Key Takeaways:
- Compact electric construction equipment is leading the transition to electric vehicles.
- Cybersecurity vulnerabilities can jeopardize entire fleets.
- AI-driven route optimization helps fleets save time and fuel by analyzing traffic, weather, and road conditions.
If you’re here, chances are you’re curious about the latest trends shaping fleet management.
You may also wonder if your construction business should adopt these trends, and if so, how and when.
That’s a proactive stance, and these trends are all about proactivity that drives efficiency, transparency, and sustainability in your fleet operations.
Some you may already know about, while others might surprise you.
So, let’s explore the six key trends transforming fleet management today.
In this article...
Accelerating Electric Vehicle Adoption
As the construction industry increasingly prioritizes environmental sustainability, the adoption of electric vehicles (EVs) and equipment is steadily growing.
The benefits of EVs in construction are clear: no diesel fumes, significantly less noise, improved efficiency, and lower operating costs.
These advantages are driving adoption in certain construction sectors, but progress remains uneven.
One area where EVs have firmly taken root is compact equipment, such as mini excavators and skid steers.
To illustrate this forward momentum, consider these projections from Fact.MR’s 2024–2034 Market Outlook:
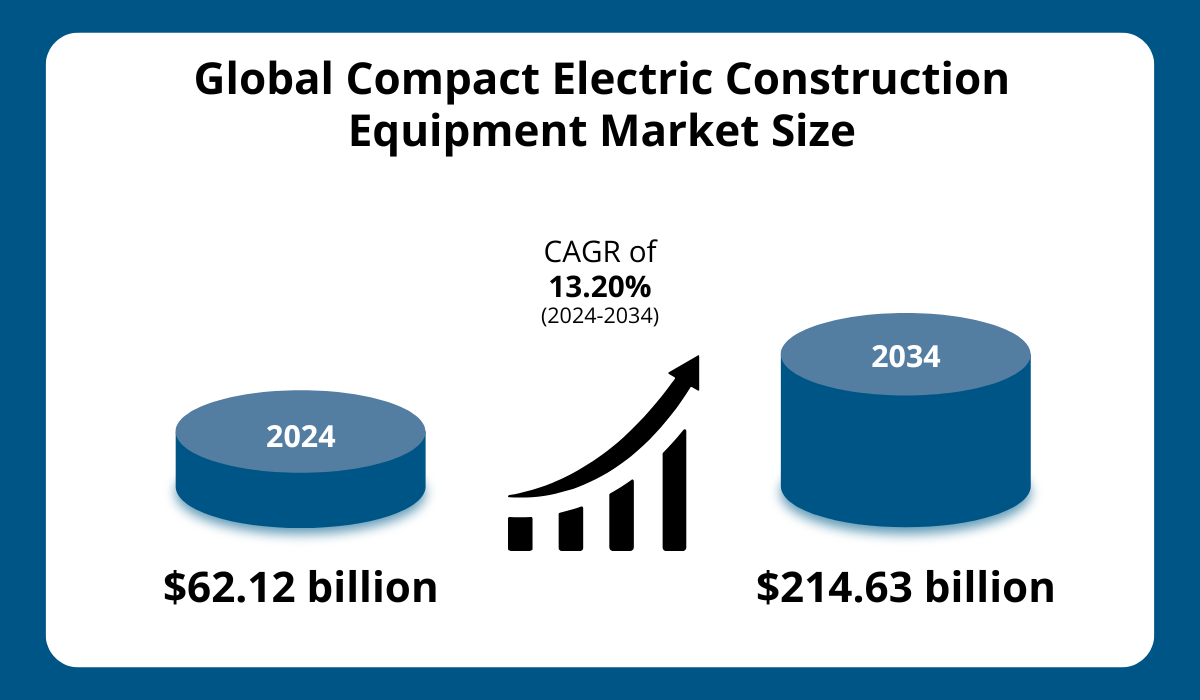
This projection is based on the popularity of smaller electric construction equipment, which is easy to understand.
These machines provide practical, sustainable, and quieter alternatives to traditional fuel-powered equipment, particularly for smaller urban projects.
Additionally, they provide an affordable way for contractors to “go green” without going broke.
Although the compact electric equipment market is thriving, progress in large, electric-powered heavy machinery remains slow.
The main challenge lies in the power requirements and large battery sizes of equipment that must lift and move tons of materials.
As Natasha Fry, Head of Sales at Mer UK, explains, this is the primary reason why:
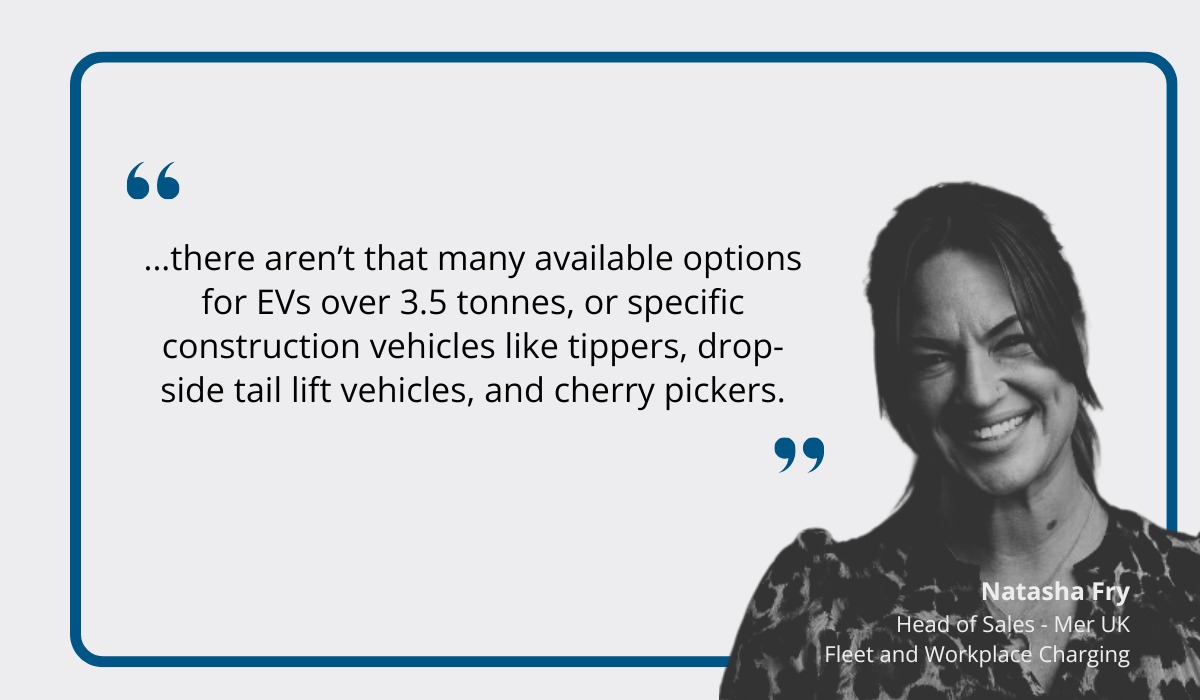
While advances in electric construction machinery with a capacity over 3.5 tons may be slower, progress is steadily being made.
Major manufacturers like Volvo, Caterpillar, Komatsu, and John Deere are leading the charge in developing hybrid and fully electric heavy machinery tailored to construction needs.
Judging by Volvo’s recent innovation, large wheel loaders and excavators with capacities exceeding 6 tons are next in line for electrification.
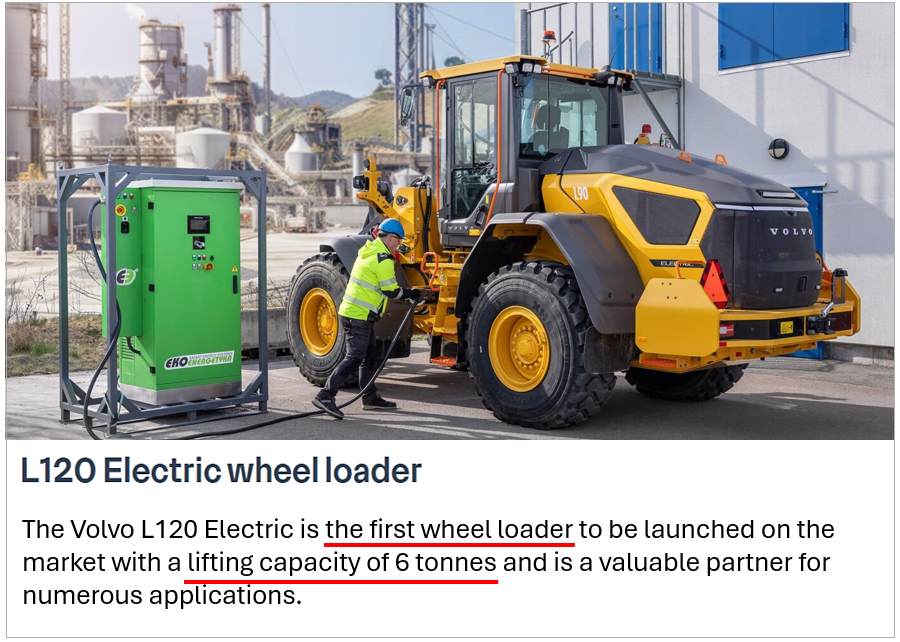
We could say that the situation with fully electric long-haul, heavy-load trucks is similar but less developed.
Only a few projects have reached limited-scale application stages.
A significant hurdle remains—the lack of charging infrastructure capable of supporting these larger transport vehicles.
So, what does all this mean for your fleet?
Simply put, it’s best to adopt a gradual approach.
Begin phasing out older models and incorporating electric options where they make the most sense for your operations.
As your electric fleet grows, fleet managers will gain valuable experience in adapting their operations to support EVs.
This may involve designing EV-specific routes and optimizing schedules around charging times.
Overall, adopting electric vehicles and equipment requires careful financial planning, strategic decision-making, and a gradual implementation strategy.
Exploring Alternative Fuel Technologies
Alternative fuel technologies can help alleviate some of the aforementioned challenges, despite some of them facing similar ones.
For instance, both compressed natural gas (CNG) and liquefied petroleum gas (LPG) are increasingly being recognized as viable alternatives to diesel in construction fleets.
The main advantages of these fuels?
Reduced emissions, comparable performance, and the possibility to convert existing equipment to new fuel.
Downsides primarily involve the number of fueling stations, where LPG has a more established infrastructure, at least in the US.
At present, these fuels are more commonly used in lighter construction equipment and vehicles, such as LPG-powered forklifts.
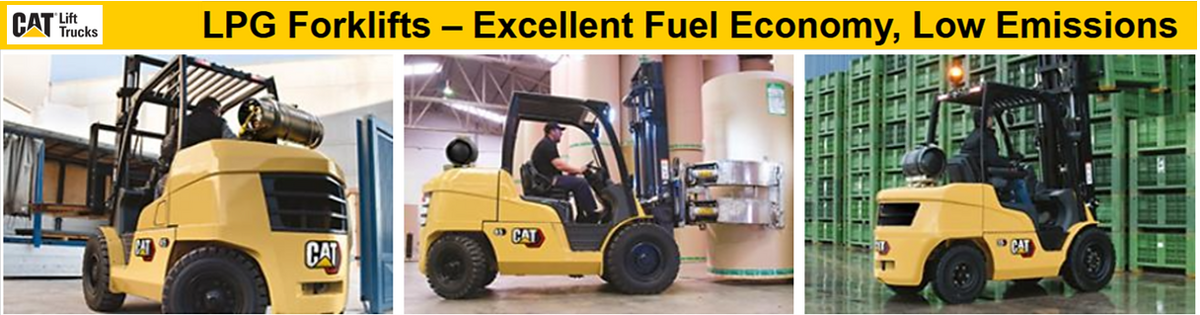
However, advancements in engine technology are gradually expanding the potential of CNG and LPG to power heavier machinery.
Then we have biofuels, which can be used in existing diesel engines with only minor modifications.
Derived from organic materials, biofuels like biodiesel and hydrogenated vegetable oil (HVO) enable contractors to reduce their environmental footprint.
While these technologies lower greenhouse gas emissions, they still generate them during combustion.
In contrast, when hydrogen fuel is combusted, it produces only water as a byproduct.
Moreover, hydrogen offers rapid refueling times and the capacity to power the heaviest construction equipment.
Recognizing this potential, Veidekke, Norway’s largest construction company, recently acquired a 20% stake in Applied Hydrogen.
As Berit Laanke, Director of Business Development Sustainability at Veidekke, explains:
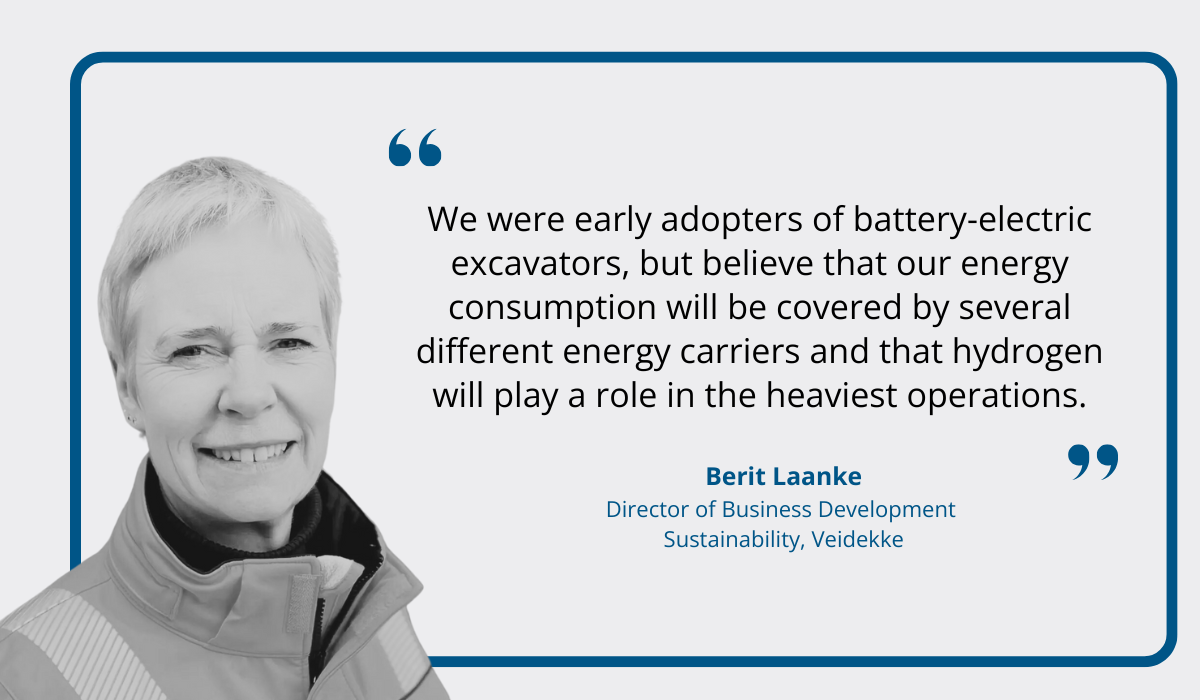
The cooperation between Applied Hydrogen and Veidekke is currently focused on converting the first large 30-ton excavator to hydrogen operation.
Another promising alternative to fossil fuels is electrofuels (e-fuels), synthetic fuels produced using renewable electricity to convert CO2 into usable energy sources.
As such, e-fuels offer a way to decarbonize hard-to-electrify sectors like heavy-duty vehicles.
Takeaways for your fleet?
Alternative fuels are worth exploring.
They provide a practical way to reduce emissions without going fully electric—in many cases, existing equipment can be converted.
This can make them a cost-effective, flexible, and sustainable option to the rising prices of fossil fuels.
With multi-fuel engines and ongoing advancements, future equipment is likely to support diverse fuel combinations, enhancing operational flexibility and sustainability.
Ultimately, alternative fuels enable construction companies to optimize performance, reduce reliance on diesel, and transition more smoothly to a greener future.
Growing Importance of Cybersecurity
As construction fleets become increasingly digitized and connected, the risk of cyber threats grows alongside these advancements.
Connectivity creates vulnerabilities that cybercriminals can exploit.
Ransomware, phishing attacks, and unauthorized access to fleet management systems are among the most common threats.
In some cases, attacks aren’t even financially motivated—hackers may simply be seeking to prove themselves or cause disruption.
Here’s an example:
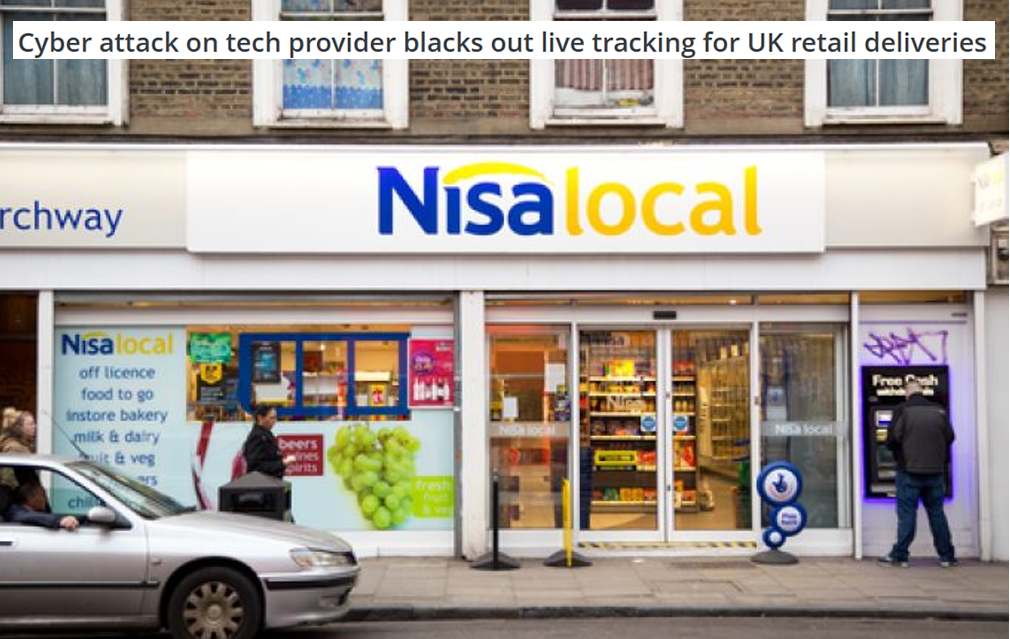
In the above case, fleet management technology provider Microlise, a supplier for DHL Supply Chain UK, was attacked.
This caused Nisa and other UK grocery wholesalers working with DHL to lose real-time delivery tracking capabilities for their customers.
Such breaches can significantly disrupt operations and result in financial losses.
So, what can you do to protect your business?
Start by partnering with fleet management providers that prioritize cybersecurity, offering an added layer of protection.
Next, invest in preventive measures like firewalls, encryption, and regular software updates.
Security testing is also crucial—hiring professionals to stress test your systems can reveal vulnerabilities before they’re exploited.
For instance, Deloitte experts were brought in to evaluate the security of a location-tracking dongle installed in 50,000 vehicles.
And they identified vulnerabilities.
As Jan Vanhaecht, Global Digital Identity Leader at Deloitte Belgium highlights:
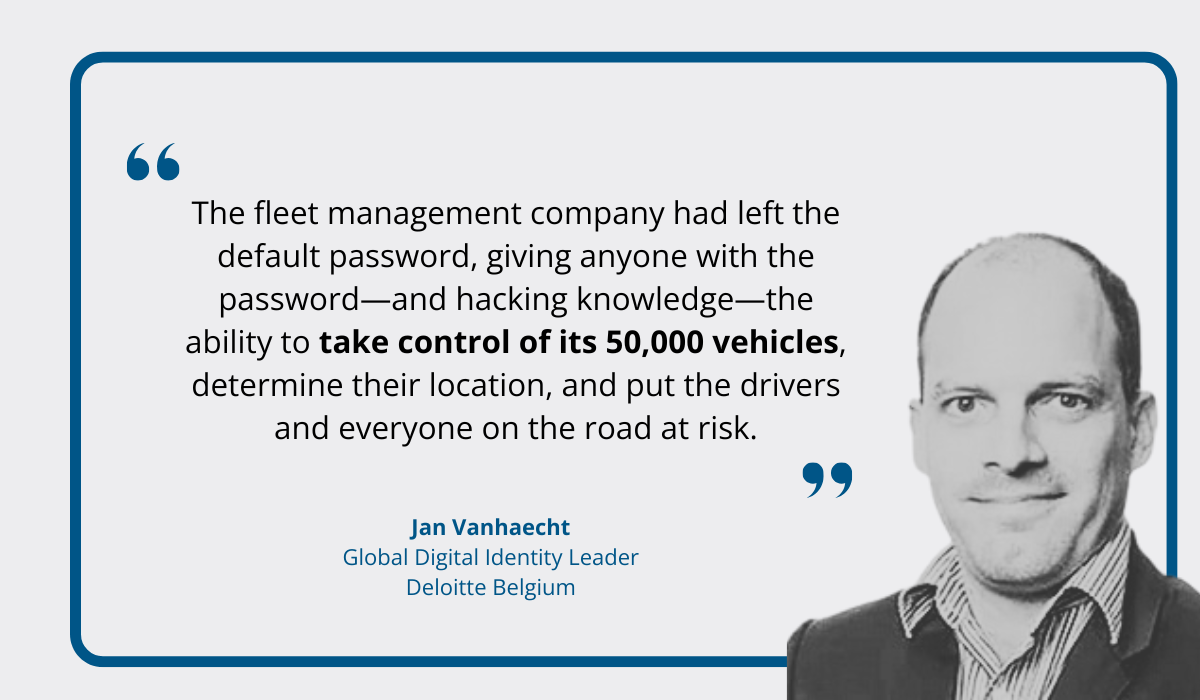
The cybersecurity flaw identified by Deloitte could have allowed hackers to take control of vehicles, enabling them to manipulate functions such as acceleration or braking.
In addition to security testing, training your employees to recognize phishing attempts and enforcing strong password policies are also essential.
Overall, despite increasing cyber threats, there are effective measures you can take to safeguard your fleet operations and data.
AI-Driven Route Optimization
We have long been accustomed to GPS routing tools or Google Maps providing directions for personal or business travel.
Similarly, construction companies have relied on basic routing systems to streamline their fleet operations and reduce delays.
However, the rise of artificial intelligence (AI) and machine-learning (ML) algorithms has fueled even smarter, more adaptive route planning.
These advanced tools go beyond traditional systems by analyzing vast datasets, including traffic patterns, road restrictions, weather conditions, past accidents, and more.
Using this technology, companies can create highly efficient and adaptable routes, saving time and fuel while improving delivery accuracy.
Alex Osaki, manager at HERE, a fleet management technology provider, argues that route planning is exactly the kind of thing that AI and ML algorithms excel at:
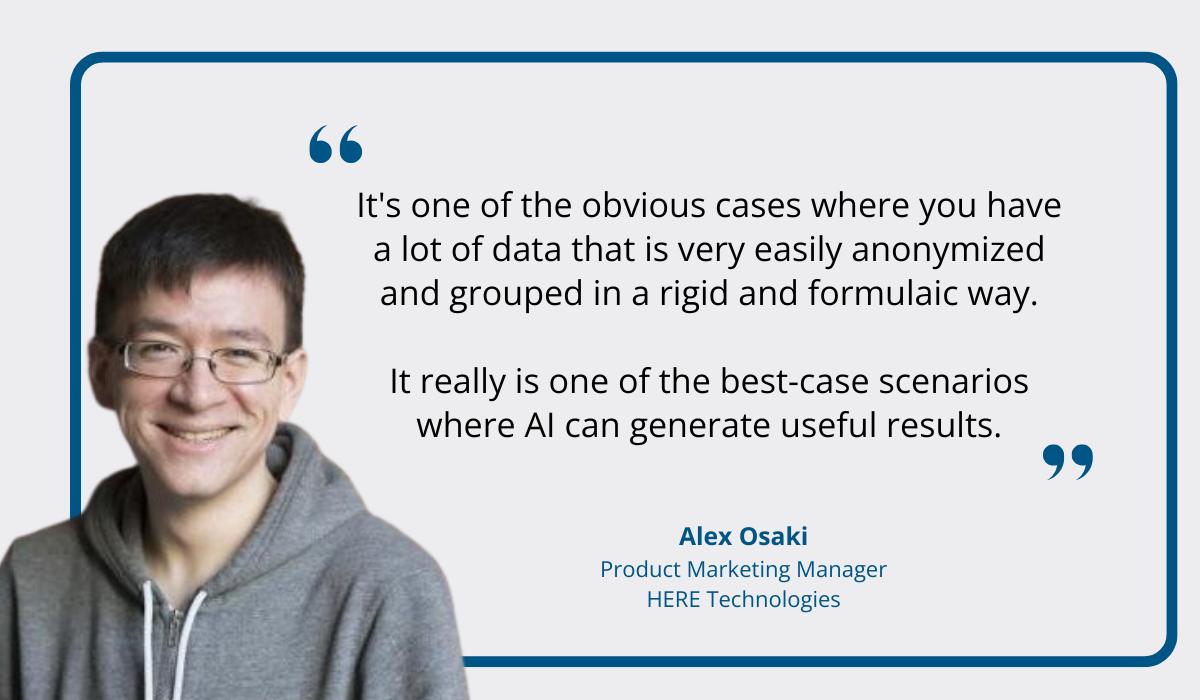
So, what can an AI-driven route planning system bring to your fleet?
It enables your dispatchers to:
- dynamically plan transport routes based on real-time conditions,
- receive alerts on load restrictions, street widths and heights, and local regulations,
- notify drivers of road closures, traffic jams, or last-minute changes, and reroute them as needed.
Ultimately, advanced route planning saves time, reduces fuel costs, and boosts operational efficiency—essential benefits for any modern fleet.
If you’re already using GPS trackers and basic route optimization systems, you can look forward to significant advancements as AI technology continues to evolve.
These improvements may come through updates from your current provider or by proactively exploring systems with enhanced capabilities.
If your fleet currently lacks such a system, prioritize adopting one that either includes AI-driven route optimization or can be integrated with your fleet telematics.
Integration of Fleet Telematics
Telematics is the technology used to track a wide range of critical data about individual vehicles or entire fleets, such as location, driver behavior, engine diagnostics, and more.
This rich asset and driver data helps fleet managers strategically allocate resources, eliminate inefficiencies, and ultimately maximize the value of their fleets.
Telematics systems typically use GPS trackers equipped with their own sensors or connected to in-vehicle sensors, which may be built-in or added later.
However, the wide variety of telematics solutions available can be overwhelming, often leading to unnecessary features and costs.
That’s why, for those new to telematics, focusing on solutions that provide essential features in a user-friendly way is key.
One such practical and cost-effective solution is our fleet-tracking app, GoCodes Asset Tracking.

With GoCodes Asset Tracking’ real-time GPS trackers, your fleet manager and other team members gain full visibility into the movements and locations of your vehicles and equipment.
Additionally, fleet managers can set up invisible security perimeters, known as geofences, around sites or storage areas.
If equipment is moved outside the designated area, the manager receives immediate notifications, helping prevent theft or unauthorized use.
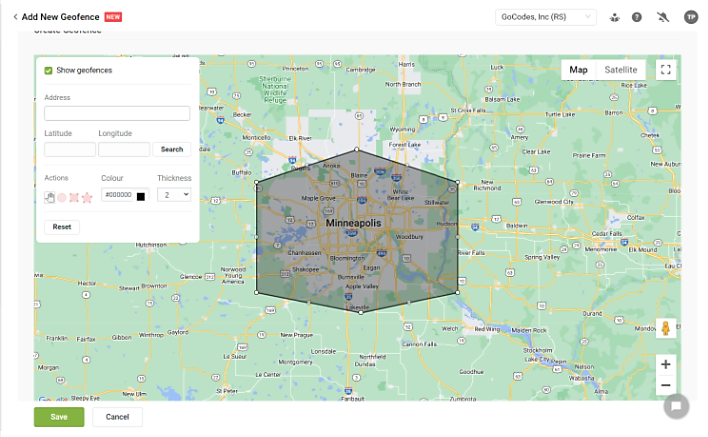
GPS trackers also capture key driver and vehicle data, such as engine hours, speeding, harsh braking, sudden accelerations, and more.
This data enables managers to monitor driving behavior, ensure safety, and improve fuel efficiency.
The GoCodes Asset Tracking tracking system also includes affordable tracking devices like QR codes, Bluetooth beacons, and RFID tags, which can be used to monitor other assets.
Of course, there are more comprehensive telematics systems in the market that include additional devices, sensors, and road- and driver-facing cameras.
However, higher complexity comes with higher costs, longer installation and setup, and more extensive training.
Whatever you decide, remember that telematics enhances fleet efficiency and security, leading to cost savings—making it an increasingly essential standard across the industry.
Shift Towards Predictive Maintenance
The shift from a reactive to a predictive model is enabled by the technologies we’ve already explored.
When GPS trackers, IoT sensors, and fleet management software join forces with AI-driven models, fleet managers gain the ability to anticipate vehicle issues and respond proactively.
How does it work?
Predictive systems rely on sensors to monitor critical components such as engine performance, brake conditions, and tire pressure.
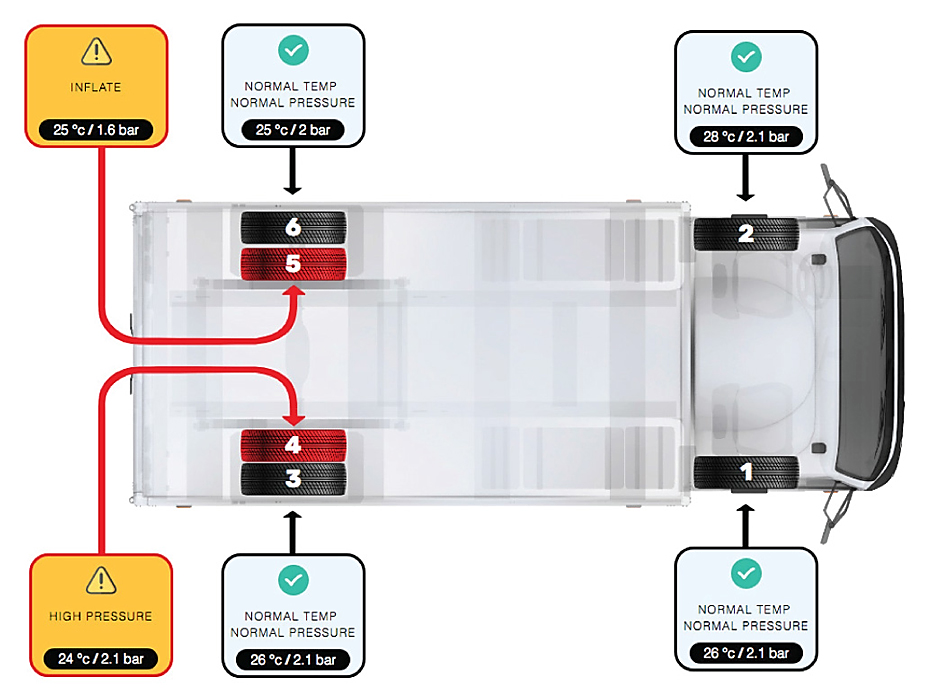
From there, AI-powered algorithms analyze the collected data and learn to detect early signs of wear or malfunction.
The system then alerts the fleet manager, who can schedule repairs or replacements before issues escalate into costly breakdowns.
Here are the main predictive analytics features of one such solution, Stratio.
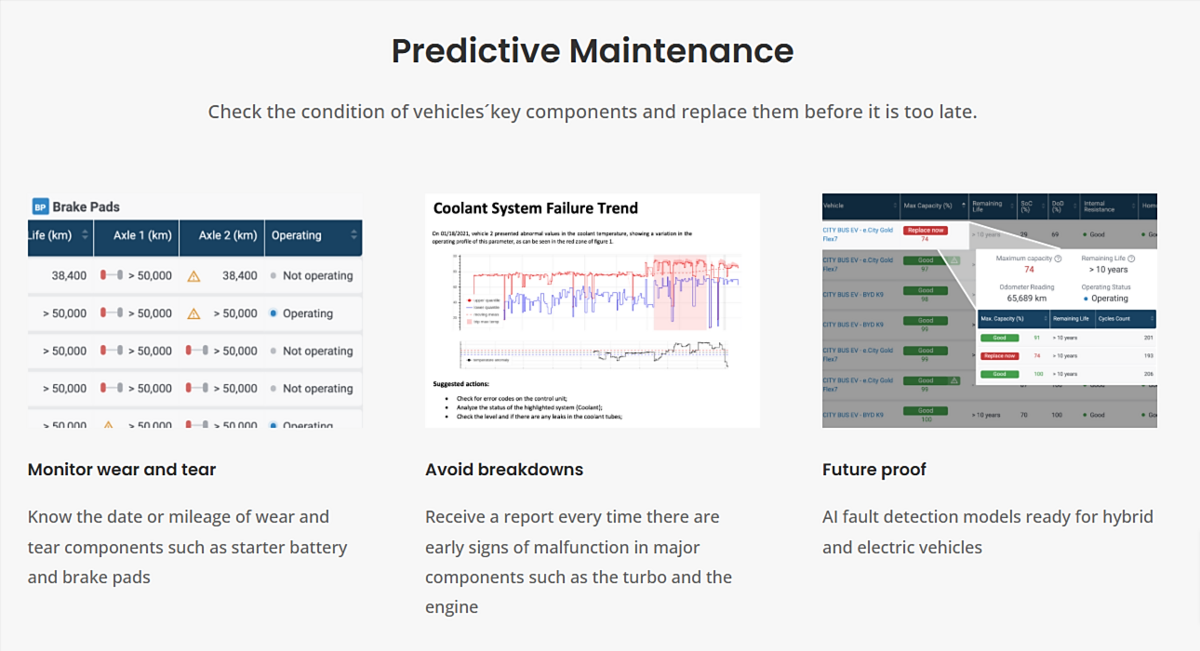
These capabilities of predictive maintenance solutions are slowly but steadily transforming fleet management, enhancing the efficiency of the entire construction process by extension.
How? By minimizing unplanned downtime, enhancing safety, reducing maintenance costs, and extending the lifespan of construction vehicles and equipment.
As these technologies continue to evolve, predictive maintenance is poised to become a cornerstone of smart fleet management, driving more sustainable and cost-efficient operations.
Conclusion
Clearly, all these trends are worth exploring.
While some technologies are well-established in the market, others are still emerging, offering the potential for even greater efficiency, sustainability, and safety.
To maximize benefits, focus on adopting technologies with a proven track record of utility, cost-efficiency, and reliability.