Key Takeaways:
- Asset tagging reduces theft risk and speeds up equipment recovery.
- Asset tagging and GPS tracking cut unnecessary purchases and last-minute rentals.
- Telematics and asset tracking systems improve uptime by 25%.
- Comprehensive digital records streamline warranty claims.
Upsurge in construction equipment theft and common foes like unplanned downtime will strain any budget, turning small oversights into major financial setbacks.
Fortunately, asset tagging offers a simple, scalable way to cut costs and safeguard your equipment.
In this guide, you’ll discover five practical ways asset tagging reduces expenses while improving equipment lifespan and overall site efficiency.
In this article...
Reduces Asset Theft
Asset theft remains one of the most expensive and disruptive problems in construction.
Addressing it successfully requires various strategies, including asset tagging.
In 2024, security solutions provider BauWatch released a report with several concerning findings on construction crime.
Now, a preview statistic from their new report indicates that 67% of construction professionals believe crime rates on jobsites have risen again this year, with no signs of easing.
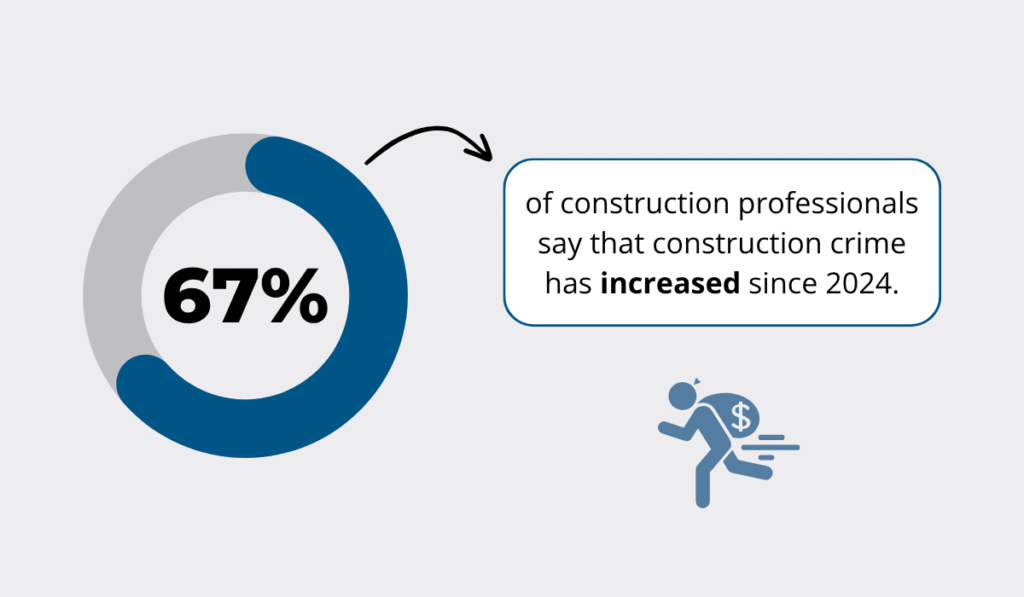
Illustration: GoCodes Asset Tracking / Data: BauWatch UK & Ireland on LinkedIn
The reason these numbers are so worrying lies in the hidden costs of tool theft.
Replacing your stolen gear is expensive on its own, but the real damage comes from delayed schedules, stretched budgets, and even failed projects.
While industry groups and lawmakers are working on new measures to help, the day-to-day responsibility for protecting assets still falls on businesses.
That’s why it’s essential to understand theft patterns and put the right safeguards in place.
Joël Fruchart, President of the Rental Commission DLR in France, highlights that excavators, generators, and telehandlers are currently among the most targeted items on jobsites.
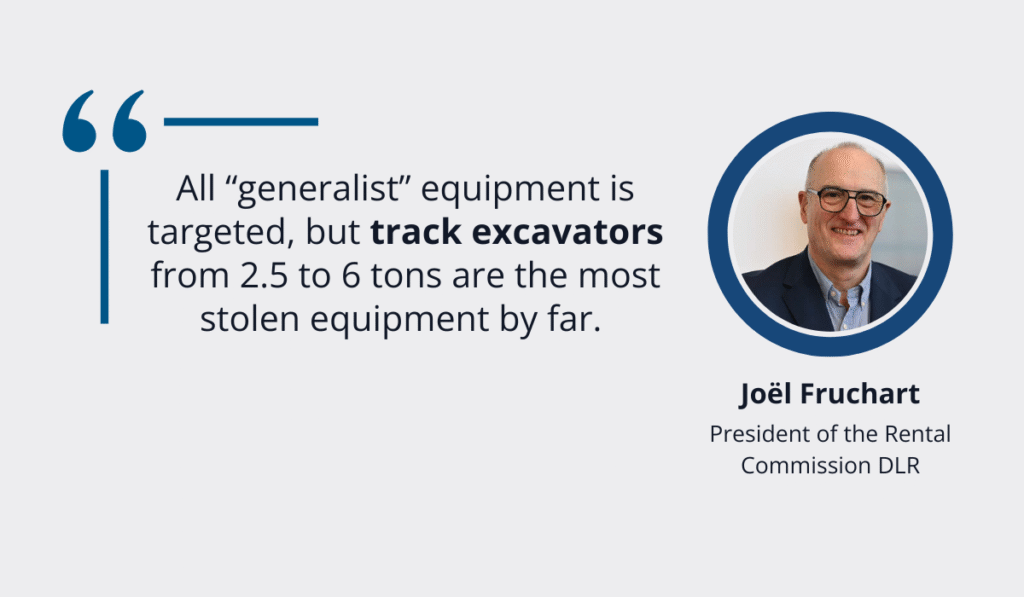
Illustration: GoCodes Asset Tracking / Quote: International Rental News
So, how can asset tagging reduce theft on jobsites?
It increases the visibility and traceability of all your equipment, including small tools.
By equipping tools and machinery with barcodes, QR codes, RFID tags, or GPS trackers, you’re creating a reliable deterrent and a recovery system in one.
Labels and tags with tamper-resistant adhesives are difficult to remove discreetly.
This makes would-be thieves think twice before stealing them, while also increasing the chances of recovering stolen equipment.
In contrast, unmarked tools are notoriously hard to return to their owners, even when recovered by law enforcement.
For example, after recovering over £50,000 worth of stolen tools, Essex Police urged businesses and tradespeople to mark and photograph their tools, record serial numbers, and keep detailed inventories of all their equipment.
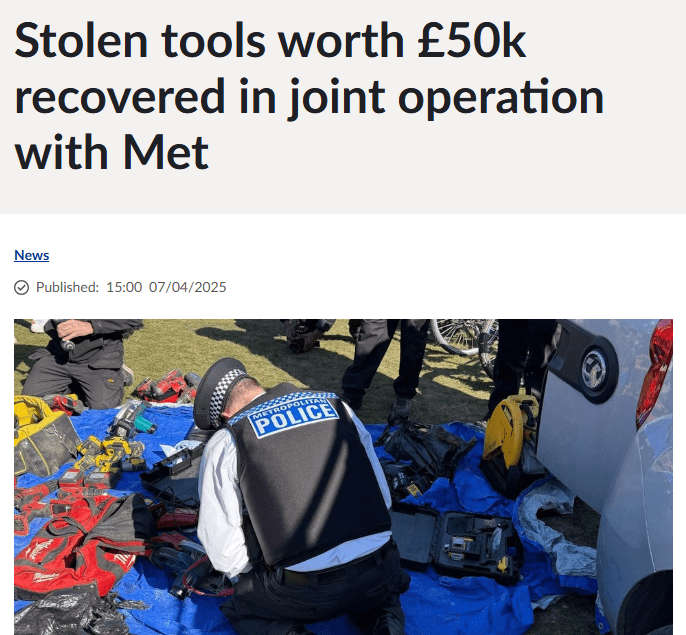
Source: Essex Police UK
All this can be done faster and with more confidence when using an asset tagging system.
In fact, CIOB’s findings show that over 65% of surveyed construction professionals see asset tracking or unique identifiers as effective theft deterrents.
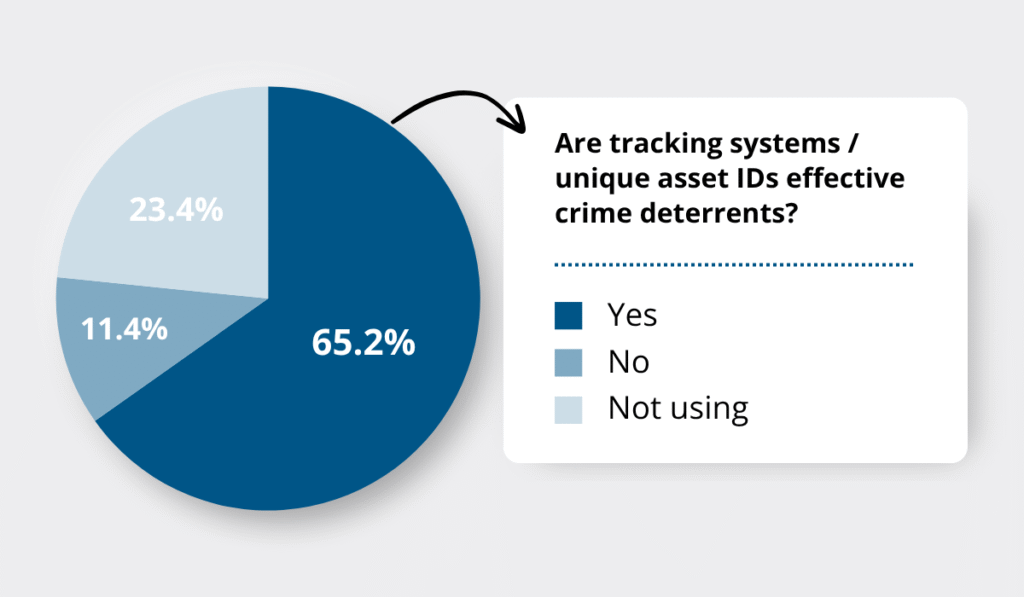
Illustration: GoCodes Asset Tracking / Data: CIOB
Cloud-based systems with scannable asset tags provide instant access to each item’s last known location.
When combined with real-time GPS trackers and geofencing, they offer an even stronger line of defense.
These systems let you set virtual boundaries around jobsites or storage yards and trigger instant alerts if any tagged asset or material shipment crosses them.
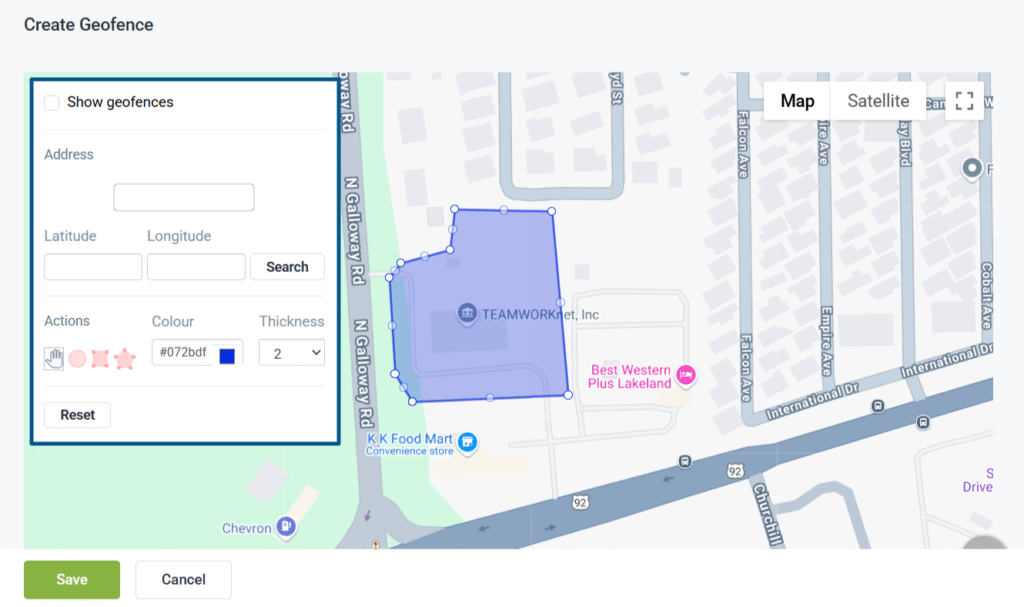
Source: GoCodes Asset Tracking
In other words, costly disruptions are nipped in the bud.
If you’re looking for a practical, proven way to reduce losses and protect both your property and bottom line, asset tagging is the way to go.
Minimizes Unnecessary Purchases
One of the simplest ways to control costs in construction is by making sure you’re only buying what you truly need.
Asset tagging plays a key role here by preventing equipment loss and enabling better use of the resources you already have.
This matters more than ever as equipment costs continue to rise.
A quick look at current listings on sites like Machinery Trader shows just how expensive both new and used machinery has become, particularly essentials like skid steers.
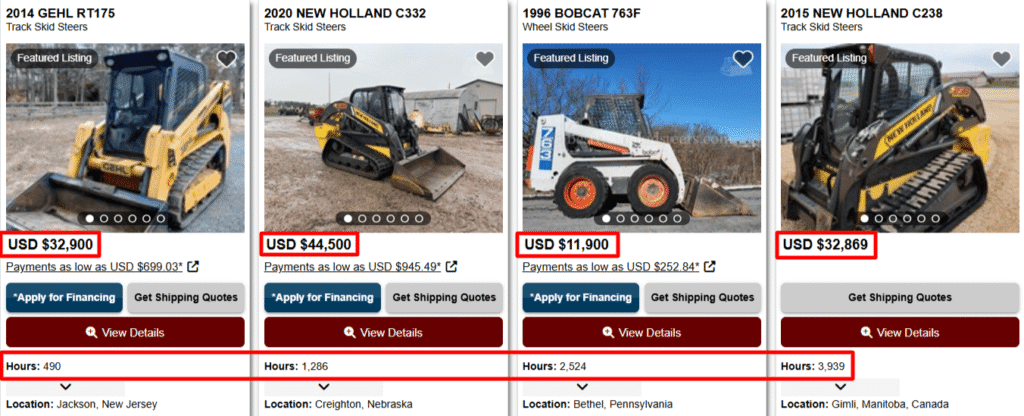
Source: Machinery Trader
It’s no surprise, then, that owning and operating equipment can account for up to 50% of total project costs.
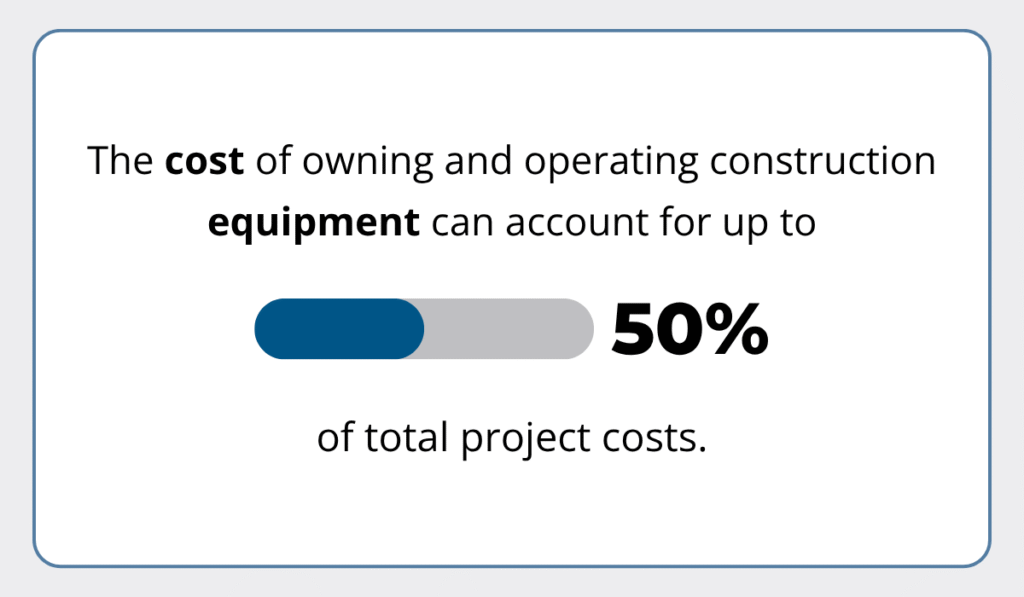
Illustration: GoCodes Asset Tracking / Data: Equipment Watch
If you’re wondering why, consider that simply moving equipment between sites adds to the strain.
The same Equipment Watch report found that roughly a quarter of construction professionals rent equipment simply to avoid the high cost of transporting their machines to the jobsite.
So, how does asset tagging contribute to reducing these costs?
Again, it comes down to increased visibility and traceability of your entire inventory.
Tagging your assets lets you instantly see where your equipment is located through a simple map view, helping you plan and avoid last-minute hires or costly emergency deliveries.
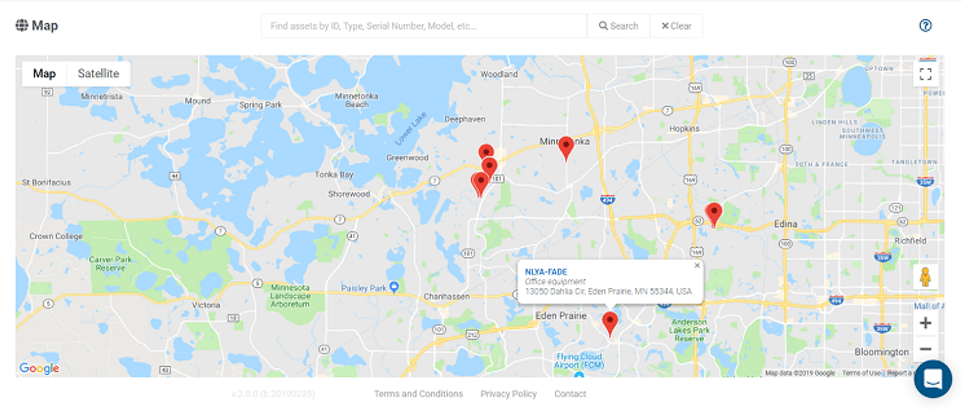
Source: GoCodes Asset Tracking
This is especially useful for companies managing larger fleets or working on bigger projects, but the benefits are universal.
When every asset is labeled, tracked, and accounted for, there’s far less risk of double-booking, over-ordering, or mistakenly replacing equipment that was simply misplaced.
Even better, when tagging systems are paired with asset management platforms like GoCodes Asset Tracking, you gain utilization insights.
Key summaries based on real-time data show you how often and how efficiently specific pieces are used.
Custom reports can be quickly generated for any period, helping you identify underused equipment and opportunities to redistribute rather than repurchase.
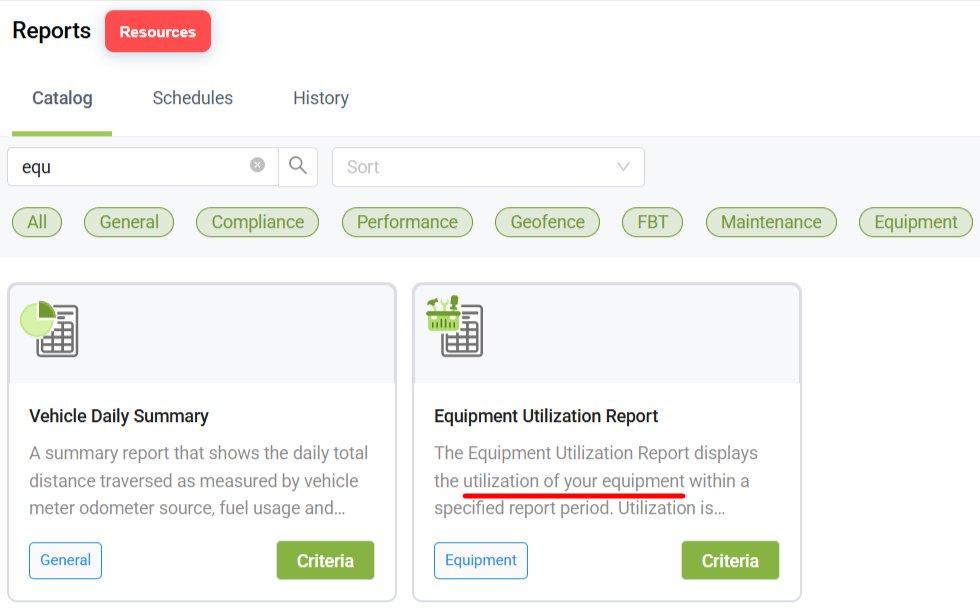
Source: GoCodes Asset Tracking
By mapping these weak areas, you can avoid bottlenecks and improve productivity, keeping costs in check.
Ultimately, smarter asset use cuts down on unnecessary purchases, while keeping existing assets in good condition extends the time between replacements.
Extends Asset Lifespan
Asset tagging directly contributes to longer asset lifespans by improving visibility, enabling proactive maintenance, and supporting smarter resource management.
Think about it.
When you can easily track an asset’s location, usage, and maintenance history, keeping your equipment in optimal condition—and controlling costs—becomes far easier.
Every construction business benefits from reducing equipment maintenance costs, but there are different approaches, including:
- Cutting staff or delaying maintenance to reduce short-term costs
- Implementing regular and effective maintenance
- Improving efficiency by automating processes
For example, the first option might offer immediate savings, but it impacts asset reliability, inevitably leading to much higher expenses later on.
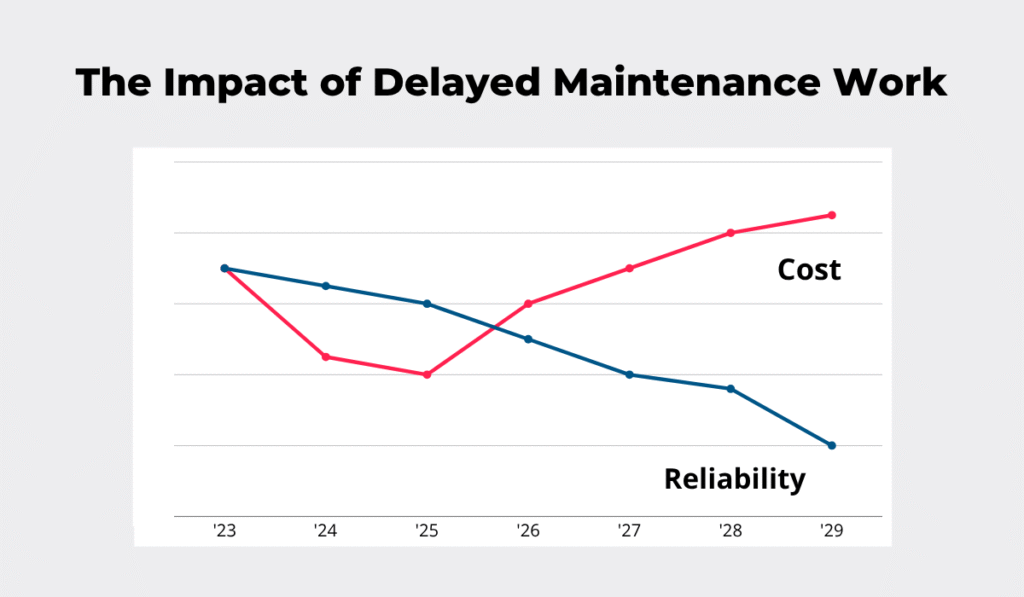
Source: GoCodes Asset Tracking
Asset tagging helps you avoid that trap.
By attaching physical tags to your equipment, you can track maintenance records, schedule routine inspections, and quickly identify which assets require servicing.
This proactive strategy prevents costly breakdowns, extends equipment lifespan, and keeps your operations running smoothly.
In fact, Equipment Watch data shows that continuous asset health monitoring can extend asset lifespan by 20 to 40%.
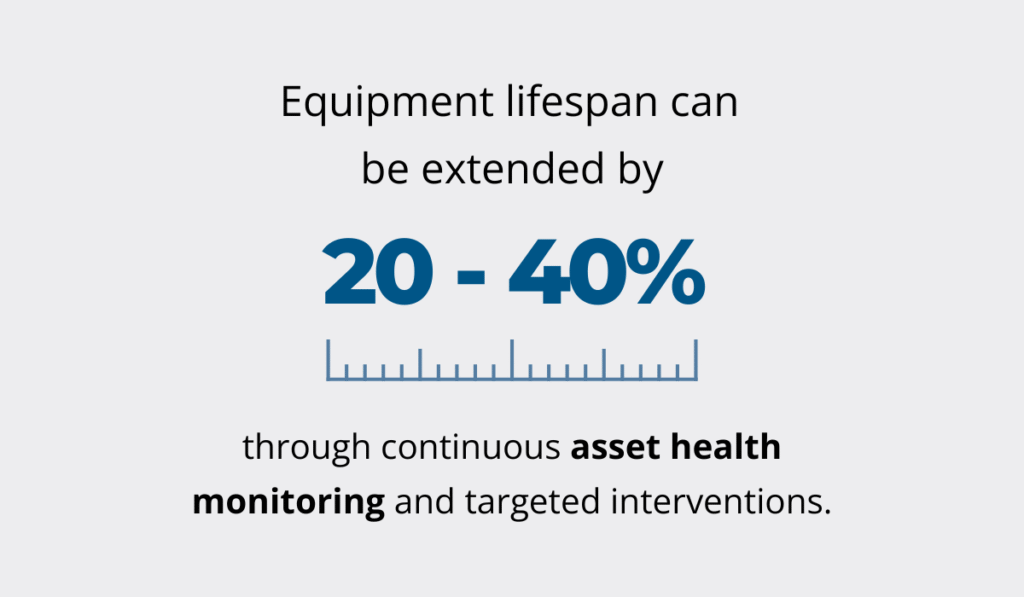
Illustration: GoCodes Asset Tracking / Data: Equipment Watch
Accurate, accessible data is the backbone of this process, and that’s why manual processes simply won’t do.
Asset tags enable precise data capture by providing a consistent, reliable method for recording and retrieving asset information.
Scanning a tag eliminates manual entry errors and ensures up-to-date access to maintenance records, machine specifications, warranty details, and more.
Even better, maintenance teams can instantly access service histories, check schedules, and add notes without ever leaving the site.
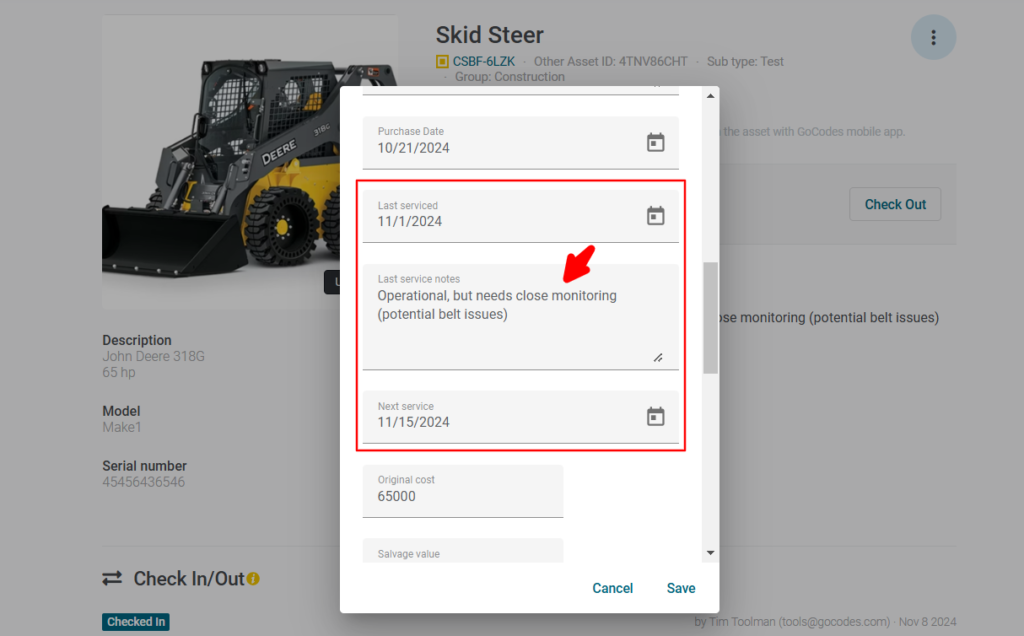
Source: GoCodes Asset Tracking
This level of visibility makes it easier to plan maintenance proactively, improve asset reliability, and avoid non-compliance with any safety or regulatory standards.
Moreover, with systems that simplify scheduling and enable a quick overview of upcoming maintenance tasks, keeping equipment in good working order becomes second nature.
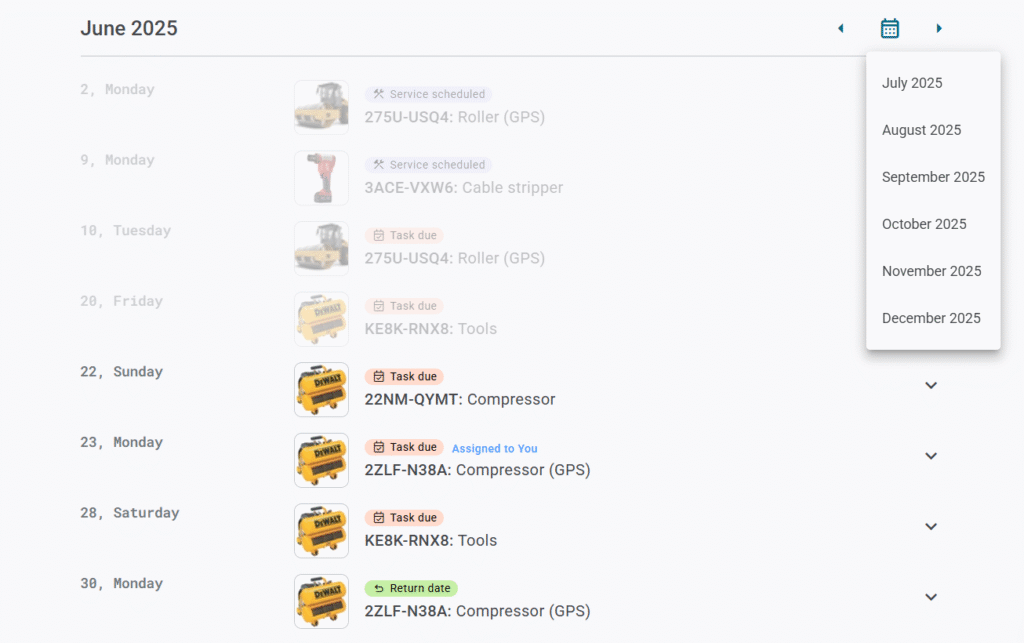
Source: GoCodes Asset Tracking
Dewantara Akbar, branch manager of one of ofi’s processing factories, notes that effective maintenance relies on early fault detection, proper planning, and swift intervention.
And it all leads to prolonged asset life and reduced downtime.
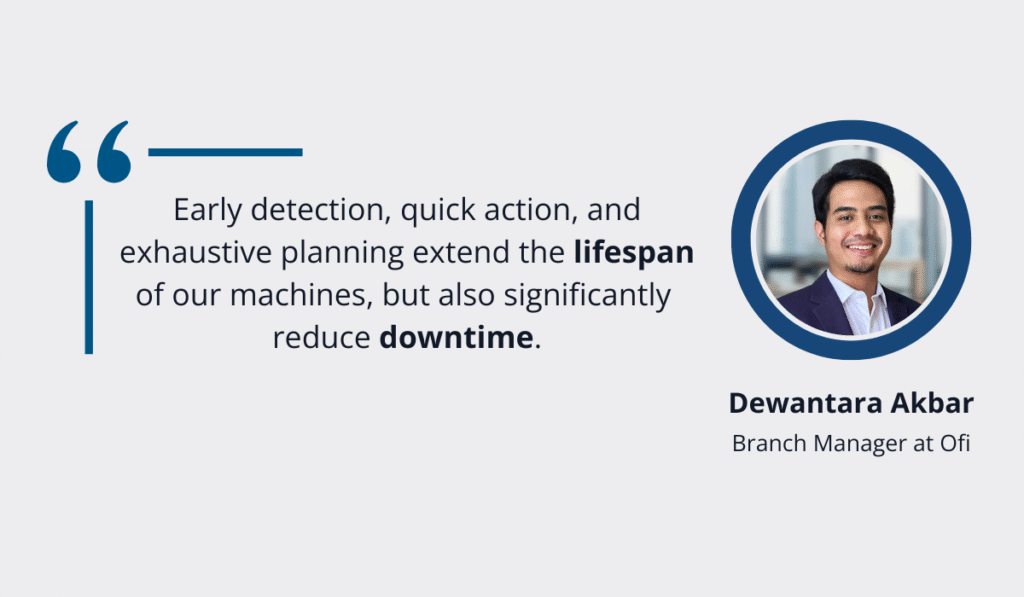
Illustration: GoCodes Asset Tracking / Quote: LinkedIn
None of these processes would be as efficient without asset tags, trackers, and sensors delivering the necessary data.
In the end, asset tagging protects your investments by helping keep your equipment in optimal condition for as long as possible.
Reduces Downtime on the Construction Site
Tagging your assets plays an important role in reducing costly downtime on construction sites.
Every minute a machine sits idle can eat into your budget, derail schedules, and in some cases, jeopardize entire projects.
As equipment manager Dan Corbett points out, the delays caused by downtime often cost more than the actual repairs.
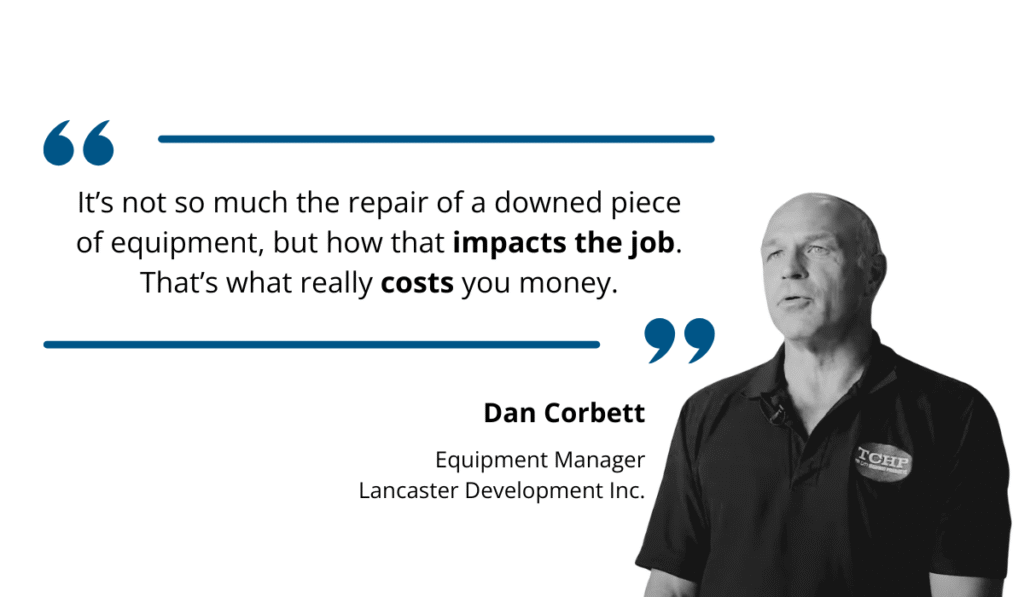
Illustration: GoCodes Asset Tracking / Quote: For Construction Pros
Consider the example of a Canadian plant where managers faced a difficult choice: pay CAN $50,000 for an immediate fix of the vital lime kiln or postpone repairs until a planned shutdown.
They chose to wait, but just six weeks later, a major breakdown occurred, ultimately costing the company CAN $300,000.
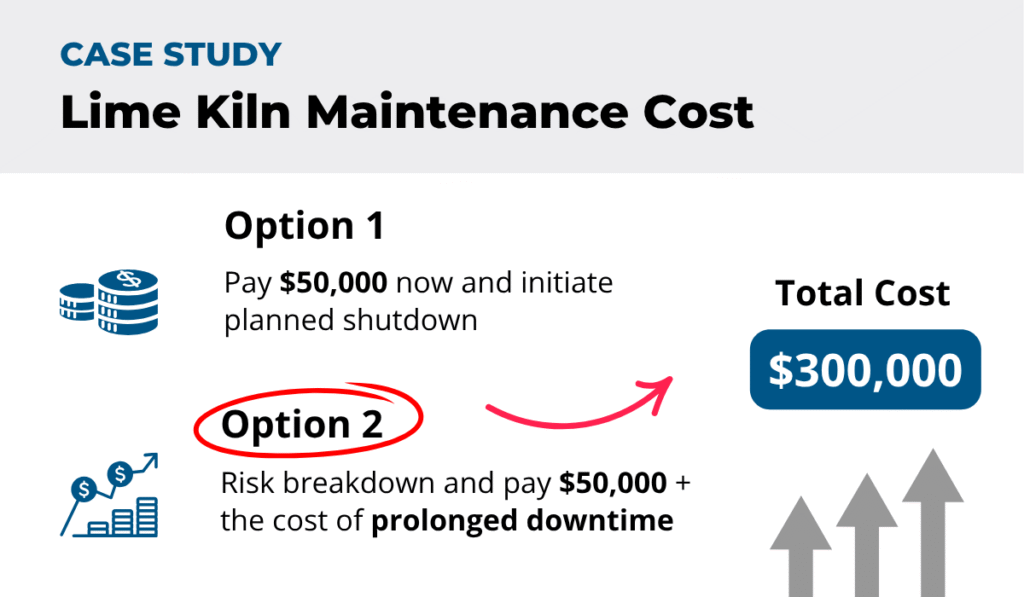
Illustration: GoCodes Asset Tracking / Data: ReliablePlant
While this isn’t a construction-specific case, the lesson is clear:
Proactive maintenance always costs less than reacting to equipment failures.
And this is where asset tagging and tracking systems prove invaluable.
By tagging equipment and tracking its maintenance history, usage, and location, businesses can better predict when machinery needs servicing, reducing unplanned downtime.
In recent years, this has evolved beyond basic tagging.
Modern telematics systems that combine trackers, sensors, and data analytics work alongside asset tags to deliver a complete picture of asset health.
These systems monitor fuel usage, machine hours, idling time, and more, helping companies manage not just their assets’ whereabouts but their performance, too.
A Verizon Connect study confirms that telematics have become essential for reducing downtime, especially in vehicle and heavy equipment monitoring.
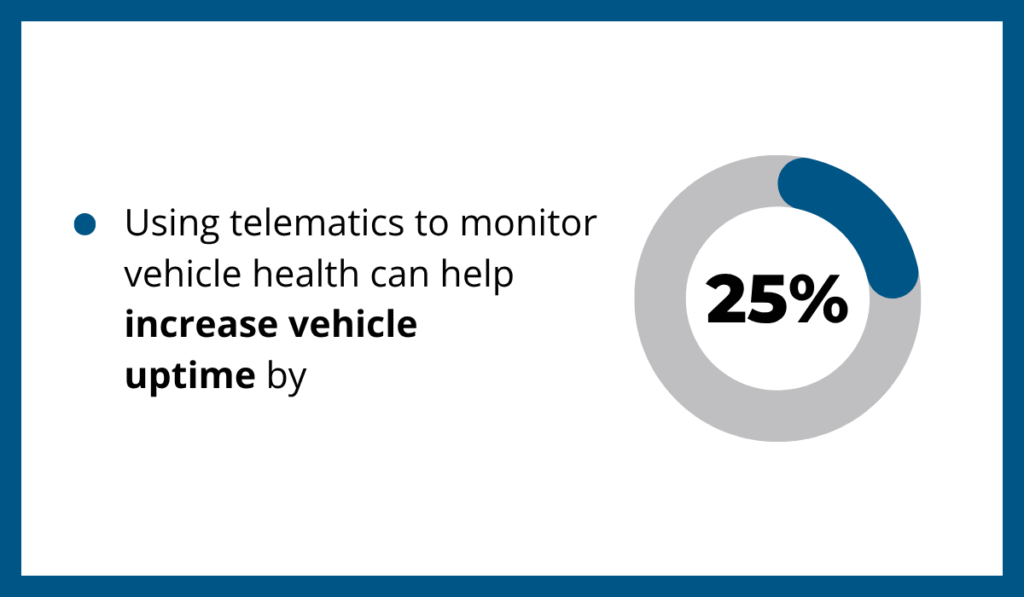
Illustration: GoCodes Asset Tracking / Data: Verizon Connect
The ability to remotely track equipment conditions means problems can be spotted and addressed before they escalate.
However, collecting accurate downtime data can be challenging.
Without reliable tracking, you risk:
- Unreported idle periods
- Incomplete records
- Misidentified causes of downtime
Tagging assets ensures you capture essential details, while integrated systems can automatically log events and flag issues.
Tools like Limble’s CMMS software use this data to calculate key metrics like Mean Time Between Failure (MTBF) and Mean Time to Repair (MTTR).
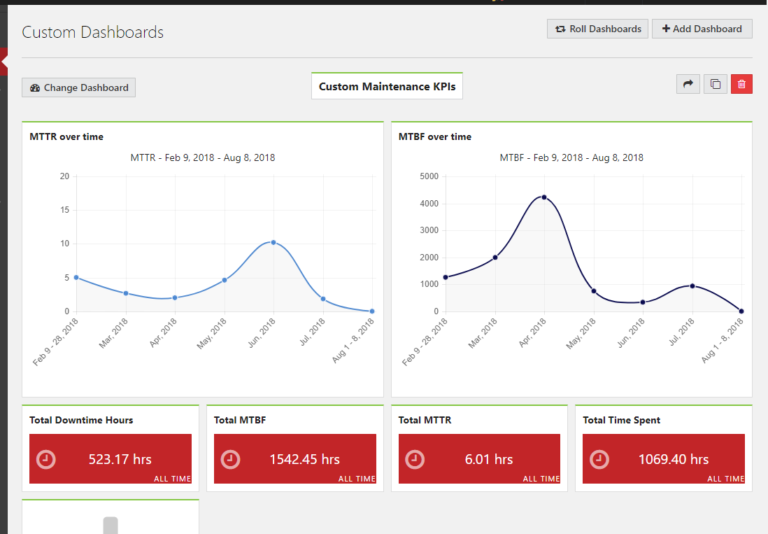
Source: Limble CMMS
These are essential insights for businesses that want to improve operational efficiency and control costs more effectively.
By combining asset tags with telematics and smart software, construction firms can prevent breakdowns, reduce costly downtime, and keep projects moving on schedule.
Helps Validate Warranty Claims
If you’re tired of missing out on warranty claims due to incomplete records or missing documentation, it’s time to look into asset tagging systems.
When equipment breaks down unexpectedly, one of the most overlooked cost-saving opportunities is a valid warranty claim.
This is ironic given how one study of 392 professionals working in construction, landscaping, agriculture, and forestry sectors puts warranties among the strongest purchase drivers for heavy-duty equipment.
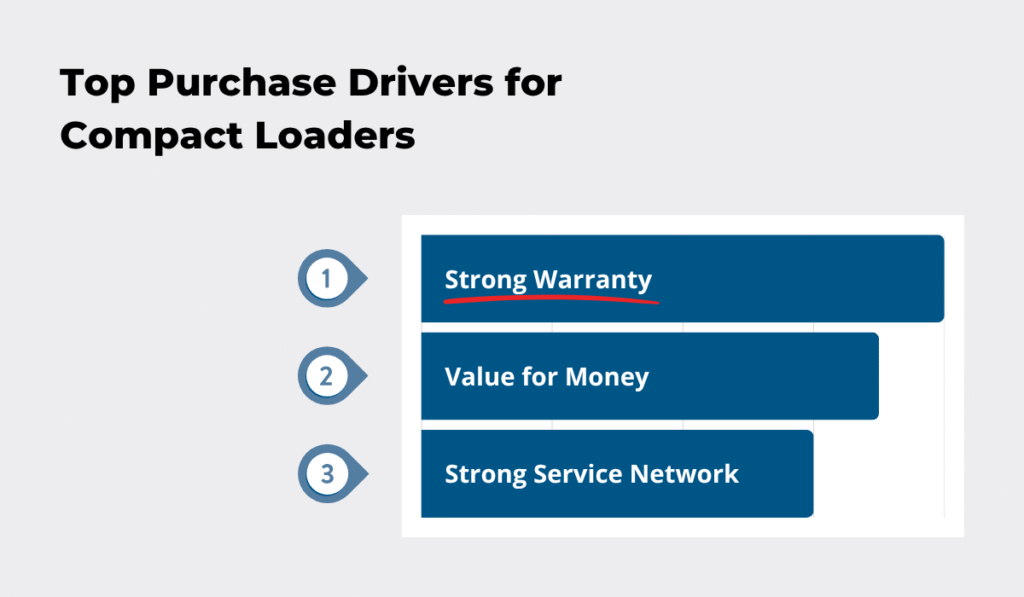
Illustration: GoCodes Asset Tracking / Data: Hanover Research
So, how does this happen then?
Warranties typically require proof of purchase, maintenance history, and usage logs to validate a claim—without this information, claims may be denied or delayed.
For construction companies managing dozens or even hundreds of assets, it’s easy for paperwork to go missing or for important details to get buried in outdated spreadsheets.
And you know that means having to pay for repairs or replacements out of pocket.
Asset tags solve this by linking each machine, tool, or vehicle to a cloud-based record containing purchase dates, serial numbers, service logs, and warranty expiration dates.
Solutions like DreamzCMMS leverage RFID, QR codes, barcodes, and IoT sensors to ensure seamless access to key maintenance, warranty, and asset lifecycle data.
One scan, and you can access all the information you need to submit a successful claim.
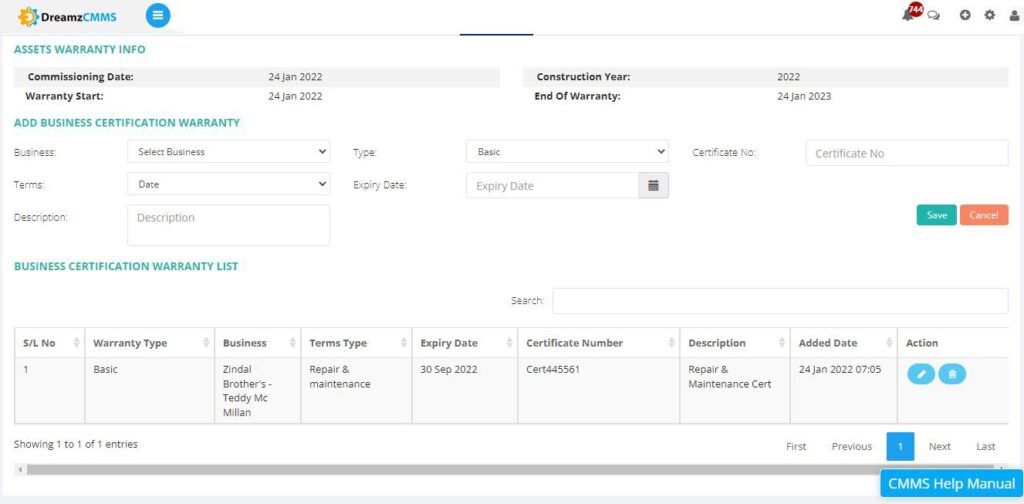
Source: DreamzCMMS
The financial impact of this is significant.
Fast, successful claims mean less time covering expenses yourself and less disruption to your cash flow.
And for higher-value machinery, the savings from a single approved claim could cover the cost of an entire tagging system.
A good asset management system will also notify you when warranties are about to expire, allowing you to arrange inspections or file claims before coverage lapses.
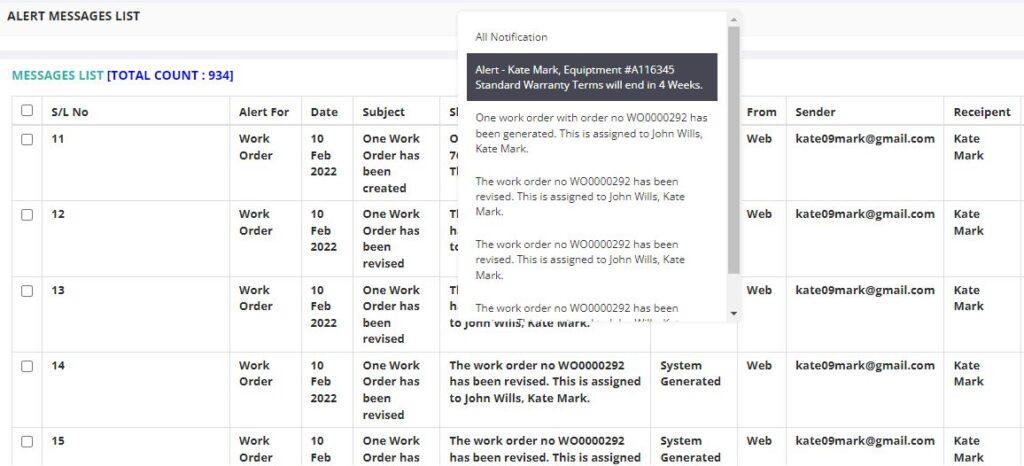
Source: Dreamz CMMS
That’s a valuable feature for any manager handling dozens, hundreds, or thousands of assets.
In conclusion, asset tagging helps you recover costs even when equipment fails, so don’t miss out on this opportunity.
Conclusion
Prevention is always more affordable than reaction, and nowhere is that clearer than in construction.
Every untracked or poorly managed asset represents a financial risk, whether through theft, downtime, or premature replacement.
Fortunately, asset tagging solutions give you the oversight and data to stop losses before they start, optimize equipment usage, and recover costs quickly when issues arise.
With so many proven benefits of connected, cloud-based tracking systems, there’s no reason to delay.
Start tagging, and you’ll also start saving!