Key Takeaways:
- By providing you with real-time vehicle data, telematics empowers you to stay updated on your vehicles’ usage and health, allowing you to make smarter decisions about your maintenance strategy and activities.
- Telematics solutions provide you with diagnostic trouble codes whenever a vehicle issue is detected and verified by the system. This enables instant intervention and issue resolution.
- By automating maintenance scheduling, telematics eliminates the need for manual recording, monitoring, and scheduling of vehicle service. That way, you can focus on more value-added activities.
Struggling to organize your maintenance schedule?
Fed up with your vehicles breaking down at the worst possible moment?
Do you often catch yourself sifting through a sea of spreadsheets and paperwork trying to figure out when each vehicle had its last oil change?
Now, that’s certainly no way to efficiently manage your fleet.
But fortunately, there’s a solution: it’s called telematics.
Want to learn more?
Keep reading, because we dive into the five ways this game-changing technology can take your maintenance game to a whole new level, ensuring your valuable assets stay in top-notch condition for as long as possible.
In this article...
Provides Real-Time Vehicle Data
Telematics empowers you to stay updated on your vehicles’ usage and health in real-time, in turn helping you make smarter decisions about your maintenance strategy and activities.
More specifically, with this technology, you always know how much each asset is idling and the number of miles it drives each day, which allows you to identify any irregularities or potential issues with more precision.
For instance, if one of your vehicles is experiencing poor gas mileage, this information will be readily available in the system, enabling you to intervene on time and make necessary repairs to prevent further trouble.
So, put simply, real-time data is the key to timely response to fleet issues, and therefore, improved maintenance efforts.
Russ Young, chief business development officer at Tenna, seems to agree.
He points out that, before telematics, tracking fleet performance was significantly slower, more cumbersome, and error-prone, ultimately leading to substantial long-term expenses:
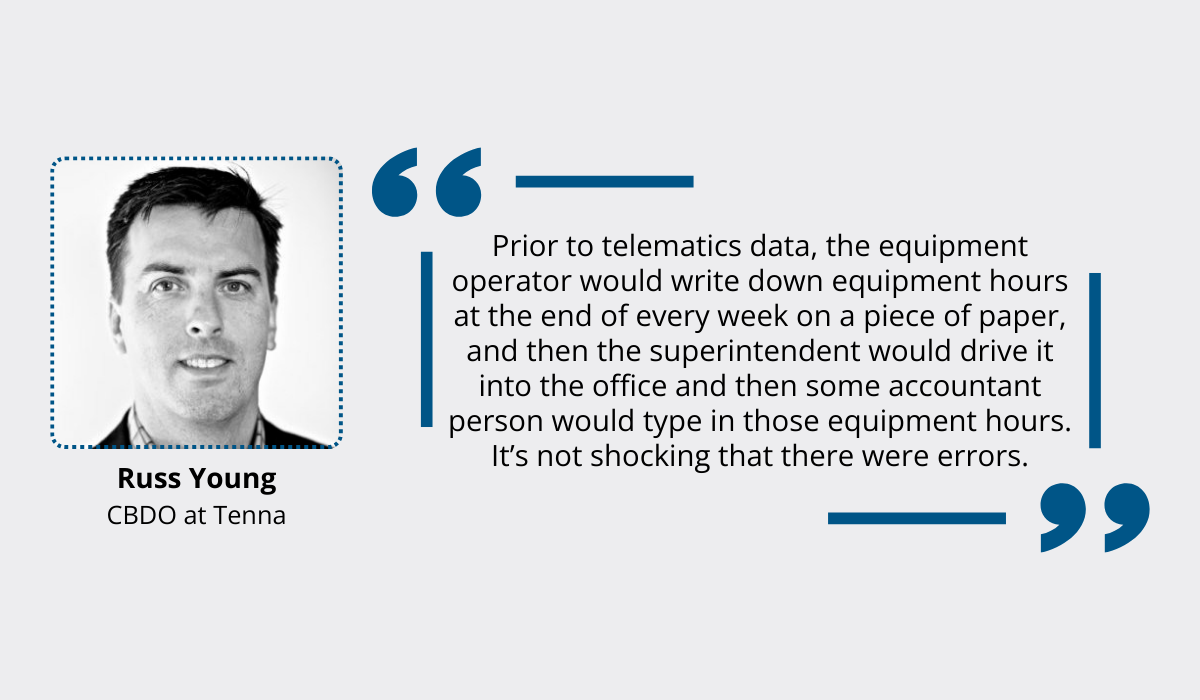
For example, instead of doing “an oil change for 30 bucks”, he says, you’d “end up having to replace the engine for $30,000” just because you weren’t able to monitor your assets’ upkeep needs properly.
But it’s not all about the bottom line and cost savings, either.
Real-time fleet information is a huge productivity booster, too.
With maintenance fueled by up-to-date insights, you’re nipping vehicle problems in the bud, thereby preventing failures, and minimizing unexpected downtime in the process.
And guess what?
According to research from Advanced Technology Services, Inc. (ATS) on industrial maintenance, it’s precisely unplanned downtime due to machine breakdowns that is the primary cause of productivity loss.
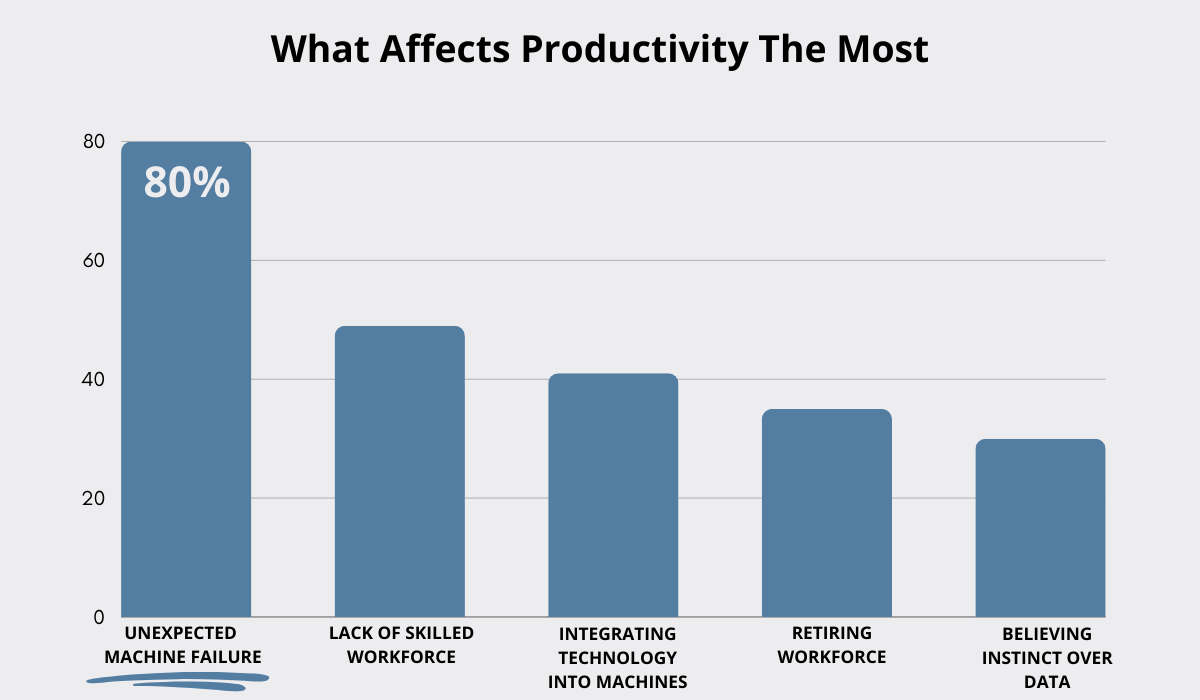
Now, although the research primarily focuses on manufacturing, instead of construction, its findings are universally applicable.
When an important asset fails, no matter what kind, the scheduled work usually has to be brought to a halt so that the issue can be examined, fixed, and a replacement found, resulting in considerable time losses and a dip in productivity.
Maintenance facilitated by real-time data addresses such scenarios upfront, leveraging timely fleet insights to maintain the health, efficiency, and reliability of your vehicles.
Essentially, this up-to-the-minute data allows you to always be one step ahead of the fleet’s upkeep requirements, catching potential malfunctions before they even have a chance to disrupt your operations.
That way, you’re not just reacting, but proactively solving problems, ensuring that every vehicle performs at its peak, every second of the day.
Keeps Track of Odometer Readings
Telematics solutions are able to keep tabs on odometer readings and alert you when particular milestones are reached, making vehicle service planning that much simpler and more efficient.
Now, it’s common practice to rely on mileage for timing maintenance, but the issue lies in the fact that many still have the drivers manually input their daily mileage, which often leads to unreliable data and mistakes during scheduling.
This, then, usually results in missing maintenance altogether.
Telematics, however, resolves this problem by automating mileage tracking entirely, guaranteeing accurate schedules, and making sure upkeep is never put on the back burner again.
As you already know, every vehicle is accompanied by specific maintenance intervals based on the miles driven, as recommended by their manufacturers.
And these recommendations exist for good reason, says Tyler Smith, product manager at Volvo Construction Equipment.
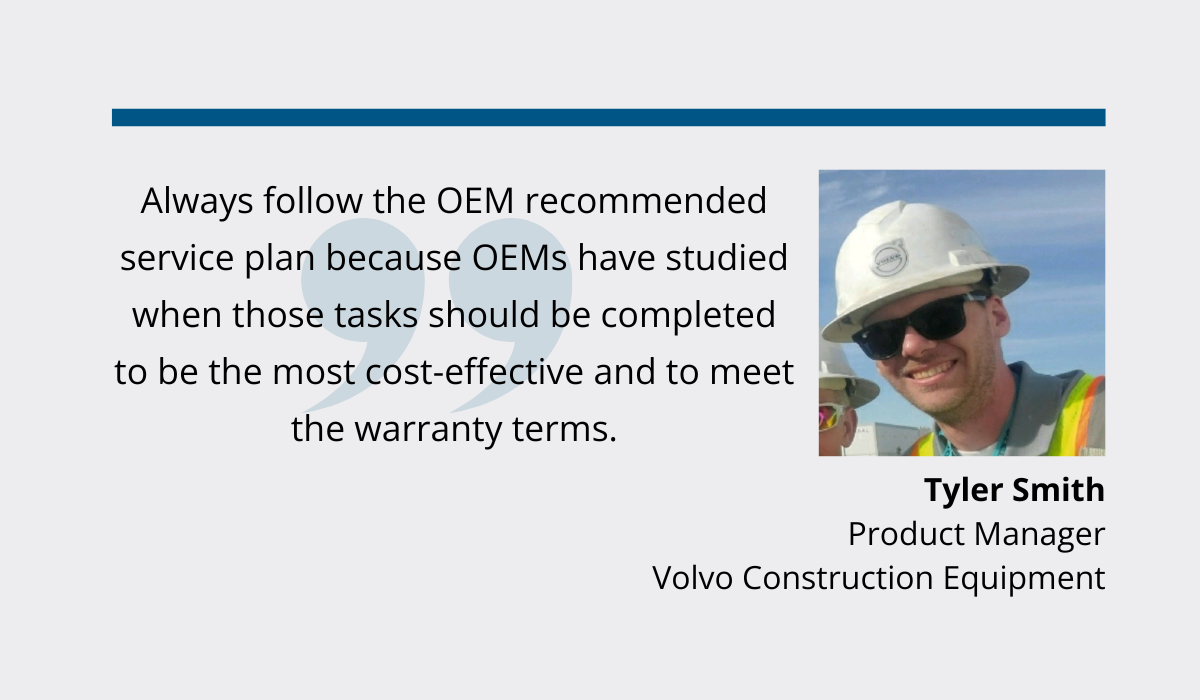
OEM recommendations are carefully crafted to help you make the most out of your upkeep processes and extend the lifespan of your valuable assets.
The reason telematics is so important in this context is that it simplifies compliance with these OEM instructions by consistently logging odometer data, eliminating data entry errors, and issuing timely notifications for upcoming service tasks.
But why bother with all this precision? Wouldn’t scheduling maintenance based on time intervals be simpler?
For example, why not simply set a calendar reminder for an oil change every, say, three months?
Yes, this may seem more convenient at first glance, but the diverse vehicle usage patterns make such generalized schedules impractical and ineffective—even user manuals will tell you as much.
Don’t believe us?
Take a look at an excerpt from the 2023 Cadillac Escalade owner’s manual below.
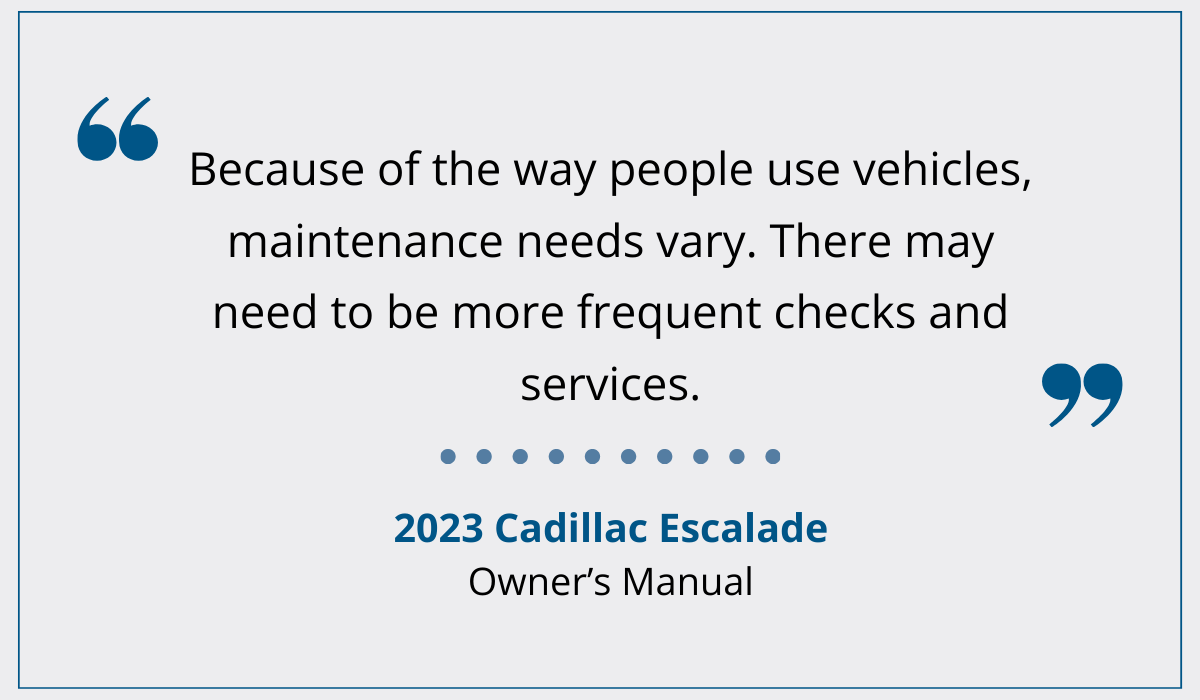
The same principle can be applied to any sort of vehicle.
Since vehicle use varies, so do the maintenance needs: one-size-fits-all service schedules just don’t cut it.
Luckily, telematics takes the guesswork out of the equation and, by relentless odometer readings monitoring, it ensures that maintenance tasks are performed exactly when needed, tailored to each asset’s unique usage patterns.
Notifies You of Diagnostic Trouble Codes
Telematics solutions provide you with diagnostic trouble codes (DTCs) as soon as a vehicle issue is detected and verified by the system, enabling swift intervention and resolution before the problem spirals out of control.
Generated by a vehicle’s onboard diagnostic system (OBD), DTCs are alphanumeric codes that pinpoint specific underlying causes of vehicle problems, empowering maintenance personnel to diagnose and fix issues more quickly.
Here are some examples of common DTCs, along with their descriptions.
P0300 | Random/Multiple Cylinder Misfire Detected: Indicates that the engine’s control module has detected misfires occurring randomly across multiple cylinders. |
P0420 | Catalyst System Efficiency Below Threshold (Bank 1): Suggests that the catalytic converter is not operating efficiently on bank 1 of the engine. |
P0171 | System Too Lean (Bank 1): Indicates that the engine is running too lean (too much air, not enough fuel) on bank 1 of the engine. |
P0172 | System Too Rich (Bank 1): Opposite of P0171, indicating that the engine is running too rich (too much fuel, not enough air) on bank 1 of the engine. |
P0442 | Evaporative Emission Control System Leak Detected (Small Leak): Indicates that there is a small leak in the evaporative emission control system. |
These are just a few examples of the thousands of possible DTCs that can be generated by a vehicle’s onboard diagnostic system.
Each code corresponds to a specific issue or condition that the vehicle’s computer has detected.
With telematics and DTCs, gone are the days of having to rely on drivers to notice the dreaded check engine light and hoping they report the problem on time.
Telematics devices interpret trouble codes and relay their descriptions to mechanics preemptively, often before drivers are even aware of warning lights.
This ensures fleet service needs are consistently addressed, preventing minor issues from evolving into major operational and financial setbacks.
In fact, did you know that, by leveraging telematics for asset health monitoring and trouble code alerts, you can increase your fleet’s uptime by up to 25%, as reported by Verizon Connect?
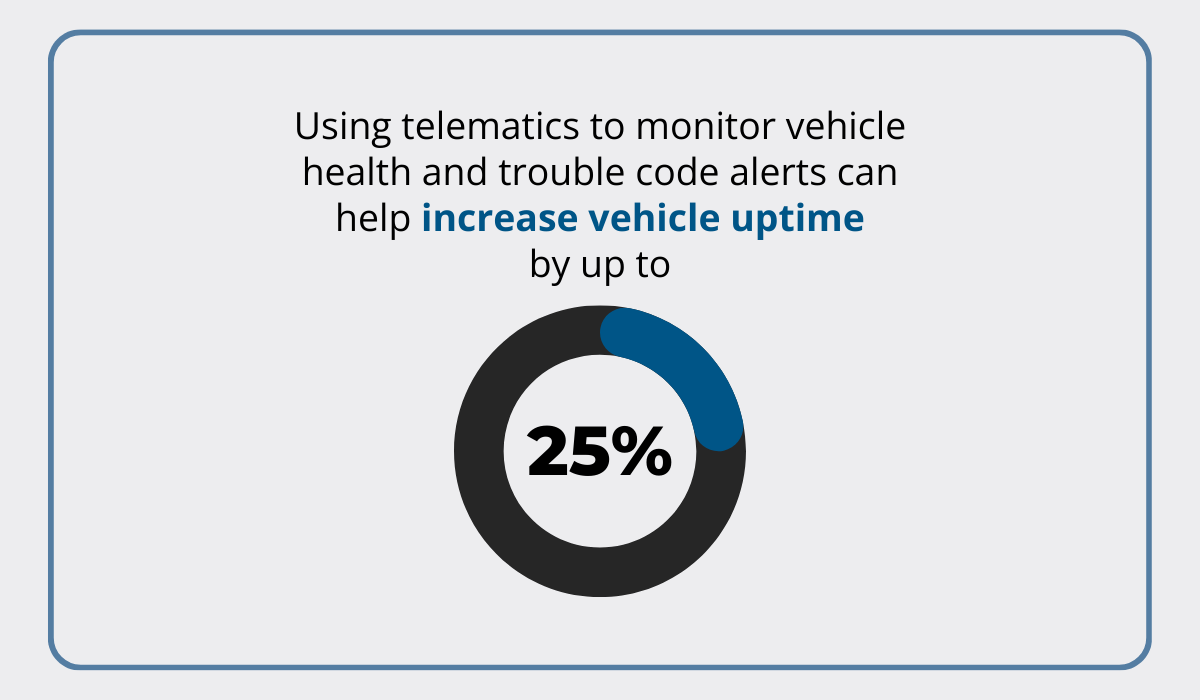
Talk about boosting your ROI.
At the end of the day, the effectiveness of your maintenance efforts largely depends on how quickly and accurately you can determine the root cause of vehicle malfunction, a task DTCs handle with ease.
Telematics systems, in this case, act as the conduit, translating these codes into actionable insights and immediate notifications, ensuring uninterrupted fleet performance and minimizing operational disruptions.
Automates Maintenance Scheduling
As a fleet manager, you already have a lot on your plate, so keeping tabs on and planning maintenance schedules for every single asset in your fleet is definitely the last thing you need.
Luckily, telematics can handle this tedious task for you.
In fact, it completely eliminates the need for manual recording, monitoring, and scheduling of vehicle service, freeing you up to focus on more high-level responsibilities.
Since telematics systems are capable of tracking DTCs, odometer readings, and other aspects of fleet health, they are also able to predict when vehicle servicing will be needed and schedule it automatically.
It doesn’t get any more efficient than that.
Guillaume Poudrier, the president of fleet management solution provider Géothentic, suggests that telematics can, through automation, prevent the two major issues of vehicle service planning: under and overscheduling.
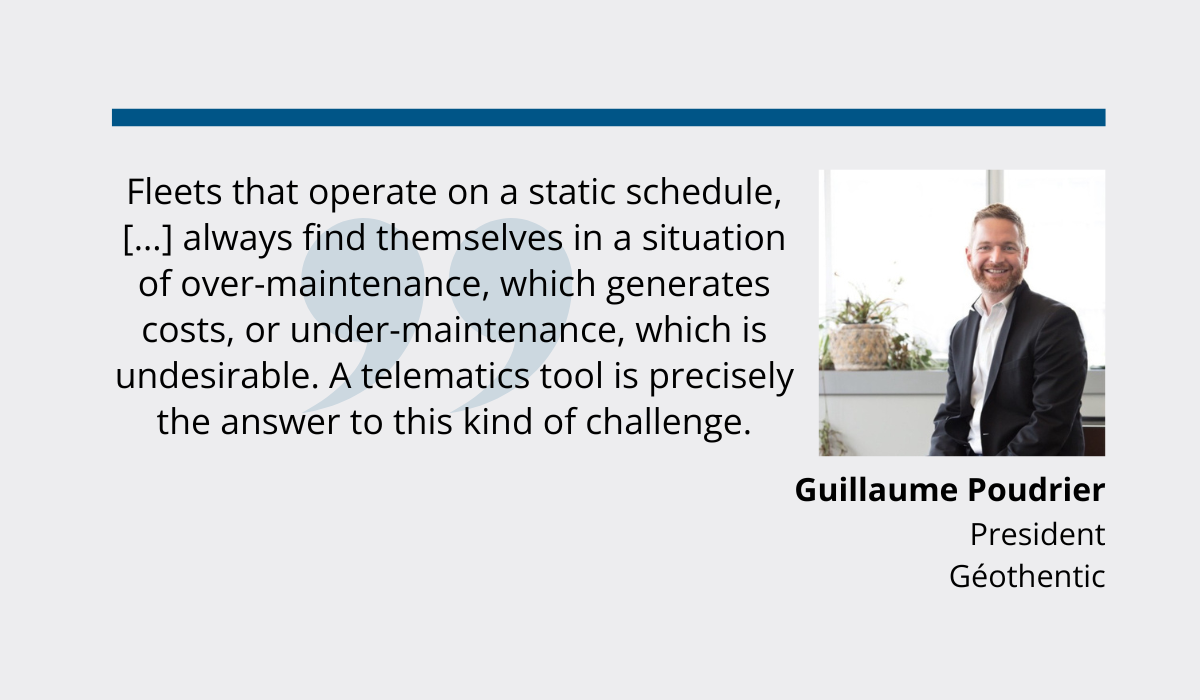
He believes that maintenance schedules have to be flexible—not static—to be effective and that telematics can make that happen by analyzing each asset closely and organizing upkeep tasks based on data-driven insights rather than guesswork.
After all, when it comes to fleet maintenance, guesswork is a recipe for disaster.
When you rely on intuition to plan and schedule vehicle service, you can inadvertently cause all sorts of operational problems.
For instance, UpKeep’s head of partnerships, Bryan Bieschke, warns that neglecting proper scheduling or doing it without considering actual asset needs can ultimately lead to a loss of productivity due to unplanned downtime:
“Teams struggle to this day to control asset downtime […] We continue to operate our machines outside of the design specifications and do not build an asset-based maintenance strategy that looks at context, environment, or age to name a few. Planning and scheduling is a misunderstood process and it’s often put on the back burner for today’s downtime.”
Telematics technology, on the other hand, never misses a beat when it comes to vehicle tune-ups.
It tells you what needs to be done, when it should be done, and why it’s necessary, as well as alerts you when the maintenance is due, making it impossible to skip scheduled service.
Such an automated approach not only keeps your fleet well-maintained at all times but also provides peace of mind, eliminating the need to waste time and energy on inefficient processes.
Aggregates Data into Visual Reports
To master your maintenance game plan, you need to dive deep into the inner workings of your fleet and have detailed insights into the performance and health status of your vehicles.
Telematics provides precisely that by aggregating important data into actionable, easy-to-understand, visual reports, covering areas such as:
- Vehicle activity (mileage, usage, operator, work orders)
- Vehicle diagnostics (engine, transmission, brakes, exhaust, tires issues)
- Idling analysis (evaluating its impact on vehicle health)
- Harsh events (assessing their impact on vehicle components)
Who needs manual maintenance tracking, which is highly prone to errors, labor-intensive, and time-consuming anyway?
With automated reporting, the days of drowning in spreadsheets and paperwork are long gone.
No more mistakes, no more missing information, no more guesswork—just crystal-clear data guiding your every move.
And, according to Kevin Aries, director of product marketing & employee engagement at Verizon Connect, when you’ve got data in your corner, your maintenance game reaches a whole new level.
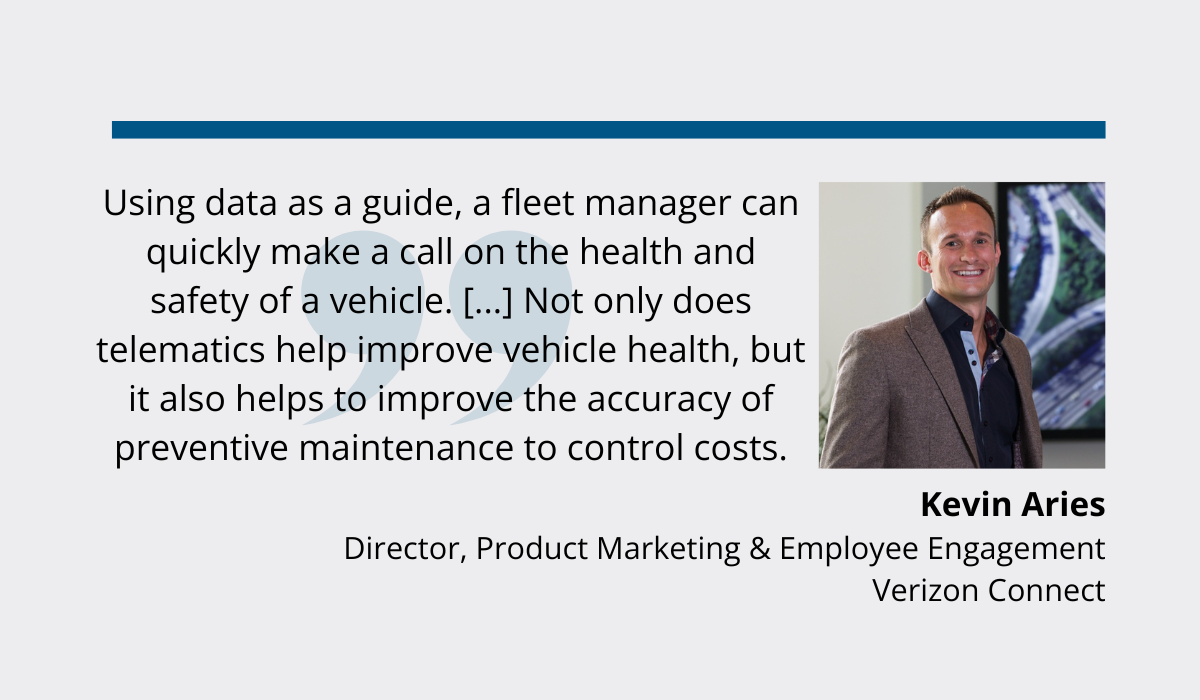
Suddenly, you’re no longer grappling with reactive asset repairs, but instead extending your vehicles’ lifespans, slashing fleet costs, and keeping your fleet at its peak performance.
The best part?
These reports aren’t just for predicting and addressing your current maintenance needs.
You can also archive them for future reference and use this historical data for benchmarking purposes, which enables you to analyze and score your maintenance efforts over time and identify areas for improvement.
Overall, reporting can be quite a useful telematics feature, helping you transform mountains of fleet data into usable information.
Its primary goal?
To steer your decision-making with precision, accuracy, and efficacy.
Conclusion
All in all, it’s safe to conclude that the biggest strength of telematics is its ability to automate virtually all facets of fleet upkeep.
By doing so, it not only lightens your workload and eliminates unnecessary processes but also enhances maintenance efficiency overall.
This, in turn, translates into a wide variety of perks, such as lower repair expenses, increased vehicle uptime, prolonged fleet lifespan, and ultimately, smoother business operations.
Eager to unlock these benefits yourself?
Embrace telematics and you’ll level up your fleet maintenance game in no time.