Work orders help your team function better since they serve as detailed explanations of the problems and instructions for a solution.
When it comes to maintenance, work orders are beneficial to the entire team—anyone can see what happened with the asset, who is in charge of fixing it, and by which date.
This is especially true if you use software that centralizes all assignments.
This article will list the benefits of work orders, explain the most common types of maintenance, and advise on better work order management for all those who deal with equipment that they want to service regularly to minimize health and safety risks, downtime, and monetary losses.
In this article...
Benefits of Maintenance Work Orders
Work orders are instructions on what needs to be done and by whom.
When a company feels the need to track tasks and their progress, they use work orders, thus ensuring employee productivity and efficiency.
Because you can assign work orders to an employee, they promote responsibility. The employee receives a task and knows that they must fulfill the work order and report back.
Work orders include the necessary data, instructions, and a deadline, available to view for anyone who accesses the work order, making the company more transparent.
Having the equipment-related data at hand allows technicians to start working on fixing the issue right away instead of spending a lot of time gathering the necessary data.
By introducing work orders into your company’s everyday operations, you’re saving your team time.
On top of that, work orders help you, your employees, or customers report an issue as soon as you notice it, eliminating downtime and prolonging the equipment’s useful life while increasing worker safety.
All of these benefits lead to an unbelievable equipment reliability increase of 35-50%.

It’s important to note that since the customers can report an issue to an employee, who can create a detailed work order based on that information, you will increase customer satisfaction. The customer will feel that you have met their needs since the assignee will know exactly what issue the customer is experiencing and focus on it.
When creating a task, you can assign a certain level of priority to the job, meaning that the employees can see which of the assignments are the most important to tackle.
Thus, you can rest assured that your employees will solve the highest priority tasks ASAP and that nothing will get lost in communication.
What Work Orders Should Include
Every work order needs to include specific information to help the employees understand the issue or request and solve it quickly and efficiently.
Without detailed data on what equipment is experiencing which problem, the maintenance team might have difficulty understanding what they need to do, slowing them down and decreasing productivity.
Information | What it entails |
---|---|
Asset | The piece of equipment which is experiencing an issue or failure |
Description | The explanation of the issue at hand, what happened to the item |
Work Scope | What the assignee has to do to finish the task and which skills they need |
Required Parts and Tools | Explain which spare parts and tools need to be used to finish the task |
Health and Safety Points | Mention any safety procedures or health risks associated with the equipment or maintenance process |
Task Checklist | Insert a checklist if you have one for this specific type of task |
Associated Documents | Attach and name any documentation that might help the employees complete the task |
Assignee | Assign the task to an employee based on their skills, experience, and current workload |
Priority | Determine how important the task is to you and assign priority |
Requester Information | Provide all relevant data, so the employees know who to contact in case they need further clarifications |
Date of Request | Enter the date of the request submission |
Deadline | Define when you need the assignee to finish the task |
Date of Completion | The technician will fill this field once they finish the task |
Expected Work Hours | Give an estimate of how many hours it will take to fix the issue |
Actual Work Hours | The technician will fill this field once they finish the task |
The data above is just the basic information your work orders should include, but you can add any fields that would help your employees with task fulfillment.
They can be industry-specific or company-related.
Whatever you add, make sure that it is helpful and relevant to the task at hand. Otherwise, you’re burdening the employees with unnecessary information, which might slow them down.
For more detailed information on work order details, visit this article.
Common Types of Maintenance Work Orders
Maintenance work orders are tasks related to equipment maintenance, which can be planned or unplanned.
Planned activities include scheduled maintenance performances, i.e., routine checks that your team performs to assure the equipment is safe to use and functioning correctly.
On the other hand, unplanned activities are unexpected issues, breakdowns, and malfunctions that might set your team back. Therefore, the priority of such tasks is higher.
We will now explain the four most common types of maintenance work orders.
Corrective Maintenance Order
Corrective maintenance (CM) refers to the fixing of equipment after a problem arises. This type of servicing causes unexpected downtime and slows your team down as it is a form of unplanned maintenance.
The equipment might not be functioning at all, or it might be slower or less efficient.
The person who notices it creates a work order and requests corrective maintenance, which means that the technician will have to investigate the cause of the issue and fix it, if possible.
When the technician cannot fix the equipment, they might need to replace certain parts for it to run smoothly again. However, there are times when there is no way to fix the item, and a total replacement is needed.
If CM isn’t obligatory, i.e., you can still use the asset, you’re dealing with scheduled corrective maintenance.
The opposite, unscheduled servicing, happens when it’s not possible or safe to use the equipment for its intended purpose and an immediate fix is required.
Such tasks are usually high-priority and expensive as they are unplanned and most likely to happen when someone is using the equipment, meaning that they have to stop performing their tasks to report the issue.
CM is costly and causes project downtime and safety issues.
However, it can be helpful in certain situations when the equipment at hand isn’t as valuable, or when it costs less to get a new asset than to invest in other types of maintenance for that asset.
Condition-Based Maintenance Order
Condition-based maintenance (CbM) is a proactive type of maintenance, as opposed to the reactive types such as CM.
Instead of waiting for an issue to occur, companies that use CbM inspect the assets for signs of problems or use sensors that point to low performance or condition levels of specific equipment.
The sensors constantly monitor the equipment, aware of the normal levels.
As soon as a parameter reaches a critical level, the sensors alert you of the problem. You can then create a CbM work order and request an employee to further check and fix the issue.
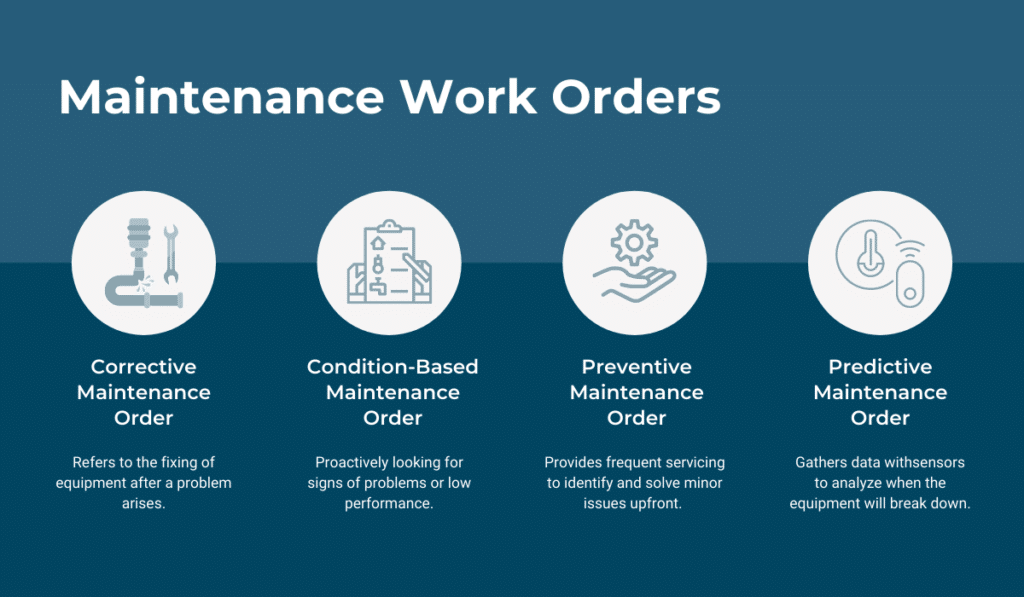
Once the levels reach the lowest point assigned, the asset needs maintenance. The team can fix the problems and get the condition to normal and performance levels back to satisfactory.
CbM is an excellent solution for those who don’t want to wait until an asset malfunctions to fix it, but also don’t want to waste a fortune on frequent maintenance.
Such servicing represents the middle-ground between the two options: one high-risk, the other expensive.
This type of servicing includes expensive sensors and well-trained professionals who know how to read the sensor information to fix the issues.
Another disadvantage is the inability to predict when the sensors will point to the low values, which can happen for many assets simultaneously and burden the maintenance team.
Preventive Maintenance Order
Though similar to CbM, preventive maintenance (PM) uses the current state to fix the issue and forecast future maintenance needs.
It lets you perform regular, scheduled checks on your equipment, preventing breakdowns and emergency repairs, thus reducing costs.
While CbM focuses on the current condition of the item, PM considers its future state and provides frequent servicing to identify more minor issues and solve them before they become more prominent.
This prevents breakdowns, downtime, or pose a threat to worker safety.
To implement this type of servicing, you need to have a maintenance schedule for each piece of equipment that will use it.
You can use the manufacturer’s recommendations or develop company guidelines after inspecting the equipment and consulting with the specialists.
The most important part is sticking to the said weekly, monthly, or yearly schedule.
If you think it would be impossible for your team to write down maintenance dates for each item, try using software that lets you scan the item, select the next service date, and reminds you of maintenance dates.
By choosing this option, you’re saving your employees time and reducing the risk of human error and maintenance documentation loss while ensuring that the equipment gets serviced on time.
PM prevents downtime and costly emergency repairs, but it requires more frequent servicing and more technicians to inspect equipment regularly.
Predictive Maintenance Order
Predictive maintenance (PdM) is a type of servicing that uses current data gathered through sensors and the asset’s history to analyze when the equipment will break down.
A specialized PdM software collects this data, communicates it, and then uses algorithms to predict when the asset will fail.
PdM helps you minimize downtime by investing in equipment before it breaks down while saving you money on frequent, regular checks.
A benefit of PdM is that it uses the best features of other maintenance methods.
PdM and CbM both use maintenance to prevent breakdowns and minimize downtime.
While CbM relies on the sensors to predict when the equipment will fail, PdM uses accurate formulas to determine the same.
In other words, CbM focuses on the present state of the asset while PdM takes the future condition into account.
However, while accurately predicting asset failure and practically eliminating downtime, PdM is expensive to implement.
You need to invest in sensors and management software that can capture and communicate asset data to make a prediction.
On top of that, you need to train your team to interpret the PdM software reports correctly.
However, despite the higher amount of money you will spend on implementation, PdM more than returns its investment, as it saves you a lot more in the long run.
What to Keep in Mind When Managing Maintenance Work Orders
No matter which type of maintenance you choose for which set of equipment, you need to use work orders if you want to address all problems promptly and avoid unnecessary downtime.
When implementing work orders, you should consider the following advice to ensure that you’re making the most of them.
Ensure Everyone Uses Work Orders
Though it might sound redundant, this step is almost always necessary if you want everyone to be on the same page and be aware of how and why they’re using work orders.
Of course, your workers will use work orders for more complicated tasks or more extensive problems, but they might be tempted to skip a step or two or even decide against using a work order at all when it comes to more minor issues.
They might think it takes less time to fix a problem than it does for them to fill out the form and the maintenance team to read it.
However, you shouldn’t encourage this behavior.
On the contrary, you should make it obligatory for each task, no matter how minuscule, to be written down as a work order as this will get your workers in the habit of using them.
At the same time, such a practice also familiarizes them with all the necessary information and the work order process in general.
Train Maintenance Operators
Your maintenance team understands how to spot issues and fix them, but you should also train them on work orders.
Other employees can handle some of the tasks.
Still, your maintenance team will have to work on most work orders, which is why they need to be familiar with the work order form and all the information that they will receive from the request, including the deadline and a possible checklist, if applicable.
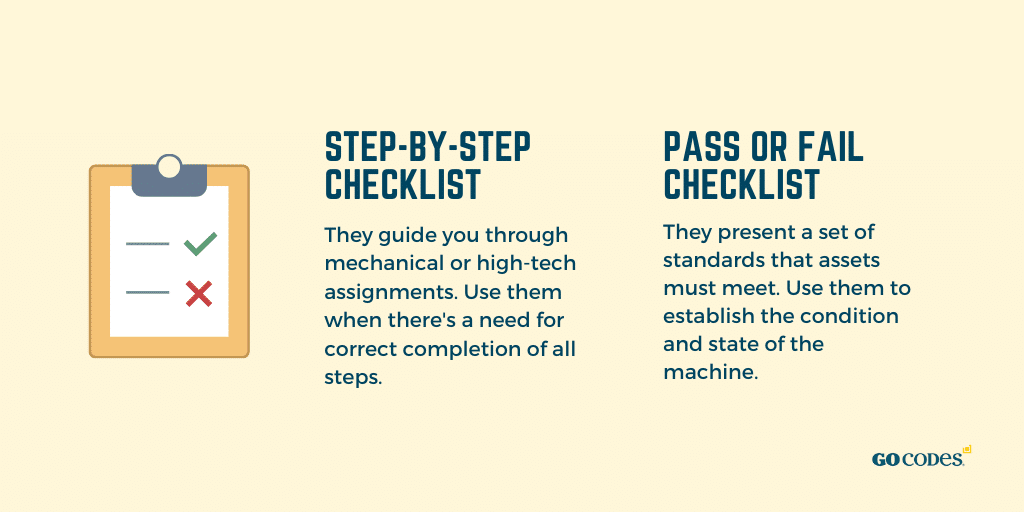
Trained operators will understand when there is an issue with a work order or when it doesn’t contain enough or correct information.
Instead of proceeding despite a faulty work order, they will contact the requester and go through the work order with them to try to understand the main points and the underlying issue.
This insight will save them time and energy.
Assign Every Work Order
An essential aspect of work orders is the assignee. Filling this field lets your employees know who handles the work order and which steps to take.
Assigning tasks to specific employees promotes employee responsibility and productivity, which benefits your company and the whole maintenance process.
If you don’t name an assignee but let the team choose the person to complete the task, some might avoid having this kind of responsibility, while others may constantly volunteer even if they are not the best choice for a specific job.
When choosing the assignee, consider the difficulty of the task and the necessary knowledge to handle it.
Also, you need to take employee workload into account to ensure the assignee can finish the task within the deadline.
The most important aspect is selecting the correct person for the job, as someone who is not an expert on the asset might take a lot more time or make the problem even worse.
Share Asset Information With the Maintenance Team
If you want your maintenance team to do their job quickly and efficiently, provide them with enough information on the problem in the work order.
When training your team to create work orders, stress the importance of details about the equipment.
On top of a detailed explanation of the issue, your team should have the option of checking the previous maintenance and repairs reports, warranties, and manuals.
This helps them understand the asset better.
Instead of wasting time figuring out what caused the problem, your maintenance staff can go through the maintenance history and see if they can notice a pattern.
They will notice whether a part needs to be replaced or fixed or if an issue keeps repeating.
This insight will allow the servicing team to leave comments in the work order, warning about the issue and suggesting a solution, for instance the replacement of a part or an entire asset.
Know How to Prioritize the Work Orders
Assigning priority to the work orders allows your team to organize their workload in a way that can help them finish the crucial assignments first.
Without prioritization, your team handles work assignments in the order they arrive without paying attention to what is urgent.
Each task is of the same value to them.
However, not all tasks are equally important to the company, as some might be more costly than others.
Of course, there’s a different level of prioritization between scheduled maintenance tasks and emergency repairs.
The latter are more costly since emergency repairs are critical and require immediate attention while also causing downtime and possible project or production delays.
Such tasks should always be prioritized, which won’t be possible if you don’t include the priority field in your work orders and fill it out each time.
Your team should prioritize tasks that threaten worker health and safety or cause downtime, while other regular maintenance tasks shouldn’t be as high on the priority list.
Automate the Process
Work orders can be done by hand, using pen and paper, but this system is outdated, slow, and less efficient due to the high risk of human error or documentation loss or damage.
On top of that, it’s difficult to have insight into the asset’s maintenance and repair history if it’s all done on paper.
It would take your team hours to locate and go through all the documentation necessary to understand the asset’s history and even more to write down the new information and the steps they’ve taken.
However, they can have all this information in a couple of clicks if you opt for software that allows you to manage work orders, attach any necessary files, and have an overview of the maintenance and asset-related comments.
Choosing to use software for work order management leads to a 28% increase in maintenance productivity.
The workers could focus more on the maintenance itself and less on gathering all the necessary papers and data and manually writing down all the steps and changes.
Conclusion
Since work orders help you minimize costly downtime, avoid unnecessary costs, and decrease health and safety risks, it would be beneficial for your company to implement them.
You can use software to have all the information you need to fix the asset in one place, regardless of what servicing type you use.
Your maintenance team will be able to follow up on work orders quickly and be as efficient as possible while ensuring that your equipment is functional and safe to use.
If you switch to work orders, adequately train your team on using them and stress the importance of using them for every assignment. The fact that you can add priority to work orders will help things run smoothly and get done quickly when urgent.