It’s no secret that equipment management is key for any business that wants to stay organized while delivering results.
When you’re good at it, you’re aware of everything that happens with the asset, from the purchasing to the disposal phase.
You utilize the tool when necessary, understand its condition, and invest in its maintenance.
To ensure that your workers have, know how to use, and easily find the necessary tools, follow the suggestions from this article.
It will leave a good impression on your clients and earn you recommendations!
In this article...
Create an Equipment Inventory
The first step in equipment management is to take inventory if you haven’t already.
Why? It’s simple—you can’t do your job unless you have all the necessary assets.
Inventory serves as a real-time database of all your assets.
You might have the equipment, but it could be in poor condition and in need of repair or replacement, which you won’t know until you try to use it.
If this happens in the field, you risk seeming unprofessional, so it’s better to produce an inventory as soon as possible.
An asset inventory is beneficial when you have limited tools to divide between several jobs.
When five people need to start working on a project, and all five of them need the same equipment, you might run into problems and delays.
Knowing how many pieces of equipment you have can help you plan projects and eliminate delays because of a single tool.
Start by writing down all equipment details, such as its state and last maintenance date, if applicable.
When dealing with tools that can’t be serviced but only replaced, make sure to write down the purchase and warranty date, assuming you got one when buying the item.
Knowing this will help you determine the optimal moment to get a replacement item, instead of waiting for it to stop functioning, causing unplanned downtime.
While you can do this manually, it’s better to use spreadsheets or, optimally, invest in cloud-based software that saves all the information in the cloud, allowing everyone to have access to real-time data.
Now that you know that doing asset inventory gives you an overview of all the equipment you have and its condition, helping you plan for projects or new purchases, you need to arrange it well.
Organize Your Tool Room
Having a clean, well-organized equipment storage room helps you manage your equipment better.
Your company should have a place where you keep all the equipment stocked and safe.
This space has to be neat and tidy to aid your employees in locating items. Otherwise, you risk losing valuable time on simply finding a piece of equipment instead of using that time to get the job done.
It’s wise to divide the room into dedicated sections for easier management.
If you have rules like keeping smaller tools in drawers and on shelves while storing bigger pieces of equipment in cabinets, your employees will at least know the general area of the item’s location.
This will enable them to locate them more quickly.
Not only that, but they will also understand where to return the items instead of leaving them wherever they see fit, which can result in a disorganized storage room and tool misplacement.
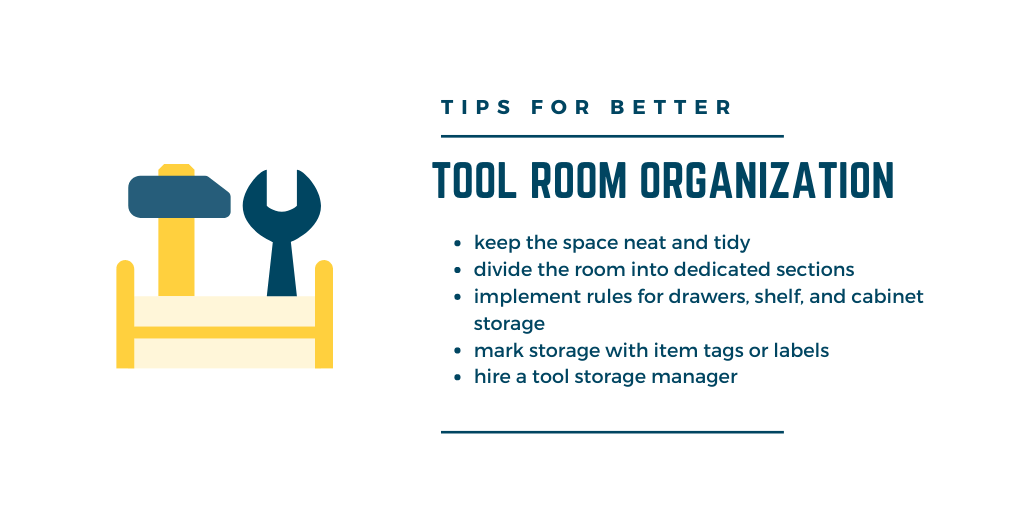
Additionally, it would be helpful to mark these areas with item tags, ensuring that everyone recognizes which tools are stored in which drawer, cabinet, or closet.
This system will make your team more efficient and productive.
Consider hiring a tool storage manager if you have a lot of equipment and find it impossible to keep it organized with that many employees.
Their job would entail overseeing the room, doing inventory, and ensuring that tools are returned to their place and in good condition.
The manager would notify you whenever there is a need to buy a new asset, replace an old one, or conduct maintenance, which is better done before a project than during it, thus saving you money.
Therefore, keeping your equipment room in order benefits you by saving time, energy, and money.
Ensure Proper Equipment Handling
It’s easier to manage your equipment when you’re sure your employees are handling it properly.
When doing equipment management, you always consider factors like the tool’s location, age, or condition since they help you understand how long you can count on the equipment.
For example, if a manufacturer guarantees that your asset’s useful life is five years, you expect it to serve you at least that long.
However, a tool’s life depends not only on its quality but also on usage.
If not used properly, it will break down or malfunction a lot sooner than intended.
The sudden breakdowns cause issues in asset management as you can no longer count on an item to serve its purpose, which is why it’s crucial for everyone on your team to know the purpose of each asset.
Your employees need to understand what a tool or a product is for and stop using it for other purposes, as this can damage the asset and cause breakdowns or additional expenses.
The essential knowledge for a mold remediation team includes correctly putting on and taking off respirators, creating and utilizing decontamination units, and using negative air machines.
Mold remediation workers also need training on health and safety, personal protective equipment (PPE), physical, chemical, and microbial hazards.
To stay on track with asset management, ensure that all new hires get proper training on every required tool, and have hands-on experience during training, as well as access to the training materials after it’s done.
Also, don’t forget to enroll everyone in training whenever you purchase any new assets that your team hasn’t used before.
To sum it up, quality employee training helps employees use assets correctly, which makes asset management easier.
Purchase Only Quality Equipment to Extend Its Life
Quality assets make it easier to manage equipment efficiently.
When managing equipment, you always consider an asset’s useful life since you need to know how much you will get out of your asset and how long you can count on it to do its job.
This data comes in handy when you negotiate new projects and rentals.
However, the quality of an asset plays an important part in this process—and that’s where price comes in.
When purchasing equipment, including PPE, consider that the cheapest option might prove to be costlier than the more expensive one based on how long it will last and whether it can cause downtime, damage, or injuries to your workers.
While price doesn’t equal quality, you should consider which item will give you the best return on your investment.
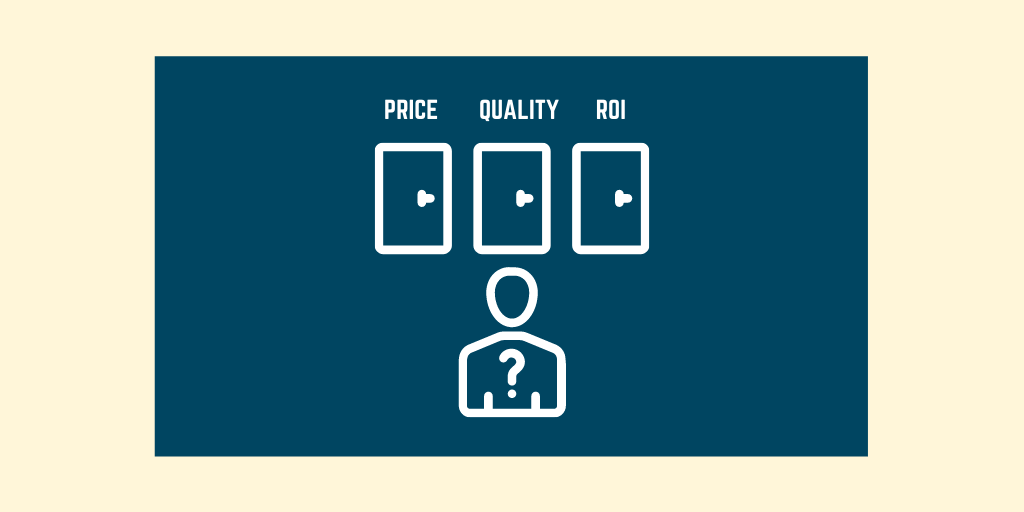
For instance, you can spend under $100 on a dehumidifier that won’t be as powerful, fast, or long-lasting as a commercial $1000 one—but what would be its benefit, other than the price?
If you want to buy quality assets but still save up, find a good manufacturer and shop there regularly, which can get you specific discounts and benefits.
Buying in bulk can also prove cost-effective, as well as a good business decision—you should have a backup piece in case of an unexpected breakdown, maintenance, or a completely new, urgent project.
Choose high-quality equipment to be assured that you can count on it for a long time, easing your asset management process.
Invest in Effective Equipment Maintenance
Effective equipment management heavily relies on regular maintenance.
Instead of reactive maintenance—having the tool inspected after a problem occurs—you should consider proactive maintenance, which helps you find problems before they arise by performing regular checks.
This means letting a specialist inspect your tools, tweak them, and give feedback.
Don’t consider it a waste of money as it helps prevent lasting damage to your equipment.
Besides, such maintenance puts an end to breakdowns and emergency service repairs, saving you $5 for every $1 you spend on it.
Proactive maintenance also lets you know if the asset was a wise investment, which helps you plan your future purchases accordingly and manage your assets better.
A specialist will bring your attention to any flaws they find with your equipment and give their opinion on it, helping you decide whether to keep purchasing from that same manufacturer.
Alternatively, you can opt for a higher-quality version.
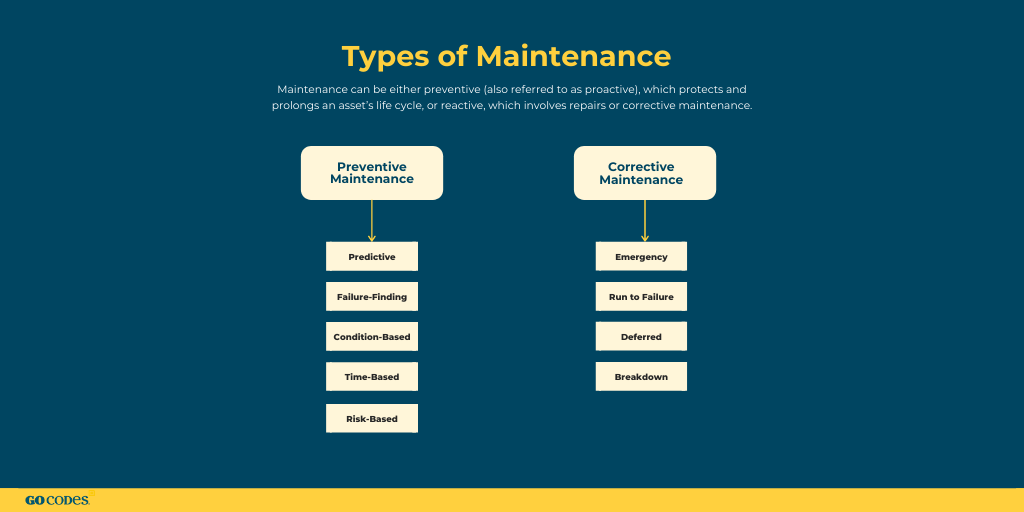
Another benefit of regular maintenance is that warranty claims are a lot easier when you have a list of all servicing checks and issues, proving your continuous investment in the asset.
On top of all that, servicing helps prevent unexpected downtime, which costs companies a staggering ten times more than planned downtime.
The technician will inspect the tool, notice issues, replace certain parts if necessary to ensure that the asset can do its job.
Downtime has a negative impact on efficient tool management, so it’s in your best interest to prevent it.
Investing in maintenance helps avoid expensive emergency repairs that impact your asset management negatively.
Pay Special Attention to Personal Protective Equipment (PPE)
Equipment management entails stocking up on PPE to ensure your workers’ safety.
Personal protective equipment (PPE) is necessary for the mold remediation industry since some strains of mold are bio-hazardous due to their byproducts, mycotoxins.
When inhaled, they can be highly toxic to adults, and even more so to infants and the elderly.
Because of this danger, it’s crucial that you provide your team with the necessary equipment, stock it in sufficient quantities, and explain how to use and dispose of it properly.
Efficient mold remediation equipment management has to entail adequate reserves.
Some equipment is optional and provides additional protection, while other forms are obligatory and serve to protect the employee from any fungus-related issues.
The assets of utmost importance to mold remediation workers are respiratory protection gear, eye protection in the form of goggles or safety glasses, and gloves when doing wet work.
Your workers need to change disposable equipment such as gloves and respirators daily while replacing other protective gear when damaged.
After working with hazardous materials, workers need to decontaminate their equipment, clean it, and store it properly.
The disposable assets need to be bagged and disposed of in closed-lid, touch-free disposal to minimize the risk of contamination.
Take this into account when deciding on the number of goods you want to order.
Disposable goods are changed daily, so you need to provide one piece a day per worker and have plenty of backup stock.
This advice works well for reusable equipment as well, as you never know when it might malfunction or get damaged, despite all of your efforts in quality asset management.
Quality equipment management considers PPE and stocks up on it to assure safety at the workplace and eliminate downtime.
Track Your Mold Remediation Tools and Equipment
Tool tracking makes equipment management a lot easier as it gives you insight into who is using your asset and what condition it’s in.
While it might seem redundant, asset tracking is becoming prevalent in industries that rely on tools, and its market should reach $34.82 billion in 2026, which is double the value it had in 2020 ($17.14 billion).
Even if you don’t have that much equipment, it’s helpful to know where each of your items is, and here is why.
First, cloud-based software like GoCodes can help you tag and track your inventory by looking it up in the system, showing you the tagged item’s last known GPS location.
Having a spreadsheet list of your assets and current users is fine, but such systems are prone to human error, can be deleted, and don’t provide the item’s location.
With software solutions, your data is available in the cloud, which you can access from anywhere and look up asset information by scanning the tag or by searching for it in the system.
Secondly, it lets you can plan your projects accordingly. If you have ten dehumidifiers but 12 projects for which you need one, you will have to postpone or cancel at least two.
Tracking tools using cloud-based software provide real-time information on who is using it, and when they will return it while offering you the option of reserving it.
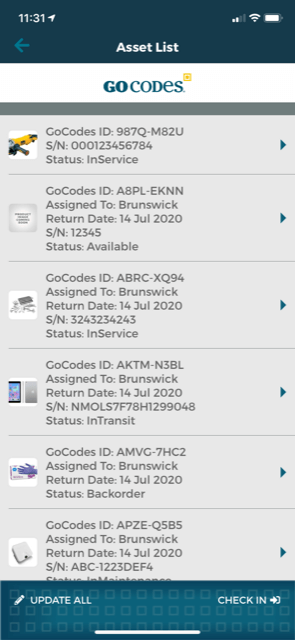
You can then arrange for projects to start later, based on when the necessary equipment is available.
This feature can be practical if you rent your high-quality equipment to others, as it will give you exact information on when to return it.
On top of that, using a tracking system lets you know how often you use the tools and whether there is a waiting list for them.
If you do have a waiting list, consider investing in one more such asset to shorten the waiting time and increase productivity.
Finally, software solutions let you add details about the item’s condition and maintenance, ensuring that everyone knows whether they can count on the item. The software can remind you of the scheduled maintenance date.
Track your tools for better planning and productivity!
Conclusion
You need to know the quality, quantity, and condition of your assets to be an effective equipment manager.
Once the relevant data is written down in a shared, easily accessible place, you should train your workers on the proper usage of equipment to ensure they don’t cause themselves or the assets damage.
Furthermore, boost asset management efficiency by keeping the tool room well-organized, and investing in a tool room manager if you have lots of equipment.
Stay on schedule and have all the necessary tools by tracking them using software that lets you know who is using your equipment and where it is.
Start applying this advice today to improve your equipment management!