Key Takeaways:
- Effective equipment management is crucial for landscaping businesses to reduce downtime.
- Using tools like QR codes, GPS trackers, and software systems simplifies equipment tracking.
- Proactive maintenance and detailed equipment records maximize tool lifespan.
Ever found yourself looking for a specific piece of equipment, only to discover it’s missing, due for maintenance, or at another job site?
Effective management is absolutely essential if you want to keep your landscaping equipment fully functional and well-utilized in your operations.
But that’s easier said than done, especially if you’re running a multi-site operation.
Juggling equipment across different locations, keeping track of maintenance schedules, and ensuring operator competency can quickly become a logistical nightmare.
But don’t worry, we’re here to help.
In this article, we’ll discuss some key challenges in managing landscaping equipment, offer practical solutions, and provide actionable tips to help you get started.
In this article...
Why Equipment Management Matters for Landscaping Businesses
When it comes to landscaping operations, managing your equipment is an inevitable task.
But the real question is whether you’re doing so effectively or just getting by.
This is a crucial question to consider, especially in an industry like landscaping.
After all, as highlighted in this LMC Houston article, labor shortages are a significant challenge for this sector.
This makes having the right equipment that much more important.
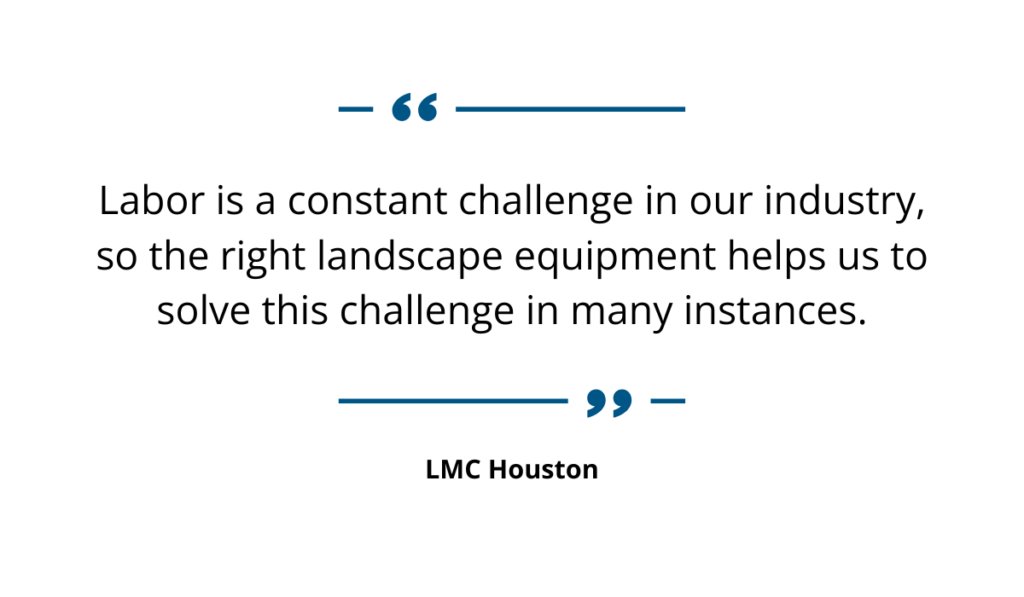
Illustration: GoCodes / Quote: LMC Houston
And while the article points out that, with the right tools, the same landscaping job can often be accomplished with fewer crew members, this increased efficiency is only achievable when your equipment is properly managed.
In fact, without a robust management system in place, you simply can’t allocate your resources optimally.
This means that you risk introducing unnecessary downtime or having to deploy additional personnel to a site to finish a job.
Both of these are bound to negatively impact your profitability.
Also, equipment management involves good maintenance practices for preventing costly breakdowns and extending the lifespan of your valuable tools.
For example, EquipmentShare, a construction equipment and tool rental, recommends maintaining a 70/30 ratio for all your equipment.
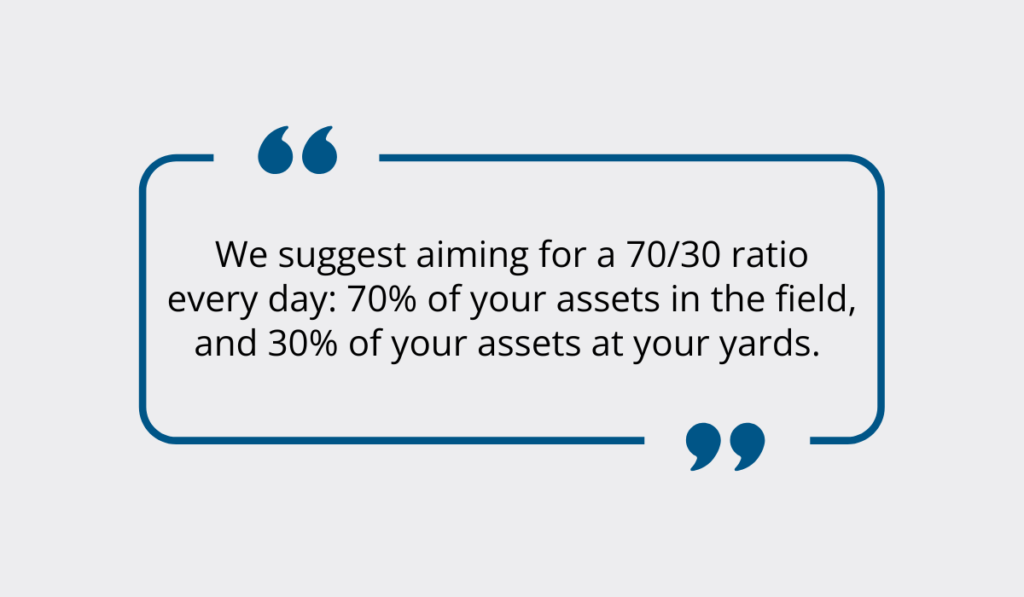
Illustration: GoCodes / Quote: EquipmentShare
This ratio suggests having 70% of your equipment actively deployed on projects while keeping 30% available for routine servicing and unexpected repairs.
Of course, this approach requires efficient equipment management.
This includes organized maintenance schedules, accurate tracking of equipment location, and much more.
Otherwise, you risk deploying tools due for checkups or fixes.
Ultimately, with proper management, you enhance your overall operational efficiency and save money in the long run.
Key Challenges in Managing Landscaping Equipment
While the benefits of proper equipment management are clear, that doesn’t mean there aren’t challenges that can slow down the process.
Landscaping involves a lot of equipment, and one key challenge is efficiently tracking it all.
Now, while this tracking issue is most pronounced in large operations, it’s present even if you’re running a small landscaping business.
In fact, even with just a few crews to manage, you might find yourself asking the same question as this Reddit user shown below.
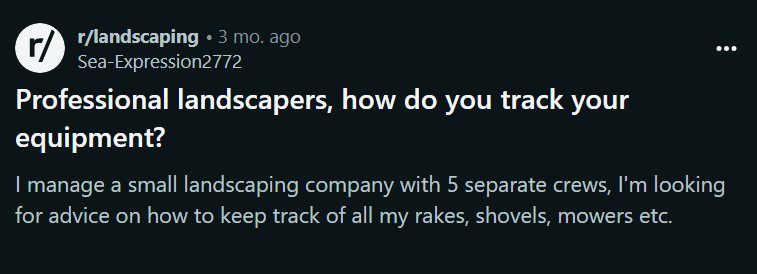
Source: Reddit
Tracking smaller landscaping equipment like grass cutters, leaf blowers, and hedge trimmers is especially problematic.
These tools are easily misplaced on a site or completely lost, particularly during larger projects.
Managing larger machinery presents a different challenge, often centered around ensuring optimal utilization.
Unfortunately, inefficient tracking across job sites makes it difficult to know which machines are available and where they’re located, leading to potential delays and underutilization.
Not to mention, ineffective tracking of both small and heavy equipment can lead to poor theft prevention practices.
As an example, take a look at this CBS12 report of a theft in the value of over $160,000 in landscaping gear.
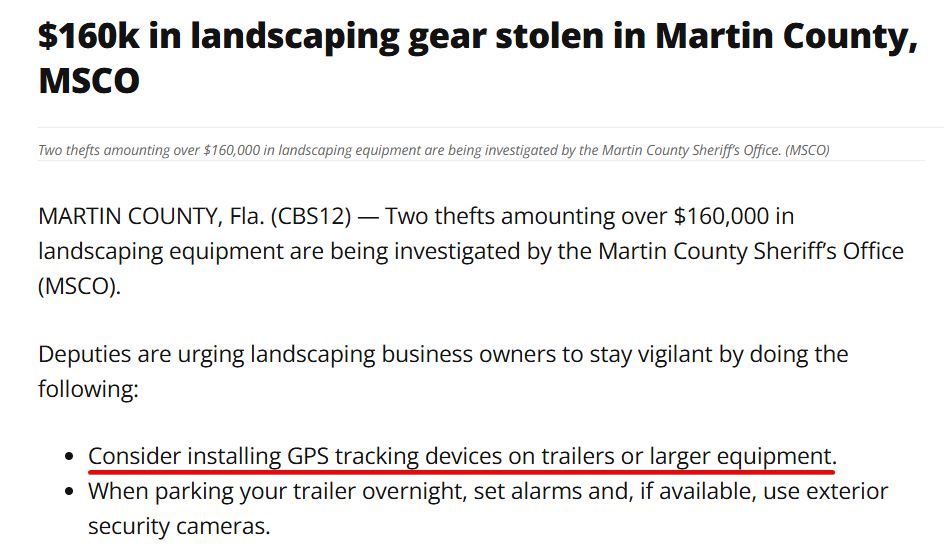
Source: CBS12
As highlighted above, law enforcement recommends installing tracking devices, such as GPS trackers, on whole equipment trailers or individual heavy equipment to help prevent large-scale thefts.
In short, from misplaced hand tools to underutilized machinery and the risk of theft, managing your landscaping equipment presents a significant challenge that you need to overcome.
Different Solutions for Effective Equipment Management
Fortunately, all of these challenges have their solutions.
From implementing smart management practices to utilizing the right tools and systems, there are several ways to improve your equipment management.
Let’s cover four of the main practices you can follow in your own landscaping operations.
Attaching Physical Trackers
A fundamental practice for effective equipment management is using trackers.
Attaching physical trackers to all of your assets is a tangible way to identify and locate your equipment.
This is going to streamline the tracking and maintenance of your machinery, as well as theft prevention.
But the effectiveness of this solution depends on selecting the right trackers to suit your specific needs and use cases.
In fact, there’s a wide variety of trackers to choose from.
They can range from simple tracking stickers to more advanced options.
To make the comparison easier, we’ve compiled some key options in the table below.
Feature | QR Tags | GPS Trackers | Bluetooth Beacon Tracking | RFID/NFC Tags |
Cost | Low setup cost; durable, customizable tags available. | High initial cost; ongoing fees for data plans. | Moderate setup cost; additional fees for advanced features like alerts. | Low for NFC; moderate for RFID with advanced readers. |
Durability | Rugged, weatherproof QR tags withstand dirt, sun, and moisture. | GPS devices are durable but require maintenance in rugged outdoor conditions. | Compact and durable, suitable for outdoor and indoor environments. | NFC/RFID tags can be weatherproof and embedded for heavy-use equipment. |
Range | Requires visible access to the QR tag. | Tracks globally. | Limited to ~100 meters. | 4 cm for NFC, up to 10 meters for RFID. |
Use Case | Small tools, hand equipment, or inventory storage areas. | High-value machinery (e.g., mowers, excavators), vehicles, or remote job sites. | Tools frequently moved on-site, like hedge trimmers or portable generators. | Tool sheds, storage facilities, or high-turnover small tools. |
Ease of Use | Simple to scan; quick tagging for inventory management. | Requires initial setup and training for advanced features. | Easy to use; auto-detection simplifies finding misplaced tools. | Simple and fast, especially for check-in/out or tracking multiple assets. |
As you can see, all of these trackers have their merits.
For simpler options in daily operations, you can opt for QR code tags, or NFC/RFID tags for additional functionality and more data storage on the tag itself.
Even more advanced options, like Bluetooth beacons, are straightforward to implement and quite durable, as shown in the image below.
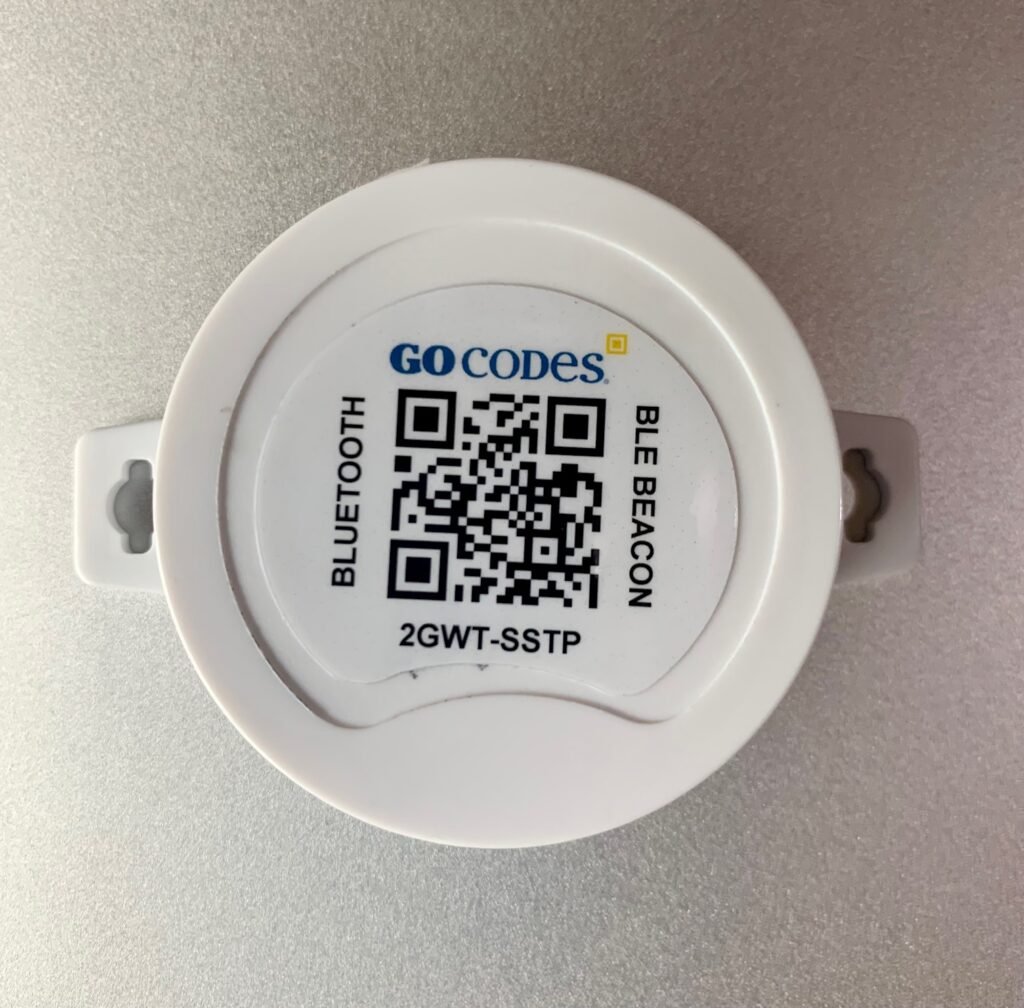
Source: GoCodes
These beacons are particularly helpful in landscaping.
Namely, they can pinpoint the location of equipment within a specific job site, even if it’s buried under a pile of mulch or stored in a shed.
Finally, if you’re running an operation with remote job sites, nothing beats the tracking capabilities of GPS:
It enables you to monitor equipment location in real time, regardless of where it is.
So, from simple to sophisticated, a range of physical trackers can significantly improve your landscaping equipment management.
Using Software Tools
The trackers presented in the previous section often go hand in hand with tracking systems and devices to help you scan and manage your tools.
And while minimal systems can be helpful on their own, using feature-rich equipment management software can bring additional benefits your business.
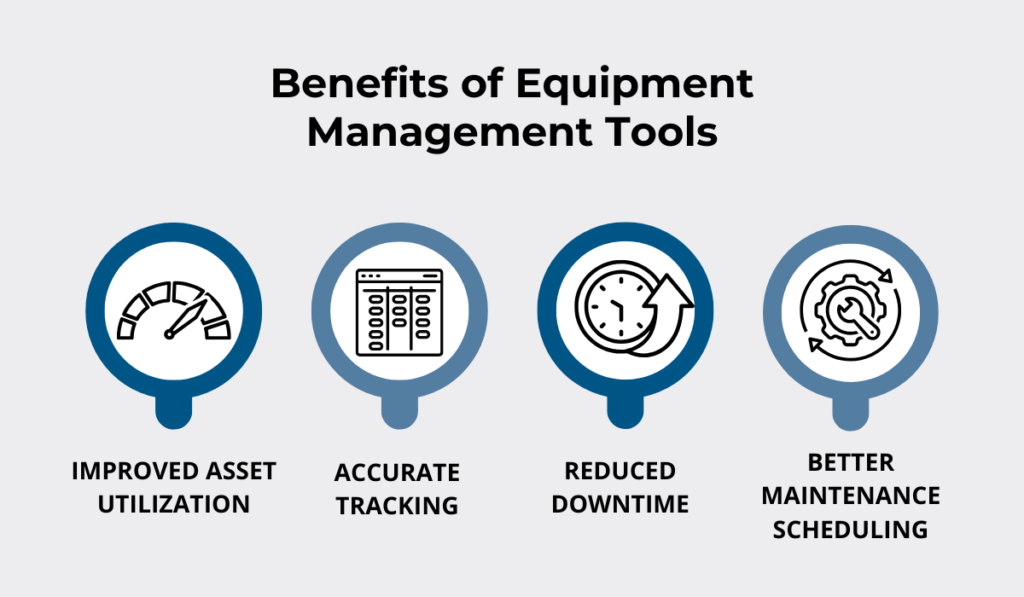
Source: GoCodes
With real time tracking facilitated by these tools, you can quickly locate available equipment, minimizing downtime and ensuring that resources are used effectively.
On top of that, software tools facilitate proactive maintenance scheduling.
They track usage hours and send reminders for upcoming service, thus preventing breakdowns and unwanted equipment downtime.
But which software tool should you choose?
Of course, there many landscaping-specific systems on the market, such as:
- Workyard
- Yardbook
- Housecall Pro
- SortScape
However, you should also consider using the powerful features of general equipment management systems like GoCodes.
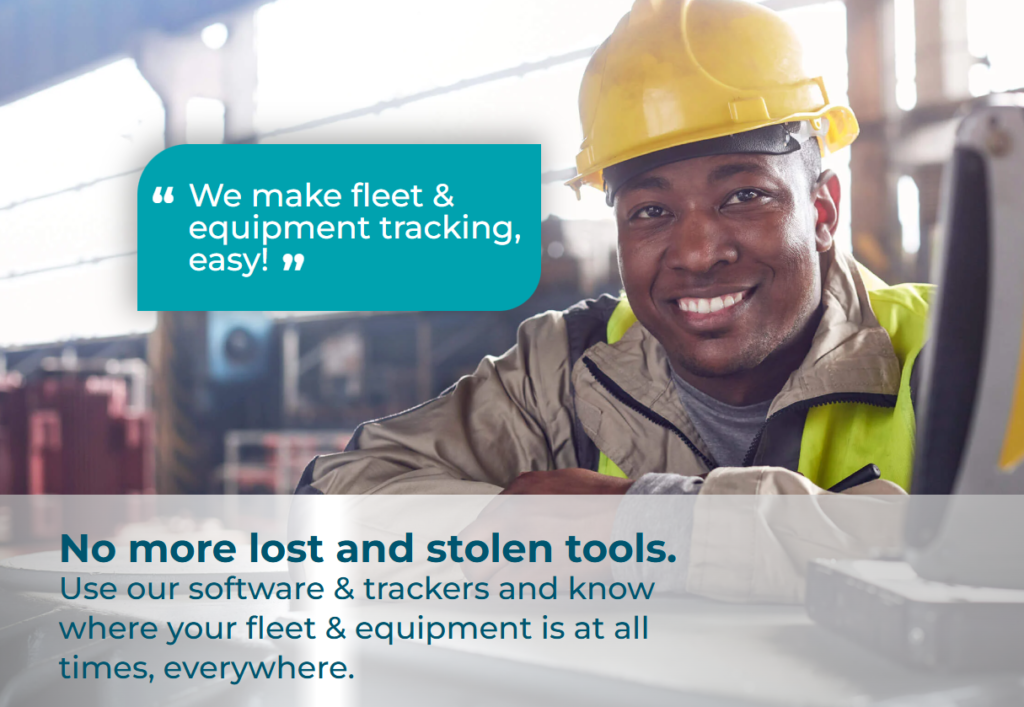
Source: GoCodes
GoCodes can benefit landscaping businesses by helping you easily track all of your assets, from small tools to larger equipment.
We offer all physical tracker options, including QR, NFC, and RFID tags, along with GPS trackers and Bluetooth beacons.
These are bound to cover all your tracking needs.
These tags are available in various durable materials, which will ensure they withstand the demanding conditions of landscaping work.
And, when one of our tags is scanned, you instantly get access to detailed information on the asset it’s attached to.
This includes the asset’s location—automatically updated and displayed on a map, as shown below.
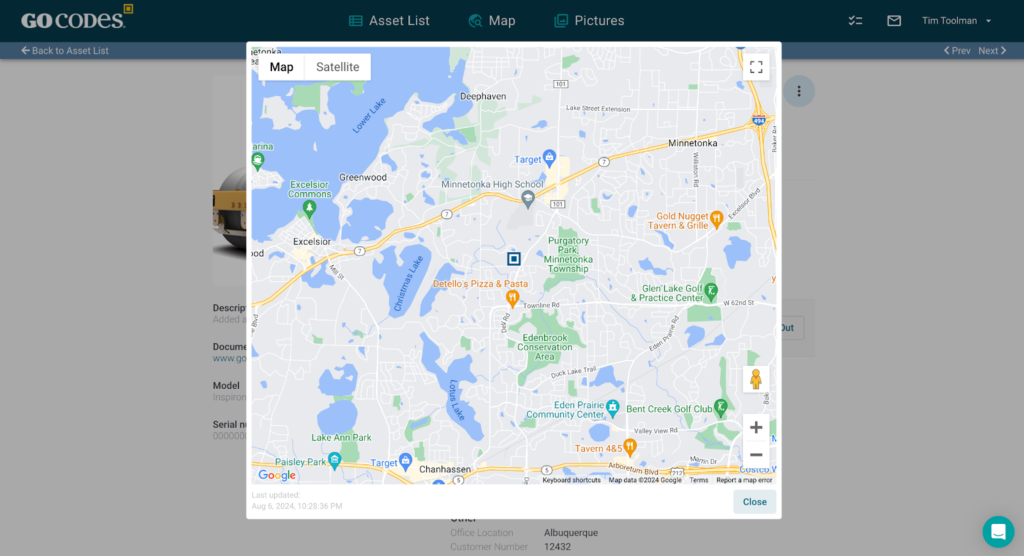
Source: GoCodes
This feature helps you effortlessly track landscaping tools, even in multi-site operations.
Aside from this, a tool like this can help you organize maintenance schedules, usage logs, and other crucial information—all in one centralized location.
In short, implementing software provides numerous advantages, so trying out these systems is a great practice to build a robust equipment management process.
Better Maintenance Strategies
We’ve touched on maintenance throughout this article, and for good reason.
Building strong maintenance strategies is an essential part of equipment management.
And research shows that being proactive about it is key.
Namely, a 2021 survey on the importance of maintenance techniques found that predictive and preventive maintenance brought the most benefits.
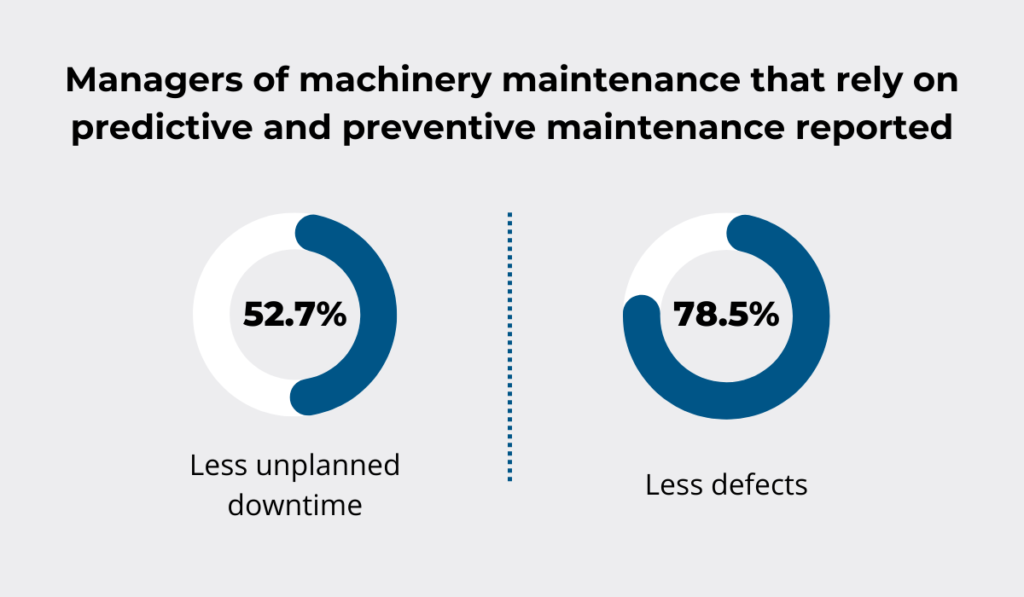
Illustration: GoCodes / Data: PHMSociety
Predictive and preventive maintenance involve proactively addressing potential issues before they escalate into major problems.
This includes:
- regular inspections,
- scheduled servicing, and
- using data analysis to predict potential failures and take preemptive action.
One aspect of building such a maintenance strategy involves setting regularly scheduled maintenance checks at consistent intervals.
For example, here’s what a maintenance schedule for a mower might look like.
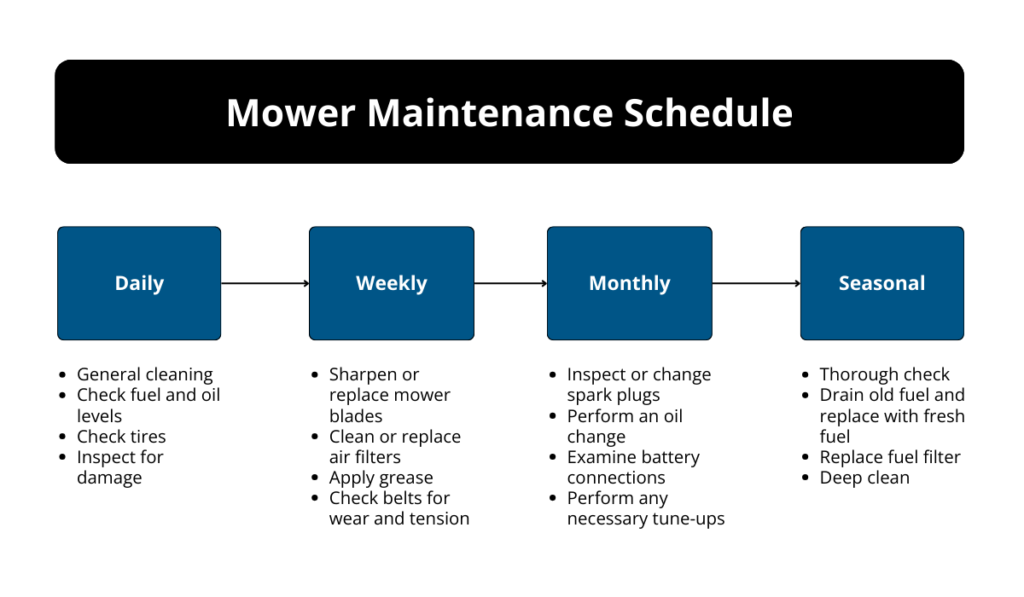
Source: GoCodes
Sounds like a lot to manage?
Yes—if you’re going to do it all manually.
That is why, more often than not, some maintenance checks are overlooked or postponed until a defect arises, leading to more extensive and costly repairs.
That’s why using digital tools to streamline this process is crucial.
Digital tools can automate maintenance reminders and track completed service, ensuring that nothing falls through the cracks.
They can also provide valuable data on equipment usage and performance, helping you identify potential problems early on.
Overall, implementing proactive maintenance strategies, supported by digital tools, is essential for maximizing the lifespan of your landscaping equipment.
Keeping Detailed Equipment Records
Finally, a closely related practice is keeping detailed records of all of your equipment.
This means maintaining documentation for every aspect of your equipment lifecycle, including:
- purchase date and cost,
- warranty information,
- maintenance history,
- usage logs,
- repair records,
- depreciation schedules, and more.
One of the most important records to keep is the maintenance history of each piece of equipment.
This is essential for tracking maintenance costs, identifying recurring problems, and ensuring that equipment is serviced according to the manufacturer’s recommendations.
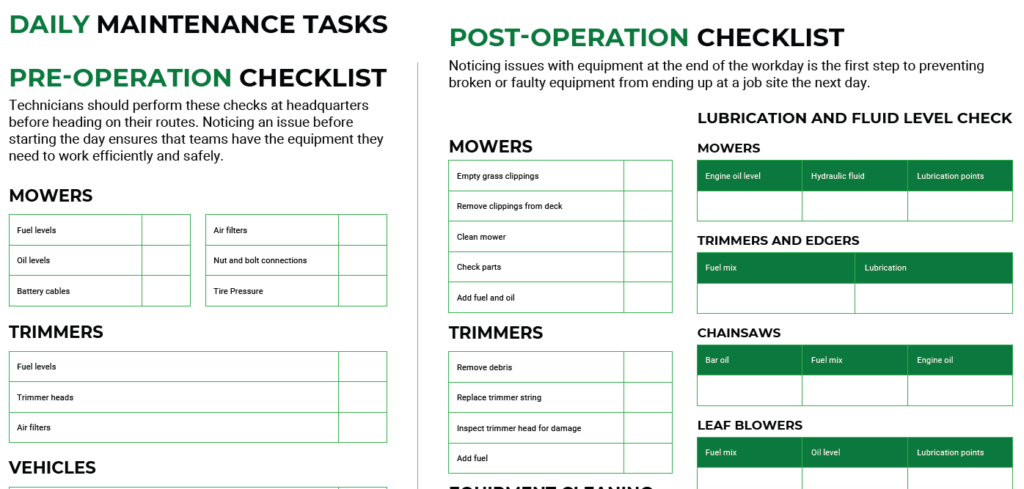
Source: Aspire
This information can be invaluable when diagnosing issues and making repair decisions.
However, these records can pile up—especially if you’re managing everything on paper.
A more efficient approach is to store all this information and these records digitally.
For example, take a look at how some crucial equipment information is stored when using GoCodes.
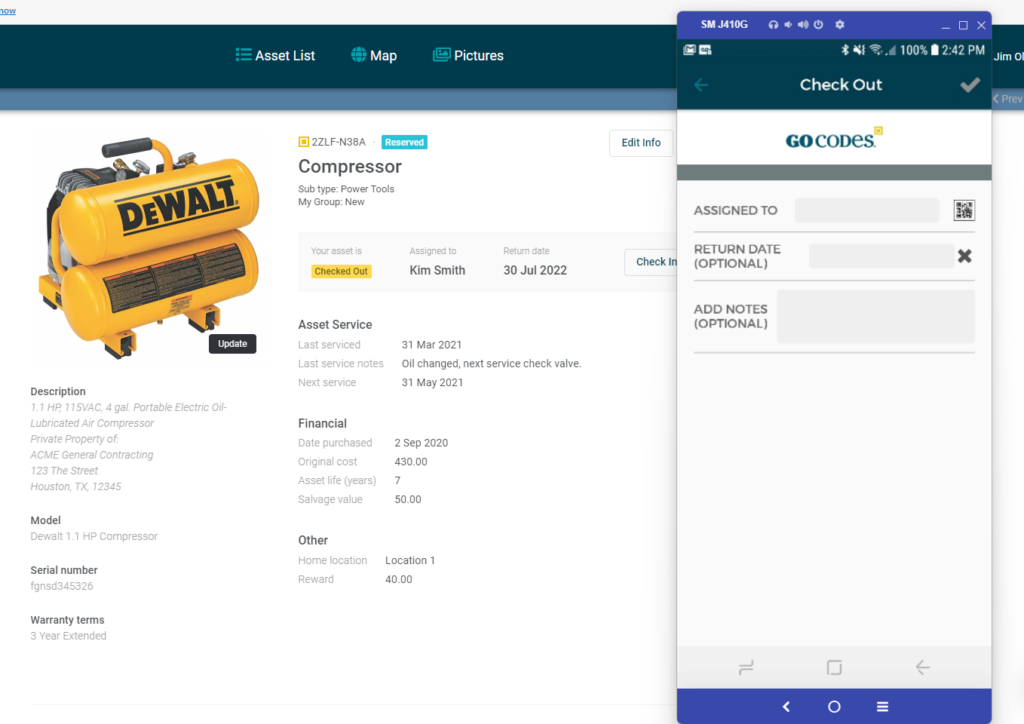
Source: GoCodes
As you can see, this compressor has a detailed description, model and serial number, along with warranty information.
There’s also maintenance information, including the last service date and service notes, along with financial details.
With GoCodes, you can also track asset check-in/check-out details, including who it’s been assigned to and what the expected return date is.
All of this streamlines equipment management, improves accuracy, and makes it easier to access critical information when needed.
In summary, maintaining detailed equipment records—especially when digitized—is a cornerstone of effective equipment management.
Tips to Start Managing Landscaping Equipment Efficiently
Finally, let’s go over some tips to help you get started with efficient landscaping equipment management.
First, conduct a complete equipment audit.
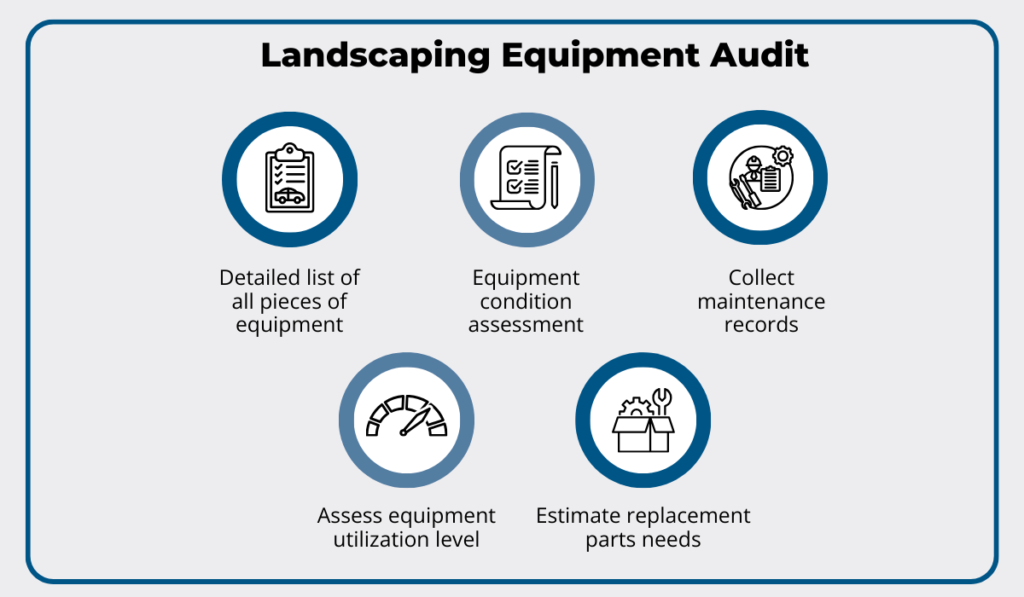
Source: GoCodes
Even starting with a simple list of all your equipment can be incredibly helpful.
You can use this list to plan which trackers to implement on different pieces of equipment, ensuring that nothing, no matter how small, gets left behind.
Plus, you can estimate and monitor the utilization of each tool.
This can help you determine if you need more careful planning for certain tools, or even if you should invest in additional units to manage the workload more effectively.
Next, since you’ll likely use technology in your management process, ensuring that your staff is well-versed in using these tools is essential.
As Phil Harwood, senior business advisor, explains, any new process or technology can be disruptive to operations.
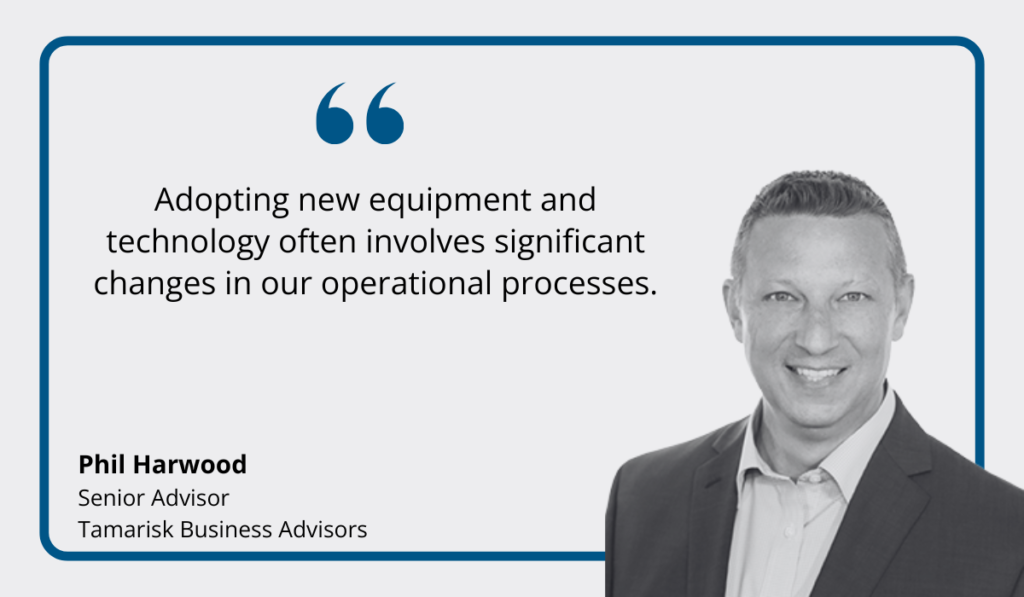
Illustration: GoCodes / Quote: Landscape Management
He goes on to emphasize the importance of strategic implementation, thoughtful planning, good communication, and accountability to make changes more seamless.
This includes proper training for any tracking or equipment management software you implement, as well as adjustments to daily processes.
For example, one main activity you may want to stress is equipment check-in and check-out.
This practice is crucial for any tracking system to function properly, as it provides data on equipment location and usage.
Without consistent adherence to these processes, and the proper training for using any implemented systems, data in your software will be unreliable, hindering your ability to manage your equipment effectively.
Conclusion
While landscaping equipment management certainly poses unique challenges, hopefully, this article has shed some light on tackling them effectively.
We’ve covered the core benefits of equipment management, explored some of the key challenges you might encounter, and provided a few practical tips to streamline your processes.
Plus, we showed how embracing technology can be a game-changer for many aspects of your equipment management operations.
By implementing some of the practices and software solutions we explored, you can be well on your way to making this process as effortless as possible, ensuring your equipment is always ready to go when and where you need it.
Explore tools like GoCodes to streamline your equipment management today!