Equipment inspections may not be the most exciting part of running a construction business, but they’re incredibly important.
Regularly inspecting construction equipment can save a company significant amounts of money, ensure better company efficiency, and eventually contribute to client satisfaction.
In this article, we’ll cover the many benefits of conducting regular equipment inspections, as well as explain what they should cover and how often they should be conducted.
We’ll also give you some advice on some best practices to implement when tackling equipment inspections.
Let’s dive in.
In this article...
Why Is Inspecting Equipment Important?
In the construction industry, your entire business hinges on your equipment, so it goes without saying that regular inspections are important.
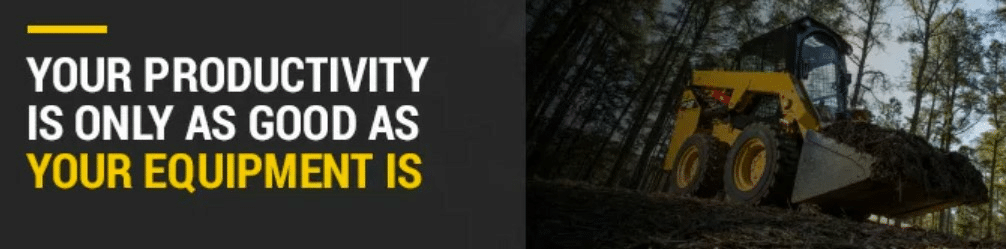
Inspections contribute to increased equipment productivity, reduced risk of equipment failure, prolonged equipment lifespan, and lower risk of workplace injuries.
In the following sections, we’ll take a closer look at each of these benefits.
Increased Equipment Productivity
Regular inspections help you ensure that your equipment is as productive as possible, since, by tracking work orders, you can gather data that allows you to monitor key performance indicators (KPIs) and generate accurate reports.
To be able to stay on top of this information, construction companies need a good asset tracking solution.
Systems such as GoCodes Asset Tracking can quickly streamline and instantly update your inspection information, as well as store indisposable operators’ manuals within an easy-to-scan QR code.
The information obtained in this way allows stakeholders to make data-based decisions that will improve processes and the company’s efficiency, which will, in turn, improve its long-term fiscal stability.
Reduced Risk of Equipment Failure
Construction equipment failure, whether a temporary malfunction or a total breakdown, places timelines and milestones at risk.
It also costs money in the form of renting temporary equipment, paying for employee overtime to catch up, paying out milestone fines, or rushing to purchase replacement equipment instead of concluding research to make the most of your asset’s life span.
With regular inspections, small defects in equipment are noticed before they have a chance to escalate and cause full breakdowns that can lead to downtime, resulting in losses for the company.
Prolonged Equipment Lifespan
Regular inspections will help your team to detect problems and worn parts early, so that repairs can be done quickly and reliably.
Caring for your heavy equipment in this way helps ensure its longevity, so the equipment is more likely to enjoy an extended lifespan before replacement is necessary.
This helps your company reduce spending in the long run.
Lower Risk of Workplace Injuries
The hazards on a construction equipment site are many, and equipment failure that happens without warning is one of them.
If a piece of equipment malfunctions suddenly, it may injure operators, contractors or bystanders, which can have devastating consequences for your company, ranging from failed inspections to employee sick days and even expensive lawsuits.
However, regular inspections minimize the chances of such occurrences, which protects your employees and your company.
What Should the Equipment Inspection Cover?
There are many different types of construction equipment, all performing different tasks and boasting different characteristics, which determine what the maintenance team should focus on when conducting inspections.
Some of these characteristics include the intensity of weight, vibration or amount of off-road usage that a specific piece of equipment is subjected to.
It’s best to consult the asset’s manufacturer for information about not only what you should inspect, but which red flags to look for.
Here are some items that should be examined in an inspection:
- Window glass
- Tire treads
- Cracks in attachments (buckets, etc.)
- Undercarriage
- Lights
- Breaks
- Fan belts
- Attachment points
- Battery
- Mirrors
- Seat belts
- Gauges
- Joints
- Fluid levels
Some are surprised when they see the long list of inspection points that heavy equipment requires.
However, each item is important and essential to maintaining the safety for you and your crew.
Taking inspections seriously will lessen the chances of a frustrating breakdown and will help to ensure that your equipment stays with your company as long as it’s projected to, if not longer.
When Should You Inspect Your Equipment?
Inspection should vary based on the tasks your construction equipment is designed for and how frequently the equipment is used.
For example, a dump truck that spends almost all of its time outside in harsh weather and is subjected to extreme temperature variations should probably undergo inspections more often than, for example, a refrigerator in the employee break room.
It might seem inefficient to spend time every shift or every month on inspections when your team is eager to take on their assigned tasks for the day.
However, construction equipment almost always represents a large investment of company time and money.
It is worth spending some time ensuring the machine is in good health and does not require minor fixes, as these tiny cracks and chips might represent a large and expensive repair if left unattended.
OSHA (Occupational Safety and Health Administration) suggests certain guidelines for construction assets.
For example, OSHA stipulates that each piece of heavy machinery must pass inspection every time it is used.
Below is an example of a company offering a service inspection in addition to a regular oil change.
Since this machine is offline while the oil change is completed, this is a good time to ask for checks on such important components as belts, air filters, and fluid levels:
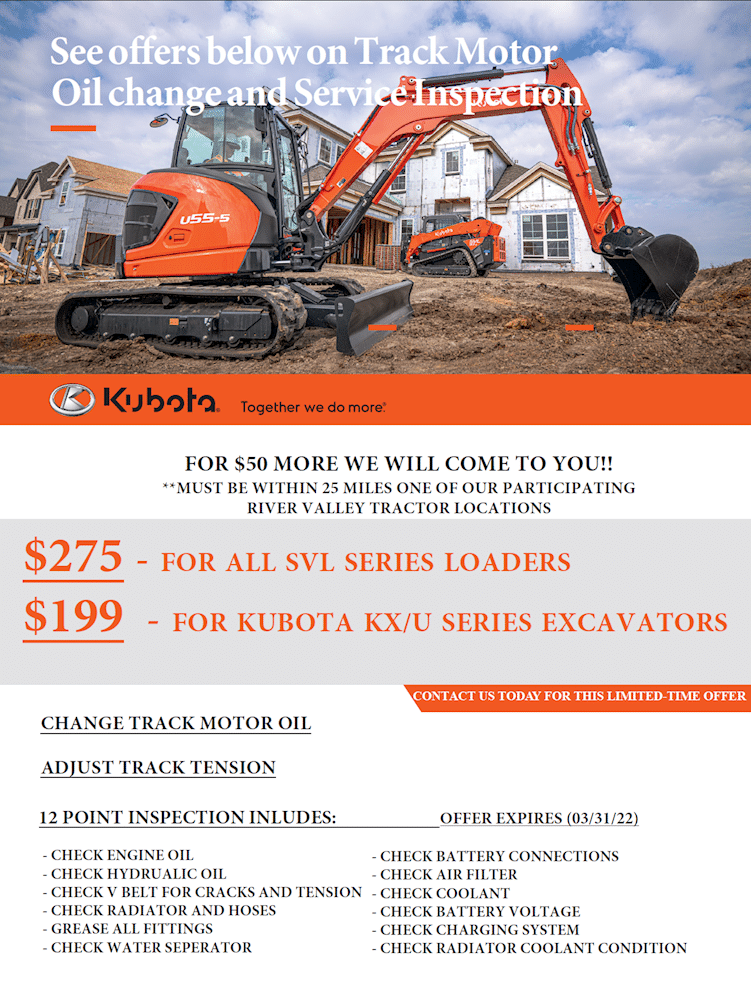
Inspections are so important that some construction company owners consider asking third parties to cast a fresh pair of eyes over their valuable assets.
This is because sometimes, when the same machinery is inspected by the same parties over and over, potential problems can be overlooked.
Equipment inspections should come in many forms and happen at different intervals.
Conducting an inspection can take place at the start of every shift, on a monthly basis, or as the original manufacturer suggests by other means– for example, mileage, work hours, or number of jobs.
The most important aspect of the “when” question is to understand when those responsible for the machine—or those who engineered and manufactured it–suggest that an inspection should take place.
Best Equipment Inspection Practices
Not every company will follow the same inspection practices.
For example, a house construction team doing work near salt water might have a different procedure than that of an oil rig in cold, flat areas.
To make sure the equipment handles these different environments, the best place to go for guidance is operators’ manuals or other sources of information from the manufacturer.
Follow OSHA Inspection Guidelines
Officials from OSHA will appear on your site without warning to conduct an inspection of its own to make sure construction companies are abiding by their rules.
In addition, members of a workforce can ask for an OSHA inspection if they think they are working in unsafe conditions.
The good news is that OSHA provides plenty of information about how to prepare for these visits to your work areas.
As long as these guidelines are already followed, this process shouldn’t disrupt your workflow.
Here are some inspection guidelines from OSHA:
- Encourage employees to share any safety concerns or suggestions
- Quickly attend to safety problems that team members have pointed out, such as frayed fall prevention equipment
- Keep your mandatory safety log up to date
- Designate an employee to speak with inspectors
OSHA can change its guidelines from time to time. It’s a good idea to remain alert for new or updated requirements so that your worksite is up to date.
Create an Equipment Inspection Checklist
It is best to have a construction machinery checklist at hand so that the team member in charge of the inspection will remember to look at each item.
Here is an example of such a checklist:
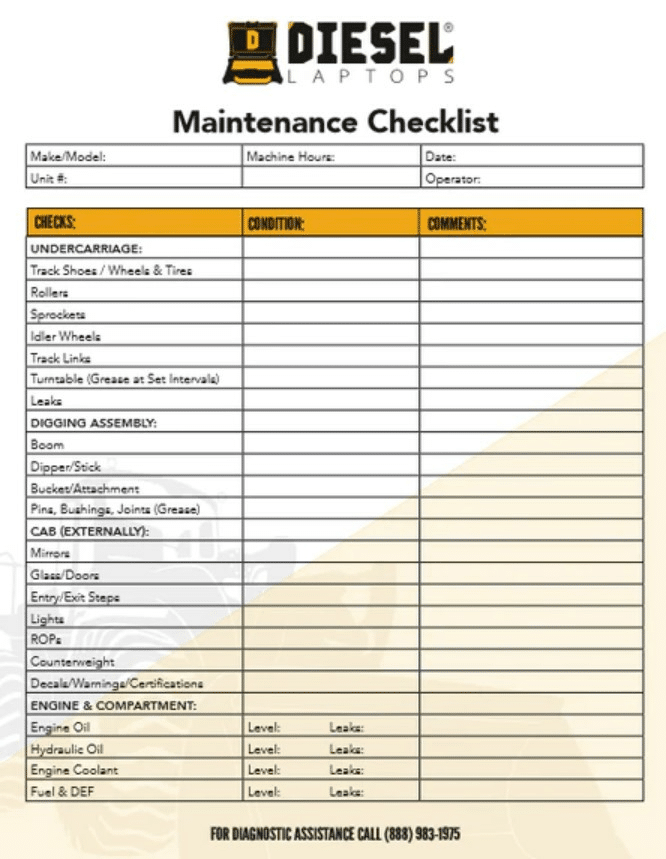
Inspection checklists are not only used on active build sites.
Equipment might also undergo inspection in warehouses, manufacturing, and in tool cages.
These inspections can involve ensuring that the equipment is safely stored or parked, electronic gauges are in good repair, and that logs for mileage, employee use, and the like are up to date and make sense.
When you welcome a new piece of equipment to your fleet, especially one with which you and your operators are not familiar, consider asking a technician from the manufacturer to show you what to watch for during an inspection.
This way, you can know what a healthy machine looks like, and how to tell when repairs, cleaning, or other maintenance action is necessary.
Track Your Equipment Inspections
Checklists are easily stored on an asset tracking system such as GoCodes Asset Tracking.
Its task feature is especially helpful for these situations, as it allows users to create tasks, assign them to maintenance workers and then monitor their completion.
Going as paperless as possible on your site helps to increase efficiency, as well as improve record security and availability.
Shifting your checklists to a company-wide cloud database is a good way to simplify and organize your equipment inspections.
Doing so also enables your team to remotely check inventory, run a diagnostic, or pull information for a report—and your team will thank you for not disturbing them at the work site.
Conclusion
Equipment inspections should exist as a regular part of the work processes on construction sites.
Inspections help to increase productivity, reduce the risk of equipment failure, prolong the asset’s lifespan, lower risk of workplace injuries, and provide a more efficient workflow.
Equipment inspections should cover checks for good electrical connections, evidence of worn parts, warning lights, or such damage as cracks or chips.
Contractors and construction company owners should coordinate with the asset’s manufacturer to know when to inspect and what to look for.
Best practices for equipment inspections include following OSHA guidelines, creating an equipment inspection checklist, tracking each inspection, and using an asset tracking system to systemize the inspection process.
By adhering to these best practices, you ensure that your equipment stays in the best possible condition throughout its life cycle.