If you’re in the construction industry, you know that heavy machinery is your most valuable investment. You rely on your bulldozers, excavators, forklifts, and front-end loaders and should keep them in top condition.
But this is often easier said than done, and many companies make maintenance mistakes that can lead to more downtime, extra expenses, or even potential accidents.
Below are some equipment maintenance mistakes that can hinder your construction projects and what you can do to avoid them.
Let’s start.
In this article...
Skipping Regular Maintenance
The first mistake you might be doing that could hinder your construction projects is neglecting regular maintenance.
Neglecting regular maintenance can have severe consequences; machine breakdowns, costly repairs, and more downtime.
Many construction companies don’t put much effort into creating a maintenance plan, or, if they do, they rarely stick to it.
This is a big mistake, since without a proper maintenance plan, it’s going to be hard to keep up with the repairs necessary for your machinery to remain in top condition.
The best thing you can do to avoid this mistake is to make sure you’re doing upkeep regularly.
You see, companies often ignore the need for routine maintenance until it’s too late and the equipment is already severely damaged.
Sticking to a regular routine means bringing your equipment in for maintenance on time and preventing costly downtime by conducting repairs and replacing parts before any existing issues escalate so far that the equipment breaks down.
By being diligent, you can seriously reduce your overall maintenance expenses.
For instance, imagine that you paid 100,000 dollars for your excavator and that it requires 30,000 dollars in maintenance over 7,000 hours of operation.
You might think that’s a lot of money, but, actually, by doing so, you would be saving 25% compared to what your expenses would be without a preventive maintenance strategy.
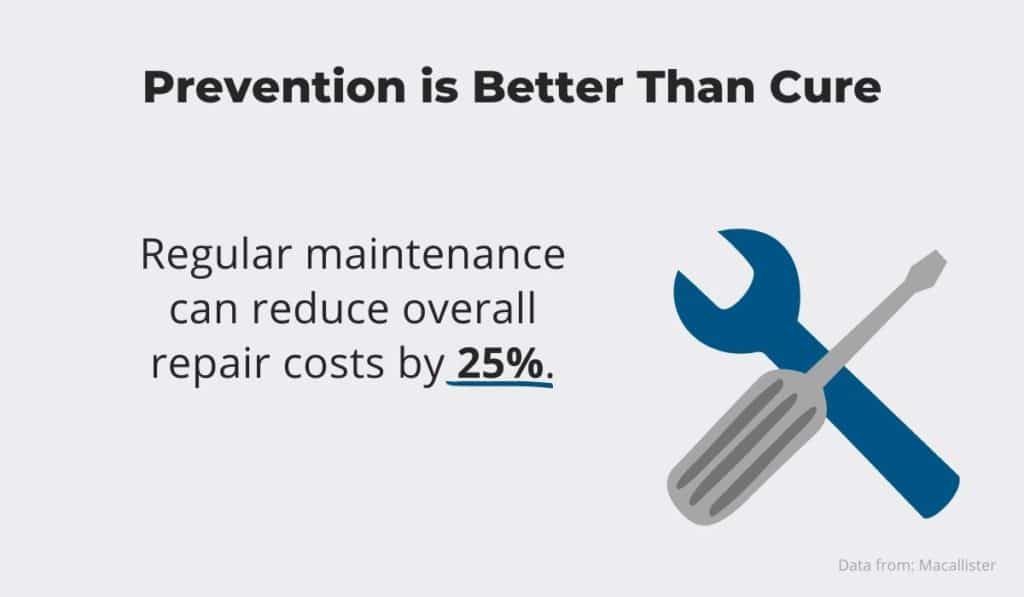
Another maintenance-related mistake you can make is to opt for a one-size-fits-all approach. You should understand that each piece of your equipment has unique specifications and requirements.
One machine might need lubrication every 100 hours, while for another, it will be enough to replace fluids every few weeks.
If you conduct maintenance on all of your machines at the same time, one item will probably get too much attention while another will be underserved.
Maintenance schedules should be based on the equipment type, age, and duty cycle, and it’s important to prioritize the machines with the highest chance of failing, be it because of their age, or because of the harsh conditions in which they are used.
To sum up, skipping regular maintenance might seem like a good way to save some time and cash, but in the long run, it will cost you a lot more than you’ll initially save, and it is likely to disrupt your whole project.
Leaving Your Equipment Unprotected
This one might seem obvious, but it’s worth noting that you can actually hinder your projects if you leave your equipment unprotected.
In addition to the obvious possibility of theft, other dangers are lurking as well.
For instance, many companies underestimate the detrimental effects of exposing their equipment to the elements.
After all, it’s called heavy equipment, so it should be durable no matter what, right?
Wrong.
The components of your machines are highly vulnerable to the elements and can be quite expensive to fix or replace.
Weather and temperature changes are some of the biggest enemies of your equipment. For example, a big mistake many contractors make in the summer is ignoring that heat and sunlight can negatively affect their machines.
The best thing you can do to avoid this is to keep your equipment out of the sun as much as possible. Of course, construction does not stop during the summer, but you can take a pause when the sun is at its peak.
Also, when it comes to storage, it’s important to never, ever leave your machines in the sun. If you simply must, and there is no other option, make sure to use a sun-protecting tarp to provide some shade for your machines.
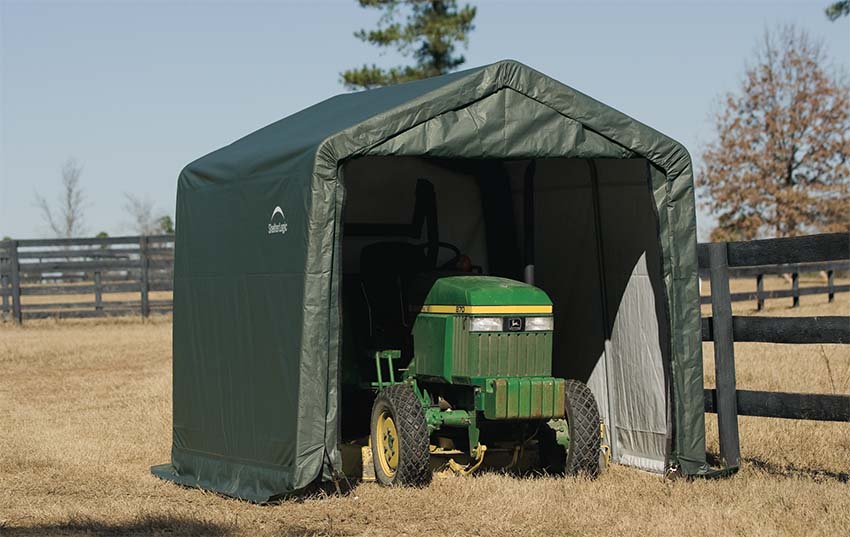
Similar mistakes are made during the winter months when freezing temperatures can severely damage your machines. The best way to protect them is to store them indoors.
However, if that is not possible, and you must keep your machines outside, the best thing to do is to park them in a dry place, sheltered from the wind.
Again, a trap cover might come in handy as it will prevent snow and moisture from building up and damaging your machines.
Another mistake that happens a lot is inadequate storage of equipment, which can occur during all seasons.
It may sound odd to you that stored equipment can get damaged, but inadequate storage can cause high humidity levels, leading to problems like corrosion.
To avoid that, always store your equipment and machinery in a clean and dry place, and take necessary precautions to prevent moisture from building up.
All in all, you never want to leave your equipment unprotected, whether in storage or outside in extreme temperatures.
Keep your machines protected from the heat, moisture, and cold at all times if you want your project to succeed.
Not Training Your Operators
We can’t emphasize enough the importance of avoiding the next mistake that can hinder your project, and that is not training your operators.
We all know that one of the biggest reasons for machine breakdowns is improper use. A lot of companies seem to assume that their operators know how to operate every piece of equipment ever made. This is, of course, false and probably even impossible.
Failing to train your heavy equipment operators can also result in injuries and compromise the safety of your site.
In fact, research shows that new employees are much more likely to experience a workplace accident, highlighting the need for quality training.
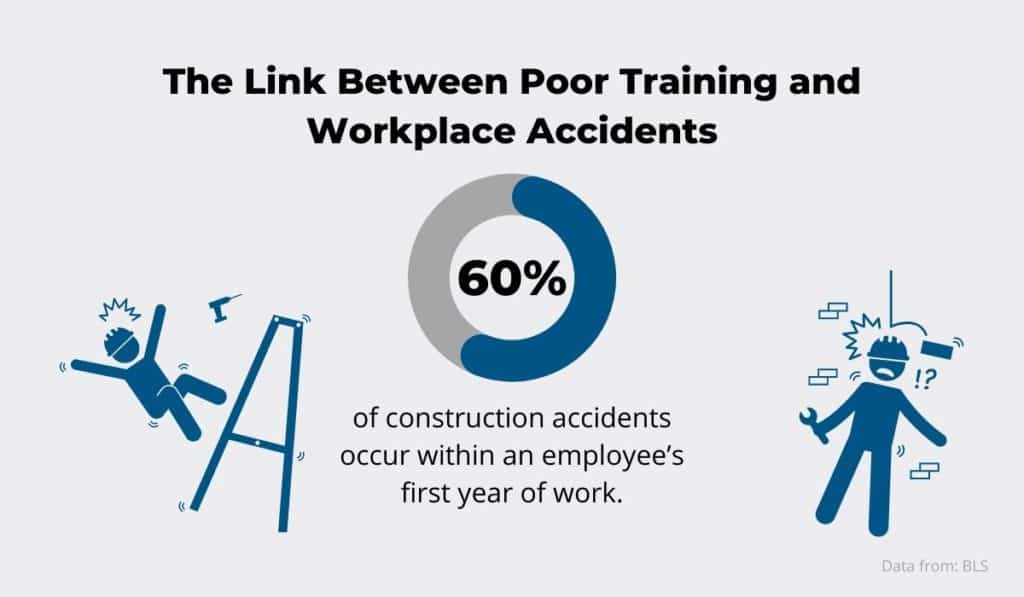
That is why it’s essential to provide proper training for your operators, teaching them how to safely and properly use every piece of equipment you own.
But even if you put effort into educating your employees, you can still make some mistakes. A common one is related to training styles.
For instance, traditional types of training are performed in classrooms and not on construction sites.
This isn’t the best way to train your workers because you automatically make training seem like something separate from the job, making your operators easily forget presented skills.
You should opt for a more modern, on-site training program instead.
Other than the privilege of learning new skills in a familiar environment, your operators will also be able to put safety measures into perspective and have them always in the back of their minds.
In this way, there’s a bigger chance that they will take the necessary precautions while operating your equipment.
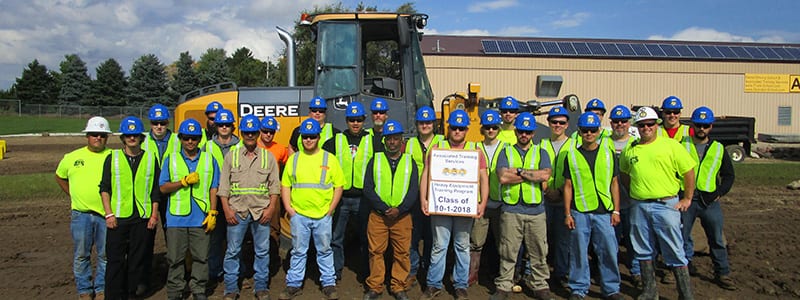
It’s simple: if you neglect training your operators, they’re more likely to handle your equipment improperly and make mistakes that lead to costly repairs, more downtime, or even accidents and injuries.
Remember, employee training may cost a lot of money, but the mistakes made due to the lack of training are far more expensive and will disrupt your projects.
Overlooking the Importance of Cleaning Heavy Equipment
Another common mistake that can disrupt your projects is neglecting the importance of cleaning your heavy equipment.
Cleaning your machinery is no different than cleaning your home—it should be done regularly, or you will end up with a big mess.
When we’re talking about cleaning your machines, we’re not talking only about aesthetics.
Sure, it’s nice to see a sparkly clean excavator, but the reason it’s important to keep your equipment tidy is because a build-up of dirt can cause damage to your equipment in the long run.
Sand, grit, rocks, concrete, and other abrasive materials can damage the engine, the undercarriage, and other parts of your machines.
This will expedite wear and tear, but these abrasive materials won’t get the chance to build up if you clean your equipment regularly.
It’s also important to pay attention to your filters. You probably know you should clean and replace them regularly, but here’s a short refresher on how to do it, just in case.
However, overdoing it can also be harmful. For example, cleaning your air filters too often is a common mistake. Believe it or not, air filters are more efficient the more they are used.
A certain amount of dust that collects in the filters actually helps the filter function better because, thanks to it, the filter will capture even the smaller particles of dust that would reach the engine otherwise.
Therefore, you shouldn’t hurry to clean the dust straight away since it can bring more harm than good.
It is good practice to follow some ground rules for cleaning. It is important to know how to clean your equipment and what tools and products to use.
For instance, people often make the mistake of starting the cleaning process with the cabin.
However, you should always start with the undercarriage since it’s most likely the dirtiest part of your machine, and after that, simply wash the whole machine from top to bottom.
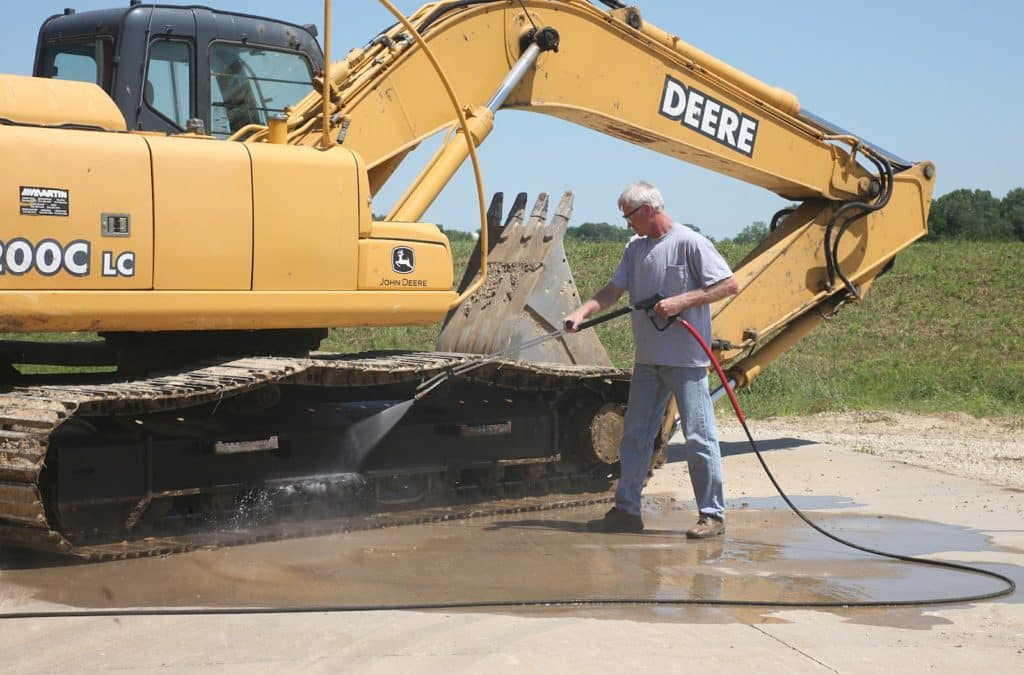
And while you’re at it, make sure you’re using the right tools to clean your machines. We recommend using a pressure washer since it can get into the tiniest crevices you could never reach by hand.
In conclusion, clean machines will perform better; there will be fewer breakdowns, downtime, and unexpected expenses.
Pushing Your Equipment Beyond Performance Limitations
The last mistake that could disrupt your projects is a big one. Pushing your equipment beyond its specifications is always a bad idea.
If your job requires above-average performance, it’s a better idea to buy some heavy-duty equipment than push your weaker equipment to its limits because this will result in constant repairs.
Also, a common mistake a lot of contractors make is ignoring manufacturers’ guidelines on optimal performance and utilization.
Those guidelines are here to maximize and protect your heavy machinery, and the consequences of ignoring them can be disastrous and expensive.
You paid a lot of money for your machines, so it’s in your best interest to keep them in mint shape for as long as possible, and the best way to achieve that is to follow manufacturers instructions.
Except following the manual, you should also keep an eye out for the signs you’re overextending your equipment. For example, changes in exhaust color can be a clear indication of overextension.
Normally, the exhaust should be colorless, so it’s not a good sign if you’re seeing color coming out of your machine.
There are three abnormal exhaust colors: white, black, and blue. If you see either one of these colors, it’s a sign that it’s time to visit your mechanic.
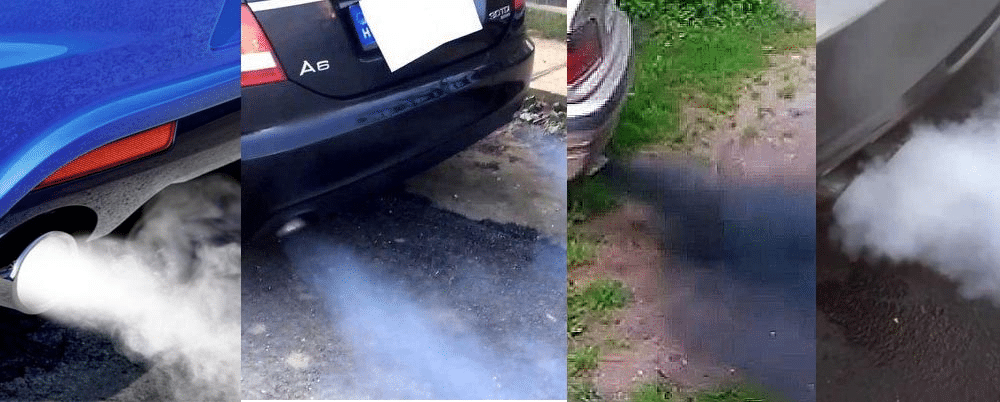
Another mistake most contractors make is ignoring unusual noises. This is usually due to the fact that heavy machinery is noisy by default. However, there are some changes in the sound you should pay attention to.
For instance, low oil pressure can cause a rumbling sound coming from the engine when accelerating. The correct term for this type of noise is crankshaft-bearing noise.
The worst mistake you can make if you hear this noise is running the engine again before the oil pan is removed.
In most cases, the engine can be saved if the crankshaft is not damaged, so it’s important to promptly head out to your mechanic to avoid serious damage.
All in all, pushing your equipment beyond its limits should be avoided as much as possible. Always follow the manufacturer’s guidelines and keep an eye out for any signs that could warn you that your equipment is being overworked.
Conclusion
Mistakes in equipment maintenance are common and can hinder your construction projects.
In order to keep your project plan on track, you should maintain your equipment regularly to avoid any unexpected breakdowns or even accidents on your construction site.
If you follow the advice listed in this article, your equipment will run strong for many years to come and won’t interfere with the progress of your construction projects.