Key Takeaways
- Idle time is a period during which your equipment is available and functional, but isn’t being used.
- Downtime describes the time during which the asset isn’t in shape to run due to a breakdown or scheduled maintenance.
- Tracking equipment idle time and downtime with the help of software solutions can help you maximize equipment utilization.
When we talk about equipment utilization in the construction industry, a couple of terms keep popping up that you’re likely familiar with.
Among these are equipment idle time and equipment downtime.
There is some confusion about the difference between the two, and the fact that they’re sometimes used interchangeably isn’t helping.
Addressing utilization-related problems requires a deeper understanding of idle time and downtime, and that’s exactly what you’ll find in this article.
Join us as we illustrate the overlapping points, the similarities, and the differences!
In this article...
What Is Equipment Idle Time
When an asset is fully functional, but simply isn’t tackling any work-related tasks—assigned or unassigned—we’re talking about idle time.
Equipment idle time refers to the unproductive, in-between time when there is no legitimate reason why a piece of machinery isn’t being used to its full potential.
Your machinery isn’t experiencing failure or undergoing maintenance, yet it’s not working.
To illustrate this, think about how idle time can be applied to both workers and machinery.
An employee who’s waiting for the system to come back online is experiencing idle time, but so is a truck on the job site waiting to pass by an asset that’s blocking the path ahead.
So, what causes idle time?
There are some typical situations and scenarios, such as:
- Lack of raw material
- Power outages or other technical issues
- Dependency on other processes to complete the job
- Unexpected stoppage because of external factors
Nevertheless, it’s useful to categorize these situations into common causes along these four lines.
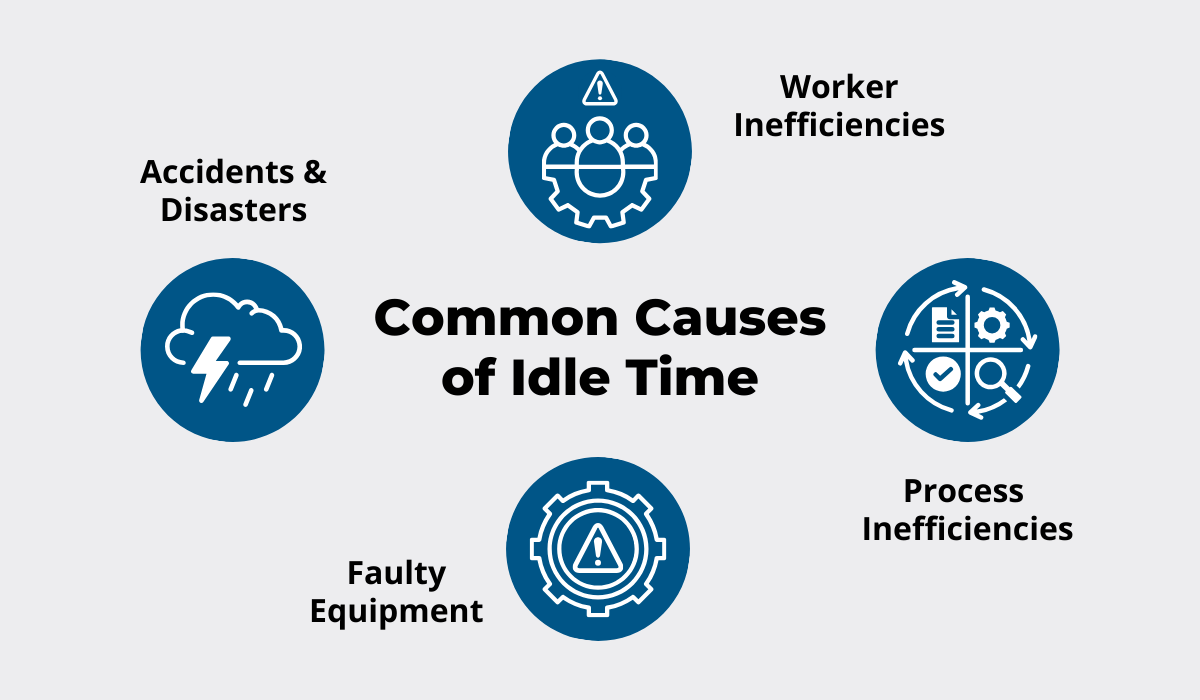
Construction firms often find it difficult to pinpoint the exact causes of idle time, since there are many contributing factors.
For the time being, we’ll disregard accidents, natural disasters, and faulty equipment, and move on to worker and workflow inefficiencies.
Worker inefficiencies encapsulate a whole range of behaviors that stem from employees, spilling over into equipment idle time.
It’s the human factor, plain and simple.
For example, an employee’s attention can wander away from the task if they’re impacted by something from their personal life.
Drops in efficiency and awareness are also fairly common with new employees, who are still getting used to the new setting and may still be unfamiliar with all the procedures.
However, not all employees are handling distressing life events or are fresh out of onboarding.
So, how does idle time still happen?
Well, inefficient processes and workflows have a way of eating away at productivity, too.
If scheduling is not done exactly right, the unproductive periods will accumulate, and last a longer time.
It’s the same when it comes to asset management and resource allocation.
The crucial point is to recognize which idleness situations are the most problematic for your construction business and address them differently from normal idle time.
This important distinction between normal and abnormal idle time is captured in an example shared by Limble, which you can see in the image below.
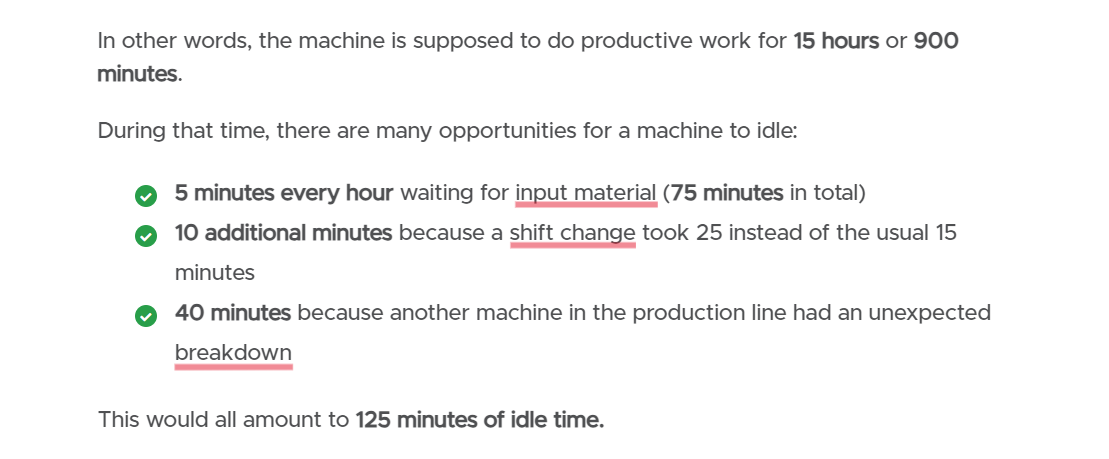
The two-hour long idle time may raise an alarm at first glance, but the fact of the matter is, reducing idle time to zero is neither achievable nor always advisable.
After all, if the additional 10 minutes during shift change ensures that the machine operator stays focused, it’s a much smaller price to pay compared to the repair and maintenance costs of heavy machinery.
Completing preventive maintenance tasks is another example of normal idle time.
This is precisely where some confusion about the terminology usually seeps in.
But before we dive into the key differences between the two terms, let’s find out more about equipment downtime.
What Is Equipment Downtime
Equipment downtime describes assets that are undergoing maintenance, and as such aren’t operational or available at the moment.
The beginning of equipment downtime is easy to establish, as it directly relates to the asset’s condition and availability.
For instance, the maintenance crew could either check out a piece of equipment from the warehouse based on their schedule or pick it up directly on the field.
But the moment the asset stops or cannot perform its job counts as the beginning of the downtime.
Moreover, regardless of whether the maintenance is planned or unplanned, the asset immediately becomes inactive, rather than linger in the construction site limbo.
Simply put, it cannot return to the construction site until it’s been cleared from maintenance.
Now, what causes equipment downtime?
Take a look at some of the common culprits in the image below.
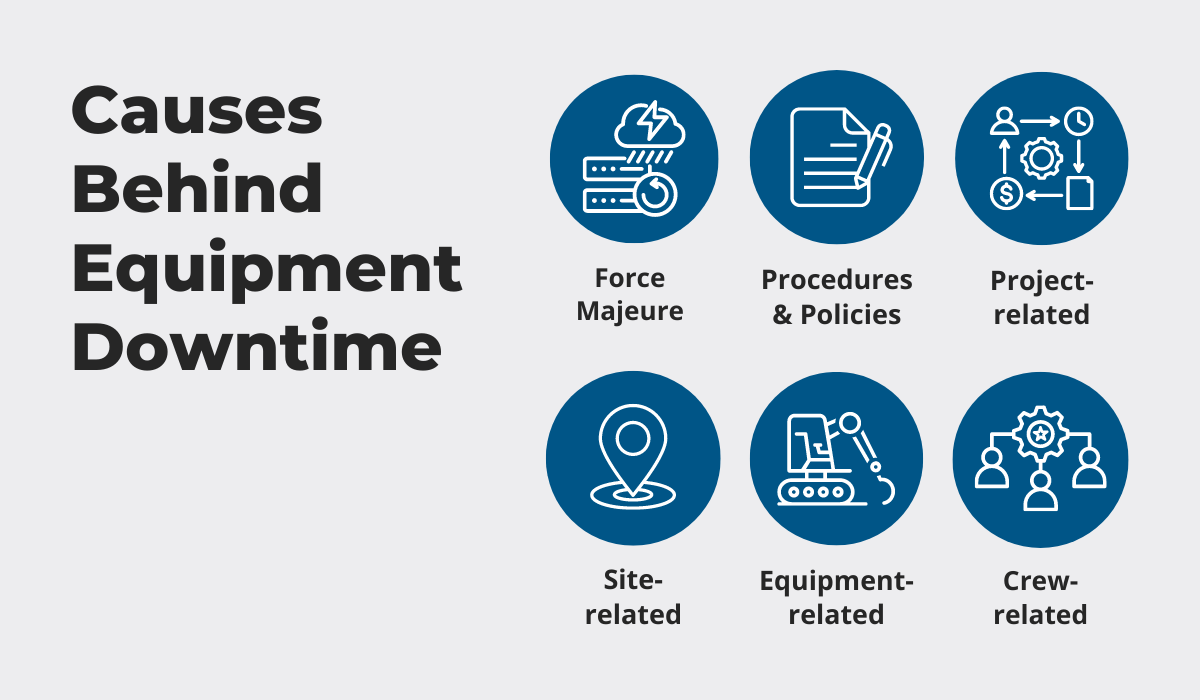
A good starting point is an enduring downtime model developed specifically with the context of construction equipment management in mind.
It’s based on six distinct factors that contribute to downtime, covering everything from working conditions and terrain to worker fatigue, motivation, and skill level.
The model is another tool that facilitates and encourages a thorough analysis of the root causes of the downtime that businesses experience.
But to interpret results correctly, it’s crucial to differentiate between planned and unplanned downtime, rather than lumping them together.
We broke down the difference between the two in the image below.
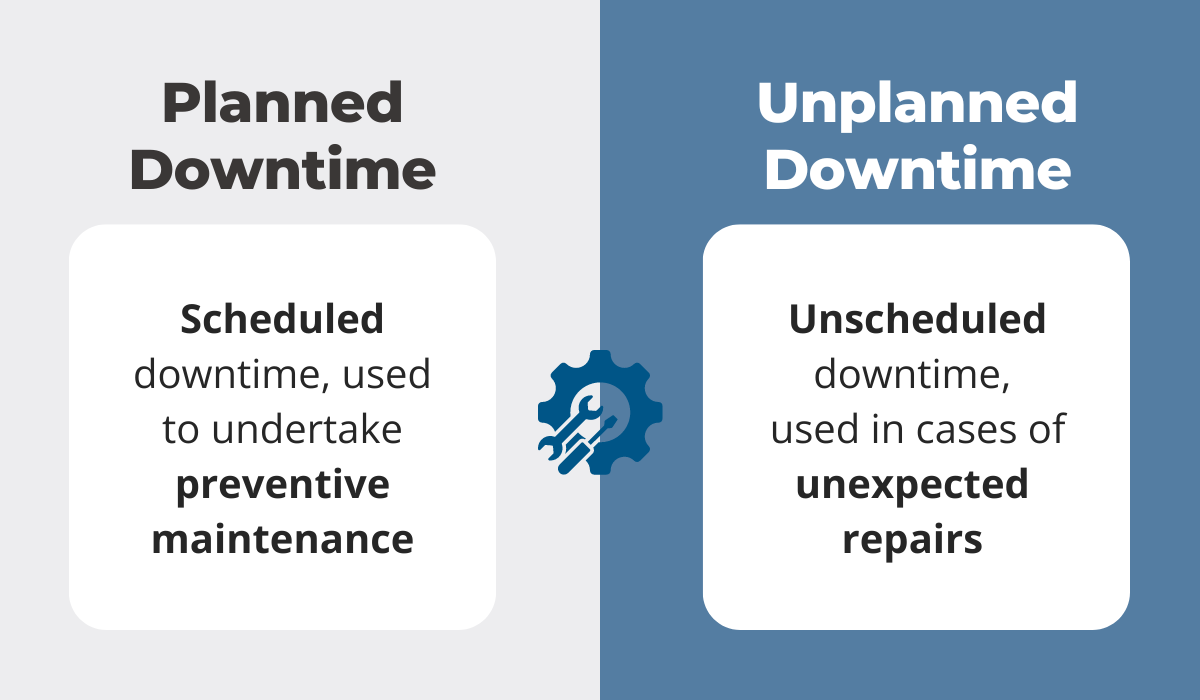
Planned or scheduled downtime means that the construction company allocated a specific time slot for preventive maintenance of a certain asset.
Equipment maintenance is conducted as a necessary step to ensure optimal condition and peak operational efficiency.
Nevertheless, given that the asset isn’t productive while in maintenance, and that this intervention is planned, the allocated period doubles as idle time.
This overlap between planned downtime and normal idle time is one of the reasons why some of the confusion about the terminology remains.
On the other hand, unexpected machine failure leads to breakdown maintenance, meaning that the asset requires care and repairs before it can be functional once again.
Breakdown maintenance is synonymous with unplanned, i.e. unscheduled downtime, as well as abnormal idle time.
And if you’re wondering why “abnormal,” take into account that the equipment breakdown event is often outside of the business’s control and has the potential to hurt overall productivity.
Finally, paying close attention to planned and unplanned downtime means giving a wealth of insights to construction managers, including:
- Organizing maintenance staff
- Enhancing implementation of maintenance tasks
- Increasing profit and lowering maintenance costs
- Determining replacement and repair priorities
- Ensuring higher machine uptime, efficiency, and reliability
Now that we’ve covered each of these terms separately, it’s time to draw more concrete parallels and compare the two.
Equipment Idle Time vs Downtime: Key Differences
As we’ve already established, the key distinction between equipment idle time and downtime has to do with the asset’s status.
If the asset is functional, but not used for whatever reason, we’re talking about idle time.
And if the asset can’t be used because it’s undergoing maintenance, think downtime.
However, since scheduled maintenance is sometimes referred to as normal idle time, there is some overlap between the two terms.
This comes from the fact that quieter business periods (or idle time), are considered the perfect time to conduct maintenance.
By scheduling preventive maintenance, companies counter and prevent unexpected breakdowns and unplanned downtime, keeping workers safe, and protecting their assets.
When it comes to some key characteristics and differences between equipment idle time and downtime, here is a quick overview.
IDLE TIME | DOWNTIME |
---|---|
Asset inactive; available and functional, but isn’t running | Asset inactive; isn’t in shape to run due to breakdown or scheduled maintenance |
Insufficient productivity, but also an opportunity to schedule maintenance | Non-availability or non-operability |
More ambiguous and multifaceted causes | Simpler causes behind it |
Should be minimized or otherwise used only for maintenance | Only unplanned downtime should be minimized, planned downtime is essential |
Now, you may be wondering why would idle time and downtime need to be tracked separately if both give you information about inactive equipment.
Although both represent a loss in productivity, idle time can prove beneficial for your business, with the collected data used as the basis for creating a preventive maintenance strategy.
First, however, you need to clearly define what constitutes idle time, and make note of it to be able to meet your utilization and profitability targets.
Meanwhile, with unplanned downtime, the trick is to detect and precisely measure how much time is spent on unplanned, prolonged, and costly reactive maintenance.
By tracking the metrics separately, you’re capturing accurate data and immediately funneling it in the direction you need.
Good asset tracking or equipment maintenance software makes a world of difference when it comes to tracking and collecting data.
It’s a simple premise: by monitoring your equipment, you can find out which of your assets are sitting idle and why.
And once you have the baseline, you can adjust your scheduling, and simply reassign the assets when and if needed.
Relying on software to gain insights is the norm in this day and age.
RJV Construction’s Equipment Manager, Dave Pacella, couldn’t agree more.
Pacella notes that relying on spreadsheets, pieces of paper, or memory means that “things were getting overlooked” and that the whole process was far from smooth.
However, things changed when this underground utility contractor started using specialized construction software.
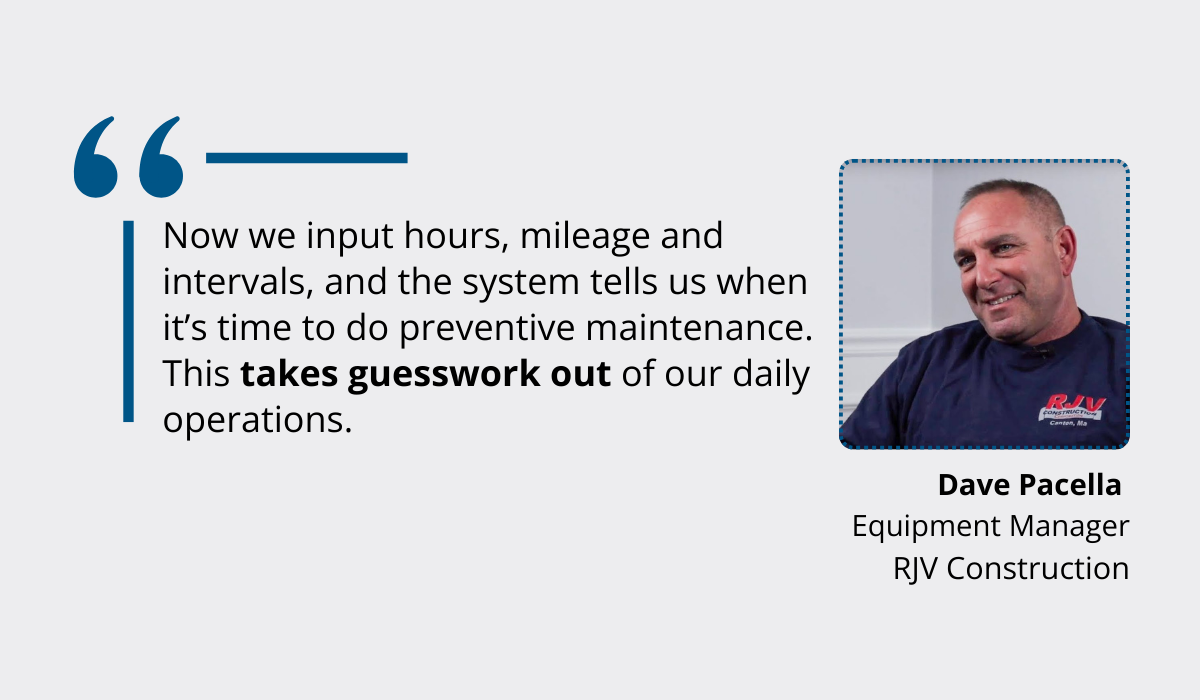
Real-time accurate insights offered by software solutions create the basis for all operations, including preventive maintenance programs that enhance equipment utilization.
By regularly inspecting and repairing their equipment, construction companies can counter unexpected breakdowns while reducing additional expenses.
Preventive maintenance programs are created based on different data, including idle time and downtime, which are then used to extend equipment lifespan and enhance overall project productivity.
Our own asset tracking software, GoCodes Asset Tracking, was created to empower construction businesses by offering plenty of functionalities at an affordable price.
In addition to tracking each piece of machinery in real time, powerful reporting features compile everything you need to know about your assets’ utilization and maintenance needs in one place.
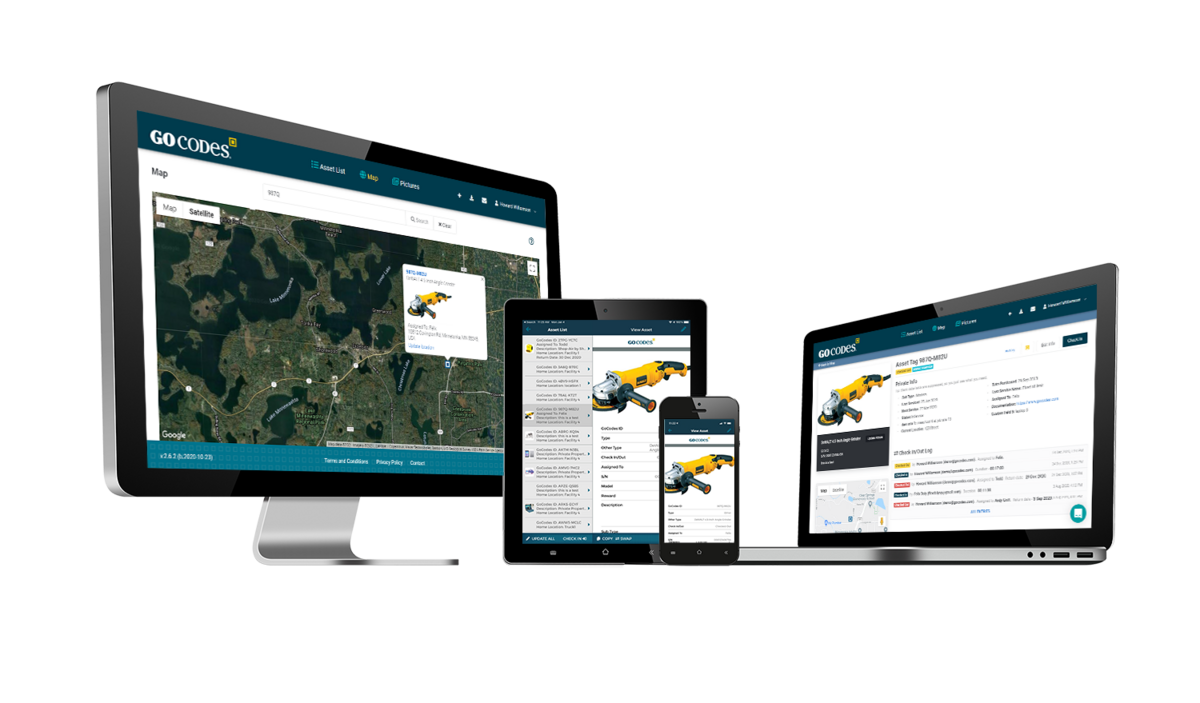
Finally, automated field service requests are easily sent via smartphone, and email reminders ensure that everyone who needs to be in the loop regarding maintenance is notified promptly.
With all of this at your fingertips, it becomes easy to avoid unwanted idling and unplanned downtime of your equipment.
Conclusion
Distinguishing between equipment idle time and downtime is crucial for construction companies that want to close productivity gaps and boost equipment utilization.
Idle time refers to situations when assets are functional but not productive. Luckily, this time can be put to good use for scheduled maintenance.
Meanwhile, downtime indicates that the asset is inactive, either due to regular maintenance or catastrophic failure.
This results in unplanned downtime which should be minimized as much as possible.
Software solutions help you track both metrics separately, refine your predictive maintenance plans, and transform your business.
So it’s time to get the most out of them!