Safety should be the number one priority on every construction site.
It affects the well-being of your employees and impacts the project itself.
Being lax about safety can lead to injuries and accidents and cost you a lot of money in fines, penalties, downtime, and postponed projects.
Here’s what you can do to improve your construction site safety!
In this article...
Have a Detailed Safety Plan
Safety always begins with a plan.
Protecting your employees is your responsibility: you’re the one in charge of creating a foolproof safety plan.
To do this, you have to understand the essential safety requirements of your industry and the relevant laws and regulations, which differ from state to state.
With this understanding in mind, you can craft a general safety plan that you and your employees need to follow to keep safety at a maximum.
You should write about the involvement of employees and management, worksite analysis, hazard prevention and control, and training.
Each of these aspects is vital for a functioning plan.
Keep in mind that this plan is a living document—it’s not set in stone.
You should have the option of changing and updating the document whenever a specific law or regulation changes, or when the project demands it.
Also, every safety incident is an opportunity to update and hone your plan.
If your plan doesn’t leave room for change, it’s not a sustainable option for your team, so create one you will be able to update whenever necessary.
Enforce Your Construction Safety Plan
After creating a great construction site safety plan, it’s time to apply it.
Simply having a safety plan isn’t enough—you have to enforce it.
In other words, even if you’ve created the perfect program and followed through with all the necessary steps, you have to ensure that people are following it.
Because of their training, most employees will respect the plan points and care about safety.
However, there will always be some who forget about certain aspects of it, inadvertently endangering the workspace as a result.
If you enforce your plan correctly, your employees will feel encouraged to speak up about potential hazards and warn you in time to fix them.
If you want to be sure that workers are following the plan, invest in supervision.
That way, you will have direct reports from the worksite and a clear understanding of how well the team in the field is following your safety plan.
Another benefit of supervision is being able to note every incident at the worksite, which will help you discover the faults in your safety plan and adjust it accordingly.
Enforce your safety plan to ensure maximum safety at the worksite.
Promote a Safety Culture
Promoting a safety culture moves safety from a decision maker’s commitment to a shared goal.
After you create and enforce a safety plan, you have to turn your work culture into a safety culture to ensure everyone understands its importance to the company.
Safety has to become one of your company’s core values instead of being a checklist that everyone wants to get done ASAP and move on.
Only then will you be sure that you and your employees are on the same page and that you share the same beliefs and values related to workplace safety.
After all, you’re trying to keep your employees safe from harm, and the work you put into safety benefits them directly. Fostering a safety-first type of culture will help them understand that.
Don’t treat safety plans and measures as a necessary evil. Rather, they should be the core priority for any company that values its employees and their safety.
When your employees understand the importance of safety, you’ve created a good safety culture.
Always point out the many benefits of adhering to safety standards to your employees and explain why it’s so important to you and the company.
The more they understand, the more likely they will be to follow the rules and report any hazards right away.
Invest in Training
Investing in employee training helps you enforce your safety plan.
OSHA names training as one of the four pillars of safety at the workplace.
This is no surprise, especially when you consider that many aspects lie in the hands of your employees, from PPE to using tools and equipment.
They’re the people in direct contact with your equipment and materials.
Your employees can notice and warn others if they are misusing equipment or endangering others by failing to adhere to any safety standards.
Employees are the ones who can report hazards they discover in the workplace, thus preventing accidents from happening.
However, if you want employees to do all of that, you need to train them properly.
Organize compulsory safety training for every new hire in your company and ensure that everyone goes through it and passes the test.
Create the training in line with the state laws and industry regulations and try to involve the team as much as possible to ensure you’ve covered all points.
OSHA also offers safety courses for many construction site activities and equipment, which you can use to additionally train your team.
When you offer your employees detailed training, they can recognize and avoid safety hazards.
Involve Your Employees
An essential aspect of workplace safety is employee involvement.
As previously mentioned, a safety culture cannot exist without your employees. You can think of worker protection as your core value, but it won’t matter if your employees neglect to implement that.
Your employees are those who have first-hand experience in the field—they use the equipment, see others use it, oversee many aspects of construction, and notice potential hazards.
Suppose there is an issue with the scaffolding at one of your construction sites. A supervisor who walks around the site might not notice it unless they use the scaffolding themselves.
However, the employee using it can report an issue as soon as they step on it and feel wobble under their feet.
Unfortunately, many fail to do this because they aren’t sure how unstable the scaffolding has to be for it to become a concern.
If you set high standards and expectations for your equipment, employees will know when to report an issue to prevent an accident from happening.
Encourage employees to report the hazards they notice in the workplace for maximum safety.
Provide Quality Equipment
Proper equipment can prevent fatalities and severe injuries at the construction site.
Each construction worker needs to have their own personal protective equipment (PPE) and protective clothing, depending on their task.
However, no one should go out on the worksite unprotected. Still, many do due to insufficient training, impaired judgment, or lack of supervision.
In 2019, a fifth of all worker deaths happened on construction sites. This shocking fact points to the need for quality protection for employees in this field.
Ensure that all of your employees have the necessary PPE, including hats, ear, eye, face protection, protective clothing, including hats, gloves, and boots.
On top of that, you also need to invest in quality tools and equipment. If you opt for cheaper solutions, you might be putting your workers at risk.
For example, equipment that can break while the employees use it can easily injure them and cause an accident.
Invest in proper PPE and equipment to ensure worker safety at the construction site.
Conduct Internal Safety Inspections
Construction site safety inspections help you improve your safety.
Because of the high accident and fatality rate, construction companies should perform regular, even daily, safety inspections and ensure that their safety plan is up to date and without flaw.
If you send an employee out to the site with a checklist, they can thoroughly review each point and decide whether you’ve passed or failed the inspection.
This employee can also monitor the workers to determine if they are using the equipment correctly if they’re wearing PPE, and respecting the company safety standards.
If you fail a safety inspection, use it as a learning opportunity. After all, you’re getting the chance to understand which point of the safety plan your team isn’t using correctly.
You can improve your strategy, enforce it, and train the team on doing the same.
The point of safety inspections is to detect hazards on the site, allowing you to remove them before an accident happens.
Therefore, safety inspections serve as a way of testing and tweaking your safety plan.
Promote Accountability
Encouraging accountability positively affects workplace safety.
Construction site safety begins with your employees noticing the differences between what should be and what is, to put it simply.
The training you offer to your employees gives them the knowledge to realize when something is not as it should be.
However, another point your training should teach is accountability.
It’s not enough for your employees to just be able to recognize a potential hazard—they should know it’s okay to hold themselves and others accountable.
If your employees understand that they are responsible for their own and the safety of others, they are a lot more likely to pay attention to it and notice more issues.
On top of that, the accountability culture isn’t punishment-based, which is why everyone feels free to point out errors or safety hazards, even if the managers are to blame.
Each employee can be held accountable in such a culture—from the very top to the bottom. Because of this, everyone feels responsible for their actions.
Fostering workplace accountability helps improve safety.
Report Near-Miss Situations
Hearing about near-miss situations on time helps you prevent accidents and injuries.
Near misses are unplanned events that have almost happened and resulted in injuries or fatalities.
If your workers experience them at the workplace, you need to know about them. Otherwise, you’re risking another incident.
However, many employees won’t report something that’s almost happened, be it an almost fall over a left-behind tool, assets falling from shelves, a ledge falling from the scaffolding.
As we can see in the statistic from this article, scaffolds are the third reason for fatal injuries in construction, just below roofs and ladders.
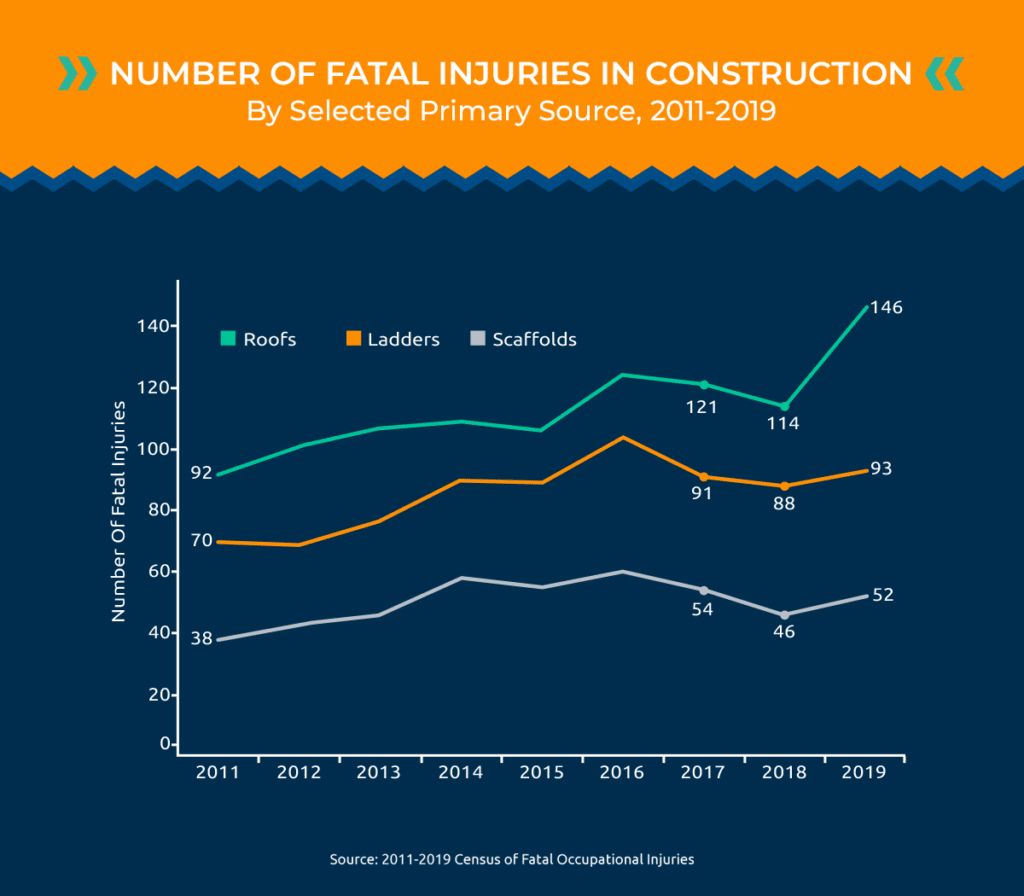
After all, why report something that never really happened?
The sad reality is—it will.
Unless you implement the right measures, although it might not happen to that same employee or on the very next day, sometime in the future, that near-miss will come to pass.
And one or more of your employees will pay the cost.
If you don’t want that to happen, explain the importance of reporting such instances to your employees.
Help them understand why you need to know about near-miss accidents to prevent them in the future and make the workplace safer for all of them.
Removing the cause of near-miss workplace situations helps improve safety.
Stock up on Tools and Materials
Having enough equipment in stock helps promote safety.
Your employees want to get the job done as soon as possible, which is why they will sometimes use any available tools and materials to finish what they started.
However, if an employee uses a tool for something other than its intended purpose, they risk injury.
Even if they don’t injure themselves, they might damage the equipment, which can later malfunction and hurt someone else.
Let’s say an employee is using a hammer to drive nails into a piece of wood.
Unfortunately, the hammer breaks, and the employee doesn’t have a replacement because there are none in stock.
So instead of waiting for you to restock, the employee uses a different tool to finish the task—which is far less efficient.
To prevent this from happening, ensure that you have enough equipment in stock.
Equipment is often hard to manage, especially if you have a lot of it, so using inventory and material management applications can help you.
Such software can even notify you when you’re running low on stock so you can order and have the equipment delivered before you even run out, eradicating the risk.
Having enough stock ensures that your employees can use the tools for their original purpose.
Conclusion
Start ensuring safety at the workplace by coming up with a safety plan, enforcing it, and encouraging everyone to do the same by fostering a culture of safety and accountability.
Of course, employee training and involvement play a massive part in any safety plan.
For further protection, provide quality PPE and tools to your team and always have them in stock.
Go the extra mile by encouraging your team to report near-miss situations and performing regular inspections at the construction site.
If your team understands the importance of safety and hears about it from the second they join the company, you’re good to go!