Even the simplest construction contract disputes can disrupt an entire project, or force you to do expensive rework after the job was supposed to be done.
Therefore, you owe it to your business and your subcontractors to carefully examine your contract and all of the “what-ifs” contained in the fine print.
Taking a long look at the contract before you sign it is the only way to avoid problems. Here are some of the things you should be on the lookout for.
In this article...
Inadequately Drafted Contract Terms
Poorly drafted contracts invite not only confusion and conflict, but also litigation and a damaged reputation.
Some contracts include language or clauses that place the blame on project managers or contractors when issues like underruns, defects, injuries and delays occur—even when your company is not at fault.
To avoid this, it’s important to hire a legal expert to parse these terms and ask for language that allocates the usual risks of construction in a fair manner.
This might cause a short delay in contract negotiations, and you may be worried about how your clients will react to it. However, rest assured that polite insistence on your rights and self-interest are more than worth it.
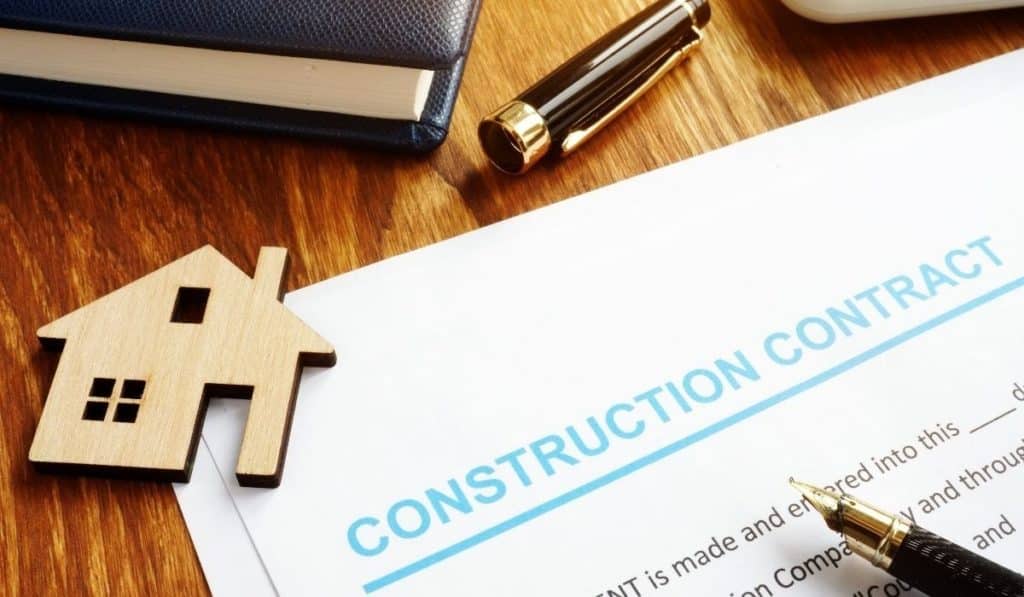
After all, there’s no going back once your signature is attached to the document.
It might seem tempting to glance over a simple two-page contract and put your name on the dotted line, but it might turn out that the suspiciously short contract fails to provide adequate coverage for simple contingencies.
So, be mindful.
Are you protected in the event of weather-related disasters or owner-caused delays? What about if the client has misrepresented the project, or doesn’t pay at specified milestones?
Inadequate contracts might leave you without redress if these issues aren’t mentioned.
Finally, as simple as it sounds, ensure that the type of contract you are signing is the correct one.
There are many different types of contracts used in the construction industry, and it’s vital to pick one that best suits the relationship between you and your subcontractor.
Here are a few different categories of construction contracts. Do any of these sound like the deal you’re about to close? If not, why not?
Type of Contract | Description |
Cost-Plus | Contractors pay for all expenses related to construction and overhead in addition to a stipulated profit amount |
Design-Build | Construction begins before plans are finalized; design and building happen in parallel |
Guaranteed Maximum Price (GMP) | Limits amount the owner/client will pay contractor; overages are paid by the builder |
Incentive Construction | Contractor receives a bonus if the project is completed before the specified date and/or beneath an agreed-upon amount of money |
Integrated Project Delivery (IPD) | Agreement involving more than one party that distributes risk, reward, and payment |
Lump Sum | Construction, design, and administration are delivered at a single agreed-upon price |
Time and Materials (T&M) | Cost is calculated by the amount of materials and labor expended |
Unit Price | Divides prices by “unit,” which could include labor costs, overhead, profit, labor, etc. |
Complex contracts might seem daunting, but an adequate legal review can help protect your interests.
Ensuring that both you and the client are legally protected is the point of a good contract—so ensure that the one you sign is doing its job.
Disputes Over Differing Site Conditions
A common phrase in construction regarding differing site conditions (DSC) is “expect the unexpected.”
What’s a DSC, and why is it so scary?
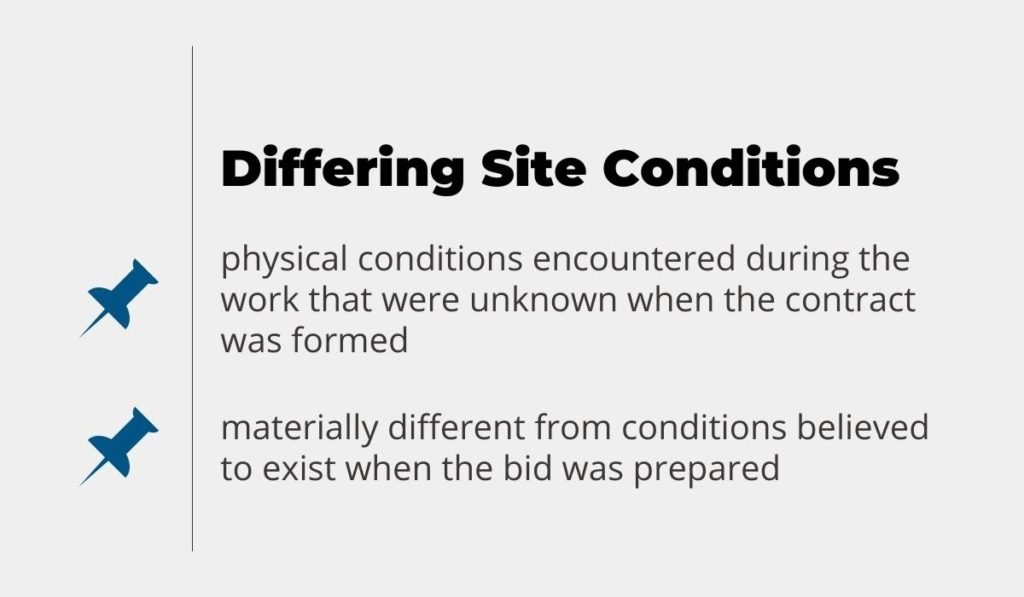
A differing site condition (DSC) is any physical characteristic of a project site that varies from what was previously expected.
Stumbling upon a DSC (also called a “changed condition”) does not necessarily mean the client or property owner has neglected to inform the project manager of its presence.
It does mean, however, that sometimes completion of a project requires timelines, materials, changes, or labor costs that vary materially from what was originally expected.
This means the allocation of additional funds to take on the DSC, right? Not necessarily.
It depends on whether or not the changed condition was specified in the contract.
A strong construction contract contains specific language that is fair to both the client and the project manager in the event that a DSC appears.
Examples of differing site conditions include:
- Soil that cannot bear the weight of the project
- Solid rock underground instead of soil
- Conditions within a building, such as the discovery of asbestos
- Groundwater
- Hazardous materials, gasses, or biohazards
- Underground rock formations or caves
- Quicksand
- Manmade objects of archeological interest
- Environmental impact roadblocks
DSC problems can make a workplace hazardous or wreak havoc on budgets. Disputes over differing site conditions have led to many costly and time-consuming lawsuits.
For example, Metropolitan Sewerage Commission of the County of Milwaukee v. R.W. Construction, Inc established important state case law in the matter of DSC.
In this instance, a contractor discovered more water than expected during a sewer project. The county declined to provide more funds, and the project came to a standstill.
The courts ultimately found for the contractor, stating that a project manager does not need to understand the underground conditions of a construction site at a scientific or geologic level.
While this particular decision limits the liability of contractors, it also clarifies what both parties consider “reasonable.”
Therefore, before starting a project, it’s also important to investigate the local and legal definition of what “reasonable” is when it comes to differing site conditions.
Lack of Proper Risk Management
Risk management is a complex, ongoing process that assiduously finds, assesses, and plans avoidance of potential hazards, as this graphic depicts:
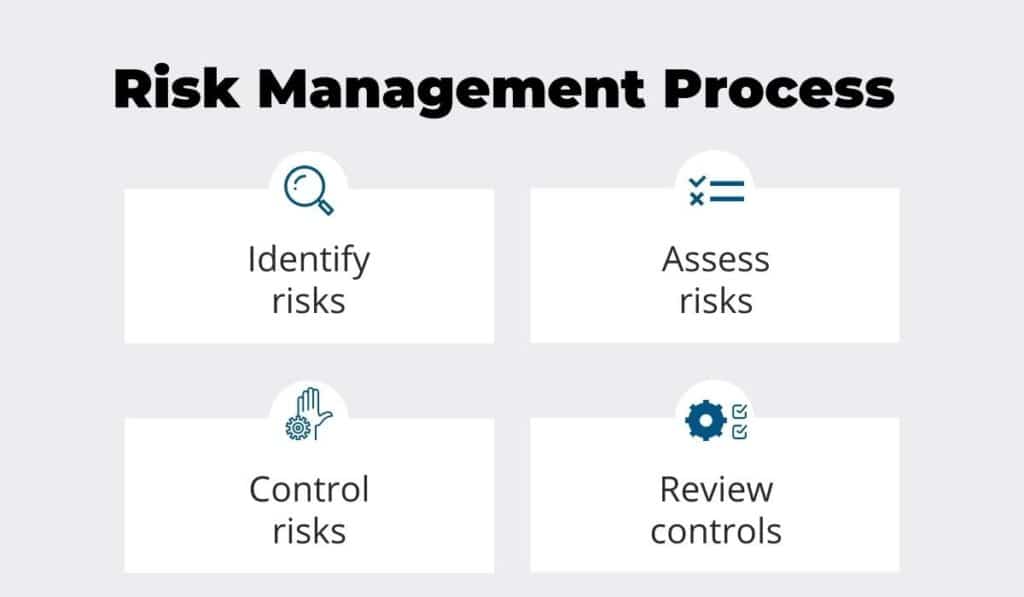
The more complex a project is, the more extensive the risk management assessment should be.
This process should take into consideration site conditions, time of year, terrain, data from similar projects, and input from safety guidelines.
When a company skips proper risk management, employees and the project itself are in danger.
Safety considerations should be continually re-evaluated, particularly in the event of discovering a DSC or receiving news of new safety codes.
One way to focus on proper risk management is to fully define risk in the contract and discuss the probability of occurrence, as well as risk impact.
Plotting these on a risk matrix helps your team to decide on the roles and responsibilities of each person involved with the project.
A comprehensive risk management plan includes:
- Deciding on which levels of risk to tolerate
- Training to minimize the existing risk
- Conducting preventive maintenance and protocols
- Implementing mitigation methods that help establish a safety culture
- Determining responses to identified risks
- Establishing contingency plans
It is important to be aware that any construction project is prone to financial, physical, and natural risks.
However, as long as you and your team have thoughtfully undertaken risk management, you can rest easy knowing that you’ve done everything you can to mitigate them.
Disputes Over Quality
Defining quality in execution is another factor to consider when undergoing contract negotiations. While some contracts include clauses that allow changes, others contain language that hampers flexibility.
However, a well-made contract will allow leeway for unforeseen circumstances, such as unexpected delays or problems in the supply chain, in good faith.
Plans, blueprints, or designs can be ambiguous or even contain errors.
Additionally, sometimes potential roadblocks aren’t considered until the project is well underway.
To combat such situations, project managers should choose subcontractors and consultants with care, and allow space in the contract for redress if findings are in error.
But sometimes the most significant obstacle to a project’s progress is the client. Clients can provide conflicting requests, coordinate poorly, provide faulty information either on purpose or accidentally, and even run out of funds mid-project.
They can also suffer from unrealistic expectations, lack understanding of the site’s characteristics, or fail to take zoning and codes into consideration.
Quality in execution is a complex concept and process, as this illustration shows:
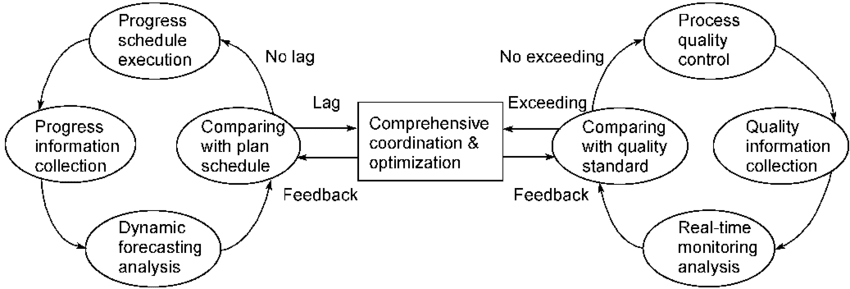
This factor of construction projects is fluid. In other words, it can change depending on site factors, client expectations, and communication initiatives. It involves real-time monitoring and analysis, quality control, and forecasting analysis.
If the contract accounts for as many eventualities as possible, the risk of conflict arising further down the line is minimal.
Understanding responsibilities, management techniques, and the scope of a project are essential in coming to an agreement on quality in execution.
Poor Employee Accountability
When responsibilities and obligations are not clearly outlined, working relationships will quickly deteriorate. This is equally true of the relationship between you and your employees, and you and the client.
Consistent and respectful communication is the bedrock of any successful project.
Strong employee accountability is directly connected to effective leadership.
If the employees don’t feel empowered to do their job properly, or if project managers don’t adhere to the rules that they have set themselves, this will give rise to a culture of disorganization.
Lax attitudes lead to a lack of respect and dismissal of details, which can be devastating to the project at large.
Building employee accountability includes clarifying expectations, as well as ensuring that the workforce has proper training and access to the necessary tools.
Just like risk management or safety monitoring, maintaining accountability is an ongoing process, as depicted in this illustration:
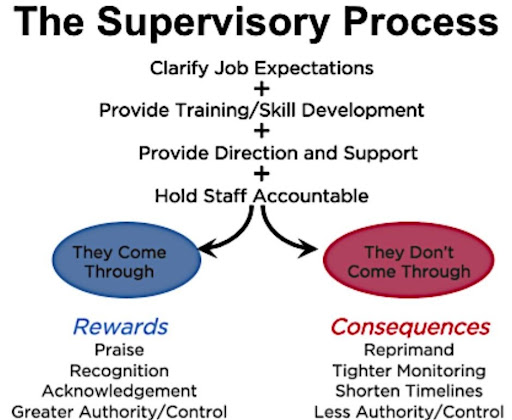
Accountability also involves delineating who is at fault in the event of a problem or reportable incident. Sometimes this even involves legal obligations.
Site owners are generally not considered responsible for the safety of employees on a construction site; this liability usually transfers to the contractor once work begins.
Case law tends to side against project managers in the event of subcontract work.
For example, in Beil v. Telesis Construction, Inc, a subcontractor fell from scaffolding while attempting to fix a roof. A separate subcontractor installed the scaffolding.
The employee, who suffered a concussion and other serious injuries, sued not only the contractor and the other subcontractor, but also the site owner.
Courts ultimately found that only the site owner was not responsible for the accident.
As this example demonstrates, attention to detail and employee accountability are crucial when arranging complex projects.
Disputes Over Payment Claims
Disputes over payment claims in construction can take any number of forms, and none of them are pleasant. Especially in major projects involving multiple parties, payment disputes can drag on in courts, holding up projects and draining resources.
The first step to avoiding payment claims is to provide protection and clear definitions within the contract. Establish a timeline and payment milestones, along with provisions for changes if necessary.
Answering “what ifs” in the early phases of negotiation can de-escalate disputes before they even begin.
However, respectful and effective communication between disagreeing parties can save not only court costs, but valuable time.
While the knee-jerk reaction to a disagreement—especially one involving payment—may be to file a lawsuit, it is often faster and less expensive to rely on standard payment forms, which provide details and verification of a contractor’s claims.
Here’s an example of a standard payment form:
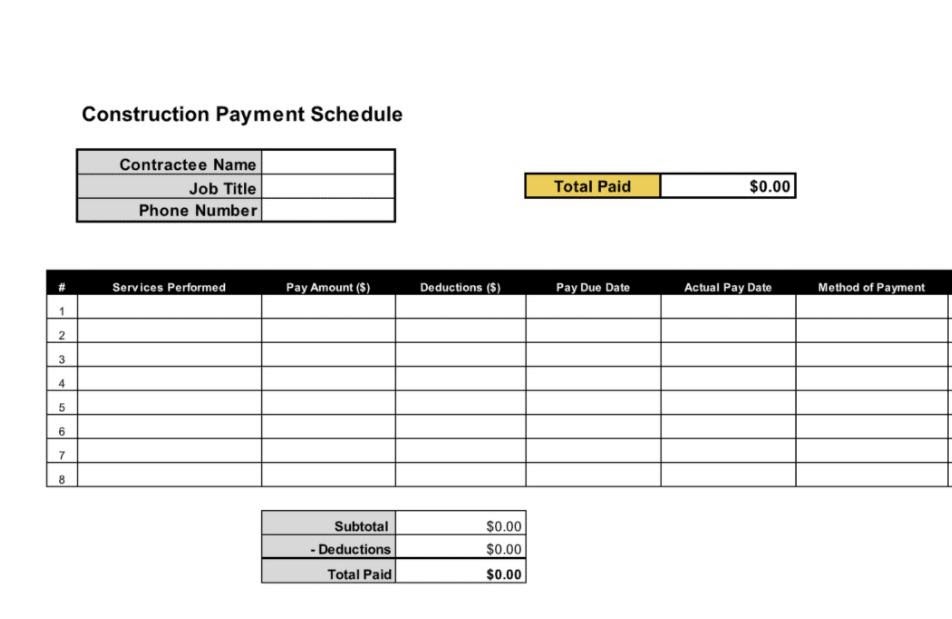
Such invoices and payment schedules are best managed with a software system that automatically tracks expenditures in real time, then securely stores the data in the cloud.
Also, working with inventory management software with GPS real-time updating, such as GoCodes Asset Tracking, helps ward off legal challenges by providing equipment delivery updates, employee location statistics, and details about unit costs.
Conclusion
Forward-thinking project managers can avoid payment disputes, legal challenges over site condition differences, and misunderstandings by committing early to a workable and sensible contract.
Ask legal experts for help to ensure the contract contains provisions for any circumstance that could hinder the progress of your project.
The contract should cover everything from liability in case of differing site conditions and other unforeseen dangers in the worksite, to disputes over quality and payments.
In any case, being aware of the most common causes of construction disputes will help you better prepare for your next project and mitigate risks on and off-site.