Now your asset tracking solution is up and running, you can begin collecting the data you need to effectively manage your equipment over its lifecycle, for improved efficiency all around.
So, where should you start?
In this article...
Track Utilization by Project
Start by running a Utilization report.
This report will capture all the check-in and out activities accomplished by your team. The report will organize the data into a simple view, grouped by project.
Using the information, you’ll be able to see the exact equipment deployed on any given project, including the duration that each item was used.
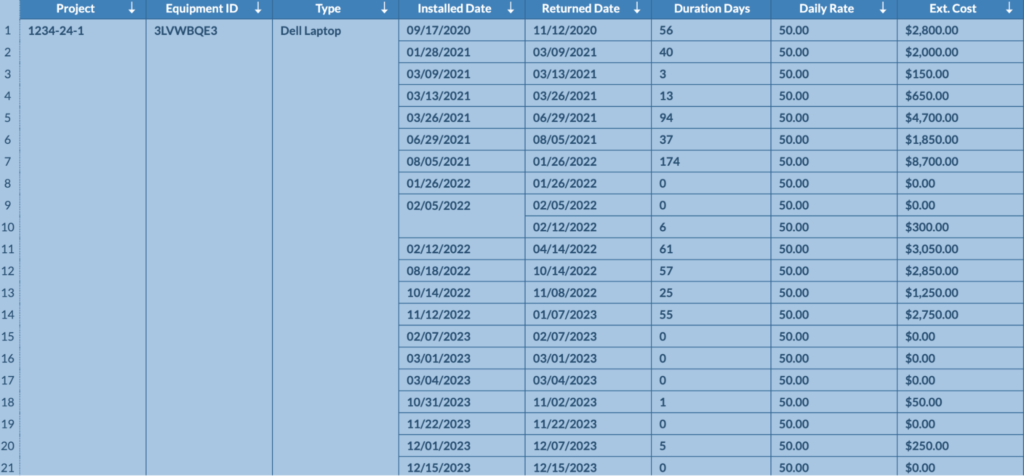
You can also apply hourly costs to each item.
The report will automatically calculate the total costs for all the equipment used on a specific project, ensuring precise financial management and accurate project management.
Breakage and Maintenance History
Next, track the Breakage and Maintenance history of your equipment to help identify any problematic patterns.
For example, it may become apparent that you should replace a certain piece of equipment, as its breakage history reveals that it’s now become too costly to repair.
You can also schedule and track maintenance activities to ensure that equipment is always in good condition and ready for use.
Risk Management for Equipment Losses
Your business likely owns expensive equipment, which is at a high risk for loss, especially if it’s frequently moved from job site to job site.
Use your asset tracking system to generate a daily report that will show the high-value equipment that is overdue for return.
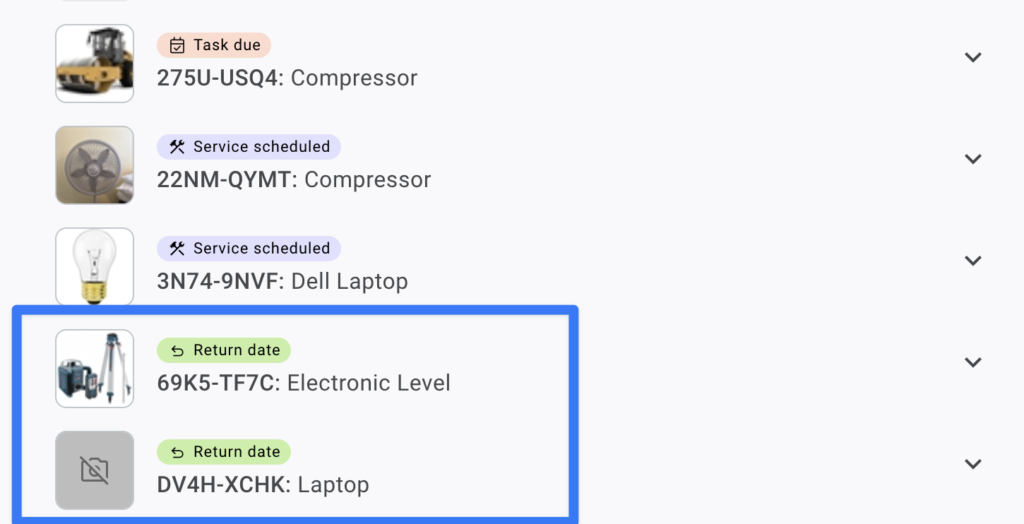
Harness this information, to implement recovery activities and plan for equipment audits. This will improve your operation and reduce loss.
Budget Planning and Forecasting
Planning for next year is made easier with Utilization data, which can be reviewed to help you build accurate budgets and forecasts.
For example, if you know the equipment’s purchase date and lifespan, you can predict its end of life and make plans to procure replacements.
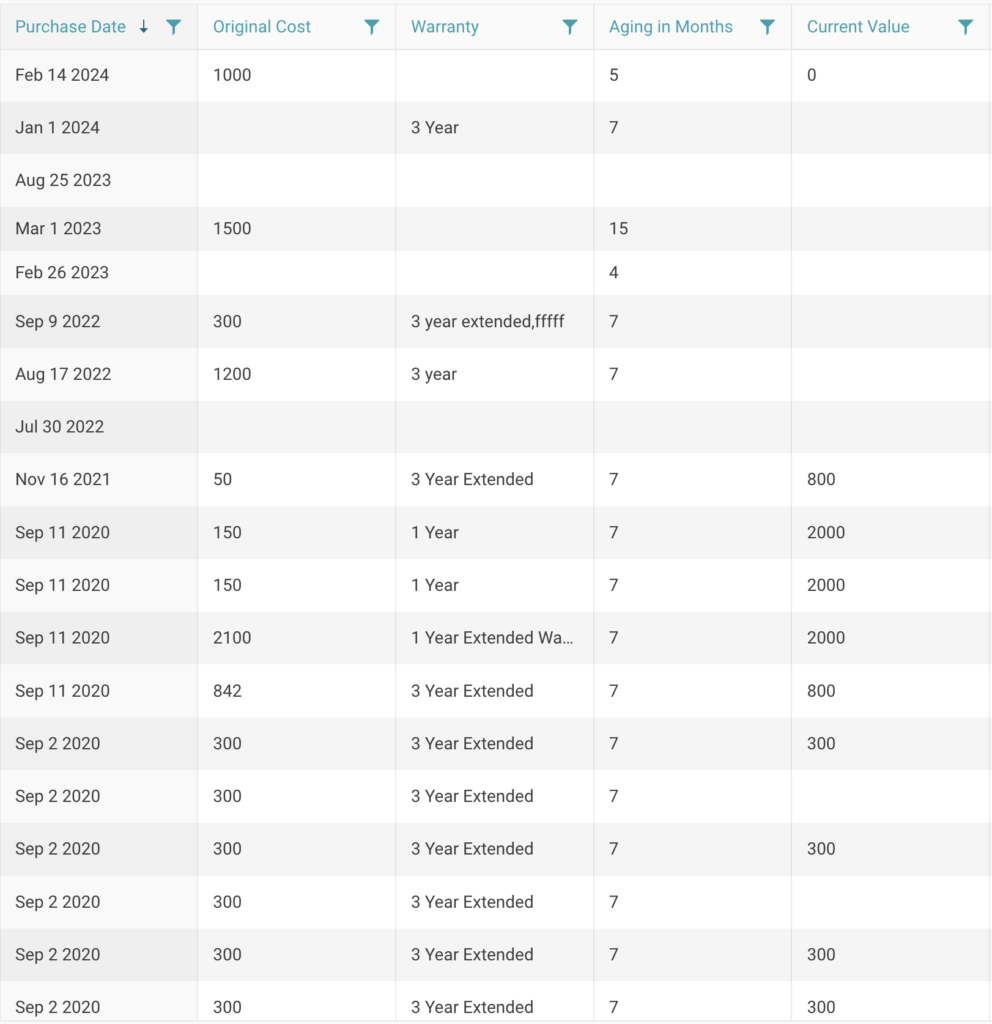
Easily review annual records for losses, breakages, and repairs to determine which items will need to be replaced in the coming year.
Also, predict what additional equipment you’ll need, so that you’re able to respond to new opportunities and know you’ll have the right equipment, ready to go!
Ghost Assets
Ghost assets are items of equipment that are still in your asset list but are no longer in your possession.
An asset tracking solution will help you complete your audit and help identify ghost assets so you can remove them from your inventory.
Then you can cancel any insurance, maintenance plans, or extended warranties that you’re still paying for on them while knowing you have an accurate list of all working equipment.
Both fiscally and operationally, leveraging data equates to great business sense!