Implementing system-wide changes to existing work structures is a significant challenge for any business.
In the case of asset tracking, the amount of time and effort required for software installation, data import, and staff training means production might have to slow down for some time.
This, combined with the price of the system itself, constitutes a costly investment, which is why you need to be certain that the changes you make provide a return on that investment.
In this article, you will find seven notable benefits of fixed asset tracking that should help you decide if it is a worthwhile endeavor for your construction company.
Let’s start with going over how tracking assets affects their utilization rate.
In this article...
Increased Asset Utilization
Just like an employee idling on the job instead of doing his or her tasks is a waste of your company’s resources, underutilized equipment also constitutes a cost.
Granted, it’s not a direct cost.
However, every asset has a purchasing price and operating expenses, such as maintenance, whether it’s used or not.
Therefore, to maximize the profit on those expenses, businesses must ensure they use their equipment to its full potential.
A metric used to track the use of equipment is called asset utilization.
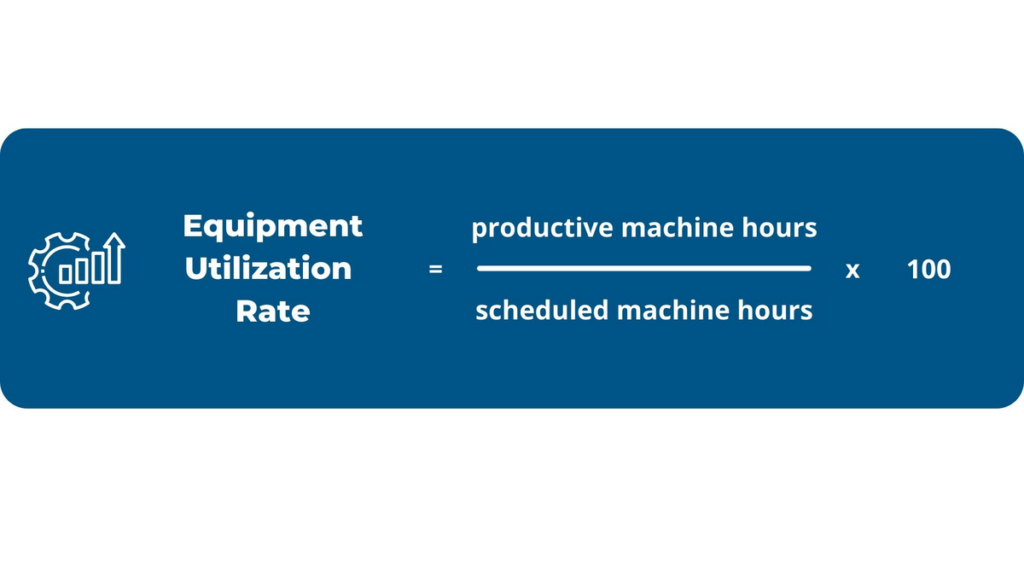
As John Sessions and his co-authors define it in their scholarly paper on the subject, equipment utilization “measures the percentage of the scheduled time that equipment is either expected or observed to work.”
With a fixed asset tracking system, construction companies will have access to every metric needed to increase the productive hours of their equipment.
For example, they will know exactly how many assets they have, where they are located, who is using them, and for what amount of time.

Armed with this information, managers can more effectively allocate assets to different time slots, workers or job sites.
This leads to improved utilization rates and, consequently, a more efficient workflow overall.
Ultimately, tracking fixed assets gives businesses a better understanding of how their equipment is utilized, allowing for more effective equipment allocation, increased operational efficiency, and subsequent profit growth.
Better Employee Accountability
Everyone who’s done any type of construction job knows how easy it is to misplace tools.
After all, construction sites are large areas filled with people doing multiple tasks using different tools.
With no consequences to taking shortcuts, it’s easy to see how some of those tools might get left behind.
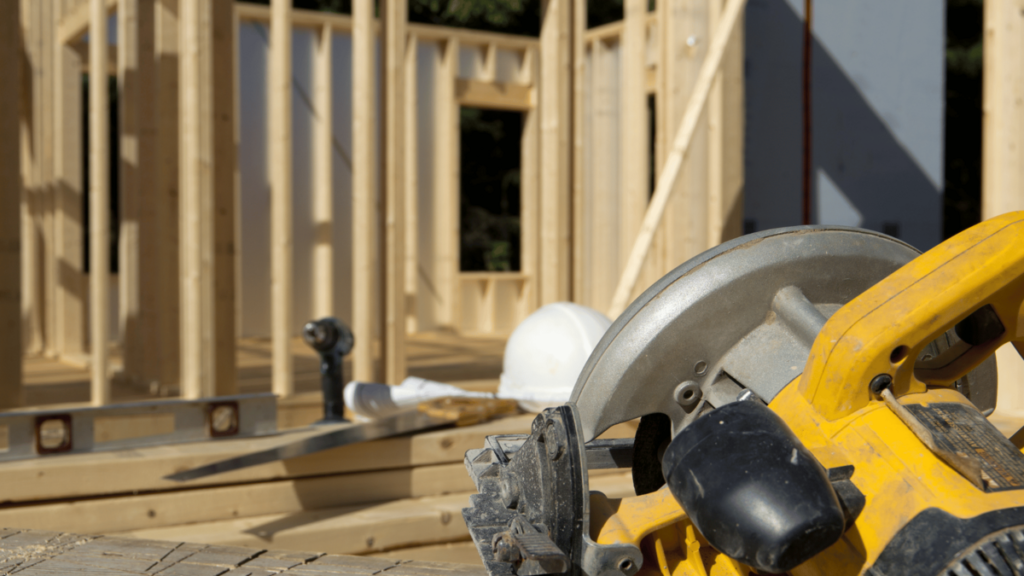
By providing insight into who uses the equipment and when, fixed asset tracking can help businesses in making employees more accountable for the tools in their care.
After all, if they stand to face repercussions for improper use, even if it’s only a verbal reprimand, workers will act more responsibly in using the equipment, as well as take better care to ensure it finds its way back to storage.
All you need is tracking software with a check-in/check-out feature.
The way it works is pretty straightforward.
Similarly to taking out books from a library, workers can use the system to check out equipment under their name when taking it from storage.
For those familiar with how it works, the process can be done in under 5 seconds. The authorized personnel first need to scan an asset’s QR code tag with a smartphone.

This opens up its database entry page. From there, it’s easy to view and update any number of data points or do a quick check-out.
All it takes for the latter is assigning the asset to a particular person, with an optional projected return date and additional notes.
Returning the equipment also takes just a scan and a few clicks, making the process simple for workers to adopt.
All in all, fixed asset tracking enables businesses to assign equipment to employees, which incentivizes them to pay more attention when using it on the job.
Lower Risk of Theft
Increased visibility
Theft is a pretty common occurrence in the construction industry.
In fact, several years ago, the National Equipment Register reported more than 11,000 instances of misappropriation in the US in one year alone, causing an estimated $400 million worth of damage.
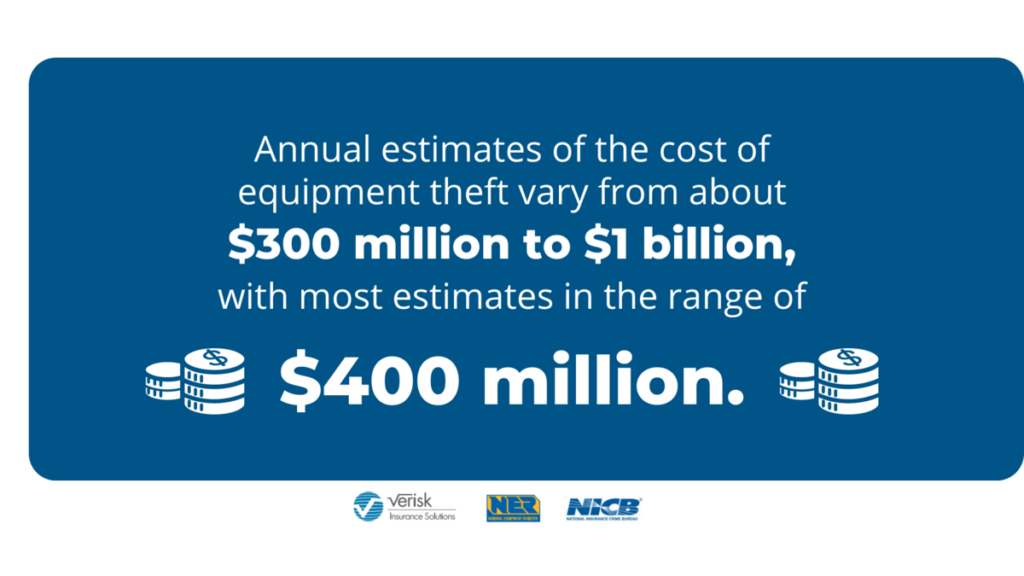
Not to delve too deep into the details, the reasons for this are commonly understood to be the high value of equipment, lacking construction site security, and relatively low penalties for criminals.
With tracking software like the one GoCodes Asset Tracking offers, businesses are able to track the location of their assets, providing a better chance of preventing theft and recovering items once they are noticed missing.
There are two location tracking methods to choose from or use conjunctively.
For the first one, you need QR code tags and smartphones.
Since you have to be in close proximity to an asset to scan the tag, the system uses the smartphone’s GPS coordinates to update the location of an asset whenever it’s scanned.
While not providing real-time tracking, this method can help you determine the asset’s last known location and user.
This information can be essential in helping the authorities recover the equipment that’s been stolen from your lot.
The second method includes BLE (Bluetooth Low-Energy) trackers or, as GoCodes Asset Tracking refers to them, Bluetooth Beacons.

These are low-cost, low-maintenance trackers that send out radio signals in a range of up to 300 feet.
The signals can be picked up by any Bluetooth-enabled device, such as computers, tablets, and smartphones.
The signal reveals the asset’s identity and the distance from the scanner, giving you real-time insight over as many assets as are in your range.
To prevent theft, GoCodes Asset Tracking has developed the accompanying Guardian feature, which automatically sends out alerts when an asset/beacon goes out of its range.
That way, you can react as soon as the theft happens, dramatically increasing the possibility of successful recovery and discouraging further attempts.
Overall, construction equipment theft is a relatively common occurrence and is bound to happen to most companies at one point.
However, fixed asset location tracking can go a long way in recovering stolen property and keeping criminals from your site.
Decreased Maintenance Costs
The importance of utilization for maximizing profits has already been discussed in a previous section.
However, to make the best out of their assets, businesses also need to ensure that their equipment is properly and regularly maintained.
That means developing and keeping to a preventive maintenance schedule, all of which can be helped with a fixed asset tracking system.
As opposed to reactive maintenance, which aims to fix a problem only after it occurs, preventive maintenance is based on the principle of failure prevention.
This is because critical failures cause excessive damage and usually require expensive repairs and replacement parts.
Seeing as equipment usually shows signs of an issue before it escalates into critical damage, businesses can avoid the worst-case scenario by performing maintenance at regular intervals.
According to the US Department of Energy, a predictive maintenance schedule leads to:
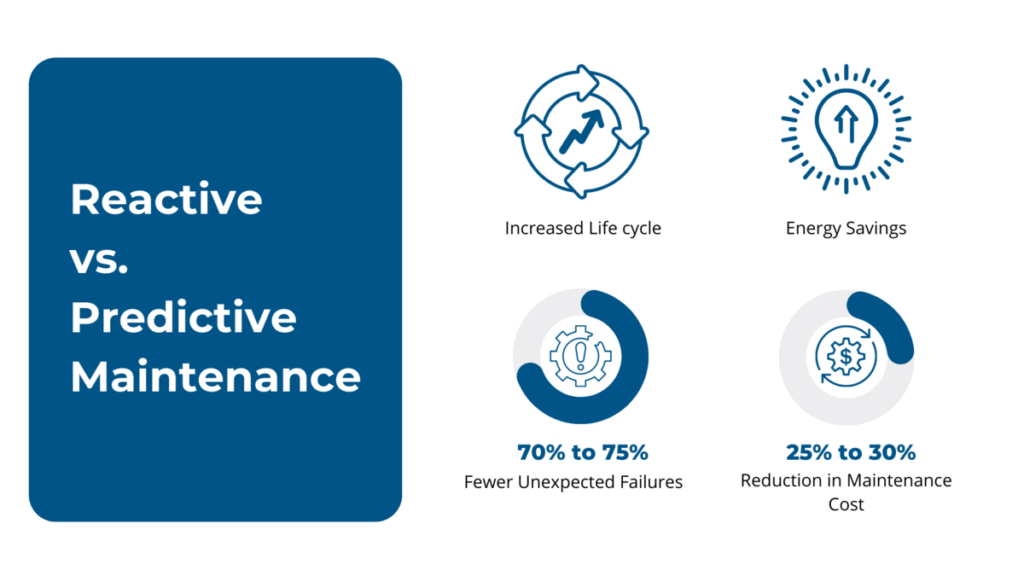
A fixed asset tracking platform allows you to track asset data like maintenance history, usage, and condition, allowing you to create optimal maintenance schedules for every piece of equipment.
Additionally, businesses can use it to schedule maintenance tasks and set timely email reminders, which ensures no asset is left unchecked.
In summary, fixed asset tracking gives construction managers the ability to create a preventive maintenance schedule.
This leads to fewer unexpected failure events and reduced maintenance costs, making for a more profitable business.
Informed Decision-Making
To successfully manage a construction company, one needs to be skilled at making quick decisions on a daily basis.
However, to make the right calls, it’s also essential they have access to all the relevant data.
With fixed asset tracking, businesses are privy to various information on the whole lifecycle of their equipment, from the initial purchase to the inevitable end of service.
Analyzing this data allows them to gain valuable insight into their asset management practices, enabling them to make appropriate changes and keep track of the results.
To make said results presentable and easily digestible, asset tracking software often comes equipped with a reporting feature.
This allows you to use the data from the asset register to create any number of reports, such as inventory reports, maintenance information, financial reports, and workflow reviews.
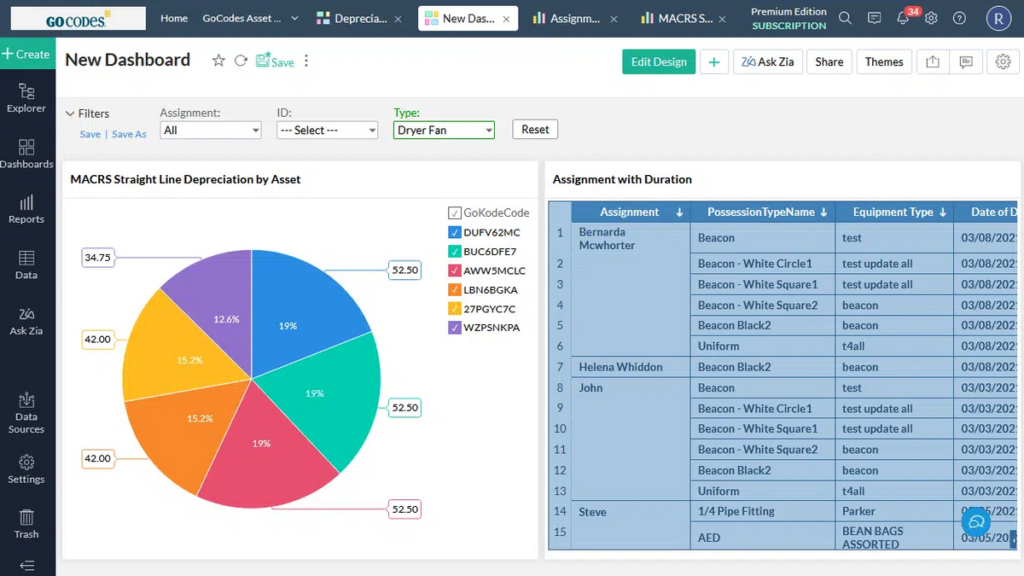
Seeing as every business is different, many asset tracking systems allow you to make custom reports for a particular time frame, asset type, or data set.
This way, it’s easy to adjust it to fit your company’s unique needs or management strategy.
Other than that, reports can help you with sharing and updating your team on the company’s progress.
Tracking software usually has the option to create and send reports automatically in designated intervals.
Moreover, some also provide dynamic reports, which are placed online under an URL and are updated in real time.
In conclusion, by granting access to different data points across the equipment’s life cycle, fixed asset tracking can help construction managers make better-informed decisions on their strategies going forward.
Easier Asset Audits
Although audits are usually seen as time- and energy-consuming processes, there are many benefits they can bring to your business.
Verifying that equipment is present and checking its condition can help companies with everything from reducing redundancy and waste, to lowering asset loss and tracking depreciation.
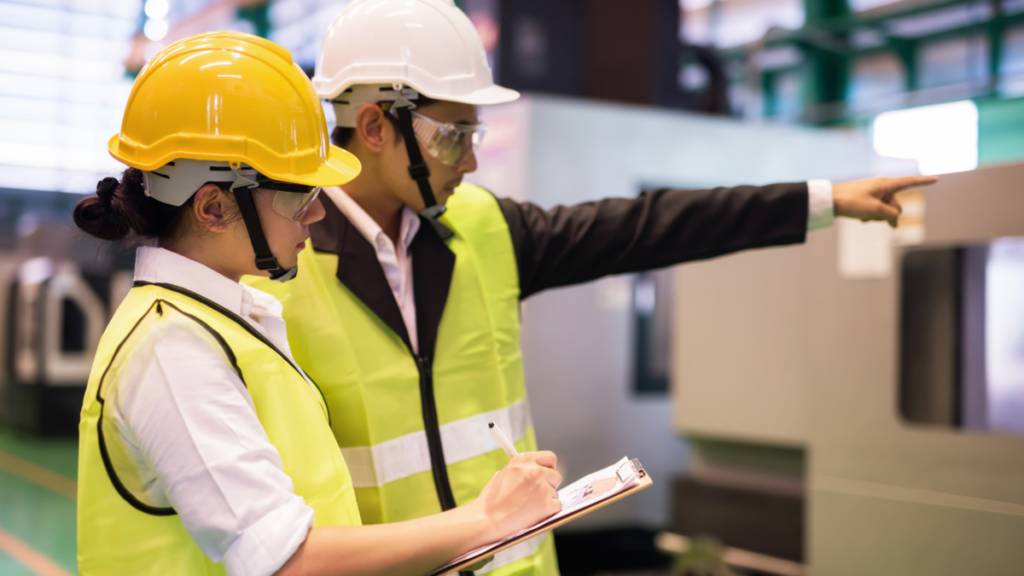
By using asset tracking software, performing audits becomes an effortless and relatively short process.
Therefore, companies can enjoy the benefits of audits without suffering the drawbacks that come with a manual workflow.
After all, manually checking serial numbers and entering the information onto a spreadsheet is a repetitive task and one that is easy to lose concentration on.
Given that the research shows that the human error rate in similar tasks is between 1.8% and 16%, automating the process will eliminate a lot of course-correcting tasks related to mistyping or mismatching assets.
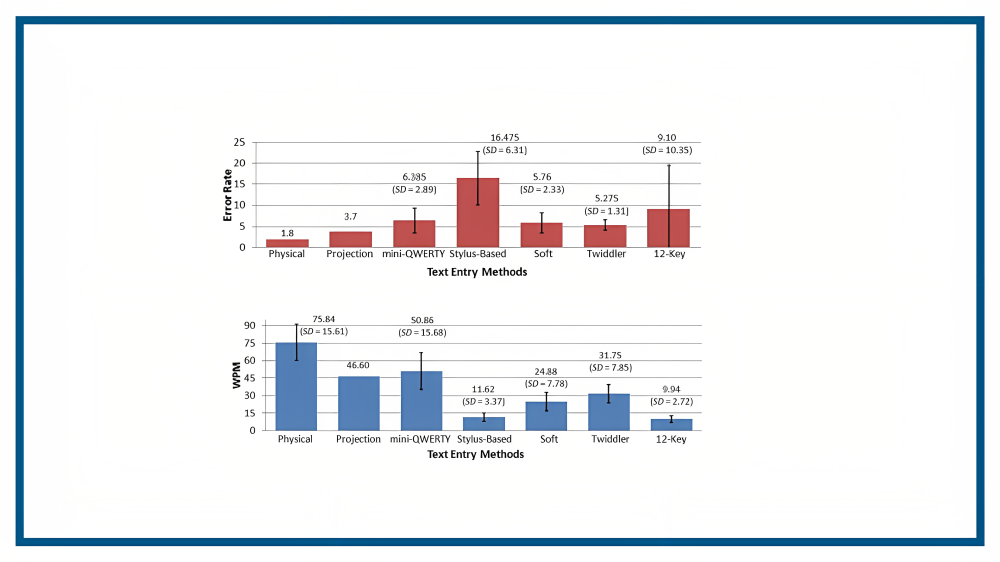
It is also a slow process, with the fastest typers only managing about 75 words per minute, and that’s in optimal conditions.
On the other hand, going around a warehouse checking asset numbers against a database with the right tracking solution is both fast and accurate.
For instance, with GoCodes Asset Tracking, you simply have to scan the asset tag with a smartphone, which automatically updates the asset’s location in the database, confirming the equipment is still in place.
Some asset tracking software even enables you to scan and update multiple items at once.
Not only does this take less than a second to do, but it also dramatically reduces the chance of error.
Overall, tracking equipment with asset tags and smartphones facilitates audits by replacing much of the repetitive, manual tasks that are susceptible to error with a fast, accurate automated process.
Improved Regulatory Compliance
Construction is a heavily regulated industry. This is not surprising, as it is in the best interest of everyone to have safe, stable structures that are not a danger to those in or around them.
Moreover, construction companies also need to guarantee the safety of the workers, who are often working in dangerous and life-threatening conditions.
Therefore, they have to be careful to comply with all of the rules, regulations, laws, and standards prescribed by their governmental and regulatory bodies.
Otherwise, they risk facing fines and other penalties that can have a strong negative impact on a business’s reputation or finances.
Here are some of the challenges in managing asset compliance:
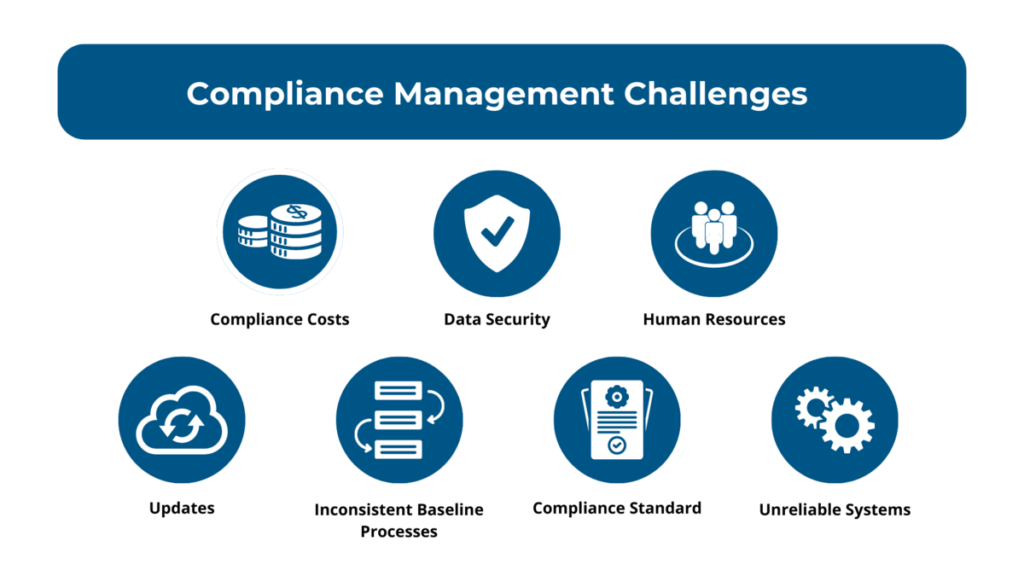
With asset tracking software, most compliance-related activities are automated.
This solves many of the challenges named above, such as inconsistent baseline processes, unreliable systems, and the lack of human resources.
In turn, your business processes will be conducted in accordance with the relevant regulation, driving management costs lower and boosting workplace efficiency.
Asset tracking software also ensures your definitions are always up-to-date, freeing you from constantly checking for new regulations, so you don’t inadvertently end up with a fine on your hands.
All in all, fixed asset tracking provides construction businesses with an automated, resource-light method to overcome the various obstacles and complications of compliance management.
Conclusion
As mentioned at the beginning of this article, implementing asset tracking in your construction is certainly a challenge and an investment.
Now that you’ve learned about the benefits asset tracking can bring to your construction business, ranging from improved operational efficiency to increased profitability, you can determine whether you think this is a worthwhile investment.
If you decide that it is, consider taking the next step by researching available asset tracking solutions to find the best fit for your company.