Key Takeaways:
- Natural materials and innovative coatings can absorb airborne pollutants and improve indoor air quality.
- Self-tinting glass can reduce a building’s HVAC and lighting energy use by 20%.
- Self-healing concrete incorporates limestone-producing bacteria or microcapsules that automatically seal cracks.
From air-purifying surfaces and self-healing concrete to on-site 3D printing of structural components and even entire buildings, the industry is brimming with innovation.
Driven by technological advancements and growing environmental concerns, new materials and techniques are redefining construction.
In turn, they’re delivering superior efficiency, durability, and sustainability.
Does this sound intriguing?
If so, keep on reading, as we’ll explore six key trends set to shape the future of construction.
Let’s get started!
In this article...
Prioritization of Health and Wellness
Increased awareness of the harmful effects of emissions from indoor construction and finishing materials is driving demand for solutions that enhance air quality and occupant well-being.
In the past, asbestos and lead paint were prized for their superior insulating and durability properties, respectively.
Today, we know that their detrimental effects on health far outweigh any such advantages.
A similar shift is occurring with volatile organic compounds (VOCs), harmful chemicals released by some construction materials and coatings that often persist long after installation.
These chemicals—each with different toxicity and health impacts—are found in both solid and liquid construction products.
You can see the usual suspects in the table below.
Category | Examples of products |
---|---|
Wood products | Plywood, particleboard, medium-density fiberboard (MDF) |
Flooring materials | Vinyl flooring, synthetic carpets |
Insulation materials | Spray foam, fiberglass |
Synthetic fabrics and plastics | Wall coverings, upholstery, various plastics |
Paints and coatings | Oil-based paints, traditional varnishes, wood stains |
Adhesives and sealants | Construction adhesives, contact adhesives, silicone sealants |
Not all of these products contain high VOC concentrations, but certain ones can release significant levels, especially when newly installed.
In fact, research from 2018 highlights that newly constructed or renovated buildings tend to have higher VOC concentrations due to off-gassing from fresh materials.
Here’s a comparison of VOC emission levels in newer versus older buildings.
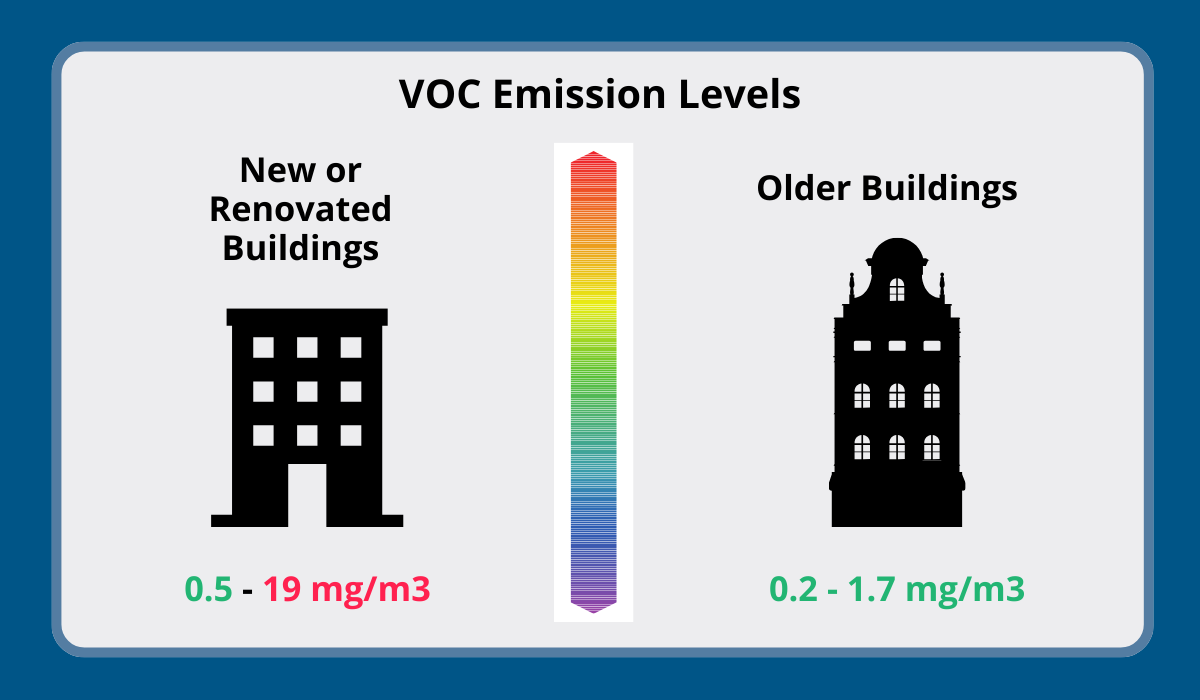
High VOC concentrations in many new buildings can—with prolonged exposure—lead to eye, nose, and throat irritation, headaches, nausea, and even liver, kidney, and central nervous system damage.
Many of these symptoms are reported by those suffering from Sick Building Syndrome (SBS), a condition where VOC emissions are believed to play a significant role.
In response, the U.S. Environmental Protection Agency (EPA) and regulatory bodies in many other countries now recommend that contractors use less harmful materials and finishes in new builds and renovations.
This shift has driven the development of health-promoting solutions, including low-VOC materials, VOC-free paints, antimicrobial surfaces, and air-purifying materials.
For example, natural sheep’s wool has been shown to absorb harmful airborne substances for up to 30 years.
This makes it an excellent indoor air-purifying option when used as an insulation material.
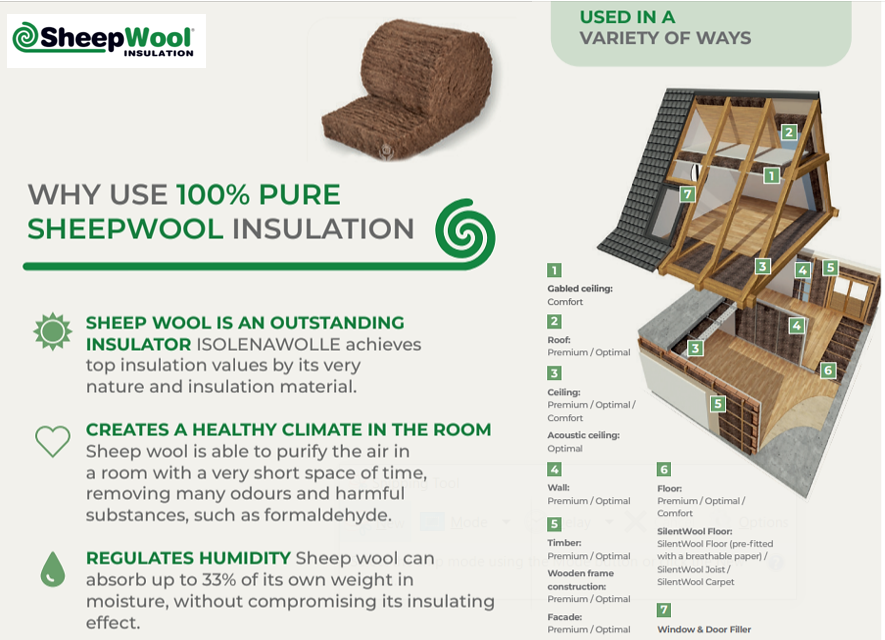
Another natural material that absorbs airborne pollutants is hemp, so construction products and furnishings made out of hemp can contribute to better indoor air quality.
Significant progress has been made in creating VOC-free paints and varnishes, too.
One example is Graphenstone, an organic lime paint infused with graphene—a carbon-based material discovered in 2004 that’s 200 times stronger than steel.
This innovation allows these natural paints to be offered in a full-color palette.
There’s also Airlite: a 100% mineral, VOC-free paint with photocatalytic properties that not only purify the air but also eliminate microbes and viruses from surfaces.
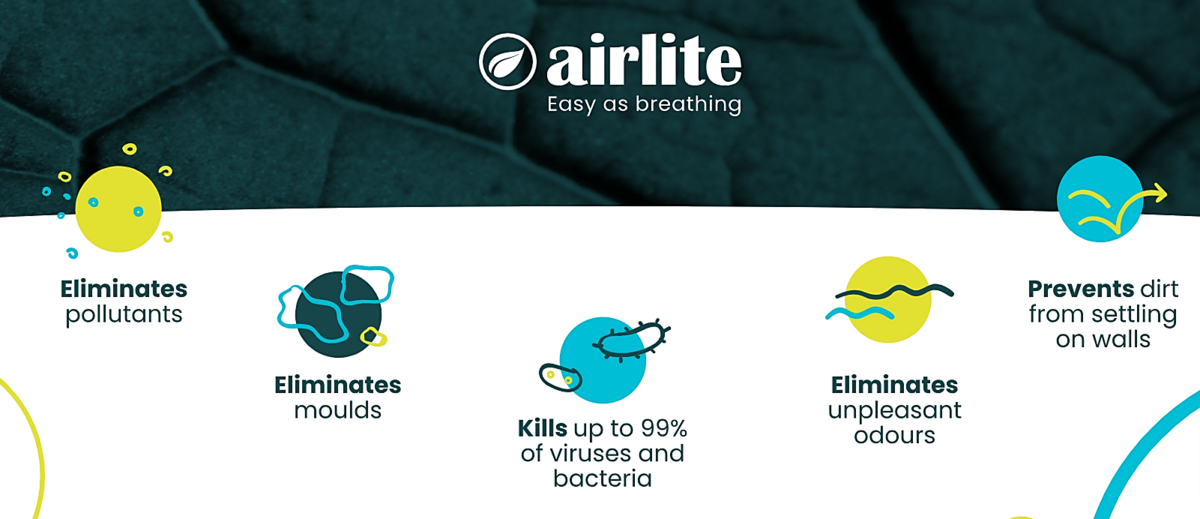
The above claims were verified by three independent studies, confirming that the ionizing effect created by Airlite acts as a natural air purifier and disinfectant.
Together, these examples indicate where the trend of prioritizing health and wellness in building materials is headed.
By blending traditional natural materials with advanced technology, construction companies can create healthier spaces that better support the long-term well-being of future occupants.
Integration of Smart Building Materials
Smart materials are increasingly incorporated into buildings to help regulate temperature and improve energy efficiency.
What unites these diverse materials is their ability to adapt to environmental changes, reducing energy demands in the process.
These materials respond to external stimuli such as changes in temperature, light, pressure, moisture, electrical currents, magnetic fields, or chemical exposure.
A good example of such a smart, energy-saving material is electrochromic glass, commonly known as self-tinting windows.
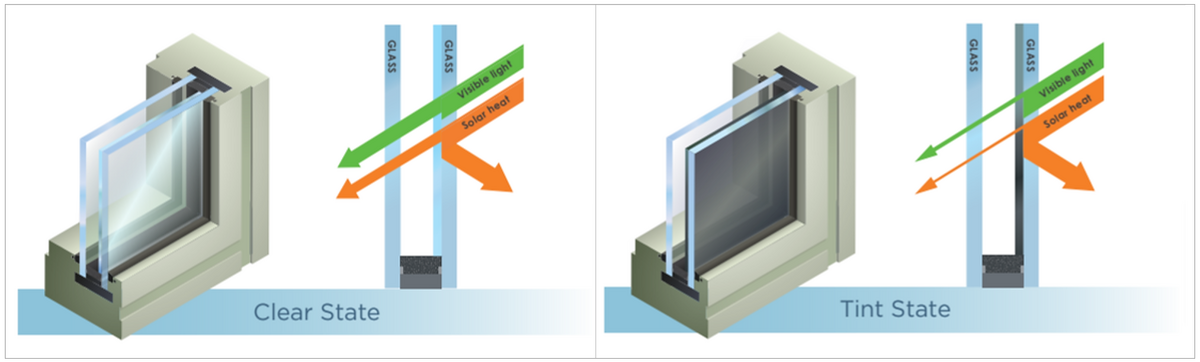
The ability to allow or block sunlight, controlled automatically via smart sensors with user override options, can yield substantial energy savings.
For instance, the View Dynamic Glass shown above can reduce HVAC and lighting electricity use by 20%, translating to a 10% savings in total building energy demand.
And that’s when this glass is compared to already energy-efficient, high-performance Low-E glazing.
Here’s a comparison of those savings, averaged across five cities in different climates, along with the realized building’s cooling peak reduction.
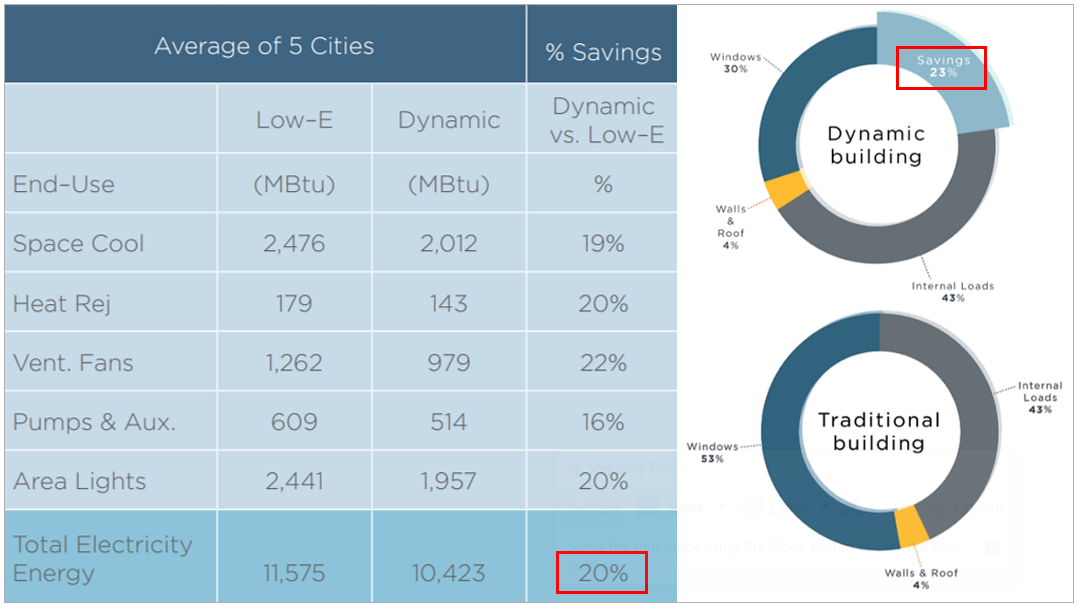
In addition to the 20% electricity savings, the 23% reduction in peak cooling load is significant because it can enable further savings by allowing for smaller HVAC systems.
With a building’s lower maximum cooling capacity requirements, HVAC systems can be sized more efficiently.
This, in turn, may reduce initial installation costs and support the use of alternative, smart cooling solutions.
Electrochromic windows also minimize or even eliminate the need for external shading and internal blinds or curtains, reducing material costs and maintenance.
Another group of smart materials gaining traction is phase change materials (PCMs).
These materials transition between solid and liquid states at specific temperatures, enabling them to store and release thermal energy as needed.
Here’s how this process works.
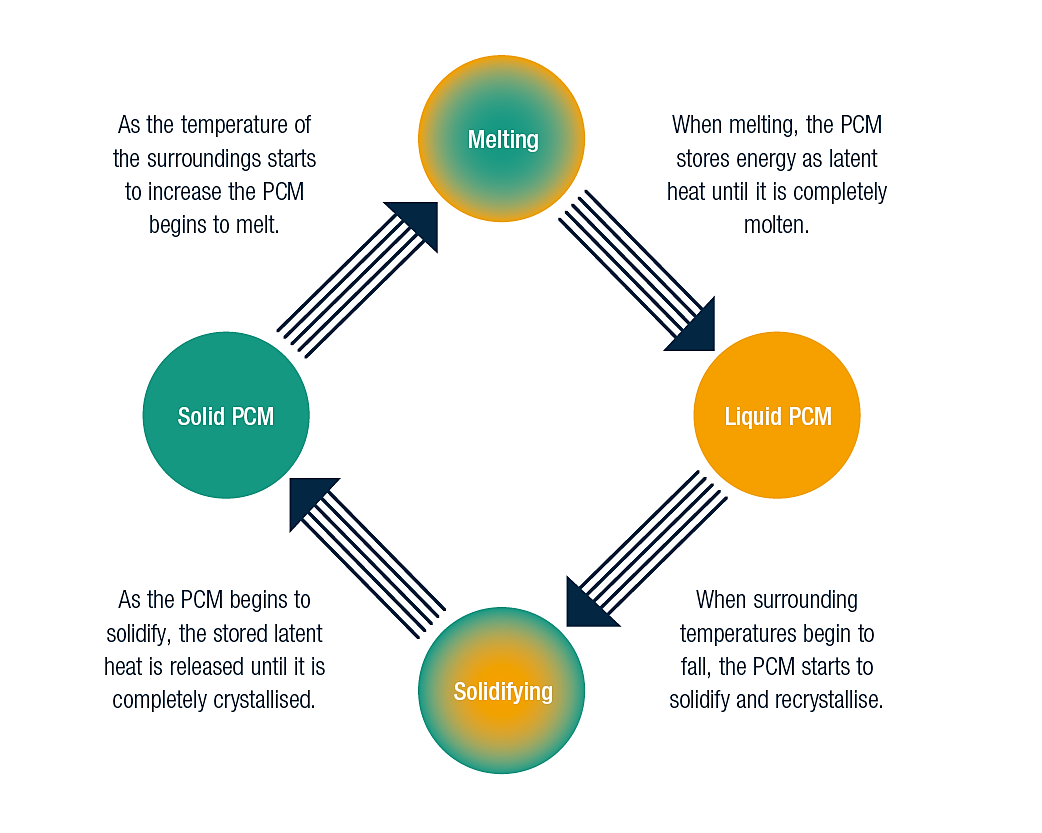
When integrated into a building’s envelope (roof and external walls), PCMs store excess heat during the day and release it at night.
They work similarly in other building components, like internal walls, ceilings, and flooring.
Additionally, PCMs can be incorporated into advanced insulation materials that adapt their thermal resistance based on external temperatures.
In this way, PCMs help stabilize indoor temperatures and reduce the energy required for heating and cooling.
While self-tinting glass and PCMs are among the smart materials making the biggest strides in construction today, they’re not the only options.
To name a few, shape memory alloys (SMAs), self-healing coatings, and thermochromic films also offer impressive adaptive capabilities that support energy efficiency and durability.
For instance, SMAs are alloys that return to their original shape when exposed to temperature changes.
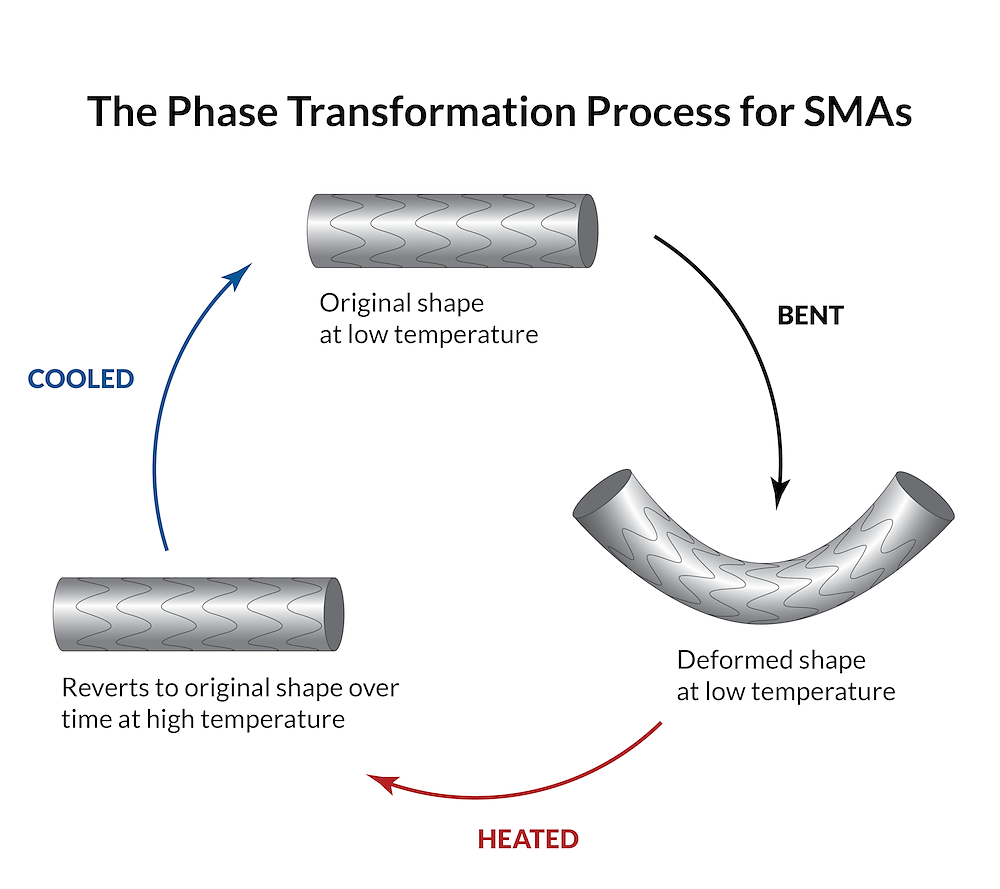
SMAs can be incorporated into building components that adjust their form for improved ventilation or shading based on environmental conditions.
As technology advances, integrating smart building materials is bound to become more widespread, making them increasingly affordable and accessible.
Together, these materials and their versatile applications in construction pave the way toward more adaptive, climate-resilient, and energy-efficient buildings.
Increased Use of Engineered Wood Products
Engineered wood products like cross-laminated timber (CLT) and glue-laminated (glulam) beams are being increasingly used for structural applications.
These products are manufactured by combining natural wood with adhesives and other materials to enhance their strength, stability, and versatility.
Moreover, since engineered wood products can be made from sustainably sourced timber, they represent eco-friendly, even carbon-negative options for construction.
CLT consists of layers of solid-sawn timber boards that are glued together in a crosswise pattern.
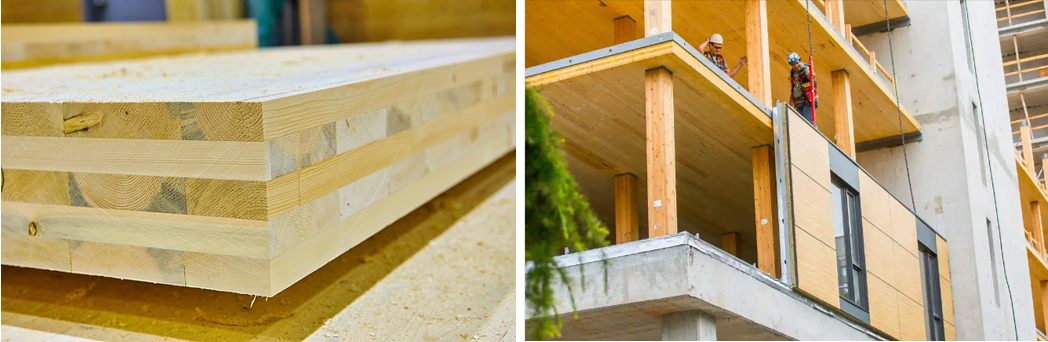
Due to their increased strength and rigidity, CLT products can be used as an alternative to concrete when constructing walls, roofs, ceilings, and floors of a building.
CLT is ideal for off-site prefabrication technologies, where custom-sized panels, including openings and trunking channels, are delivered on-site ready for installation.
Glulam beams are another wood product that can be sourced from sustainable forests.
They’re manufactured by bonding dimensional lumber in layers using durable adhesives.
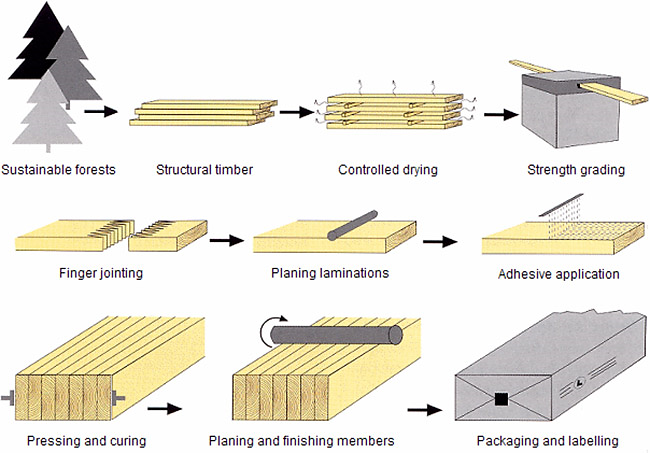
Lighter than traditional wood beams, glulam beams can support heavy loads over long spans.
They’re commonly used as structural elements in commercial buildings, bridges, and large open spaces with extensive spans.
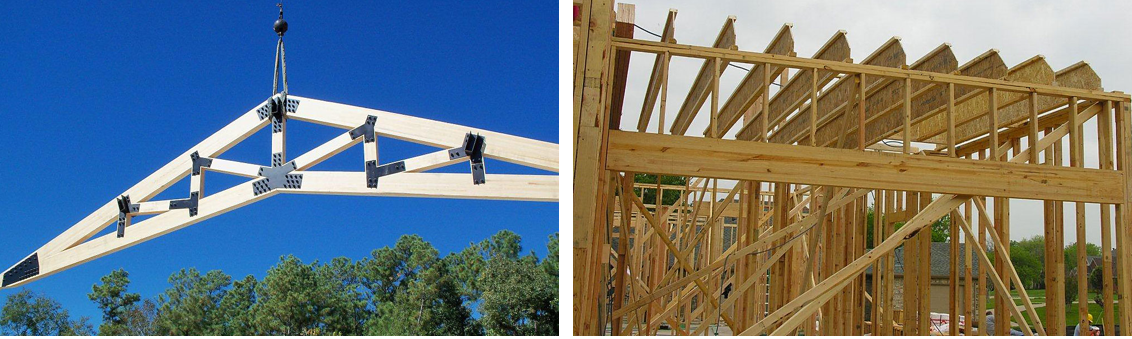
Glulam beams can be manufactured in various sizes and shapes, including curved arches, and provide good fire resistance due to their mass.
Overall, these and other engineered wood products offer a renewable, strong, and lightweight alternative to concrete and steel, with lower embodied carbon and faster construction times.
Reliance on High-Strength Lightweight Materials
However, engineered wood is just one example of a lightweight material that can reduce building weight without compromising structural strength.
This is part of a broader trend of using materials that provide lighter, equally strong alternatives to traditional choices like concrete and steel.
There’s also a range of materials—such as lightweight concrete aggregates—that don’t fully replace conventional materials, but rather make them lighter while maintaining their strength.
These types of materials can:
- reduce foundational requirements,
- lower transportation costs, and
- allow for faster installation.
While generally beneficial, such advantages are especially relevant for high-rise buildings and renovations.
For example, the U.S.-based startup SusMaX repurposes waste from coal combustion to create a lightweight concrete aggregate called SPORA.
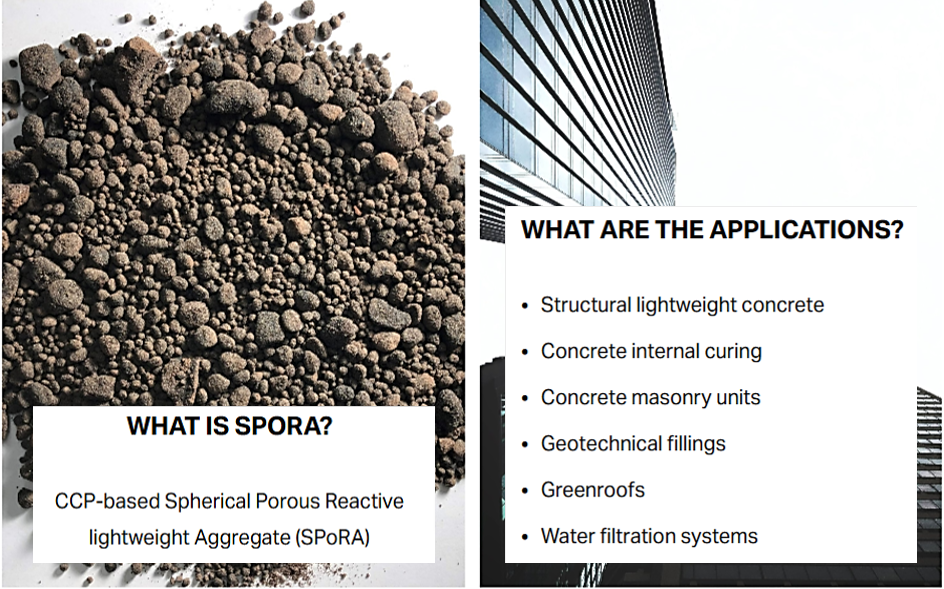
In addition to reducing concrete weight and minimizing environmental impact, SPORA enhances concrete’s service life, workability, and compressive strength.
For instance, in internal curing applications, testing by Schuster Concrete found that adding SPORA increased concrete strength by 15% after 7 days and by 22% after 28 days.
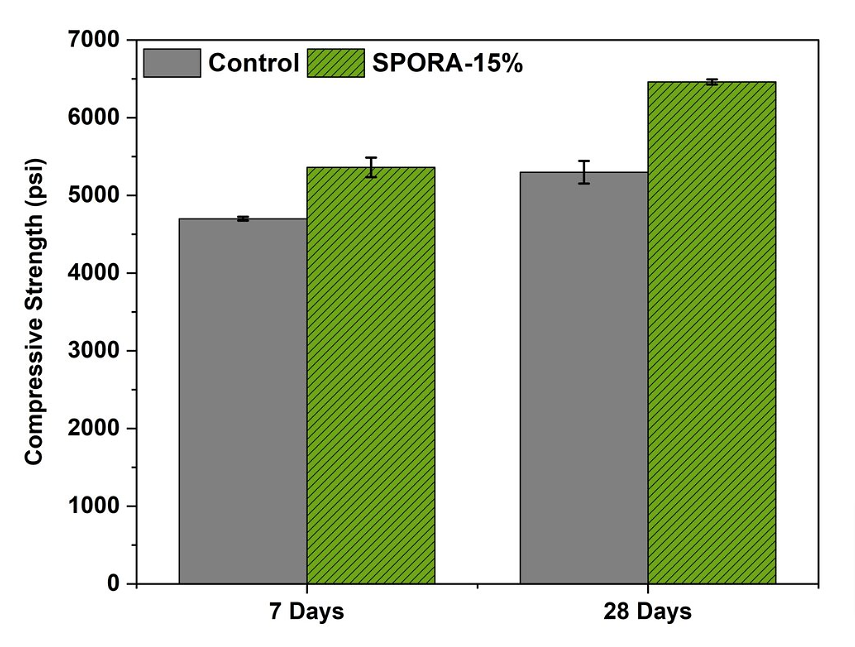
This increase in concrete strength translates to enhanced durability and structural reliability, reducing the need for frequent repairs and increasing resistance to earthquakes.
While the products we described are strong examples, they’re only part of a broader movement in construction toward innovative, lightweight materials and techniques.
Other options, like aerated concrete, advanced composites, and recycled aggregates, also contribute to making buildings lighter and more efficient.
Together, these advancements support faster, more sustainable construction without sacrificing structural integrity, setting a new standard for resilient building practices.
Rise of Concrete Innovations
Advancements in aggregates, and additives, and improved mixing, curing, and placing techniques have led to numerous concrete innovations.
So, products like high-performance concrete (HPC), self-healing concrete, and carbon-cured concrete are transforming traditional concrete use.
These innovations improve durability, reduce maintenance, and help lower the environmental impact of concrete, one of the most widely used materials globally.
Let’s start with the American Concrete Institute’s (ACI) definition of high-performance concrete:
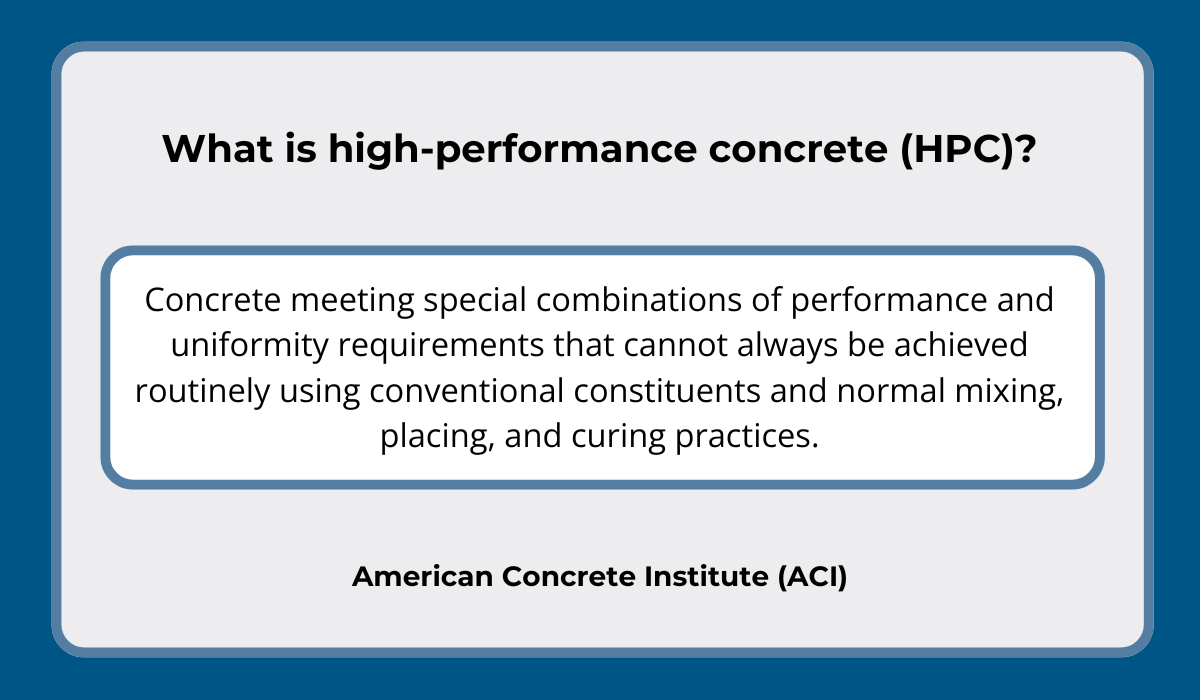
The high performance of HPC is primarily achieved through a combination of material selection, mix design, and specific construction practices.
Various types of HPC are characterized by:
- high compressive strength,
- low water-cement ratio,
- enhanced durability, and
- improved workability.
Due to these qualities, HPC is widely used in the construction of bridges, high-rise buildings, and underground infrastructure such as tunnels and parking garages.
In the future, HPC’s superior properties will further expand with the incorporation of advanced materials and technologies like the PCMs we mentioned, nanomaterials, and self-healing innovations.
On that note, how about cracks in concrete that repair themselves?
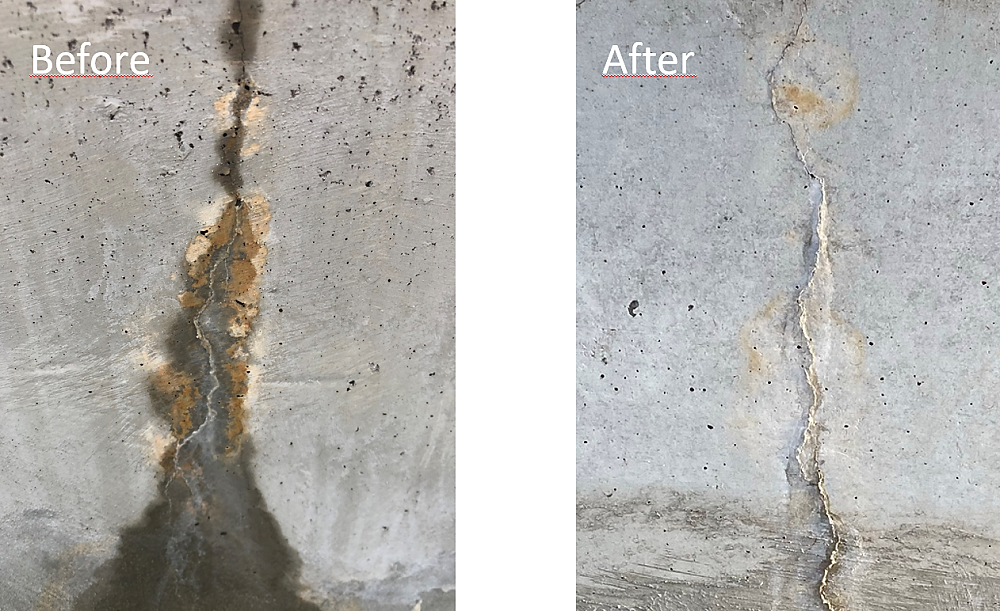
This is achieved by incorporating limestone-producing bacteria into the concrete mix.
When a crack forms and water seeps in, these bacteria are activated and produce limestone that fills the crack.
Another self-healing method involves adding microcapsules containing a healing agent, such as sodium silicate, into the concrete mix.
When a crack appears, it breaks these capsules, releasing the chemicals that react with the concrete to form a repairing gel.
Both of these methods can significantly extend the lifespan of structures and reduce maintenance costs.
As for carbon-cured concrete, this technique not only results in stronger concrete with less cement used but also permanently sequesters CO2 emissions.
Here’s how CarbonCure technology works.
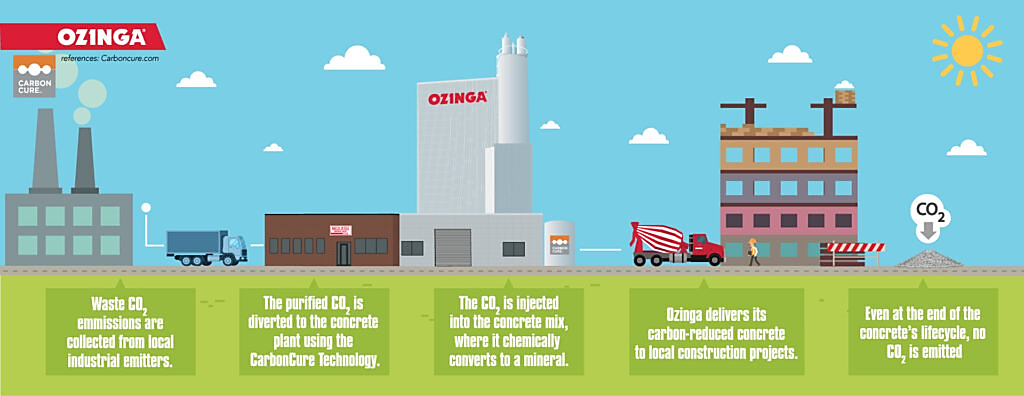
The mineralization process described above leads to improved compressive strength while capturing CO2 emissions and lowering the building’s carbon footprint.
In fact, a medium-sized building constructed with carbon-cured concrete sequesters as much CO2 as a medium forest would in 200 years.
Overall, these concrete innovations demonstrate a significant shift towards more resilient and sustainable construction practices.
By embracing these advancements, the construction industry can enhance structural performance, reduce maintenance costs, and minimize its environmental impact.
Adoption of 3D-Printed Materials
3D printing technology is transforming construction.
How?
By enabling the creation of concrete and other building components either directly on-site or in controlled environments.
The technology works by using modeling software that instructs 3D printers to build objects of various sizes, applying concrete or other materials layer by layer.
This approach allows for the production of components with customized designs and complex geometries that traditional casting methods can’t achieve.
Applications of 3D concrete printing are extensive: from on-site printing and customized facade panels to modular elements, various building components, and even furniture.
You can see some of them outlined below.
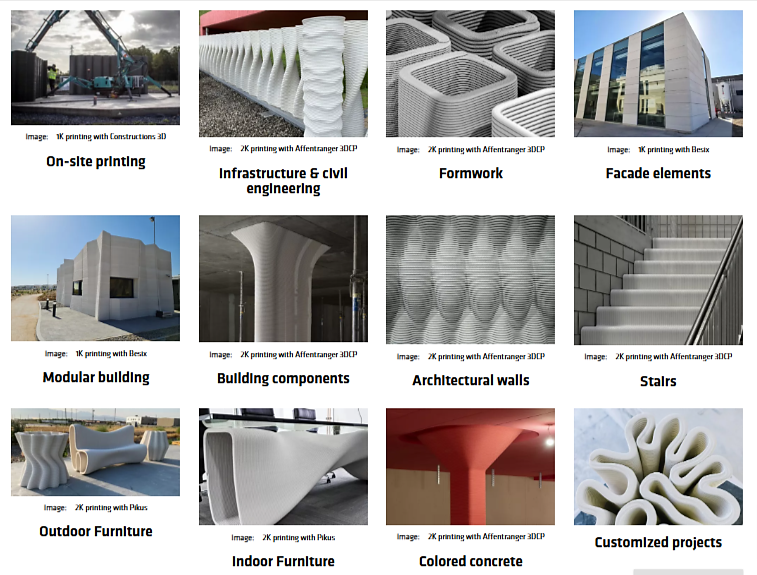
Whether components are printed directly on-site or prefabricated in a factory setting, 3D printing technology:
- offers greater design flexibility,
- minimizes material waste, and
- reduces labor costs.
Not to mention the fact that printing elements on or near the job site can also cut transport expenses and prevent delays associated with shipping.
And with large-scale 3D concrete printers already creating entire buildings—like in the example below—it’s clear that the possibilities for construction applications are expanding rapidly.
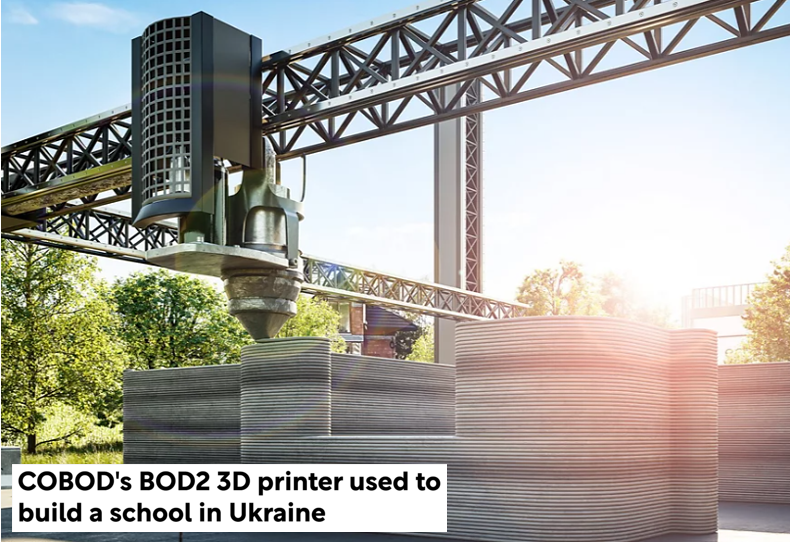
The described limitless potential of 3D printing goes beyond concrete and includes ongoing advances in printing other materials, such as:
- PCM-rich coatings for energy-efficient buildings,
- metals for high-strength structural components, and
- polymers for customized interior elements.
All these innovations are expected to drive the 3D printing construction market from $3.5 billion in 2022 to an impressive $520 billion by 2032, signaling a new era in efficient and sustainable construction.
Conclusion
The material trends outlined in this article signal a transformative shift in construction, offering enhanced health, sustainability, and efficiency.
From air-purifying paint to 3D-printed components, these innovations are, however, not only strengthening building resilience and reducing environmental impact.
They’re also opening new avenues for cost savings and design flexibility.
As these trends continue to evolve, they are set to pave the way for smarter, more sustainable construction that meets the demands of modern architecture and eco-conscious standards.