Owning and operating a fleet of heavy construction equipment is an expensive venture, so construction managers often seek ways to trim the expenses related to equipment.
In the midst of this, you might find yourself grappling with decisions on whether to buy new equipment or opt for rentals.
Tracking your equipment efficiently, figuring out the ideal times for regular equipment downtime and preventive maintenance, and finding time for employee training, are tasks you should thoroughly consider.
This article further analyzes these important cost management strategies that will help you cut down on construction equipment expenses without compromising efficiency.
In this article...
Decide Between Renting vs. Buying
Determining whether to buy a new piece of construction equipment or opt for renting is a critical decision that requires careful consideration, taking the overall cost into account.
It’s commonly known that construction machinery and heavy-duty vehicles come with higher price tags.
Merely as an illustration, the average price range for a mid-sized wheel loader that would serve most construction companies can cost between $100,000 and $200,000.
On the other hand, depending on the type, size, and power of the equipment, you can expect a cost from as low as $100 to as much as $3,500 per day or more to rent one.
Understandably, both options have their advantages and downsides, so before choosing which way to go, you’ll have to weigh several key factors such as usage frequency, total costs, and urgency.
But first, you’ll have to analyze your current work volume and needs and do the math.
In construction, a general guideline is that if you use a piece of equipment less than 60% to 70% of the time, renting is a better option.
However, if your usage goes beyond that, it might be worth considering buying or leasing.
Try to see the big picture and anticipate your future needs—if renting becomes as expensive as owning, it’s a sign that it’s time to make a purchase.
On the other hand, owning equipment comes with its own costs, including ownership expenses such as storage, maintenance, and transportation.
To have a better understanding of all the factors, let’s take a look at the following example.
Your San Francisco-based company wins a project bid in Los Angeles.
To do the job, you need to factor in the expenses associated with transporting equipment over a distance of 400 miles.
This includes costs for the truck, driver, loading and unloading time, and fuel.
Additionally, upon reaching the job site, there’s the need to hire personnel for equipment maintenance and refueling.
On top of that, you should also include costs for insurance, maintenance, and depreciation.
This leads to the conclusion that, sometimes, it might be more cost-effective to rent equipment locally rather than incurring additional costs.
To help you get a clearer picture, the comparison below breaks down the pros and cons of renting, leasing, and buying construction equipment.
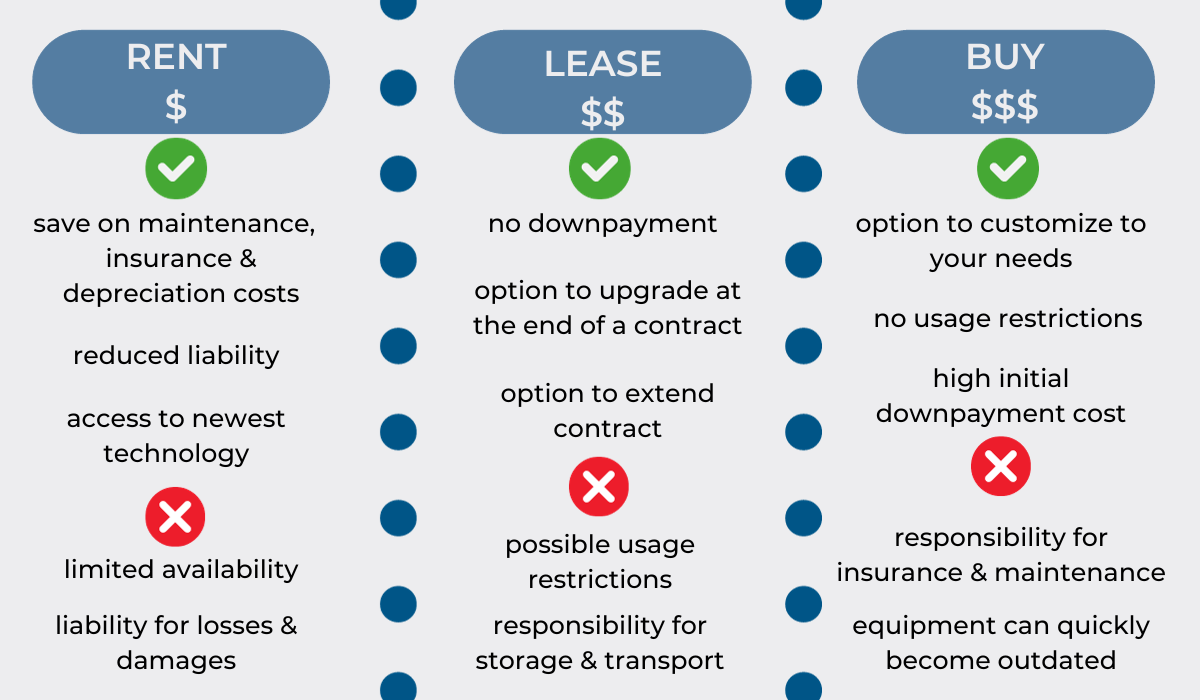
However, to be able to make an informed decision start with assessing your current needs and capacities—how often do you need a particular piece of equipment?
Are you ready to make a hefty investment?
How do ownership expenses compare against total rental costs?
Finally, whether you opt for renting or owning, or do a mixture of both, focus on a strategy that will ultimately reduce your operational costs.
After all, expanding your business can be a straightforward process if you track your expenses and budget wisely.
Keep Track of the Equipment
Construction sites are very often targeted by thieves due to the number of high-value equipment deployed for the build.
Large sites can contain hundreds of thousands of dollars of equipment and building materials.
If not secured, these items can be stolen quickly and without notice.
And when a valuable piece of equipment gets stolen, it’s often gone for good, as statistics show that only 21% of stolen equipment is recovered.
Falling victim to theft can seriously disrupt your operations and finances, potentially leading to debt because impending losses extend beyond the value of the lost equipment itself.
Namely, if theft occurs during a project, you’ll experience unexpected downtime and costly delays.
On top of that, finding a replacement piece of equipment on short notice can also incur substantial expenses.
So, the best way to protect your business is to protect your assets.
An equipment tracking software solution offers an effective prevention against theft. It can help you significantly reduce the risk of your critical equipment being stolen or lost, saving you thousands of dollars.
The tracking solution provided by GoCodes Asset Tracking includes tagging equipment with QR codes on the identification labels.
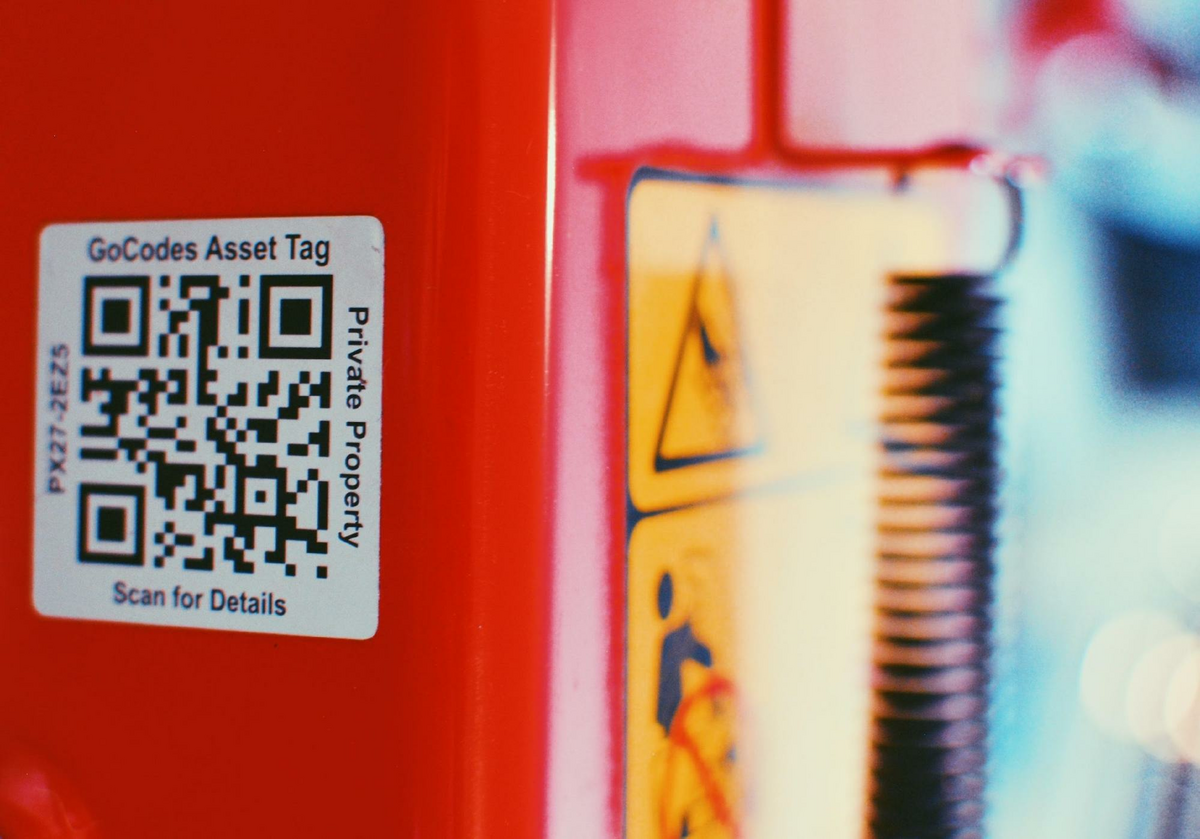
These labels are easy to scan with the GoCodes Asset Tracking app.
Each scan records its current GPS location and reveals all of the information pertinent to that piece of equipment, including the name of its owner.
In other words, by using QR code tags, you not only discourage potential thieves, both internal and external to the company but also enhance the likelihood of equipment recovery.
The software also allows you to incorporate a check-in/check-out system for your equipment.
When a member of your team of builders needs to use the equipment for the day, they simply scan the tag to check it out, linking themselves to the equipment until it’s checked back in.
This system allows you to view the equipment’s last known GPS location and a list of users, helping you keep a close eye on your company’s valuables.
In conclusion, theft can cost construction businesses a lot of money.
Using equipment tracking software is the most viable option when it comes to deterring thieves and safeguarding your company’s assets.
Train Employees on Proper Equipment Use
The efficiency of your equipment depends on the skills of your operators.
Learning the basics through on-the-job training with experienced crew members is a great start for new workers.
However, this level of training may not be sufficient to consistently maintain a safe environment and high productivity.
Moreover, today’s advanced construction equipment is packed with functions and features, while new software tools are increasingly integrated into everyday processes.
Implementing formal training on equipment usage puts every employee on the same page regardless of their experience level—new employees will receive standardized training and the more experienced ones will refresh their knowledge or learn to use a new technology.
Consistently training employees is also vital for preventing workplace accidents due to improper use of heavy equipment.
When equipment operators are well-trained, they will be able to avoid unnecessary risks more effectively and work at a higher level of safety.
Trained employees are less likely to experience accidents that may result in injuries and fatalities, or cause damage to equipment.
For instance, the image below provides visual guidelines on how to properly use a forklift to avoid accidents.
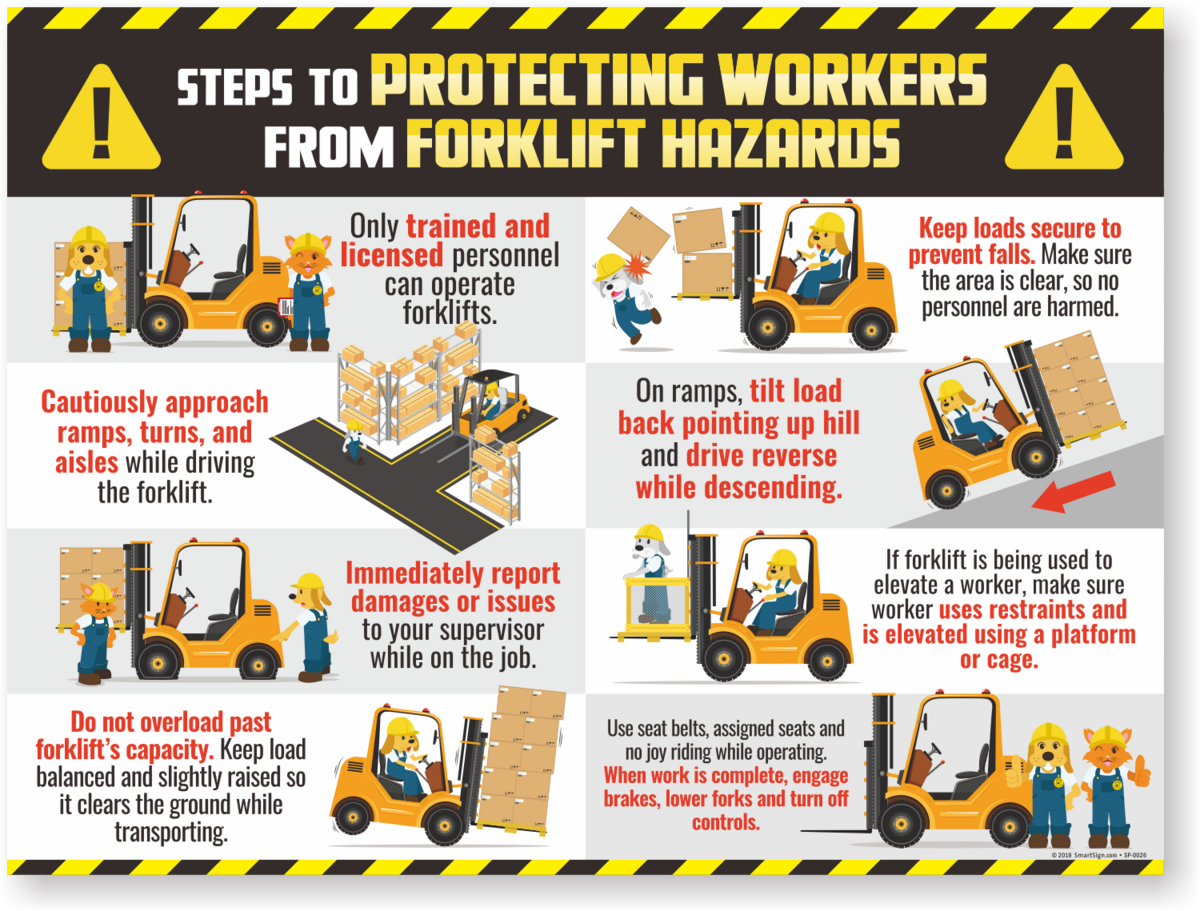
Additionally, mistakes made by operators can lead to situations that require rework which consumes a considerable amount of time and money.
Reworks can increase the original contract cost by around 9% and extend the initial project schedule by nearly 10%.
Skilled operators are less prone to making that kind of error, helping you to keep on schedule and within budget.
At last, employees with proper training can better understand equipment’s limitations and specific features, enabling them to operate within its designated limits.
Skilled operation helps preserve components longer compared to rough and insecure usage, saving the equipment from damage.
When your operators grasp the equipment’s performance and are knowledgeable about its capacities, they can considerably contribute to reducing maintenance and ownership costs.
In a nutshell, regular training and upskilling can enhance your workers’ efficiency, ensuring safer work environments and saving your business from unexpected labor and equipment-related expenses.
Schedule Regular Downtime
Most of the construction equipment is not intended for continuous 24-hour use.
Pushing a piece of equipment to operate beyond its designed limits can potentially lead to damage or premature failure.
Scheduling regular equipment downtime will help you extend your assets’ lifespan and avoid spending extra money for expedited maintenance services if a piece of equipment malfunctions in the middle of a project.
Scheduled downtime can be strategically planned to minimize its impact on production.
You can use that time, for example, to focus on smaller, lower-priority projects that can be completed without the use of heavy equipment.
Moreover, by scheduling more planned downtime, you reduce the need for reactive maintenance, thus ensuring that efficiency and profitability remain at high levels.
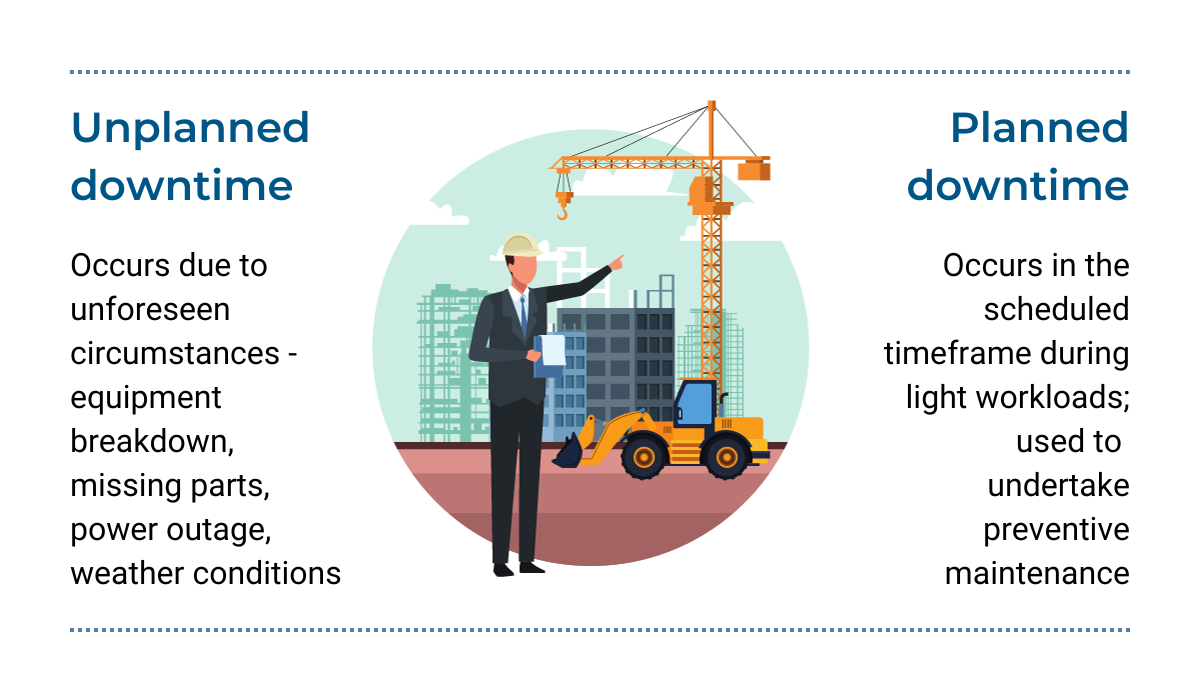
In essence, planned downtime is all about strategy regarding upcoming tasks.
Consider the following example.
If you know that a motor requires shutdown and lubrication every 100 hours, you can plan for this downtime in various ways.
This could include setting up an alert for when the motor reaches 100 hours, ensuring you have the right lubrication available, and creating a task for your maintenance team.
In other words, scheduled downtime can allow you to plan in advance and make sure that necessary resources, such as labor and parts, are available.
This approach will reduce the total costs of downtime and increase efficiency.
In general, overworking your equipment will increase the risk of wear and tear, resulting in mechanical failures.
Therefore, scheduled downtime is an inevitable step in ensuring your equipment gets enough resting hours and proper preventive maintenance.
Implement Preventive Maintenance
While every piece of equipment has its average lifespan, preventive maintenance can make all the difference in optimizing equipment utilization and safeguarding your profits.
The importance of the issue is reflected in the fact that just a 1% drop in equipment productivity can cause a 2.75% drop in total project profits.
Therefore, putting extra effort into keeping your equipment in good shape will undoubtedly prevent more serious problems in the future.
The first step is to establish daily visual inspections of your equipment.
These may include checking oil and fluid levels, the condition of tires and tracks, and the functioning of lights and indicators.
In the long run, implementing a robust preventive maintenance schedule will ensure that your critical assets run smoothly and enjoy an extended lifespan.
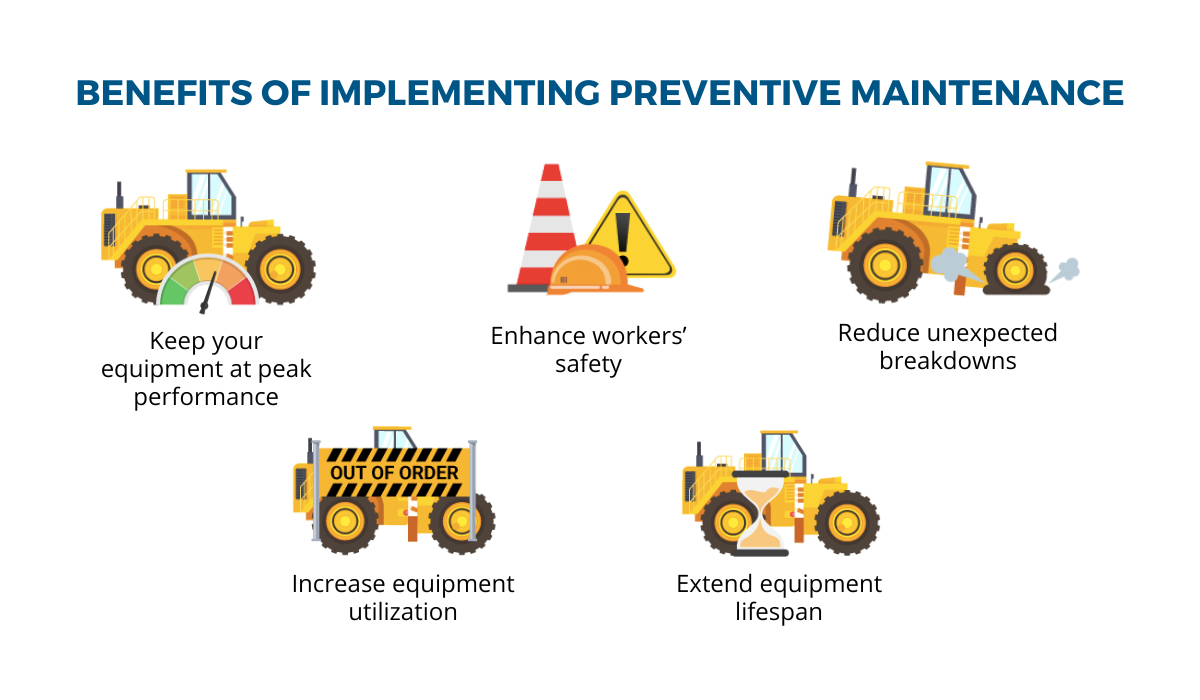
An efficient equipment monitoring solution can assist you with this task as it allows you to keep detailed maintenance logs and equipment records in your central database.
With GoCodes Asset Tracking’ scannable QR codes, operators and maintenance staff can easily access a wealth of information about the equipment.
This includes operator manuals, manufacturer details, and a history of maintenance actions.
Moreover, the software offers a maintenance scheduling feature to help you set a future service date and assign the task to your maintenance team.
In addition, setting up automatic service notifications is an effortless way to guarantee that preventive maintenance is never missed.
This will allow you to put an effective preventive maintenance system in place, thus prolonging the useful life of your critical construction equipment.
Conclusion
Running a fleet of heavy construction equipment comes at a steep price.
In the heat of the cost-cutting battle, you should be mindful when choosing between investing in new equipment or embracing the flexibility of rentals.
Efficiently tracking your equipment, strategically scheduling regular downtime and maintenance, and ensuring thorough employee training are monumental tasks that demand your careful consideration.
Ultimately, adhering to this plan will leave a positive impact on your year-end bottom line.