Industrial equipment labels are very diverse and serve a variety of purposes.
So, when choosing the right one, it might be hard to make a decision with so many options and factors to consider.
We’ll take you through the process of how to choose proper industrial labels for your equipment right now.
In this article...
Define Your Requirements First
The first thing is to define what your requirements are. In other words, what labels do you want on your equipment, and what labels need to be there.
Making informed decisions in these matters can save you a lot of trouble down the road and confirm that your business and equipment can be trusted.
Let’s start with the types.
Generally speaking, some labels identify a particular piece of equipment, meaning they provide information such as the manufacturer’s name, serial number, date of manufacture, relevant regulatory approvals, and other prescribed data.
They usually come in the form of permanent markings, also known as compliance tags, data plates, nameplates, or rating plates.
Here are some examples.
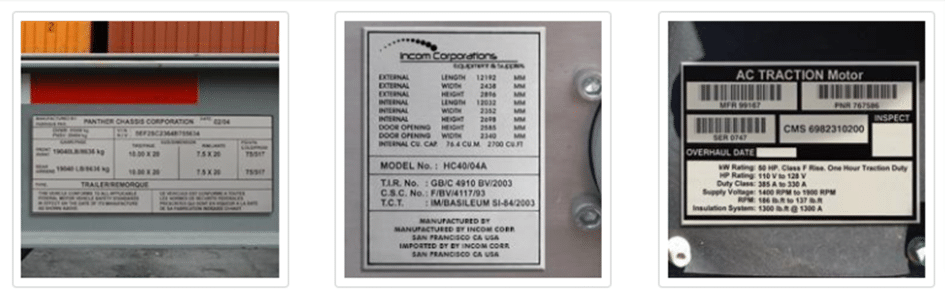
Notice that the last nameplate has three barcodes on it. Compliance tags often convey data in a scanner-readable format, which lends itself to asset tracking.
So, when considering your requirements, scannable codes should have their place on one or more labels.
We shouldn’t forget safety and instructional labels, either. While some are optional, others, like the ones shown below, are mandatory.
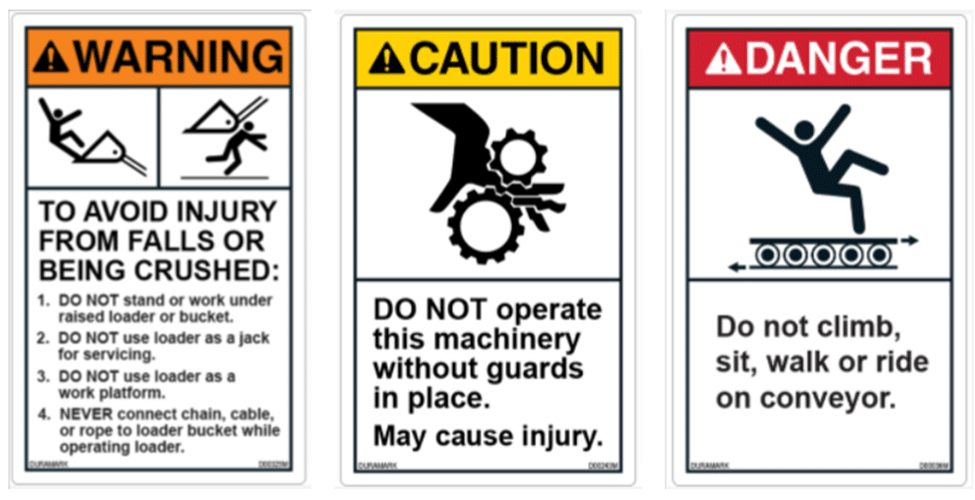
The first one must be on backhoes and excavators, and the second on any equipment with guards, including conveyors. The latter should also have labels like the third one shown above.
So, a piece of equipment will probably have multiple labels on it. This depends on its type, use, industry-specific labeling standards and safety regulations, as well as your asset management and branding preferences.
The next critical thing to consider is the environment in which the equipment will be located.
- Will it be used indoors, outdoors, or both?
- Will it be exposed to fluctuating temperatures or direct sunlight?
- Is it going to be stored inside or outside?
- What’s the desired durability of each label type?
And so on.
The answers to these questions will inform your decisions on what kind of industrial equipment labels best suit your needs, what materials are the most applicable for the purpose and what information should be displayed.
Defining your labeling requirements first can save you both time and money.
For example, choosing the right durability of labels will save you the costs and hassle of frequently replacing them. However, more durable labels may cost more, which leads us to our next section.
Do the Budgeting Now
Knowing your labeling budget is always a plus, especially if you’re working with, for example, a large fleet of heavy machinery for rent.
Learning about different factors that affect the price of labels can lead to better choices for your business.
The label material often has the biggest impact on the price, and the choice of material will, as we’ve mentioned earlier, largely depend on the environment in which the label will be used.
As we’re talking about industrial labels, the most affordable paper labels are seldom the right choice.
But polyester (or PET) labels, like the one below, might suffice in some less demanding applications.
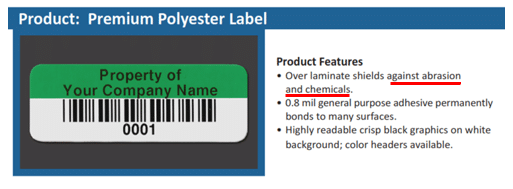
This durable label is resistant to standard cleaning agents, mild acids, oil, and water and has an expected outdoor life of up to two years. However, it’s unfit for many situations industrial equipment can face.
On the other side of that spectrum, there are the exceptionally resilient anodized aluminum labels.
The ones shown below were proclaimed the most durable by the National Association of Graphic and Product Identification Manufacturers (GPI).
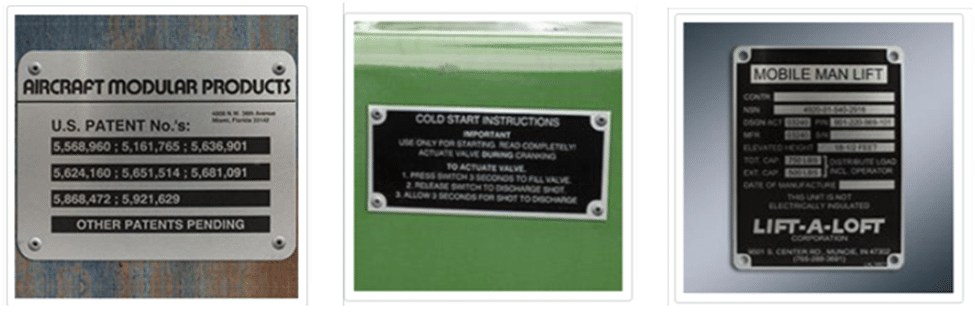
These labels remain legible for decades in the most challenging applications and harshest environments.
We’ll mention VIN tags and nameplates, safety and instructional plates among their many uses. Or coded labels that improve tracking and traceability of fleet vehicles, like the ones on these trucks.
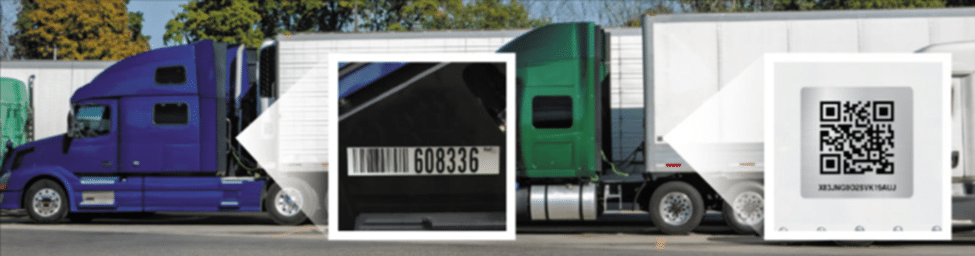
Of course, there are other labeling techniques to consider, like laser etching or dot peen marking.
Even if you decide to purchase a laser marker, you’ll still need to order some labels, and how many you order will naturally affect the price.
Each label design needs to be prepared according to specifications. This means that the set-up costs per label are the same whether you’re ordering 100 or 1,000.
However, this also means that the unit price will drop significantly as the number of ordered labels increases.
All in all, knowing how much you can spend and what to spend it on will inform your choices and help you manage your resources better in the long run.
Choose the Right Design
After you have defined the regulatory, safety, and asset management requirements for your labels and become aware of the budgeting implications of different label types and materials, it’s time to choose the right design.
The size of the equipment and the purpose of the label will dictate its shape and overall look.
For example, if the machine’s surface available for labeling is relatively small compared to the number of labels, the size and design of the labels must reflect that.
Luckily, at GoCodes Asset Tracking we offer even labels as small as coins, as you can see in the image below.
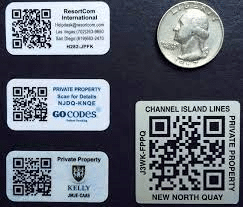
For instance, here’s how different labels look inside a forklift.
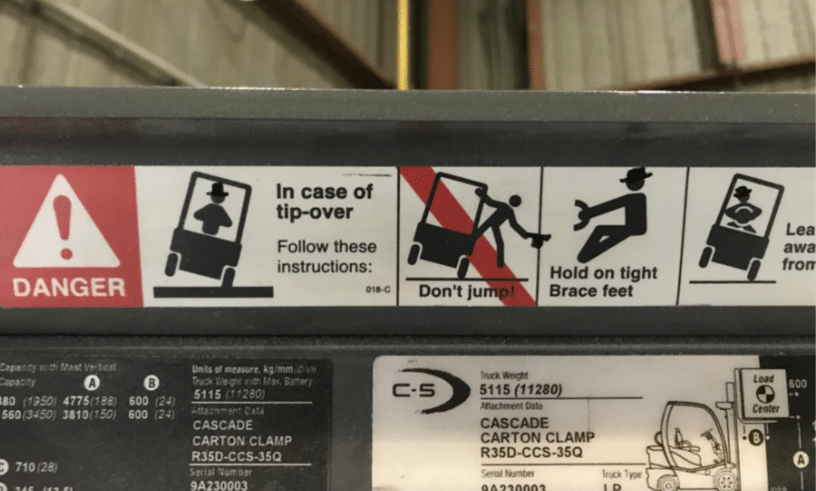
Their positioning also needs to be considered. For instance, barcode labels meant to be scanned from a distance need to be extra visible.
As mentioned, some labels on your equipment are mandatory and thus regulated by law.
This means their design and other details are subject to certain standards.
Where safety labels are concerned, standards regulate the colors and their meaning, as well as the design and use of safety symbols and signs, even the placement of the label.
The purpose is to ensure uniformity and consistency in application.
In other words, labels have to be designed in such a way as to avoid any misinterpretation or confusion that might lead to injury or death.
This means that their design elements are predefined, like you see here.
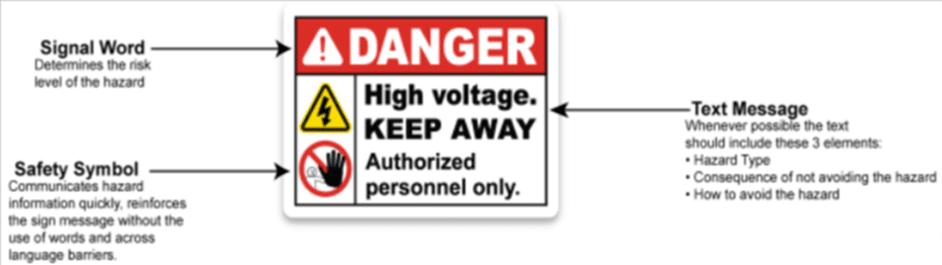
In this image, the signal word, color combination, and safety symbols are standardized. As for the text message, it can vary but should include the hazard type, potential consequences, and how to avoid them.
The same goes for other equipment labels depending on their function, specific industry, and some other factors like whether equipment contains chemicals or other hazardous substances.
This means you need to explore label types in your industry and their associated standards.
GoCodes Asset Tracking offers a variety of label types for tracking and managing your equipment, such as:
- Standard Poly BS 5609 2 x 1
- Premium_Poly_Bar_Code
- Photo Anodized Metal_Bar_Code
- Photo Anodized Foil_Bar_Code
Some other labels, like the instructional and inspection ones, offer some more breathing room for designers, but advice like making the language as clear as possible or not placing a label where it might interfere with the operation of equipment is applicable in all situations.
Learn more about what information should be included in your labels here.
Choosing the right design that meets industry-specific identification and warning labeling requirements, while also allowing you to organize and track your assets, will improve overall productivity and increase the safety of your operations.
Order Your Labels
Now that you have determined label specifications, done the budgeting, and settled on the right design, it’s time to choose your supplier. In doing so, there are things you can do to make sure you’re getting the best price, quality, and service.
First, buying quality labels for your industrial equipment is a necessity in most cases. In other words, you don’t want to save a few dollars on labels that will fall or peel off easily.
That will only result in additional costs and lost time for relabeling.
So, choosing the right label converter company is crucial in getting quality labels coupled with a good price from a supplier that knows their business.
You may decide to go with several suppliers for different label types, or prioritize identification and tracking labels while saving some money on warning and instructional labels.
For example, you can order custom warning labels like these.
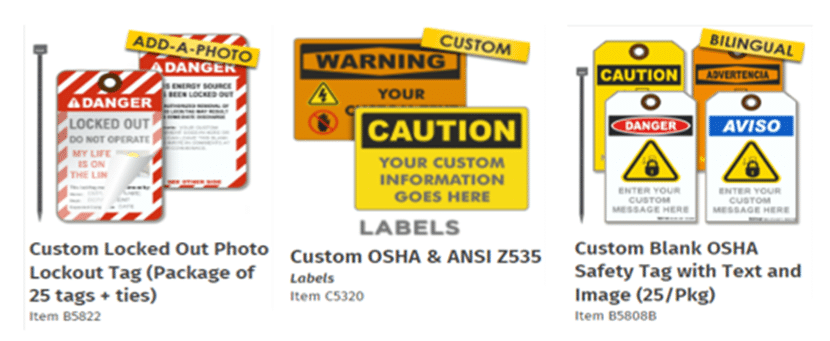
As you can see, you can order labels with custom text, insert a photo or create bilingual labels. It all depends on your needs. And, sometimes, it’s hard to know exactly what they are.
Naturally, many companies offer end-to-end equipment labeling solutions.
When you contact them, they can offer expert advice about the best choices for your specific needs.
Or to quote the website of just one of them, Resource Label Group, as an example:
“We guide you through the equipment labeling process.”
However, they also say that clients are responsible for compiling all relevant regulatory and safety information and other data that needs to be on each label.
So, it’s ultimately up to you to know exactly what you want on your labels, so you can count on their professional advice as they formulate a solution that will benefit you the most.

So, your label converter should be an expert that can keep up with your instructions and answer all your questions.
Remember, in all likelihood, this is not a one-off ordering process, and you want the best supplier for a long-term relationship. Naturally, you also want them to provide high-quality labels at a reasonable price.
If done correctly, ordering your labels—finding the right supplier and placing an order—should be easy when you know what you want.
Prudent decisions in these matters can lower your business’s short- and long-term labeling costs.
Apply Your Labels
So, you reached the phase of applying labels to your equipment. As with other steps, there’s a lot to consider and choose from.
However, there are things to look out for that will help you make the best choices before the actual application.
For example, here is what premium polyester labels that can withstand the harshest conditions consist of:
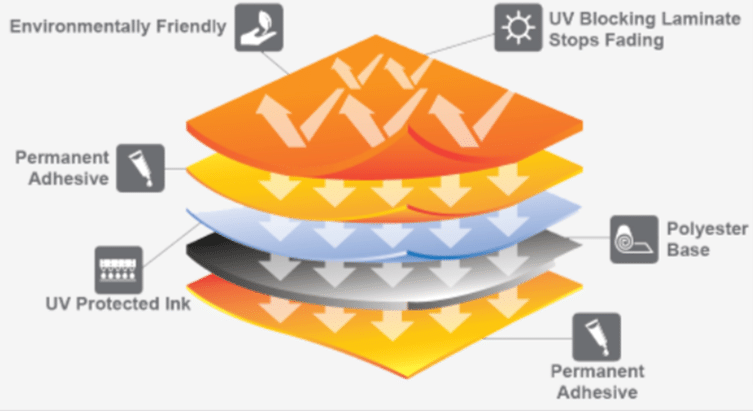
These labels are designed to last over ten years with unmatched durability and adhesion regardless of the environment.
Note that it has two layers of permanent adhesive.
However, the type of adhesive will depend on the available application surface and the conditions to which the equipment will be exposed.
Basically, there are three questions to ask:
- What kinds of surfaces will the labels be applied to?
- What type of adhesive would be best for such surfaces?
- Which labels can be applied manually and which require the use of a machine?
As for the first two questions, it’s important to remember that not all surfaces are created equal. And the same goes for adhesives.
Here’s what one company offers as possible label adhesive applications.
We highlighted only the options relevant for industrial labels.
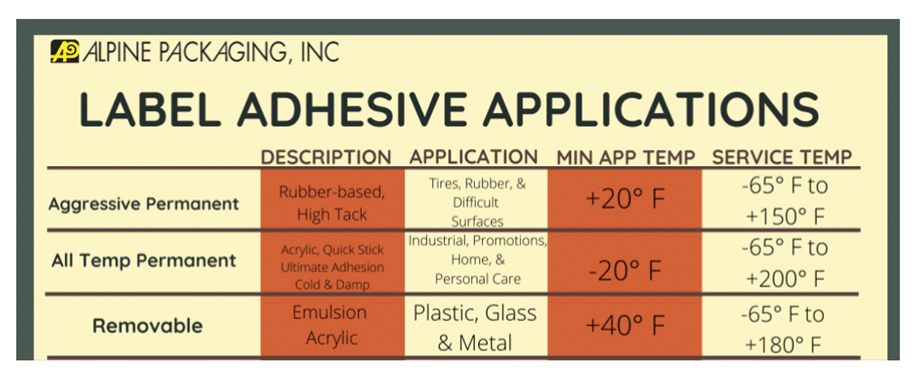
Depending on your needs, you can choose aggressive permanent applications for difficult surfaces, labels that will withstand all temperatures, or removable yet sturdy labels.
Since most industrial environments are not clean and dry, your label provider should be given detailed information about the application surfaces and the environment that the labeled equipment is going to be exposed to, so that they can provide the best possible solution.
You can check our own label application instructions on this link.
This will allow them to offer you an appropriate adhesive for the environment in question, as well as actionable tips on how to best prepare the surface before applying the labels.
Otherwise, you may end up having to replace labels frequently, which costs both time and money.
For example, here at GoCodes Asset Tracking, we offer a wide range of solutions for our clients’ needs.
Our patented QR labels come in smaller, metal foil versions optimal for use on office equipment or larger, more durable plates for large-scale equipment that’s usually kept outdoors.
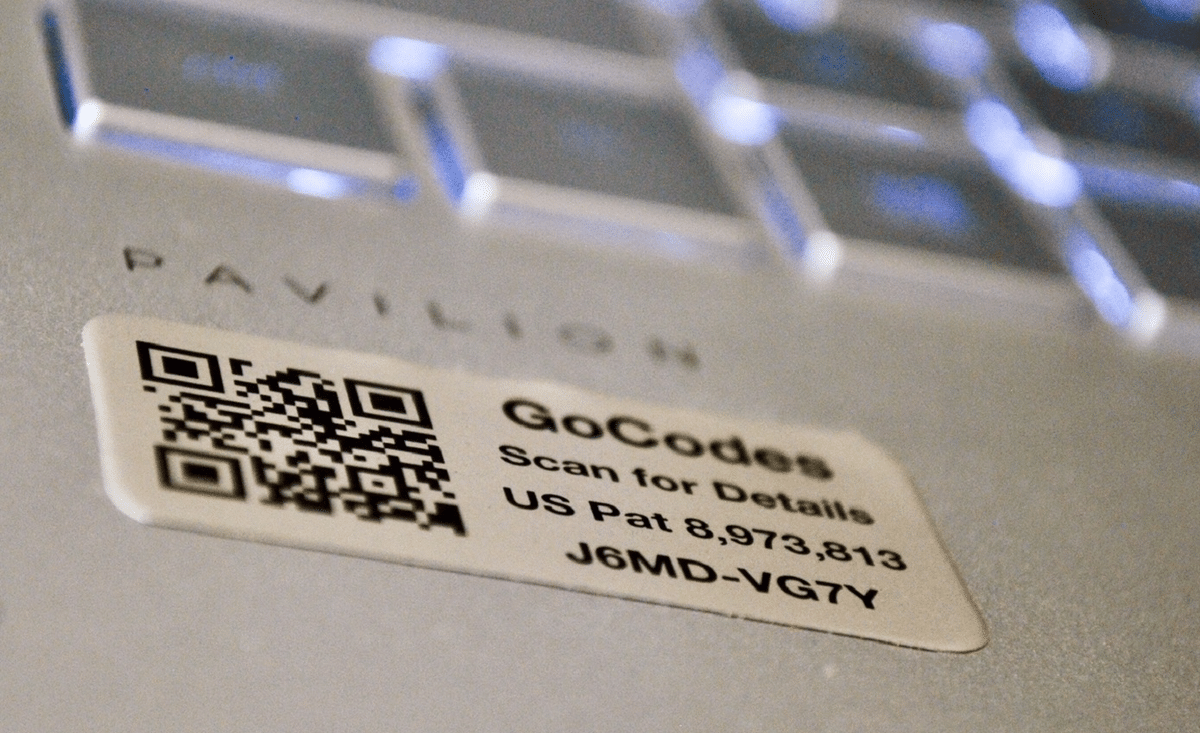
As for the manual vs. machine question, the answer depends on the number of labels and the frequency of applying them.
Answers can range from ordering your labels and tasking your staff to attach them by hand to owning multiple labeling machines to produce and apply your own custom labels.
Hence, it’s clear that there’s much more to applying your labels than just sticking them onto equipment.
Again, the right choices in this matter will save your business costs and time, thus raising its overall productivity.
Conclusion
As we’ve seen, labels are an indispensable part of any equipment and are used for everything from asset identification and tracking to branding.
Regardless of their use, each label category brings its own design challenges.
We hope this article proves helpful in guiding you toward the best labeling decisions for your business.