Key Takeaways:
- Construction fleet tracking leverages GPS and wireless telematics devices in conjunction with fleet management software to provide construction companies with full asset visibility.
- It helps you achieve optimal productivity, enhances driver safety, and prevents costly fuel overconsumption.
- The features to look for in a fleet tracking solution include real-time tracking, geofencing, reporting, and integration capabilities.
Fleets hold a special place in construction operations.
These powerful machines can handle heavy tasks with unparalleled efficiency and precision, enabling companies to undertake large, complex projects with confidence.
But it isn’t all about having the biggest fleet with the latest, top-of-the-line machinery.
It’s about how you keep track and manage those valuable assets, too.
That’s what we’re here to talk about today: the art of construction fleet tracking.
We’re diving deep into the heart of this essential process, showing you why it’s the backbone of every successful construction project, and revealing key factors to consider in selecting your own fleet tracking software.
Let’s get started.
In this article...
What Is Construction Fleet Tracking
Today, fleet tracking is an indispensable component of construction project management.
It leverages GPS and wireless telematics devices in conjunction with fleet management software to enable real-time monitoring of vehicles and machinery across multiple projects and job sites.
In the illustration below, you can see the mechanics of such systems:
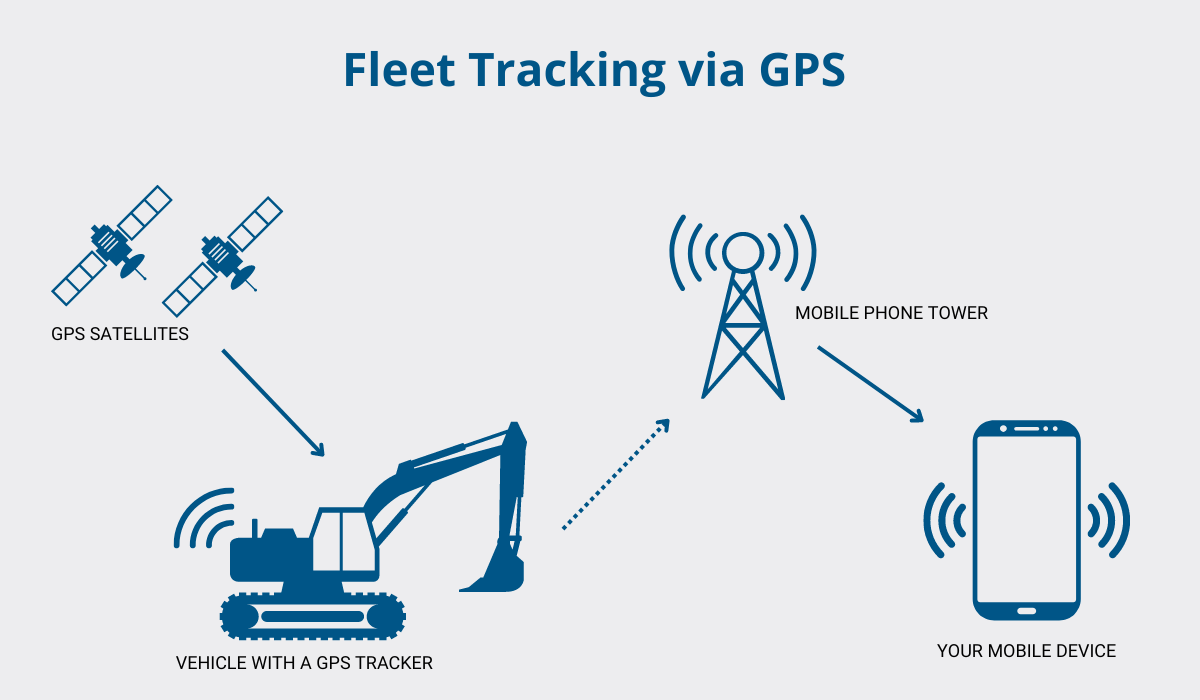
At the heart of fleet tracking systems are tiny, yet highly efficient GPS tracking devices.
Once attached to your equipment and activated, they use signals from GPS satellites to capture and transmit asset location data.
This data is then processed by a central server and finally translated into updates accessible via fleet management software—be it on your phone or computer.
However, modern fleet tracking and telematics have evolved beyond simple GPS location monitoring.
Through different sensors and devices integrated into your machinery, you can now keep track of the information such as:
- engine performance,
- tire pressure,
- driver behavior,
- fuel usage, and
- environmental conditions within vehicles like temperature, humidity, or pressure.
Essentially, today’s fleet management technology helps you unlock full asset visibility.
It tells you all about where your machines are, how they’re used, who’s operating them, the project they’re assigned to, and even their maintenance status.
In the fast-paced and fiercely competitive world of construction, this information isn’t just nice-to-have anymore, but a must-have.
Let’s see why that is.
The Importance of Construction Fleet Tracking
In the construction industry, where success is measured by the ability to adhere to budgets and schedules, achieving optimal productivity while slashing costs wherever possible is the number one goal.
Nothing empowers you to reach that goal quite like fleet tracking.
It does so through strategic resource allocation, optimized equipment utilization, increased driver safety, and identification of cost-saving opportunities.
Simply put, keeping your eye on the fleet’s performance and movement makes you smarter about optimizing its use.
Is a vehicle on the wrong job? Is it idling too often?
Is it perhaps being overworked, or could it be of more use somewhere else?
Fleet tracking uncovers any inefficiencies immediately, allowing you to reallocate resources on the fly and ensure each job site has exactly the equipment it needs—no more, no less.
This, in turn, helps you keep your operations running smoothly, while simultaneously reducing rental expenses for machines you don’t really need.
Fleet monitoring also boosts your drivers’ safety.
Telematics devices can quickly detect risky behaviors like speeding, tailgating, distracted driving, or harsh braking, and send alerts to the machine operators, warning them about the potential danger.
This can significantly reduce accidents and injuries on the job.
In fact, according to a report by GPS Insight, 57% of fleet managers agree that vehicle tracking is very effective in improving the overall safety of their fleets.
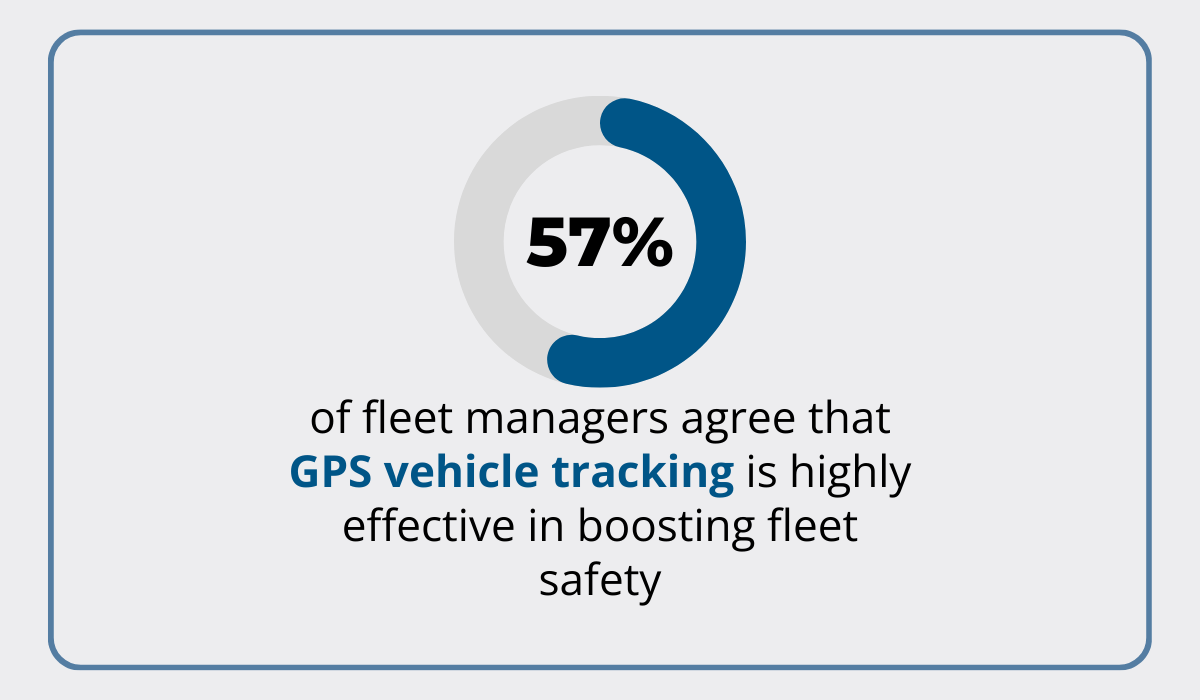
Your drivers are the backbone of your operation, and their well-being should be a top priority.
So, why not rely on a system that prioritizes their safety as well?
But the perks of fleet tracking don’t end here.
This important process can also serve as an efficient cost-saving measure.
For example, if you keep track of fuel consumption and identify excessive idling or overuse, you can save a lot of money on fuel costs.
Given that fuel prices are one of the major concerns in the industry right now, the ability to cut these costs can be a real game-changer for a company’s profitability.
Interestingly enough, a survey from Samsara shows that, as a response to the volatility of fuel prices, a large number of construction companies are turning precisely to the monitoring of their powered assets.
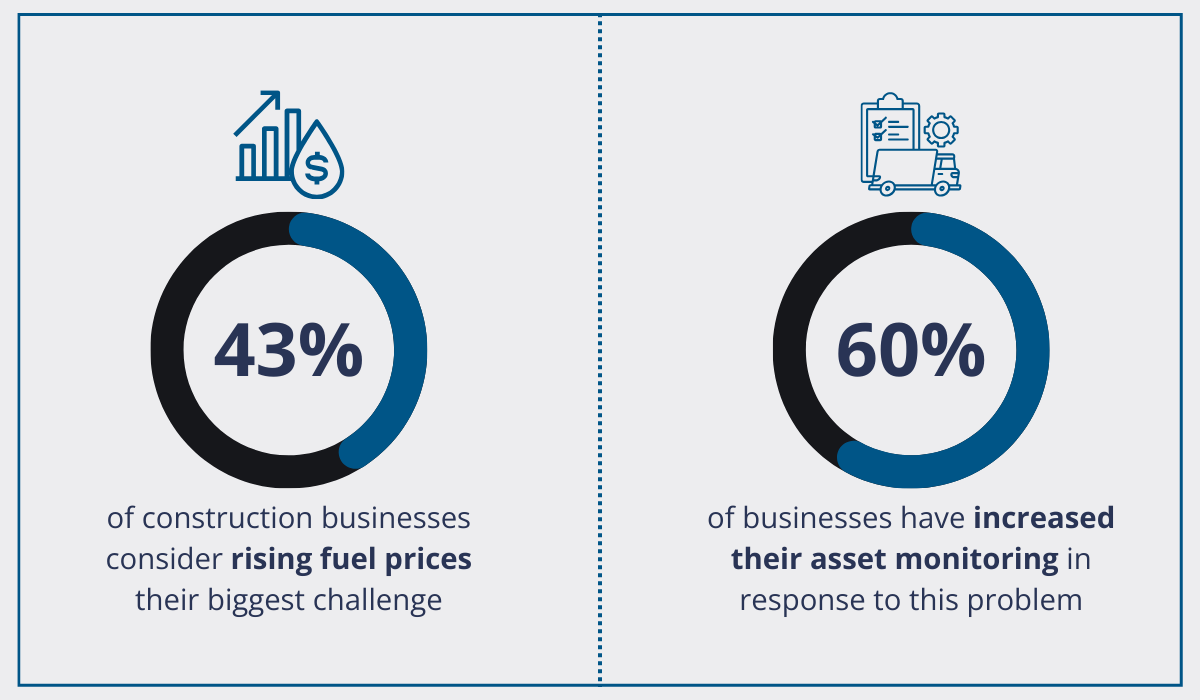
After all, you can’t improve what you don’t measure.
And there’s no better way to measure than through a robust asset tracking system.
All in all, the benefits of construction fleet management are too many to count.
From cutting down unnecessary expenses to making the most out of your valuable assets, fleet tracking is definitely your ticket to successful project completion.
What to Look for In a Fleet Tracking Solution
Now, to unlock all these benefits, you’re going to need the right tool.
And the right tool, in this context, is an automated one.
The vast majority of fleet managers today agree that automation through dedicated software solutions is crucial for increased productivity.
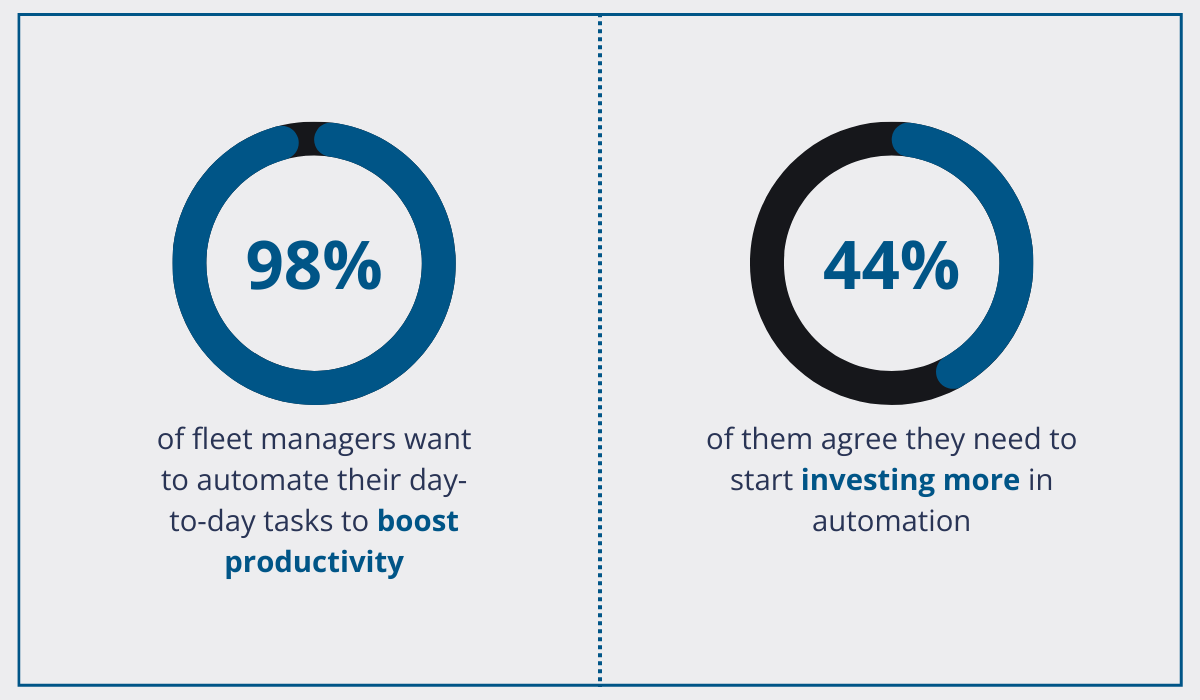
In fact, 44% of them plan on investing even more in automating their operations in the future.
However, bear in mind that not all software is created equal. To truly reap the rewards of fleet tracking, you need a system with the right features.
Let’s explore what those features are.
Real-Time Tracking
Software with real-time tracking capabilities enables you to keep your eye on your fleet at all times, providing accurate and up-to-date data on its whereabouts and performance.
This level of insight facilitates agile decision-making, empowering you to proactively identify possible risks, and take corrective action to protect your assets, drivers, and overall operational efficiency.
For instance, such software can dynamically optimize routes, taking into account variables like road work or traffic congestion, offering your drivers safer and more efficient alternatives on the fly.
Moreover, these systems can monitor environmental conditions within vehicles, ensuring transported goods arrive at their destination in perfect condition.
For example, a fleet tracking solution with real-time temperature monitoring can alert drivers to temperature fluctuations or refrigeration system failures, preventing damage to temperature-sensitive materials en route.
Similarly, systems that can detect excessive vibrations are crucial when transporting delicate cargo, such as electronic devices or valuable heavy equipment.
Farrukh Rafiq, Vice President of Fleet Operations at Asplundh Tree Expert, LLC agrees that real-time information is a must in the construction industry:
“With real-time operational data, we can make smarter business decisions that directly impact our bottom line. For example, we recently sold $10 million of underutilized equipment, freeing up cash flow to invest in areas that matter—like new equipment we really need.”
It allows you to work faster, smarter, and better.
Without it, you’re basically operating blindfolded, with no clue where exactly your assets are or how (if at all) they’re being used.
Geofencing
Geofencing involves establishing a digital perimeter around a specific geographic location in the physical world.
In construction, these virtual boundaries are typically deployed around job sites or warehouses, serving as a barrier that vehicles and machines aren’t allowed to cross.
This software feature plays a major role in enhancing overall job site security, particularly in combatting theft—a persistent concern for fleet managers within the construction sector.
According to a survey conducted by BauWatch, it seems that theft incidents are on the rise.
A staggering 62% of industry professionals report they saw an uptick in theft in 2023 compared to the previous year.
Even more alarmingly, 70% of the survey respondents say they witness theft on-site at least once a year.
Of all the stolen goods, high-value vehicles and machinery account for 24% of the losses.
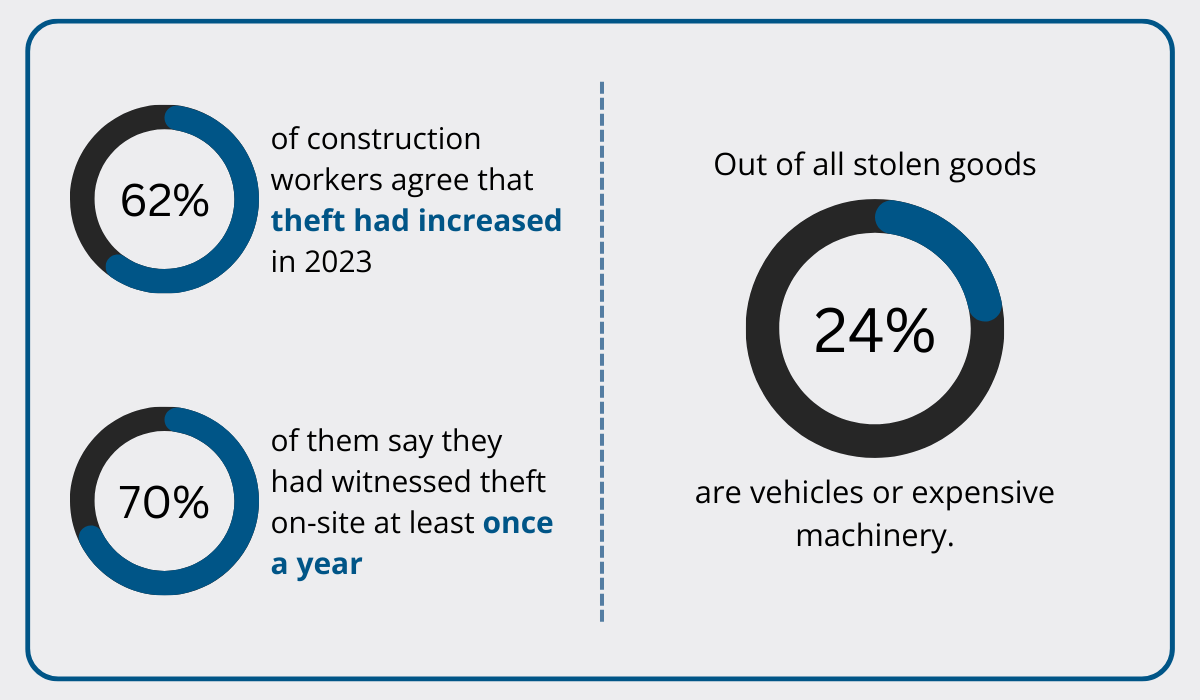
These numbers only further underscore this industry’s pressing need for robust security and theft prevention strategies.
Geofencing should definitely be a part of those strategies.
Now, worry not. Although this feature may seem somewhat complex and high-tech, using it doesn’t have to be all that daunting or time-consuming at all.
In fact, with our asset management software, GoCodes Asset Tracking, you can create a geofence around your valuable machinery with just a couple of clicks.
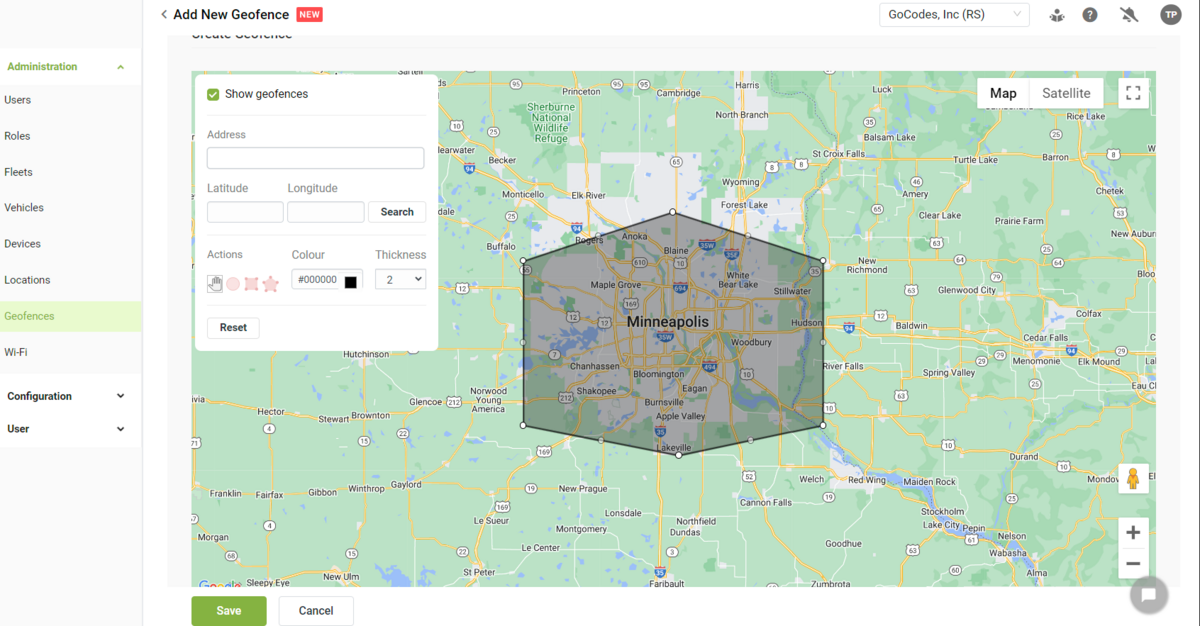
And guess what? Should any unauthorized movement occur, our system notifies you immediately.
After all, in situations involving robbery, the sooner you act, the better.
Overall, this feature represents a significant advancement in construction security protocols and can substantially improve your fleet management practices.
Therefore, when selecting a new fleet tracking system, look for this simple, yet powerful feature.
It can be a real game-changer when it comes to the protection of your assets and job sites.
Reporting Features
Reporting and data analytics capabilities empower you not only to collect information on fleet performance, but also to analyze, visualize, understand, and use that data more easily and efficiently.
Put simply, these features are your ticket to more reliable and actionable asset information that can help guide your projects in the right direction.
As Troy Dahlin, VP of Heavy Construction Segment US/CAN at Leica Geosystems, says, it’s one thing to be able to compile vast amounts of data, but another to make that info useful.
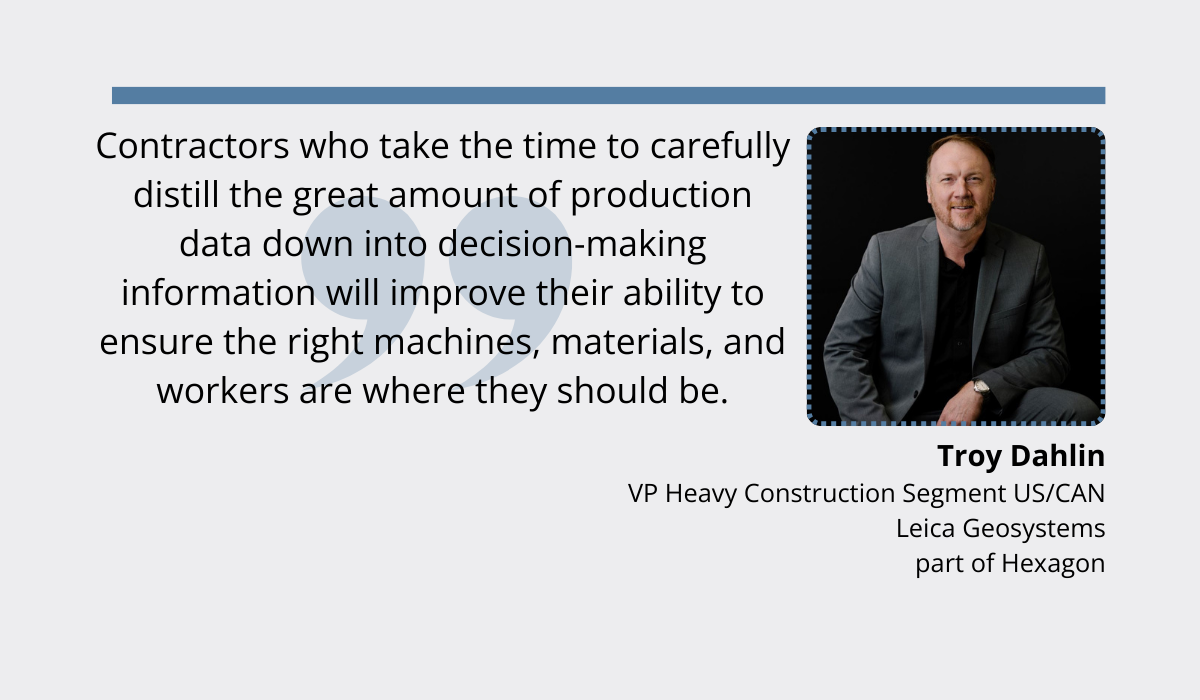
So what bridges the gap between the two?
That’s right, reporting.
With the right reporting features at your disposal, you can take your decision-making to another level and, in turn, give your entire operations a boost—from increasing asset utilization to reducing fleet management costs.
According to a Deloitte survey, a whopping 94% of construction companies already agree that data analysis significantly improves their business decisions, resulting in benefits such as cost reduction, business growth, heightened operational efficiency, enhanced worker safety, and much more.
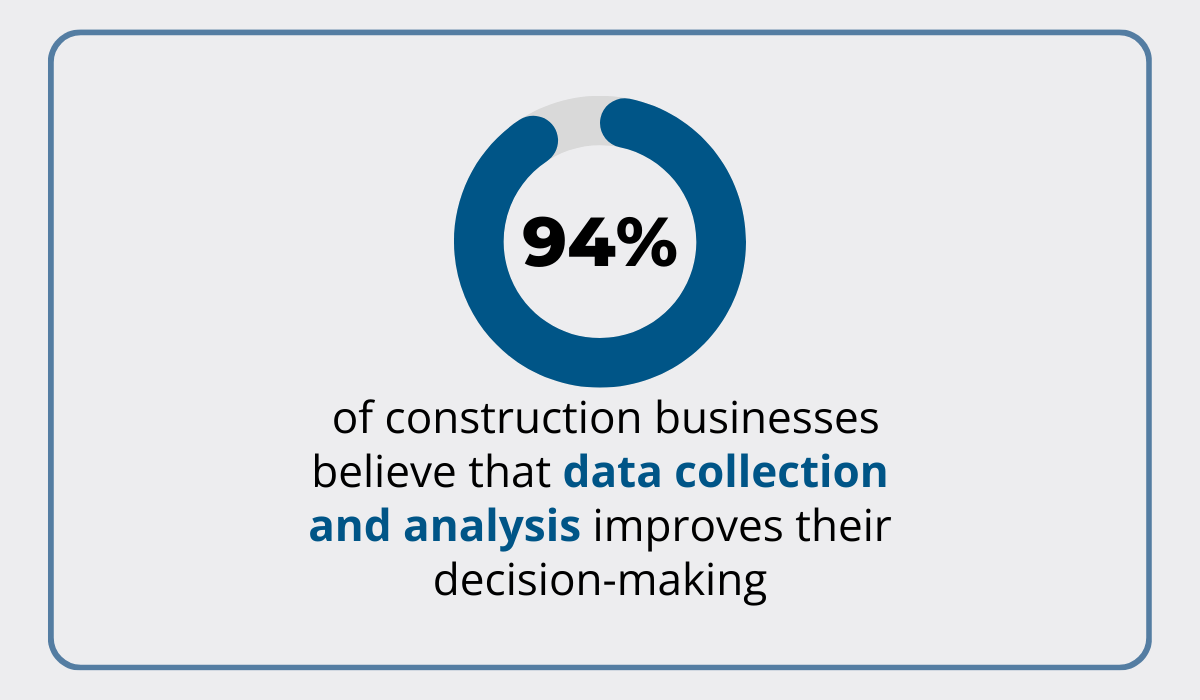
Why should you and your fleet miss out on those perks?
Look for a fleet management system with robust reporting features capable of thoroughly analyzing and generating reports on vehicle utilization, maintenance history, fuel management, driver performance, and compliance.
Armed with such comprehensive data, you and your fleet will become practically unstoppable, driving efficiency and achieving superior business and project outcomes.
Integration with Other Solutions
Integration refers to the ability to connect your fleet tracking system with other digital solutions you use to manage your projects and business operations.
This capability considerably simplifies communication among various departments and streamlines data transfer across all the platforms your team uses, helping establish a single source of truth for all project stakeholders.
Below are specific examples of common integration options and their benefits:
ERP Systems | For quick and smooth communication across different organizational departments |
Mobile Devices | For fleet tracking, management, and data access on the go |
Accounting Software | For easier, quicker, and more accurate depreciation and fleet cost management |
Takeoff Software | For more precision in project budgeting and resource needs forecasting |
Now, to understand why this capability is so important, we need to take a closer look at what happens when systems don’t integrate.
According to a survey by JBKnowledge, when this happens, workers resort to inefficient data transfer methods such as spreadsheets or pen and paper, which are highly time-consuming and error-prone.
Even more worrying is the fact that about 15% of construction workers choose not to transfer data at all in such scenarios.
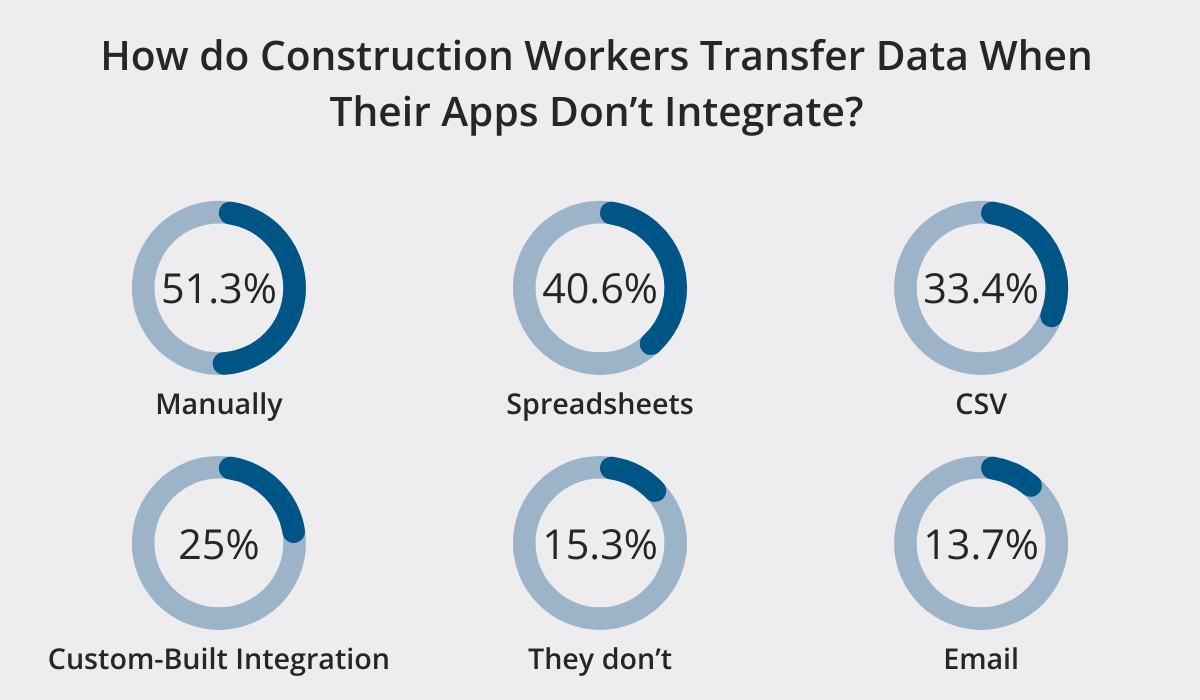
This results in incomplete, inaccurate, and inconsistent fleet data, which can lead to poor decisions and, of course, asset mismanagement.
The bottom line is this: integration isn’t just a nice-to-have bonus feature.
It’s the key to unlocking smoother communication among stakeholders, improved data accuracy, and better-informed decision-making.
Conclusion
All in all, your fleet tracking strategy holds the power to either make or break the projects you’re working on.
Neglect your machines, and you’re inviting trouble.
Expect soaring equipment costs, unexpected downtime, budget overruns, and a host of other critical issues that’ll ultimately lead to unhappy clients and even reputational damage.
However, with a bit of patience, lots of data-driven decision-making, and the right fleet tracking tools at your disposal, you can flip the script on these obstacles.
By doing so, you steer your operations away from disaster and toward success.