The success of construction companies hinges heavily on effective resource management.
Among these resources, a wide range of tools, equipment, and other assets stand out as critical components.
However, managing these assets is often a challenging task.
Manual tracking methods are often ineffective, especially when there is a high volume of equipment to be tracked. This can lead to increased costs and inefficient operations.
Fortunately, there are numerous benefits associated with using equipment tracking software that can help you avoid these problems.
Here are nine of them.
In this article...
Reduced Reliance on Manual Processes
Many construction companies still rely on manual processes to track their equipment.
While tools used for manual tracking such as Excel are undoubtedly great and have numerous advantages, they are not meant for equipment tracking.
Using them for this purpose can result in valuable resources being used up and avoidable mistakes being made.
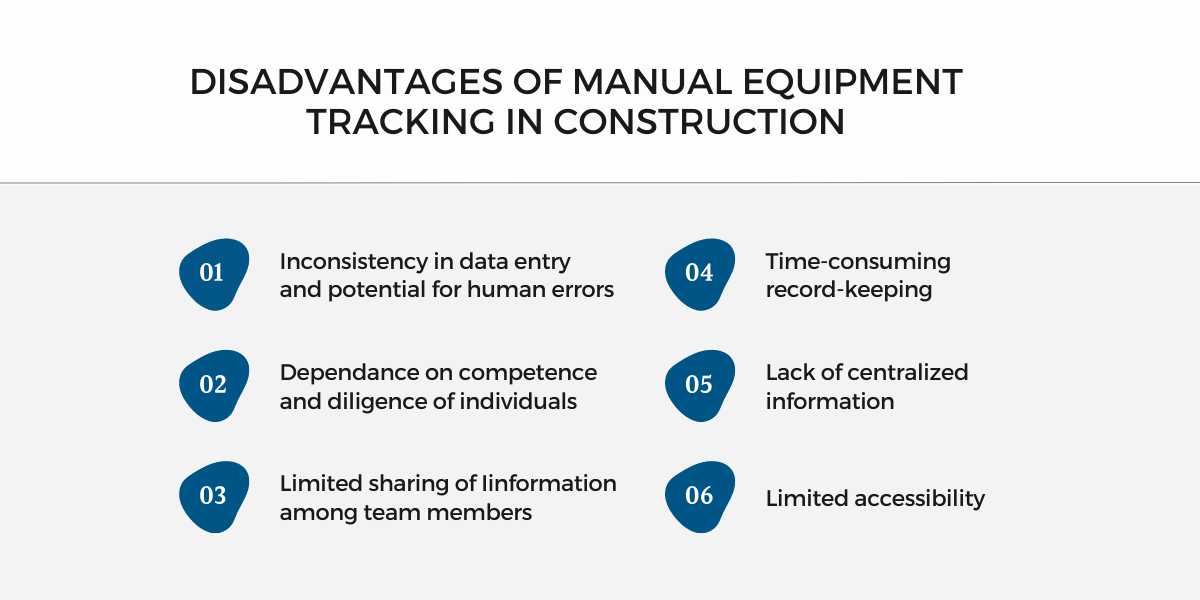
When workers have to manually track equipment locations, monitor equipment usage, and keep records of equipment maintenance, there is a higher chance of human error.
If workers have to constantly update equipment tracking spreadsheets with the latest data but forget to do so, those spreadsheets become outdated.
Also, sharing Excel spreadsheets with other departments and employees can be challenging and result in duplicate files where nobody knows which version is the latest.
A better solution exists in the form of equipment tracking software.
As it enables centralized data management, it allows users to access the digital inventory of equipment from any compatible device, be it a smartphone or laptop, and update their statuses accordingly.

For example, if a loader is being transported from one job site to another, the operator can simply log into the software and immediately report it.
Information will be instantly updated across the system and made accessible to all users.
This not only ensures that everyone is working with real-time, accurate information, but it also reduces the chance of human error.
Therefore, if you want to streamline processes and improve efficiency, switching to equipment tracking software is a wise move.
Increased Equipment Utilization
Underutilized equipment can be likened to a leak in the company’s resources.
Even if you are not using equipment, it still comes with expenses.
In other words, services, repairs, storage, insurance, licensing, and permits all count as ongoing expenses, whether the equipment is idle or not.
That is why it comes as a surprise that, according to Gartner study, 30% of companies don’t know:
- which assets they own
- where the assets are located
- who is using them
That’s where equipment utilization comes in. It is a metric that helps gauge how efficiently the equipment is being used.
Calculating equipment utilization is straightforward.
Simply divide the time the equipment is actively in use by the total time it’s available for use, and then multiply that by 100 to get the utilization rate percentage.
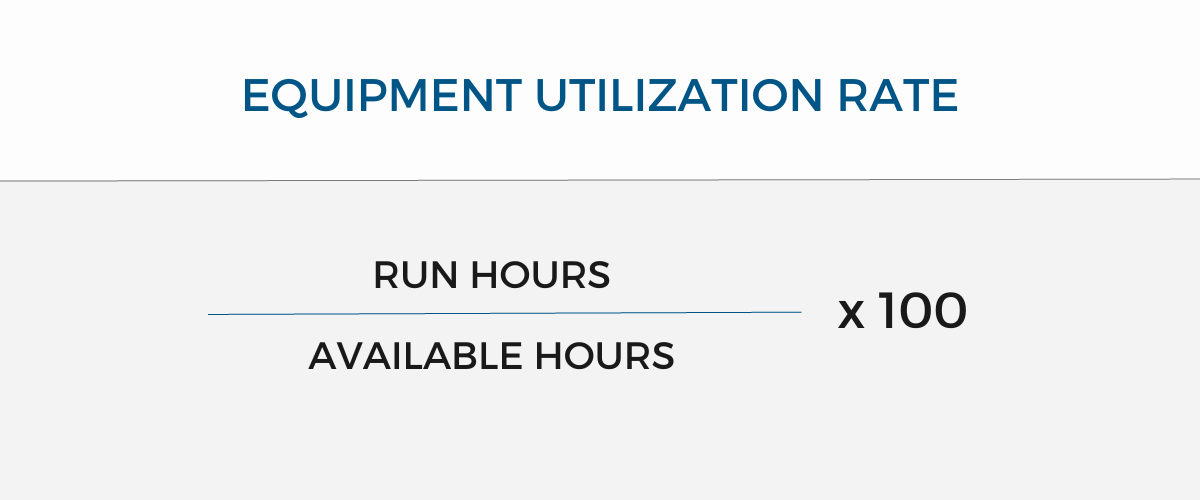
Let’s take this from theory to practice with an example.
Imagine you have a crane scheduled for 8 hours a day, five days a week, giving it 40 hours of available time per week.
However, unexpected factors come into play, and the crane ends up running for only 32 hours that week.
By plugging those numbers into the formula, you can calculate the utilization rate, which in this case is 80%.
But how can equipment utilization be increased? The answer lies in implementing an equipment tracking system.
This system gives you access to essential information that can help you increase the productive hours of your equipment.
You can track your equipment, their locations, who is using them, how long they are being used, and when they are scheduled to be used next.
Equipped with this information, you can optimize asset allocation by assigning equipment to different work schedules, workers, or construction sites.
As a result, your utilization rates improve and your operational efficiency increases.
Higher Employee Accountability
Construction sites are bustling places full of activity, with various tasks being carried out by different workers using a wide range of equipment.
By implementing equipment tracking software, you can keep tabs on the equipment and make employees more accountable for the equipment they’re using.
Let’s examine the explanation behind this claim.
As we mentioned earlier, equipment tracking software provides valuable insights into who is using the equipment and when.
When workers know that their equipment usage is being monitored, they tend to act more responsibly and take better care of the equipment.
This ensures that equipment is returned in good condition and to storage where it belongs, making it accessible for the next task.
Implementing this type of tracking is easier than you might think. All you need is tracking software with a handy check-in and check-out feature.

How does it work? Well, when workers need to use specific equipment, authorized personnel simply need to scan the QR code tag on it.
This action opens up the equipment’s database entry page, where workers can do a quick check-in.
Assigning the equipment to a specific worker, adding a projected return date, and adding any additional notes can all be done with just a few clicks.
Returning the equipment is again as simple as a quick scan and a check-out.
The main advantage of this system is that it encourages employees to pay more attention to the equipment they are using, making them more likely to handle the equipment with care and ensure its safe return.
Improved Equipment Maintenance
Keeping your equipment in top shape is crucial to the company’s bottom line.
The best way to do this? Regular preventive maintenance.
Rather than waiting to fix problems as they arise, called reactive maintenance, preventive maintenance aims to prevent failures from happening altogether.
This, as you can see below, brings many noteworthy benefits to the table.
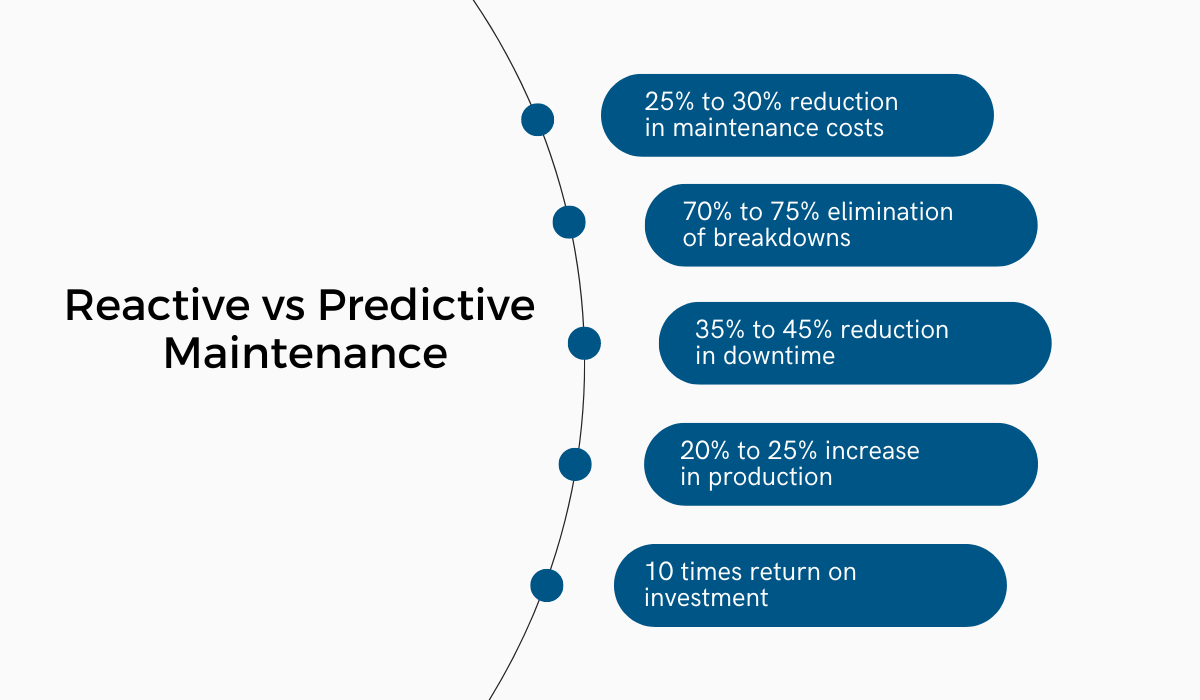
Why is this relevant? Because critical equipment failures cause excessive damage and often require costly repairs.
The resulting equipment downtime can also cause costly project delays.
By performing preventive maintenance at regular intervals, you can avoid these worst-case scenarios.
Thankfully, an equipment tracking system can help you develop and maintain a solid preventive maintenance schedule.
Tracking equipment data like present condition, maintenance history, and usage allows you to create optimal maintenance plans for each piece of equipment.
For example, you can use this data to identify when particular equipment needs maintenance, instead of waiting until it breaks down and leaves you stranded in the field.
Also, equipment tracking software allows you to schedule and assign maintenance tasks and set email reminders to workers to ensure that no piece of equipment is left unmaintained.
Ultimately, this can help you stay on top of your equipment maintenance and prolong the life of each piece of equipment.
Better Equipment Lifecycle Management
Unexpected breakdowns and emergency repairs can wreak havoc on project timelines and budgets.
One of the main causes of these problems is the failure to track equipment lifecycles, which is a common challenge in the construction industry.
When companies lack an understanding of where the equipment stands in its lifecycle (as shown in the image below), it can be difficult to optimize its use, make decisions regarding repairs and replacements, and remain prepared for unexpected emergencies.
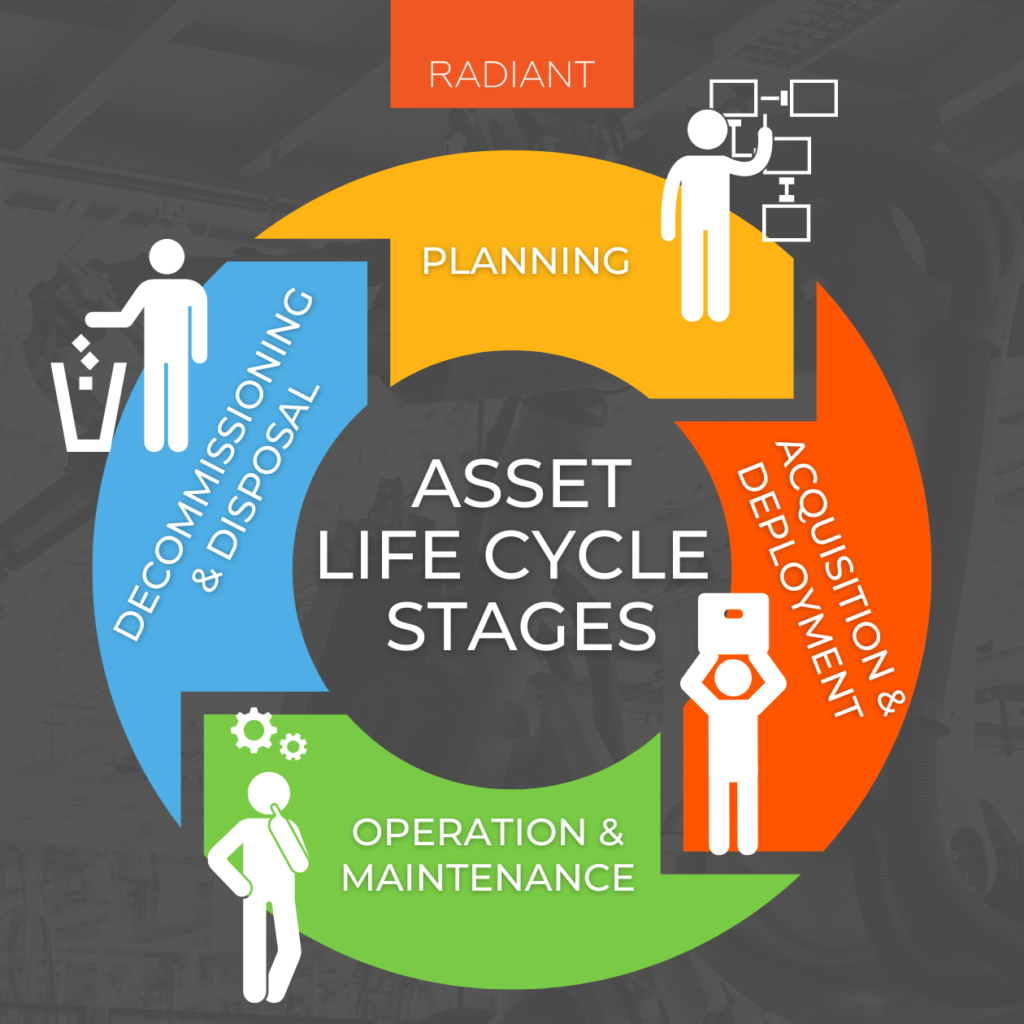
To overcome this challenge, equipment tracking tools can be of great help.
By integrating each equipment’s entry with information such as the manufacturer, purchase date, warranty status, and dates of major maintenance actions, you gain access to valuable data that will guide maintenance schedules and help monitor depreciation.
With this knowledge, you can take preventive measures, reduce breakdowns, and extend the lifespan of your equipment.
Furthermore, you can make better decisions about whether to purchase new equipment, repair existing ones, or replace them altogether.
Reduced Risk of Equipment Theft
Equipment theft is a harsh reality in the construction industry.
The reasons behind this trend are many, including inadequate security on construction sites, the high price of equipment, and low penalties for theft crimes.
The numbers are striking: National Equipment Register reports that equipment theft costs the construction industry up to one billion dollars.
And when it comes to recovering stolen equipment in the construction industry, the recovery rate is less than 22%.
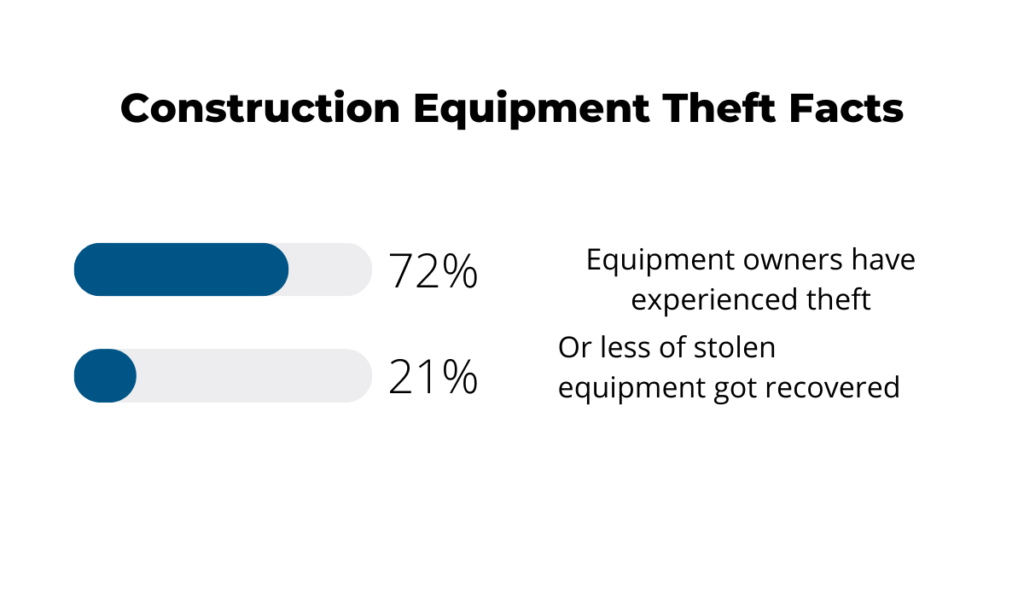
This means that the chances of getting back what was stolen are quite low.
Tracking software, like our own tool, GoCodes Asset Tracking, gives you an effective means to track the equipment’s location, reduce the chances of theft, and recover stolen equipment.
That is because it provides two methods of location tracking.
The first one can be done using QR code tags and smartphones.
First, each piece of equipment receives its own QR code tag, which serves as its unique identification.

Then every time the tag is scanned, the software uses the smartphone’s GPS coordinates to update the equipment’s location.
While not providing real-time tracking, this method enables you to determine the equipment’s last known location and user, which can be helpful in recovering missing equipment.
The second method involves Bluetooth beacons.
Any Bluetooth-enabled device, such as smartphones, tablets, or laptops, can pick up beacon signals, giving you the ability to monitor your equipment in real time within a 300-feet range.
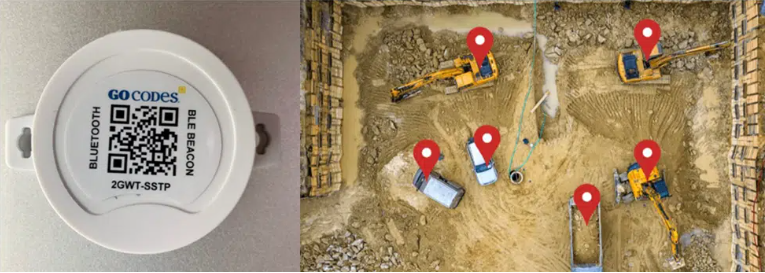
Additionally, GoCodes Asset Tracking provides you with the Guardian feature, which enables you to stop theft in its tracks.
When a piece of equipment with a Bluetooth beacon attached to it goes out of range, you immediately receive a text message.
This gives you an opportunity to act quickly and successfully recover the equipment.
Regardless of which method you choose, equipment location tracking is a valuable solution for maintaining a secure worksite by deterring theft and recovering stolen equipment.
Lower Insurance Premiums
Running a construction company comes with a variety of expenses, including but not limited to equipment expenditures.
However, one expense that often catches construction owners and contractors off guard is insurance premiums.
These premiums typically cover a range of items, including materials in transit, scaffolding at job sites, tools, and heavy equipment, just to name a few.
Considering that insurance premiums can account for anywhere from 1% to 5% of project costs, it’s crucial to keep them as low as possible. Otherwise, they can quickly eat into the budget.
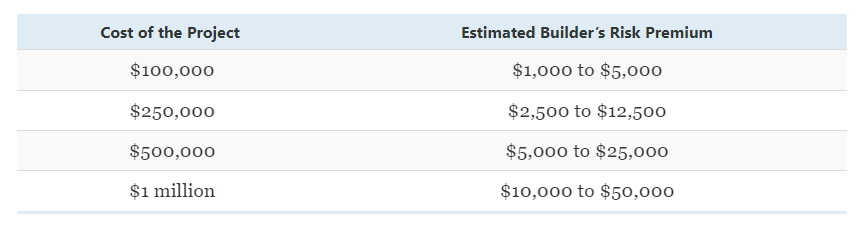
To potentially negotiate lower premiums, therefore, you need to actively reduce your risk and support your actions with proper documentation.
One highly effective method to achieve this is through equipment tracking.
Equipment tracking software, especially software utilizing GPS technology, enables real-time monitoring of the equipment’s location, as we discussed earlier.

This feature is crucial as it significantly reduces the risk of loss and theft, which can potentially lead to insurance claims.
By tracking the equipment, you not only protect your valuable assets, but also demonstrate to insurance companies that you are taking proactive measures to minimize risks.
This shows them that you are a responsible and reliable company, which can positively influence their assessment of your insurance premiums.
Additionally, equipment tracking software provides visibility into equipment usage and maintenance.
These records play a crucial role in assuring insurance providers that your equipment is well-maintained and in optimal condition.
As a result, the risk of accidents or malfunctions that could lead to insurance claims is significantly reduced.
Remember, insurance companies value businesses with robust documentation practices to support their risk-reduction strategies.
By incorporating equipment tracking measures and maintaining solid documentation, you not only protect your business but also have the potential to benefit from reduced insurance premiums.
Improved Regulatory Compliance
In the construction industry, compliance requirements can be complex, and there are many of them to keep track of.
While safety regulations, like those set by OSHA, apply universally, there are additional requirements that can vary from location to location, such as:
- building codes
- insurance regulations
- contractual agreements
- wage and union payroll requirements
- bonding requirements
Failing to comply with these regulations can have serious financial implications for construction projects and even bring them to a halt.
This financial toll is just the tip of the iceberg. Non-compliance can also result in legal repercussions and damage to the company’s reputation.
Equipment tracking software can help you stay proactive and streamline compliance requirements. Here’s how.
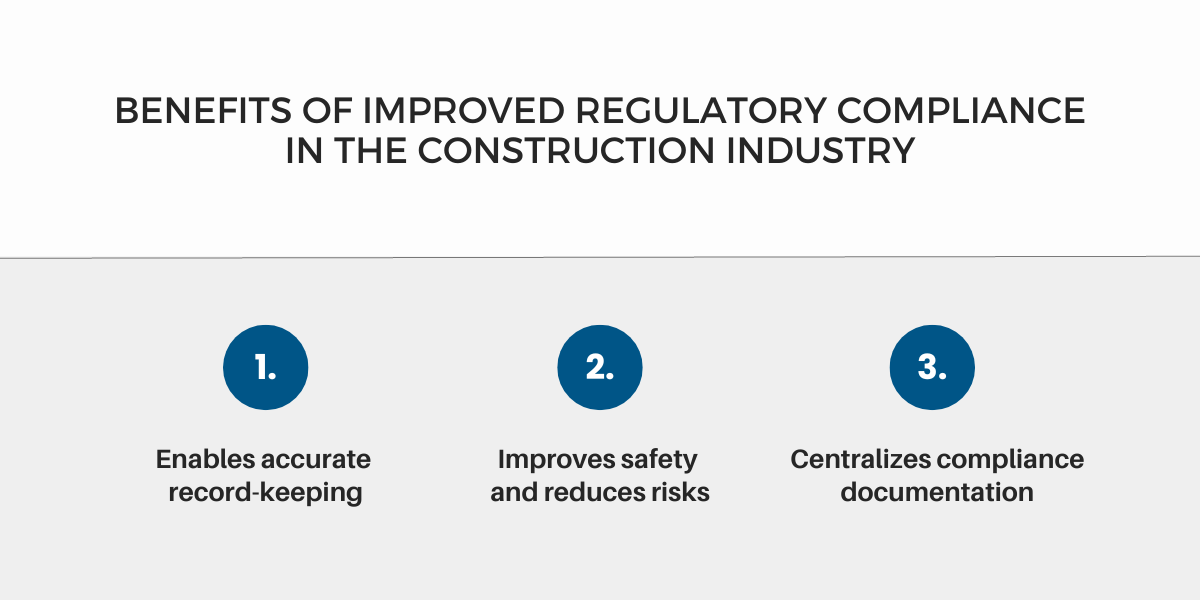
For starters, it allows you to maintain accurate and detailed records of the construction equipment.
These records provide the necessary documentation to demonstrate compliance with regulatory requirements during audits or inspections.
Additionally, with equipment tracking software, you can store all compliance-related documentation in a centralized and easily accessible location.
This includes licenses, permits, certifications, and safety documentation.
This way, there is no more hassle of sifting through heaps of paperwork. When it’s time for critical compliance checks, you will have everything you need at your disposal.
Compliance is not an option but a necessity in the construction industry.
By implementing equipment tracking software and adhering to regulatory requirements, you will benefit from improved efficiency, increased safety, reduced risks, centralized documentation, and a strong brand reputation.
More Accurate Job Estimation and Billing
Estimating construction jobs and billing accurately can be quite challenging.
The unpredictable nature of construction projects means that setbacks can arise at any moment, throwing off initial projections.
Even more, the cost of materials has skyrocketed in the last few years, making this process even more difficult.
However, there are a few practical solutions that can significantly help in achieving more precise estimates.
One such solution is implementing equipment tracking software.
By recording the number of days each piece of equipment is used, it gives you real-time data on actual equipment usage.

This eliminates guesswork and provides accurate data to estimate the correct equipment requirements for future projects.
Next, accurate equipment usage data enables you to account for the costs associated with equipment rental or ownership.
This results in more precise billing estimates and helps avoid potential disputes with clients.
In other words, having accurate data on equipment usage and costs is crucial because it allows you to steer clear of both overestimating and underestimating equipment requirements.
Overestimating equipment needs can lead to unnecessary costs, while underestimating can cause project delays and additional expenses.
Equipment tracking software can help you find the right balance between the two.
Conclusion
As you can see, equipment tracking software holds a wealth of benefits waiting to be discovered, and the nine we have outlined here merely scratch the surface.
Equipment tracking software will enable you better utilize your equipment and keep up with equipment maintenance to extend the lifespan of your equipment.
It will increase accountability among your employees and prevent your equipment from being stolen. Even if a piece of equipment is stolen, the best tracking software will help you recover it.
Lower insurance premiums and easier regulatory compliance are a nice added bonus.
By implementing equipment tracking software, you will not only unlock all of these benefits but also uncover even more benefits specific to your construction business.