Asset tagging is a key part of efficient asset management.
Without proper tagging, companies can’t keep an eye on their valuable machinery and critical equipment as it moves across job sites, which leads to equipment losses, and project delays.
Fortunately, effective use of different tags and tracking methods enables you to mitigate the risks while also reaping additional benefits.
In this article, we’ll explore five essential asset tagging practices that can transform every construction business.
Without further ado, let’s jump right in!
In this article...
Categorize Your Assets First
Asset tagging begins once you have full insight into all the physical assets you own and manage, and the categories they fall under.
This is the perfect opportunity to classify your assets into distinct categories and make a preliminary list of what you need to tag.
These categories serve as a preview that will help you determine the most suitable tagging technology for each asset type.
As such, you can start with fairly broad categories that you can input into the system and change later.
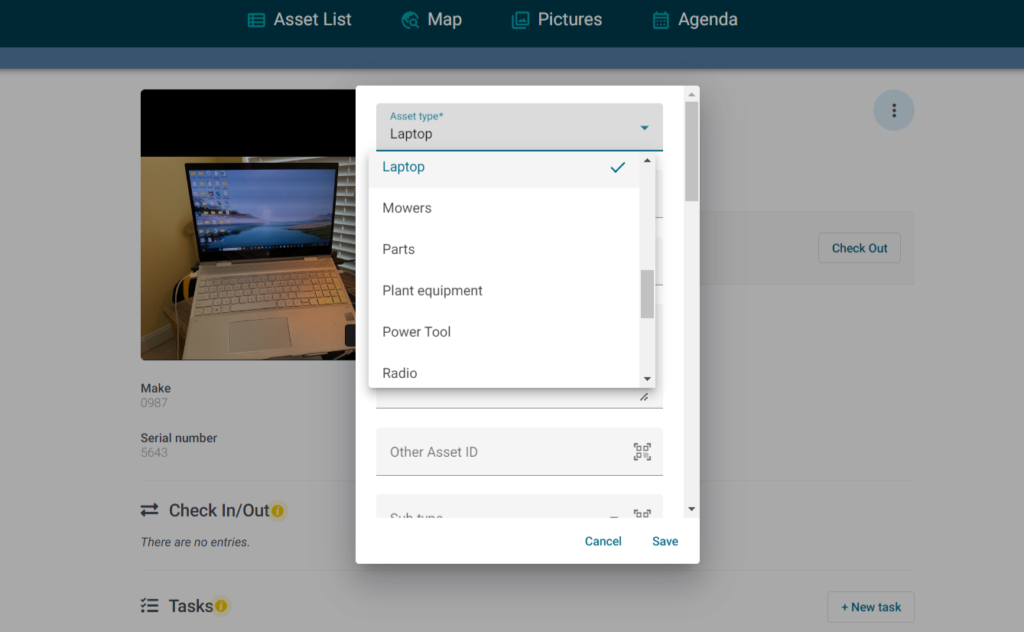
Alternatively, you can draw up a more detailed categorization, and pinpoint distinct subgroups of assets.
Heavy Equipment | Dozers, excavators, graders, skid steers, cranes |
Vehicles | Trucks, utility vehicles, trailers, vans |
Power Tools | Drills, jackhammers, saws, welding machine |
Hand Tools | Wrenches, hammers, shovels, spades |
Attachments | Buckets, blades, augers, hammers |
Safety Equipment | Hard hats, safety vests, steel cap boots, gloves, harnesses |
Consumables | Fuel, lubricants, cables |
Technology Assets | Laptops, tablets, mobile phones, drones, GPS trackers |
Temporary Structures | Scaffolding, site offices, fencing |
Office/Site Furniture | Desks, chairs, storage units |
To make everything run smoothly, here’s how we can organize the process in three steps:
- assign tasks and responsibilities to several team members,
- conduct a structured site-by-site inventory audit, and
- verify and standardize data.
The last step will also help you catch costly ghost assets and document any inconsistencies before you introduce tagging.
After you do this, you’ll ensure you’re using the best and most relevant tracking methods.
Carefully Consider Which Assets to Tag
Prioritizing which assets to tag is another essential practice.
Even smaller construction businesses manage numerous assets, from multiple sets of tools and scaffolding to large volumes of consumables.
But you don’t need to tag and track all of them.
To determine which assets you do need to tag, ask yourself:
- How valuable is this asset?
- How often is it moved around?
- How critical is it to our operations?
These questions can act as your tagging criteria.
They will ensure you’re prioritizing assets that are costly to repair or replace.
In addition, you’ll add a layer of security for the pieces that are particularly exposed to theft and loss and/or are essential to operations.
Equipment theft is a major risk for construction companies, as evidenced by the number of incidents reported on Memorial Day last year.
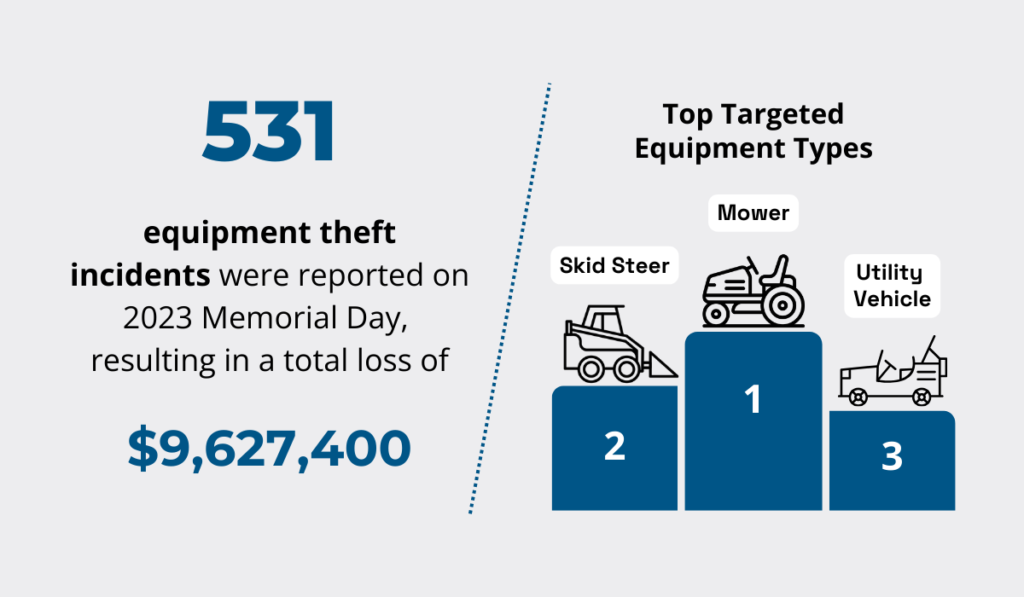
According to the National Equipment Register (NER), the losses amounted to over $9 million, but it’s particularly interesting to note which equipment was targeted.
While heavy machinery that’s easier to move is often on the thieves’ radar, BauWatch’s 2024 construction crime report also shows that small tools emerged as the most commonly stolen pieces of construction equipment.
This is in large part due to how frequently tools move all over the site, making them easier to steal or misplace accidentally.
Therefore, you should balance things out, and tag both the most expensive machinery, and those smaller tools that are most likely to get lost or stolen.
Construction materials and fuel are also frequent targets of theft, as shown by the recent case in Hoima, Uganda where the stolen fencing materials were luckily recovered, but still caused significant delay in the project.
So consider tagging consumables as well.
To simplify this, you can bundle some items into kits and tag them as one group. Then, you’ll treat the whole group as an individual asset.
The bottom line is this: while you could tag all your assets, start with those that are most valuable to you and those that are most prone to different risks.
By tagging the right assets, you will be able to minimize disruptions, while also increasing the overall efficiency of your operations.
Select the Right Type of Tags
Next, you should choose the right type of tags.
Making the right choice requires thorough research, and starts with these considerations:
- Asset’s nature and usage
- The environment
- Tracking range
- Budget
With the right criteria in place, you’ll be able to confidently determine your preferred tag type.
We’ll be taking a look at QR codes, real-time GPS trackers, Bluetooth Beacons, and RFID.
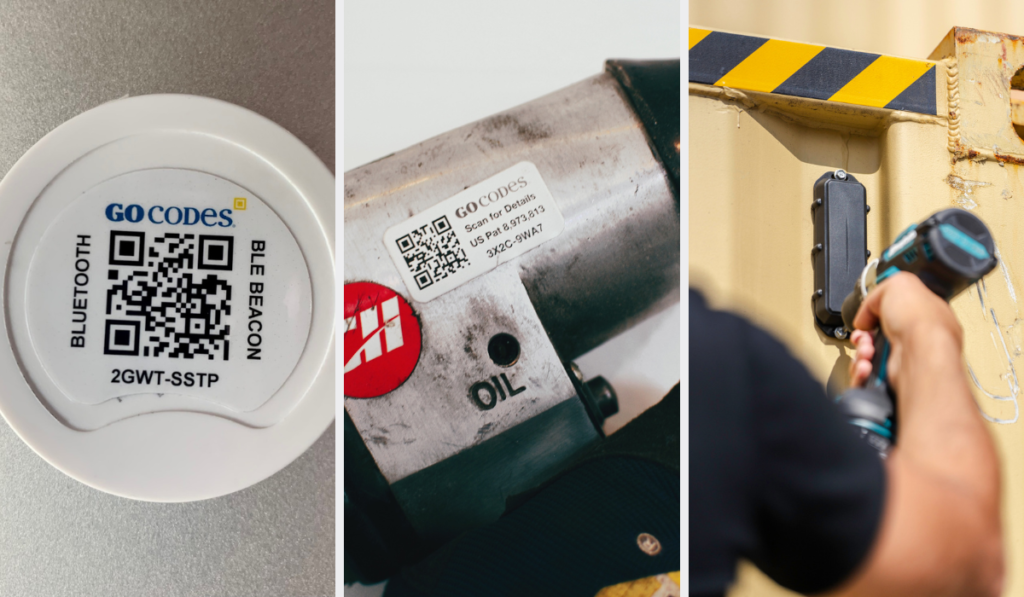
QR code tags are affordable, versatile, and quick to deploy.
They also don’t have to be replaced often because they’re made of high-quality, durable materials.
For example, metal asset tags are capable of withstanding harsh outdoor conditions for many years.
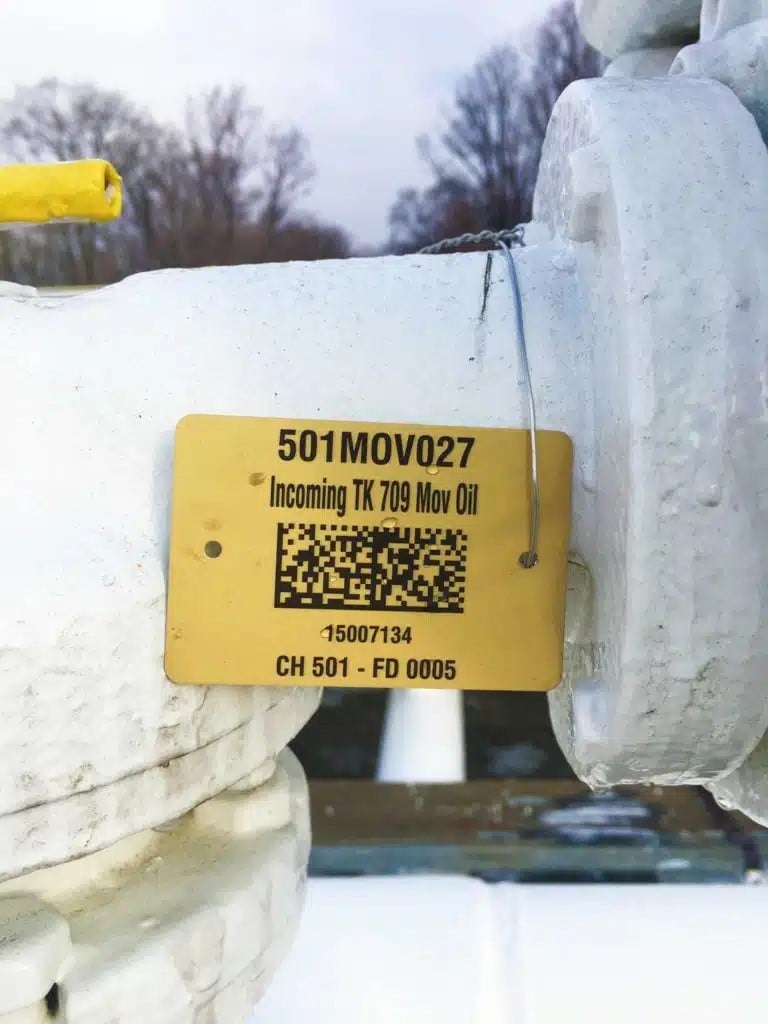
Think of QR codes as a miniature, self-contained database with relevant information on each asset.
A quick scan with your mobile app is all you need to get information on the asset, assign tasks, and much more.
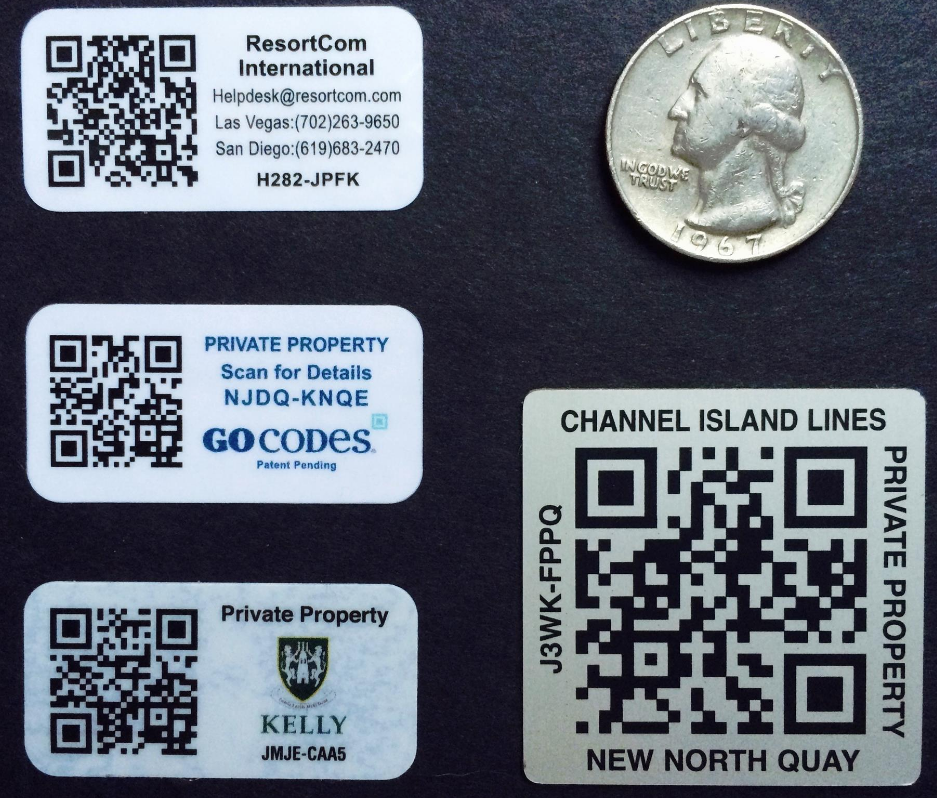
However, while QR-coded tags are GPS-enabled and can obtain location data, they lack minute-by-minute insights.
This is why the most valuable assets are usually equipped with real-time GPS trackers.
Knowing the precise location of mission-critical equipment is essential for efficient operations and logistics.
Moreover, these trackers are indispensable for theft prevention and usage monitoring.
Solutions like GoCodes Asset Tracking come with integrated telematics and geofencing features that ensure you’re collecting a wealth of data, from vehicle management and safety to driver behavior.
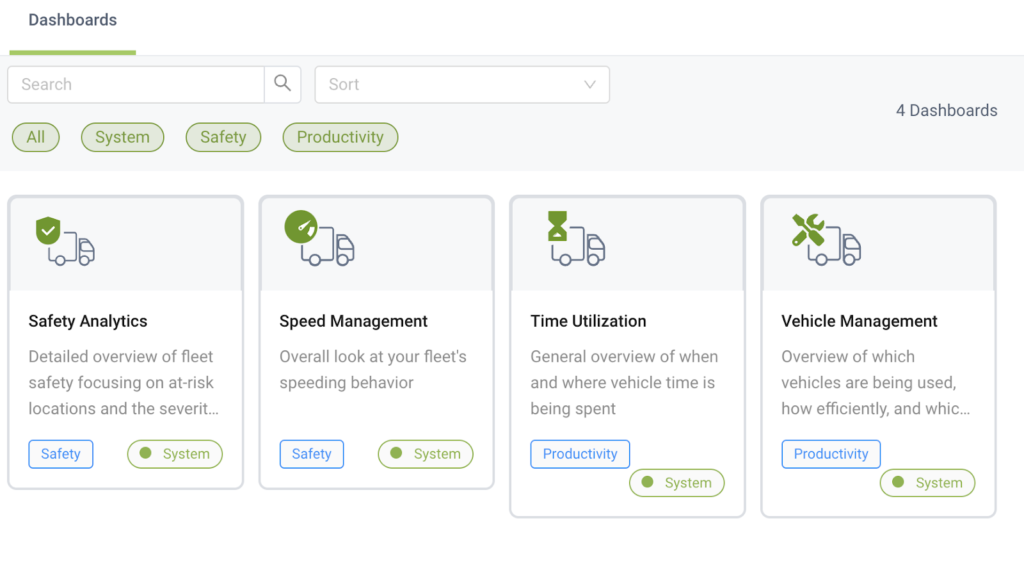
On the flip side, the size and costliness of GPS trackers mean they aren’t suitable for smaller tools, or non-essential machinery.
Next up, we have Bluetooth Beacons (BLE).
This wireless technology doesn’t rely on scanning but uses radio signals for automatic asset discovery in both indoor and outdoor settings.
Bluetooth Beacons offer a cost-effective and energy-efficient alternative to real-time GPS trackers, but there is a catch.
The system allows only short-range and proximity-based tracking.
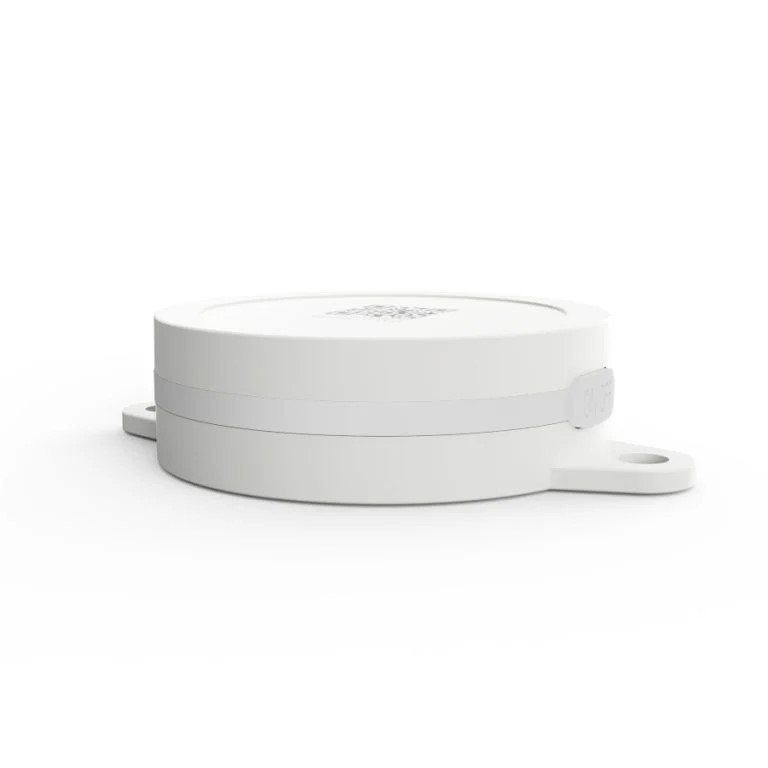
So this won’t help you track assets that frequently move across large distances or when you want to cover bigger areas.
However, beacons can help you if you’re working in enclosed spaces or on smaller sites.
Finally, we have RFID (Radio Frequency Identification) technology comprised of three main components:
- RFID reader,
- RFID tags, and
- RFID software.
The system supports scanning out of the line of sight and enables you to quickly read multiple tags and account for a large number of assets.
Most importantly, it ensures high accuracy in tracking assets and provides real-time data.
Nevertheless, integrating RFID with your existing systems may prove challenging because of the steep prices of this technology.
While you can choose between passive and active RFID tags which have their own power source, you may still encounter scrambled readings near a water source or a large metal structure.
However, RFID can be effectively deployed in warehouses and similar spaces.
Keep in mind that you can always combine different asset tags.
The key is to understand the opportunities and limitations of each tag type and determine whether they align with your current needs.
Connect Essential Asset Information to the Tags
Asset tags are only a bridge to essential asset information because they can only show the data you provided in the system.
Start by adding basic information such as:
- Asset ID number
- Asset name and description
- Model and serial number
- Date of purchase
- Add asset photos
To aid equipment lifecycle management, it’s helpful to add additional information such as the original purchase price, salvage value, and current value, as well as all documentation and warranties.
Any information you add will be available at a glance after scanning the asset tag, along with the equipment’s current custody status.
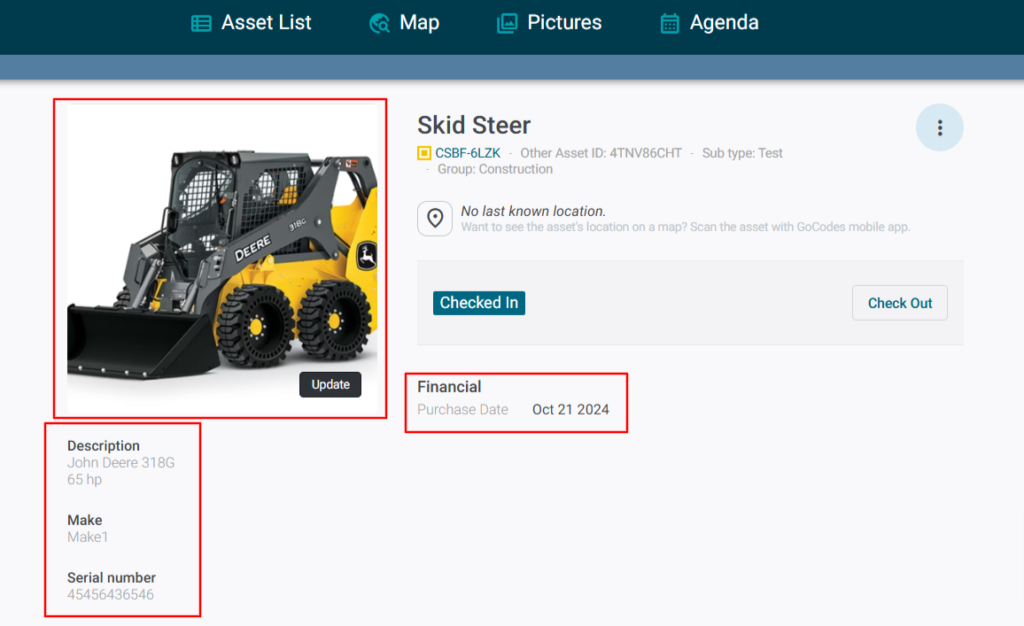
The majority of asset management systems let you customize the data fields and add additional information.
For example, you might add maintenance-related information.
Then, you will have an overview of maintenance and service history, including the last service date or next scheduled maintenance.
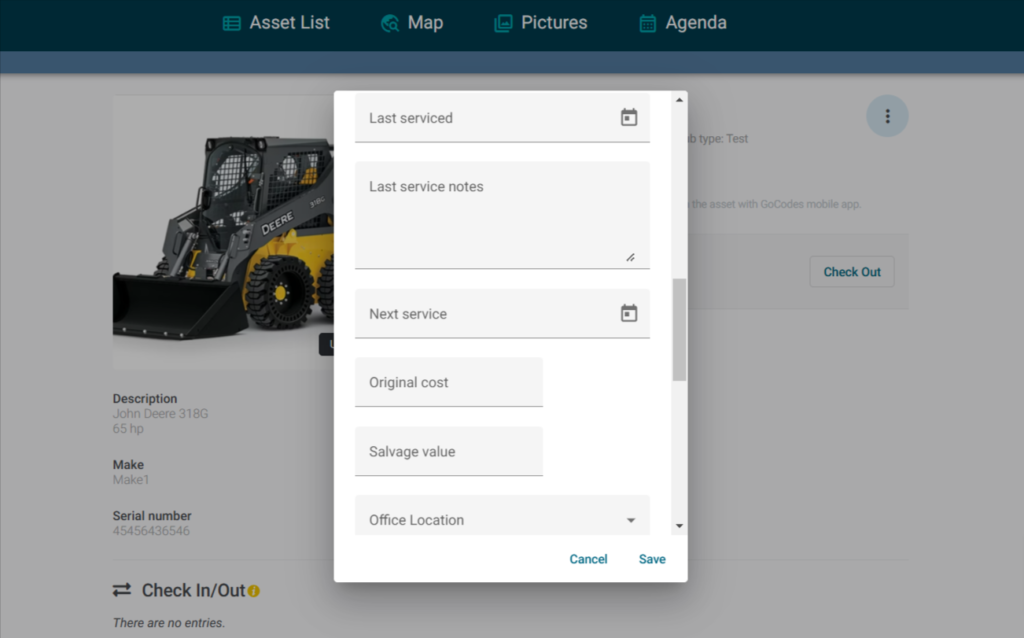
That way, your workers can simply use a mobile app to scan the tag and access the latest service information, updating it if necessary.
Such comprehensive insights are far superior to using multiple spreadsheets that often contain inaccurate or outdated information.
Autodesk’s Matt Racher, an experienced assistant project manager, highlights one of the main limitations of Excel spreadsheets when it comes to asset tracking and construction project management in general.
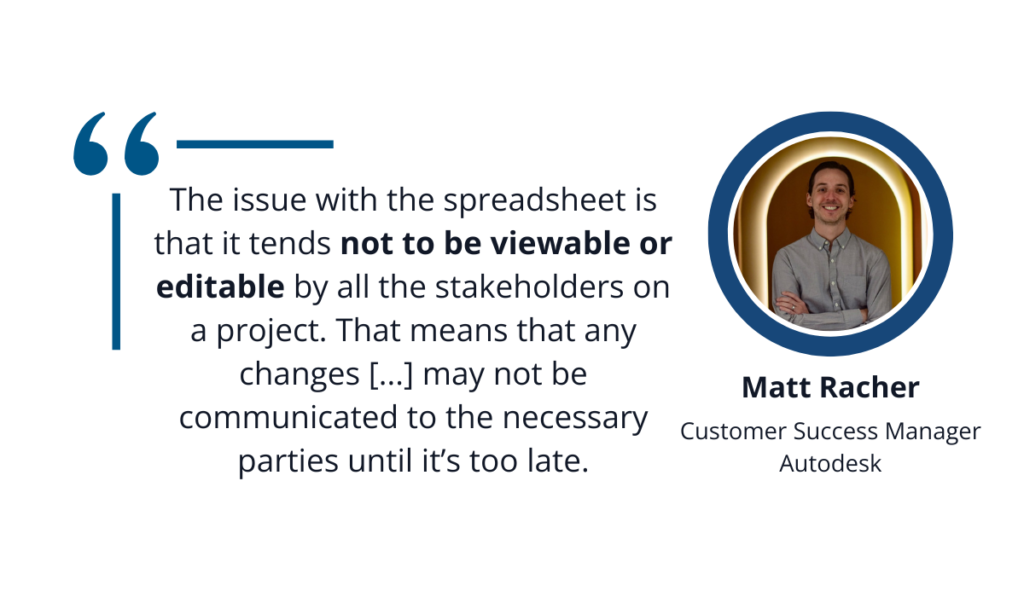
Although Racher primarily talks about broader project management issues, the lack of information on available equipment can easily lead to unnecessary idle time and similar delays.
With tagging, you’re making sure everyone on the field and in the office can quickly access relevant information from any device.
Say the logs show a potential issue with the nearest compressor, the worker will know to use another one until a full inspection can be conducted.
The bottom line is that data received through asset tags should enable the following:
- location and usage tracking,
- maintenance, and
- reporting.
Tags and trackers give you information about all asset locations and usage, accessible from a single map on your dashboard.
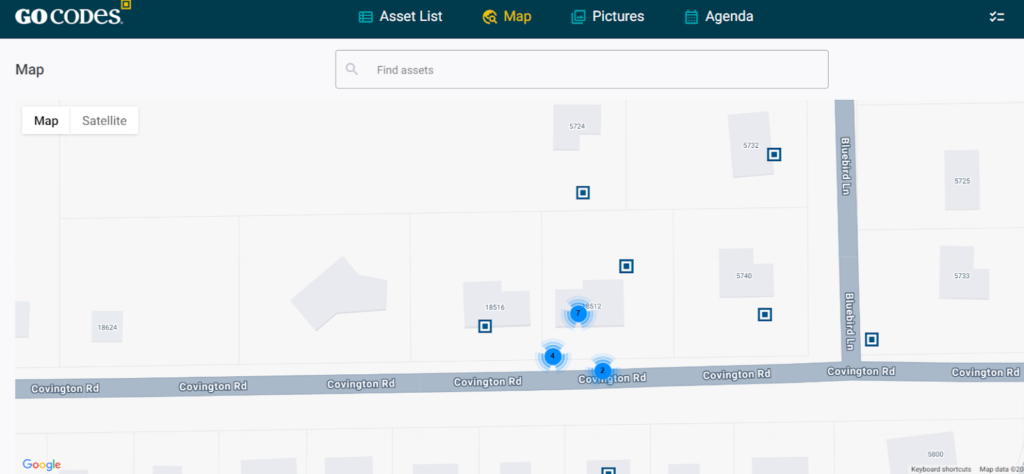
In conclusion, asset tags can become your greatest allies, but only if you keep your data in one spot and easily within reach!
Place Your Tags Strategically
The right location contributes to accurate tracking and data consistency because the hidden tags won’t get scanned, derailing the overall effectiveness of asset tagging.
Therefore, a lack of forethought in this area can minimize the positive effect of previous practices.
The aim is to make sure that the tags stay fixed, and are easy to access for scanning, like in the example below.
The tag is visible and easy to find, which brings us to another important point.
Asset tags shouldn’t hinder regular equipment use or maintenance in any way.
An optimal placement means that the tag is visible and easily accessible, doesn’t get in the way of equipment use, but is also protected to maintain its durability.
GoCodes Asset Tracking has an array of labels made of durable material, including:
- Polyester, tamper-evident tags
- Rugged metal labels
Since these can’t be easily removed, and certainly not without leaving a trace, they can be safely placed in a visible spot.
Then, they effectively communicate that the asset is tracked and can’t be resold without detection, acting as a theft deterrent.
GPS trackers also discourage theft, but their placement is typically more discreet than QR codes. Sometimes even entirely concealed.
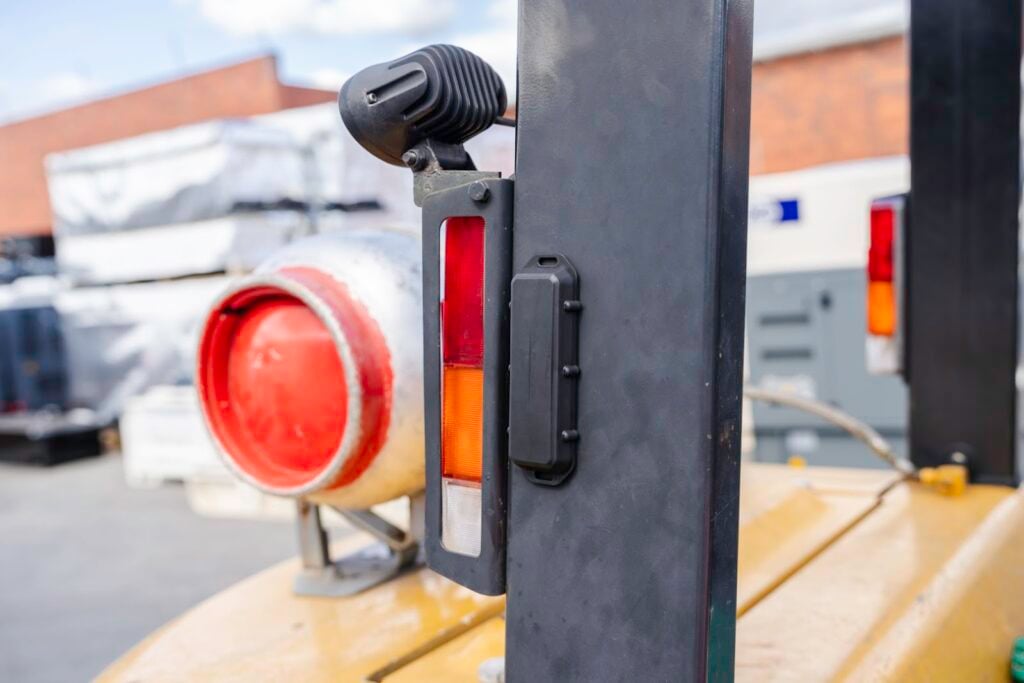
That might be a smart move as theft is also becoming more sophisticated, including ways of detecting and disabling GPS trackers.
For instance, trackers don’t have to be physically removed.
Thieves can just use GPS signal jammers or block the signal in other ways.
Of course, more advanced systems can send immediate tamper alerts, but concealing the tracker is an effective countermeasure because it increases the chances of trackers staying operational and aiding retrieval.
If you’re hiding a GPS tracker, it’s important to keep in mind signal-related issues that can occur around metal, as explained by one of TekamoHD’s mechanics, a company specializing in heavy equipment services.
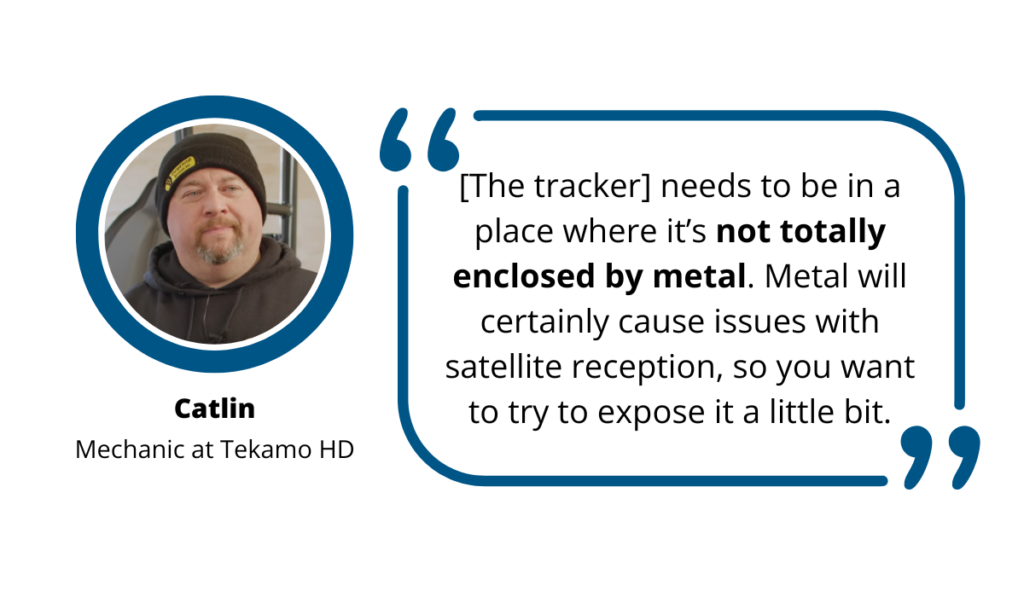
To sum up, be mindful of how accessible your tags are, and make sure you don’t hinder the functionality of either the asset or the tag!
Conclusion
Asset tagging drives efficiency and bolsters your equipment security.
The five practices we’ve outlined build on each other, underscoring the value of cohesive asset management strategies and careful planning.
A well-thought-out tagging strategy is based on priority asset categories and an in-depth understanding of tag types and their placements.
It helps you make the most of different technologies and collect valuable data.
We trust that this article equipped you with the necessary knowledge to maximize your asset usage, stay on track with the projects, and set strong foundations for future growth!