Even though it can be quite costly, regularly servicing your machinery is vital for keeping your equipment and business running. Failing to perform regular maintenance will eventually lead to substantial monetary losses and project delays.
So, construction companies rely either on in-house or outsourced maintenance to keep their equipment in optimal condition.
Nevertheless, many of them run into hurdles along the way and, as a result, struggle to keep their business afloat despite their efforts.
This article will explain the most challenging aspects of maintenance and offer ways of overcoming them. After reading, you should have a clear understanding of what you need to change to get the most out of your equipment.
In this article...
Keeping Maintenance Standards
Not following the rules of adequate, safe maintenance can land you in hot water with the Occupational and Safety Health Administration (OSHA).
The agency can issue fines if they find you aren’t compliant with their rules. The penalties can go up to $13,653 per single violation, or as much as $136,532 for repeat violations, so it’s always in your best interest to adhere to regulations.
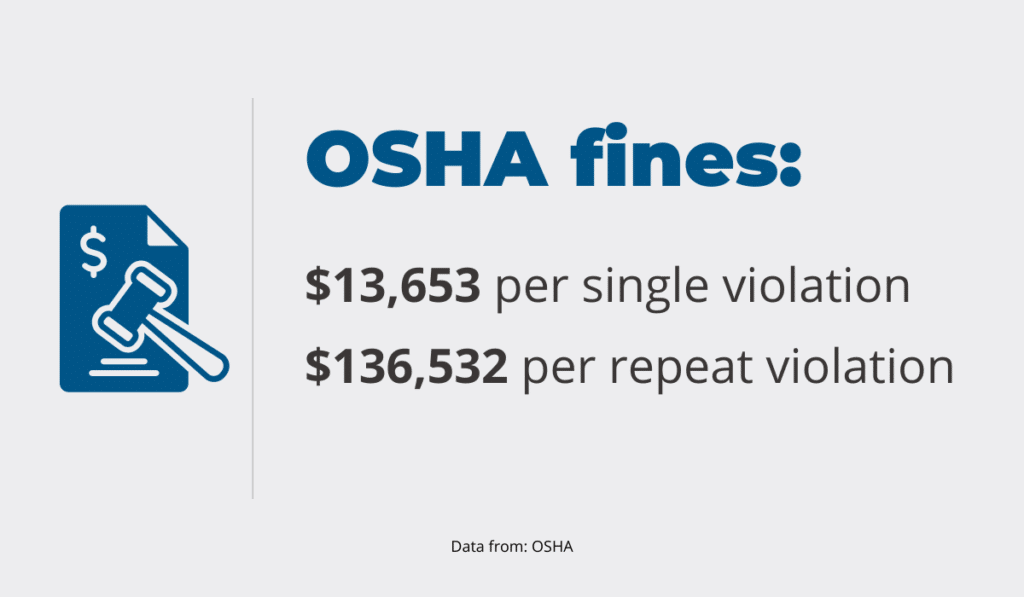
OSHA considers preventive maintenance, which includes regularly scheduled equipment checks, a hazard control measure, since it eliminates possible safety issues before they cause a serious malfunction or an injury.
Your maintenance team will notice any possible problems on time, protecting your field employees and anyone else on your construction site.
For example, OSHA guidelines require you to perform regular machinery checks, make a note of the results, and keep records of them for a set amount of time.
In case of an accident or injury, this data serves to prove your commitment to safety at the construction site.
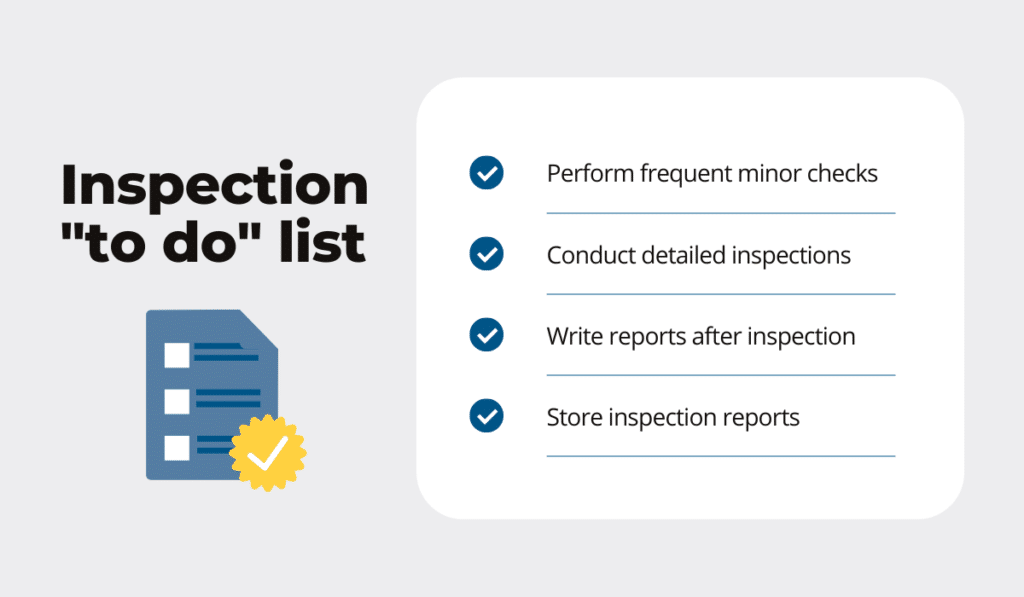
As an employer in the construction industry, you should invest in a good hazard prevention program based on OSHA’s requirements and any other state or federal regulations that apply to your construction company.
Once you know what you’re supposed to do, make those things a part of your company’s standards to ensure you don’t miss anything.
Lack of Spare Parts
Even the best maintenance team in the world won’t be able to fix certain problems on your machinery without quality replacement parts. Because of this, you should order those parts in advance and store them safely until your team needs them.
Of course, doing this for every part of every machine you own is unsustainable, as it would mean wasting money and space. However, specific equipment pieces are made to last longer than others and can often outlast the equipment itself.
That’s where your service team can help.
Regular maintenance can help your team keep track of equipment parts that are likely to give out soon and make a note in their report so the procurement team can order the part in a timely manner.
That way, when the workers need to replace the piece, you’ll already have it.
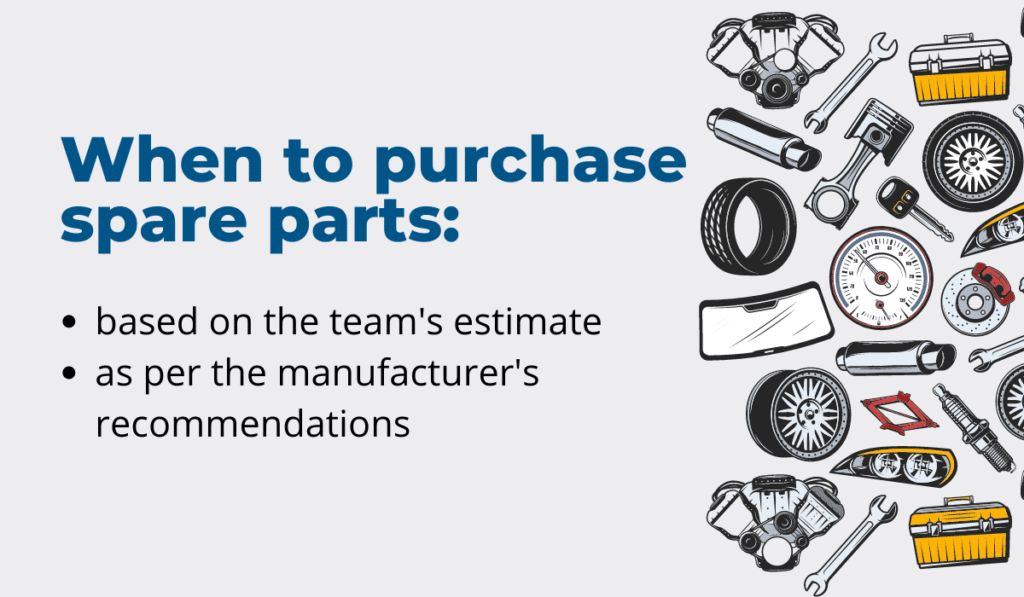
Manufacturer’s manuals are also a great source of knowledge about your equipment and spare parts. They can let you know when you can expect to replace specific pieces, so you can stock up on them on time.
Another great way to stay on top of spare parts is to have an inventory list of all your assets, including the spare pieces.
If the list is a paper one, it’s as good as nonexistent when you’re trying to locate the piece you need. Instead, you should opt for a cloud-based inventory database.
A database like that can help you keep track of where the equipment and spare parts that you own are, and understand how many parts you need to purchase.
Frequency of Unplanned Downtime
Construction companies struggle with delays and cost overruns caused by unplanned downtime, which challenges maintenance teams.
McKinsey reports that almost all (98%) construction projects are finished later than expected or require more resources than initially planned.
What’s even more concerning is that this type of downtime costs US industries $50 million annually, with equipment breakdowns accounting for 42% of this amount.
Since both cost overruns and delays are affected by unexpected downtime, you should invest in proper maintenance to eliminate them.
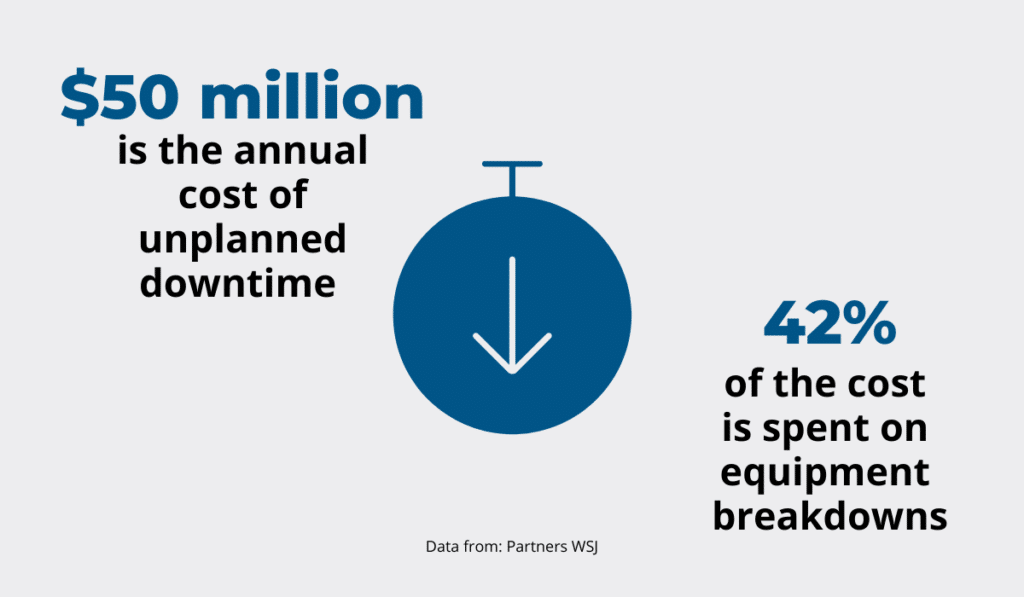
It is a good idea to combine different types of maintenance to avoid running your equipment to the point of failure.
While preventive maintenance includes investing in more frequent servicing, so you can plan for downtime when it suits you, the need for corrective maintenance often arises unexpectedly during use.
It is these types of issues that cause all those project delays and extra costs. Therefore, waiting for your equipment to break down before you service it is not a sustainable strategy.
While that approach, also known as run-to-failure or reactive maintenance, works for smaller, easily replaceable, and cheap items, consistently relying on it can end up costing you 10x more than preventative maintenance.
So, how can you tackle maintenance effectively?
First, you need to train your team on proper machine use and servicing.
The 2019 Plant Engineering survey reports that 38% of maintenance specialists plan to decrease their unplanned downtime hours by improving training and holding it more frequently.
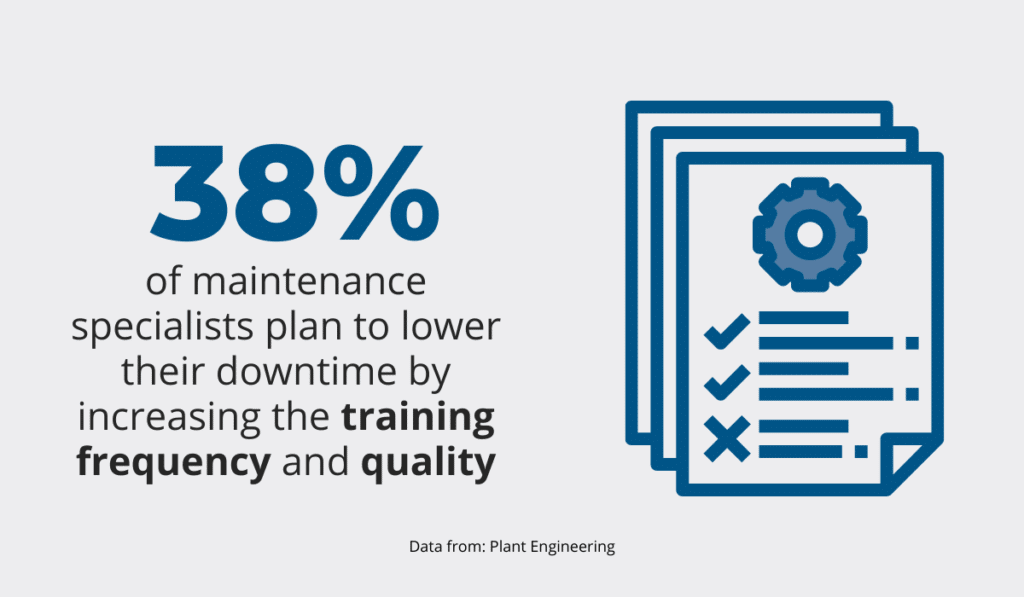
Try to do the same and see how better and more frequent training affects your maintenance.
You should see a spike in issue reports from field employees who will learn to recognize the warning signs for a variety of issues before they escalate.
Moreover, you should also notice an increase in your maintenance team’s efficiency. This will ultimately lead to a decrease in unplanned downtime and related costs.
Employee Training
The better and more frequent your training, the more successful your team. After all, quality training ensures that your employees know what they’re doing and that they do it safely.
As already mentioned, industry specialists are aware of the importance of continuous skills development: 32% of them named lack of it as a key challenge to improving maintenance at their facility.
They also listed “operator error” and “lack of proper training” among the most common causes of unplanned downtime.
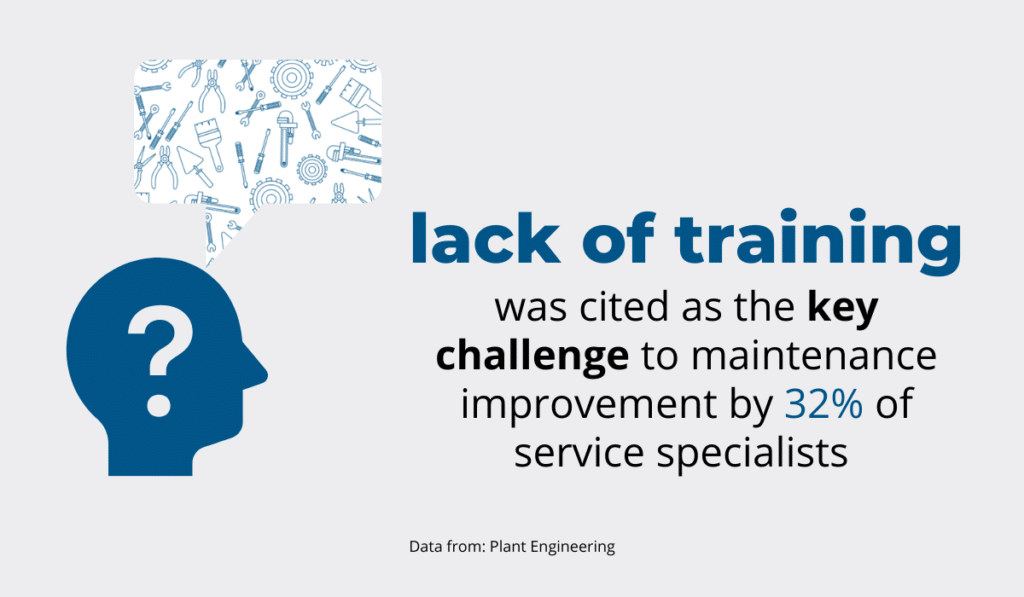
Moreover, safety is one of the biggest concerns in construction, since construction workers have a 71% higher chance of getting injured at work.
Nevertheless, it doesn’t take much effort to take the necessary precautions, and it also saves you money. In fact, according to OSHA, you can save from $4 to $6 for every dollar you invest in safety programs.
When it comes to operator training, you need to stress the importance of the proper use of equipment.
The operators have to understand how the machine behaves when everything is okay. That way, as soon as an issue arises, they can notice it and alert your maintenance team, so that they don’t use and damage the equipment that has a problem.
A less trained or experienced employee probably won’t notice the warning signs and will keep using the equipment until it fails.
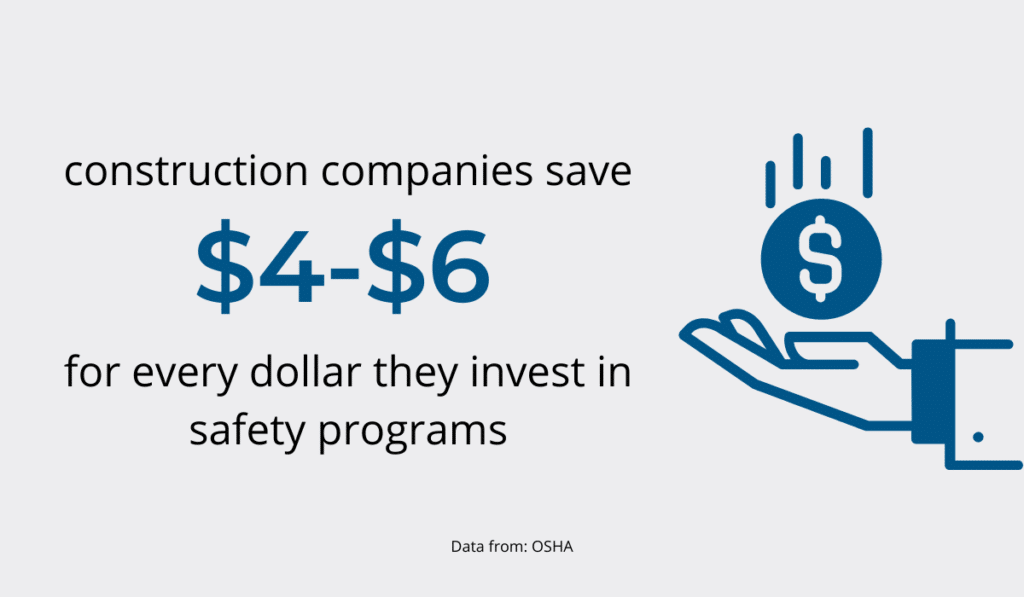
Your service staff also has to be well-trained to conduct effective equipment maintenance. If you’re worried about potential knowledge gaps, create service checklists for each piece or type of equipment, at least.
Doing this guarantees that each maintenance specialist goes through each step of the maintenance process and ensures that the machine is safe to use.
Your most experienced and knowledgeable team members should handle the more complicated, detailed checks, especially if they’re trying to identify the underlying cause of an issue.
Maintenance Budgets
Construction companies tend to overspend on maintenance, especially considering its often poor results.
Companies often direct anywhere between 5 and 10% of their budget into maintenance every year, which should be more than enough to keep things running smoothly.
More precisely, 35% of maintenance specialists report that their companies spend more than 10% of their operating budgets on maintenance, while 34% spend between 5% and 10%.
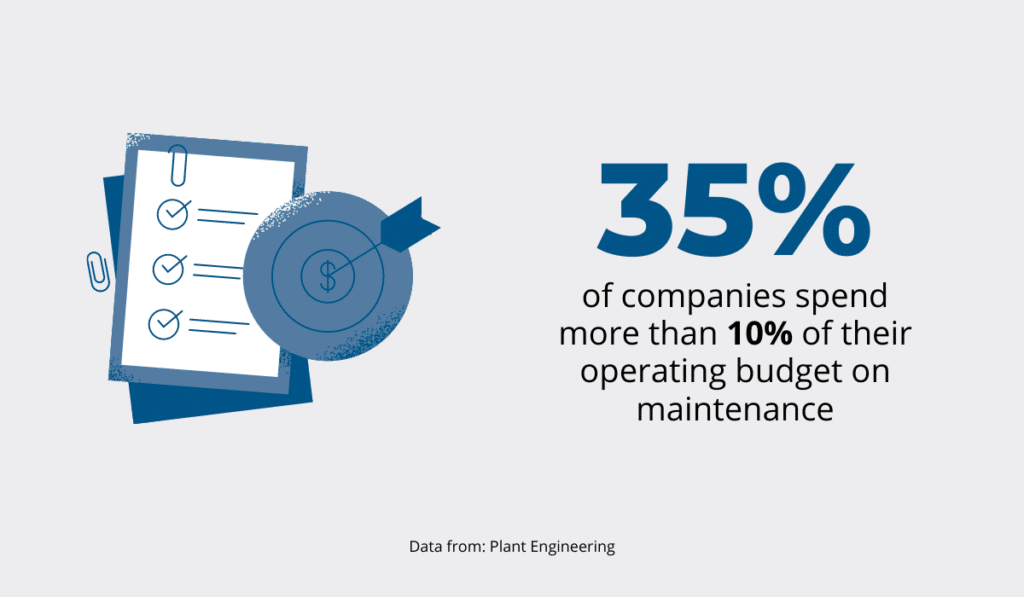
In other words, businesses often spend more than enough on maintenance. However, problems arise when poor servicing leads to increased costs.
We have previously stated that 42% of the unplanned downtime costs can be attributed to equipment breakdowns, which means poor issue recognition and maintenance cost US businesses $21 million a year.
If you’re trying to reduce your maintenance costs, focus on quality training. A study found that training your team and offering refreshment training dramatically decreases maintenance costs and the need for costly corrective maintenance.
Clearly, many businesses make the mistake of not training the team at all or offering coaching only during onboarding.
Your team should have the opportunity to constantly learn and grow since honing their skills benefits your equipment and, therefore, your budget.
Managing Priorities
One of the chief struggles that your maintenance team faces is prioritizing service tasks.
Usually, the teams handle the requests as they come, which is in part due to outdated systems.
After all, construction and agriculture are the least technologically developed sectors in the US, so it’s not really a surprise they still rely on paper documentation or save maintenance work orders in spreadsheets.
Both options ensure you have written evidence of a problem and the solution, but they don’t help you organize or prioritize.
However, if a construction company turns to technology to deal with this problem, they will have a much easier time organizing their tasks and assigning priorities.
Let’s say your company starts using a cloud-based solution that allows you to save any equipment data and attach corresponding documentation. In that case, you’d always know where to look for the information you need on your machinery.
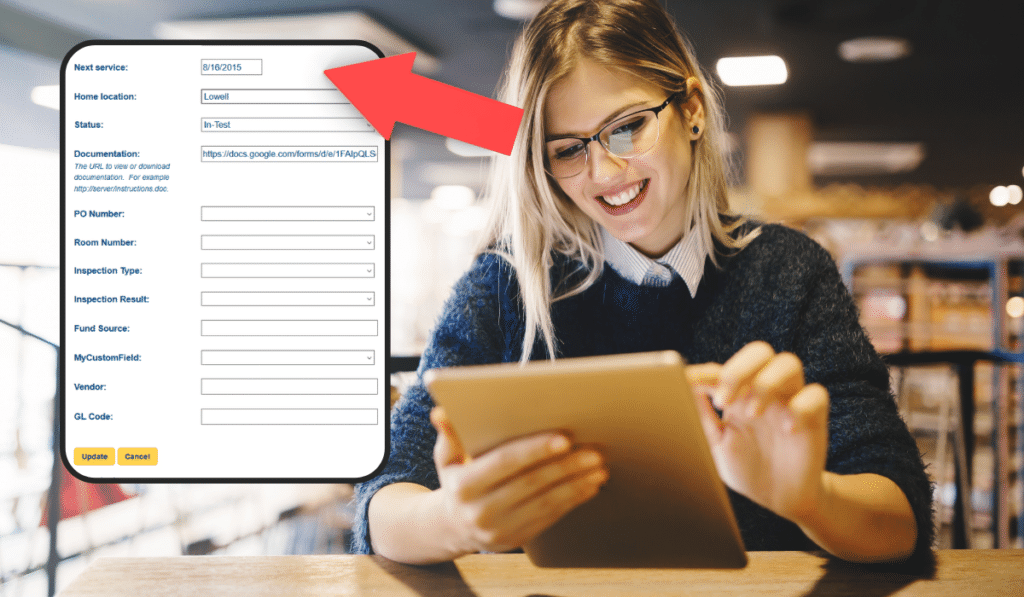
This information can include whatever you find necessary, which means you can add maintenance records, list current issues, and attach the manufacturer’s manuals, as well as any other data that can help the team in the field and the maintenance staff.
Software helps you centralize all your equipment-related documentation, meaning you have a place to save all your pending maintenance work orders.
Equipment tracking solutions will let your operators add comments on the item’s current condition and change the status to “in need of maintenance”, if necessary.
Then, you can appoint the maintenance manager or shift leader to go through these work orders and prioritize them.
Points that can help you with prioritizing include:
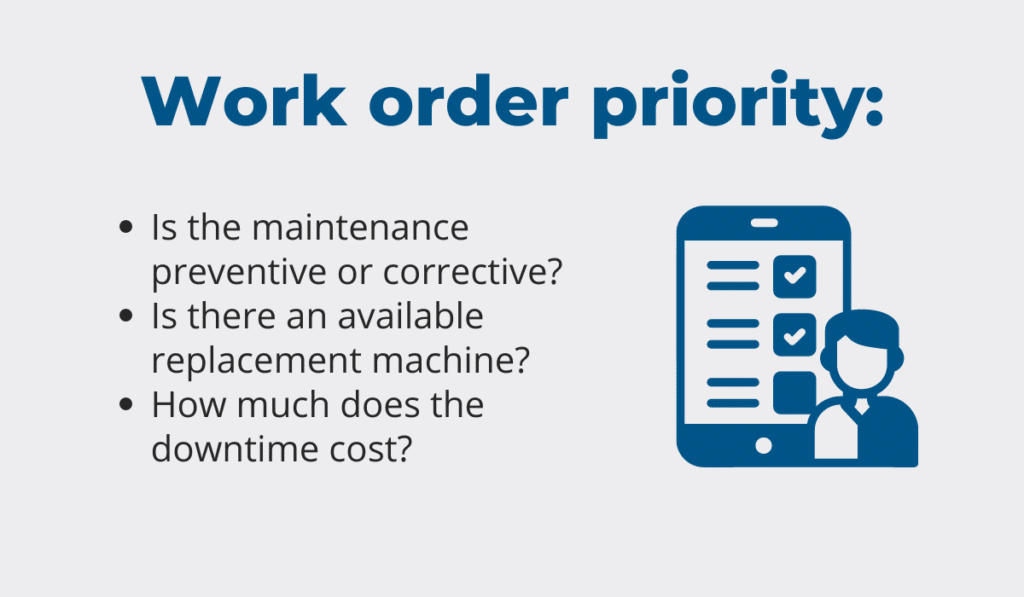
When scheduling, corrective maintenance takes precedence over the preventive type, because if a problem occurs, you can no longer use the affected equipment safely.
There’s also a high possibility that the machinery broke down during use, which usually happens during a project, so getting the machine back up and running is crucial for meeting your goals on time.
Of course, if you can replace the piece of equipment with its equivalent and it happens to be free, the repair isn’t as urgent as it would be for the equipment you can’t easily replace.
Lastly, consider how much a day of downtime costs for the machines in need of service—the more expensive the downtime, the more urgent the repair.
Data Capturing
You can’t know if your maintenance plan is effective without the right documentation.
If you fail to keep records of past maintenance sessions and issues, you can’t leverage any previous experiences or insights.
Sadly, this isn’t new in the construction industry. Research has found that 96% of all data collected in construction goes unused.
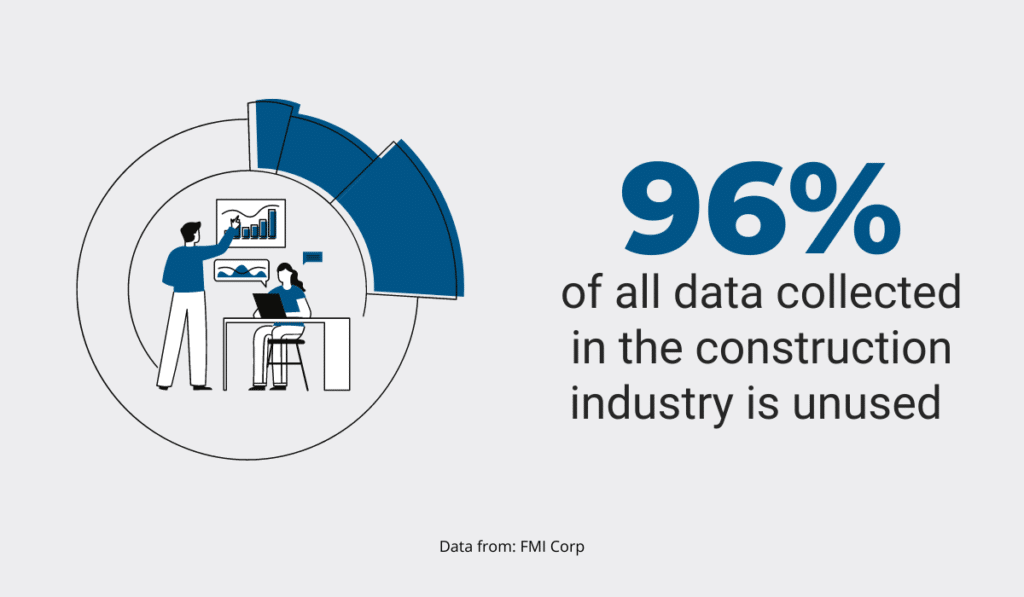
Without that information, you will have difficulty determining which brands work best for you, which machines you should replace instead of fix, or which maintenance team member has a bad track record.
Consequently, you’ll keep doing things the same way, and you’ll end up with the same unsatisfactory results.
Besides, if you keep previous records of breakdowns and checks, you’ll have an easier time determining the optimal time for an inspection. Basing inspection frequency on service records is the best way to go about preventive maintenance.
All of this is why construction professionals have been turning to cloud-based software, which allows them easy access to all the data they need. According to Dropbox, 75% of construction companies nowadays store their data in the cloud.
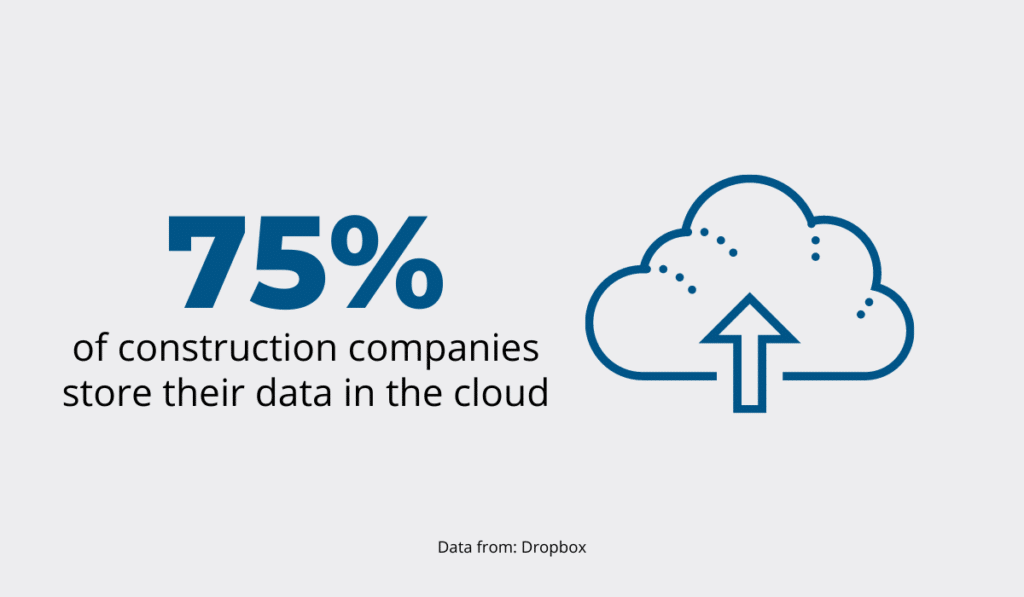
Cloud-based software lets you save all equipment information in the same place, making it easy to look up the machine’s whereabouts, status, previous maintenance records, as well as any future service dates.
Instead of having to shuffle through papers to find the exact piece of information you need, you can simply type it in the search bar and see the results almost immediately.
Conclusion
Construction maintenance involves many challenges, ranging from staying compliant with the industry’s standards, to having enough resources and staying within budget.
However, you can overcome most of the challenges mentioned in this article with the help of technology.
A simple equipment-tracking solution will go a long way for anyone who wants to organize their maintenance documentation, including records and work orders.
Centralizing your equipment data helps you stay on track with your fleet and, therefore, its maintenance.