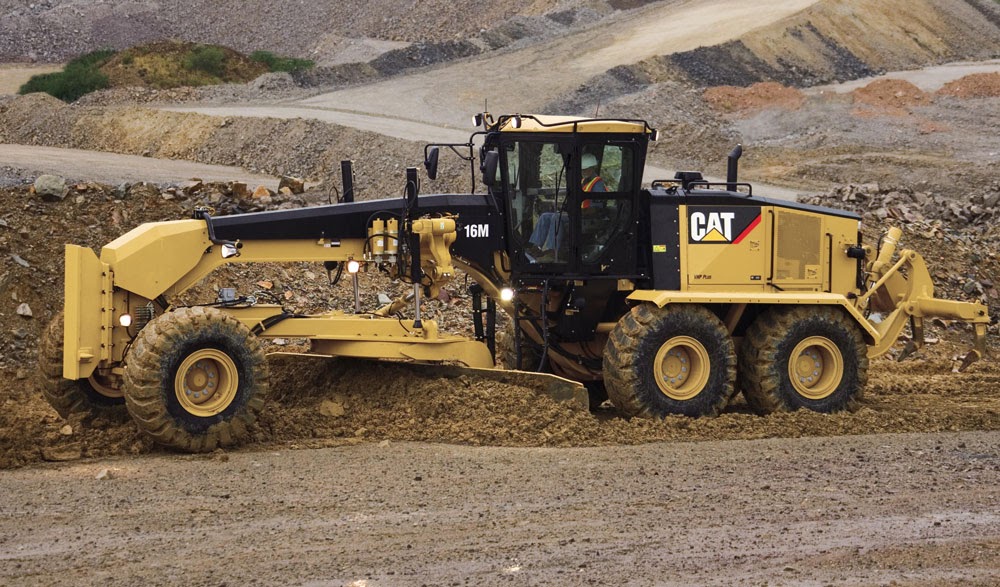
Removing those materials would be a near-impossible task if miners did it manually.
However, a mining grader has an adjustable blade in front to clear out any rocks so that trucks don’t drive over them. This effectively increases the lifespan of all the heavy machines on the site and protects the tires.
If the weather becomes rainy or windy, affecting the passability of the roads, a mining grader will even out the terrain to avoid disrupting the other machinery that is being used in hauling materials.
The main benefit of using mining graders is their impact on overall mining site productivity. You can’t run a tight operation without prepping the terrain and keeping it clear.
Hydraulic Mining Shovels
Hydraulic mining shovels have been the go-to machinery for the mining industry since the 1970s. Such shovels load rock and coal onto other heavy machines.
This is what they look like in the field:
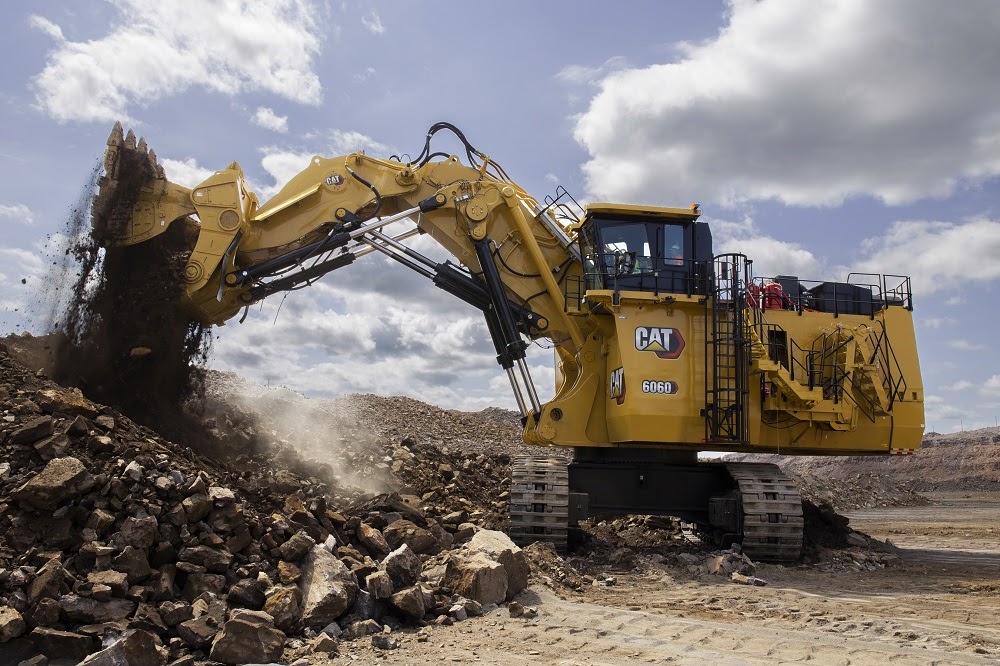
A standard-size hydraulic shovel can carry about 30 cubic meters of material in the metal bucket at the front.
Like loading rubble on construction sites, a hydraulic mining shovel will dig into the pile of material, pick it up and place it on the designated spot, thus clearing the way for other heavy machines and equipment.
Besides their load capacities, hydraulic mining shovels are very mobile for their size and can move around rough terrain. This makes them a must-have part of the mining machinery fleet.
Dragline Excavators
Dragline excavators are among the giant heavy machines you’ll see on the surface of mining sites.
A dragline excavator is a complex system of massive parts that work to clear enormous loads from the mining zone.
The most important part of the system is the dragline bucket, which can carry 30 to 60 cubic meters of material, and move up to 450 tons of rocks in a single cycle.
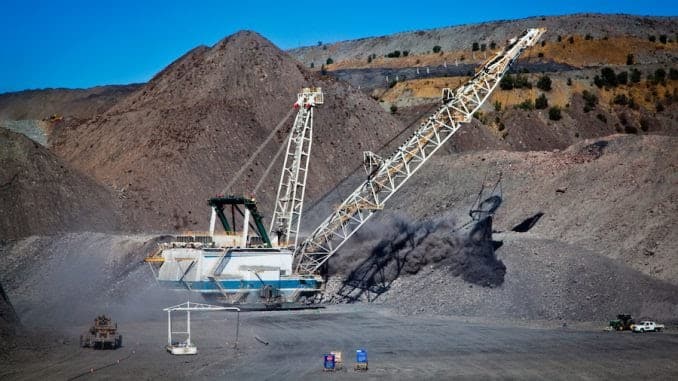
Dragline excavators start the excavation process by swinging the bucket and dragging it upwards along a large pile of rocks or material.
When the bucket is filled, the operator swings and unloads the bucket in the designated area and then repeats the process.
While dragline excavators are powerful and irreplaceable machines, they have excessive energy costs, which is why it’s common to see them working overnight when electricity is cheaper.
To ensure efficient operations, it’s absolutely essential to successfully determine the ideal position of the dragline excavator before deploying it. It’s paramount to regularly check and perform maintenance on dragline excavators.
How to Manage All Mining Equipment
As with all equipment essential for regular day-to-day operations, mining equipment needs to be appropriately managed.
When it comes to industrial mining gear, tracking is the most critical aspect of managing it. Tracking your industrial mining equipment and machinery enables your team to understand where the assets are in real time and monitor their current state.
Your team can then schedule maintenance cycles to greatly reduce the chances of critical equipment breaking down in critical moments. Since mining sites are dangerous environments, the equipment being used has to be in top running order.
If you’re in charge of a large mining operation with many different pieces of machinery and gear, it’s impossible to track everything manually.
There’s no way you’ll be able to tell when a mining machine has been maintained last, and there’s always a possibility of a critical breakdown.
That is, unless you use heavy equipment tracking solutions, like the one provided by GoCodes Asset Tracking.
With our system, your team can put labels on every piece of equipment in the field and track their location and current condition in real time.
Since every smartphone can scan QR codes nowadays, your onsite miners can quickly scan the tag on a machine, get info on its status and update it.
This enables you to stay ahead of any unpredictable breakdowns. By tracking equipment condition reports, you can be sure that the machinery being used is in top order.
In addition, the labels are durable and can withstand harsh conditions, both outdoors and underground. The labels use permanent adhesive, which means there’s no chance of them getting scratched off or falling from the mining equipment.
Conclusion
Mining operations are some of the most intense activities that involve heavy machinery. There are many types of mining equipment with specific use cases, with each one demanding special attention and management.
We hope that this article has given you some valuable insight into mining equipment and its various uses.