Monitoring different maintenance metrics helps you improve the way you conduct maintenance and provides data that you can use to decide whether to keep investing in an item or replace it.
One such metric is the mean time between failures (MTBF), which estimates how much time passes between two breakdowns of otherwise repairable systems.
This article will explain this metric, its calculation, its importance and offer advice on improving your asset’s MTBF value.
In this article...
What Is Mean Time Between Failures (MTBF)
Mean Time Between Failures, or MTBF, is a maintenance metric that allows you to determine the average amount of time that passes between natural failures of an asset.
Of course, you can only use MTBF for equipment that you can restore to working order since it measures the time between failures that occurred and that you managed to fix.
If assets aren’t repairable, there will be no multiple failures.
The failures MTBF takes into account are any kind of changes that stop the equipment from functioning properly, i.e., like intended.
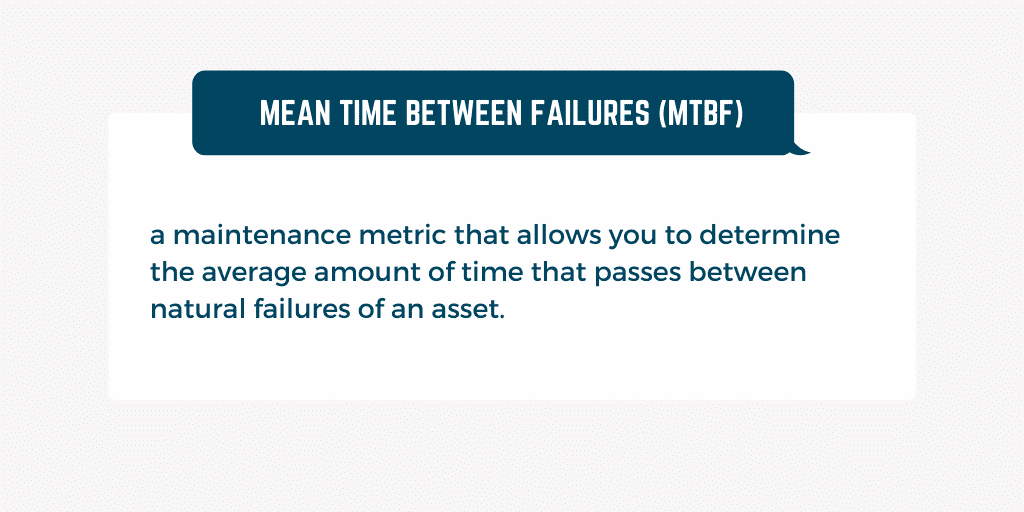
Keep in mind that a failure doesn’t necessarily mean that you can’t use the asset—it simply means that you can no longer use it at its 100% capacity because at least one aspect of the equipment no longer functions.
Most importantly, it’s a process.
An asset doesn’t break down in a matter of seconds. The issue is most likely present for a while before it hinders the performance of your equipment.
This metric is connected to an asset’s reliability and availability, both of which are equipment metrics that give you more insight into your equipment usage.
The former explains how likely the piece of equipment will fulfill its purpose in the predetermined time without breaking down.
The latter determines the time the asset was available at any given time.
MTBF measures the equipment’s level of reliability since it provides you with information on how long you can rely on your equipment before it suffers a breakdown.
How to Calculate MTBF
To calculate the mean time between failures, you need to consider the total uptime of the equipment and the number of failures that occur during that time.
The total uptime measure stands for the number of hours the equipment spent in an operational state. If you have more of the same item, you can group them to calculate their MTBF.
For example, you can have two bulldozers that worked 1,000 each this year, so the total bulldozer uptime is 2,000 hours in that case.
The total number of failures represents the number of times your equipment ran into a problem during the period you’re measuring.
In the case of the bulldozers, let’s assume they experienced seven failures each during the year, bringing the total number of bulldozer failures to 14.
You calculate the MTBF by dividing total uptime hours by the number of failures.
MTBF = total uptime hours / number of failures
In the bulldozer example above, the total uptime hours (2,000) divided by the number of failures (14) equals 142.85, which means that you can expect to use your bulldozers for an average of almost 143 hours before experiencing a breakdown.
How Mean Time Between Failures Helps Your Business
You can use MTBF to make predictions about failures and to determine the equipment’s reliability and availability.
As explained, MTBF uses the total operational hours and failures to calculate an average. This average then helps you plan maintenance.
For example, if your preferred kind of maintenance is preventive, MTBF can help you decide when to schedule it.
When you estimate how long you can use a piece of equipment before it breaks down, it’s easier to understand when you need to send the asset to the upkeep team.
In that sense, MTBF helps you minimize unexpected downtime—you use the metric to know when to perform maintenance to avoid breakdowns.
However, keep in mind that MTBF doesn’t take the fact that equipment ages into consideration, nor can it predict its service life.
MTBF is also helpful for your business because it helps you figure out the reliability and availability of your equipment.
When you constantly track reliability and availability based on past failure rates, it’s easier to notice when you need to replace an asset instead of repairing it.
Therefore, MTBF can also help you reduce costs as it points to when it’s time to stop spending money on an asset’s maintenance and invest in a new piece of equipment instead.
The MTBF metric helps you save money by predicting future failures and determining how reliable your equipment is.
MTBF Challenges
While MTBF can be beneficial when used with other metrics and practices, it has some downsides.
MTBF cannot accurately measure the time between failures in the sense that you will know exactly when the equipment will break down.
Instead, it’s a general estimate that helps you determine equipment reliability and plan maintenance—the probability of an asset operating after the MTBF is 37%.
However, if you use MTBF in addition to other reliability metrics, you can determine when the equipment will need maintenance.
Still, some may consider this a downside since MTBF works best when combined with other metrics.
Also, bear in mind that this metric always assumes a failure rate. Therefore, it won’t be as reliable or correct in the earlier stages when there are little to no failures.
In those stages, the result will be high.
However, over time, issues will occur, and the metric will determine the average more correctly.
Still, even then, it won’t take into account the fact that next year, your equipment will be older and even more prone to failure due to the constant wear and tear.
MTBF will be determined by the period you decide to measure.
For example, you can choose to focus on a period when no significant failures happen and then have a period when you face multiple breakdowns.
Unfortunately, it’s difficult to estimate which period would be the most accurate to focus on. Therefore, you need to measure MTBF consistently to get the most reliable estimate.
Finally, contrary to popular belief, MTBF does not measure the equipment’s useful life. Instead, it only focuses on estimating the time between two failures.
How to Improve Your MTBF
Since MTBF can prove helpful, especially when used with other metrics, you should use it in your calculations.
What can you do when your MTBF numbers are too low for comfort? It means that you will have to spend more money on maintenance and the downtime the failure causes.
You can optimize your upkeep processes, perform root cause analysis, and opt for condition-based maintenance.
Work on Maintenance Processes
The better your maintenance processes, the higher your MTBF will be.
If your MTBF numbers are low, it might be time to review your maintenance procedures.
When done right, preventive maintenance helps prolong the mean time between two failures by letting the maintenance team inspect and tweak the asset before a breakdown occurs.
As a result, they can find and eliminate possible causes of future issues and address them before they cause damage.
However, if your preventive upkeep isn’t stopping your equipment failures, there is something wrong, either with the maintenance process or the equipment itself.
The equipment might be too old, so you can look at its statistics to determine whether it’s time to get a replacement.
Moreover, maintenance processes can be inconsistent or inadequate.
If you want your maintenance to be efficient, your team needs manuals for different equipment and a checklist for preventive upkeep.
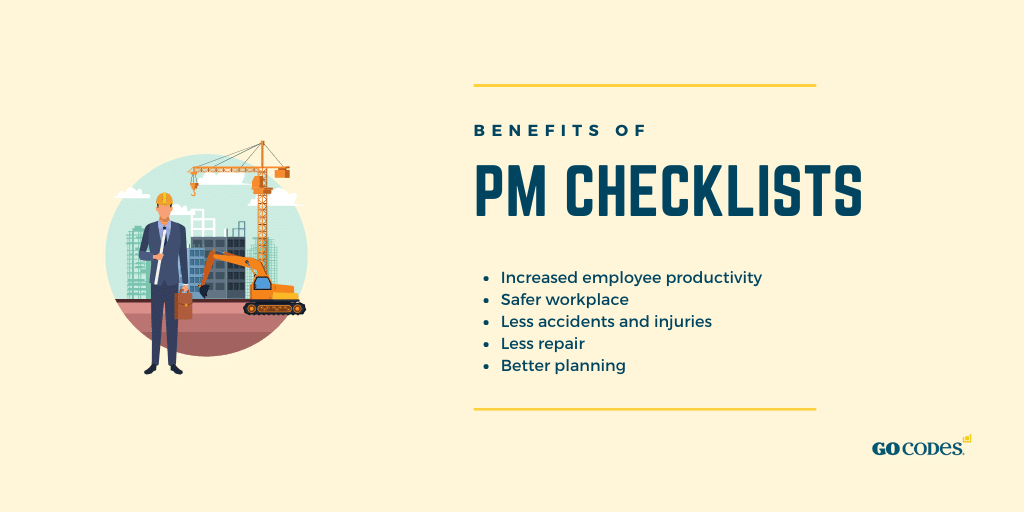
Most importantly, your team needs adequate, detailed training on performing maintenance on all assets under their care.
Go through the manuals and checklists to understand whether you’ve missed a specific step, or if something needs to be changed or added.
You can also examine the types of failures that happened to determine which part of the maintenance process should have covered it.
That’s how you will understand what improvements are necessary.
Updating your maintenance processes will help increase your equipment’s MTBF.
Perform Root Cause Analysis
When you understand why a failure happened, you can fix the root cause, improving the MTBF in the process.
You should regularly perform root cause analysis to get to the bottom of the issue.
While maintenance fixes the problem and gets the equipment running again, determining the root cause helps you determine what caused the situation in the first place.
The same asset can fail repeatedly, and you can quickly fix it, but if you want to be able to implement a long-term solution, you have to understand why it breaks down—i.e., identify the root cause.
The root cause is something you can work on, thus eliminating breakdowns.
Root cause analysis directly impacts the MTBF because it offers a concrete solution to the deeper problem underlying a particular failure.
To get to the solution, you first have to understand what is causing the issue. You can do that by using the five whys technique (5Y).
You start by asking a why-question along the lines of: “Why did the equipment break down?”
When you get the answer, ask a further why-question, and then another one. You should be able to get to the root cause after five questions.
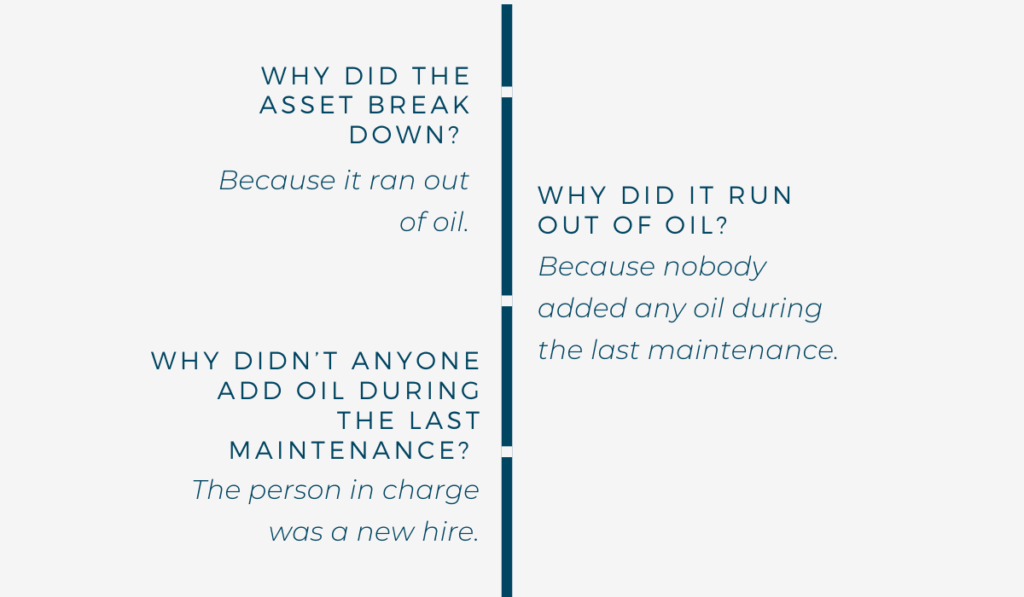
P.S. Try not to ask yourself who-questions (such as “Who failed to add oil during the last maintenance?”), as that only leads to pointing fingers and doesn’t help you get to the solution.
Ask yourself five why questions to understand the root cause of a problem if you want to prevent future failures from happening.
Implement Condition-Based Maintenance
Condition-based maintenance (CbM) alerts you of problems as soon as they arise, allowing you to improve your MTBF.
If you set up the type of system that can recognize early warning signs of a problem, you can prevent more significant issues from happening.
This type of upkeep is preventive, as it focuses on solving smaller issues before they cause further damage or lead to downtime.
When you opt for CbM, you need to find a way to figure out when an asset will reach a critical level.
You have to have a condition to monitor and base your maintenance on, hence the name.
Most companies use sensors set up manually, as each piece of equipment has its own set of critical levels, depending on the part.
Once the levels are down, the sensors alert you of the issue, allowing you to determine what is happening, and fix it.
This occurs while the asset is still running, which means you can avoid downtime and additional costs.
If obtaining sensors for all your assets seems too expensive, start with the most critical—those whose downtime would cost you the most in terms of downtime, delays, or costly repairs.
CbM allows you to deal with an issue as soon as it appears, preventing a failure.
Conclusion
When selecting the metrics you want to measure, consider MTBF if your aim is to estimate the reliability of your equipment and determine how long passes between failures for a particular type of asset.
In combination with other metrics, MTBF can determine whether you can rely on your equipment and how often to invest in upkeep.
To prolong the period between two failures and improve your MTBF rate, work on your maintenance processes, determine the root cause of an issue, and opt for condition-based maintenance.
Those three changes will enhance the longevity and reliability of your asset, saving you time and money in the process.