Construction companies can employ different strategies to address the long-standing shortage of skilled labor and other recent challenges so that they ensure they’re adequately staffed to complete construction projects on time and within budget.
For example, they can specialize in target niches and outsource other tasks to subcontractors, widen their employment pool to attract a more diverse workforce, or hire less skilled and experienced workers.
Whatever strategy you’re using, there is certain due diligence you need to do when hiring all your construction labor and some more specific ones for your subcontractors.
In this article...
Do Pre-employment Screening
Whether you’re hiring your project management team members, your construction workers, or your subcontractors, pre-employment screening can help you increase the quality and the safety of your workforce, not to mention avoid some costly mistakes.
Pre-employment screening practices for future employees and subcontractors can overlap in background, credential, and reference checks and differ in some other assessments specific to each group.
For instance, when you’re looking for full or part-time employees, your candidates can take standard or customized construction aptitude tests to evaluate, among others, their professional skills in the fields of, e.g., civil engineering, carpentry, or electrical engineering, or their ability to read blueprints or safely operate machinery, equipment, and tools.
Naturally, to do this quickly and remotely, you can choose one of the available online talent assessment solutions like eSkill and get the results in just three steps.
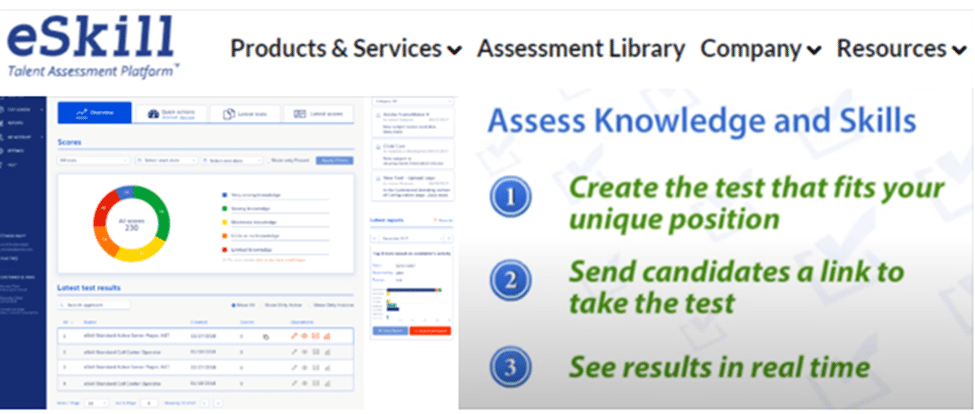
Other practices include engaging a third party to do your pre-employment screening.
For example, such specialized firms can legally check personal criminal history and motor vehicle records and conduct reference checks.
This way, pre-employment screening assessments can help identify candidates prone to unwanted or counterproductive workplace behaviors like poor work ethic and time management, absenteeism, alcohol or drug abuse, theft, or fraud, thus dodging some costly mistakes.
As for subcontractors, your selection process should also include checking their work history, qualifications, and references, like with your future employees.
However, the process of hiring your subs should also cover other checks to evaluate them against different criteria (other than the price).
For instance, when Priority Matrix interviewed a group of construction project managers, they provided these eight most common subcontractor prequalification benchmarks:
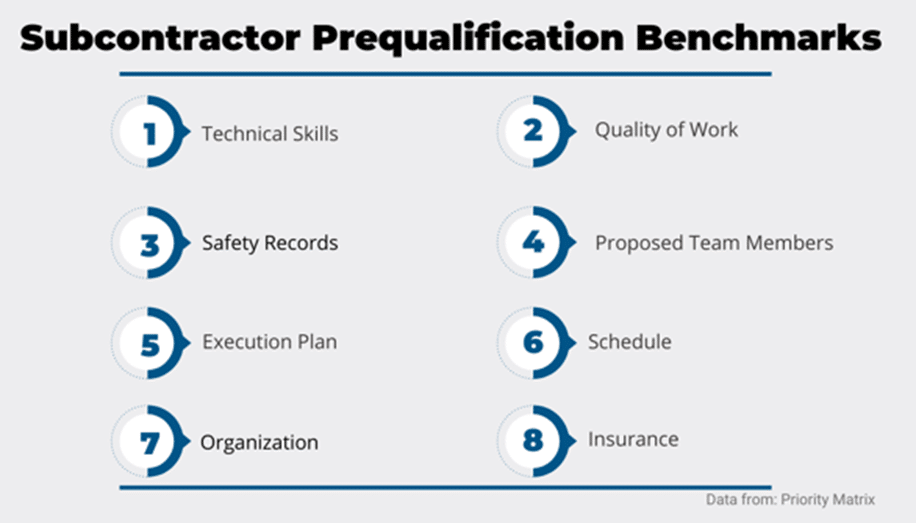
For example, “Technical Skills” would include verifying a subcontractor’s know-how and experience and their operating license (if required in your state), while “Schedule” would imply checking their availability and capacity to do the job within the set timeframe.
Another important tip is to inquire about the credentials of the subcontractor’s workers.
After all, they’ll be doing the actual work, so their expertise and experience are often more relevant than the subcontractor’s reputation or references.
Finally, the subcontractor’s capacity for cooperation, coordination, and clear communication should be high on your priority list as well.
All in all, whether you’re hiring employees or subcontractors, the practice of doing pre-employment screening can ensure you get quality workers and subs whose behavior and standards enhance the safety of your construction site.
Demand Quality Controls for Subcontractors
Insisting on quality controls when hiring subcontractors ensures that the agreed quality of workmanship and materials on a construction project is met regardless of who’s doing the work, your workers, or subcontracted ones.
Quality is defined by the client, building codes, regulatory agencies, and your company’s professional standards.
Quality assurance (QA) and quality control (QC) are part of construction quality management, whereas QA is concerned with ensuring quality in the construction process, and QC with inspecting and verifying that quality meets the set standards.
Naturally, the quality you agreed with the client extends to your subcontractors, so it’s wise to check their QA/QC programs and procedures, define their scope of work, and set clear QA/QC expectations during the pre-employment screening process.
For example, after subcontractors meet the prequalification conditions and are hired by East & Westbrook, a Kentucky-based company specializing in precision concrete foundations, their subcontractor agreements oblige them to strictly adhere to the company’s QA/QC requirements, such as these we highlighted:
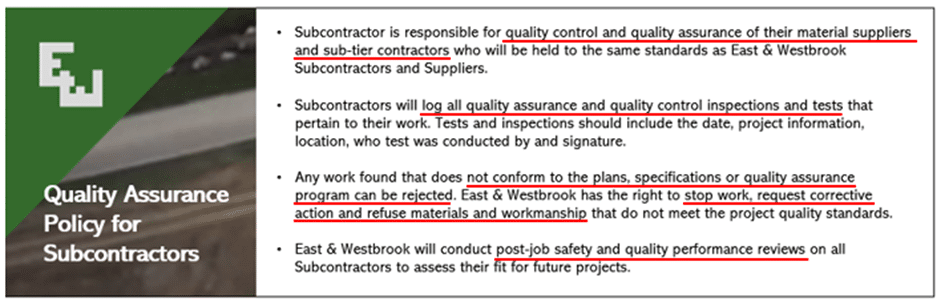
As you can see, subcontractors are also responsible for QA/QC of their material suppliers and sub-subcontractors and required to log all QA/QC inspections and tests.
Furthermore, they’re subject to regular QA/QC supervision and post-job performance reviews.
When we consider that quality deviations are the most frequent cause of rework in construction, consistent quality controls can prevent many construction cost overruns and delays caused by human factors like unskilled labor or inadequate supervision, accounting for 55% of all construction errors.
That’s why the above-cited QA policy states that subcontractors are required to:
- Provide competent workers in sufficient numbers to complete the work as scheduled
- Provide competent supervision for all phases of their work
If you want to ensure the quality of your construction projects, look at our tips and consider how they specifically apply to your subcontractors:
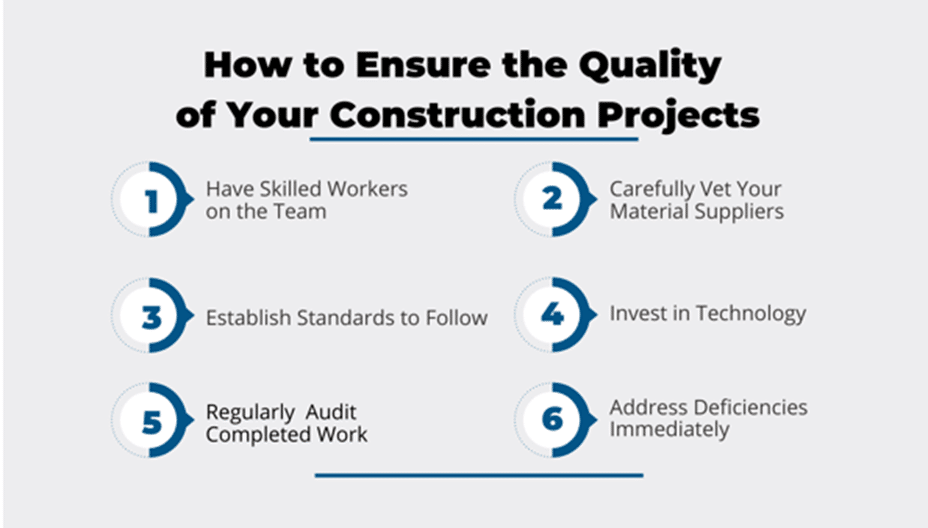
It’s clear that all of them are relevant if you want to make sure that your subcontractors meet the project quality standards throughout its lifecycle.
For example, investing in construction management software can provide a single source of information for all project stakeholders, streamline communication, coordination, and supervision of subcontractors, and monitor their quality of work.
In conclusion, requiring quality controls for subcontractors like vetting their QA/QC practices, defining their scope of work, and required quality, and specifying your own QA/QC requirements before hiring them, along with performing consistent quality checks during their engagement, will ensure your company is delivering top quality, on-time, and on-budget construction projects.
Check if Your Subcontractors Are Bonded and Insured
Whether you as the main contractor are required to be bonded and insured or not, you should consider ensuring that your subcontractors have insurance coverages and bonds needed to protect your construction projects from various risks.
First, when hiring subcontractors, you should ask them to provide proof of insurance they’re required to have under law, such as:
- Workers’ compensation insurance (mandatory in all states but Texas, where it’s optional for private employers)
- Commercial auto insurance (for the subcontractor’s vehicles)
- General liability insurance for builders (required by law in some states and often required by contract)
Otherwise, your business might be liable for injuries of your subcontractor’s workers resulting from construction site safety failures and any damage they caused to property or third persons.
Here’s an overview of these and other construction insurance types, courtesy of Construction Coverage:
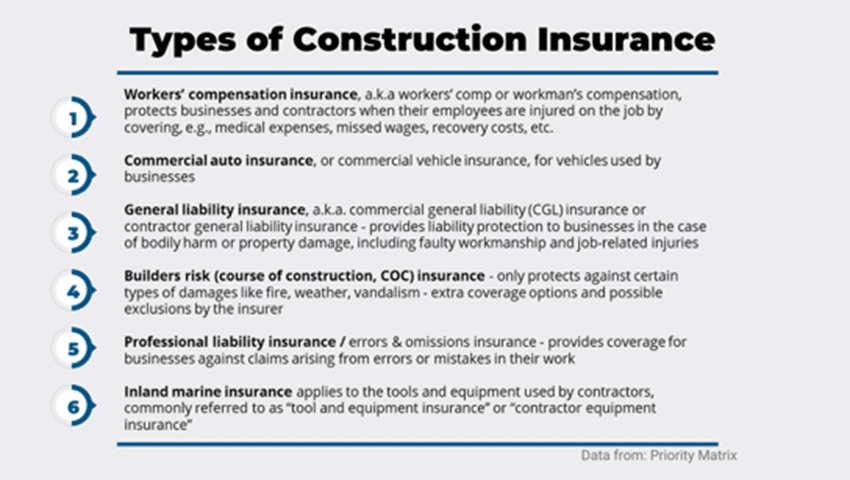
Which of these you expect from your subcontractors will depend on the project type and other parameters.
Still, they should protect you from liability for the subcontractors’ errors, omissions, and substandard work.
While insurance transfers risks to other parties (insurers), surety bonds distribute risk differently.
For subcontractors, construction/contract bonds would be agreements between you (the main/general/prime contractor), your subcontractor, and their surety to guarantee their performance, compliance, or payment.
In essence, such bonds guarantee that, if a subcontractor violates their contract, underperforms in some way, or fails to pay their subs and suppliers, the surety will step in and cover their obligation while collecting the total amount from the subcontractor.
All this after confirming that the subcontractor’s default is proper, of course.
There are many companies offering bonds like Surety Bonds Direct, which also lists different types of construction bonds:
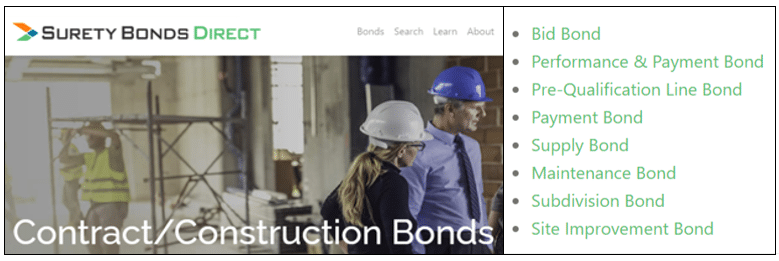
Among the listed, performance and payment bonds are most frequently required from subcontractors.
They basically guarantee that the subcontractor will do their job according to plans and specifications and pay their own subcontractors and suppliers on time.
Some contractors also prefer bonds as a way of getting the surety to verify the subcontractor’s financials, performance, and quality.
So, when hiring subcontractors, ensuring they have the proper insurance to protect themselves, their employees, and you from various construction risks can save you from many problems, disputes, delays, and costs throughout the project lifecycle.
Review Your Contracts
Of course, contracts form the basis of any relationship with your employees and subcontractors.
Therefore, they should be well-written, clear, and transparent for all the parties involved while ensuring your business is protected against different risks.
In this section, we’ll focus on your contracts with subcontractors.
It’s no secret that poorly written subcontracts can quickly turn into major obstacles to successful project completion.
For example, if the subcontractor’s scope of work is badly defined or change order rules are not clearly established, that can lead to budget and schedule overruns, rework, lost time, conflicts, disputes, and even lawsuits.
Here’s an overview of the key features of subcontractor agreements to focus on when drafting and reviewing your subcontracts, courtesy of Software Advice:
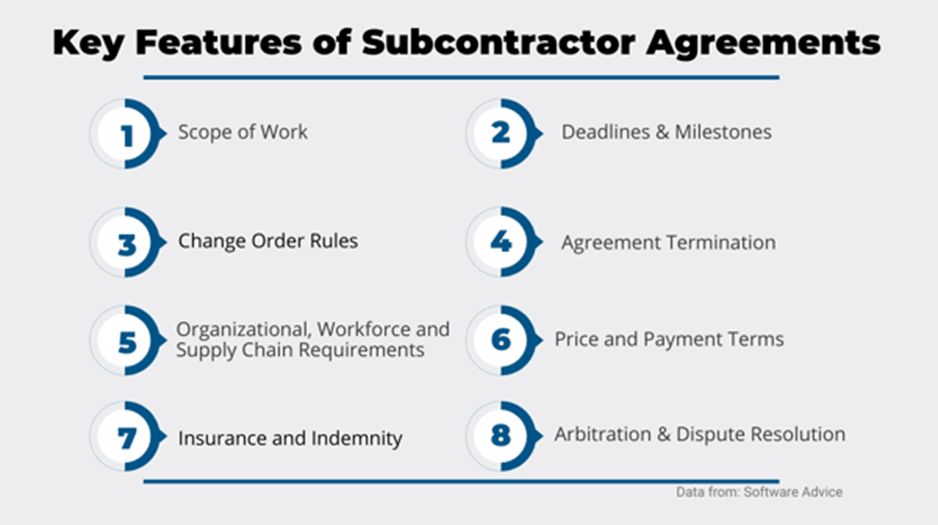
For instance, a contract with your subcontractor should describe exactly what work the subcontractor will be performing and specify milestones with deadlines stipulating when the subcontractor is expected to deliver, including consequences of defaulting on those deadlines.
As for dispute resolution, including an arbitration clause in your contract can lead to major savings in legal fees and other litigation costs because any potential claims and disputes between your business and the subcontractor will be settled through binding arbitration, not the courts.
Moreover, there are things you should avoid doing when hiring subcontractors to prevent major disputes altogether.
Besides steering clear of informal verbal agreements and ensuring your contracts have the above key features, you should use standard contract templates when drafting subcontracts.
For instance, the American Institute of Architects (AIA) offers standard and more specific forms of contractor-subcontractor agreements like these.
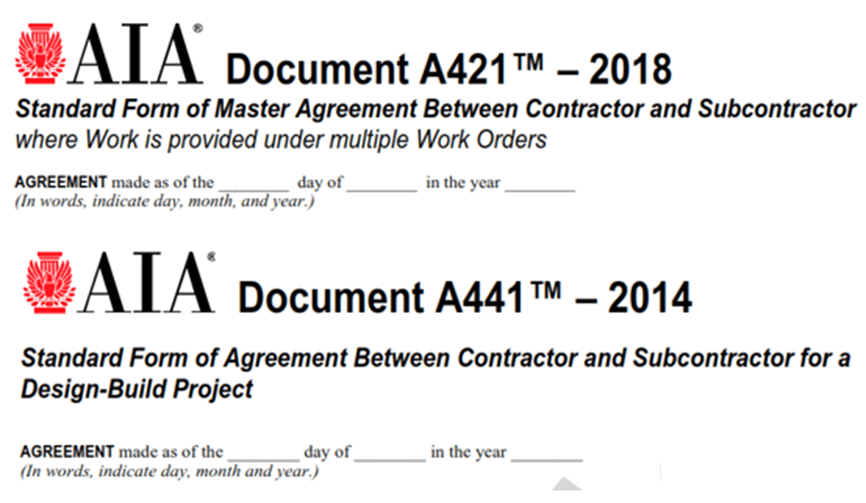
The first one is used when the subcontractor’s scope of work needs to be defined on-the-go through work orders and ensures that it can be done quickly without renegotiating the contract terms, while the second one regulates contractor-subcontractor relations in design-build projects.
In conclusion, reviewing your contracts when hiring subcontractors and ensuring you (and the project owner) are protected against the subcontractor’s underperformance risks can prevent many headaches, delays, and extra costs.
Ensure a Safe Working Environment
Due to numerous safety hazards inherent to construction projects, ensuring a safe working environment on your jobsites should be your top priority.
Naturally, this safety-first culture, its principles, rules and procedures, and jobsite safety expectations need to be considered when hiring both employees and subcontractors.
Without going into construction injury statistics, we’ll just say that safety is critical as it saves lives, prevents major and minor injuries, minimizes workers’ compensation costs, and ensures compliance with the Occupational Safety and Health Administration (OSHA) regulations, to name a few.
We provided five tips on how you can ensure jobsite safety below.
The requirements resulting from applying them on your jobsites should be considered when screening your potential employees and subcontractors.
They can help you determine whether the candidates would fit into your safety culture and not jeopardize it by reckless behavior and unsafe practices.
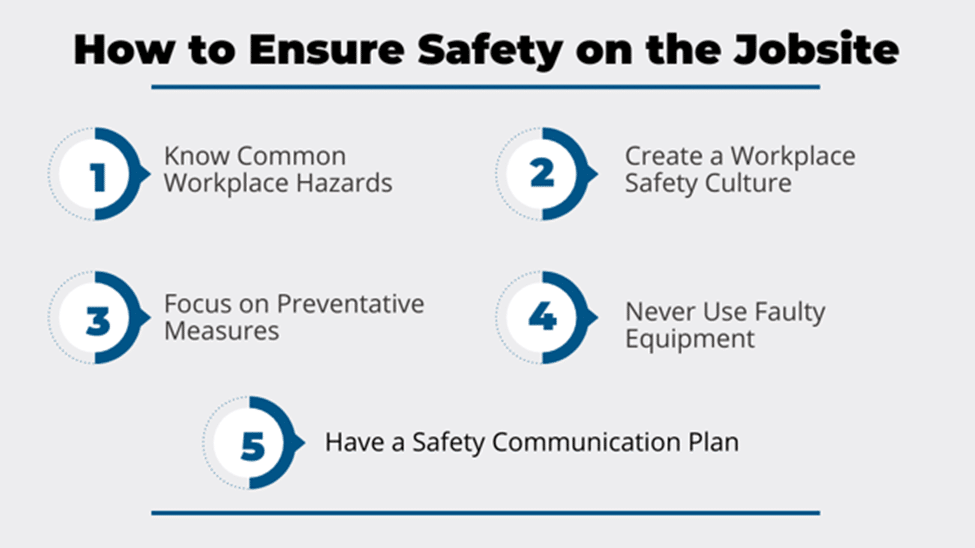
Naturally, once hired, your employees and subcontractors, including their sub-tier contractors and suppliers (and everyone else present on the site), should understand and follow all required workplace safety procedures.
In today’s world, a safer working environment can be achieved by utilizing various construction management software and technologies.
For example, one of those technologies, drones, increases the safety of construction workers by 55%, according to research. And that’s just one of the benefits they offer.
Another way of improving jobsite safety is keeping track of your machinery, equipment, and tools at any time, along with their condition, maintenance status, and the last service date.
You can use a variety of tools to do so.
Such tracking solutions can prevent injuries caused by the breakdown of poorly maintained equipment or worn-out tools in a simple and affordable way.
If that sounds interesting, try GoCodes Asset Tracking.

We’ll close this section with a quote from Roger W. George of AECOM, speaking about screening potential subcontractors:
“Evaluate safety, quality, and performance in that order. Performance is a byproduct of safety and quality. Those that achieve high standards in safety and quality have a performance factor which speaks for itself.”
Overall, ensuring a safe working environment starts at the pre-employment screening stage and stretches throughout the project lifecycle.
Conclusion
Smart pre-employment screening procedures, professional contract drafting, and insisting on quality controls, insurance or bonds, and safety can help you hire a great construction workforce.
Sticking to the practices we’ve described in this article will help you complete projects on time, within budget, and while offering high quality.