Thanks to construction inventory management, construction companies, and suppliers are able to keep track of materials, equipment, workforce, etc.
This is especially useful if your company manages multiple projects since, in that case, things can get a little more complicated.
However, managing construction inventory is not an easy task, and a single mistake could cost you a lot of money.
That is why it’s extremely important to avoid and prevent some common mistakes while overseeing your inventory.
In this article, we will go through six typical construction inventory management mistakes and show you how to avoid them.
Let’s start.
In this article...
Daunting Yearly Physical Inventories
The first mistake we’ll discuss is doing inventories only once a year. Do you remember how businesses used to shut down for a day or longer due to inventories?
That was because people had to physically count everything in the warehouse to ensure it matched their records.
Hopefully, you are not still doing inventory like that since it’s an outdated practice, expensive and time-consuming.
Besides, there are some much better options nowadays.
For instance, modern logistics experts recommend doing cycle counts.
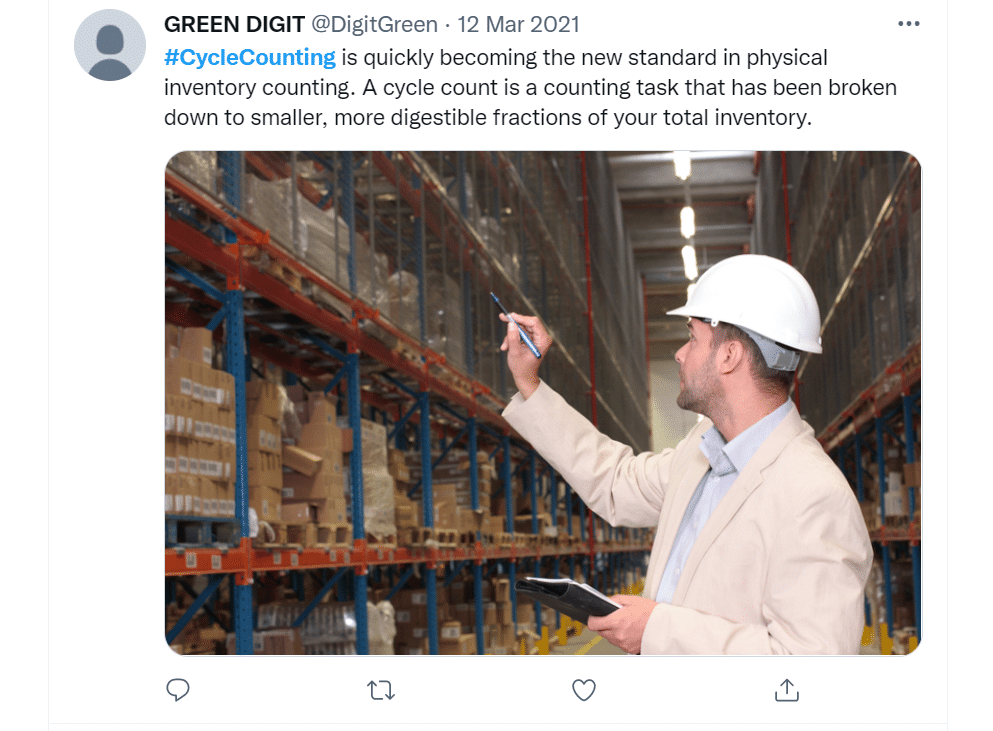
So what are cycle counts exactly?
It’s a method of counting inventory on a more frequent basis throughout a year, making keeping an exact inventory count far easier as counting is done in increments, instead of all at once.
The great thing about it is that it works on all warehouse sizes, even massive ones, like in this Reddit poster’s case.
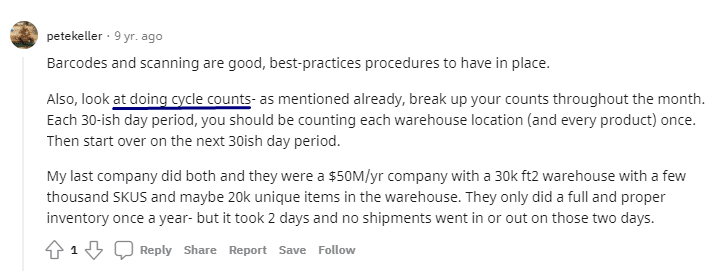
And don’t think you’ll have to do the counting manually.
There are warehouse management systems (WMS) that can help automate cycle counting and make it more accurate and accessible.
Experts like Ken Mullen, senior managing partner at enVista, recommend using this kind of software to bring your inventory management practices to a whole new level.
“A WMS can help drive the cycle counting process and keep track of what’s on hand or in transit, what’s come into a dock, or on an outbound dock. Many companies don’t take advantage of real-time inventory capability. But having a more realistic snapshot helps minimize cost disadvantages of poor inventory practices.”
In conclusion, avoiding doing inventory for an entire year just exacerbates the problem.
Instead, try doing cycle counts periodically to avoid shutting down your business for a day or longer.
That way, it will be easier to maintain the accuracy of your inventory, and comply with audits and other requirements.
Disorganization in the Warehouse
Disorganization in the warehouse is a major impediment to productivity and efficiency.
When your employees spend ages wandering around the warehouse in search of the items they need, that’s time and money down the drain.
In the worst-case scenario, items can be permanently lost and have to be replaced, which can put an enormous strain on your finances.
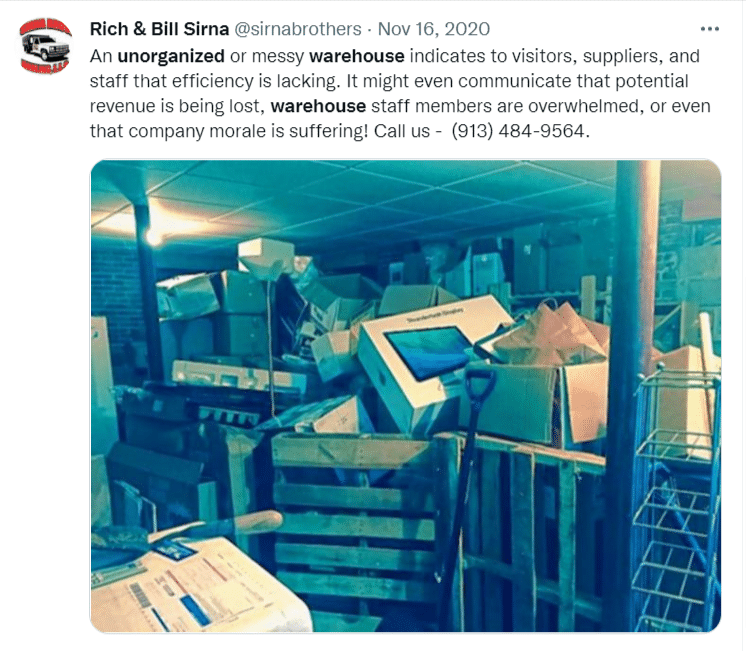
Fortunately, keeping your warehouse organized isn’t all that complicated and there are numerous solutions and practices you can use to keep everything in order.
For instance, you can label items so they can be quickly scanned and saved into your inventory management system.
With the item scanned and its location in the warehouse recorded, you’ll always know where to find it and possibly even who had it last.
Take Trinity University in Leeds, for example.
The university has a huge inventory of AV and educational equipment that they keep in stock rooms and lend out to students and faculty.
Before coming up with a labeling system, they had a hard time tracking the equipment and, since they weren’t diligent about tracking who borrowed it, it wasn’t unusual to have 130-180 items late for return.
Now, with a labeling system in place, the system tells them exactly where the equipment is and who’s in possession of it.
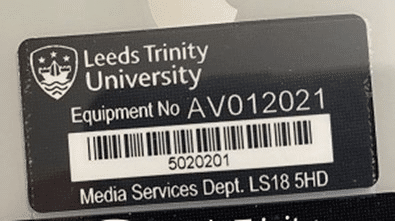
Now, it’s more common to have 20 items late for return, meaning that the equipment is more available to staff and students who need it.
In this way, barcoding ensures ease and accuracy, and it’s at least 75% faster than manual data entry; it also eliminates the possibility of human error.
Another practice that will keep your warehouse organized is called lean inventory.
Basically, it means that you should keep only the inventory you actually need and nothing more.
Also, in this way, your employees will save some time by having fewer items to worry about.
To achieve it, you can reduce your safety stocks, but if that’s not an option, you can ask your suppliers to deliver smaller loads more frequently.
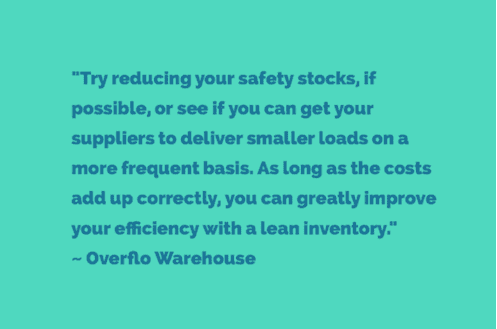
So a lean, clean warehouse with everything properly labeled will keep your business running efficiently.
People That Don’t Know How to Use the Technology
Over the past few years, many changes have been made to construction sites, and one of the biggest is the continued adoption of contech (construction technology).
The rapid progression of contech is making builders, investors, and others adapt to modern ways, and a recent survey proves this. 91% of respondents have witnessed their previously uninterested colleagues embracing contech.
However, after spending all that money on software, they are often unwilling to pay for the specialized training that would allow their employees to make the most of the software.
That’s a common mistake that often proves detrimental, since even the best software in the world won’t do any good if your employees don’t know how to use it.
To avoid months of struggling before your staff figures out the basics of your new software, consider bringing in an expert to train your staff on how to use the new equipment and systems.
Better yet, pick tools that are intuitive and easy to use instead of systems that require heavy expertise.
This is a quick and easy way to cut down on training time and get the new system up and running.
But how can you know if some new technology you want to implement is easy to use? Easy.
Your first step is to do some research and check out some reviews.
These will usually mention how intuitive a system is.
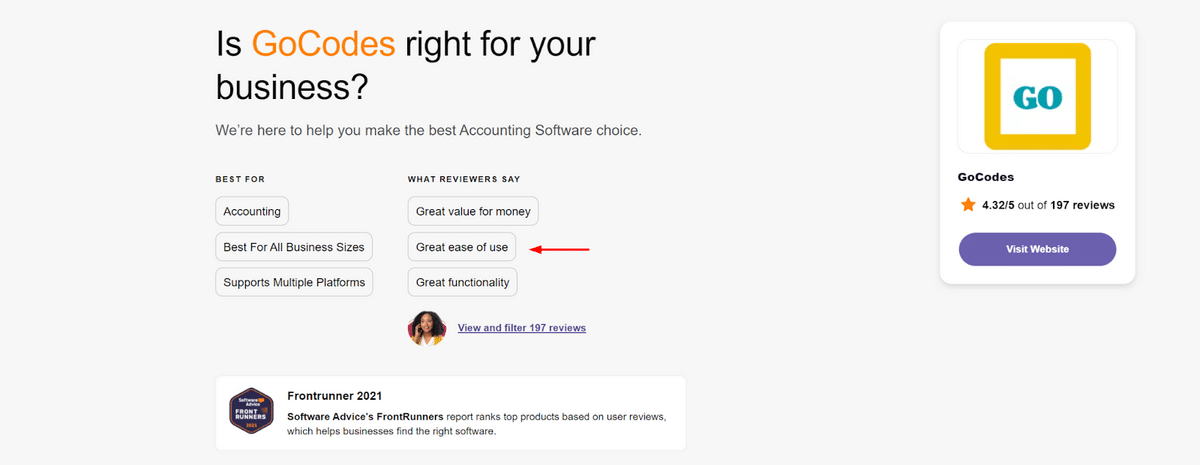
For example, as you can see in the example above, our own asset management system is often praised for its ease of use by customers we’re happy to serve.
In short, while implementing technological solutions in your construction business is mandatory nowadays, it won’t do you any good if your staff dreads using it.
Therefore, you should invest in training, and simply pick easy-to-use tools for the benefit of your workforce.
Not Checking the Orders
Order management is one of the most important operations for any warehouse but also the one that leads to the most errors.
You need to be on top of what’s ordered, when it was delivered, and where it’s stored if you want your business to function smoothly. Also, this will help you to avoid any forgotten orders.
Order management starts the minute you receive an order; it includes accepting the order, packing, and shipping, and ends with post-sales processes like refunds and returns if needed.
Any mistake that might occur during that period can collapse the entire process. That would, of course, be a huge waste of resources.
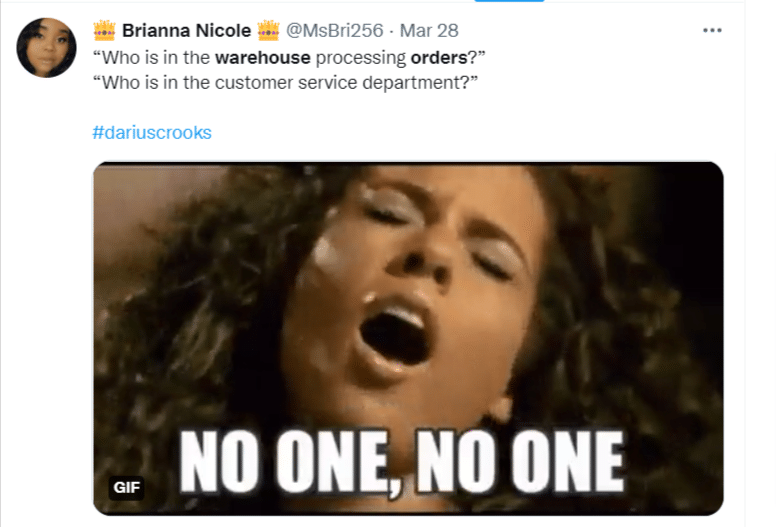
So, to keep the orders running smooth, many companies use a cloud-based order management system.
They can manage the whole process through such systems, including shipping and customer notifications, in real-time.
Also, since everything is stored in a secure online database, authorized personnel can check orders or update information from absolutely anywhere.
So a cloud-based order management system has many benefits.
These include fewer delays, better tracking, and finding everything you need with just a few clicks instead of going through disorganized records.
Also, tracking your inventory levels will help you avoid backorders and have enough items to fulfill your sales orders.
This is because these tools have a feature for reorder points (also known as min and max levels), and those are the best method for ensuring you have the right amount of inventory in your warehouse at all times.
Our own tracking solution, GoCodes Asset Tracking, can do that as well, thanks to its patented QR code system that enables you to receive low quantity alerts and restock.
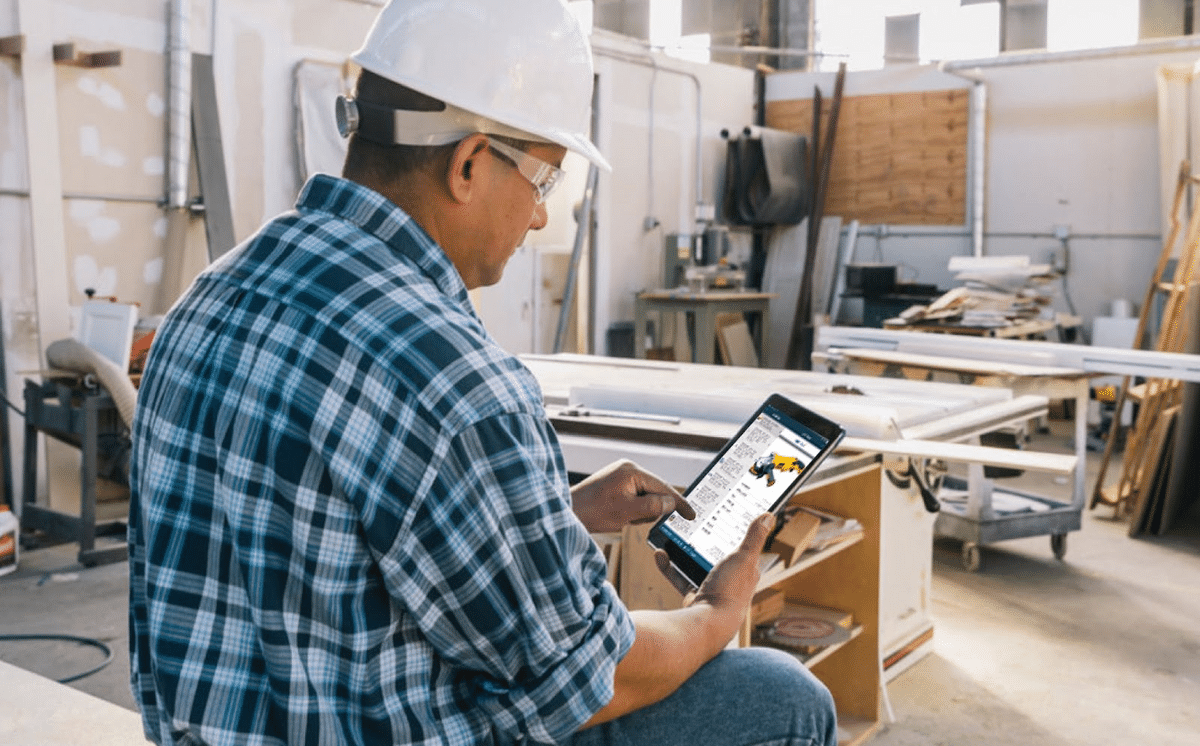
Order management is a crucial aspect of any successful business, so using an outdated ordering system will do you more harm than good.
When your order management is on the cloud, everything is neatly organized in the same place, easy to find and updated.
Not Managing Inventory Documentation
Just imagine this scenario: one of your forklifts gets broken, and that’s an expensive machine.
You need it repaired as soon as possible, but it takes you forever to find the warranty in your filing cabinets and drawers. You are only losing time and money due to your poor organizational skills.
Unfortunately, managing inventory documentation often gets neglected.
Of course, you’ll also need to access and manage documents on the go. This feature is important because you want the documentation to be accessible whenever and wherever you need it.
So, anytime you’ll have to make a real-time decision, you can simply pull up the necessary documents.
In order to achieve all of this, the first thing you’ll need is to choose software that uses cloud technology because the key benefit of cloud storage is the ability to link documents to an entry.
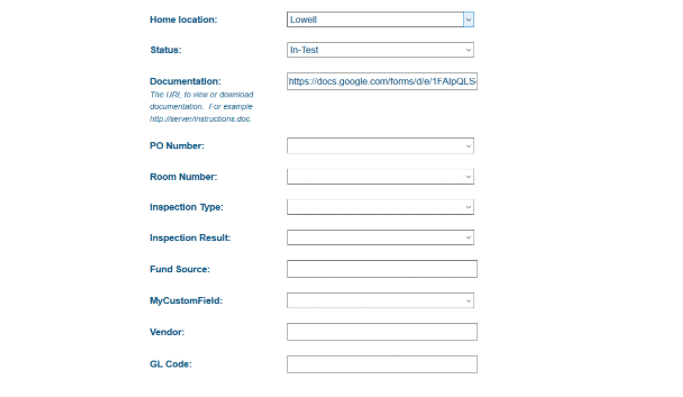
Once you do that you’ll need to transfer your data to the cloud and connect documents to the equipment so that when you search for an item, you see all the product details and the description you’ve added, including a link to the related documentation.
So, it’s as simple as that, and you will have all your inventory documentation in one place, accessible wherever and whenever you need it.
Conclusion
Inventory is a crucial part of your construction business, and neglecting the way you manage it can cause serious issues down the line.
Even though mistakes in construction inventory management are quite common, they can cost you time and money.
This is why it’s important to use the right tools to track your inventory and keep everything organized, from your warehouse to your inventory documentation.
In this article, we’ve covered six typical inventory management mistakes and given you some helpful tips on how to avoid them. We wish you success in implementing them!