With supply chain challenges to face, as well as a shortage of raw materials, project managers increasingly find themselves looking beyond their regular sources for supplies.
Especially where heavy equipment replacement parts are concerned, the marketplace can prove daunting.
When crucial equipment is down and project managers are pressed to return to schedule, it’s easy to panic and grab the first available item.
And while it might seem tempting to reach for whatever is available or cheaper, contractors can save money and time by undertaking a bit of research.
The two choices that present themselves are aftermarket equipment parts and OEM (original project manufacturer) parts.
The latter, as the name suggests, are parts made by the same company that produced the equipment.
Aftermarket parts, on the other hand, are those available from third parties. The providers might specialize in one company’s products, or try to provide alternatives for many.
With practice and a bit of research into the differences and similarities between these types, project managers can make the right choice taking into account machinery warranties, and the life cycle of their equipment.
Here is a starter primer for choosing between OEM and aftermarket equipment parts.
In this article...
What Are OEM Parts?
Since original equipment manufacturer parts are sourced from the same company that made the original machinery, you can be sure that they’re both compatible.
Moreover, since the replacement parts serve as a reflection of the company’s strong craftsmanship and attentive customer service, the original business is motivated to ensure their quality.
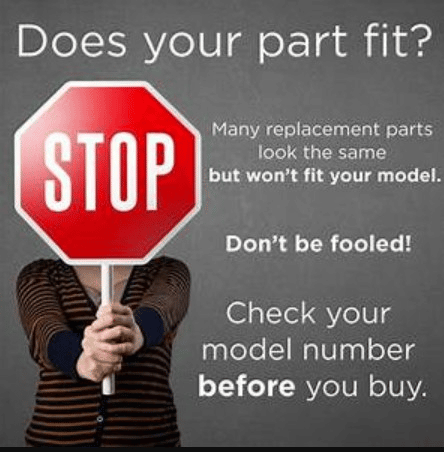
Of course, as evidenced by the customer-facing graphic above, companies prefer end users to purchase only OEM parts.
Not only is this good for a manufacturer’s bottom line, it provides a more stable, less unpredictable experience to company techs called in for upkeep.
And one size definitely does not fit all when it comes to repair and maintenance.
Although it can sometimes feel frustrating to discern between almost identical model numbers for purposes of ordering or invoicing, when they put in the effort to do so, the customer is rewarded with an exact replacement for the particular machine the company owns.
While traditionally more expensive than their aftermarket competitors, OEM parts offer construction companies the assurance of staying within warranty.
Often, using any aftermarket parts, even those added for visual effect, can void the warranty.
That’s an expensive mistake to make in an attempt to save a few dollars on manufacturer-sourced parts.
In addition, OEM parts tend to yield higher performance, more longevity, and more easily directable maintenance actions.
When a company purchases a piece of machinery for its fleet or workforce, tech teams or equipment managers are often the designated point of contact between the company and the distributor.
This means an easy and fast phone call to a single maintenance rep or hotline when time is of the essence.
What Are Aftermarket Parts?
The world of aftermarket parts can feel like a walk through an enormous craft show—so many items crowd in next to one another, all wildly different.
It might seem overwhelming to know who to trust and who is merely seeking to profit from a desperate contractor.
And companies often come to aftermarket parts in search of a cheaper, faster route to dragging a limping piece of machinery back online.
Especially with the rise of 3D printing, close replicas of original pieces are possible—and increasingly affordable.
New and more efficient manufacturing procedures can mean that an aftermarket part is just as solid and reliable as the original part, and, perhaps even more importantly, is available at a lower price.
As this graphic shows, the aftermarket arena involves an ecosystem of many different sub-industries:
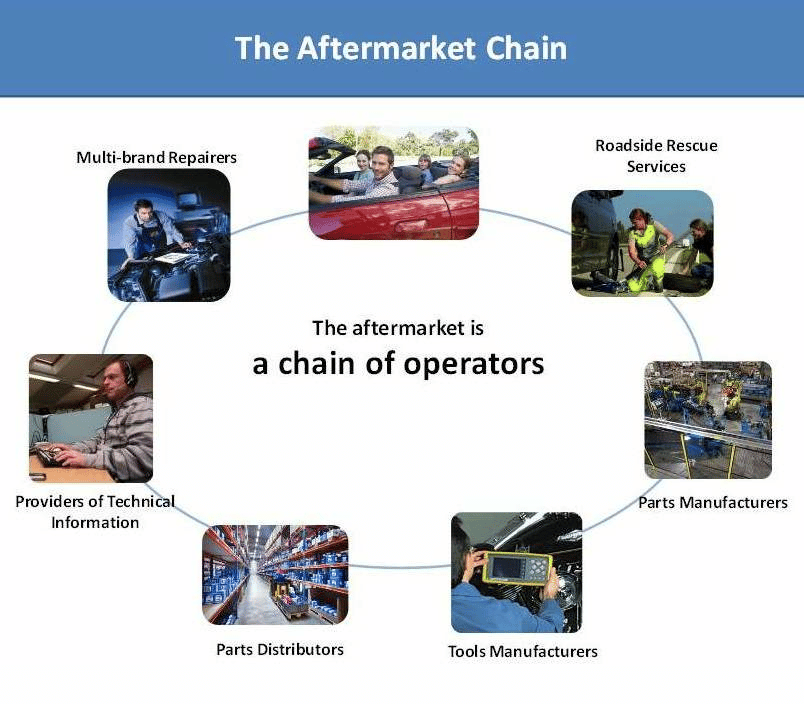
In an era in which people are becoming more and more able to customize their environment, aftermarket parts offer the lure of personalization and modifications specifically to suit their own tastes and needs.
Aftermarket parts provide a virtually unending chance to take generic pieces in a whole new direction for their heavy equipment.
One might think that OEM parts are the best purchase when consumers uncover a ubiquitous flaw or bug in their machine. However, that’s not always the case.
Aftermarket manufacturers are able to stand back and watch a machine’s company of origin work through the flaws and weak points—and then engineer their own response to the issue.
The product they come up with is often free from the constraints of design lock that can prevent techs and engineers from seeing solutions for products they may have shepherded to the showroom over a long period of time.
In situations such as this, a scrappy competitor just might supply a better solution for less money.
OEM vs. Aftermarket: Key Differences
Construction companies also face many differences in price, delivery time, and customer service or tech support.
For example, while reverse engineering might make for a better product with a non-OEM part, this process also requires time.
Moreover, a great deal of resources is necessary to feed the part into the supply chain.
Where newer models are concerned, then, customers might find that ordering from an aftermarket provider, while cheaper, might take longer on the delivery end.
That’s time a project manager might not have if the breakdown occurred while sprinting towards project completion or a milestone.
In addition, aftermarket merchants might not offer technical or maintenance support, leaving the company on its own to conduct the actual service.
However, this might prove a benefit to companies who prefer to allow in-house employees to service their fleets.
This chart is an excellent summation of other OEM and aftermarket differences:
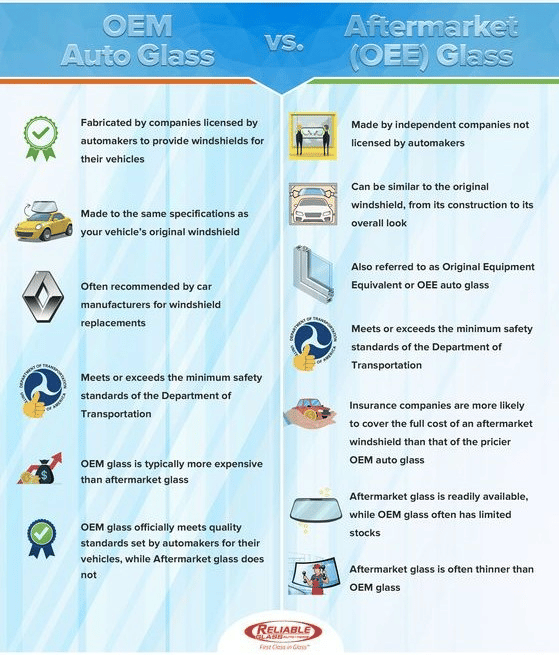
Sometimes, manufacturers direct clients to a single point of contact with requests for parts, usually a regional representative.
While this can make for an easy and fast phone call to just one maintenance rep or hotline, it can also mean that the construction company must suffer whichever employee happens to service its territory, regardless of the quality of their work, with no competition to explore.
In addition, this lack of competition could mean that some manufacturers are not as robust in handling customer care and repair as they are in sales.
The maddening bureaucratic process of enduring the order placement and shipping process can seem endless to a contractor struggling to steer a project back on track.
However, all this frustration might prove worth it if the part is still under warranty and the manufacturer also helps with complex technical problems.
How to Choose Between OEM and Aftermarket Equipment Parts
There’s no question of where to go if a piece of equipment is older and its parts are no longer produced by the original manufacturer.
Construction companies might also have unhappy experiences with the manufacturer, and seek to use aftermarket parts as soon as the warranty expires–or even before.
If replacement parts are still manufactured by the original equipment manufacturer, choosing between OEM and aftermarket will depend on the company’s priorities.
Companies should take into consideration the following factors when trying to decide between aftermarket and OEM parts:
- Project budget
- Availability of the parts
- Where the machinery is in its life cycle
As part of the issue of availability, the accessibility of replacement parts is also an important consideration.
In other words, if a construction business owner finds an aftermarket part for a machine that is out of warranty, inexpensive, and a reliable match for the original, it’s also important to consider where the part is.
If the shipping might take a while and the vendor isn’t nearby, it might make sense to pay for an OEM part that’s more readily available.
As you can see from the chart below, many construction companies have made this very decision:
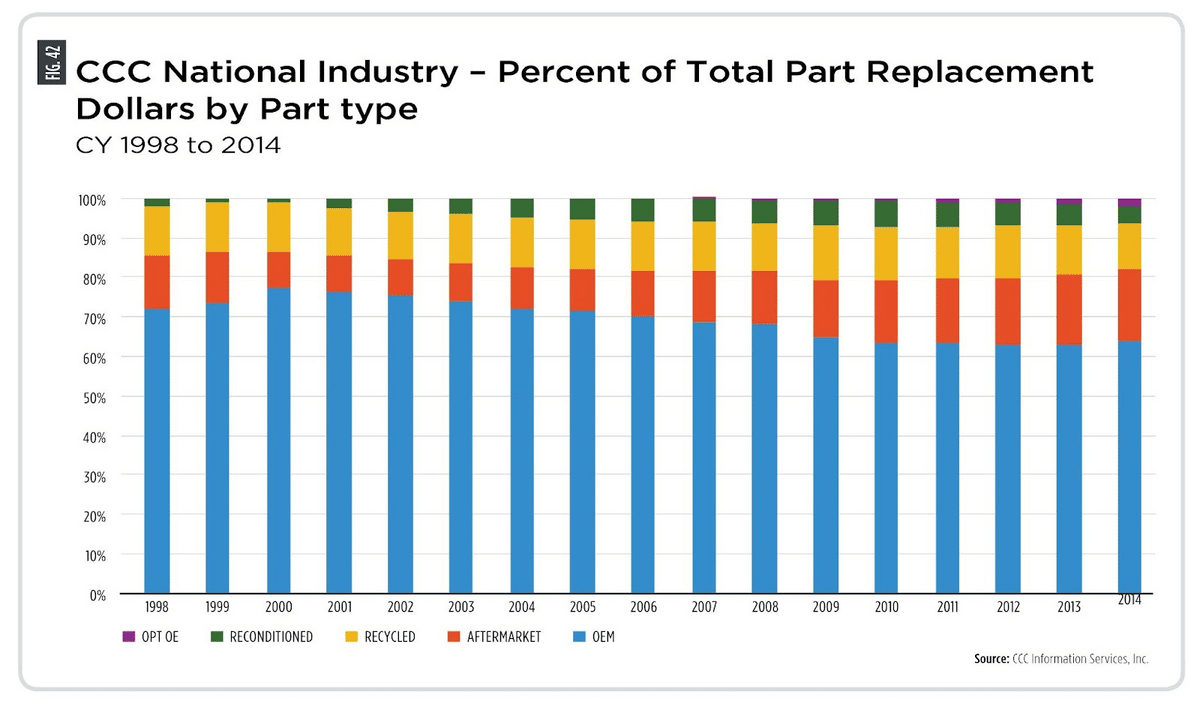
Regarding the life cycle of the machinery, taking stock of how long the equipment has depreciated is an important factor.
If its disposal or resale is imminent, decision makers should take time to weigh the cost of repair versus advancing the purchase of replacement equipment.
How to Manage All Your Equipment Parts
To lessen the chances of a catastrophic breakdown that might prevent careful consideration of whether OEM or aftermarket parts are a better solution, it’s best to invest in robust inventory management such as that provided by GoCodes Asset Tracking.
This way, construction companies can keep automatic watch over which machine is ready for preventive maintenance or where a broken-down vehicle is located.
Efficient equipment audits are also available, along with reports and analyses of asset performance.
The below photo shows sample GoCodes Asset Tracking QR tags, along with the ease of scanning them on nearly any mobile device.

Asset tracking can help techs and mechanics know which parts require ordering.
Maintenance departments will then have plenty of time to make informed decisions on purchasing OEM or aftermarket parts.
This tracking involves labeling each asset, and with GoCodes Asset Tracking, construction companies are welcome to choose the type of tags and tracking to use, such as QR codes, Bluetooth connectivity, and barcode scans.
Conclusion
The decision of whether to buy original equipment manufacturer (OEM) parts or aftermarket parts will depend on the machinery, supply ecosystem, and the project in question.
Often, construction companies have to weigh cost against time to make a choice that serves the client and company best.
The warranty or life cycle status of the machinery also comes into play.
OEM parts will provide an exact replica for the original part and might contribute to helping the machine stay in warranty.
On the other hand, aftermarket parts are usually available for a fraction of the cost and are a better solution for companies that choose to perform maintenance in-house.
Whether choosing to use OEM parts, aftermarket substitutions, or a mix of both, construction companies are wise to track their assets in partnership with GoCodes Asset Tracking.