Pre-construction planning is a proactive way to approach a project in order to ensure you complete it on time and within budget.
To achieve this, all relevant aspects of the project need to be addressed and decided on ahead of time. This includes expected quality, project goals, profitability, and worker safety.
When you have a clear overview of the project, you can anticipate issues and prevent errors.
Here are the top 6 benefits of the pre-construction planning process that are sure to convince you that all construction companies need a planning process.
In this article...
Defines Clear Objectives
Starting any work without clear objectives hinders your ability to get the results you want.
During the pre-construction planning process, you need to ask yourself:
- What are your business goals?
- What are the client’s main needs?
- Which tasks are crucial to the success of the project?
- What resources are essential to accomplish these crucial tasks?
These initial questions will be the foundation on which you can set more tangible objectives. It’s also important to mention that goals and objectives constitute separate categories.
Goals are the end result, while objectives are steps to get you to those results.
Generally, objectives cover different areas in a construction project, such as:
Performance and quality | Clear metrics and standards ensure quality is preserved to the end of the project. |
Budget | Improper budgeting can lead to project failure so it’s important to plan for resources, investments, overhead, insurance, and other financial requirements of the project. |
Completion time | Planned progress needs to follow actual progress. Objectives determine how much time workers need to complete each task and how that affects the final project completion time. |
Sustainable development | How will you address environmental concerns and regulations? Which sustainable materials do you need to procure? How will you take care of your construction waste? |
Health and safety | Evaluate different risks that can pop up during the construction phase, conduct safety training, and set protocols to protect everyone onsite. |
Remember that objectives are guidelines so your entire team and workforce can work in harmony.
They will know what’s expected of them, so they’ll be more driven and waste less time. This also helps you further evaluate their performance and assess failures.
Therefore, you’ll be better prepared for other construction phases once you have clear, feasible, and measurable objectives in the pre-construction planning process.
Determines the Deadlines
We’ve mentioned that you’ll need to set time constraints for your project during the pre-construction planning process. But we need to emphasize how vital creating deadlines is.
Currently, over 66% of contractors are experiencing delays on their projects.
This means that they accrue additional expenses on labor, permit extensions, and equipment rental, among other things, which can negatively impact their profitability.
Or, in the case of this construction company, they’ll need to offer compensations to their end users because of the construction delays.
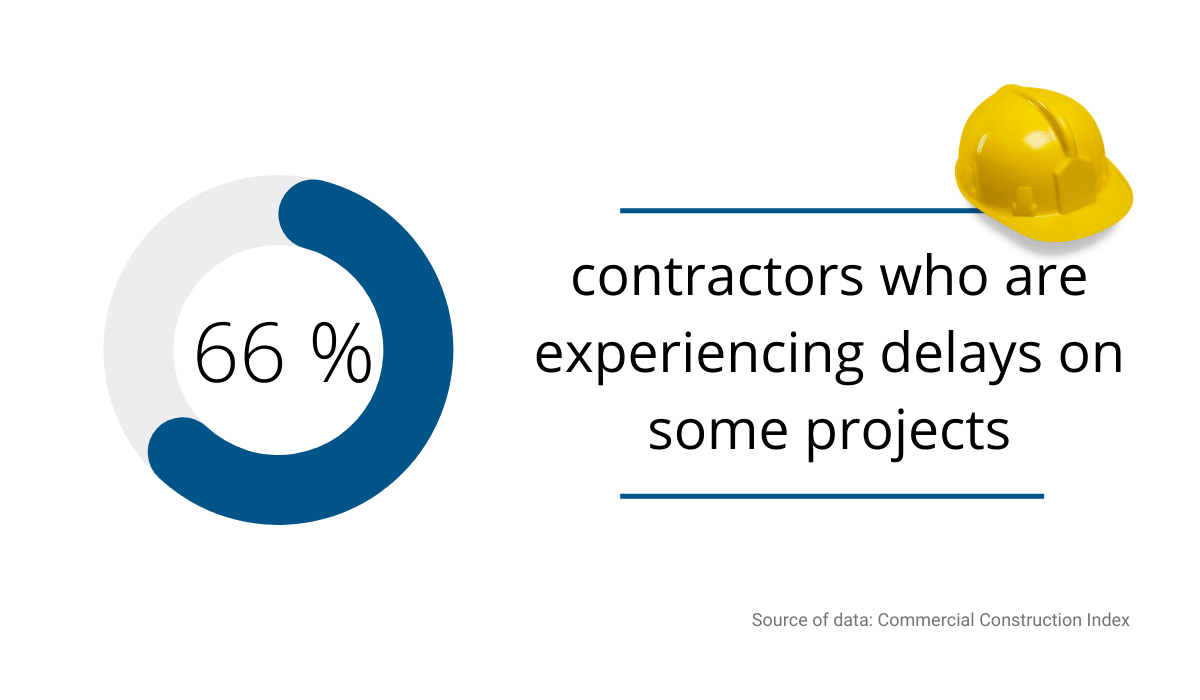
As you can see, such delays can negatively affect your relationship with clients.
Contractors have agreed to finish a project in a certain timeframe, so the client depends on those promises.
If contractors don’t fulfill the deadline agreement, the client won’t be able to rent, sell or use the project when they expected.
The client’s satisfaction promotes your business and generates more projects, so if you break deadlines frequently, this can break your future business prospects.
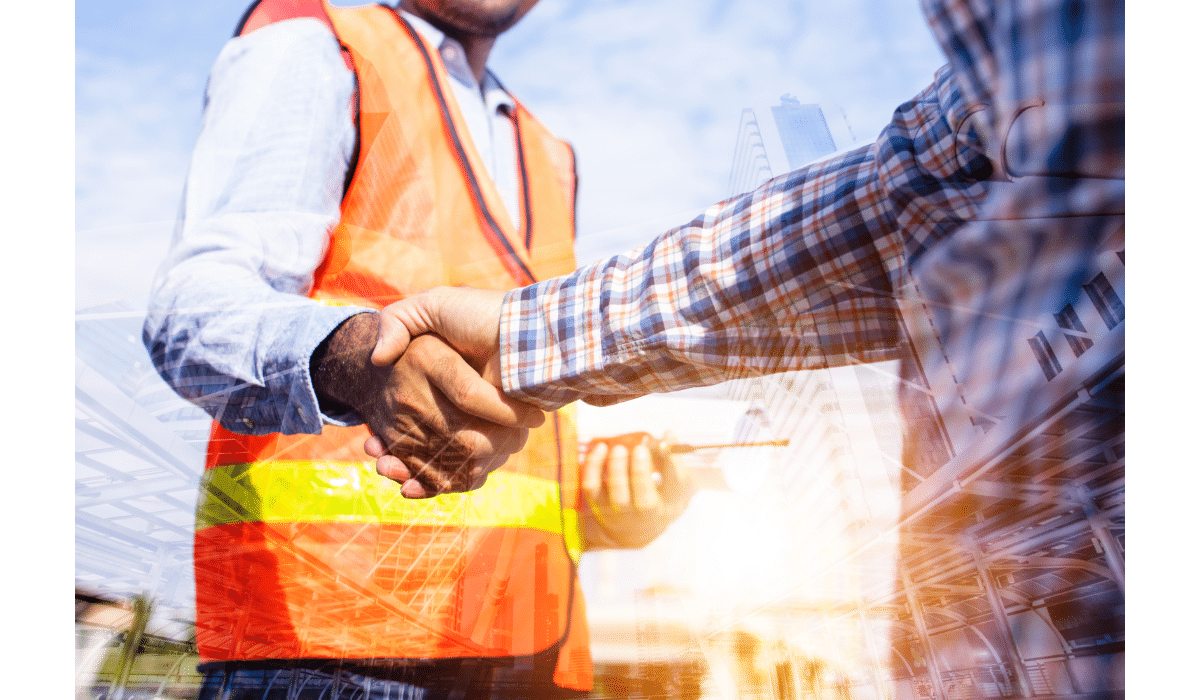
Obviously, some delays are inevitable, but not all delays are created equal.
For example, there’s nothing you can do if it rains heavily for a week and you can’t install a new roof on time.
But if you notice that your heavy equipment tends to arrive at the site late, you can put scannable tags on them and monitor their transport more closely, to minimize these delays before they start affecting the entire project.
It’s important to establish deadlines you can control during the pre-construction planning process and make sure they aren’t too tight.
That way, your workers will not ignore safety protocols as they rush to finish their tasks on time. Tight deadlines can make people cut corners, so they’re not just jeopardizing their health, but the overall quality of the project.
Poorly done work can extend deadlines even more.
According to Travis Voss, Leader of Innovative Technology at Mechanical Incorporated, overtime on a project rarely pays off, so it’s important to be more proactive in preventing delays.
A pre-construction plan will help you set realistic deadlines your workforce can follow. This will ensure everyone sticks to the schedule to finish the project on time.
Estimates the Costs More Effectively
A construction project’s finances are one of the essential elements in the pre-construction planning process. Think about the various components that go into project estimations:
- Material Prices
- Quantity Takeoff
- Labor Hours and Rates
- Equipment Costs
- Indirect Costs
You can’t get anything done if you don’t know how much you’ll have to spend.
More importantly, the clients need to know how much funding the project really requires. That way, they can make adjustments to save money and find adequate channels to cover various expenses.
So, the more comprehensive your estimates are at the beginning, the better informed you and your clients are about the project’s financial constraints.
Also, effective planning makes the procurement process easier, and gives you better control of the project’s expenses in later construction stages.
For example, South Bay Construction often presents options to the client to increase value and reduce costs after looking at the materials and design choices at the beginning of their project planning process.
According to the company, this approach holds developers and contractors accountable in case of increased costs.
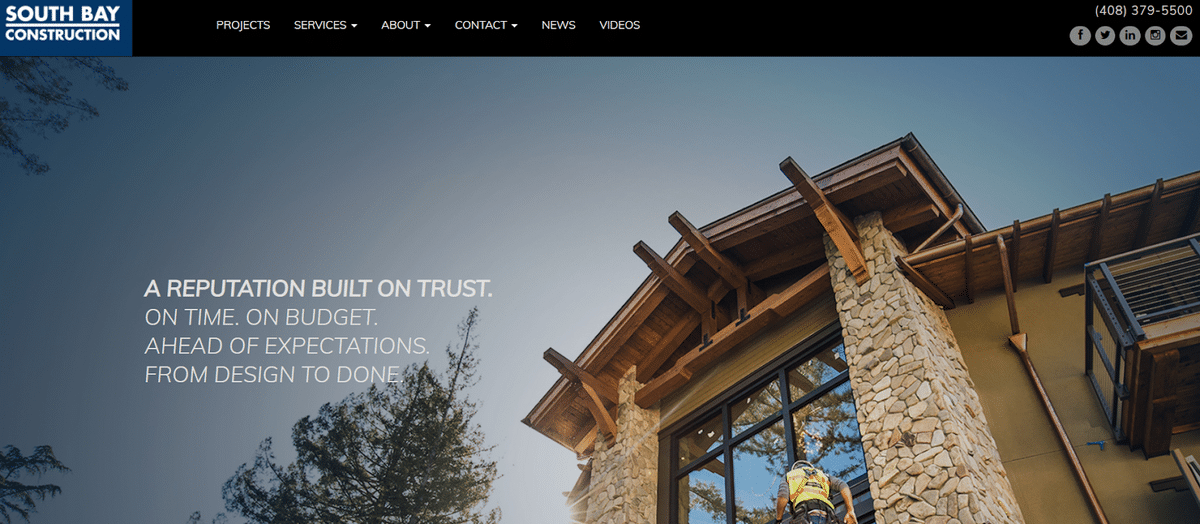
A feasible budget controls most design choices in project planning. Pre-construction planning helps you evaluate the feasibility of these design choices and prevent any surprises.
Additionally, you can find major cost savings at the beginning and protect yourself in case of material cost changes.
Remember that the pre-construction planning process can help you provide more clarity on various expenses and secure adequate funding.
Troubleshoots Anticipated Issues for Project Managers
Unfortunately, construction sites are not immune to setbacks.
Difficult weather conditions, equipment failure, scheduling problems, and many other issues can halt even the most carefully planned projects.
But that’s not a reason to abandon pre-construction planning! Just because you can’t eliminate these issues, doesn’t mean you shouldn’t have systems in place to minimize their impact.
By carefully examining the project’s scope, requirements, and plans at the beginning, you can anticipate issues in various areas.
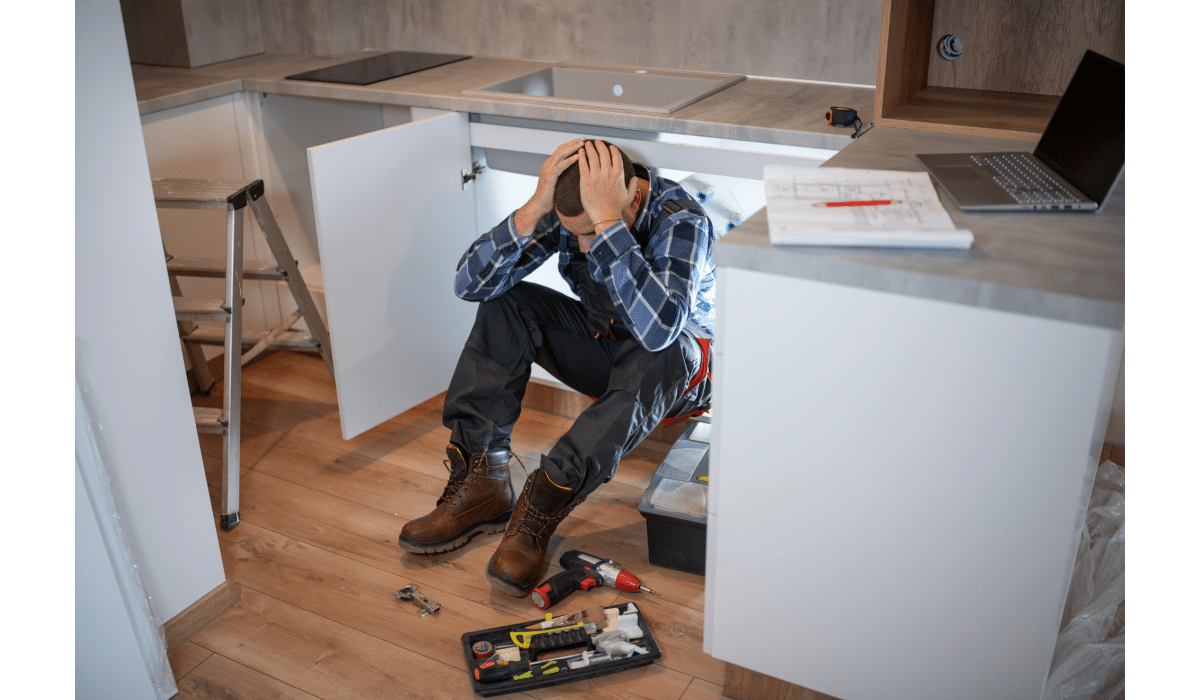
In essence, if you have to react to a problem, you might not be able to mitigate negative consequences.
This is especially important regarding safety management.
According to a report by Deloitte, if companies have to react to safety issues, it means they haven’t adequately prepared their company to reduce safety risks in their operations.
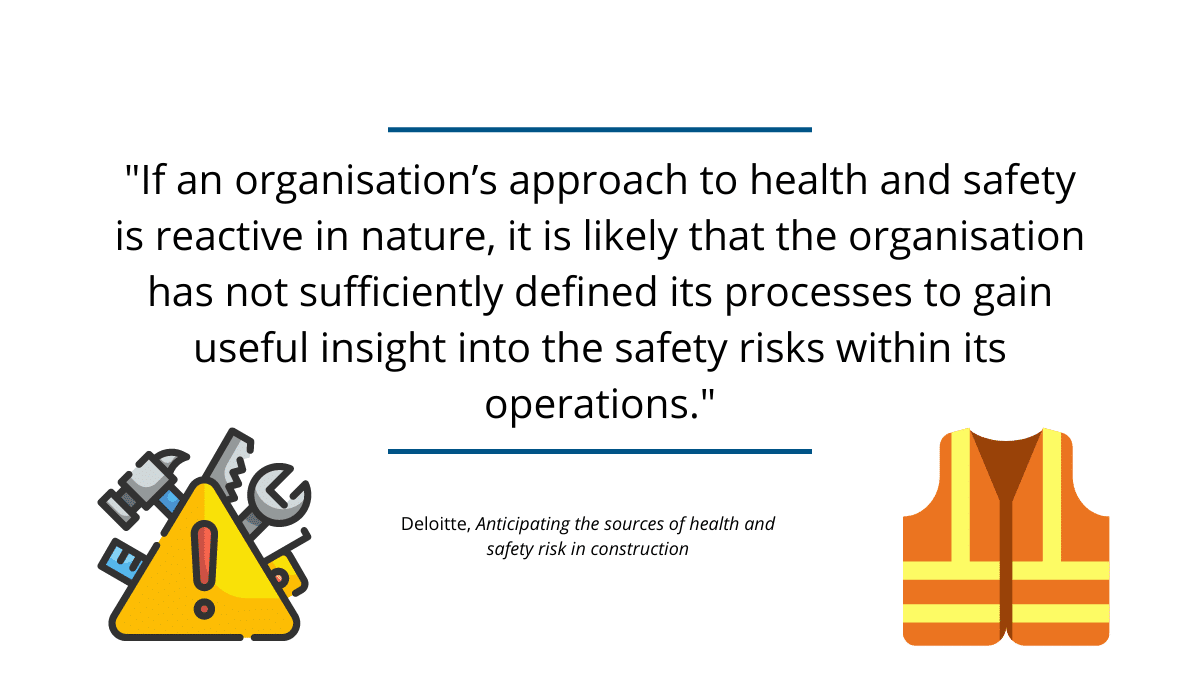
In other words, inadequate risk management can lead to an escalation of problems in your company, causing additional expenses, unexpected downtime, ruined reputation, or stress.
Following that, the pre-construction planning process will aid you in making better decisions and acting proactively during the entire construction process when it comes to mitigating project risks.
Early identification of potential issues is crucial for the whole team to know what to expect and implement necessary solutions to the problem on time.
So, the sooner you start accounting for potential obstacles in your operations, you’ll help yourself and your team effectively solve problems (if they occur) and keep the project moving forward smoothly.
Prevents Possible Errors During the Construction Phase
As you start your construction project, Ron Black believes three things happen:
“(…) things that you thought wouldn’t happen did, things that you didn’t even think about happen or things that are completely impossible happen.”
Or, to put it differently, while some problems you can’t prevent, there are others you can.
Creating drawings, plans, models, and blueprints for a project are necessary tasks that need to be done before a shovel hits the ground.
This is what you’ll cover during the pre-construction planning process.
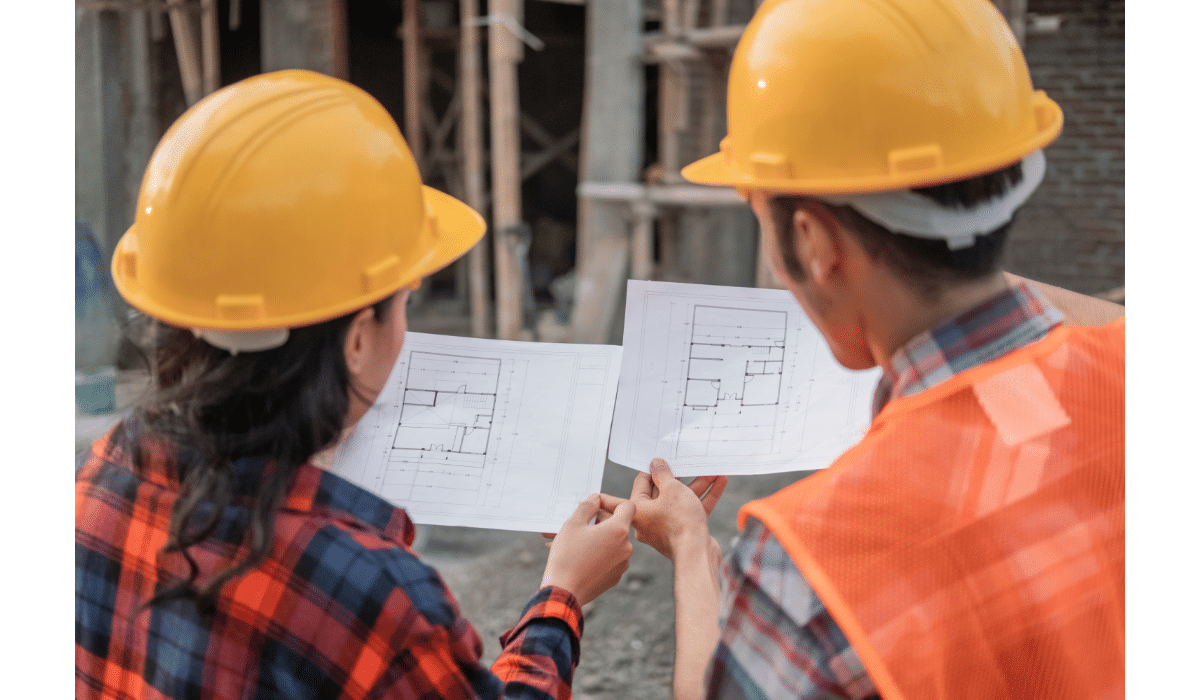
Essentially, this is the phase where you can find and eliminate most errors that concern project design, which ultimately reduces the amount of RFIs and rework during the construction phase.
A clear pre-construction plan can save resources and time, not to mention preserve the required quality.
With so many processes in place, Black’s advice is to take any possible errors into account as early as possible. Most importantly, get your entire team on board.
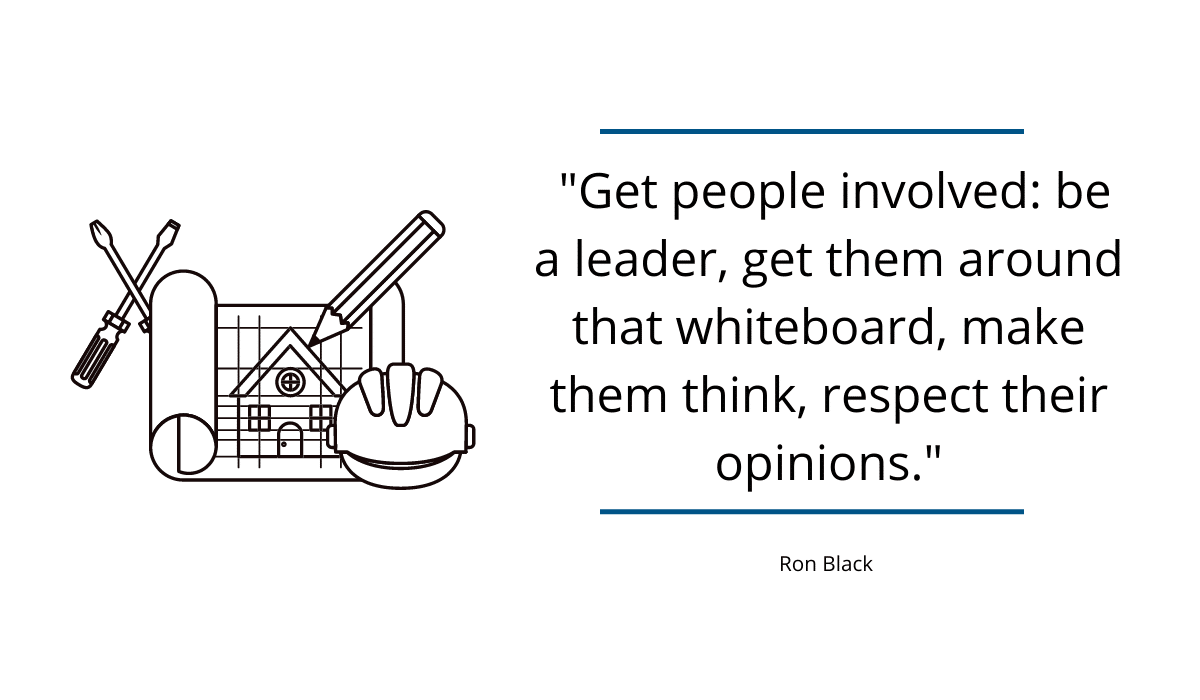
Everyone involved in the project needs to get their input at the beginning, so you have a better overview of potential issues.
Not to mention that different people can use their experience and knowledge to ensure the project is completed successfully.
Or, to put it simply, what architects and engineers might overlook, contractors can notice on time and prevent the problem from escalating (or vice versa).
It all boils down to creating effective project plans to prevent errors during construction, which you can do during the pre-construction planning process.
Maximizes ROI
This is the primary question for any business endeavor: “What is the return on investment?” Obviously, you don’t want to take on an unprofitable project.
That’s not why you started your construction business.
ROI will vary from project to project, but it’s important to do the math to determine if it’s worth your time and effort.
But while you’re probably used to associating ROI with monetary gains, there are different ways to measure ROI.
Sometimes that can include:
- Satisfied clients
- Happier workforce
- Reduced waste
- Increased competitiveness
- Improved productivity
This is where the pre-construction planning process truly proves its worth.
With an early detailed analysis, estimating, and input from different stakeholders, it’s easier to determine ROI for any project.
In turn, you can pick profitable and suitable projects that will scale your business in the way you want.
Additionally, it can also mean investing in other areas such as equipment and software that will optimize your business operations.
That way, you can take on bigger and better projects without fear you don’t have the right resources.
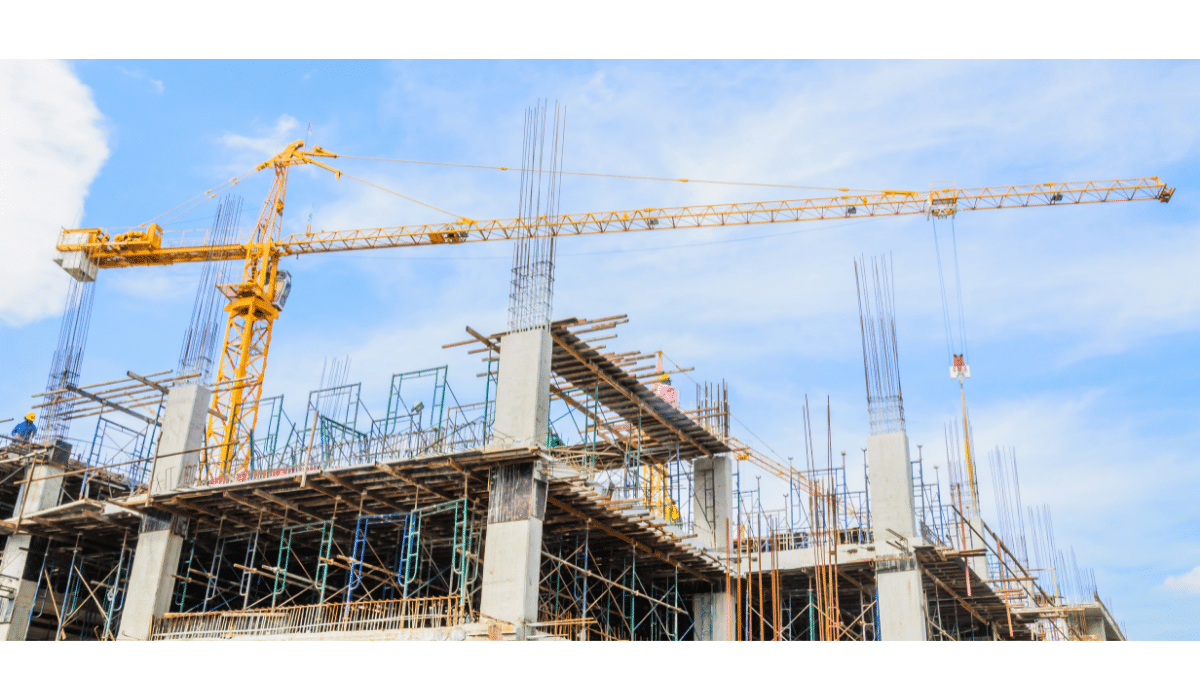
For example, if you notice in the planning process a job requires hiring a crane that might be out of your current budget, but the overall ROI is positive for the company (e.g., expanding to other sectors, faster completion rate, etc.).
With a pre-construction plan, you can better decide whether the investment is worth the future profitability.
The more valuable data and information about a project you have at the very beginning, it’s easier to determine ROI on various projects and make better business decisions.
Conclusion
Construction projects are severely complex, so having a pre-construction plan is essential to avoid going over deadlines and budgets.
But time and monetary concerns are not the only benefits of pre-construction planning.
You can reduce preventable errors and even establish different protocols if you’re aware of issues that frequently pop up on construction sites.
All in all, creating detailed plans beforehand can make all your future projects more profitable and enable you to scale your business.