Every successful construction endeavor begins with a solid plan.
Without it, projects would not only exceed their budget constraints but also struggle to meet deadlines.
But, what lies at the core of a good project plan?
That’s right— construction material takeoff.
This document ensures that there are just enough construction materials, equipment, and skilled workers to guarantee the success of every project.
So, continue reading to discover the key elements of a well-executed construction takeoff.
Who knows?
Perhaps some of these insights will prove instrumental in securing that next bid.
In this article...
Quantities and Measurements
When it comes to construction material takeoff (MTO), the primary task is to identify how much of each material you need for successful project completion.
This involves calculating the quantity requirements for every element involved in the construction of a specific structure, ranging from raw materials like lumber to intricate details such as kitchen cabinet handles, all based on the project’s blueprints or design.
Depending on the material type, various measurements are employed for quantity takeoff, with the most common ones being count, length, area, and volume.
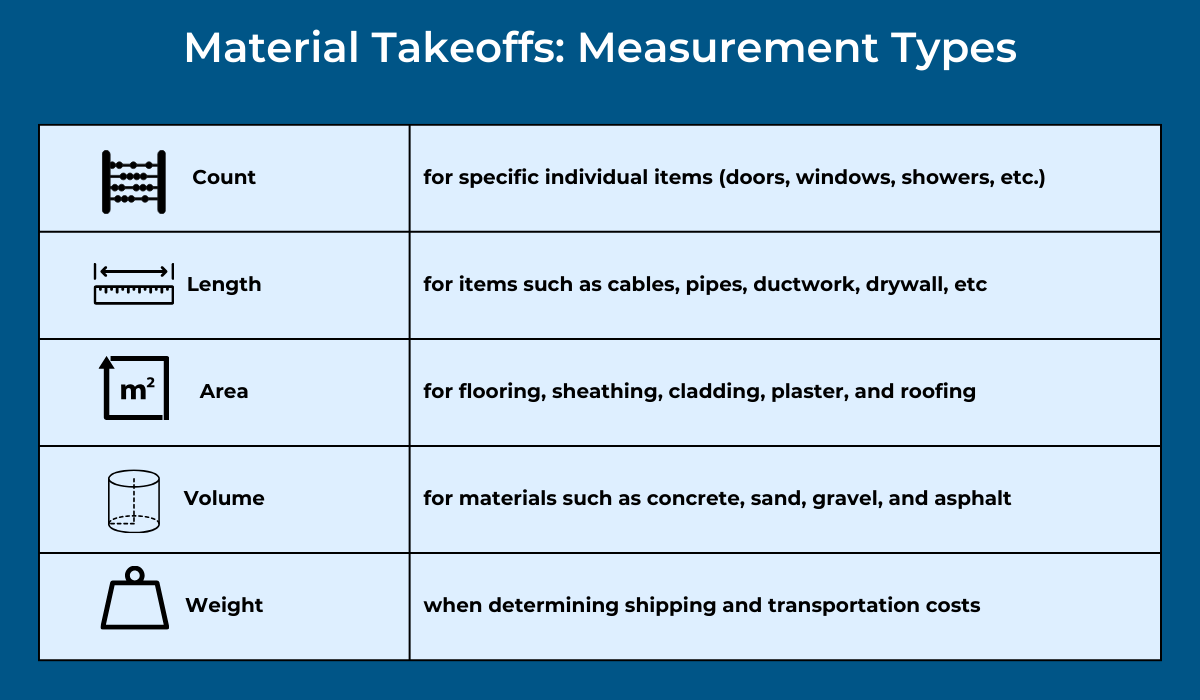
Weight, however, is not always included in takeoffs, but it can be relevant for large-scale projects when determining shipping costs.
Precision is paramount in this process, as these assessments play a crucial role in cost estimation, budgeting, procurement, and, most importantly, winning bids.
In simpler terms, if this task isn’t executed well, you face the following risks:
- Lost business opportunities
- Budget overruns
- Project delays
- Reputational damage
As Marisol Escobar, scheduling manager at Alamo NEX Construction, says, material takeoff is the foundation of project success.
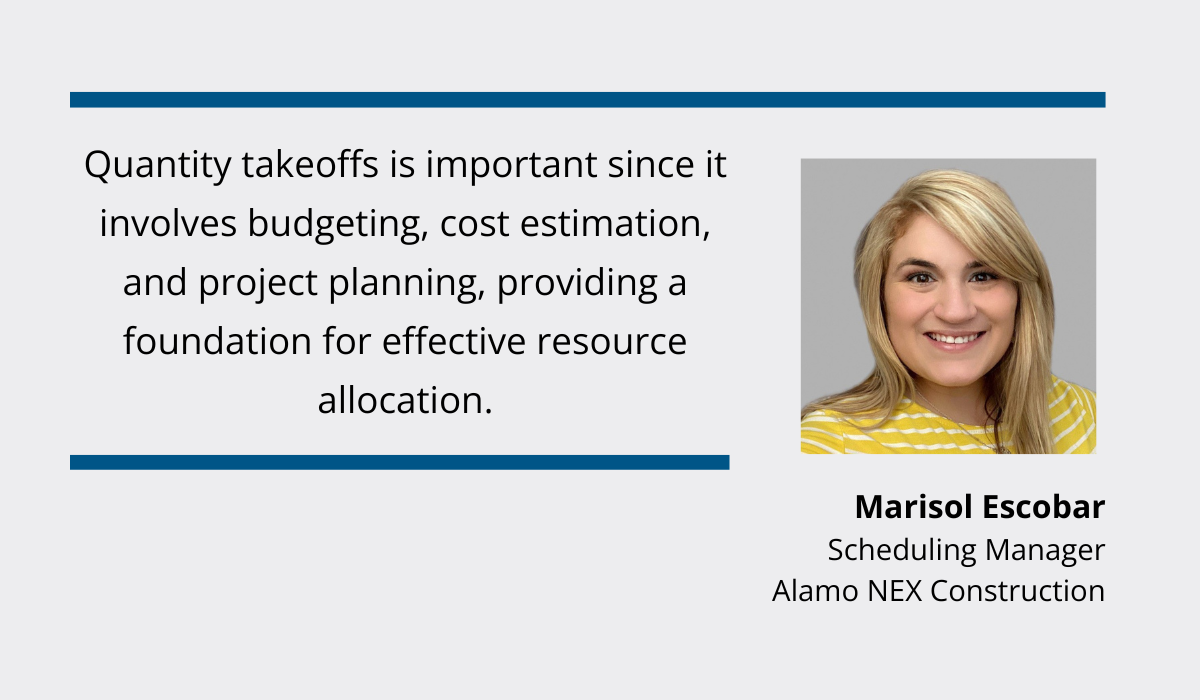
She emphasizes that MTO helps with efficient resource allocation, guaranteeing that you have everything you need precisely when you need it.
In a way, material quantity estimation impacts every aspect of a project, from the operational to the financial one.
Lack of key materials, for example, can impede the team’s ability to complete tasks on schedule.
Excessive material acquisition, on the other hand, may present challenges in terms of limited cash flow and diminished profitability.
All in all, you can view MTO as the starting point in the project journey, with successful realization being the final destination.
Accurate material quantities then act as a guiding force, ensuring the work progresses within budgetary constraints and adheres to the established timelines.
Material Specifications
In addition to specifying the quantity of materials needed, it’s crucial to provide detailed information about their specifications as well.
This includes determining:
- Quality
- Grade
- Size
- Brand
- Manufacturer
For instance, just listing “lumber” on the raw materials list won’t cut it.
Instead, precise details such as size (e.g., 2x4s, 2x6s, or 4x4s), grade, type, moisture content, and species or species combination should be laid out.
In the takeoff documentation, this would look something like this:
All wall and floor framing shall be (minimum) No.2 S-DRY Douglas Fir. Roof framing shall be pre-manufactured wood trusses.
This level of precision is simply a must.
It ensures that the correct materials are used, ultimately contributing to the highest possible quality of the structure and ensuring a smooth and safe construction process.
To illustrate the significance of this attention to detail, consider a notable case from the ‘70s in New York involving the construction of the Citicorp Center, a massive 59-story skyscraper.
Despite being one of the tallest buildings at the time, it faced a serious issue due to incorrect material choices.
In order for the design to work, load-bearing braces in the form of inverted chevrons were needed.
The braces were fabricated in sections and assembled on-site, requiring five joints in each brace.
The structural designer, William LeMessurier, specified welded joints for this, but the steel subcontractor on the project, Bethlehem Steel, suggested using bolted joints to save money.
Unfortunately, this recommendation was accepted without LeMessurier’s knowledge.
Combined with other wrong choices in the structure design, this compromise made the building highly vulnerable to strong winds, posing a significant risk to the hundreds of people working inside.
Fortunately, timely repairs were made, and no one was injured.
This cautionary example underscores the critical importance of selecting the right materials for a project.
Remember, the lowest price should not be the sole consideration during takeoff.
A good estimator always tries to look at the bigger picture and selects materials that will help ensure the longevity and resilience of the structure.
Equipment Needs
Your takeoff should also comprehensively itemize all heavy equipment, vehicles, and additional machinery essential to meet project deadlines.
After all, having the right equipment is just as important as having the right materials.
So, make sure that, in your takeoff, you consider:
- The type of equipment needed
- Quantity
- Specifications
- Operating costs
- Rental costs
- Storage costs
- Shipping and transportation costs
This detailed overview will empower decision-makers to make informed and cost-effective choices during the equipment procurement phase.
To help you select the best machinery for the job, we’ve curated a list of factors to take into consideration.
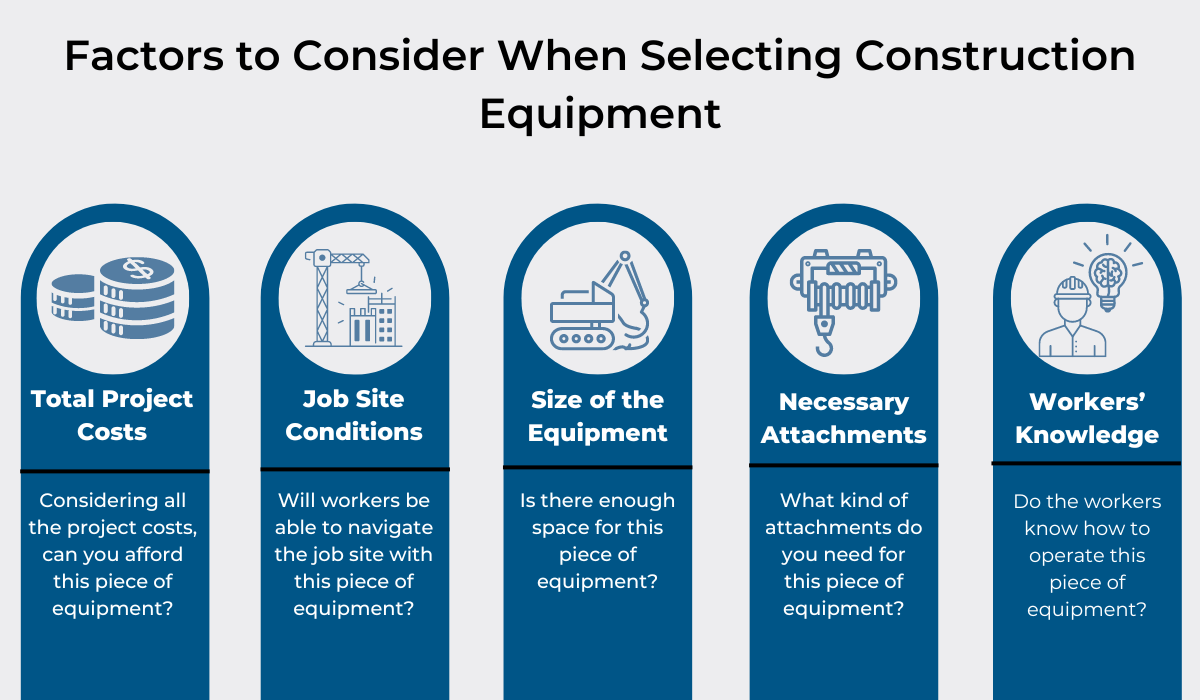
As you can see, acquiring the latest, state-of-the-art machines shouldn’t be your sole focus.
Rather, it’s much better to holistically examine the entire project, and identify potential risks such as limited storage space, a shortage of skilled operators, adverse weather conditions, or uneven terrain.
This analysis will be your guide in finding the most suitable machines for each specific task.
Adam Williams, Executive Vice President of Asset Management at MCG Civil, a company overseeing multiple civil construction projects across North America, provides another valuable piece of advice in this context.
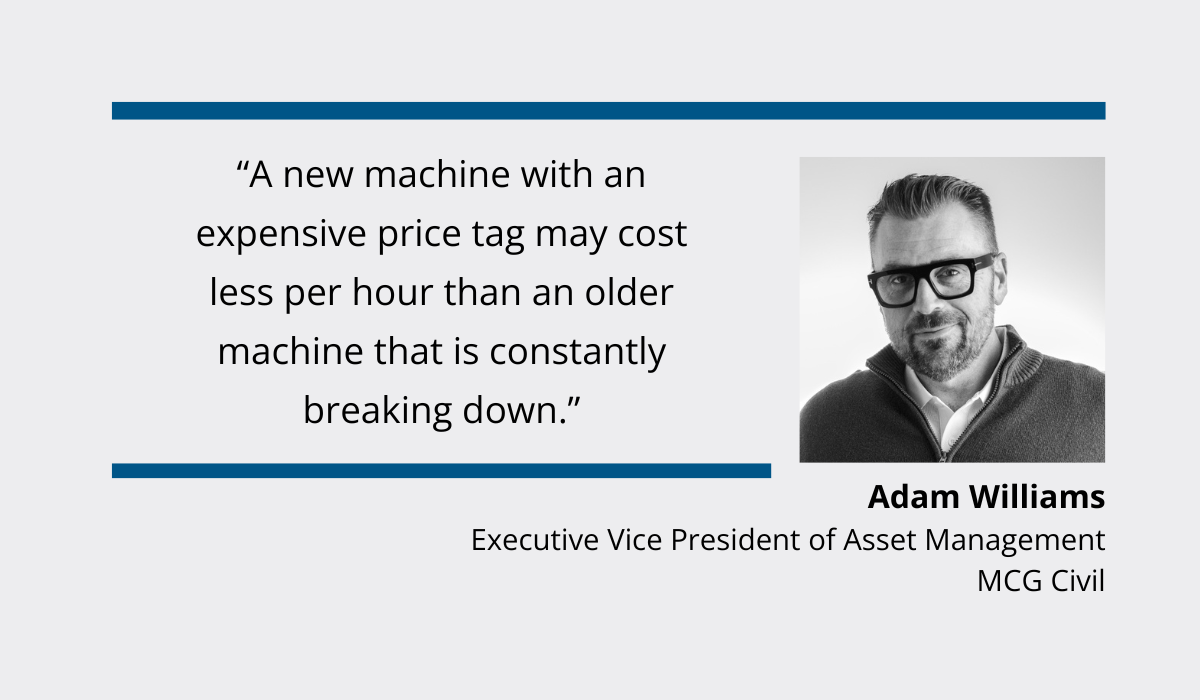
He emphasizes the importance of a strategic mindset, cautioning that a seemingly cheaper option may incur higher long-term costs.
Therefore, be sure to thoroughly evaluate the pros and cons of each piece of equipment before incorporating it into the takeoff.
Overall, integrating equipment requirements into the construction takeoff directly translates to being well-prepared for the challenges the project may encounter.
This means that, with the right combination of machinery, you can maximize productivity, decrease unplanned downtime, and, ultimately, ensure the success of the project.
Labor Requirements
What would all the equipment and materials be without the expertise of skilled workers?
When working on material takeoff, consider all the activities involved in bringing a design to fruition, like, for example, excavation, plumbing, or roofing, and then:
- Determine the required number of workers for each task
- Identify the necessary skills each worker must possess
- Estimate the total working hours for the project
- Define the working hours for each individual worker
- Compile a comprehensive list of payroll-related costs
By anticipating labor requirements for each task beforehand, you enable decision-makers in charge of employee management to strategically optimize workflows, enhancing overall efficiency.
For instance, they may choose to group similar tasks to minimize downtime and shorten the project duration.
Similarly, if there’s a considerable volume of materials and workers to oversee, they may opt for specialized equipment management software like GoCodes Asset Tracking to assign particular equipment and tasks to the workers.
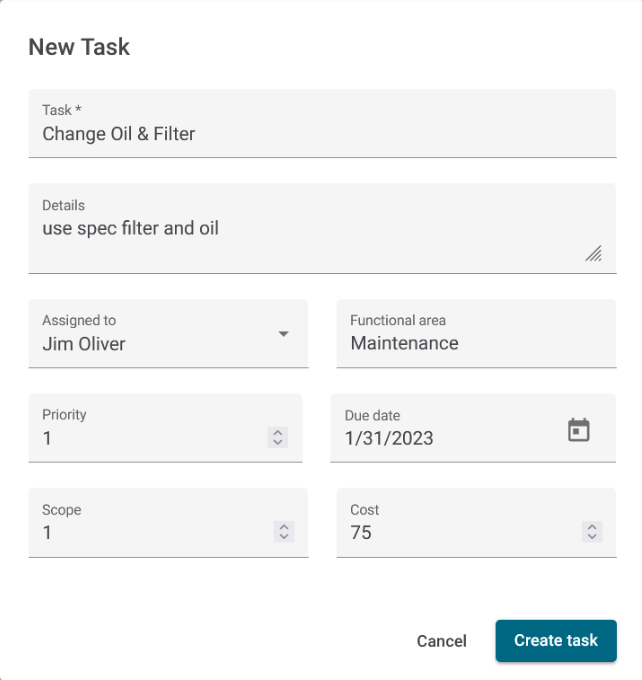
That way, everyone can rest assured that all the equipment, materials as well as workers are always where they are needed the most.
At the end of the day, it’s the skilled team that transforms raw materials into tangible structures, and securing a proficient workforce is undeniably one of the top priorities during MTO.
Therefore, allocate ample time to assess labor needs for the project.
In doing so, you lay the foundation for the recruitment of individuals with the necessary expertise, ensuring that you have a team capable of executing the job with excellence.
Contingency and Waste Factors
Material takeoff is all about considering various what-if scenarios and integrating them into your final estimations.
This includes accounting for potential wastage during construction and establishing contingencies for unforeseen circumstances.
Unfortunately, material waste is a common occurrence in the industry, stemming from several factors, such as:
- Frequent changes in design
- Inadequate material storage
- Weather
- Poor planning
- Ordering errors
- Workers’ mistakes
Experienced quantity surveyors are adept at anticipating such situations and incorporate additional supplies in the takeoff to ensure the team is adequately covered, thus reducing material waste.
For instance, when specifying the amount of piping or lumber, it’s a good idea to include some extra length to accommodate any potential wastage during the construction process.
To assist in this task, Civil Planets provides a useful list of allowable wastage percentages for reference.
Below, you can see the recommended values for some of the materials.
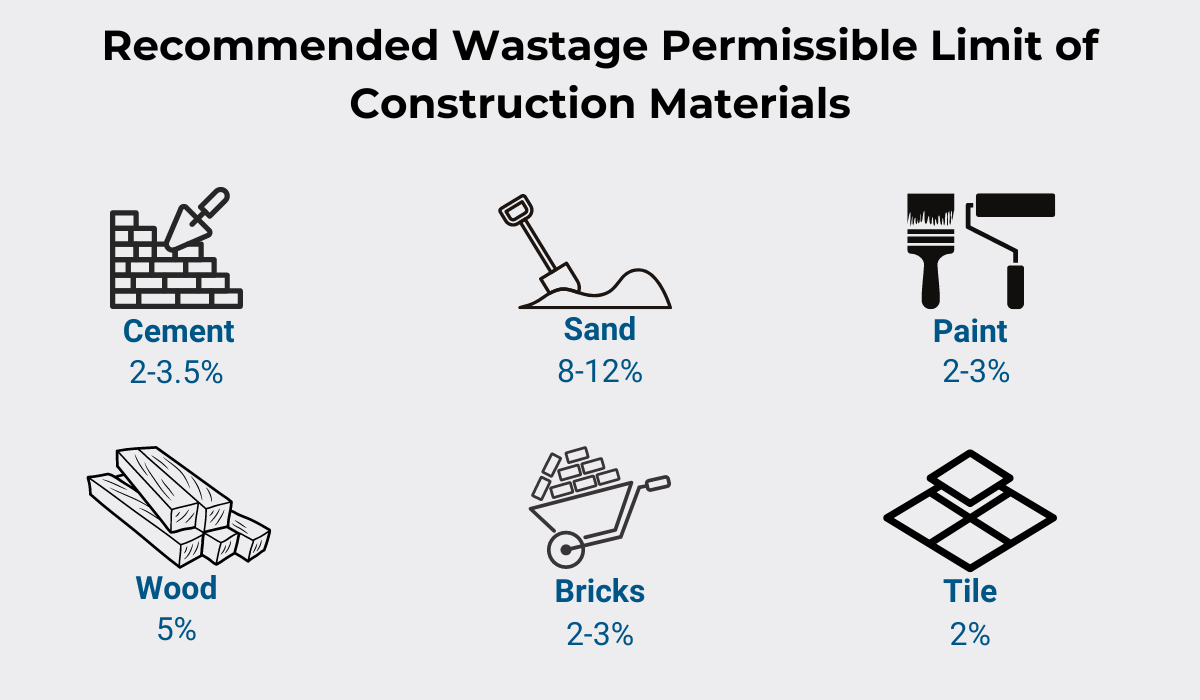
Realistically, complete prevention of wastage is impossible, so integrate it into your plans to avoid unnecessary expenses in the future and mitigate possible work delays.
Another crucial aspect to consider in the takeoff is the contingency fund.
Given the inherent unpredictability of construction work, planning for scenarios like inflation, worker errors, and similar occurrences is vital.
Typically, the safety net budget is set at 5-10% of the total project cost.
However, it’s up to you to assess if this provides enough breathing room to keep costs under control and protect the deadlines.
In conclusion, forward-thinking during the material takeoff is paramount for overcoming unexpected challenges and ensuring the project stays on course.
By addressing material wastage and setting up a contingency budget in the early stages, you guarantee that the entire team navigates the hurdles of construction work with ease and confidence down the line.
Conclusion
Ultimately, a well-executed construction takeoff is far more than just a list of materials.
It serves as an invaluable foundation for decision-making throughout all aspects and stages of construction work, from initiation to completion.
Do this task right, and the projects you’re involved in will be much less prone to experiencing unplanned downtime, material loss, delays, and cost overruns.
Isn’t that the aspiration of every construction professional?
Therefore, be thorough, forward-thinking, and analytical, and watch your future takeoffs become the guiding force for the construction of remarkable structures.