The construction industry depends on proper maintenance.
Without it, everyone would be running their equipment to the point of failure and spending a lot more resources than necessary in the process.
Nevertheless, 44% of companies continue to outsource at least some of their servicing.
The main reasons for this? A lack of in-house time, personnel, and skills to perform maintenance.
Since you’re reading this article, it’s clear that you’re determined not to let this happen to you.
Luckily for you, the servicing process is something you can teach and simplify. This article will show you how to do it.
In this article...
Why Educate Your Staff on Maintenance Training
If you’re unsure why your maintenance team can’t just learn their trade on the go, you’ve come to the right place.
So, let’s get to work and figure out the importance of proper maintenance training through some statistics. These numbers will help you put things into perspective.
- Equipment operators cause 18% of all unplanned downtime. What does this mean for your business? It means that investing in operator training, can eliminate at least 18% of unscheduled downtime in your company.
- Companies that offer detailed maintenance training programs have a 218% higher income per employee than those that don’t. Sure, such training will cost you, but you can’t deny those results are promising. If you earn 218% more per employee, you’ll likely cover the initial training costs.
Now let’s see some of the ways in which offering detailed education to your maintenance staff pays off.
First, training your staff guarantees that you have an educated team. Such a team is invaluable if you consider how much downtime is caused by employee errors.
Investing in your team’s knowledge pays off because they will be quick to notice when something is off and know how to perform the necessary repairs.
Second, staff education helps reduce equipment damage. An employee who knows how to properly use and repair machinery is less likely to damage it. This makes your equipment overall more efficient and reliable.
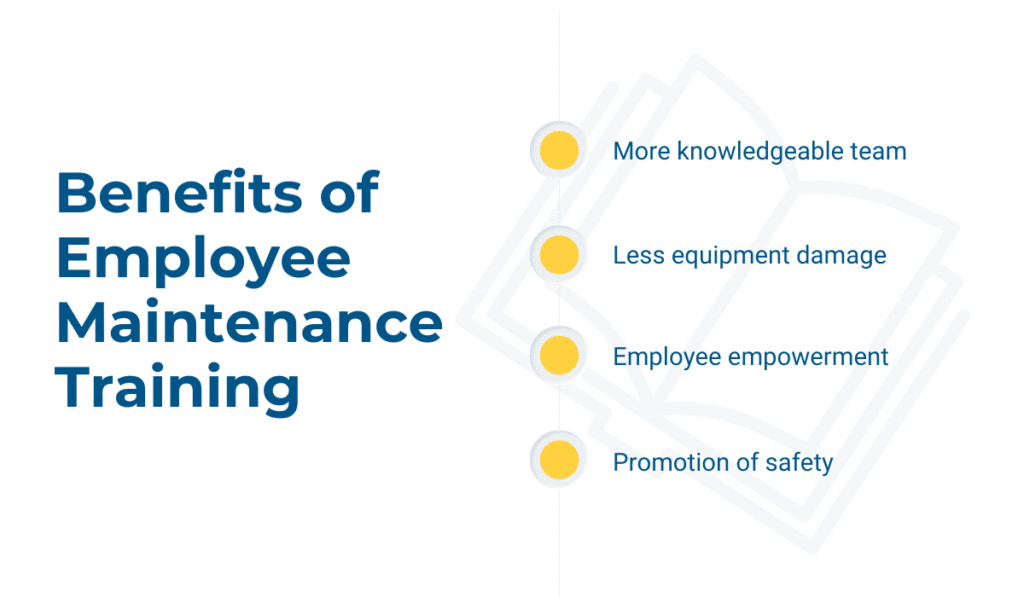
Additionally, training can benefit your employees in many ways, including the fact that they will feel more empowered to do their job. This, in turn, makes them less likely to leave your company.
The general rule is: the more you invest in your employees’ development, the more motivated they will be to stay.
Studies confirm the same thing. When companies prioritize learning, employee retention rates go up by 30-50%. And not only does retention ensure that you have competent people on your team, it also saves you money in the long run.
The final benefit of proper training is your team’s safety.
In 2019, the maintenance and repair industry reported 21,490 injuries that led to time off work. Do you really want your employees to be a part of that statistic?
Invest in training that will show them how to safely use and fix machinery.
However, avoid the pitfall of putting your team through various courses just for the sake of it.
Remember that ineffective training costs up to $13.5 million per year for every 1,000 employees. In other words, inadequate training can be just as costly as no training at all.
So next, we’ll talk more about how you can make sure that the equipment maintenance education you offer is worthwhile and, above all, applicable for your team.
Understand Different Types of Equipment Maintenance Education
Before implementing employee maintenance training, you have to get familiar with different forms of employee education at your disposal.
You shouldn’t just opt for in-house training because it seems like the easiest and cheapest option. Instead, it would be wiser to explore different training methods and then determine which one best suits your company’s needs.
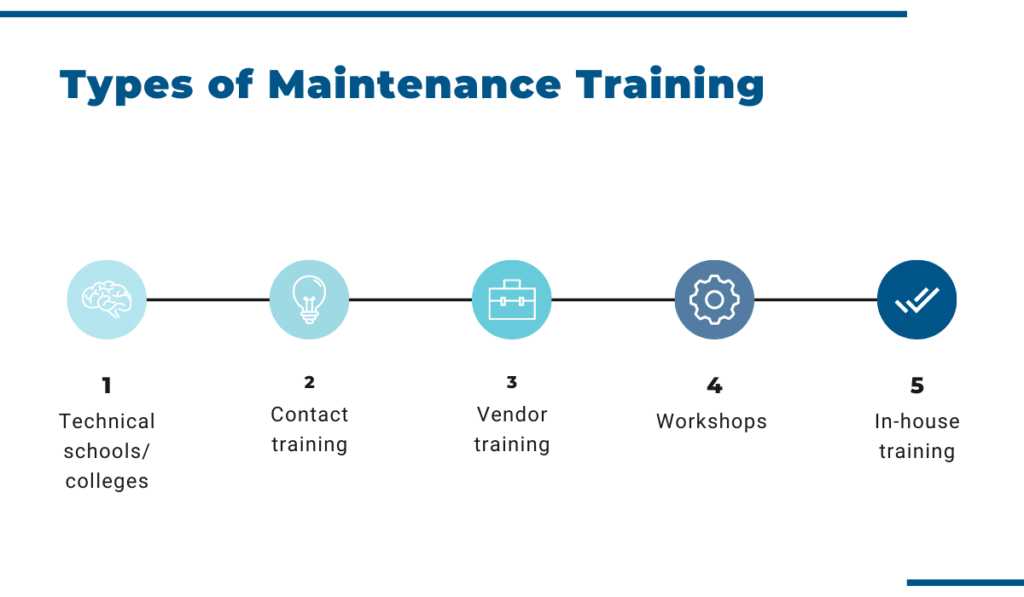
Equipment maintenance training programs can be any of these:
Technical schools/colleges mean you can send your staff for training instead of educating your team in your own company. This way you entrust them to professionals at a specialized institution. Of course, you will have to arrange all the training details with the staff there to make sure the training program suits your needs.
Contact training lets you hire professional trainers to teach your staff how to keep your machinery in optimal condition. Even though the training firm specializes in offering this kind of service, you should still go over the training plans with them to make sure they’re adequate.
Vendor training is where your team gets educated directly by a vendor or manufacturer. This is highly beneficial when you obtain completely new equipment. Who knows how to make the most of a piece of equipment better than the people who created the machinery or specialize in selling it?
Workshops help your team get precisely the type of information they are missing. Such training is held by an expert who develops the program in agreement with you or the person in charge of training.
In-house training means you organize your staff training at your facility and use your in-house team to teach. The person teaching should be a maintenance expert to ensure a smooth transfer of knowledge.
No matter what type of training you provide for your employees, there’s one thing you should keep in mind, and it’s this:
Ensure that what you teach is actually relevant for the trainees.
Research shows that a meager 12% of employees apply the skills they were taught during professional development. In other words, 88% of trainees were trained on things they can’t even use in their everyday work.
What is more, a whopping 62% of trainers believe that the training doesn’t meet the needs of attendees!
So, why waste their time with something they won’t use? Prioritize your employees’ needs when creating a professional development program.
Let’s find out how you can do that!
Leverage Manufacturer’s Manuals
If the knowledge you convey to your employees during training doesn’t include the manufacturer’s instructions, you’re doing it all wrong.
Neglect those instructions, and your team won’t even know how to use the equipment correctly, let alone repair it.
Why are we so sure? Because the manuals include detailed information on:
- Proper equipment usage
- The suggested equipment maintenance schedule
- Proper maintenance
- Equipment limitations
These are all vital points your team has to know about before using or repairing the machinery.
The Occupational Safety and Health Administration (OSHA) fines businesses that fail to follow the manufacturer’s recommendations.
Just look at Sunfield Inc., a car parts manufacturer that had to pay a $3.42 million fine for not training operators on how to use and service equipment safely.
Yes, you’ve read that right—$3.42 million!
Their negligence caused two severe injuries in the workplace, which is why OSHA stepped in.
Therefore, the manufacturer’s instructions are an indispensable part of maintenance team training.
But here’s the scary part: most of the time, they’re not enough.
You can stick to the manual only if you use the equipment precisely as recommended. Otherwise, you’ll have to make some adjustments.
Don’t worry; we’ll help you figure out what to consider!
When teaching your team how to use and repair equipment, you should incorporate these instructions into your maintenance plan. That will let your workers see the bigger picture and allow them to proceed in any situation they find themselves in.
However, your company’s maintenance plan will work best if you base it on:
- manufacturer’s recommendations
- information on the frequency of use
- weather conditions
- equipment age
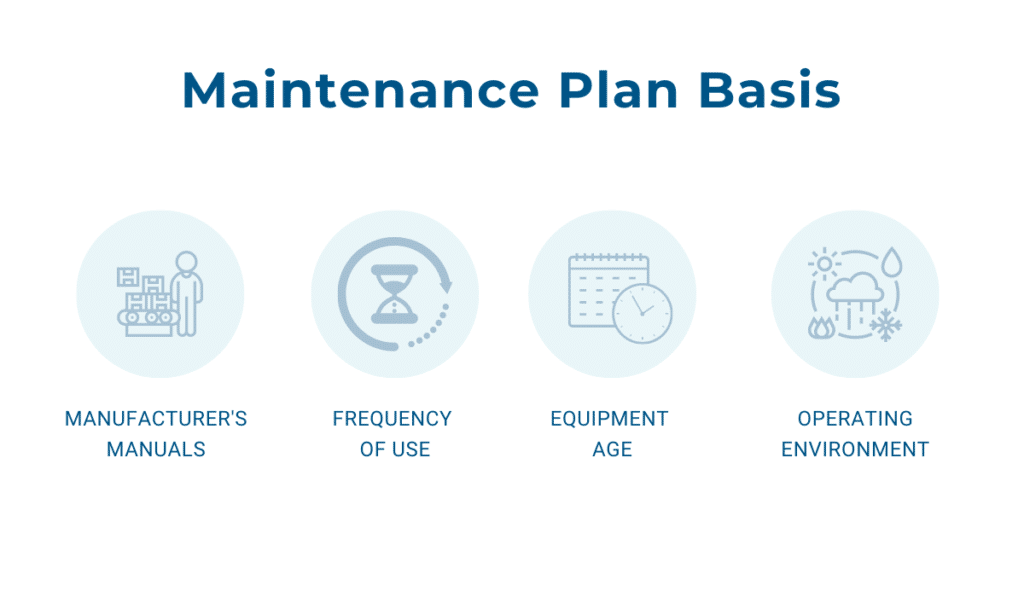
All of these points can make a difference.
The manufacturer’s manuals should be the basis of any good maintenance plan as they contain all the basic data relevant to equipment service.
However, additional factors also shape the need for regular maintenance, such as frequency of use. If you use a piece of machinery more than recommended, it stands to reason that the servicing should happen more often, too.
Of course, if you rarely use specific equipment, then you can adjust the maintenance schedule accordingly, but only after careful consideration.
The age of your equipment also plays a part: the need for maintenance will increase the older the machinery is. You can’t afford not to service your older equipment as you’re risking the safety of those who use it.
Finally, the operating environment can also impact your maintenance plan. Equipment that is constantly exposed to colder weather will need different types of maintenance than that which is used in above-average temperatures, especially compared to machinery used in normal conditions.
When you take all that into account, you’ll be better able to leverage the information you possess and teach your employees proper maintenance.
Have Updated and Detailed SOPs
Are your standard operating procedures (SOPs) outdated? If they are, so is your training, and your maintenance isn’t any better.
Your SOPs are put in place to make sure your service is uniform and consistent. Employees A and B should have the same results when inspecting the same piece of equipment, and you can ensure that by asking them to follow your SOPs.
However, if you don’t invest in updating your SOPs and new additions get around by word of mouth, you’ll lose your uniformity. Employee A will use the new version, while employee B sticks to the old one. Sooner or later, this will result in chaos and cause safety hazards.
Because of all of this, you should make your procedures as detailed and optimized as possible.
The more details there are in your procedures, the easier it is to follow them. In other words, there is less room for mistakes and improvisations if you write down the whole plan in detail.
But, how can you optimize the plan?
To do that, you first need to track your maintenance.
Nowadays, this is fairly easy because you can use software that allows your team to upload maintenance session results into the system. That way, these results are available whenever you access the equipment’s page.
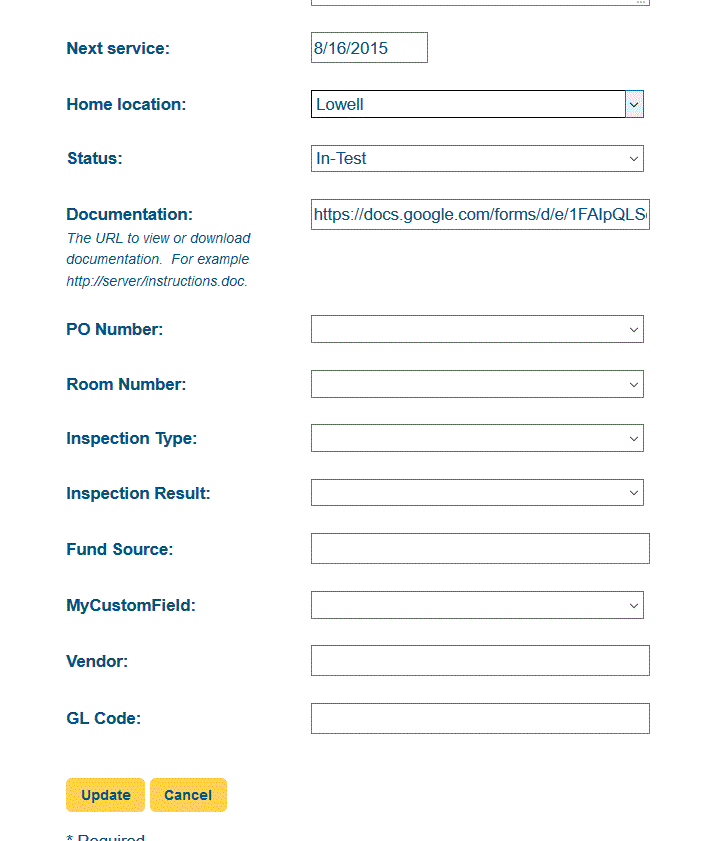
Over time, your system will store enough data for you to do reports and notice patterns or discrepancies. Once you figure out which part of the process to improve, it will be easy to upgrade.
What does this mean for your service process? That it will be prone to change, which directly affects training.
After all, you’ll have to regularly present all of the continuous adaptations and improvements you make to your SOPs to your team. Otherwise, what’s the point of making those changes in the first place?
You should share the new SOPs with the team during training if you want everyone to start using them as soon as possible. Therefore, education has to be a regular occurrence in your company and not just a part of the employee’s onboarding process.
Involve Equipment Operators in Upkeep
You can further optimize your training by involving operators in maintenance.
Doing this creates an additional layer of protection against failure.
Look at it like this: all maintenance tasks, whether preventive or predictive, serve as protection against machinery breakdowns.
So if you teach your operators to safely use and inspect the equipment, you’re adding another safeguard, further minimizing the chances of failure.
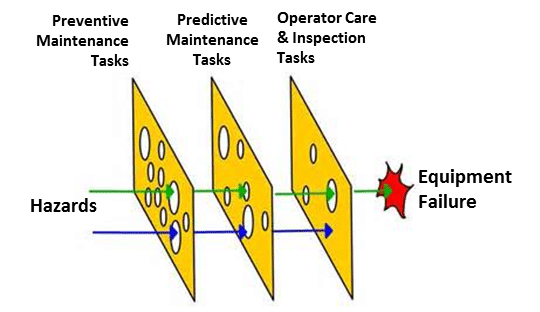
Training your operators to do basic maintenance tasks improves your time-effectiveness as well. The more activities an operator can handle on their own, the more time your maintenance team will have to dedicate to more complex issues.
Clearly, the operators can’t tackle more complicated problems on their own, and that’s why your maintenance team is there. So, assign the simple daily tasks to operators and save time for your servicing team in the process.
This advice is old news in Japan, where the idea of total productive maintenance (TPM) originated.
The core value of TPM is that everyone is responsible for the equipment they use.
That way, TPM shifts the focus from the maintenance team to the operators and anyone else who uses the machinery.
The 5-S principles are at the heart of this type of maintenance.
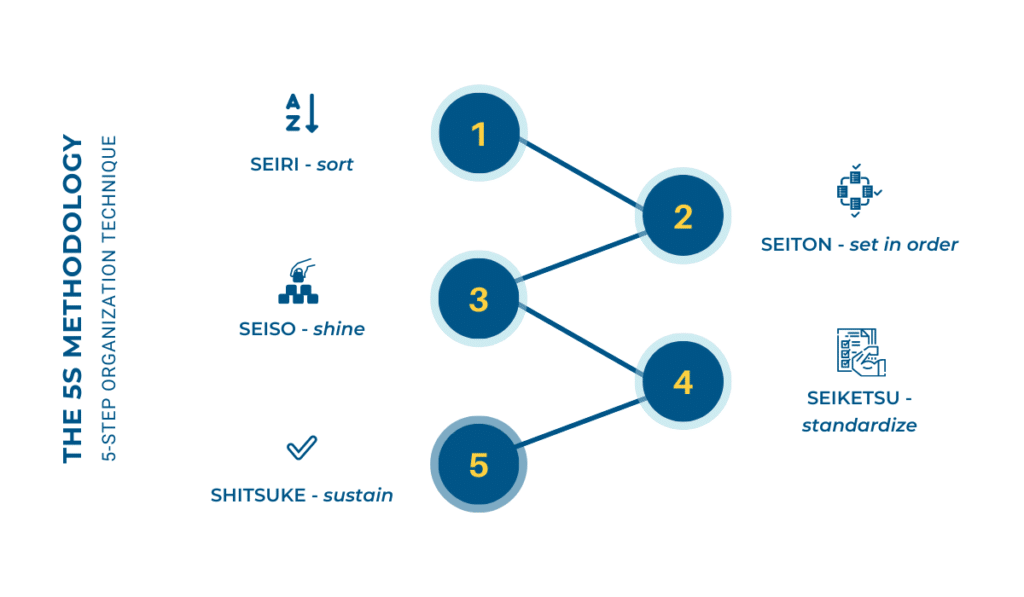
Companies using this principle prioritize systematizing the workplace and organizing equipment in a way that ensures everything has its right place.
For example, Instead of leaving your maintenance tools lying around, sort them right away for easier locating.
Then, the principles also emphasize the importance of cleanliness. Keeping the workplace clean lowers the risk of safety hazards and accidents.
As mentioned earlier, standardization, for instance, in the form of creating checklists to ensure everyone can easily follow the same steps, will also improve the reliability of your maintenance efforts.
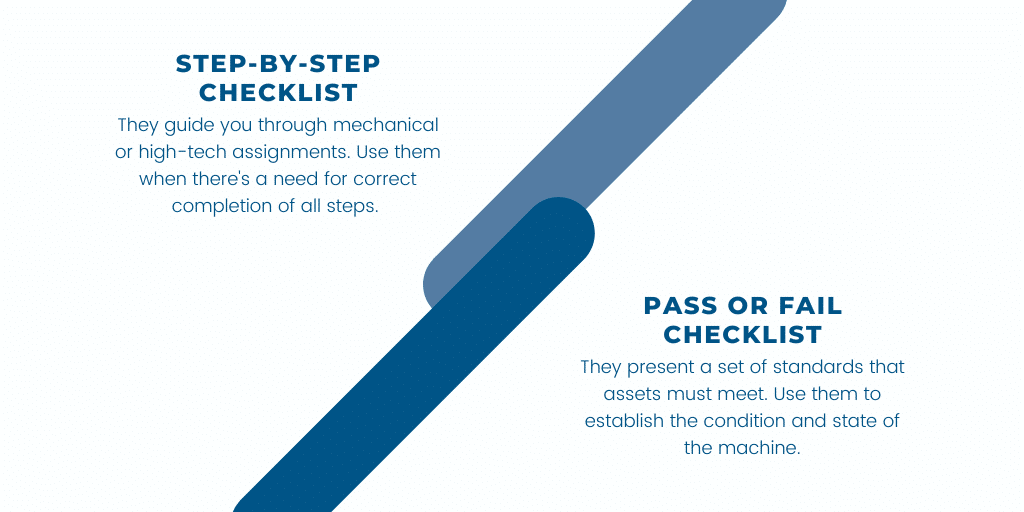
After you implement these principles, your team should have an easier time following your SOPs.
What else can you do to help your operators?
One of the most important things you can teach your team is to stop using the equipment as soon as they notice something is wrong.
The issues can range from strange sounds and minor changes in performance to visible damage to the machinery. In all cases, your team should avoid using the equipment until the issue is resolved.
Of course, there will be times when the operators will be able to fix the issue themselves, using the manufacturer’s instructions or your checklists. However, on other occasions, they will have to report the problem to the maintenance team. Because of this, it’s crucial that you instruct them on how to report the issue properly.
If operators are specific in their description of the problem, they make it easier for the servicing team to determine the cause and fix it quickly.
Teaching your staff how to perform basic maintenance saves the entire team time and energy. At the same time, it makes you more productive!
Conclusion
If you take away anything from this article, let it be this: education is the basis of good equipment maintenance.
A trained maintenance team knows how to recognize, report, and eliminate potential equipment issues, promoting safety in the workplace.
Remember that equipment maintenance is an ever-changing process, so you’ll need to dedicate your best efforts to its continuous improvement.
However, neglecting to invest in maintenance would cost a lot more. So, whenever you change your maintenance SOPs, inform and retrain your team again to ensure consistency.