Welding operations are some of the most critical tasks on the construction site. They demand outstanding care, skill—and the best possible welding equipment.
In this blog post, you’re going to read about 15 essential pieces of welding equipment you should add to your list if you want to complete your welding operations successfully.
Let’s begin!
In this article...
Welding Helmet
No construction site operation is safe without the use of helmets to protect the worker’s head. Welding is certainly no exception to that rule.
As you can imagine, welding operations are pretty intense, and without proper protection, you’re risking life-threatening injuries. The first one is the increased risk of severe burns to the face.
Pure iron is welded at the temperature between 2,500 °F (1,400 °C) and 2,700 °F (1,500 °C). Suppose a worker sustains an injury from a burning welding lamp or a hot piece of metal.
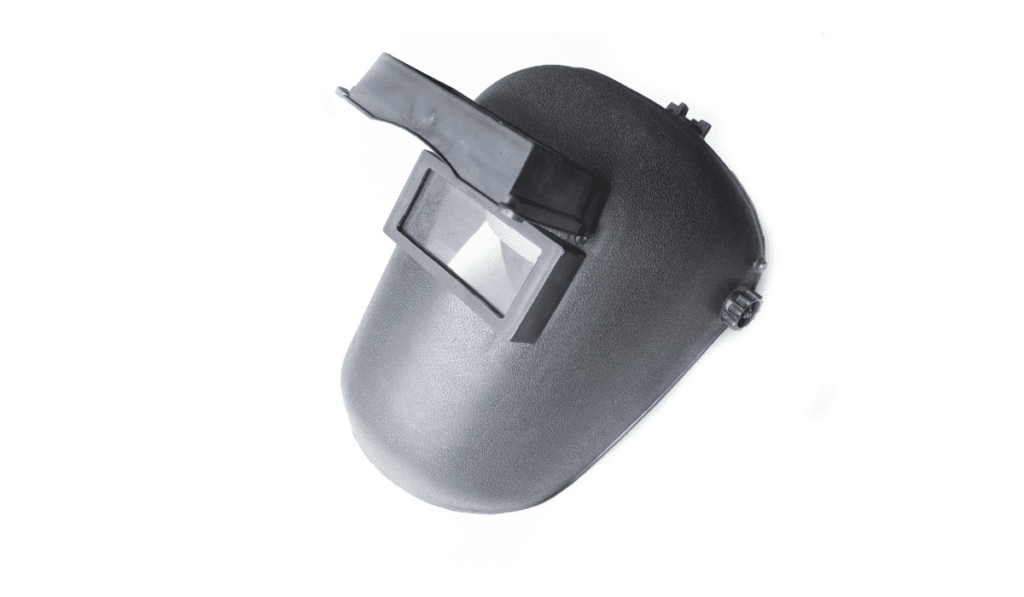
In that case, it can very well permanently disfigure them or lead to a fatal secondary infection. In addition, welding without a mask can lead to severe injuries to the worker’s eyes.
There are hot particles flying towards the face, along with toxic fumes and intense exposure to UV light.
According to OSHA standards, wearing welding helmets is mandatory during welding operations. They play an active role in protecting the safety of workers.
Welding Jacket
Similar to welding masks, welding jackets are also critical for keeping workers safe.
Welding jackets can be made from different protective materials, from leather to fire-resistant wool.
A welding jacket won’t catch fire if a piece of burning matter falls on its surface, keeping welders from sustaining burns and injuries to their front while welding and working in extreme heat.
A major advantage of wearing a welding jacket is that it protects all the body parts that are typically more exposed, such as the worker’s neck or the upper part of the arms.
This is what a welding injury to the upper arm looks like:
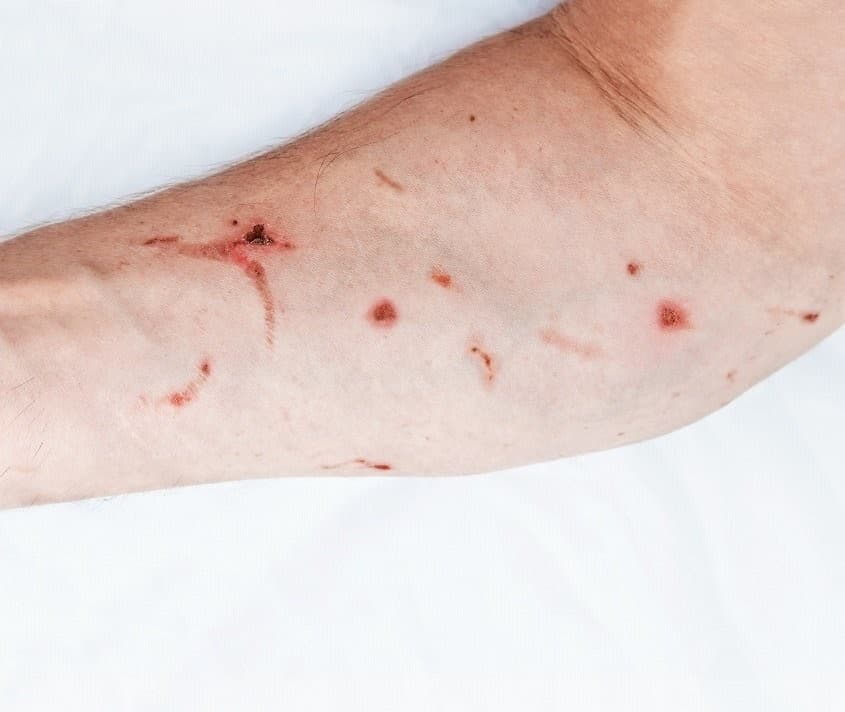
If you want to prevent such—or worse—injuries from occurring, you have to take the proper precautions, and providing the appropriate protective equipment is a major aspect of that.
Welding Gloves
It’s impossible to complete a welding job safely without wearing welding gloves.
A welder’s hands are always close to the welding point, so they’re exposed to immense heat and splatter materials.
Since welding tasks involve various heat levels and materials, it’s essential to pick up the type of glove that can match a particular welding assignment.
For instance, horsehide gloves are suitable for Tungsten Inert Gas (TIG) welding because they allow for great precision of movement while maintaining firmness and durability.
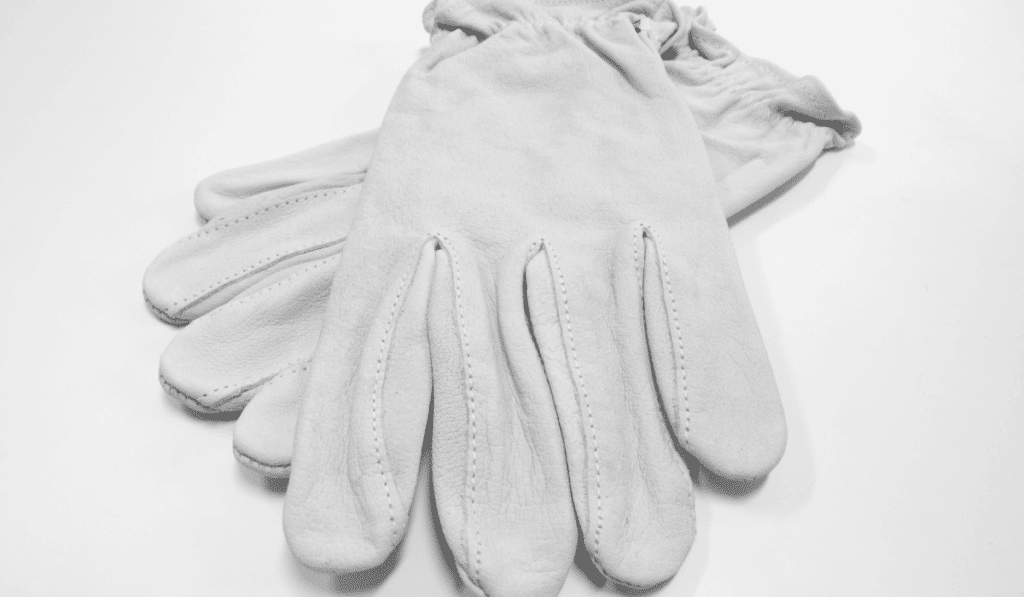
On the other hand, stick welding and Metal Inert Gas (MIG) welding are usually done with materials like elkskin or cowhide.
Make no mistake, without welding gloves hands are constantly exposed to damage.
It’s important to note that welding gloves vary in size, meaning that a contracting firm is obligated to secure welding gloves that can comfortably fit the welder’s hands and offer dexterity.
Ear Protection
When you’re welding metals, you’re exposed to high levels of noise.
To put things into perspective, sounds at or below 70 dB are safe, according to the National Institute of Deafness and Other Communication Disorders.
However, unless we’re talking about TIG welding, welding lamps reach noise levels well over 85 dB during operations.
When people are exposed to noise exceeding that level for a longer time, they’re putting themselves at risk of damaging or permanently losing their hearing.
One academic study on noise exposure among welding workers found that roughly 93% of welders lack adequate hearing protection. These numbers are alarming.
Thankfully, various forms of hearing protection are inexpensive and easy to acquire, the most common ones being earmuffs and earplugs.
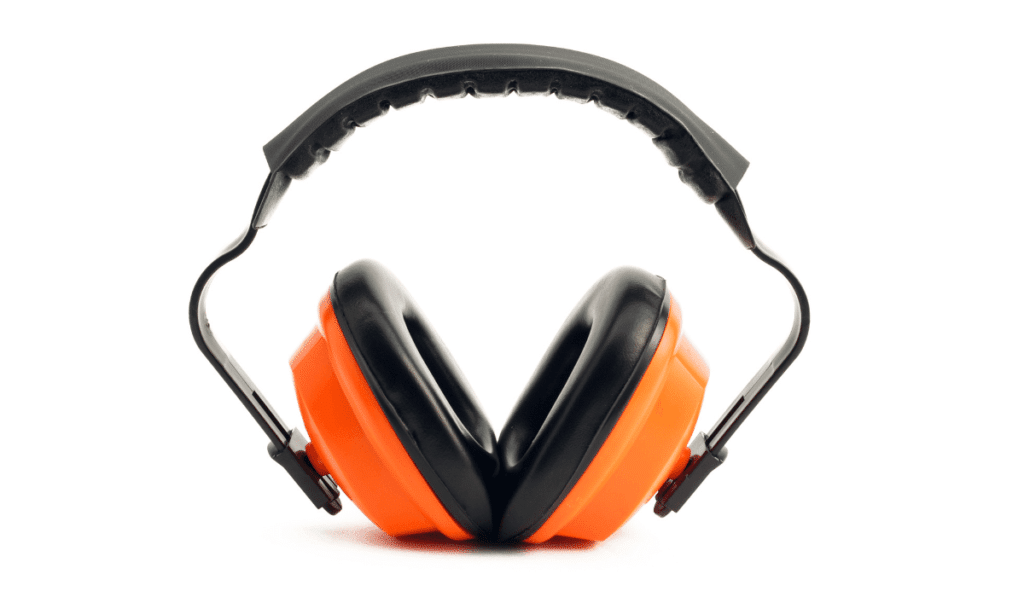
Keep in mind that, according to OSHA’s rules, ear protection is mandatory for welding operations for workspaces where employees are exposed to noise over 85 dB for over 8 working hours.
Welding Shoes
Welding shoes are the last piece of essential personal protective equipment for welding we should mention.
When they’re welding a metal surface, your workers can acquire injuries from falling hot objects, which might cause burns, or electrical hazards.
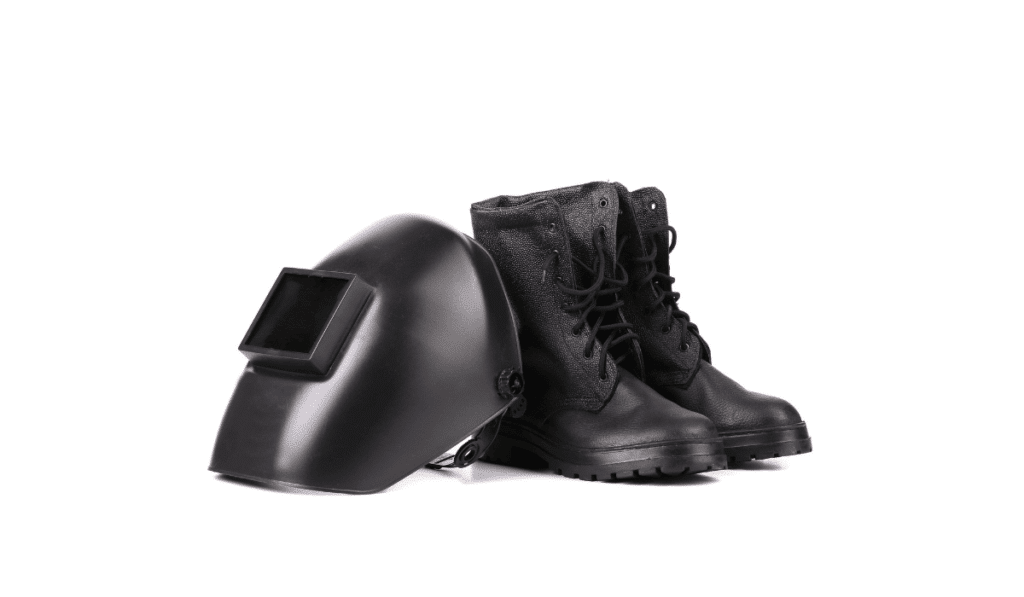
If you don’t address these issues, you’re likely risking a serious worksite accident.
That’s why welding shoes are so important.
Welding shoes are a distinctive piece of PPE; they are fire-resistant and have a steel-toe top.
They are made to provide a secure footing so that the welder won’t trip or fall during welding. As with other welding PPE, such shoes are mandatory on worksites.
Welding Magnets
Since precision is essential in welding, professional welders use welding magnets as supporting equipment, in order to set up an accurate holding for welded materials.
This enables them to handle the filler metal instead of holding the base materials together.
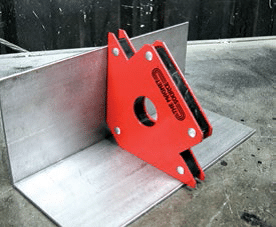
You can see how the welding magnet makes welding easier in the picture above. Not only are the welder’s hands freed, but the materials are held together at a perfect 90° angle.
Welding magnets can stick to any metal surface and secure the objects at an angle of 45, 90, or 135 degrees. There are also adjustable 360-degree ones available that can attach to any piece of metal.
The next must-have item on our welding equipment list is, of course, the chipping hammer.
Chipping Hammer
Skilled workers use chipping hammers to finish off their welding projects.
Often, welding leaves an uneven edge that needs to be flattened out before the project is done. One of the best ways to do this is to even it out with a chipping hammer. However, the hammer has to be quality-made to avoid breakage.
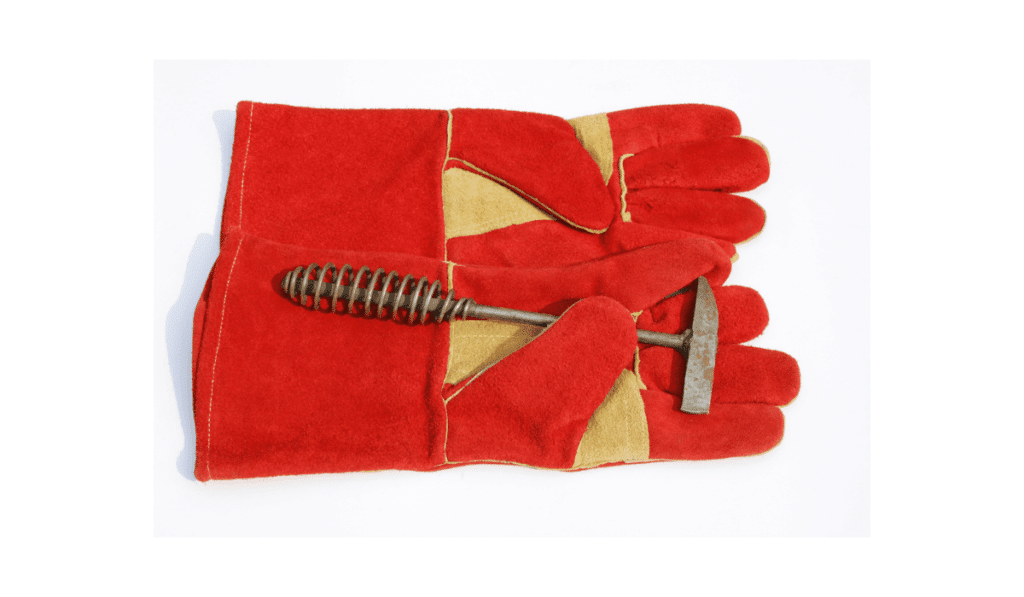
A great chipping hammer also has a firm handle that can absorb the force of impact while remaining comfortable to handle.
Chipping hammers usually have pointy or square hammerheads, depending on their specific purpose.
Another must-have supporting tool for welding are welding pliers.
Welding Pliers
Welding pliers enable welders to work with their lamps in a way that’s safe and quick.
As you know, welding lamps have lots of interchangeable accessories for specific tasks. Since lamps are burning hot, it’s often impossible to remove accessories directly by hand.
In those situations, welders use welding pliers.
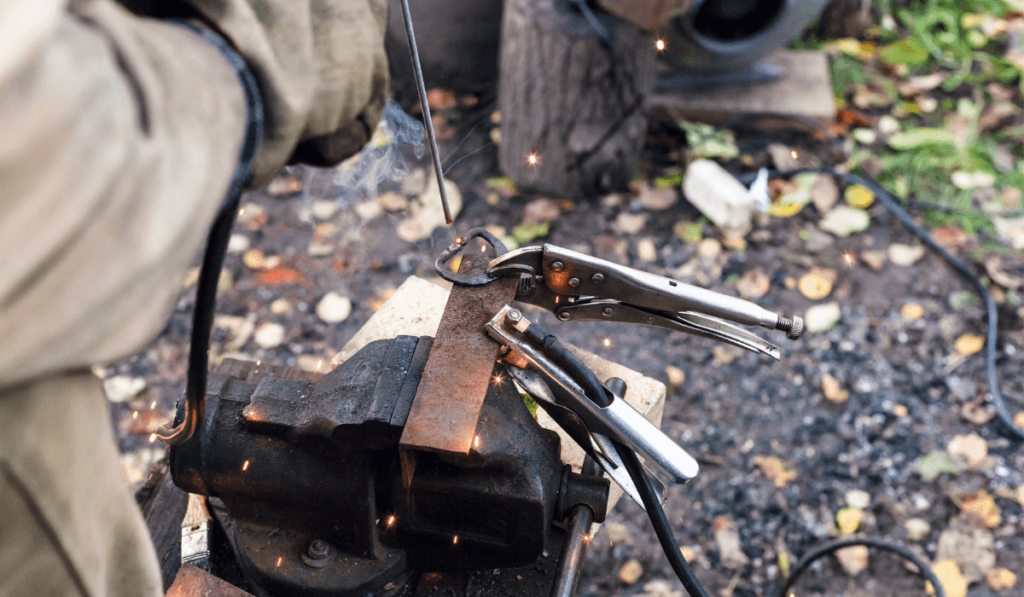
For example, if you want to remove the nozzle or loosen the contact tip, you’re best off doing so with welding pliers.
Welding pliers come in different shapes and forms, but they’re inexpensive, so there’s no excuse for leaving them out of your welding toolbox.
Welding Wires
If you want to weld a piece of metal, you need to light a wire on fire to connect two pieces of metal together.
When exposed to heat, the wire will soften and melt between the two welding points.
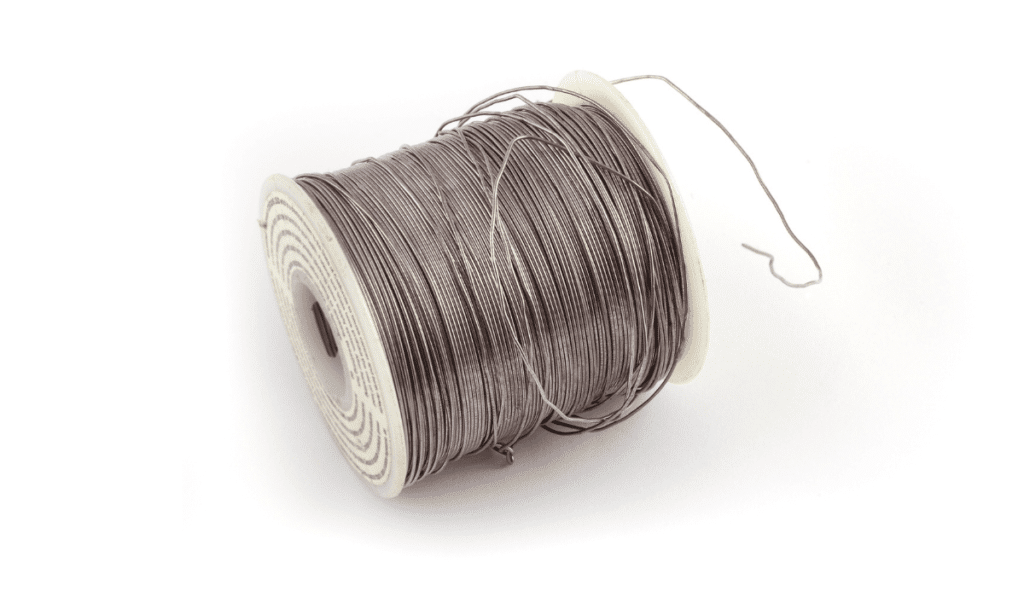
Naturally, there are various types of welding wires, which differ based on factors such as their diameters and chemical composition. The wire you’ll need should be made of the same material as the metal you’re welding.
So if you’re welding a stainless steel surface, for instance, you’ll use wires with steel as the primary material.
If you want to get the correct welding wires for your project, always identify the metal you’ll be welding first and then pick the matching wires.
Stick Welders
When people think about welding lamps, stick welders are usually the first thing they imagine.
Stick welders are popular around construction sites and home welding shops alike.
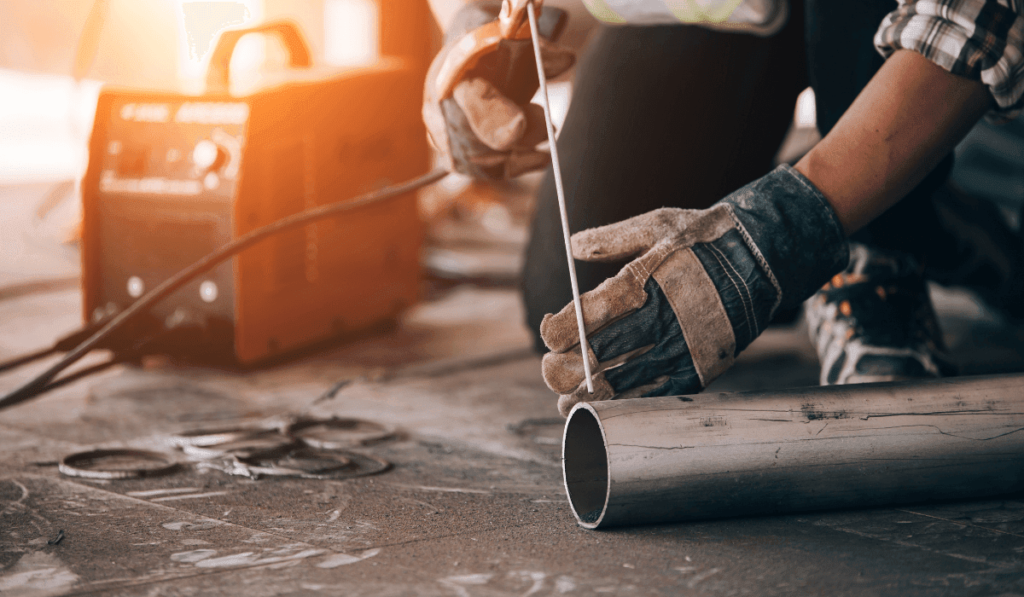
A typical stick welder is powered by an electrical current that powers the lamp and enables the metals to fuse.
Another great trait of stick welders is that they’re the cheapest in terms of energy consumption. However, their use is limited to metals thicker than 1/16 of an inch.
MIG Welders
As mentioned earlier, MIG welding refers to metal inert gas welding.
During MIG welding, a thin metal wire acts as an electrode at the end of the torch. The wire is continuously fed through the nozzle when a welder pulls the trigger.
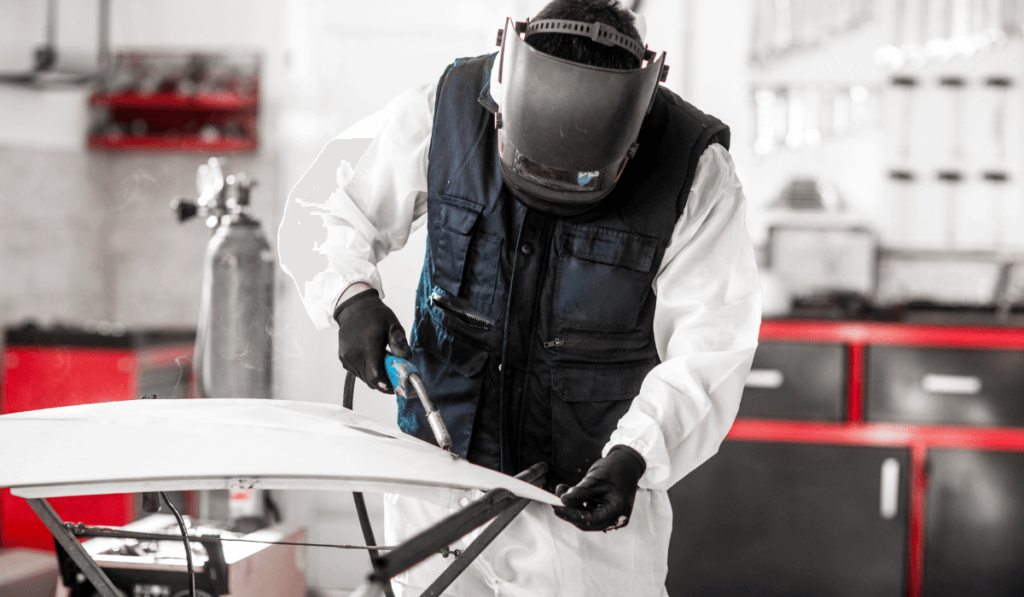
The electric arc heats both metals above their melting point and enables them to melt together.
MIG welders are renowned for being clean and portable. They are a common choice of welding machines on busy construction sites that work with steel.
TIG Welders
Similarly, TIG welding stands for tungsten inert gas.
TIG welders are unique in their use of the tungsten electrode. Unlike the electrodes in MIG welders, when tungsten electrodes get hot, they don’t melt and become filler metal.
Therefore, we can use a TIG welder without filler metal by applying its arc directly to the base metal.
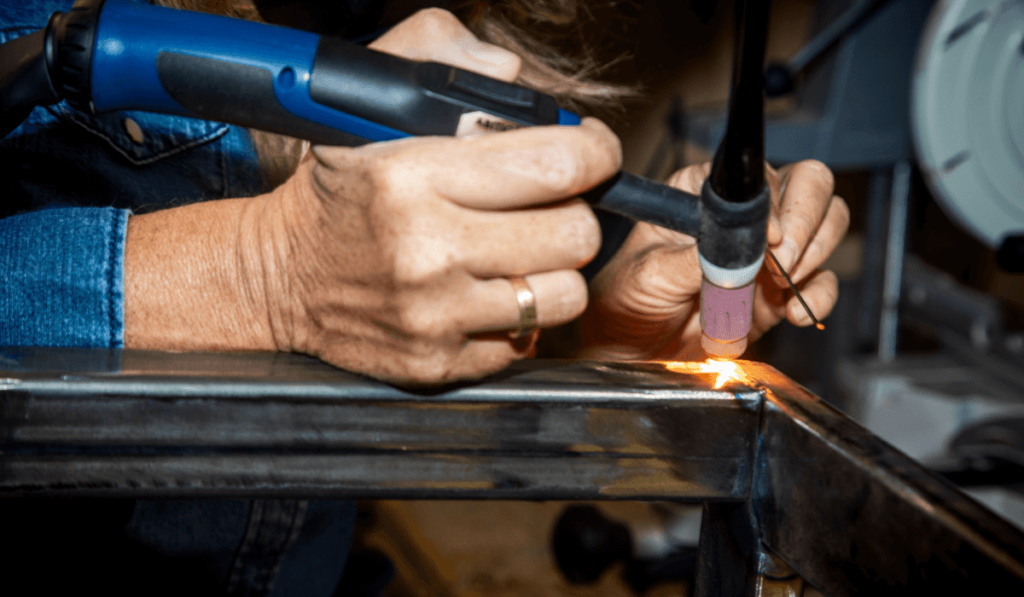
The tungsten electrode is non-consumable, meaning you don’t have to replenish them constantly as the welding process goes on.
TIG welding is often used to weld thin alloy steel, stainless steel, copper alloys, and aluminum. Operating a TIG welder requires skill, and they are essential for complex and precise welding projects.
Multi-Operator Welding Systems
Multi-operator welding systems offer an outstanding combination of multiple welding modules operating on a single power supply.
For instance, you can have a multi-operator with both MIG and TIG welders on one unit, which is a welcome boost in productivity in demanding and busy worksites.
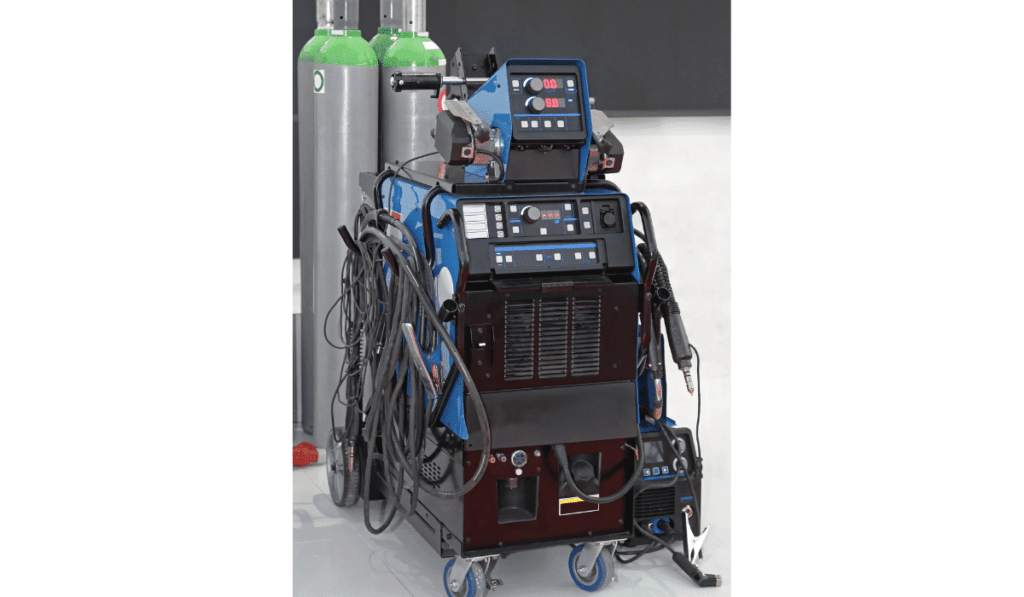
You’ll commonly see them at factories, repair yards, and construction sites. Multi-operator welders enable more workers to tackle tasks independently without having to use multiple power sources.
Besides increased productivity, their main advantages are:
- Low installation costs
- Low maintenance requirements
- Fewer energy costs compared to multiple welding machines
- Easy to transport
Lastly, let’s discuss cylinder trolleys.
Gas Cylinder Trolley
Even though gas cylinder trolleys aren’t the first thing that comes to mind when we think about welding, they’re an indispensable asset for this type of activity.
When handling gas cylinders for welding lamps, you’re going to need a tool to transport them safely. Workers should always transport gas cylinders in a vertical position.
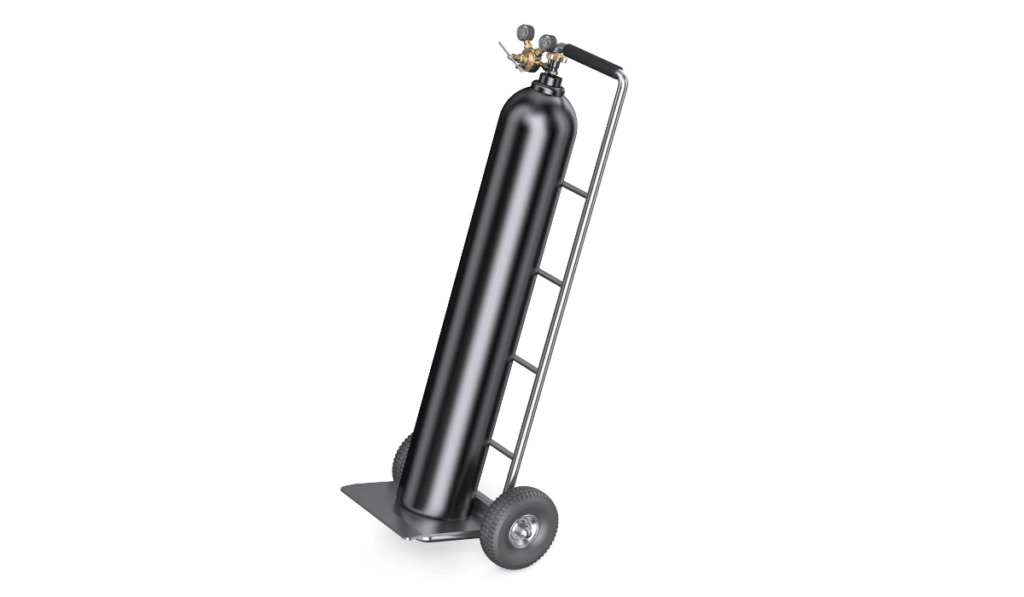
However, since the cylinders are tall and heavy, moving them is difficult without trolleys. If workers try transporting them without a proper tool, they risk dropping the cylinder and injuring themselves.
That’s why gas cylinder trolleys deserve their place on this list of indispensable welding equipment. They represent safe and practical means of transporting cylinders across worksites.
Conclusion
If you’ve managed a construction project, you’ve likely seen your fair share of onsite welding.
This article has covered PPE welding gear, supporting equipment, and different types of welders you might use for your welding needs. As with every construction site task, your workers need their essential welding equipment to complete it efficiently.
Hopefully, after reading this article, you’re more familiar with the equipment you need for efficient welding.