As business processes become more complex by the day, so does proper equipment inventory management. However, if you lack the means to track your equipment in real-time (or close to it), that can be a really daunting task.
On the other hand, neglecting inventory management will result in extra costs and operating inefficiencies, and perhaps even lead to injuries.
To prevent that, here are the best practices to follow for successful equipment inventory management.
In this article...
Keep the Complete Inventory up to Date
Smooth-running equipment requires proper maintenance—which, in turn, requires a budget. And how can you competently allocate budget resources if you don’t know what equipment you have and what its current condition is?
A complete, up-to-date equipment inventory is a major advantage for your business.
Starting from the top, it provides you with everything you need to know about the equipment you own.
For instance, budgeting resources for maintenance moves from the realm of guesswork to the domain of more objective assessment.
In other words, knowing exactly what your organization owns results in more realistic budget calculations, thus improving your overall planning process.
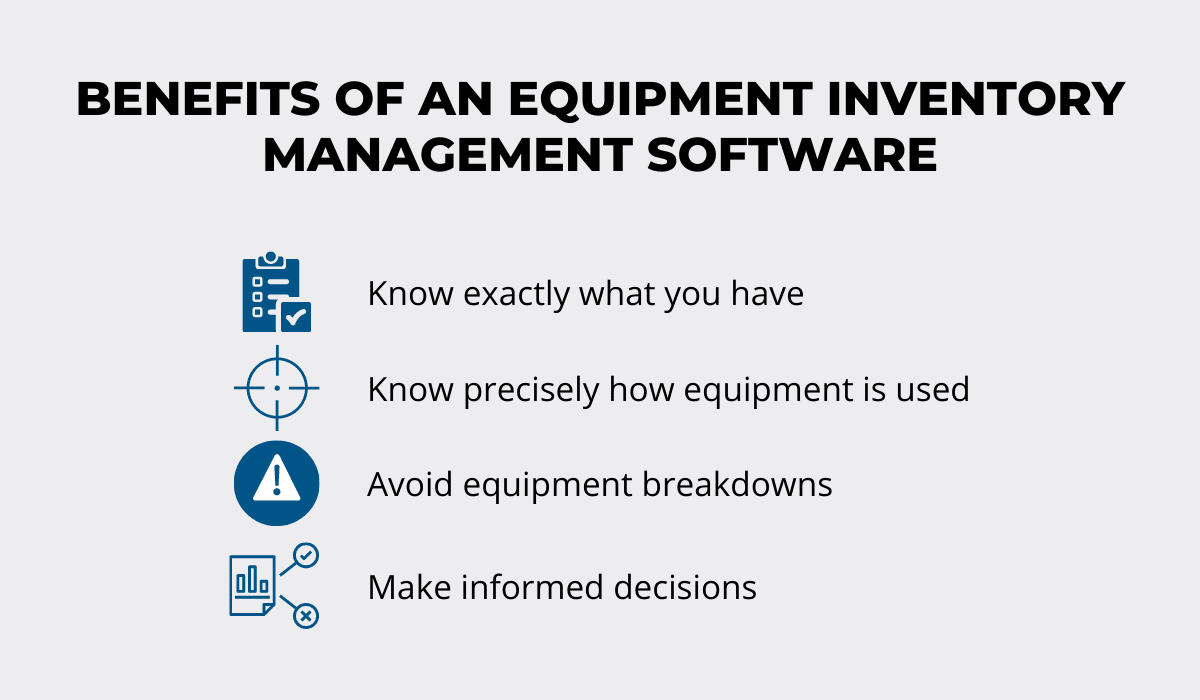
Furthermore, having an equipment inventory management system enables users to report any equipment-related issues more quickly and accurately.
The system then efficiently directs the reported issues to relevant decision-makers, thus speeding up approval and execution processes.
However, there’s some work to be done before your business can reap the above benefits.
To gain an in-depth insight into your company’s equipment, it’s first important to perform an inventory audit of all the gear your company owns. This includes that old copier no one is using anymore.
When doing the initial top-to-bottom audit, you should first decide what information you want to collect (and track from now on) for every piece of equipment.
Such information should answer at least these basic questions:
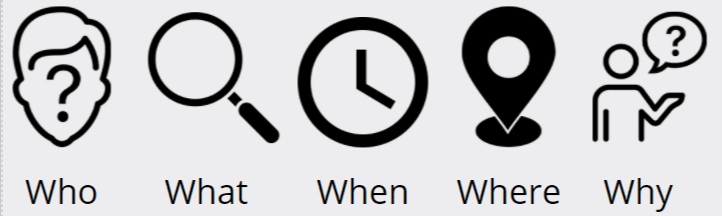
Let’s look into each of them in more detail.
Who owns the equipment?
If you’re a solo player, the answer is clear. But if your company has departments, it should be clear who is accountable if, for instance, equipment gets lost. This can also include the owner info on rented equipment, if any.
What’s the equipment make, model and serial number?
This question is self-explanatory. This information will be used for subsequent equipment tracking, among other things.
When will the equipment warranty expire?
This information is crucial for equipment management. When warranty information is systematically stored, it provides invaluable data that can be used to improve your organization’s planning and maintenance practices. Of course, this includes the purchase date, warranty start and expiry date, and the expected lifespan of the equipment.
You can find this information on the warranty card or certificate.
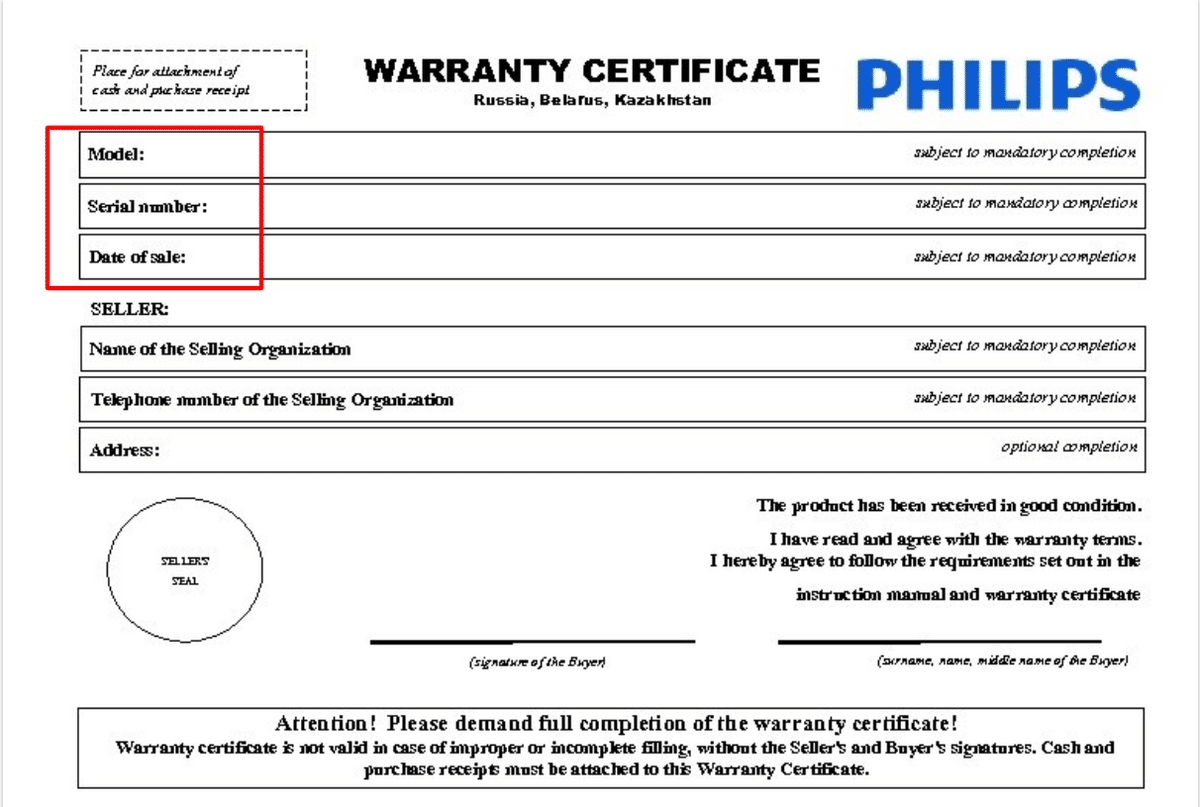
The warranty card or certificate is usually included with the purchase of the tool.
Where is the equipment currently located?
Another self-explanatory question. How could you use an item if you don’t know where it is?
Why (and how) is the equipment used?
This includes its intended purpose, whether it’s repurposed for other uses and other relevant information.
Once you have all this information in a system, you just need to schedule periodic reviews at intervals that best suit your organization.
Armed with such knowledge, keeping the complete inventory up to date will be an easy process that can be used to streamline all other equipment-related processes, thus boosting your organization’s overall productivity.
Use Inventory Management Software
Assuming you know what equipment you have, you need to make sure you can update and use all this valuable information. This is best achieved by using inventory management software.
Why? Because it gives you access to equipment details in one centralized place.
What’s more, it enables you to inspect the lifecycle of assets and discover hidden synergies. Or finally pinpoint those recurring issues you’ve been noticing.
More specifically, inventory management software will provide data on:
- the frequency of use
- the type of use
- the maintenance intervals
Here’s an example of an equipment maintenance calendar.
This is a wise practice to implement to give you a clear idea of when and how often your equipment needs to be maintained, so that you can foresee downtime for your tools and ensure your tools are kept in optimal condition.
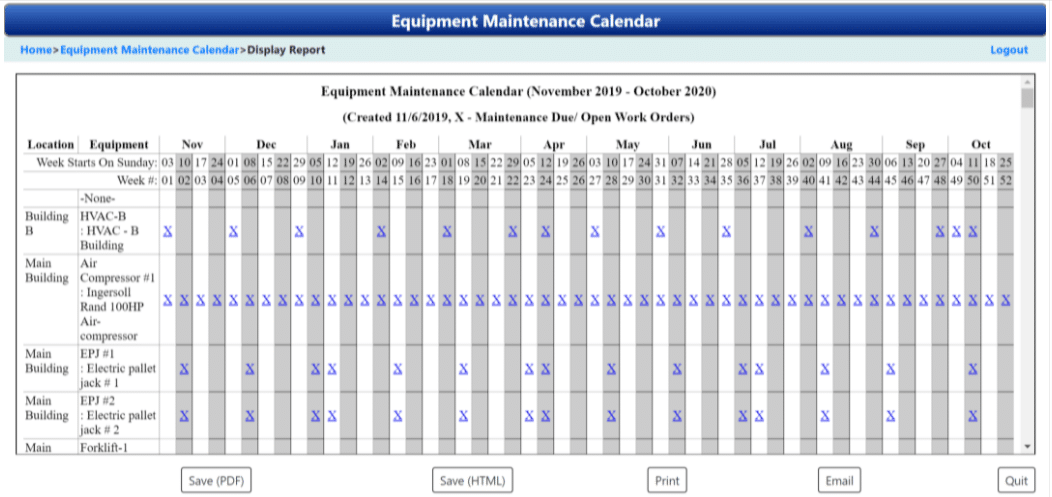
Further, inventory management software will significantly reduce the amount of time usually spent on finding where a particular piece of equipment is located.
If not found, more time was spent figuring out who has it and when it will be available again.
That’s because this type of software logs each individual user so you always know who had the tool last.
It will also improve safety. Since it contains safety-related information about all your company’s equipment, such as tests, inspections, and upgrades, it’s much easier for all involved to establish whether all safety standards are met.
Finally, it will provide an organized system in which companies can track all their assets and store all relevant equipment details, including its location, status, and value.
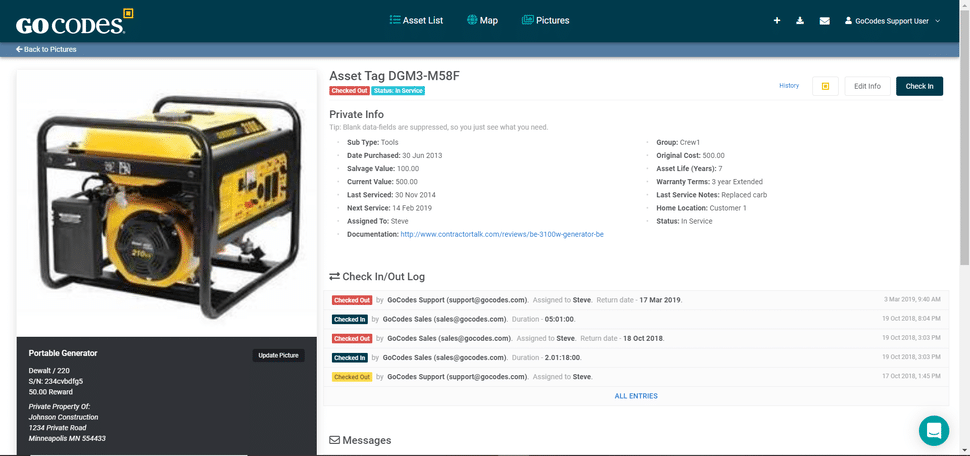
That said, the still ongoing pandemic and growing climate changes have propelled the use of such software to new heights. Faced with social distancing and remote work, companies started using it to track their equipment remotely.
As for climate action, companies deploy inventory management software to better track the use of their resources, thus moving towards sustainability.
To quote Paul Miller, principal analyst at Forrester Research, a company specialized in technology research and advisory services:
“I think the big interest at the moment is around better uses of finite resources.”
To use their equipment more sustainably, companies first need to know where it is and how it’s used.
This process starts with auditing your equipment and tagging it.
Among many available solutions, there is tagging equipment with barcodes and using special scanners to track them.
Additionally, more advanced solutions have replaced barcodes with QR code tags, and costly scanners with a smartphone app.
One such solution, which is both easy-to-use and affordable, is our asset and inventory tracking software, GoCodes Asset Tracking.
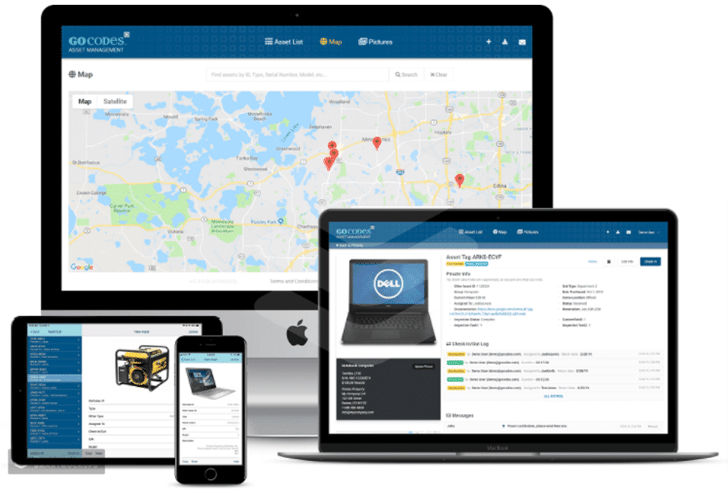
Furthermore, inventory management software can also be used to establish an equipment check-in/check-out system and automate equipment inventory counts.
Like with some other high-value goods, such software can help with equipment maintenance and stock control.
It allows you to set minimum threshold levels according to the equipment or material type, thus automating and streamlining procurement cycles.
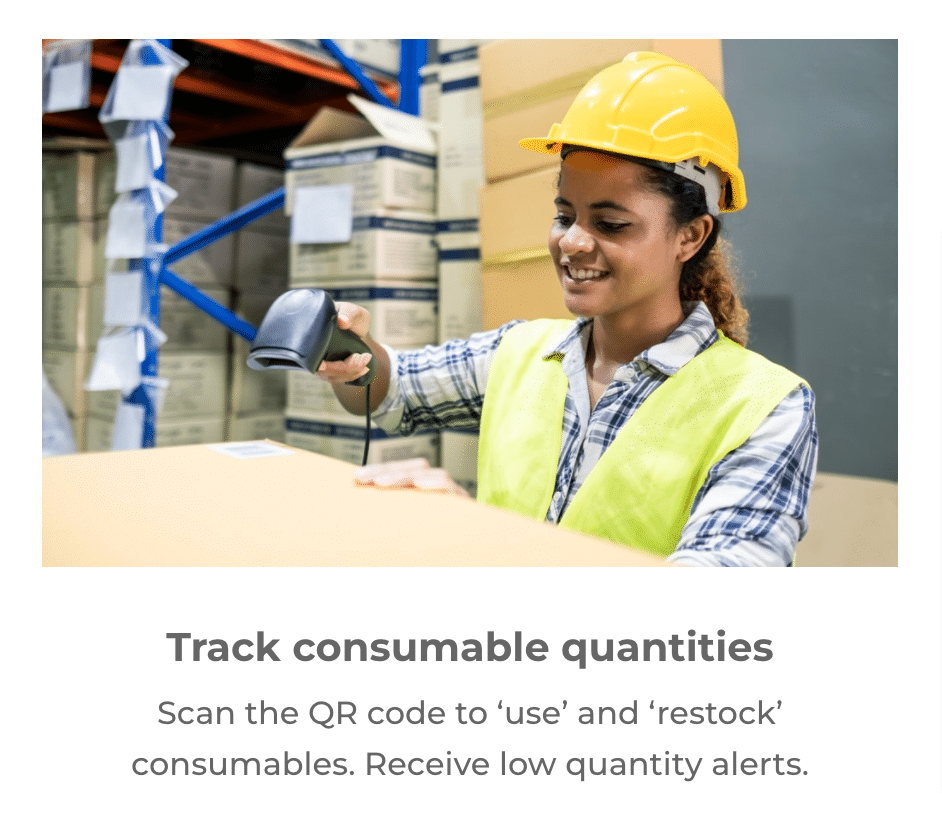
Once that’s done, software will alert you when maintenance is needed, or the stock level is low.
To sum up, inventory management software brings many benefits to your organization, including access to centralized data, monitoring equipment lifecycle, improved time management and safety.
All of these lead to higher productivity.
Note How Equipment Is Used
Knowing how your equipment is used means you can manage its lifecycle and accurately assess its performance over time. This will ultimately result in lower costs and higher productivity across your company.
An ideal equipment management software will track equipment from its purchase to disposal.
This leads to a better understanding of when the time is for replacement, upkeep, and overall maintenance of all your equipment.
When equipment is tracked, it’s easier to schedule preventive maintenance, thus avoiding unnecessary or late servicing, both of which involve excessive costs down the line.
For example, this solution intended for utility companies provides equipment health and performance insights to prevent breakdowns and optimize lifecycle costs.
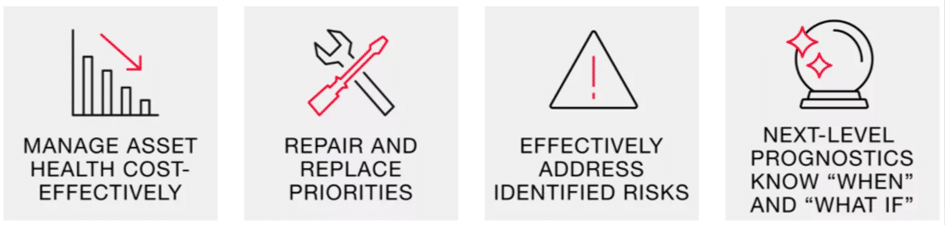
Maybe the biggest advantage of equipment management solutions is that they enable you to analyze how you use your equipment.
Armed with usage data, you can gauge the performance of each piece (and category) of equipment and determine which is most frequently used, which brings the most benefits to your business, and which is slowing down your productivity.
You’ll be able to compare equipment performance at customized time intervals, usually weekly or monthly.
Further, you’ll be able to identify usage trends over time. For instance, this means you’ll have data to determine what happened before a piece of equipment broke down.
For example, tracking devices or data loggers can be attached to equipment to measure their running hours, like in this video.
Such solutions enable you to make better-informed decisions on a series of issues related to equipment usage.
So, having data is important, but how that data is used is critical.
One course of action is to utilize data reports embedded in the software that allows for real-time (or almost real-time) equipment tracking.
Here’s an example of how creating custom reports looks in our solution, GoCodes Asset Tracking.

Such enterprise reporting solutions allow you to customize equipment usage reports according to your needs.
Another advantage of software solutions is that they allow you to send and receive instant equipment status notifications. And this works both ways—operators can notify managers about any issues, while managers can send equipment status changes or updates.
There’s also the ability to assign equipment to individual operators. This is a simple solution for monitoring equipment and promoting accountability.
For example, users can be informed what equipment is assigned to them via a mobile app, thus avoiding confusion when they get to a construction site.
In short, knowing how equipment is used across your organization allows you to cut costs on both ends of the spectrum by making both equipment and people work smarter.
Don’t Forget Equipment Quality Control
Quality control is a critical process for any organization that manufactures products, parts, or components.
But quality control of the equipment used to do so can ensure more reliable and safer operations, which translate into better performance and enhanced productivity.
This is often overlooked when companies are faced with tight budgets or limited personnel. However, it shouldn’t be.
Just think about the cost of replacing an expensive piece of equipment because it wasn’t properly maintained.
Then add the cost of downtime this causes for your staff, which can halt your project for hours, days, or even weeks.
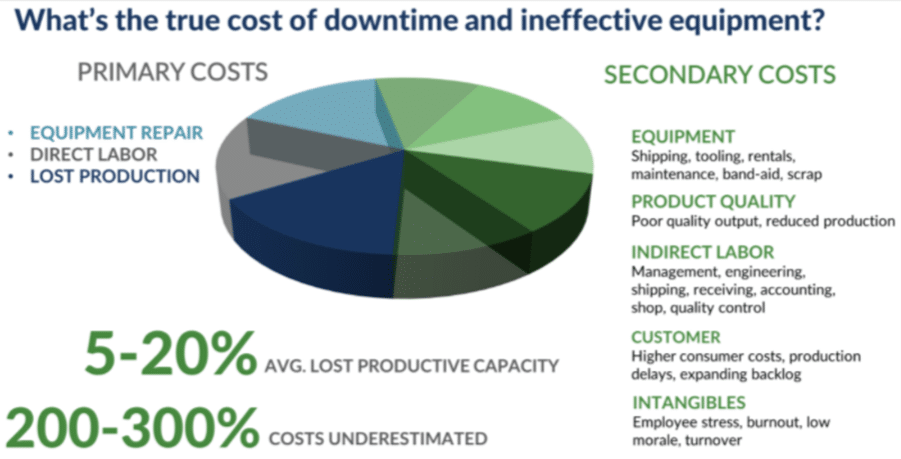
That’s bad enough but in the worst-case scenario, poorly maintained equipment can even cause injuries ranging from minor to fatal.
It’s a simple fact: reliable equipment improves worker safety.
And equipment maintenance goes hand in hand with its reliability.
That’s why it is crucial for companies to see that these elements—maintenance, reliability, and safety—are intrinsically connected.
Where equipment quality control is concerned, one of the typically utilized “tools” is the P-F curve, which is used to pinpoint when it’s best to adopt a proactive approach in order to avoid reactive maintenance. It looks like this.
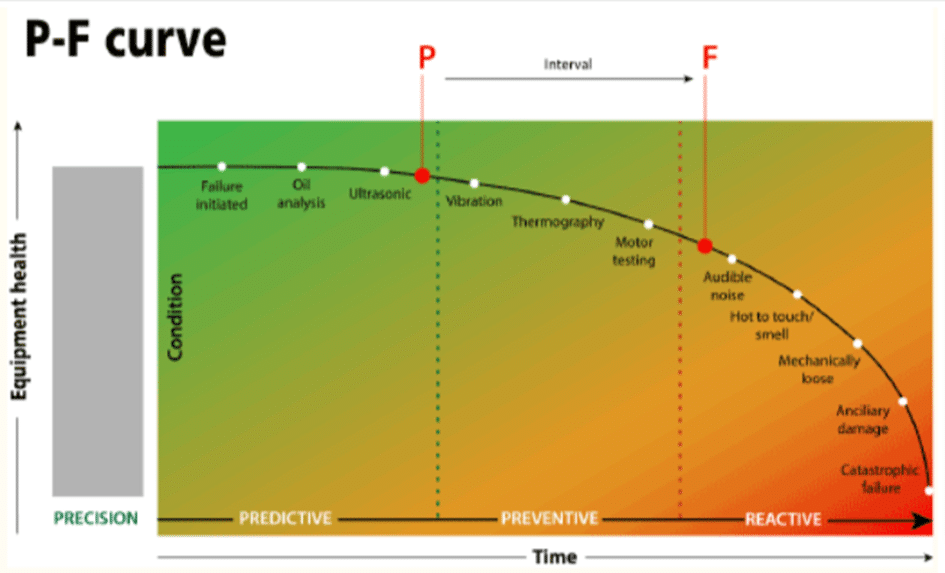
The interval between P (potential failure) and F (functional failure) shows which period in the equipment lifecycle should be used to schedule preventive maintenance, thus avoiding extra costs and preventing injuries.
Poorly maintained equipment can also increase the company’s cost of goods sold (COGS) and reduce its gross income and the value of its inventory presented in financial statements.
So, how do we ensure that equipment quality control is diligently applied?
One way is to assign this task to a specific person who then performs regular quality control checks (weekly, monthly, or other). It’s also a good idea to have built-in maintenance cycles.
For example, maintenance or calibration checks can be assigned before equipment is checked out or returned.
If you want to learn more about calibration management, you can do so here.
One last thing. Always keep in mind that the costs incurred by using equipment all the way to the point of failure far outweigh the ongoing costs of a preventive maintenance program.
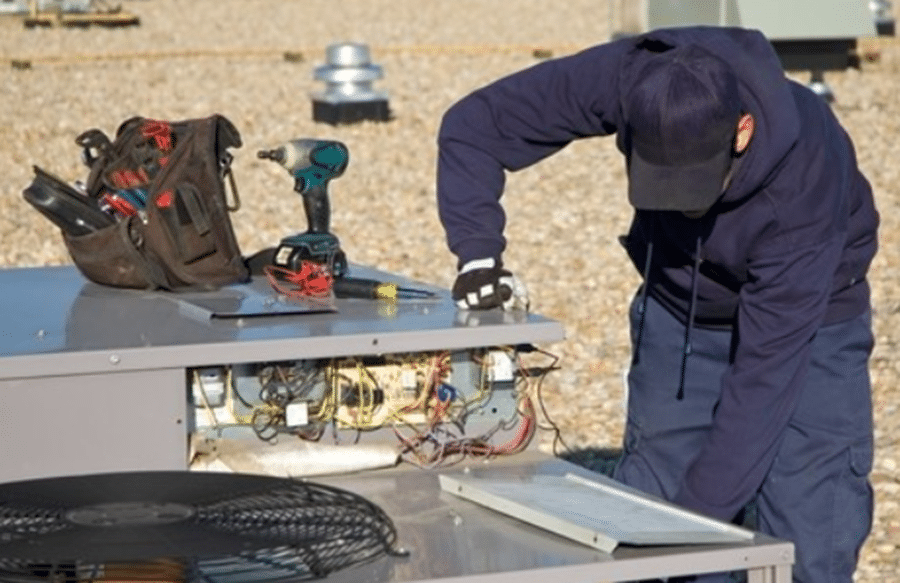
In the words of David Auton, a senior reliability engineering director at Cushman & Wakefield:
“Run-to-fail or repair easily costs somewhere between 3 and 10 times as much as a good maintenance program”.
So, don’t forget equipment quality control because it definitely saves money, and it can also save lives.
Conclusion
As we’ve reached the end, it’s important to remember these best practices.
Having a complete and updated inventory of your equipment embedded in an appropriate inventory management software will inform you how equipment is used and let you apply the right quality control measures.
Following these practices will ensure that your business is safely and sustainably using equipment and thriving in the process.