It’s simple. Construction materials cost money. Construction material management saves it.
Especially now.
Just consider the galloping prices of building materials in the U.S. and the U.K., where they’ve gone up almost 20% and 21.5%, respectively, in 2021 vs. 2020.
In light of this, it becomes clear that having a solid construction material management system is not only a smart idea but also your best option to keep the costs of construction projects down in the current global climate.
The benefits? Numerous and multifaceted.
Here are the five key ones.
In this article...
Data Access and Control
It’s clear that the benefits of having access to and control of your data span much wider than materials management.
For starters, it gives construction managers the opportunity to fine-tune project-specific elements like time (milestones and deadlines), costs, risks and, what is most relevant for this article, resources.
In terms of materials, this means you know exactly how much you need, how much you have and where you have it.
As for your construction business, this means you’re in control, enjoying a bird’s eye view of all processes that allow you to make better decisions.
Once a centralized database of all vital data is established, you can easily track progress across the key stages of the lifecycle of construction materials.
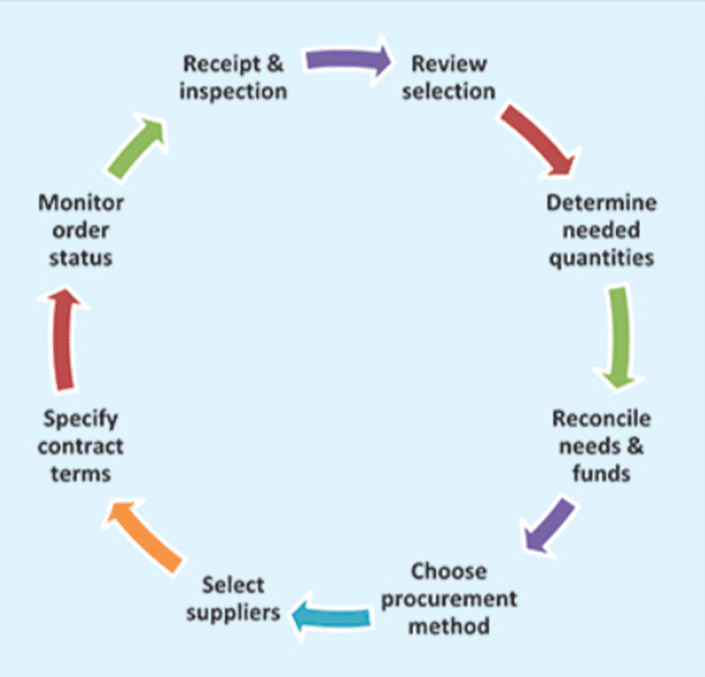
To gain that “aerial” snapshot of all pertinent information, companies use different technological solutions, which have changed the construction industry in recent years.
Way back in 2018, the number of construction managers who were using construction management software to handle their data better was already at 54.2%.
In another survey, 79% of construction managers found that software significantly reduced the time needed to complete the project.
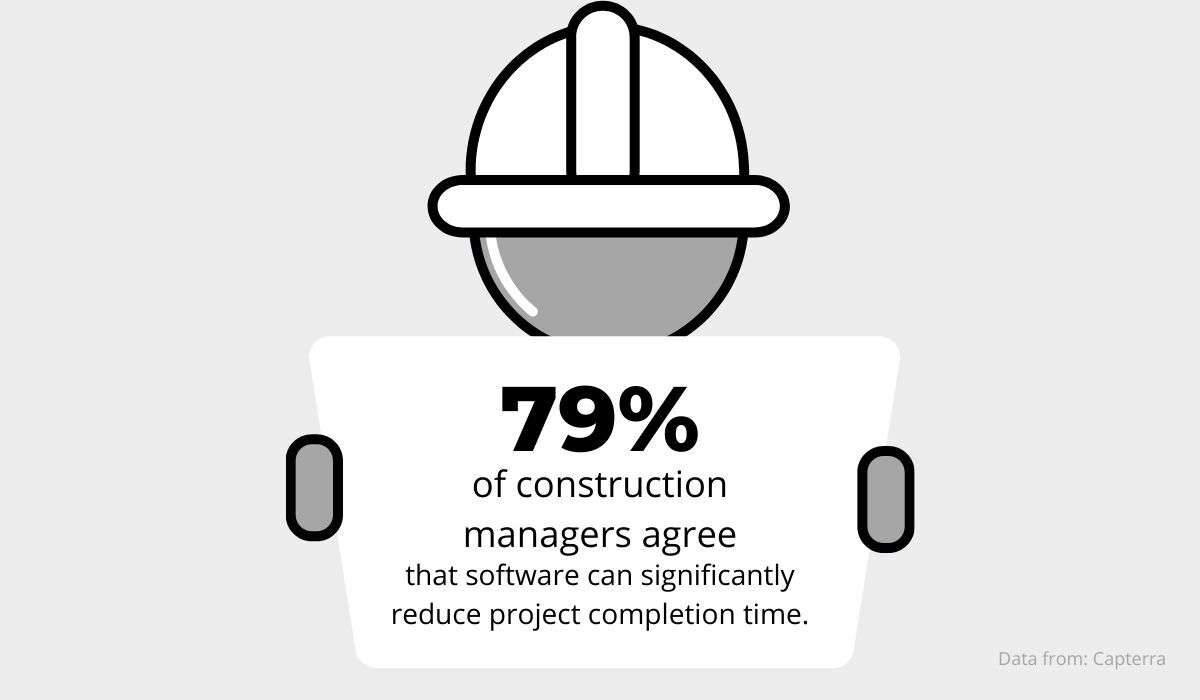
And not only that, but having such a range of access to materials data also means that decision-making can become much easier.
Planning and scheduling can now take giant steps forward in bringing costs down and maximizing worker productivity.
Of course, even if the planning stage was done perfectly and scheduling is going seamlessly, a lot of things can still go wrong.
For example, as we’ll see below, the weather is just one of many factors that can delay or even derail an ongoing construction job.
However, having access to centralized materials data and being able to track materials from when they’re procured until they’re used gives you the power to quickly adjust to the new circumstances.
Since you know precisely what materials you have, how much was used until now, and where they are, you can handle many unexpected situations that occur in the construction industry a lot more easily.
So, data access and control will streamline the preparation stage (planning and scheduling) and facilitate the execution stage (problem-solving) of material management.
Lower Chance of Theft or Damage
Being aware of the state, quantity and location of your materials minimizes the chances of your materials being damaged or stolen.
In the latter case, there is no simple way to protect construction site equipment and materials from being stolen. This requires a holistic approach.
However, what good material management does is that it enables you to see exactly what types and quantities of construction materials are needed for each project and precisely when they are needed.
This leads to more accurate scheduling of deliveries, thus cutting the time between their delivery and their use on a construction site.
That way, you’re not only minimizing the chance of theft but also reducing potential weather damage, especially when there is no suitable storage on-site.
As the weather has become less predictable and more extreme, the protocols that most construction companies have to protect materials from weather damage are quickly becoming outdated.
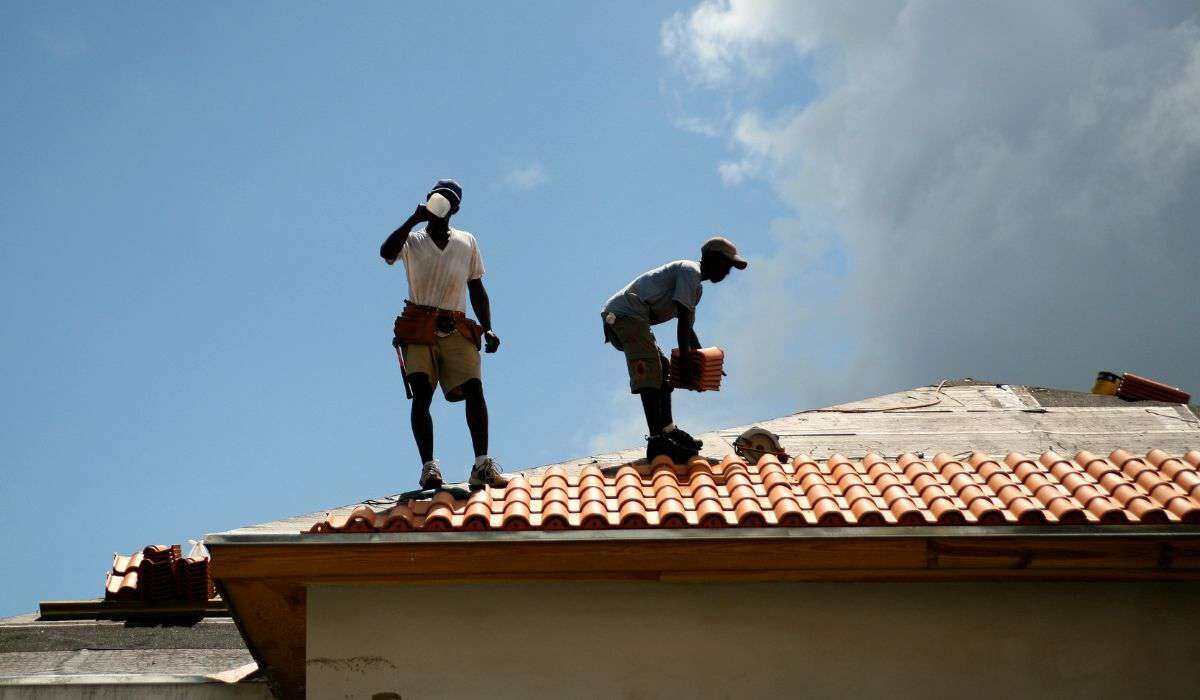
For example, sudden heatwaves can reduce the efficiency of different construction materials like mortar and adhesives.
Extreme weather events can also have negative effects on the supply side of materials.
This can be, for instance, a flood in the area where certain construction material constituents are extracted, a drought that cuts down the water supply required to finish a construction project, or erosion that can even lead to shortages of sand.
Of course, a lot of these issues can be mitigated by planning and securing sufficient quantities of materials and their storage on time, but you still have to deal with unexpected delays, mix-ups, storage problems and “pop-up” costs.
All in all, the construction business can be quite unpredictable. However, good material management gives you much more control over your project.
Reduced Material Waste
Ordering an excessive quantity of materials, as well as ordering the wrong type, will almost certainly result in increased amounts of waste in need of disposal.
But with expert material management, you can prevent a lot of useful materials from becoming waste at your site.
Having a schedule that clearly defines what materials and quantities are required for each project stage, as well as the time of their arrival on-site, can go a long way in reducing the generation of waste.
Conversely, any miscalculations can lead to an increase in material waste. And they do.
In fact, about a third of all construction materials on-site can end up discarded as waste, which has staggeringly adverse environmental and financial effects.
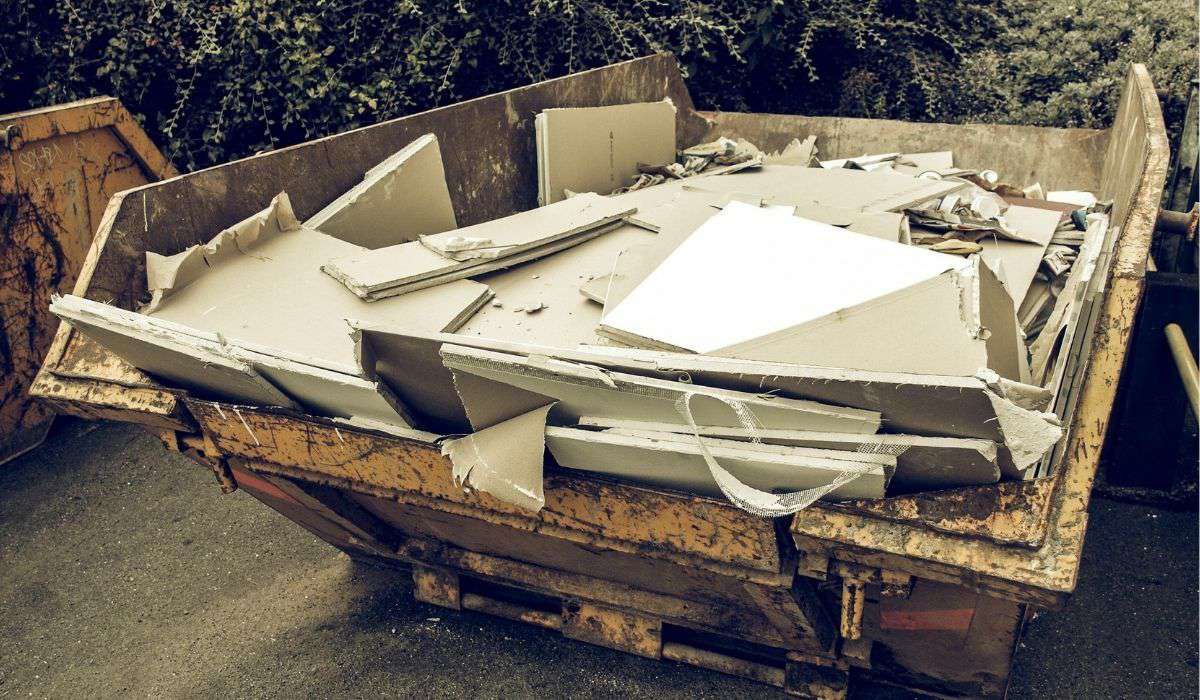
You can take steps to prevent that. Let’s look at surplus materials that can be found on any construction site.
As construction is usually a complex endeavor, estimating the quantity of materials needed for a project can be a challenging task.
To avoid surpluses on their sites, some contractors order about 20% less materials than the projected quantity and get the rest as the project completion draws nearer.
Why would they do so? Because having excess materials on-site comes with excess problems.
First off, materials in storage deteriorate. Materials in improper or non-existing storage degrade even quicker.
Next, some materials lose efficacy just by sitting in storage, while others’ expiry dates pass without someone noticing.
Ultimately, they end up as waste.
An effective material management system can prevent all of the above since it gives you control over the entire construction material stream.
Not to mention that using it would improve your ESG and sustainability ratings, making your company more attractive to investors.
Material management that results in reduced material waste will also minimize costs and alleviate the effects on the environment.
Improved Budgeting
A fitting construction management system can streamline and accelerate all stages of a construction project lifecycle. In material budgeting, it can help optimize costs, improve planning and forecasting, and enhance the overall quality of operations.
As construction projects are usually time-sensitive, they require detailed planning of milestones and deadlines, and the costs associated with each project stage.
Every project budget boils down to essentially three things: labor, equipment, and material.
Since the costs of construction materials typically make up 50-60% of an overall project budget, it’s paramount to develop a detailed budget and stick to it.
This is also vital for completing projects on time and within a predetermined budget.
If budgeting is done right, companies can achieve huge savings when they don’t over-order materials, don’t waste them, lose them, or damage them, which is what material management is all about.
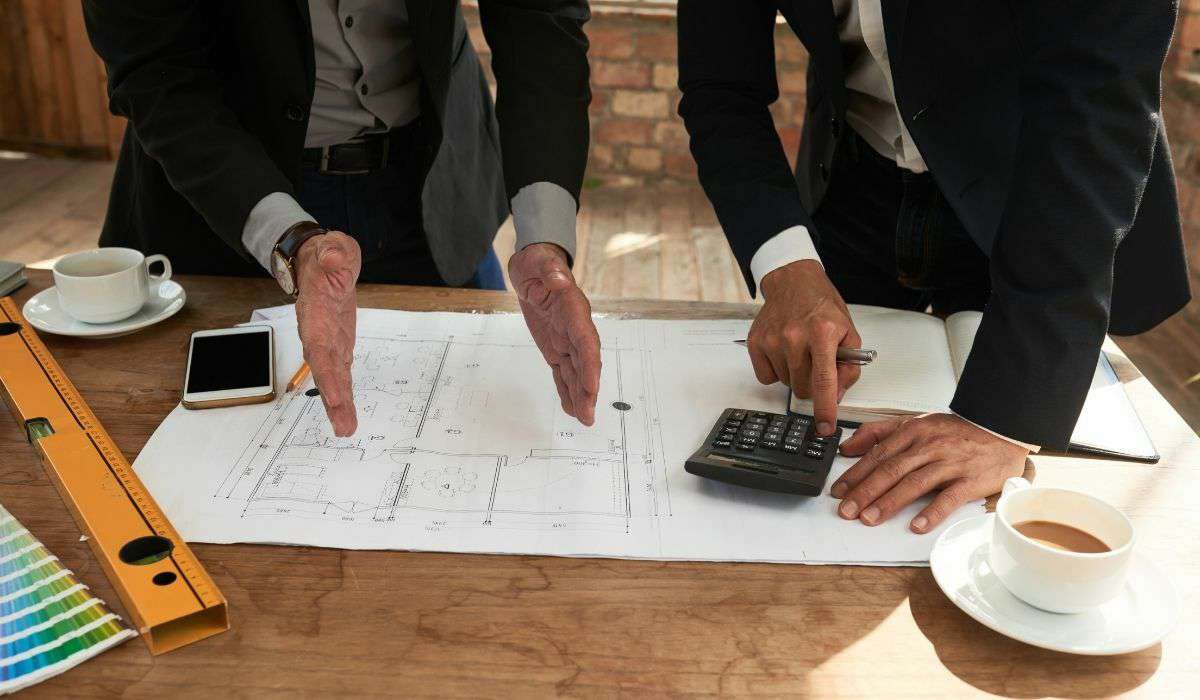
On the other hand, any construction job has many moving parts. This means it’s susceptible to different risks across all phases of the project lifecycle.
These risks include rising prices of materials, issues associated with their quality and quantity, ordering, shipping and storage and, finally, waste management.
Among them, those that can have a major impact on the budget are:
- increase in material prices (just a reminder: up 20% in the U.S.)
- theft of materials (see above)
- fuel scarcity (supply chain issues)
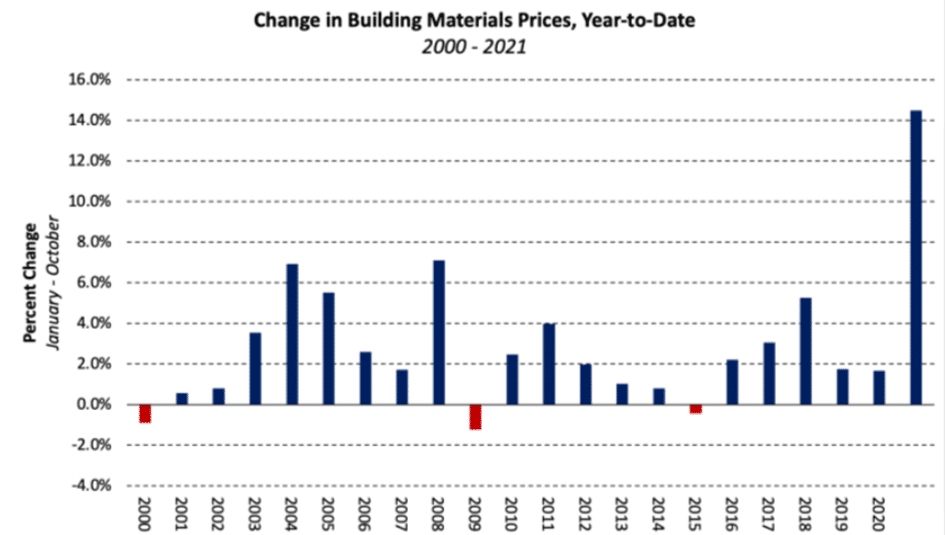
As construction is an inventory-heavy business, tracking your materials and other inventory makes sense.
Companies will often use an internal barcoding system to keep tabs on their inventory. Such systems usually utilize Stock Keeping Units (SKUs) encoded on barcodes.
However, nowadays, there are more advanced solutions that use customizable QR codes, which can hold much more information than ordinary barcodes.
GoCodes Asset Tracking is a perfect example of how patented QR code tags can be used for inventory management.
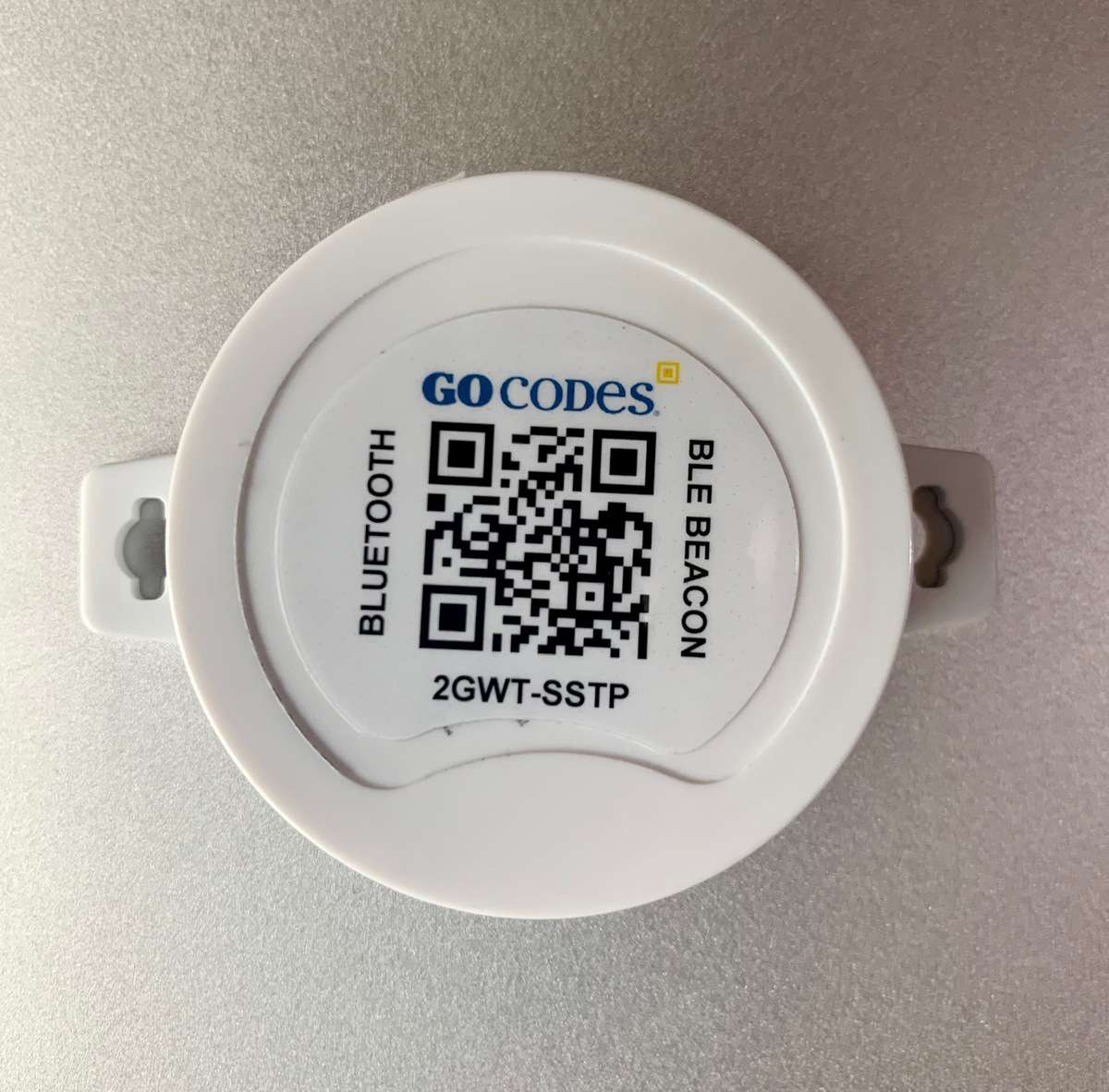
There are many perks, but here we’ll highlight the fact that separate scanners are not needed because scanning can be done with any smartphone, and you’re able to track materials wherever they go while all data is stored in the cloud.
So, an effective material management system can help you budget in a way that allows you to solve problems as they arise, minimize delays, reduce costs and improve budget planning and materials tracking.
Greater Adherence to Project Milestones and Deadlines
Reaching milestones and meeting deadlines are of critical importance for all players involved in a construction project.
To achieve this in an industry notorious for setbacks, many companies have turned to different material management solutions.
We’ve already covered what efficient material management can do. The right system will do wonders for timely project completion and boost a company’s productivity.
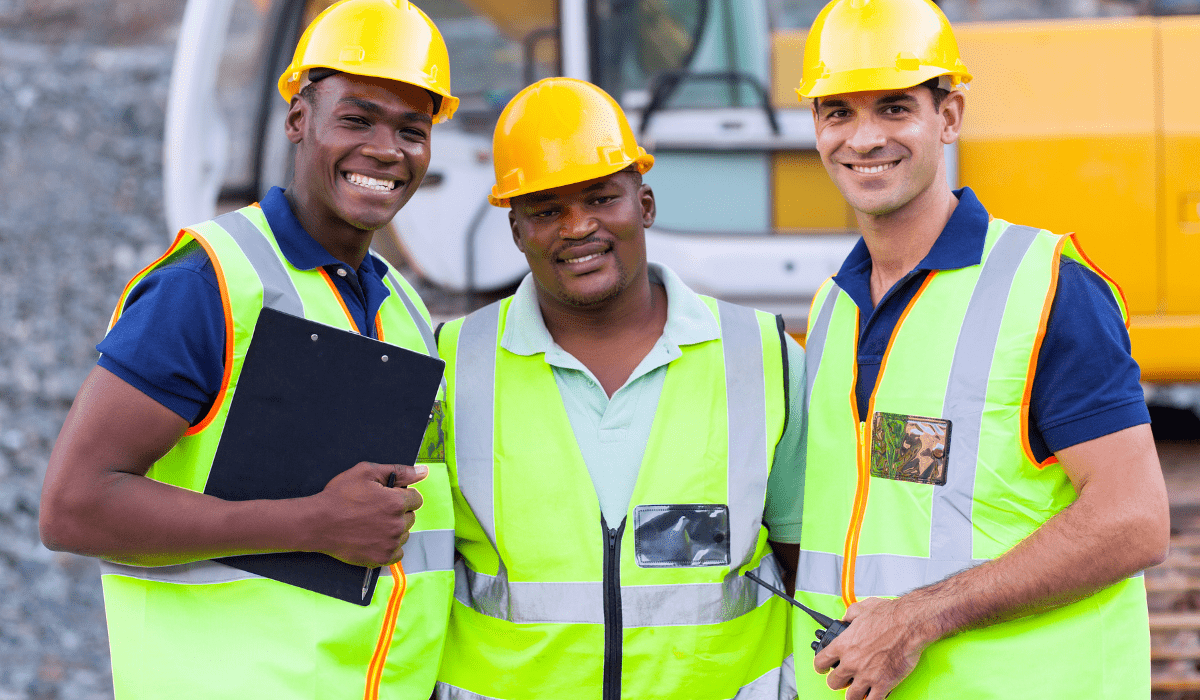
However, if materials are poorly managed, that can have a myriad of negative consequences on the construction site.
You may have seen the effects of this in your experience as a site manager. For example, workers sitting idly because the materials aren’t there or wasting time looking for them.
In contrast, a busy construction site means material management is running smoothly and workers have everything they need.
For instance, this means that materials were pre-scheduled and delivered on time, with the staff there to unload and inspect them.
Since those in charge of procurement planning have done their job, the inspection concludes that the materials are of the right type and quantity and can be used for their intended purpose.
Since the materials are immediately transported as near as possible to where they’ll be used, there is no double handling. And this list of material-related benefits continues all the way to waste management.
So, you can see how efficiency in material management is vital for construction managers.
They are responsible for delivering projects within the budget and proposed timelines. Otherwise, they must deal with breach-of-contract claims.
Since it’s said that delays are the only sure thing in construction, they have their work cut out for them.
However, the best construction managers (using the best tools) know how to get over any hurdle.
Keeping a project on schedule means managers save the company money by avoiding late fines and other incurred costs.
Furthermore, meeting deadlines is a sign of smooth communication between different project lifecycle stakeholders.
Finally, it indicates that your company is using the best technology available.
When a company is ready to apply the latest tech developments, that is a sure indicator of its agility and ability to survive on the market.
So, effective material management will not only help adhere to deadlines but will also increase revenues, boost reputation, and result in more projects for your company.
Conclusion
As we’ve reached the end, it’s clear that proper material management brings numerous benefits, ranging from having superior data access and control to greater adherence to deadlines.
It’s also clear that smart material management can help any construction company operate more efficiently, thus reducing the time and money required to finish construction projects.
As the global construction market is projected to grow and environmental trends are quickly evolving, material management has never been so important.
And it has never been so easy to organize it with the right tools.